Titel: | Beschreibung der Fabrication des Flint- und Kronglases; von G. Bontemps, Director der Glasfabrik zu Choisy-le-Roi bei Paris. |
Fundstelle: | Band 79, Jahrgang 1841, Nr. X., S. 44 |
Download: | XML |
X.
Beschreibung der Fabrication des Flint-
und Kronglases; von G.
Bontemps, Director der Glasfabrik zu Choisy-le-Roi bei
Paris.
Aus dem Bulletin de la Société
d'Encouragement. Octbr. 1840, S. 400.
Mit Abbildungen auf Tab.
I.
Bontemp's Beschreibung der Fabrication des Flint- und
Kronglases.
Am 27. Jan. 1840 habe ich der Akademie der Wissenschaften (in Paris) eine Abhandlung
über die Geschichte der Flintglasfabrication mitgetheiltPolytechn. Journal Bd. LXXVI. S.
47.; J. L. Guinand aus Brennets in der Schweiz, war
der erste, welcher ein besonderes Verfahren hiezu entdekte. Nach seinem Tode kaufte
ich von seinem Sohne das Geheimniß dieser Fabrication, und im Jahre 1828 gelang es
mir ein brauchbares Flintglas zu fabriciren, wovon ich auch der Akademie der
Wissenschaften im October desselben Jahrs große Muster vorlegte. Der wichtigste
Theil des Problems war nun zwar gelöst; ich wollte aber auch mit der
Kronglas-Fabrication ins Reine kommen, um das gegossene Glas für optische
Instrumente zu ersetzen; dabei stieß ich auf sehr große Schwierigkeiten, die ich
endlich überwand, so daß ich nun ein Kronglas fabricire, welches eben so gut wie das
Flintglas, nämlich frei von Streifen, Blasen und Fäden ist, auch keine Feuchtigkeit
anzieht.
Die Erfindung Guinand's d. Vat. besteht im Umrühren der schmelzenden Glasmasse mittelst eines Werkzeugs
aus demselben Material wie der Glashafen.In dieser Idee allein scheint auch das Verdienst Guinand's d. Vaters um die Flintglasbereitung im Wesentlichen zu
bestehen. Unseres Wissens war er dieser Fabrication, als er nach
Benedictbaiern kam, noch keineswegs Meister, und erst nach vielen
kostspieligen Versuchen, welche alle auf Utzschneider's Rechnung gingen, gelang es ihm kleine brauchbare
Partien davon darzustellen; größere fehlerfreie Massen bereitete zuerst Fraunhofer.Hr. Prof. Steinheil in München hat bei seinen
Versuchen, ein homogenes Flintglas zu produciren, die lezte Mengung im
möglichst flüssigen Zustande der Masse nicht durch einen Rührapparat,
sondern mittelst hindurchgetriebener Luft bewirkt; seine Absicht dabei war,
daß die großen Blasen beim Aufsteigen die kleinen Bläschen mitreißen sollen
und überdieß der Sauerstoff der Luft durch seine oxydirende Wirkung die
Masse möglichst entfärbe. Das Durchblasen von Luft durch die Glasmasse, um
die kleinen Luftblasen auszutreiben, geschieht auch bisweilen von den
Glasmachern unbewußt auf einem andern Wege; sie spießen nämlich einen
Erdapfel auf einen eisernen Stab und stoßen ihn rasch bis auf den Boden des
Glashafens; die dadurch entstehenden Luft- und Dampfblasen nehmen die
kleinen Bläschen aus der Glasmasse mit sich fort.A. d. R. Er verfertigt aus feuerfester Erde einen hohlen Cylinder, welcher so hoch
wie der Glashafen, an seinem unteren Ende verschlossen, oben aber offen und mit einem platten, einige
Centimeter breiten Rand versehen war. Dieser Cylinder wurde rothglühend gemacht,
sodann in das geschmolzene Glas eingeführt und hierauf das rechtwinklich umgebogene,
einige Centimeter lange Ende einer Eisenstange in den Cylinder gestekt; das Glas
wurde umgerührt, indem man die lange Eisenstange horizontal hin und her drehte.
Ich habe zur Fabrication des Flint- und Kronglases einen runden Ofen gewählt,
in dessen Mitte ich den Hafen stelle, welcher folglich allenthalben derselben
Temperatur ausgesezt ist; ich lasse ferner den Hasen zugedekt, damit das Glas nicht
durch Stükchen des Brennmaterials oder Tropfen des Ofengewölbes verunreinigt werden
kann. Die Form und Verhältnisse des Ofens und Hafens sind nicht ohne Einfluß auf das
Gelingen der Operation.
Ich will nun das Schmelzen des Flint- und Kronglases umständlich beschreiben.
In Fig. 1,
2, 3 und 4 ist der Ofen,
der Hafen, der Thoncylinder, dessen Haken und sein Träger abgebildet. Das Flintglas
von gewöhnlicher Dichtigkeit wird wie das Krystallglas, welches man zu Tafelservice
etc. verarbeitet, meistens aus 300 Theilen Sand, 200 Theilen Mennige und 100 Theilen
(reiner) Potasche geschmolzen. Die Dichtigkeit dieses Flintglases ist 3,1 bis
3,2.
Mein Glassatz besteht aus: 100 Kilogrammen Sand, 100 Kilogrammen Mennige und 30
Kilogrammen (reiner calcinirter) Soda; diese Quantität ist nöthig, um den Hafen zu
füllen. Damit erhalte ich ein sehr weißes Flintglas von 3,5–3,6 Dichtigkeit,
welches zu den Zweken der Optiker vollkommen geeignet ist. Es versteht sich von
selbst, daß die erforderlichen Materialien in reinem Zustande angewandt und
sorgfältig gemengt werden müssen. Kalk oder Arsenik anzuwenden, ist unnöthig; sie
können nur der Weiße des Glases schaden.
Schmelzen des Flintglases. Man erhizt den Glashafen in
einem hiezu besonders bestimmten Ofen, und wenn er weißglühend ist, schafft man ihn
auf gewöhnliche Art in den ebenfalls geschürten Schmelzofen; diese Operation
erkaltet den Ofen und den Hafen; man muß also den Ofen nachschüren, um ihn auf den
möglichst hohen Temperaturgrad zu bringen, ehe man den Hafen besezt; dazu gelangt
man in beiläufig drei Stunden; alsdann hebt man vom Hafen die zwei Dekel auf (womit
er verschlossen war, um keinen Rauch hineindringen zu lassen) und besezt ihn mit
beiläufig 10 Kilogrammen Glassaz; eine Stunde darauf beschikt man ihn wieder mit
ungefähr 20 Kilogrammen Glassaz und zwei Stunden später mit 40 Kilogrammen, indem
man jedesmal den Hafen sorgfältig wieder zudekt und mit dem Besezen den Zeitpunkt abwartet, wo die auf
den Rost gebrachte Steinkohle keinen Rauch mehr gibt. Nach 8 bis 10 Stunden ist der
ganze Glassaz eingetragen; man läßt den Hafen beiläufig 4 Stunden uneröffnet; dann
aber nimmt man die Dekel weg, um den Thoncylinder einzuführen, welcher in demselben
Ofen besonders erhizt und bis zum Einführen in den Hafen weißglühend erhalten wurde;
er muß ganz rein und frei von Aschentheilchen in die Glasmasse eingesenkt werden. In
diesem Zeitpunkt ist das Flintglas geschmolzen, aber die Masse noch wallend; dessen
ungeachtet sezt man eine Hakenstange in den Cylinder und rührt zum erstenmal um,
wodurch der Cylinder verglast und schon eine innigere Mischung erzielt wird; nach
beiläufig drei Minuten ist die Stange weißglühend; man nimmt sie weg, indem man den
Rand des Cylinders auf den Rand des Glashafens sezt; da der Cylinder specifisch
leichter als das Glas ist, schwimmt er schwach geneigt, weil sein oberer Rand
außerhalb des Glases ist. Nun legt man die zwei Dekel wieder so auf, daß der Rand
des im Glase befindlichen Cylinders nicht verrükt wird und beginnt das Nachschüren
wieder. Fünf Stunden später rührt man neuerdings mit einer Hakenstange um, wo dann
das Glas schon sehr geläutert ist und nun von Stunde zu Stunde das Rühren mit einer
Hakenstange wiederholt wird; beim Umrühren ist sehr darauf zu achten, daß kein Rauch
im Ofen ist und die Thüren des Grubenraums geschlossen sind. Nachdem auf diese Art
sechs Hakenstangen verbraucht sind, wird kalt geschürt; man bringt nämlich eine
25–30 Centimeter dike Steinkohlenschicht auf den Rost, welche bald in Kohks
übergeht, so daß man den Ofen erkalten lassen kann, ohne daß der Rost bloß bleibt.
Man öffnet die Schürlöcher und die Arbeitslöcher, und so kühlen sich der ganze Ofen
und der Glashafen nach und nach ab; der Zwek dieser Operation ist, die Blasen
aufsteigen zu machen, welche sich noch nicht entbunden haben. Nach zwei Stunden ist
diese Operation beendigt und der Ofen wird wieder in vollen Fluß gebracht; nach
fünfstündigem stärkstem Schüren ist das Glas so flüssig als möglich geworden und die
Blasen sind verschwunden; alsdann wird der Rost unten genau versperrt und das große
Umrühren begonnen: sobald nämlich eine Hakenstange heiß ist, ersezt man sie durch
eine andere und fährt damit beiläufig zwei Stunden lang fort. Nach Verlauf dieser
Zeit hat die Masse eine gewisse Consistenz angenommen und läßt sich nur schwer
umrühren; alsdann beseitigt man die lezte Stange und nimmt den Cylinder aus dem
Hafen, welchen man, so wie die Schornsteine und Arbeitslöcher genau verschließt, mit
Ausnahme eines kleinen Loches von 2 Centimenter, durch welches das etwa im Brennmaterial
noch befindliche Gas entweichen können muß. Wenn sich kein Gas mehr entwikelt,
sperrt man den Ofen vollends ab und läßt ihn so erkalten, was ungefähr acht Tage
dauert; alsdann beseitigt man die Ofenthüre und zieht den Hafen mit seinem Inhalt
heraus, welcher ihm anhängt und bis auf wenige losgerissene Stüke meistens eine
zusammenhängende Masse bildet. Ehe wir von der Behandlung dieser Masse und der
einzelnen Stüke sprechen, wollen wir ausführlich das Schmelzen des Kronglases
beschreiben, welches natürlich der Flintglasbereitung sehr ähnlich ist.
Schmelzen des Kronglases. Folgenden Glassaz habe ich nach
vielen Versuchen als den besten befunden: weißer Sand 120 Kilogramme, Potasche 35
Kilogramme, Soda 20 Kilogramme, Kreide 15 Kilogramme, Arsenik 1 Kilogramm.
Der Hafen wird gerade so wie für Flintglas in den Schmelzofen eingesezt und der ganze
Glassaz in ungefähr acht Stunden eingetragen, sodann vier bis fünf Stunden später
der Thoncylinder eingeführt und zum erstenmal umgerührt, worauf man von zwei zu zwei
Stunden mit einer einzigen Hakenstange das Umrühren wiederholt; auf diese Art wird
sechsmal umgerührt. Man schürt für zwei Stunden kalt und heizt dann den Ofen wieder
sieben Stunden lang, weil dieses Glas seine Hize nicht mehr so leicht wieder annimmt
wie das Flintglas; man beginnt hierauf das große Umrühren, welches beiläufig fünf
Viertelstunden lang dauert; nun verschließt man den Hafen, die Schornsteine und
Arbeitslöcher (wie beim Flintglas) und läßt den Ofen abkühlen. Meistens erhält man
wie beim Flintglas eine zusammenhängende Masse und einige Stüke.
Zwei entgegengesezte Seitenflächen der Glasmasse werden sowohl beim Flint- als
beim Kronglas parallel gemacht und polirt, um das Innere untersuchen zu können und
zu sehen, wie sie zertheilt werden muß, denn sie ist nie ganz frei von Streifen,
welche gewöhnlich in einer einzigen Gegend angehäuft sind. Nach dieser Untersuchung
zersägt man die Masse durch parallele Schnitte und zwar nach den gemachten
Beobachtungen. Bei den im Glashafen losgerissenen Stüken werden ebenfalls
Seitenflächen polirt, um sie untersuchen zu können, worauf man sie zu Scheiben
verarbeitet; dieß geschieht auf die Art, daß man sie in einem Aufwärmeofen erhizt
und dann in eine Muffel bringt, worin man sie aber nur so weit erhizt, als es nöthig
ist, um sie formen zu können. Ist das Stük unregelmäßig, so treibt man es mit einer
Zange so zusammen, daß es gröblich zugerundet wird, faßt es hierauf mit einer andern
Zange und legt es in
die Form unter eine Hebelpresse, wodurch es genau die Gestalt der Form annimmt;
endlich faßt man es wieder mit der Zange und trägt es in den Kühlofen.
Erklärung der Abbildungen. Fig. 1 ist eine
horizontale Projection des Schmelzofens und Glashafens; Fig. 2 ein Durchschnitt
nach der Linie E F von Fig. 1, d.h. nach der
Länge des Schürlochs. Fig. 3 ist ein senkrechter
Durchschnitt nach der Linie C D des Grundrisses und Fig. 4 ein
senkrechter Durchschnitt nach der Linie A B. Gleiche
Buchstaben bezeichnen dieselben Gegenstände in allen Figuren.
A ist die Bank des zugedekten Glashafens B. C, C sind die Ofenmauern; D,
D Canäle, durch welche man die Steinkohlen auf den Rost wirft. E das Gewölbe des Ofens. F
die Thüre, durch welche man den Hafen B einführt und
herauszieht; in dieser Thür ist ein Arbeitsloch angebracht. G, G, G sechs Schornsteine. H, Arbeitsloch.
I Loch, um das Niedersezen des Hafens auf die Bank
zu erleichtern. K, umgebogene Eisenstange zum Bewegen
des Thoncylinders. L, dessen Stüze, durch welche eine
Walze geht, auf welcher die Hakenstange K aufruht. M, ein mit einem Pfropf verschließbares Loch, durch
welches man die Steinkohlen hineinwirft. N ein ebenfalls
mit einem Pfropf versehenes Loch, durch welches man den Rost reinigt. O Mantel aus Eisenblech, unter welchem die Schornsteine
zusammentreffen.
a, a Rost des Ofens; b,
Oeffnung des Hafens. c, Oberfläche des geschmolzenen
Glases. d, Thoncylinder zum Umrühren; e, Arbeitsloch; f, f die den
Rost tragenden Böke. g, Thüre des Arbeitsloches e.
Tafeln
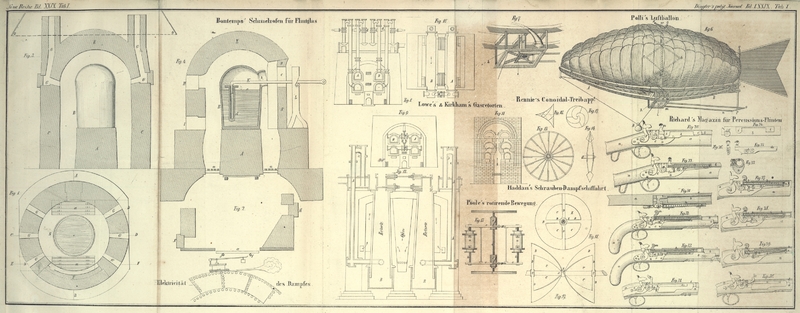