Titel: | Royle's Fabrication der Röhren für Locomotiven, Dampf- und Gasleitungen etc. |
Fundstelle: | Band 100, Jahrgang 1846, Nr. IV., S. 10 |
Download: | XML |
IV.
Royle's Fabrication der
Röhren für Locomotiven, Dampf- und Gasleitungen etc.
Aus dem Mechanics' Magazine 1845, Nr.
1163.
Mit Abbildungen auf Tab.
I.
Royle's Fabrication der Röhren für Locomotiven, Dampf- und
Gasleitungen etc.
Nach der gewöhnlichen Methode wird die Eisenschiene, woraus die Röhre angefertigt
werden soll, zuerst auf die Hälfte ihrer Länge bis zu einer Schweißhitze erwärmt und
dann vermittelst einer endlosen Kette durch Zangen gezogen, um die Ränder
zusammenzuschweißen und die äußere Oberfläche der Röhre abzurunden und zu glätten,
worauf die andere Hälfte auf gleiche Weise erwärmt wird. Diese Methode veranlaßt
einen beträchtlichen Zeit- und Arbeitsaufwand, wobei eine vollkommene
Gleichförmigkeit der Röhre schwer zu erreichen ist. Einer andern Methode zufolge
wird die ganze Eisenschiene auf einmal erhitzt, zwischen vier cannelirte Walzen
geleitet und auf diese Weise zusammengeschweißt. Die Vertiefung jeder einzelnen
Walze bildet nämlich einen Viertelskreis, und alle vier mit einander einen ganzen
Kreis, welcher die Kreisform der Röhre bestimmt. Allein auch dieses Verfahren läßt
den Einwurf zu, daß ein Theil des Eisens zwischen den Walzen hinausgepreßt wird und
an der äußeren Seite der Röhre in Gestalt von Rippen bleibt, die nachher auf eine
mühsame und kostspielige Weise durch Anwendung des Meißels oder der Feile wieder
weggeschafft werden müssen.
Hr. Royle macht nun den Vorschlag, den mit diesen beiden
Methoden verbundenen Mängeln dadurch abzuhelfen, daß man die ganze Eisenschiene von einem Ende bis
zum andern auf einmal erhitzt, und durch Zusammenschweißen, Zurunden, Glättung und
Vollendung in eine vollkommene Röhre verwandelt, ehe man das Metall sich abkühlen
läßt. Diese wichtige Verbesserung setzt er auf folgende Weise ins Werk.
Man baut zuerst einen Windofen, welcher lang genug ist um die ganze Schiene oder
Röhre aufzunehmen. Die Schiene wird sodann durch den gewöhnlichen Mechanismus
gebogen, so daß die Ränder einander berühren oder übereinander greifen. Die so
gebogene Schiene erwärmt man nun in dem Windofen bis zur Schweißhitze, nimmt sie
dann heraus und läßt sie zwischen einem Walzenpaare hindurchgehen, das so cannelirt
ist, daß es, wie Fig. 16 zeigt, an den Berührungsstellen eine Reihe von sechs von der
Linken zur Rechten kleiner werdenden Kreisen bildet. Ist die Röhre auf das erste
Strecken hin noch nicht genügend zusammengeschweißt, so bringt man sie, da sie sich
bei ihrem Durchgange durch die Walzen nothwendigerweise etwas abgekühlt hat, wieder
in den Windofen, erwärmt sie bis zur Schweißhitze und wiederholt die Operation des
Streckens zwei- oder dreimal, wenn man es für nöthig erachten sollte. Die
Röhre kann mit einem Kern versehen seyn oder nicht. Nachdem die Röhre zum
letztenmale durch die Walzen gegangen ist, wird sie durch einen beweglichen
klampenartigen Schaber gezogen, der Fig. 17 geöffnet und Fig. 18
geschlossen dargestellt ist. A ist das Untergestell des
Schabers; B ein Keil zum Niederhalten desselben; C der Druckhebel; a¹a¹, a²a² halbrunde Einschnitte, die
auf einander passen und kreisrunde Oeffnungen, die eine größer als die andere
bilden. Die Röhre wird zuerst durch die größere und dann durch die kleinere Oeffnung
gezogen und auf diese Weise geschabt und geglättet.
Um die Röhre durch das Schabeisen zu ziehen, bedient man sich einer Art Zange, welche
die Röhre am einen Ende erfaßt, und dann an das Glied einer endlosen Kette befestigt
wird. Diese Kette rotirt an der einen Seite um eine durch Dampf oder eine andere
Kraft getriebene Zahnwalze, an der anderen Seite um eine glatte Walze, und zieht die
Röhre durch das Schabeisen. A, Fig. 19, ist die endlose
Kette; B die zu glättende Röhre; C die Zange; D das Zahnrad; F das Schabeisen. Sollte die Qualität des Eisens von der
Art seyn, daß dasselbe leicht Blasen erhält (blister),
so kann man sich anstatt der beweglichen Schabevorrichtung einer soliden Form mit
einem runden Loche bedienen.
Tafeln
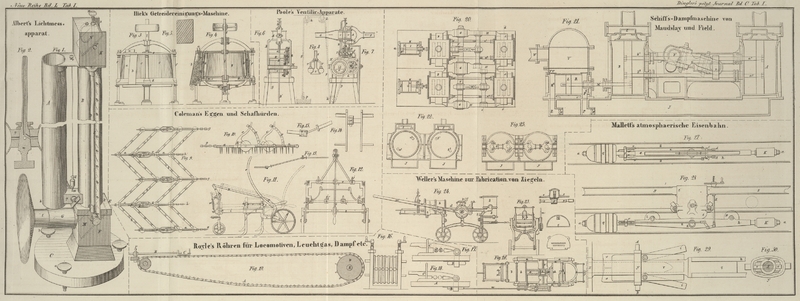