Titel: | Beschreibung des Verfahrens bei der Fabrication der Ziegel und des Mörtels auf der königl. preuß. Ziegelei bei Joachimsthal; von Hrn. Menzel. |
Fundstelle: | Band 102, Jahrgang 1846, Nr. XXXVII., S. 195 |
Download: | XML |
XXXVII.
Beschreibung des Verfahrens bei der Fabrication
der Ziegel und des Mörtels auf der königl. preuß. Ziegelei bei Joachimsthal; von Hrn.
Menzel.
Aus den Verhandl. des preuß. Gewerbevereins 1846, 2te
Lief.
Mit Abbildungen auf Tab.
III.
Verfahren bei der Fabrication der Ziegel und des Mörtels auf der
königl. preuß. Ziegelei bei Joachimsthal.
Die Ziegelei, am östlichen Ende des Werbellin-See's belegen, wurde im Jahr
1817 daselbst neu angelegt, behufs der Fabrication von Ziegeln und Mörtel zur
Herstellung der in jener Zeit gänzlich in Verfall gerathenen Wasserbauwerke im
Finowcanal. Die Nothwendigkeit dieser Anlage ergab sich einmal daraus, daß zu jener
Zeit in hiesiger Gegend nur wenige Privatziegeleien vorhanden waren, aus welchen ein
bedeutender Bedarf an Material schwerlich hätte beschafft werden können, sowie auch
der Umstand zu berücksichtigen blieb, daß bei der unvollkommenen Einrichtung und dem
schlechten Betrieb der Privat-Ziegeleien auf ein brauchbares Material zu
solchen Bauwerken nicht mit Sicherheit zu rechnen war. Die fragliche Anlage gewährte
aber auch noch den in
die Augen springenden Vortheil, daß bei der sehr günstigen Lage der Ziegelei an
einem schiffbaren Wasser, in einer Gegend, wo ein Mangel an Arbeitern so wenig, wie
an Holz zu besorgen war, aus dem in dem königlichen Grimnitzer Forst ganz nahe
gelegenen, außerordentlich vorhaltigen Thonlager von besonderer Güte, auch ein
vorzügliches Material zu den Wasserbauten und ein unbedenklich besseres und zu einem
ungleich billigeren Preise durch eigene Fabrication beschafft werden konnte, als es
selbst die vorzüglichsten, zu jener Zeit bestehenden Privat-Ziegeleien zu
liefern im Stande waren.
Auf dieser Ziegelei ist seit Gründung derselben, im Jahr 1817, das Material zu
folgenden hier aufgeführten Hauptbauten geliefert worden, nämlich:
1) zu 14 neuen massiven Schleußen im Finow-,
Werbellin-, Voß-, Malzer- und Oranienburger-Canale;
2) zu 7 ganz oder halb massiver Archen im Finowcanal und an
der Havel;
3) zur Glienicker Brücke bei Potsdam;
4) zur Werderschen Kirche in Berlin (mit Ausnahme der Steine
zu den Thürmchen);
5) zur grünen Brücke in Potsdam;
6) zur neuen Kirche in Sacrow;
7) zu den Fontainen-Anlagen in Sanssouci;
8) zum Schlosse und den Fontainen-Anlagen auf dem
Babertsberge bei Potsdam;
9) zum Kuppelbau der Nikolaikirche in Potsdam;
10) zu verschiedenen gewöhnlichen Bauten, welche hier nicht
angeführt werden.
Graben und Auswittern des Thons. Der Thon ist in dem
königlichen Grimnitzer Forst an verschiedenen Stellen, etwa 1/12 Meile von der
Ziegelei entfernt, in mächtigen Lagern von mehr den 20 Fuß Tiefe vorhanden.
Theilweise ist er sehr rein und frei von schädlichen Bestandtheilen, so daß er bei
gehöriger Durchwitterung im rohen Zustande gleich verarbeitet werden kann;
theilweise ist er unrein und besonders stark mit Mergelnieren durchzogen und muß
deßhalb durch Schlämmen erst zum Verarbeiten fähig gemacht werden.
Das Graben des Thons geschieht immer im Herbst, vom October ab, zu welcher Zeit die
Betriebsarbeiten auf der Ziegelei sich etwas vermindern und dann die nicht mehr
gehörig zu beschäftigenden Arbeiter zu diesem Geschäft, welches etwa 6–7
Wochen dauert, benutzt werden. Beide Thonarten werden beim Graben schon von einander
gesondert und in flachen Haufen von höchstens 2 Fuß Höhe in und neben den Thongruben
aufgeschüttet, woselbst der Thon bis zum Frühjahre, etwa bis zur Mitte April, liegen
bleibt und dann durch Fuhrwerk zur Ziegelei geschafft wird. Höher darf der Thon
jedoch nicht aufgeschüttet werden, weil ihn sonst der Frost und die Einwirkung der Witterung
nicht gehörig auflösen möchte.
Das Zubereiten des Thons in den ersten Jahren, wo noch keine
Maschinen angelegt waren. Es wurde derselbe in wasserdichten Sümpfen, mit
einem Zusatz von Wasser und Sand, eingesumpft und nachdem er darin gut
durchgeweicht, mit hölzernen Schippen auf den vor demselben belegenen Tretplatz
ausgeworfen und gleichmäßig vertheilt. Darauf kneteten Menschen diese aus Thon und
Sand bestehende Masse mit den Füßen gut durcheinander und schlugen sie in Haufen
zusammen.
So zubereitet wurde diese Ziegelmasse zur Fabrication von Mauersteinen verwendet. Auf
dieselbe Weise konnte auch nur die Erde zu den Klinkersteinen bereitet werden,
jedoch mit der Verbesserung, daß bei letzteren, statt 1/4 Sandes als Beimischung,
nur der fünfte Theil beigemengt und die auf dem Tretplatz zusammengeschlagene,
geknetete Thonmasse dann noch mit gekrümmten Schroteisen oder Messern geschroten
wurde. (Fig.
28.) Durch diese Operation, die dazu dient, den Thonhaufen durch Abschaben
mit solchem Schroteisen gänzlich umzuarbeiten, erhält die mit Sand gemengte Erde
eine ziemlich gleichmäßige Consistenz, und da bei dem Abschaben oder Abziehen
derselben sehr viele, nicht völlig aufgelöste Thonstücke und auch die in dem Thon
befindlichen Steine zum Vorschein kommen, welche dann mit den Händen herausgenommen
und entfernt werden können, so entsteht daraus eine ziemlich reine, von schädlichem
Mergel und Steinstücken befreite Ziegelmasse, aus welcher hier die vorzüglichsten
Klinkersteine fabricirt sind.
Das Zubereiten der Erde auf diese Weise ist allerdings etwas mühsam und kostspielig,
indem das Abschroten nur langsam vor sich geht; es ist diese Art der Zubereitung
aber jedenfalls der auch üblichen Manier, den Thon in größeren Bahnen von Pferden
durchkneten zu lassen, vorzuziehen. Denn während beim Treten des Thons durch
Menschen schon jeder fühlbare, nicht aufgelöste Kloß, auch Steinstücke,
herausgeworfen werden können, müssen diese bei der gedachten Manier in demselben
bleiben, und kann diese Erde daher nicht mit solcher Sicherheit zu guten Ziegeln
verwendet werden.
Das Zubereiten der Erde in vorbeschriebener Art kostet, einschließlich Aufkarren der
Erde auf den Streichtisch,
a)
für das Tausend
Mauersteine
20 Sgr. bis 22 1/2
b)
„ „
Klinkersteine
1 Thlr. 5 Sgr.
Das Zubereiten des Thons durch Maschinen. Nach dieser
Zeit ist die Ziegelerde mittelst der auf der Hauptziegelei vor Wasserkraft
angelegten und auf der Feldziegelei durch Göpel eingerichteten Thonschneidmaschinen
und Schlämm-Mühlen zubereitet, und es ist dadurch die Fabrication der Ziegel
bedeutend vereinfacht und auch billiger hergestellt worden.
Beide Arten dieser Thonschneidmaschinen sind im wesentlichen von gleicher
Construction; der Unterschied besteht nur darin, daß bei dem Göpel die bewegende
Kraft durch den Zug der Pferde oder Ochsen unmittelbar an dem mit der senkrechten
Messerwelle in Verbindung stehenden Tummelbaum befindlich ist, während die auf der
Hauptziegelei vor Wasserkraft angelegte Thonschneidemaschine durch verschiedenes
Räderwerk in Bewegung gesetzt wird. Das Zubereiten der Erde durch diese Maschine ist
sonach in folgender Art geschehen:
Die Ziegelmasse muß in Sümpfen, welche sich in der Mitte der eigentlichen Maschine
befinden, mit Wasser aufgeweicht werden. Wird diese Einsumpfung vorsichtig gemacht,
d.h. ist in dem Sumpfe so viel Wasser vorhanden, daß der in kleinen Stücken
eingebrachte Thon damit vollständig umgeben ist, und also an keiner Stelle trocken
zu liegen kommt, so geht die Auflösung desselben in kurzer Zeit vor sich, und sind
in der Regel nur 3–4 Stunden dazu erforderlich. Nun sind die hiesigen Sümpfe
durch eine feste Mittelwand getheilt, und es kann so, während die eine Abtheilung
geleert ist, die andere wieder gefüllt werden, wodurch immer aufgeweichter Thon
vorhanden ist und die Maschine in stetem Gang erhalten wird. Bei dem Einsumpfen wird
auch zugleich das Quantum der, des zu fetten Thons wegen, erforderlichen Beimischung
von Sand oder Ziegelmehl in möglichst gleichmäßiger Zertheilung hinzugesetzt, und
besteht dieselbe, wie schon vorerwähnt in:
a)b)
für Mauersteinefür Klinkersteine
1/41/5
dem Volumen der Erde nach.
Diese nun zum Durcharbeiten vorbereitete Thonmasse wird mit hölzernen Schippen aus
dem Sumpfe in den senkrechten Cylinderkasten geworfen, während man die darin
befindliche, ebenfalls senkrecht stehende und auf der Höhe des Cylinderkastens (4
1/2 Fuß) mit 30 starken Messern versehene Welle in Bewegung setzt. (Fig. 29.) In diesem
Cylinder wird die Thonmasse vielfach zerschnitten und gleichzeitig, vermöge der
spiralförmigen Stellung der Messer an der Welle, von oben nach unten, durch die in
der freien Seitenwand des Cylinders dicht über dem Boden desselben befindliche
Oeffnung von 8 Zoll im Quadrat gepreßt, woselbst sie aufgefangen, daneben auf
einen Haufen zusammengeschlagen und dann zum Verarbeiten brauchbar geworden ist.
Es ist hierbei abzusehen, daß die Ziegelmasse bei der Gewalt, mit welcher die
Messerwelle in dem Cylinderkasten von 4 Fuß im Quadrat und 4 1/2 Fuß Höhe arbeitet
und dadurch die steife Thonmasse durch die unverhältnißmäßig kleine Oeffnung preßt,
viel gleichmäßiger und vollständiger durcheinander gearbeitet wird, als bei der
vorhergenannten Art durch bloßes Sumpfen und Treten.
Durch Einführung solcher Thonschneidemaschinen hat die Ziegelfabrication den ersten
Aufschwung zur Verbesserung und Vereinfachung erhalten; denn neben dem eben
angeführten Vortheile des Besserbearbeitens der Ziegelerde, gewähren diese Maschinen
auch den Nutzen, Menschenkräfte zu ersparen und besonders die Arbeiter von der, der
Gesundheit so nachtheiligen Beschäftigung des Tretens des Thons bei rauher Witterung
zu entbinden.
Indessen ist nur bei vorsichtigem Einsumpfen der Ziegelerde ein guter Erfolg von der
Benutzung der Thonschneidemaschinen zu erwarten, da der nicht gehörig gesumpfte Thon
auch in der Maschine nicht zur Auflösung kommen kann. Eine so ungleichmäßig
bearbeitete Thonmasse ist dann zwar zu Mauersteinen noch anwendbar, kann jedoch zu
Klinkersteinen nicht verwendet werden, indem diese der mehr oder weniger
unaufgelösten Thonstücke wegen beim Formen leicht Höhlungen bekommen. Wenn indessen
ein solcher Fall beim Einsumpfen der Erde zu Klinker- oder anderen Steinen
von höherem Werth, wo man den Thon statt des Sandes mit der theuren Beimischung von
Ziegelmehl versetzt, vorgekommen, so läßt man diese aus dem Thonschneider nicht
gehörig gerathene Masse noch einmal durch denselben gehen, was hier auf der
königlichen Ziegelei bei obgedachten Fabricaten gewöhnlich geschieht. Durch das
nochmalige Umschippen und Durchtreiben durch den Thonschneider wird die Ziegelerde
viel schöner und brauchbarer und das Formen der Steine sehr erleichtert.
Zu Steinen, welche eine noch sorgfältigere Vorbereitung des Thons erfordern, wird
dieser, ehe er in den Thonschneider kommt, auch noch zuvor geschlämmt. Dieses
Schlämmen der Erde geschieht mittelst der hiesigen Schlämmmühle in folgender
Art:
Die rohe Erde wird in einem, vor der Schlämmmühle befindlichen Sumpfe mit Wasser so
viel als möglich aufgeweicht, damit die nachherige vollständige Auflösung in der
Schlämmmühle um so rascher von Statten gehen kann. (Fig. 30.) Der geweichte
Thon wird dann in den gewölbten, massiven Schlämmkasten geworfen, wo ihn die
wagerechte Welle mit ihren 48 hölzernen Daumen in ziemlicher Geschwindigkeit unaufhörlich aufrührt und
dadurch, während die noch fehlende Wassermenge aus der daneben liegenden Arche
mittelst Rinnen zugeführt wird, denselben zu einem flüssigen Brei auflöst. Diese
flüssige Thonmasse wird darauf über ein Drahtsieb geleitet, dessen Maschen jedoch
nicht über 1/8 Zoll im Quadrat betragen dürfen, und welches dazu dient, die in dem
Thon enthaltenen Unreinigkeiten abzusondern, wo sie dann entfernt werden. Eine unter
dem Sieb angebrachte massive Rinne leitet die flüssige Thonschlämpe in die
Schlämmgruben, in denen sie so lange bleibt, bis das überflüssige Wasser durch
Verdunsten und Abzapfen aus den Seitenwänden entfernt, und die Erde wieder eine
solche Consistenz angenommen hat, daß sie zum Verarbeiten in dem Thonschneider
brauchbar ist. Die Schlämmgruben sind massiv, mit 1 1/2 Fuß starken Wänden in
hydraulischem Kalk gemauert und mit Decksteinen abgedeckt. Die Sohle ist
ungepflastert, nur mit reinem Sande eben ausgeglichen. In den Seitenwänden sind
Löcher angebracht, durch welche das auf dem Thon sich sammelnde Wasser nach
Erfordern abgezapft werden kann. In dieselben darf die Erde nicht über 14–16
Zoll eingeschlämmt werden, weil sonst die Masse zu schwer abtrocknet und sie dadurch
in der Oberfläche zu sehr verhärtet, während der untere Theil weich bleibt.
Obgleich die Ziegelerde durch das Schlämmen auf das sauberste zubereitet wird, so ist
sie in diesem Zustand doch noch nicht verarbeitungsfähig. Theils weil dieselbe in
den Schlämmgruben zu ungleichmäßig abtrocknet, theils auch, weil man wegen der
vermehrten Fettigkeit derselben durch das Schlämmen genöthigt ist, eine Beimischung
von Ziegelmehl oder Sand hinzuzusetzen, muß sie nochmals durch die
Thonschneidemaschine getrieben werden. Die so zubereitete Erde wird nun zu
Klinker- und Formsteinen verarbeitet, da zu gewöhnlichen Mauersteinen der
durch das Schlämmen zu beschaffende Vorrath nicht zureichend seyn würde und zu
diesem Material ungeschlämmter Thon verwendet wird. Zu den Formsteinen insbesondere
wird die Erde dann noch durch mehrmaliges Schroten viel steifer bearbeitet, weil
sonst ein reinliches Formen und Scharfhalten der Gliederungen an solchen Steinen
nicht möglich wäre, größere Steinstücke sich auch beim Austrocknen sehr leicht
versacken und verziehen würden.
Der hiesige Thon von solcher Steifigkeit und mit 1/4 Beimischung versehen, schwindet
während des völligen Austrocknens auf 12 Zoll Länge = 1 1/2 Zoll, so daß ein Stein
aus einer Form von 12 Zoll nach dem Abtrocknen und nach dem Brande nur 10 1/2 Zoll
mißt.
Das Zusammenziehen oder Schwinden der hiesigen Thonerde beim Austrocknen und Brennen
ist verschieden, je nachdem die Erde steif oder weich, und mit viel oder wenig
Zusatz von Sand oder anderer Beimischung bereitet worden ist. Das Verhältniß des
Schwindens ist folgendes:
1) Erde mit 1/4 = 25 Proc. körniger Beimischung und so steif
bearbeitet, daß sie, mit den Händen regiert, nicht anklebt, schwindet auf 12
Zoll Formlänge 1 1/2 Zoll.
2) Erde von gleicher Consistenz mit 1/5 = 20 Proc. Beimischung 1
3/5 Zoll.
3) Erde von gleicher Consistenz mit 1/6 Beimischung = 1 9/10
Zoll.
4) Erde von geringer Steifigkeit, die zu Klinker- und
Mauersteinen bestimmt ist, nur mit den Händen in solchen Formen ohne zu großen
Kraftaufwand ausgedrückt werden kann, schwindet auf 12 Zoll Formlänge mit1/4Beimischung=1 3/4 Zoll.„1/5 „=1 11/12 „„1/6 „=2
1/12 „
Mehr Abstufungen in dem Zusatz der Beimischung sind nicht erforderlich gewesen.
Aus der vorstehend zu 1 bis 3 bemerkten steifen Erde werden nur Formsteine gefertigt.
Das Schwinden des Thons bei verschiedener Größe der Steine ist ganz gleichmäßig und
selbst dann noch, wenn die zu formenden Steine unverhältnißmäßige Abmessungen
erhalten.
Dieses gleichmäßige Schwinden wird jedoch durch das gleichmäßige Austrocknen der
Steine bedingt; denn wenn dieses nicht genau beobachtet und die Wärme oder der
Luftzug nicht gehörig regulirt wird, die zu trocknenden Steine also an einer Seite
oder Fläche mehr Abzug an Feuchtigkeit erleiden als an den übrigen, so wird dadurch
nicht nur das gleichmäßige Zusammenziehen des Steins gehemmt, sondern die Steine
müssen auch nothwendig krumm werden. Welche Mittel zur Erreichung dieses Zwecks hier
angewendet werden, wird bei der Erläuterung über das Formen der Steine
angeführt.
Um nun nicht bei jeder Ausmittelung der Größe der Formen nach dem verschiedenen
Schwinden des Thons, bei mehr oder weniger Beimischung, Berechnungen darüber
anstellen zu dürfen, bei denen leicht Versehen statt finden können, sind hier zu den
verschiedenen Thonsorten die verschiedenen Schwindemaaßstäbe angefertigt und bis zu
1/8 Zoll eingetheilt. Nach diesen werden die Formen in allen ihren Abmessungen
aufgezeichnet und angefertigt.
Das Formen der Ziegel. Das Formen oder Streichen der
Mauersteine geschieht auf hölzernen, 5 Fuß im Quadrat großen, beweglichen
Streichtischen, auf welchen die zu verarbeitende Ziegelmasse aufgeschlagen wird. An einer
Seite des Tisches arbeiten zwei sich gegenüberstehende Ziegelstreicher, zwischen
welchen an eben dieser Seite ein 2 Fuß langer Trog mit Wasser angebracht ist, um
daraus die Form beim Streichen zu benetzen. Auf jede der beiden zunächst liegenden
Tischecken ist ein Brett von etwas größerem Umfang, als die Form, aufgenagelt,
welches den Thon verhindert, an der unteren Seite hervorzuquellen, und das man
leicht erneuern kann, wogegen man beim Streichen auf der bloßen Tischecke, die sich
durch das fortwährende Abziehen und Aufsetzen der Form sehr bald abnutzen würde,
gezwungen wäre, jedesmal die ganze Tischplatte abzuhobeln. Auf diese Brettchen legt
der Arbeiter die Form, besprengt dieselbe aus dem vor ihm befindlichen Trog mit
Wasser und wirft einen, der Größe der Form angemessenen Thonballen, den er mit den
Händen gebildet, mit ziemlicher Gewalt in dieselbe hinein. Den Thonballen drückt er
dann noch stark nach, so daß bei dieser Ausdehnung desselben die Form vollständig
ausgefüllt wird und schlichtet den auf der Form etwa noch überflüssigen Thon mit
einem Streichholze eben ab, worauf der fertige Stein dem Abtragejungen zum Befördern
auf die Trockengerüste übergeben wird. Das Formen der Mauersteine in dieser Art
kostet hier das Tausend 15 Sgr., und zwar: an den Streicher 10 Sgr. und an den
Abtrager 5 Sgr.
Das Formen der Klinkersteine geschieht ganz in vorbeschriebener Art, nur muß der
Arbeiter, nachdem er auf der einen Seite abgeschlichtet, die Form vom Streichbrett
abziehen, auf die andere Seite legen, auf diese noch etwas Ziegelerde nachdrücken
und gleichfalls eben abschlichten, was das Formen um 5–6 Sgr. vertheuert. Das
Formen der Klinkersteine kostet demnach hier das Tausend 21 Sgr., und zwar: an den
Streicher 16 Sgr. und an den Abtrager 5 Sgr.
Die Erde zu den Dachsteinen muß wie zu den Klinkersteinen geschlämmt, mit 1/4 Zusatz
von reinem Sand versetzt und zweimal durch den Thonschneider gegangen seyn.
Dieselben werden in einer eisernen Form, welche 5/8 Zoll hoch und so lang und breit
ist, daß der Stein nach dem Brand 15 Zoll lang, 6 Zoll breit und 1/2 Zoll stark
bleibt, geformt. Die eiserne Form ist in einer hölzernen, mit Scharnierbändern
versehenen Klappform lose eingefuttert, so daß sie aus dieser nach dem Umklappen
leicht herausgenommen werden kann. Diese Klappform ist mit der einen Klappe auf der
Tischecke befestigt, während die andere beweglich bleibt. Der Arbeiter drückt die
Thonmasse in die in letzterer befindliche eiserne Form, schlichtet dieselbe ab und
bildet mit den Fingern die zum Dachstein gehörige Nase. Während dessen hat der
Abtrager ein
Trockenbrett mit einer Schlitzöffnung neben den Streichtisch gelegt, auf welches die
Klappe mit der eisernen Form umgekehrt wird, so daß die Nase des Steins in die
Schlitzöffnung zu liegen kommt. Der Arbeiter klappt nun die hölzerne Klappe zurück
und behält auf dem Trockenbrett die eiserne Form, die er nochmals abschlichtet, dann
abhebt und den fertigen Stein dem Abtrager übergibt, der ihn in die Trockengerüste
befördert.
Dieses Verfahren erscheint vielleicht mühsam, ist es aber nicht, indem ein geübter
Ziegler bei gut zubereiteter Erde im Stande ist täglich bis 1500 Stück zu
verfertigen.
Das Formen der Dachsteine in dieser Art kostet für das Tausend 21 Sgr. und zwar an
den Streicher 15 Sgr. und an den Abtrager 6 Sgr. Da die Ziegelei hauptsächlich mit
Fabrication von Klinkersteinen und anderen größeren Baustücken und Gesimssteinen
beschäftigt worden ist, so sind seither nur so viel Dachsteine gefertigt, als die
obern Räume der Oefen, woselbst andere Steine zu Wasserbauwerken nicht mehr
vollkommen gut durchbrennen, aufnehmen konnten; die Dachsteine aber, ihrer geringen
Stärke wegen, daselbst noch vollkommenen Brand erhalten haben.
Das Formen der Gesimssteine. Da das Formen solcher Steine
so sehr verschieden ausgeführt ist, je nachdem die zu formenden Steine künstlich
construirt waren, so würde es zu weitläufig seyn, wollte man von allen bisher hier
gefertigten Kunstsachen die einzelnen Verfahrungsarten bei dem Formen derselben
angeben. Es dürfte hinreichend seyn, das Verfahren, wie es in den letzten Jahren bei
Anfertigung dieser Steine statt gefunden, zu beschreiben.
Eben so kann hinsichtlich der Construction der Formen zu solchen Kunststeinen hier
nur eine allgemeine Uebersicht gegeben werden, da diese nach Beschaffenheit der zu
formenden Steine ganz verschieden seyn müssen. Bei den vielen scharfen
Unterscheidungen und den dabei auch häufig vorkommenden Durchsichten besteht die
Form oft aus so vielen einzelnen Theilen, daß deren Zusammensetzung und
Auseinandernehmen höchst mühsam und bisweilen nicht ganz leicht zu finden ist, wie
überhaupt eine weit größere Schwierigkeit in der Anordnung der Form liegt, als in
dem Formen der Steine selbst.
Das Formen der gewöhnlichen Gesimssteine, d.h. solcher,
die sich durch einen Stempel aus der Form herausdrücken lassen, ohne daß dieselbe
auseinander genommen zu werden braucht. (Fig. 31.) Die Erde zu
denselben, wie überhaupt zu allen Formsteinen, muß besonders gut gereinigt, mit 1/4
Sand oder Charmotte versetzt und durch öfteres Schroten so steif bearbeitet seyn, daß sie weder
an den Händen noch an der Form sehr anklebt. Die Form dazu, aus Eichenholz, wird
inwendig mit Oel gestrichen, wozu hier gewöhnliches Rüböl benutzt wird, dann auf
einen Klotz von Eichenholz, der oben glatt gehobelt und mit grober Leinwand
überdeckt ist, gelegt und hier gut vollgepackt, so daß der Thon einige Zoll über die
Form hervorragt; dann wird die gefüllte Form mit Leinwand bedeckt und darauf ein
dreizölliges festes Bohlstück gelegt, auf welches der Arbeiter mit einer kleinen
Handramme einige kräftige Stöße führt. Dadurch wird der Thon in die Form sehr fest
eingetrieben und der Stein in allen seinen Theilen vollkommen dicht. Nachdem das
Rammbohlstück und die Leinwand entfernt und der überflüssige Thon mit einem
Streichholz abgestrichen ist, kehrt der Arbeiter die Form mit ihrer Füllung auf die
andere Seite, um den etwa vorgequollenen Thon gleichfalls abzustreichen und der
Stein ist bis zum Auslegen auf das mit Sand bestreute Trockenbrett fertig. (Fig. 32.) Auf
diesem Trockenbrett werden zwei vierkantige Klötzchen, die so lang seyn müssen, als
dasselbe breit ist und von der Höhe der Form, unter dieselbe so gelegt, daß der
Stein dazwischen gehörig Platz findet, welcher dann durch einen genau in die Form
passenden hölzernen Stempel auf dasselbe herausgeschoben wird. Finden sich hiebei
einige Mängel an einzelnen Stellen des Steins, so werden diese mit einem feinen
Messer sogleich nachgebessert, wie überhaupt der ganze Stein mit einem nassen
Schwamm sauber überschlichtet werden muß.
Bei solchen gewöhnlichen Gesimssteinen findet das Formen keine Schwierigkeit, auch
ist die Form leicht anzufertigen.
Das Formen der künstlichen Gesimssteine, bei denen man
nach jedesmaligem Einpressen des Thons in die Form dieselbe ganz auseinander nehmen
muß, bevor man den fertigen Stein fortlegen kann, ist schwieriger. Fig. 33 stellt einen
Stein in der Form und diese wieder in ihren einzelnen Theilen dar.
Bei der hier angenommenen Länge des Steins von 12 Zoll kann derselbe nicht mehr durch
einen Stempel aus der Form geschoben werden. Die Gliederungen würben sich bei dieser
Länge leicht verziehen; auch würde der Stein, da er bei dieser Art des Formens auf
der Grundfläche A gelagert werden müßte, bei seiner
bedeutenden Länge leicht zusammensacken und dadurch würben die Gliederungen an der
unteren Seite des Steins viel größer, als die an der obern werden.
Bei dem Lagern des Steins auf das Trockenbrett ist auch darauf zu sehen, daß nicht zu
schwere Thonmassen auf die Gliederungen drücken; man würde also den hier
gezeichneten Stein am zweckmäßigsten auf die Fläche B
legen.
Die Form besteht aus der Kastenform a, b, c, d, die den
Stein in seiner ganzen Größe umschließt, und den Formfuttern e, f, g, h, i, die mit ihren Gliederungen in dieselbe eingelegt und durch
die Einkämmungen x so in einander befestigt sind, daß
sie beim Einpressen des Thons in die Form sich nicht verschieben können. Der
Arbeiter legt in die Form einen der Größe des Steins angemessenen Thonballen, aus
welchem er mit der geballten Hand die einzelnen Gliederungen sorgfältig ausdrückt,
und füllt den übrigen Raum dann durch recht kräftiges Hineinwerfen von Thonballen
bis 2 Zoll über den Rand, worauf die Füllung mit der schon beschriebenen Handramme
noch nachgetrieben und dadurch der Stein in allen seinen Theilen dicht und fest
ausgeformt wird. Der überflüssige Thon wird mit einem Streichholz abgeschlichtet,
die Form auf dem Klotz umgekehrt, die untere Seite ebenfalls noch mit Thon
nachgefüllt und abgeschlichtet, und der Stein mit der Fläche B auf ein tüchtig mit Sand bestreutes Trockenbrett gelegt. Die sogenannte
Mutterform a, b, c, d wird durch Lösung der daran
befindlichen Schloßkeile auseinander genommen; die Formfutter e, f, g, h, i bleiben an dem Steine sitzen, werden behutsam mit den Händen
abgelöst, und der Stein ist bis auf das Nachputzen mit Messer und Schwamm
fertig.
Bei noch größerer Länge der gegliederten Formfutter kömmt es auch vor, daß der Thon
bei dem starken Einrammen in die Form an diese sehr anklebt. Solchem Uebelstande
hilft man indessen ab, wenn man die mit Oel gestrichene Form mit feinem
Holzkohlenstaub bestreut, was das Anziehen des Thons verhindert. Vor dem
jedesmaligen Zusammensehen der Form muß dieselbe, wie auch die Futterstücke, sauber
gereinigt werden.
Das Formen der Eck- und Winkelsteine wird noch
schwieriger und besonders, wenn dieselben, wie aus Fig. 34 zu ersehen, an
der oberen Seite mit einer schrägen Abwässerung versehen sind.
Die Form dazu besteht aus einer viereckigen Kastenform, welche durchweg so hoch seyn
muß, als der Stein bei g stark; sie ist, wie die
vorhergenannten, mit Zapfen und Schloßkeilen versehen und kann gänzlich auseinander
genommen werden. (Fig. 35.) An den Seiten a und b sind die gegliederten Formstücke durch Verdübelung
angebracht und nach der Schmiege bei c stumpf
zusammengestoßen. Sind keine Unterscheidungen in den Gliederungen angegeben, so
können auch die gegliederten Formfutter an den Seitenwänden der Form festgenagelt
seyn, weil dieselben dann durch ihre Trennung bei c
einzeln von dem geformten Stein abgelöst und weggenommen werden können. Ist außerdem an solchem
Eckstein eine Abwässerung an der oberen Seite desselben zu formen, so erhält die
Form auch noch ein Bodenbrett (d), worauf die
keilförmigen Futterstücke e, e im Profil und Grundriß
festgenagelt sind, welche die Abwässerung des Steins bilden. Die viereckige
Kastenform i, i in der Durchschnittszeichnung wird nun
auf das Bodenbrett zwischen die keilförmigen Futterstücke e und die im Profil mit h bezeichneten, 3/4
Zoll im Quadrat starken Leisten gelegt, welche das Verschieben derselben während des
Füllens mit der Thonmasse verhindern sollen. Das Einschlagen des Thons in die Form
kann hienach nur von der Seite f geschehen und der Stein
müßte auf Seite g gelagert werden, wobei die
Gliederungen durch die Last der Thonmasse nicht leicht verdrückt werden können. Das
Einpressen des Thons in die Form geschieht, wie schon erwähnt, mittelst der
Handramme, da Versuche, den Thon durch Schraubendruck in die Form zu pressen, zu
langsam und nicht vortheilhaft befunden sind. Wie die Form um den Stein fortgenommen
werden kann, ist aus der Zeichnung zu ersehen. Das Bodenbrett wird zuerst abgehoben,
das Seitenstück bei g durch einen Schlitz zurückgenommen
und der Stein kann dann auf ein passendes Trockenbrett auf die Seite g gelagert werden.
Das Formen der Gesimswinkelsteine nach Fig. 36 wird ebenso
ausgeführt, als das der vorigen Ecksteine.
Der mit 1/4 Beimischung versehene Thon muß, wie schon gesagt, rein und gleichmäßig
steif bearbeitet seyn. Mit diesem wird die geölte Form gut gefüllt, die Winkel und
Gliederungen werden soviel als möglich fest ausgedrückt, und dann wird die Thonmasse
mit der Handramme noch nachgetrieben, so daß die Gliederungen und Ecken an dem Stein
vollkommen gut ausgeformt sind, der Stein auch im Innern die gehörige Dichtigkeit
erhalten hat.
Die Form muß außer den Gliederungen auch noch mit einem Bodenbrett a, a versehen seyn. Die keilförmigen Futterstücke b, b, durch welche die Abwässerung gebildet wird, sind
auf demselben festgenagelt. Die Gesimsstücke sind an der Kastenform, an den beiden
Seiten c und d und an den
getheilten Klotz e befestigt. Die Form ist mit Zapfen
und Schloßkeilen zum Auseinandernehmen eingerichtet. Der geformte Stein wird auf der
Seite f gelagert.
Das Belegen der Trockenbretter mit Sand behufs des
Trocknens der Steine ist deßhalb erforderlich, damit der geformte Stein beim
Austrocknen sich leicht zusammenziehen und an das Trockenbrett nicht ankleben kann.
Bei gewöhnlichen kleinen Steinen ist dazu eine Hand voll Sand hinreichend, bei größeren und schwereren
muß aber das Trockenbrett mit einer völligen Lage Sand versehen seyn, welche nach
Erfordern 2 Zoll stark seyn kann. In solchem Fall sind die Trockenbretter mit 2 Zoll
hohen Leisten versehen, zwischen welchen der Sand fest eingedrückt und gleichmäßig
abgeschlichtet wird. Diese Sandfläche ist einmal erforderlich wegen des Schwindens
der Steine, dann auch, um dem Stein eine Menge Feuchtigkeit an der unteren Seite
abzuziehen und dadurch ein gleichmäßiges Abtrocknen zu bewirken.
Das Formen der farbigen Formsteine durch gefärbten Thon und
Plattirung.
Schon seit mehreren Jahren sind solche hier auf der königlichen Ziegelei zu
verschiedenen königlichen Bauten in Sanssouci, Sacrow und auf den Babertsbergen
gefertigt. Die zu den Decorationen der äußeren Flächen solcher Gesimssteine hier
angewendeten Farben sind folgende:
a) Dunkelbraunb) Schwarz
aus Eisenocker und hiesiger rother Thonerde.
c) Grün aus feuerbeständigem
Chromgrün-Präparat und weißer hallischer Thonerde,
d) Roth in verschiedenen
Abstufungen aus caput mortuum und der vorigen
Thonerde,
c) Gelb aus Uranoxyd und der
vorigen Erde,
f) Weiß aus weißer
Thonerde.
Das Mischungsverhältniß der hier bemerkten Farben zu der dazu erforderlichen Thonerde
ist, dem Volumen nach, folgendes:
ZuaDunkelbraun 3/4 rothe Thonerde und 1/4 fein gepulverter
Eisenocker, sogenanntes Wiesenerz,
zubSchwarz 3/5 rothe Thonerde und 2/5 Eisenocker,
zucGrün 1/2 weiße Thonerde und 1/2
Chromgrün-Präparat,
zudRoth 3/5 weiße Thonerde und 2/5 sogenannter
Todtenkopf,
zueGelb 3/5 weiße Thonerde und 2/3 Uranoxyd.
Diese Mischungen müssen auf einer Glasurmühle, die weiter unten beschrieben werden
wird, so fein zerrieben werden, daß weder mit den Händen, noch mit den Zähnen das
geringste Körnige daran fühlbar ist. Ist dieses bewirkt, so wird die ganze flüssige
Thon- und Farbenmasse aus der Glasurmühle abgezapft und in eigens dazu
vorhandenen hölzernen Zobern so lange aufbewahrt, bis das Wasser davon gänzlich
verdunstet und abgezapft, und die Masse zu einer steifen Thonmasse geworden ist.
Dieselbe wird dann mit den Händen noch einmal gut durchgeknetet und ist zur
Anwendung fertig.
Durch diese so vollständige Zerkleinerung und Auflösung der Farbenmasse wird die
möglichste Ausdehnung derselben im Brande erreicht und findet eine gleichmäßige
Färbung der Thonmasse unbedingt statt.
Die hiesige Glasurmühle besteht aus zwei genau aufeinander passenden runden
Granitsteinen, von 2 Fuß im Durchmesser und 9 Zoll Stärke. (Fig. 37.) Sie liegen in
einem völlig wasserdichten, aus Stäben zusammengesetzten, mit eisernen Bändern
gebundenen Gefäß von demselben Durchmesser, dessen Rand jedoch 8 Zoll über die
Steine herübersteht, um das Herausspritzen zu verhindern. Der Bodenstein ist auf dem
Boden dieses Gefäßes fest eingeklemmt. In der Mitte desselben ist ein 5/4 Zoll
starker und ebenso lang hervorstehender Zapfen aus Gußstahl eingelassen und mit Blei
ganz fest vergossen. Der obere Stein hat in der Mitte ein Loch von 2 1/2 Zoll im
Quadrat, durch welches eine eben so starke eiserne Spindel geht, an deren unterem
Ende sich die zu dem vorigen Zapfen passende, verstählte Spur oder Pfanne befindet.
Die Bewegung des oberen Steins geschieht mittelst eisernen Räderwerks in bekannter
Art durch Wasserkraft in der Geschwindigkeit von 20 Umgängen in der Minute. Eine
größere Geschwindigkeit ist nicht zweckmäßig, weil die sehr flüssige Masse leicht
herausspritzt.
Mit den gefärbten Thonmassen werden die sichtbaren Flächen der Gesimssteine plattirt,
und zwar in folgender Art:
Zu einem Eierstabe, Fig. 38 und 39, muß die Form wiederum
mit einem Bodenbrett c versehen seyn. Dasselbe enthält
die Gliederungen des Steins bei a; die Gliederung b ist an der Seite der Kastenform befestigt. Die Umrisse
der Eier, so wie der kleinen Dreiecke, sind durch schwaches Messingblech begränzt,
welches in das Bodenbrett eingelassen ist und über die Formfläche nur 1/8 Zoll
herüberragt. Diese durch das Messingblech gebildeten Felder werden mit gefärbtem
Thon, der mit einem Draht zuvor zu 1/8 Zoll starken Plättchen geschnitten ist,
ausgelegt, jedoch mit der Vorsicht daß, wenn eine Abtheilung mit einer Thonfarbe
gefüllt ist, die andere daneben vor der Füllung erst wieder gereinigt werden muß,
damit die verschiedenen Thonfarben nicht durch Unreinlichkeit verdorben werden. Sind
alle Felder gefüllt, so wird auf dieselben anderer, gewöhnlicher Thon mit den Händen
gut eingerieben, um damit eine vollständige Verbindung der gefärbten Thonmasse mit
der gewöhnlichen zu erreichen. Dann wird auf dem mit Thon belegten Bodenbrett die
Kastenform zusammengesetzt, mit gewöhnlichem Thon gefüllt und dieser fest
eingerammt. Der nun fertige Stein wird durch Lösung der Schloßkeile von der
Kastenform befreit und mit der Seite d auf das vorher
mit Sand bestreute Trockenbrett gelagert. Hier werden die durch das Messingblech
entstandenen schwachen Näthe in den farbigen Gliederungen mit einem biegsamen Messer
überstrichen, so daß von ihnen nichts mehr sichtbar bleibt.
Zu bemerken ist noch daß, wenn ein Stein mit mehreren farbigen Thonfarben verziert
werden soll, diese unter sich so erprobt und abgestimmt seyn müssen, daß ein
gleichmäßiges Schwinden derselben beim Trocknen statt findet, weil im
entgegengesetzten Fall sich eine Thonsorte von der andern lösen und so die ganze
Plattirung nicht haltbar seyn würde.
Dieses zu bewirken werden von den verschiedenen gefärbten Thonmassen kleine gleich
große Würfelchen geformt und getrocknet, und ein ungleichmäßiges Zusammenschwinden
derselben dadurch regulirt, daß man zu der fetteren Masse, die mehr schwindet als
die andere, ein Vermagerungsmaterial von fein zerriebenem Feldspath hinzusetzt und
mit der zu fetten Masse tüchtig durcharbeitet. Dieser Zusatz übt auf die Färbung
keinen nachtheiligen Einfluß und gewährt der ganzen Masse dadurch Vortheil, daß er
beim Brennen leichter in Fluß übergeht. In eben der Art wird auch der gewöhnliche
Thon mit dem gefärbten abgestimmt, nur mit dem Unterschied daß, statt des
Feldspaths, jenem ein Zusatz von Sand oder Charmotte beigegeben wird.
Eine Hauptsache bei Fabrication solcher Steine, die übrigens eine große Vorsicht und
Genauigkeit erfordert, ist, daß die gefärbte Plattirung so schwach, als nur irgend
möglich, aufgetragen wird, weil, je schwächer der Ueberzug, er sich desto weniger
von der eigentlichen Thonmasse ablösen kann.
Es versteht sich, daß hier auch Gesimssteine von ganz anderer Form gefertigt sind,
bei welchen jedoch dasselbe Verfahren statt gefunden hat.
Zur Glienicker Brücke bei Potsdam sind die sämmtlichen Gesims- und
Verblendungssteine durchweg aus einer mit Eisenocker gemischten Thonmasse gefertigt,
wodurch das Bauwerk die bedingte braune Farbe erhalten hat. Die Ziegelerde zu diesen
Steinen wurde geschlämmt und mit 1/6 Ziegelmehl und 1/6 in den hiesigen Stampfwerken
fein bereitetem Eisenocker gemischt. Dieselbe bestand sonach aus 2/3 geschlämmter
Thonerde und 1/3 der beiden genannten Substanzen. Das Bauwerk ist 1833 vollendet und
seit dieser Zeit noch kein Stein daran durch die Einwirkung der Witterung versehrt
worden.
Gewinnung des Eisenockers. Der Eisenocker ist bisher in
dem königlichen Groß-Schönebecker Forst in dem Aufhüttungsterrain unweit der
über den Finowcanal führenden Ruhlsdorfer Brücke gegraben und zu Wasser zur Ziegelei
transportirt worden. Derselbe findet sich an dieser Stelle nur in kleinen Stücken
von 2–3 Zoll und ist nur in geringer Menge vorhanden.
Zu den Trottoirs der Glienicker und Grünen Brücke in Potsdam sind die schwarzen
Steine mit 1/4 Eisenocker, die dazwischen befindlichen hellfarbigen dagegen von
hiesiger Thonerde mit 1/4 geschlämmtem Mergel versetzt. Der Mergel ist im Wasser
völlig löslich und wird mit dem Thon in dem angegebenen Verhältniß
zusammengeschlämmt, wodurch beide Massen eine vollständige Verbindung mit einander
eingehen. Nach dem Abtrocknen jedoch wird diese Masse, um sie in gleicher Konsistenz
zu erhalten, nochmals durch den Thonschneider gelassen. Der Mergel ist übrigens der
Ziegelmasse bei solcher Auflösung durchaus nicht schädlich. Er ist bei dieser
Verfeinerung für das Feuer leicht empfänglich und schmilzt, vermöge des ihm von der
Natur beigegebenen feinkörnigen Sandes, früher als die reine Thonerde, wodurch die
Steine eine außerordentliche Dichtigkeit erhalten und jeder Einwirkung der Witterung
Widerstand leisten. Aus diesem Grunde ist hier auch immer eine solche Mischung zur
Fabrication von Klinkersteinen zu Wasserbauten und besonders zu solchen Stellen
derselben, wo sie einen großen Widerstand zu ertragen haben, angewendet worden.
Das Formen der römischen Dachpfannen. Dieselben sind, wie
sie hier seit Jahren gefertigt und zu verschiedenen königlichen Bauten angewendet
werden, bei einer Stärke von 1/2 Zoll 14 Zoll lang und 12 Zoll breit und zu zweien
immer mit einem passenden Hohlstein überdeckt (Fig. 40). Beim Eindecken
der Steine werden die Fugen (im Grundriß) mit Mörtel verstrichen und dann die
Hohlsteine b, b, Fig. 41, darüber
ebenfalls mit Mörtel verlegt. Ist auf diese Art die erste Schicht gelegt, und sind
die Pfannen mit schwachen eisernen Nägeln ohne Kopf auf der Verschalung oder
Belattung festgenagelt, wozu dieselben bei c, c mit
kleinen Löchern versehen, so wird diese durch die zweite Schicht bis zur Linie d überdeckt. Da die Ueberdeckung hier zu 2 Zoll
angenommen ist, so bedeckt die Pfanne einschließlich Hohlstein nach der hier
angeführten Größe derselben 1 Quadratfuß Fläche.
Geformt werden dieselben folgendermaßen:
Die Ziegelmasse von geschlämmter Erde wird mit 1/4 Zusatz von Ziegelmehl sauber
zubereitet und in einer besonderen Form zu solchen Thonstücken geformt, die den
Umfang der Pfannenform A, Fig. 42, haben, also nach
dem Schwindemaßstabe 14 Zoll lang und 12 Zoll breit seyn müssen. An die beiden
langen Seiten dieses Thonstücks werden hölzerne Stäbe von 1/2 Zoll Stärke
aufeinandergeschichtet (wie
Fig. 43),
diese an den Thon fest angedrückt und, nach dem Abheben je zwei und zwei derselben,
das ganze Thonstück durch einen, in einem Bügel gespannten Draht, zu 8 ganz
gleichmäßigen 1/2zölligen Platten zertheilt. Diese Platten werden auf Bretter gelegt
und mit einer kurzen eisernen Ziehklinge auf der obern Seite fein abgezogen und
geglättet; dann an der Luft ein wenig abgetrocknet und zum Formen der Pfannen
benutzt. Die Thonplatten werden mit der geglätteten Seite auf die zuvor geölte Form
gelegt, mit nasser Leinwand ganz überdeckt und durch kräftiges Hin- und
Herreiben mit den Händen auf der Leinwand in die Form vollkommen ausgedrückt. Darauf
wird der an den Seiten hervorgequollene Thon mit einem Draht abgeschnitten, die
fertige Pfanne auf das mit Sand bestreute Trockenbrett gelegt und hier noch mit
einem nassen Schwamm sauber abgewaschen. Auf dem Trockenbrett kommt der Stein auf
Fläche d, Fig. 44, zu liegen, und
werden die beiden gekrümmten Seiten bei e durch eigens
dazu geschnittene eben so lange Thonplättchen unterstützt, weil andernfalls jene
sich leicht verziehen würden. Die dazu gehörigen Hohlsteine werden ebenfalls aus
Thonplatten, welche in vorbemerkter Art bereitet worden, gefertigt. Die Platten
werden auf einer halbrunden verjüngten Form gebogen ausgeformt (Fig. 45), an den Seiten
beschnitten und beim Auslegen auf die Trockenbretter durch Thonstöpsel in der Mitte
unterstützt.
Anstrich der Pfannensteine mit einer braunen Farbe vor dem
Brande. Um diesen römischen Dachpfannen ein schöneres Ansehen zu geben,
sind dieselben hier lufttrocken mit einer aus Thon und Eisenocker bereiteten braunen
Thonfarbe an der oberen Fläche bestrichen. Diese Farbenmasse besteht aus 2/3
hiesiger geschlämmter Thonerde und 1/3 Eisenocker, der zuvor etwas gestoßen werden
muß, damit ihn der Stein in der Glasurmühle leicht fassen kann. Die Farbenmasse wird
auf der Glasurmühle mit Wasser zu einer sehr feinen Tünche, jedoch in nicht zu
flüssigem Zustand, zerrieben und in solcher Beschaffenheit mit gewöhnlichen 2 Zoll
starken Borstenpinseln auf den Stein aufgetragen. Diese Tünche muß die Steinfläche
überall gleichmäßig und bis zu 1/16 Zoll bedecken, und damit sie sich mit der
Thonmasse vollständig verbinde, mit dem Pinsel auf den Steinen gut eingerieben
werden. Außer einem bessern Ansehen nach dem Brande gewinnen die Steine durch diesen
Anstrich auch sehr an Festigkeit, weil die fein zerriebene Thon- und
Eisenmasse beim Brennen sehr leicht schmilzt und dadurch an der Oberfläche der
Steine einen glasurartigen Ueberzug erzeugt, vermöge dessen dieselben den
Einwirkungen der Witterung mehr Widerstand leisten.
Das Formen der Fliesen. Dieselben sind hier in 4, 6 und
8eckiger Form aus geschlämmter Erde mit 1/4 Sand oder Ziegelmehl angefertigt worden.
Die Fliesen werden wie die Klinkersteine gestrichen und, wenn sie so weit getrocknet
sind daß sie sich mit den Händen nicht mehr verdrücken lassen, auf einem geraden und
fein gehobelten Bohlstück durch Aufstauchen auf die obere Seite gerade gerichtet und
vollständig glatt gemacht. Da sie sich bei diesem Aufstauchen etwas auseinander
dehnen und dadurch ein ungleichförmiges Ansehen erhalten, so werden sie noch nach
einer aus Eisenblech gefertigten Schablone, welche die richtige Form derselben
angibt, mit dem Putzmesser an den Seiten beschnitten und können dann weiter
trocknen.
Das Beputzen der geformten Steine vor dem Brande.
Klinker- und Verblendungssteine, überhaupt solche Steine, die zu einem
sauberen, hübsch aussehenden Mauerwerk verwendet werden sollen, sind hier, nachdem
sie soweit trocken waren, daß sie mit den Händen nicht mehr verdrückt werden
konnten, an den Seiten und Lagerflächen beputzt und gerade gerichtet worden. Das
Beputzen geschieht gewöhnlich aus freier Hand mittelst Putzmesser von 10–12
Zoll Länge, an den Seiten verstählt oder auch ganz von Stahl, damit sie sich beim
anhaltenden Gebrauch nicht sobald abnutzen. Mit diesen Messern werden die beim
Formen entstandenen sogenannten Brahmkanten der Steine abgeschnitten und dadurch
diesen, außer sehr scharfen Umrissen, auch eine ziemlich winkelrechte Form
gegeben.
Das Beputzen geschieht entweder in den Gängen der Trockenscheunen zwischen den
Trockengerüsten, wo es der Arbeiter auf einer kleinen Bank an Ort und Stelle
verrichtet, oder die Steine werden den Putzarbeitern durch Knaben an andere Stellen
in den Trockenscheunen zugetragen und dort nach dem Beputzen in Haufen gestellt.
Wendet der Arbeiter bei dem Beputzen aus freier Hand seinen Fleiß an und hat er ein
gutes Augenmaaß, so erhalten die Steine allerdings viel schärfere Kanten und eine
ziemlich winkelrechte Form; die Flächen derselben bleiben aber so, wie sie beim
Formen ausgefallen sind. Mit dem Messer aus freier Hand könnten nämlich die Flächen
zu leicht verschnitten oder schief beputzt werden. Sollen daher die sichtbaren
Flächen der Steine am Mauerwerk durchweg ein sauberes Ansehen erhalten, so wird das
Beputzen derselben in folgender Art verrichtet:
Es werden nämlich solche Steine mit einem hölzernen Keil in eine offene winkelrechte
Form fest eingeklemmt, die etwas länger als der Stein, und oben wie an der
Winkelseite mit Eisen glatt beschlagen seyn muß. An der mit Eisen beschlagenen Oberkante, wie auch an
der Winkelseite, ragt der Stein etwa 1/12 Zoll hervor. Diese beiden hervorstehenden
Steinflächen werden nun mit einem etwas größeren scharfen Messer bis auf den
Eisenbeschlag abgeschnitten und dadurch der Stein ganz winkelrecht und äußerst glatt
erhalten; letzteres deßhalb, weil der Stein noch nicht ganz trocken ist, und der
noch feuchte Thon beim Durchschneiden eine sehr ebene Fläche zurückläßt. Mit den
beiden andern Flächen wird ebenso verfahren und der Stein kann nun nach Belieben zum
Strecker oder Läufer im Mauerwerk verwendet werden. Der dabei verlorengehende 1/12
Zoll an Länge und Breite muß beim Formen berücksichtigt und die Form um so viel
größer gemacht werden.
Das Trocknen der Steine. Die gewöhnlichen Steine, als:
Klinker-, Mauersteine und andere von derselbe Größe erfordern beim Trocknen
nicht viel Mühe, indem die hiesige Thonerde, trotz ihrer außerordentlichen
Fettigkeit, viel Luftzug verträgt, ohne Borsten oder Risse zu bekommen. Bei Heller
warmer Witterung sind solche Steine in 14 Tagen völlig trocken und können abgerüstet
und in den Ofen eingekarrt werden. Dieselben liegen etwa 8 Tage auf der flachen
Seite, und werden dann auf die hohe Kante gestellt, damit die untere Seite ebenfalls
austrocknen kann. Bei anhaltend feuchter Witterung, wo das Trocknen der Steine nur
langsam von statten geht, und deßhalb mehr Steine geformt werden, als abtrocknen
können, müssen dieselben oft in noch feuchtem Zustand abgerüstet werden, damit die
Fabrication, wegen Mangels an Trockenraum, nicht ins Stocken geräth. Dieselben
werden dann in den Mittelgängen der Trockenscheunen in Zwischenräumen von 1 Zoll
aufgestapelt, wo ihnen der zum Nachtrocknen erforderliche Luftzug durch die
Oeffnungen der Mittelthüren zugeführt wird. Auf diese Weise können die
Trockengerüste öfter benutzt und der Betrieb der Ziegelei ununterbrochen fortgeführt
werden.
Anders jedoch muß mit dem Trocknen größerer und namentlich der Formsteine verfahren
werden. Diese müssen auf ihren Trockenbrettern so lange liegen bleiben, bis sie
völlig trocken und beim Abrüsten nicht mehr mit den Händen verdrückt werden können.
In unheizbaren Räumen bei ungünstiger Witterung brauchen sie oft mehrere Monate Zeit
zum Austrocknen; daher ist es immer sehr schwer, die bei solcher Fabrication zur
Ablieferung der Steine festgesetzten Termine rechtzeitig zu halten.
Das Trocknen dieser Steine darf durchaus nicht übereilt werden, damit der Thon ganz
gleichmäßig zusammenschwinde. In unheizbaren Trockenscheunen, wo den Steinen der
nöthige Luftzug zum Austrocknen durch Thüren und Klappluken zugeführt wird, ist das
Abtrocknen derselben immer ungleichmäßig, weil die dem Luftzuge zunächst liegenden
Flächen weit mehr betrocknen, als die entgegengesetzten. Es ist daher nöthig, solche
Steine in den ersten 3–4 Wochen gänzlich vor Luftzug zu schützen, indem man
Thüren und Luken dicht verschlossen hält. Da ihre untere Lagerfläche von der Luft
gar nicht berührt wird, so bleibt dieselbe im Schwinden immer etwas zurück, und
müssen deßhalb die Trockenbretter, wie schon oben bemerkt, stark mit trocknem Sande,
der zugleich frei von Seitenstücken seyn muß, bestreut werden.
Außerdem ist es jedoch auch noch nöthig, die Steine in der ersten Zeit öfters zu
versetzen und die den Luken und Thüren zunächst liegenden und deßhalb mehr
betrockneten Steine nach der Mitte der Scheune, die aus den Mittelgängen hingegen an
jene Stellen zu bringen, um ein gleichmäßigeres Schwinden derselben dadurch zu
erzielen.
Bei Steinen, die in unverhältnißmäßigen Abmessungen geformt sind, wird ein
gleichmäßiges Austrocknen dadurch bewirkt, daß die Steine durch Thonplatten vor dem
Luftzuge gänzlich geschützt werden.
Diese Platten a, a, Fig. 46, werden aus
gewöhnlichem Thon mit Draht zu 1/4 Zoll Stärke und etwas höher als der Stein
geschnitten und kantig zu beiden Seiten desselben aufgeklebt; über dieselben wird
noch eine Platte b gedeckt, so daß der Stein von drei
Platten eingeschlossen und vor jedem Luftzuge bewahrt wird. Es versteht sich, daß
diese dünnen Platten bald trocken werden; aber auch dann noch nützen sie dem Stein,
indem sie ihm Nässe entziehen und dadurch ein gleichmäßigeres Trocknen desselben
herbeiführen. Diese Thonplatten gehen dadurch nicht verloren, sondern werden wieder
aufgeweicht und zur Fabrication anderer Steine benutzt.
Das Einkarren und Brennen der Steine. Das Einkarren der
Steine in die Oefen geschieht, sobald jene vollständig lufttrocken, mittelst
Schubkarren, welche mit Brettern benagelt sind. (Fig. 47.) – In den
Oefen sind die Karrenrüstungen zum Absetzen der mit Steinen beladenen Karren so
angebracht, daß sie bequem nach Erfordern verändert werden können. Die Bänke im Ofen
werden jedesmal vor dem Einsetzen der Steine 1/2 – 3/4 Zoll mit Sand belegt,
welcher mit einem Richtscheit so geebnet wird, daß die durch die Schürgassen
getrennten Bänke unter sich eine ziemlich gerade Ebene bilden, Fig. 48, auf welche die
Steine dann wagerecht und hochkantig aufgesetzt werden. Die Bänke werden mit
Klinkern und Mauersteinen bis auf 3 Fuß Höhe vollgesetzt und mit solchen Steinen und
eben so viel Zwischenraum überwölbt, wodurch die Feuercanäle a, a im Innern des Ofens entstehen. Diese Ueberwölbungen b, so wie
die aufgeführten Bänke, werden dann mit beschnittenen Klinkersteinen c hochkantig auf die ganze innere Fläche des Ofens
möglichst gerade und eben abgeglichen, damit die folgenden Steine darauf gerade und
eben aufgesetzt werden können. Von hier ab wird der Ofenraum bis auf 6 Fuß Höhe (9
Fuß von den Bänken an gerechnet) durchweg mit Steinen, die zu Klinker gebrannt
werden sollen, auch in Zwischenräumen von 3/4 Zoll hochkantig ausgesetzt, weil bei
einigermaßen nachdrücklicher Heizung in diesem Theil des Ofens das Feuer seine
größte Wirksamkeit erreicht, und daher die daselbst befindlichen Klinker sehr fest
und dauerhaft ausgebrannt werden. Der übrige Ofenraum, wo das Feuer nicht mehr so
stark wirkt, wird zu Mauer- und gewöhnlichen Steinen benutzt, da dieselben
mit einem geringeren Hitzgrad vorlieb nehmen.
Sollen Formsteine oder andere künstliche Steine in solchem Klinkerbrande mitgebrannt
werden, so werden dieselben zunächst auf die oberste Schicht der Klinker gesetzt, wo
sie, theils wegen ihrer besonders sauber zubereiteten Erde, theils wegen der
verschiedenen ihnen beigesetzten Präparate doch noch Hitzegrad genug erhalten, um
vollkommen gut durchzubrennen. – Solche Steine können nun aber nicht, wie die
gewöhnlichen, hoch aufeinander fortgesetzt werden, einmal, weil sie zu unregelmäßige
Flächen haben und sich daher beim Brand leicht verschieben würden, dann auch durch
zu schwere Belastung der Gliederungen an denselben oder den gefärbten Flächen leicht
beschädigt werden könnten, sondern sie dürfen höchstens 4 Fuß übereinander
geschichtet werden. Sie werden, so gut es ihre Form zuläßt, in Gängen (Fig. 49)
zwischen Mauersteinen aufgesetzt und mit denselben überwölbt, so daß sie nur ihre
eigene Last zu tragen haben, und von den über ihnen stehenden Steinen nicht gedrückt
werden können. Beim Ueberwölben werden die Mauersteine auch in 3/4 Zoll
Zwischenräumen gesetzt, damit das Feuer sich durch die Fugen hindurchziehen und in
den Gängen überall gleichmäßig wirken kann.
Da die Formsteine sich in den Gängen nicht so regelmäßig setzen lassen als die
gewöhnlichen, so entstehen in den Gängen nothwendig größere Zwischenräume und
Höhlungen, und das Feuer wird dadurch mehr und stärker an diese Stellen hingezogen,
als an andere, wodurch die Formsteine, wenn sie nicht übermäßig groß sind, leicht zu
viel Feuer bekommen können. Um diesem Uebelstand zu begegnen, welchen man übrigens
an der, an solchen Stellen sich zeigenden, helleren Gluth leicht wahrnehmen kann,
wird durch die Decke des Ofens neben den Gängen, durch die Zwischenräume der Steine,
eine Quantität recht trocknen Sandes hinabgestreut und die Decke an solchen Stellen
stärker, als daneben, mit nassem Lehm bedeckt. Dadurch geräth das Feuer an den zu
sehr erhitzten Stellen in Stockung und zieht sich mehr dahin, wo die Decke des Ofens
weniger mit nassem Lehm belegt ist. Dieses Verfahren erscheint nicht schwierig, ist
es auch für einen Erfahrenen nicht, man kann dabei jedoch nicht genug Vorsicht
anwenden.
Sind so viele Formsteine zu einem Brande aufzunehmen, daß dazu die ganze Oberfläche
auf der vorher bezeichneten Höhe benutzt werden muß, und sind dieselben sämmtlich
von solcher Form, daß es nöthig wird, sie alle in Gängen zu überwölben, so muß
sowohl die Anzahl, als die innere Breite derselben, mit Berücksichtigung der aus
Mauersteinen zu bildenden Seitenwände zuvor ermittelt werden.
Dieses geschieht in folgender Art, wobei noch bemerkt wird, daß die Gänge in dem Ofen
der Länge nach gezogen, die innere Weite derselben also von der Anzahl der Gänge,
sowie von der Breite des Ofens abhängig ist:
Ist der Ofen 17 Fuß im Lichten breit, so würden darin 5 Gänge 22 1/2 Zoll breit mit 6
Zwischenwänden 15 Zoll stark angelegt werden können (Fig. 50). Sind weniger
Formsteine mitzubrennen, so werden weniger Gänge angelegt, und die Zwischenwände
fallen dann stärker aus. Es versteht sich, daß zur Ueberwölbung der Gänge sowohl,
als auch zu den Zwischenwänden, nur Luftsteine und niemals gebrannte verwendet
werden.
Da nun die Formsteine ihrer verschiedenen Größe und Form wegen mit den Zwischenwänden
gar nicht in Verbindung zu bringen sind, diese vielmehr in den Gängen ganz frei und
auch unter sich ohne allen Verband stehen, so ist alle Querverbindung im Ofen,
soweit diese Gänge hinaufreichen, aufgehoben. Da diese Steine selten vollkommen
trocken in den Ofen gesetzt werden, beim Brand deßhalb immer noch etwas schwinden,
so könnten sie sich dabei leicht verschieben und die Gänge in Unordnung gerathen,
oder wohl gar zusammenfallen, was für den ganzen Brand von großem Nachtheil
wäre.
Dem vorzubeugen, werden Querverstrebungen durch Einsehen von Mauersteinen mit den
Ueberwölbungen in Verbindung gebracht, welche, 1 1/2 Stein stark, mit etwas engeren
Fugen den Ofen von einer Mauer bis zur andern durchziehen. – Durch solche in
6–8füßiger Entfernung eingebrachte Querverstrebungen wird das Verschieben und
Zusammensinken der mit Formsteinen vollgesetzten Gänge verhindert, und es kann dann
ein solcher Brand, ohne Gefahr zu befürchten, ordnungsmäßig vollendet werden. Auch
das Einsetzen der Steine wird durch solche Abtheilungen sehr erleichtert, denn während man in
den ununterbrochen fortlaufenden Gängen die Steine beim Einsetzen durch allerlei
Absteifungen und andere Vorkehrungen vor dem Umfallen schützen müßte, fällt dieß bei
der angeführten Weise fort.
Ist der Ofen (ein offener ohne Gewölbe) in der beschriebenen Art mit Klinkern,
Formsteinen und andern gewöhnlichen Steinen bis zur Höhe der Ofenmauern vollgesetzt,
so wird darüber eine feste Decke aus flach gelegten, gebrannten Mauersteinen, welche
jedoch öfter dazu benutzt werden können, gelegt, in welcher gleichzeitig die
erforderlichen Oeffnungen zur Communication des Feuers von 8–9 Zoll im
Quadrat groß und 4 Fuß von einander entfernt, angebracht werden. Diese Decke wird,
mit Ausnahme der vorbemerkten Feuerröhren, 4–5 Zoll stark mit nassem mageren
Lehm beschüttet und dieser mit hölzernen Schuhen festgetreten, wodurch das Feuer an
diesen Stellen, wie bei einem gewölbten Ofen, abgeschlossen und gezwungen ist,
seinen Weg durch die angelegten offenen Feuerröhren zu nehmen. Mittelst dieser wird
das Feuer dadurch, daß sie offen oder zugehalten werden, regiert.
In dem so zum Brand vorbereiteten Ofen wird nun in den ersten 8–10 Tagen in
den Schürgassen ein ganz schwaches Schmauchfeuer unterhalten, bis durch solche
gelinde Wärme alle in den Steinen etwa noch vorhanden gewesene Feuchtigkeit
verdrängt ist und die letztern so weit trocken sind, daß ihnen ein stärkeres Feuer
nicht mehr nachtheilig werden kann. Das Feuer wird dann allmählich verstärkt und so
gesteigert, daß die Steine von den Bänken bis zur obern Decke des Ofens, binnen 2
Tagen und Nächten von der vorigen Zeit ab, schwachrothglühend gebrannt werden. Dann
erst beginnt, bei halbaufgemauerten Schüröffnungen, das sogenannte Großfeuer,
welches die Steine, so wie die Decke des Ofens, binnen 24 Stunden ziemlich
weißglühend schafft, ein Zeichen, daß der Brand seiner Vollendung nahe und nur noch
ungefähr 10–15 Stunden mit etwas verstärktem Hitzegrad unterhalten werden
darf.
Dann erst, bei so gesteigertem Hitzegrad, kann man sicher annehmen, daß die in dem
untern Theile des Ofens eingesetzten Klinker sowohl, als auch die übrigen Steine,
die gehörige Härte und Festigkeit erhalten haben und vollkommen gut ausgebrannt
sind.
Die Bereitung des hydraulischen Kalks und des
Ziegelmehls. Der hier fabricirte hydraulische Kalk hat sich bereits durch
langjährige Anwendung zu den Wasserbauwerken in seiner Vorzüglichkeit so bewährt,
daß er zu jedem Bauwerk mit völliger Sicherheit angewendet und mit andern
ausländischen Cementen in der Haltbarkeit fast gleich gestellt werden kann.
Im Wasser erhärtet derselbe in kurzer Zeit zu solcher Festigkeit, daß die Fugen im
Mauerwerk gar nicht wieder zu trennen sind, und widersteht in solchem Zustand auch
dem Frost in vollem Maaße, denn es sind an den hiesigen Wasserbauwerken im
Finowcanal nur selten, auch wenn noch spät im Herbst oder im Winter gemauert worden
war, Spuren einer Verwitterung der Fugen wahrgenommen worden.
Der hydraulische Kalk wird hier bereitet aus 3 Theilen kohlensaurem Mergelkalk, 2
Theilen hiesiger ungeschlämmter, jedoch gut durchwitterten Thonerde und einer
geringen Quantität fein pulverisirtem Eisenocker, wie er zu den Färbungen der
Formsteine angewendet wird, etwa dem 30sten Theil der beiden vorigen Massen.
Der Mergel findet sich im Wiesengrunde am Werbellin-See im erdfeuchten Zustand
und hinreichender Menge. Er wird dort im Herbst gegraben und in etwa 2 Fuß hohen
Haufen den Einwirkungen der Witterung den Winter hindurch überlassen. In gut
durchwittertem Zustande ist er im Wasser leicht löslich, was auch zu feiner
Vereinigung mit dem Thon und dem Eisenocker höchst nöthig ist.
Die drei genannten Substanzen werden mit Wasser eingesumpft und, wenn sie gehörig
aufgeweicht sind, zweimal durch den Thonschneider getrieben, damit sie unter sich
eine vollständige Verbindung eingehen, was bei einem guten Cement durchaus
erforderlich ist. Die so zubereitete Masse wird nun in gewöhnlichen Mauersteinformen
auf einem offenen Streichplatz theils in Trockengerüsten, theils auf der flachen
Erde geformt; die geformten Mergelsteine werden ausgetrocknet, in eben der Art, wie
die Ziegelsteine, in den Brennofen eingebracht und scharf gebrannt. Nach dem Brand
werden dieselben in den hier vor Wasserkraft angelegten Stampfwerken gestampft und
dieses gestampfte Gut auf dem ebenfalls vor Wasserkraft angelegten Mahlwerke
zwischen zwei liegenden Granitsteinen von 4 Fuß Durchmesser zu einem ganz feinen
Pulver zermahlen, welches in Säcken oder Tonnen aufgefangen und zum Verbrauch
versendet wird.
Beim Gebrauch wird dieses Kalkpulver in nicht zu großen Portionen bloß mit Wasser zu
einem steifen Brei angerichtet und muß dann rasch verarbeitet werden, weil es in den
Kalkbehältern sehr bald ersteift und in solchem Zustand umständlich zu verarbeiten
ist, beim nachmaligen Auffrischen mit Wasser aber auch etwas von seiner
Bindungskraft verlieren würde.
Zusatz von Sand oder Ziegelmehl verträgt dieses Kalkpulver nicht; es würde dadurch an
Bindungskraft verlieren. Das angegebene Mischungsverhältniß ist schon so eingerichtet, daß der
Kalk nicht zu fett und daher auch ohne Zusatz zu verwenden ist.Nur wenn man ihn zum Putz anwenden will, ist es angemessen etwas Sand
zuzusetzen, wenn er nicht, was allerdings besser, zu diesem Zweck schon vor
dem Brand etwas magerer gehalten ist. Eben so wenig darf man das Mischungsverhältniß ändern und etwa mehr Mergel
hinzusetzen, um den Mörtel fetter zu machen und sein Volumen durch nachherigen
Zusatz oder dergleichen zu vermehren.
Die richtig zusammengesetzten rohen Substanzen werden nämlich im Feuer chemisch
miteinander verbunden, so daß die Mischung durch bloß mechanisches Beimengen von
rohem Material zu dem gebrannten Gute niemals so vollständig erreicht werden
kann.
Bereitung des Ziegelmehls. Mittelst der beiden auf der
Hauptziegelei vorhandenen, durch Wasserkraft in Bewegung zu setzenden Stampfwerke
wird das Ziegelmehl aus dem aus den Bränden häufig erfolgenden Bruch übercompleter
und schadhafter Formsteine und auch aus eigens dazu bereiteten Charmottesteinen aus
hiesiger Thonerde gestampft und fein gesiebt, und in solchem Zustand dann sowohl zum
Versatz des Thons zu den Klinker- und Formsteinen, als auch zu Mörtel zu den
Hintermauerungen der Schleußenwände verwendet.
Mit wie viel Ziegelmehl die Ziegelmasse versetzt wird, ist
schon vorher bemerkt worden. Der aus Ziegelmehl bereitete Mörtel besteht aus 1 Theil
gelöschtem gewöhnlichen Kalk und aus 2 Theilen Ziegelmehl. Beides wird in einer
Kalkbank gut durcheinander gearbeitet, wie der gewöhnliche Mörtel aus Sand und Kalk
bestehend, und ist dann zum Vermauern fertig.
Bei Ausführung der Wasserbauwerke am Finowcanal wird zwar der Ziegelmehlmörtel
gewöhnlich aus 1 Theil Kalk und 3 Theilen Ziegelmehl bereitet; das vorher angegebene
Mischungsverhältniß dürfte aber besser und vorzuziehen seyn, den Mörtel etwas fetter
zu nehmen, weil das Ziegelmehl dem Kalk sehr schnell alle Feuchtigkeit entzieht.
Zusatz des Geheimen Raths Beuth.
Hr. B. Prössel, jetzt Assistent
seines Vaters bei der königl. Gesundheits-Geschirr-Manufactur bei
Berlin, machte als Zögling des Gewerbe-Instituts (in Berlin) eine Reise durch
England und Frankreich. Aus seinen Reiseberichten entnehme ich folgende Notiz,
welche für die Ziegelfabrication nicht ohne Interesse in Beziehung auf Ersparung an
Brennmaterial ist.
Hr. Feau, Besitzer einer
Ziegelei bei Orleans, hat die Erfahrung gemacht, daß die Höhe des Kamins auf einem
Ziegelofen wesentlich zur Ersparung an Brennmaterial beiträgt. Sein Ofen war zuerst,
wie gewöhnlich, mit einem vielfach durchbrochenen Gewölbe überspannt. Man nahm dieß
indessen ab und mauerte auf den Mantel des Ofens eine vierseitige Pyramide auf, von
30 Fuß Höhe. Da dieß eine sehr gute Wirkung hatte, so fügte man später einen
Schornstein von 20 Fuß hinzu. Folgende Tabelle gibt die dadurch gemachten
Ersparnisse:
Höhe des Aufsatzes
Brennmaterial
Brennkosten von 1000 Ziegeln
0
Klobenholz
7–8 Frcs.
0
Eichene Knüppel in Bündeln
5–6 „
30
Fuß
dasselbe
4–5 „
50 „
dasselbe
3–4 „
Die Fabrication der schwarzen holländischen Ziegel, welche Hr. Feau auf einer Reise nach Holland kennen gelernt
hatte, besteht im Folgenden:
Die Oefen haben kleine Feuerlöcher, für Holz 20 Zoll hoch und 12 Zoll breit, für
Steinkohlen 18 und 12 Zoll. Von den sechs Feuerungen befinden sich drei auf zwei
entgegengesetzten Seiten des Ofens (von 20–24 Fuß Länge und 8–10 Fuß
Breite). Die Abzugsöffnungen 4–6 an der Zahl, durchbrechen das Gewölbe und
sind bei 4 Zoll Breite 2 Zoll lang. Die Feuerungen für Kohlen haben Roste.
Man, beginnt das Feuer mit drei Oeffnungen auf einer Seite des Ofens, um zuerst den
Inhalt vollkommen zu trocknen, schließt sie dann, feuert die gegenüber liegenden an,
und fährt mit dem Feuern fort, bis die Ziegel im Ganzen 4–5 Zoll
zusammengegangen sind. Dann schließt man diese Feuerungen wieder und brennt durch
die drei ersten vollends gar. Man brennt Fichtenknüppelholz in Bündeln oder
Steinkohlen. Brennzeit 48 Stunden.
Anräuchern. Nun bringt man grünes Eschenholz in Bündeln,
welches mehrere Monate in Wasser gelegen hat, in den Ofen, schließt denselben
vollkommen von allen Seiten und öffnet ihn erst nach 8 Tagen. Waren bei dem
Einwerfen des Eschenholzes alle Theile des Ofens recht heiß, so sind die Ziegel
durch und durch schwarz.
Tafeln
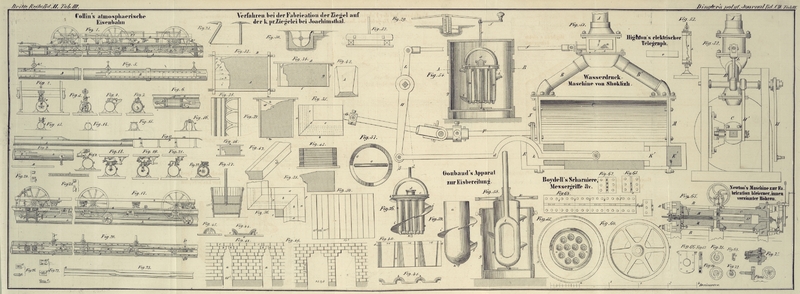