Titel: | Ueber das Brennen des ächten Porzellans mit Steinkohlen; von Vital-Roux, Porzellanfabrikant zu Noirlac bei St. Amand (Dpt. Cher). |
Fundstelle: | Band 104, Jahrgang 1847, Nr. XCV., S. 437 |
Download: | XML |
XCV.
Ueber das Brennen des ächten Porzellans mit
Steinkohlen; von Vital-Roux, Porzellanfabrikant zu Noirlac bei St. Amand (Dpt. Cher).
Aus dem Technologiste, Mai 1847, S.
346.
Mit Abbildungen auf Tab.
VI.
Vital-Roux, über das Brennen des ächten Porzellans mit
Steinkohlen.
Bisher hielt man es fast für unmöglich oder wenigstens für sehr schwierig, die
Steinkohle zum Brennen des ächten Porzellans anzuwenden. Hr. Brongniart spricht in seinem vortrefflichen Traité des arts céramiques von derartigen
Versuchen, welche ehemals zu Lille angestellt wurden und von Anwendungen dieses
Brennmaterials welche die Porzellanfabrikanten in Deutschland machten. Zu Lille
wurden diese Versuche längst aufgegeben und das Brennverfahren in Deutschland finde
ich unvollkommen und ziemlich unsicher.
Da ich entschlossen war die Lösung dieses Problems mit Ausdauer zu verfolgen, mußte
ich zuerst über die wesentlichen Bedingungen zum Brennen des ächten Porzellans im
Reinen seyn. Dann war die Aufgabe die Steinkohlen so anzuwenden, daß dabei nicht nur
an Brennmaterial erspart wird, sondern die Methode sich auch für die jetzt
gebräuchlichen Porzellanöfen eignet, d.h. daß die Fabrikanten ihre gegenwärtigen
Oefen von jeder Größe und Form bloß mittelst einer wenig kostspieligen Abänderung
der Feuerungen benutzen können.
Die Erfahrung hat mich gelehrt, daß eine lange und reichliche Flamme, welche den
ganzen Hohlraum des Ofens ausfüllen kann, eine unumgängliche Nothwendigkeit für
diese Art von Fabrication ist, Denn einerseits erfordert die unschmelzbare Masse des
Porzellans, um gebrannt zu werden, und andererseits die harte Glasur desselben, um
in Fluß zu kommen, eine beträchtliche Hitze und folglich viel Flamme. Gerade die
Schwerschmelzbarkeit und Undurchscheinenheit des Products sind nach meiner Meinung
die Ursache, daß das Porzellan so sehr geneigt ist sich im Ofen zu färben und es muß
daher die Flamme in solchem Ueberschuß vorhanden seyn, daß der Ofen beständig damit
angefüllt ist und überdieß diese Flamme mit solcher Geschwindigkeit abgezogen
werden, daß der Rauch nicht verweilen kann. In der That habe ich mich auch überzeugt, daß wenn in
Folge einer schlechten Anordnung des Zugs oder beim Einsetzen der Kapseln, die
Flamme in einem Theil des (mit Holz oder Steinkohlen geheizten) Ofens fehlt, die
Producte dieses Theils immer gefärbt (nach dem technischen Ausdruck gelb) sind.
Man betrachtete daher die Steinkohle als ein Brennmaterial welches sehr schwierig
oder gar nicht angewandt werden kann. Ihr Rauch kann schädlich seyn, weil er fette
und schweflige Substanzen enthält. Außerdem nahm man an, daß die Steinkohle bei
ihrer Verbrennung nicht so viel Flamme erzeugen kann als zum Brennen des Porzellans
erforderlich ist.
Ich mußte also einen neuen Weg einschlagen und stellte meine ersten Versuche mit
Kohks an, wobei ich folgendermaßen verfuhr. Ich brachte den Rost unter der Ofensohle
an und nachdem ich einige Zeit Kohks zum Vorfeuern gebrannt hatte, verschloß ich die
Luftfänge der Feuerungen genau; hierauf hoffte ich mittelst eines Ventilators
welcher durch verschiedene Leitungen comprimirte Luft unter den Rost führte, eine
hinreichende Menge brennbares Gas entwickeln zu können. In der That wurde auch
beträchtlich viel Hitze und Flamme erzeugt; nach Verlauf weniger Stunden hatten
dieselben aber alles zerstört, die Gewölbe der Feuerungen, die Backsteine und
Kapseln; doch erhielt ich nach siebenstündigem Feuern gut gebranntes und weißes
Porzellan.
Dessenungeachtet gab ich dieses Verfahren als unanwendbar auf; da die comprimirte
Luft so sehr viel Flamme entwickelte, so folgerte ich daß es möglich seyn dürfte die
Flamme der Steinkohlen dadurch hinreichend zu verlängern, daß man ihr eine
beträchtliche Menge Luft von gewöhnlichem Druck zuführt. Um einen Versuch hierüber
anstellen zu können, erbaute ich einen Ofen von 2,66 Meter Durchmesser und brachte
den Rost in einer Höhe von 0,5 Meter über der Aschenraumsohle an. Ich erhielt
bessere aber doch noch unvollkommene Resultate; die Flamme war noch nicht reichlich
genug. Ich bekam in gewissen Theilen des Ofens ein sehr weißes Porzellan; aber
zwischen jeder Feuerung, da wo die Flamme unzureichend war, färbte sich das
Porzellan.
Nun unterstützte mich Hr. Merkens mit seinem Rath und wir wandten ein System, nämlich Oefen
mit doppeltem Luftzug an, welches zu einem vollständigen Erfolg führte. Ich ließ nun
meine Aschenräume von 1,50 Meter herstellen und mittelst eines Gewölbes äußere Luft
einziehen. Meine Röste wurden einerseits durch den Luftfang gespeist, welcher von
der Ofensohle bis zum Rost 0,5 Meter hoch war und andererseits durch den sogenannten
Luftfang welcher unter dem Verbindungsgewölbe nach den Rösten zog.
Drei nach einander vorgenommene Brände lieferten uns vollkommene Resultate; wir
hatten nicht ein einziges gefärbtes Stück; das Glattbrennen ließ nichts zu wünschen
übrig und das Verglühen war vollkommen; kurz, es verhielt sich alles wie in einem
mit Holz geheizten Ofen; die zum Brennen verwendete Zeit war beiläufig dieselbe wie
mit Holz, auch die Flamme der Feuercanäle und des Schornsteins eben so reichlich wie
mit letzterm.
Ich wandte hierauf diese Versuche im Großen an und habe nun in täglichem
Gebrauch:
1) Einen Ofen von 4,66 Meter Durchmesser, 3 Meter Höhe am Viereck des Gewölbes und
4,33 Meter am Schlüssel (Schieber) des Gewölbes (oder Schornstein) des oberen Raums.
Dieser Ofen ist mit acht Feuerzügen versehen; das Gewölbe des oberen Raums ist mit
acht Feuercanälen (Oeffnungen) zwischen jedem Feuerzug versehen und in der Mitte
dieses Gewölbes ist der Schornstein angebracht.
2) Einen andern Ofen von 5,66 Met. Durchmesser, 3 Met. Höhe am Viereck des Gewölbes,
4,33 Met. Höhe am Schlüssel des Gewölbes des oberen Raums. Dieser Ofen ist mit zehn
Feuerzügen versehen; durch das Gewölbe des oberen Raums gehen zehn Feuercanäle
zwischen jedem Feuerzug und in der Mitte des Gewölbes ist der Schornstein
angebracht.
Die Dimensionen der Röste beider Oefen sind dieselben, nämlich 0,84 Meter Länge auf
0,48 Meter Breite; der Zwischenraum der Stangen beträgt 18 Millimeter.
Außer den Abänderungen an den Feuerungen und Luftfängen wurde also an den
Verhältnissen und Dimensionen der gewöhnlichen Oefen nichts geändert.
Als der Ofen von 4,66 Meter Durchmesser mit Holz geheizt wurde, hatte er fünf
Feuerzüge; mit Steinkohlen hat er deren acht; der Ofen von 5,66 Met. Durchmesser
hatte bei der Holzfeuerung sechs Feuerzüge, mit Steinkohlen hat er deren zehn.
Seit der Anwendung der Steinkohlen statt des Holzes in den Oefen zu Noirlac, welche
seit mehr als drei Monaten in Gebrauch ist, stellt sich die Ersparniß an den Kosten
des Brennmaterials folgendermaßen heraus:
Der Ofen von 4,66 Meter
Durchmesser verbrauchte im Mittel per
Brand 96 Sters Eichen- oder Buchenholz, wovon im Bezirk von
St.Amand der Ster gespalten und an den Ofen transportirt auf 7 Frcs.
zustehen kommt, also für
672 Fr.
Er verzehrt jetzt stündlich
150 Hektoliter Steinkohlen vonCommentry, à 1 Fr. 80 Cent. der Hektoliter
270 „
––––––
Differenz
402 Fr.
Der Ofen von 5,66
Meter Durchmesser verbrauchte per Brand
120Sters Holz à 7 Frcs.
840 Fr.
Er verzehrt jetzt stündlich
220 Hektoliter Steinkohlen à 1 Fr.
80Cent.
396 „
––––––
Differenz
444 Fr.
Außer dieser Ersparniß an Brennmaterial hat man aber noch andere Vortheile:
1) Ein vollkommeneres Brennen, indem die Artikel ganz gleichförmig gebrannt werden,
in der Mitte wie an den Seiten, oben wie unten.
2) Die Kapseln, deßgleichen die Ofenwände und Gewölbe werden viel weniger beschädigt.
Bei Anwendung von Holz verbindet sich die Asche desselben mit der Kieselerde der
Kapselmasse und der Backsteine an den Wänden der Oefen und verglast sie an der
Oberfläche; in Folge dieser Verglasung zerbrachen bisher die Kapseln beim Erkalten
leicht.
Beim Brennen mit Steinkohlen findet hingegen keine Verglasung statt; die Wände der
Oefen bleiben wie vor dem Heizen und die Kapseln bleiben ohne alle Veränderung so
wie man sie stellte.Einem Auszug dieser Abhandlung in den Comptes
rendus (welcher bereits im polytechn. Journal mitgetheilt wurde)
fügte Hr. Alex.
Brongniart die Bemerkung bei, daß Hr. Renard zu St. Gond bei Etoges (Dpt. Marne) Versuche anstellt um ächtes
Porzellan mit den aus Torf erzeugten Gasen zu brennen und daß dieselben bis
jetzt günstige Resultate lieferten.
Erklärung der Abbildungen.
Fig. 18 ist
der Durchschnitt auf der Linie CD des
Grundrisses.
Fig. 19 ist
zur Hälfte der Durchschnitt auf der Linie AB des
Grundrisses Fig.
18, und zur Hälfte die äußere Ansicht auf der Linie EF
Fig. 18.
1 innerer Theil des Ofens (Gutofen oder Glattbrennofen).
2 oberer Theil, sogenannter gewölbter Raum.
3 oberer Schornstein.
4 Schornstein des inneren Theils (Gutofens), welcher in den gewölbten Raum
hineinreicht.
5 Thüre des inneren Theils des Ofens.
6 Thüre des oberen gewölbten Raums.
7 Ausmündung der Feuerungen in den Ofen.
8 kleine Oeffnung um den Rost zu wechseln, wenn der innere Theil des Feuerraums
verstopft seyn sollte.
9 Aschenraum und Lüftungsgallerie.
10 Feuercanäle im Gewölbe des oberen Raums.
11 Sohle des oberen Raums.
12 Sohle des Ofens.
Tafeln
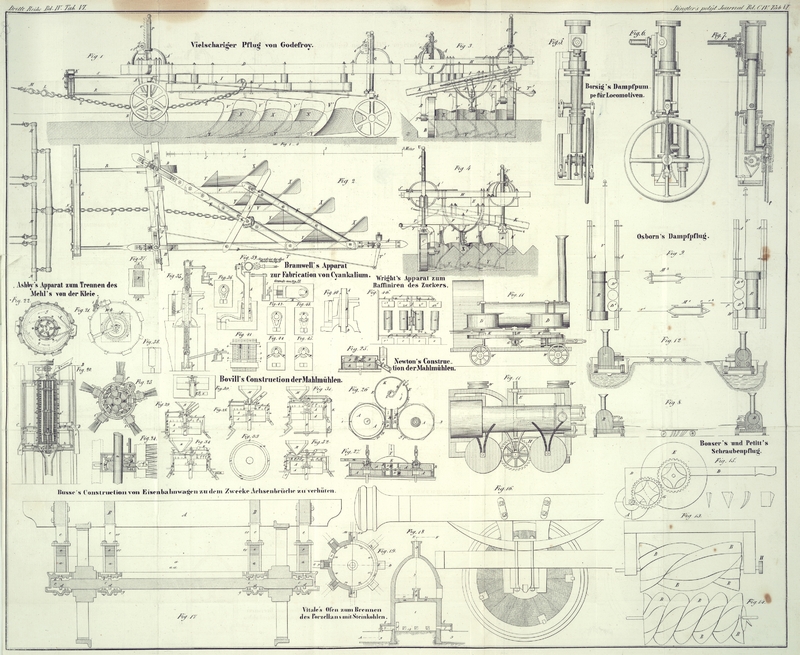