Titel: | Verbesserungen in der Fabrication der Kerzen, worauf sich Fennell Allman, Ingenieur in London, am 4. Mai 1847 ein Patent ertheilen ließ. |
Fundstelle: | Band 107, Jahrgang 1848, Nr. C., S. 421 |
Download: | XML |
C.
Verbesserungen in der
Fabrication der Kerzen, worauf sich Fennell Allman, Ingenieur in London, am 4. Mai 1847 ein Patent
ertheilen ließ.
Aus dem London Journal of arts, Dec. 1847, S. 360.
Mit Abbildungen auf Tab. VI.
Allman's Verbesserungen in der Fabrication von
Kerzen.
Den Gegenstand dieser Erfindung bildet die Anfertigung gepreßter
Kerzen; ferner die Anfertigung von Kerzen mit einer Hülle von
gutem Material, die mit einem Material geringerer Qualität
gefüllt ist.
Die in kaltem Zustande zur Verfertigung gepreßter Kerzen zu
verwendenden Materialien sind Wachs, Wallrath, Stearin oder
Stearinsäure, und Mischungen derselben; es darf jedoch kein
Elain oder Olein dabei seyn, weil dieses das Festwerden der dem
Druck ausgesetzten Materialien verhindern würde. Fig. 8 stellt die Maschine zur Anfertigung gepreßter
Kerzen im horizontalen Längendurchschnitte dar. Sie besteht aus
einem zur Aufnahme der fetten Substanz dienlichen Cylinder a, der mit einem halbkugelförmigen
Deckel versehen und in den Mantel c
eingepaßt ist. Der Cylinder wird während der Verfertigung der
Kerzen mittelst zweier in verticale Rinnen des Gehäuses c einführbarer Hervorragungen a', a' in der geeigneten Lage
erhalten. Diese Anordnung gestattet den Cylinder, wenn er leer
ist, herauszunehmen, um ihn wieder zu füllen. An den Deckel b ist eine Röhre d befestigt, durch welche die
Fettsubstanz von dem Kolben e
gepreßt wird und auf diese Weise bildet sich rings um den Docht
f die Kerze. Der Docht wird von
einer Spule g geliefert, von welcher
er um die Rolle h durch einen in der
Flansche des Cylinders a und in dem
Steg i befindlichen Canal und so
fort durch die Dille j in die Röhre
d geleitet wird. Die Bewegung
des Kolbens e erfolgt auf die
nämliche Weise wie bei einer hydraulischen Presse, indem man
nämlich Wasser durch den Canal I in
den cylindrischen Raum k preßt. Soll
der Kolben in die Vertiefung m
zurückgezogen werden, um den Cylinder a behufs der Füllung herauszunehmen, so läßt man das
Wasser durch den Canal n ausfließen,
während der Kolben durch das Gegengewicht o zurückgezogen wird. Die Liederung des Kolbens bildet
ein stählerner Ring, welcher durch den Druck der harten, fetten
Substanz gegen die innere Cylinderwand gepreßt wird.
Den aus der Röhre d herausgepreßten
zusammenhängenden Fettcylinder mit dem eingeschlossenen Dochte
schneidet man in Stücke von der geeigneten Kerzenlänge.
Mit Hülfe des in Fig. 9
abgebildeten Apparates gibt man dem Kerzenende eine conische
Gestalt. Eine Achse u, an deren
Enden zwei krumme Messer befestigt sind, wird nämlich mittelst
eines um die Rolle v geschlungenen
Riemens in Rotation gesetzt. Gegen diese Messer schiebt man die
Kerze durch ein in der Führung w
angebrachtes Loch und ertheilt ihrem Ende auf diese Weise die
erforderliche conische Gestalt.
Um dünne Kerzenröhren oder Hüllen anzufertigen, schraubt man den
in Fig.
10 im Durchschnitt dargestellten Deckel b auf den Cylinder a. Im vorliegenden Falle ist ein
Cylinder x an den Steg i befestigt, welcher die Röhre d beinahe ausfüllt und nur einen
engen ringförmigen Raum übrig läßt. Durch diesen Raum wird die
Fettsubstanz gepreßt und muß daher in Röhrenform zum Vorschein
kommen. Die Fettröhre wird nun in Stücke von geeigneter Länge
zerschnitten und jedes Stück mit Hülfe des in Fig.
11 abgebildeten Apparates mit Materialien
geringerer Qualität gefüllt. Die röhrenförmige Fetthülle a wird nämlich in die Röhre b geschoben, so daß ihr unteres Ende
auf dem zinnenen Boden c, der das
conische Ende der Kerze bilden soll, aufsitzt. Der Docht wird
von der Spule d durch die Mitte der
Fetthülle aufwärts geführt, an den Arm e befestigt und das die Kerzenröhre umgebende Gehäuse
mit kaltem Wasser gefüllt; hierauf wird die geringere Substanz
in geschmolzenem Zustande in die Röhre gegossen. Nachdem das
Ganze erstarrt ist, entfernt man die Kerze aus dem Apparate.
Tafeln
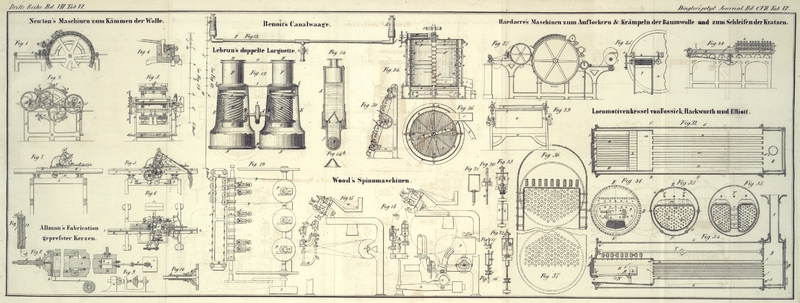