Titel: | Die Fabrication der geformten oder sogenannten Pariser Kohlen, ein neuer Industriezweig; beschrieben von Prof. Payen. |
Fundstelle: | Band 121, Jahrgang 1851, Nr. CIV., S. 422 |
Download: | XML |
CIV.
Die Fabrication der geformten oder sogenannten
Pariser Kohlen, ein neuer Industriezweig; beschrieben von Prof. Payen.
Aus dessen Précis de Chimie industrielle, 2. édition.
Paris 1851.
Mit Abbildungen auf Tab.
VI.
Payen, über die Fabrication der geformten oder sogenannten Pariser
Kohlen.
Seit vorigem Jahr wurde durch Hrn. Popelin-Ducarre
ein merkwürdiger Industriezweig gegründet, — die Fabrication einer geformten
Kohle aus den kleinen Abfällen verschiedener verkohlter Substanzen, welche in
Cylinderform verbunden werden und dann der gewöhnlichen Holzkohle ähnlich sind.
Was diesen neuen Industriezweig charakterisirt, das ist die Vereinigung und das
Aneinanderhaften der Theilchen, was vermittelst einer Substanz bewirkt wird, welche
nicht nur diese Trümmerchen unter sich zu verbinden, sondern nach ihrer eigenen
Verkohlung sie noch zusammenzuhalten vermag, indem sie dabei eine von flüchtigen
Stoffen und Asche freie Kohle zwischen denselben ablagert.
Der rohe Theer aus den Steinkohlengasanstalten ist eine derjenigen Substanzen, welche
sich zu diesem Zweck am besten eignen; derselbe hinterläßt nämlich 20 bis 25 Procent
seines Gewichts zwischengelagerter Kohle; außerdem liefert er durch seine flüchtigen
Kohlenwasserstoffe noch brennbare Dämpfe, welche zur Verkohlung der geformten
Cylinder beinahe schon ausreichen.
Man gießt den Theer, wovon man sich einen Vorrath anschafft, in gemauerte Cisternen,
aus welchen er mittelst Pumpen nach Bedarf zur Fabrication der geformten Kohle
geschöpft wird.
Das in verschiedenartigem Kohlenklein bestehende Rohmaterial liefert je nach seiner
Natur Producte von mehr oder weniger Werth.
Folgendes sind die vorzüglichsten derartigen Stoffe:
1. Holzkohlenstaub2. Torfkohlenstaub
Rückstände auf den Böden der Dampfschiffe und verschiedener
Magazine.
3. Kohle des Reisigs aus Wäldern, des Heidekrauts etc.
4. Erschöpfte und verkohlte Gerberlohe (pulverige Rückstände aus
Gasanstalten und Kohksmagazinen.)
Die für sich allein angewandten oder in gewissen Verhältnissen gemengten kohligen
Substanzen liefern mehr oder weniger wohlfeile Sorten, welche sich zu speciellen
Zwecken eignen.
Das Material zur Erzeugung der zusammengeklebten Kohlen mittelst Formens und
Verkohlens, besteht also aus Theer und pulveriger Kohle; die Verhältnisse derselben
sind nach der Natur der angewandten Kohlen und der beabsichtigten Producte
verschieden. Wir werden sie angeben, nachdem wir die für alle derartigen Kohlen
erforderlichen Operationen beschrieben haben.
Zerreiben. — Die mit 8–12 Procent Wasser
befeuchteten kohligen Substanzen werden zuerst in ein grobes Pulver verwandelt,
indem man sie zwischen zwei gußeisernen Walzen hindurchläßt, welche cannelirt oder
in facettirten Spitzen gerauht sind; diese Walzen drehen sich in entgegengesetzter
Richtung und die eine hat die doppelte Geschwindigkeit der andern; das Zerreiben
wird zwischen zwei andern Walzen mit glatter Oberfläche beendigt. Drei Pferdekräfte
genügen zum Zerreiben von 300 Hektolitern in 34 Stunden.
Vermischen. — Die pulverige Substanz wird alsdann
in den kreisrunden gußeisernen Trog einer Mühle H, H
(Fig. 37
und 38)
geschüttet, welche mit zwei kegelförmigen, cannelirten gußeisernen Läufern A, A′ versehen ist (A″ Fig. 39 zeigt sie in der Vorderansicht); eine verticale Achse, welche die
Bewegung von dem Zahnrad C erhält, dem sie das Getriebe
D mittheilt, versetzt die zwei Läufer in Umdrehung;
ein Pflug O verfolgt die Spur der Läufer, durchwühlt die
Kohle und erneuert deren Oberflächen. Man setzt auf 100 Kilogr. Kohle 33 bis 40
Liter Theer zu; das von den Läufern bewirkte Zerreiben mengt und knetet zugleich, so
daß ein sehr dicker und gleichförmiger Teig entsteht; wenn das Zerreiben beendigt
ist, zieht man eine Thür F von Eisenblech auf und läßt
einen Schaber M herab, welcher in Folge der
Centrifugalkraft das Gemenge in einen Behälter E
hinabwirft. Diese Mühle erfordert nur eine einzige Pferdekraft, um in 24 Stunden 300
Hektoliter zu vermengen.
Formen. — Folgende von Hrn. Popelin-Ducarre erfundene Maschine comprimirt und formt den auf
beschriebene Art bereiteten Kohlenteig in Cylinder.
Ein starker hölzerner Querbalken A, B (Fig. 40) steigt
abwechselnd auf und ab vermittelst der (gebrochenen) Stangen I, J und I′, J′, welchen die Hin- und Herbewegung von einem darunter
befindlichen (in der Abbildung weggelassenen) Excentricum mitgetheilt wird. Der
Balken A, B wird mittelst zweier Ringe geführt, welche
an den verticalen, cylindrischen, eisernen Ständern H, G
und H′, G auf und ab
gleiten.
Auf der Mittellinie des Balkens sind verticale eiserne Kolben befestigt, wovon die
einen b, d, den Kohlenteig in die Formen pressen, die
andern a, c, e, ihn dann aus denselben
herausdrücken.
Zwei Frauen sind beständig damit beschäftigt, den Kohlenteig in Trichter zu werfen,
deren Röhre durch eine unbewegliche gußeiserne Platform M,
M geht.
Die Kolben b, d drücken den Teig in diese Trichter und
pressen ihn in offene cylindrische Höhlungen herab, welche in einer zweiten,
beweglichen gußeisernen Platte E, E angebracht sind;
diese Platte wird horizontal hin und herbewegt (mittelst eines Excentricums, welches
seine Bewegung durch das Zahnrad K und das Getriebe L erhält), und verschiebt sich, sobald die Kolben b, d wieder in die Höhe gehen, wodurch sich eine zweite,
der ersten gleiche Höhlung unter den Trichtern darbietet, die man eben so füllt.
Eine unbewegliche gußeiserne Platte H hat den Kolben a, c, e entsprechende Löcher, so daß während neue Röhren
sich füllen, diese Kolben auf die ersten Cylinder von comprimirtem Teige drücken und
sie unten hinausstoßen.
Zwei Frauen fangen je zwei Cylinder (mit jeder Hand einen) auf und legen sie
horizontal in einen rectangulären tragbaren Korb; jeder Schlag hin und her dauert 2
Secunden, comprimirt 4 Cylinder und treibt 4 andere aus den Formen (indem die
Maschine doppelt ist, nämlich eine doppelte Reihe von Cylindern und Höhlungen in den
Platten A B, C D, EE, MM darbietet).
Ein Mann und vier Frauen, welche diese Maschine bedienen, fertigen in einem Tage 150
Hektoliter solcher Cylinder aus Kohlenteig; die mechanische Totalkraft entspricht 6
Dampfpferden.
Trocknen. — Die mit Cylindern angefüllten Körbe
werden 36 bis 48 Stunden lang an einen luftigen Ort gestellt, damit diese Cylinder
durch eine erste Austrocknung mehr Consistenz gewinnen.
Verkohlung. — Sie geschieht in Oefen mit doppelten
Muffeln Fig.
31, 32, und 33; die Muffeln A, A sind 11 Centimeter dick,
von guten Backsteinen gemauert, und werden durch einen Feuerraum B geheizt; die Verbrennungsproducte umgeben die Muffeln,
indem sie zwischen ihnen und hinter ihnen in den Feuercanälen C, D circuliren, kehren vorwärts in den Canälen E zurück und ziehen dann durch Seitenöffnungen f,
f und untere Züge g, g, g in einen liegenden
Kamin hinter dem Ofen ab, welcher sie zu einem Dampfkessel führt, um die von ihnen
mitgerissene Wärme zu benutzen.
Die 12 Centimeter langen und 4 Centimeter dicken (getrockneten) Kohlencylinder (D, E, Fig. 36) werden vertical,
je zwei übereinander, in schwarzblechene Büchsen H, H
(Fig. 31,
32, 33 und 34) oder in
gußeiserne cylindrische Gefäße I, I (Fig. 31 und 33 und A, C
Fig. 36)
eingesetzt. Diese Büchsen oder Gefäße, 24 an Zahl, werden auf Karren j, j angebracht; man stellt drei Reihen solcher Büchsen
übereinander und schafft sie zusammen in den Oefen mittelst einer kleinen Eisenbahn,
deren letzte bewegliche Schienen an die fixirten Schienen auf der Sohle jeder Muffel
anstoßen.Auch die Verkohlung in cylindrischen Oefen von 2,50 Meter Durchmesser und
drei Meter Höhe, mit einer Oeffnung von 70 Centimeter im Gewölbe und unten
mit einer Thür von 60 Centimeter im Gevierte versehen, lieferte gute
Resultate.
Eine mit Backsteinen bekleidete, gußeiserne Thür K
verschließt die ganze Vorderseite jeder Muffel; man verstreicht die Fugen mit Thon
und zündet das Feuer an (man kann zwischen der Thür und den Gefäßen noch eine Mauer
I von breiten trocknen Backsteinen aufführen, welche
die Wärme zusammenhält und die man, wenn die Muffeln entleert werden sollen, in
einigen Minuten wieder abtragen kann).
Das Wasser, welches in den geformten Cylindern zurückgeblieben ist, entweicht bald
durch die kleinen Seitenlöcher n, n; ein Theil der
Kohlenwasserstoffe des Theers setzt dann einen Antheil ihres Kohlenstoffs in den
Zwischenräumen der Kohlencylinder ab; der von diesen Kohlenwasserstoffen erzeugte
Dampf entweicht ebenfalls durch die Seitenlöcher n; da
die Außenwände der Muffeln bis zum Rothglühen erhitzt sind, so müssen diese
Producte, sobald sie aus den Muffeln durch die kleinen Feuercanäle abziehen, sich
entzünden; Zuglöcher, sür die äußere Luft, m, m (Fig. 32),
welche man durch ein Ziegelstück verengen kann, führen die erforderliche Luft
herbei, welche sich auf ihrem Weg im Mauerwerk erwärmt und diese Verbrennung
bewerkstelligt. Die so erzeugte Flamme umhüllt die Muffeln, und zieht dann durch die
Feuercanäle C, D, E in die Rauchzüge g, g ab.
Die Verbrennung der flüchtigen Producte genügt um die Verkohlung fortzusetzen.
Um die Temperatur so hoch und regelmäßig zu erhalten, daß sich die Dämpfe und Gase
entzünden, beschickt man die Muffeln jedes Ofens in Zeitabständen von sechs Stunden;
auf diese Weise hat man alle sechs Stunden eine Muffel zu entleeren, weil die
Verkohlung zwölf Stunden dauert.
Dämpfen (Ersticken). —
Man erkennt, daß die Verkohlung beendigt ist beim zeitweisen Oeffnen eines Gucklochs
m′, wenn sich durch die kleinen in den Wänden
jeder Muffel angebrachten Feuercanäle n, n keine Flamme
mehr entbindet.
Man nimmt alsdann den Lehm ab, und öffnet eine der Thüren K; man legt bewegliche Schienen vor, und zieht mit einem Haken (Fig. 35) den
Karren auf der Eisenbahn in eines der nahen Magazine heraus; hierauf verkittet man
die Fugen zwischen den Gefäßen, um eine theilweise Einäscherung zu verhüten,
deßgleichen die Fugen der Deckel B (Fig. 36).
Man schafft einen oder zwei bereits hergerichtete Karren mit ihrer Ladung (Fig. 34) in
den Ofen. Ebenso wird nach 6 Stunden mit der zweiten Muffel, die folgenden Tage mit
allen andern Muffeln verfahren.
6–8 Stunden nach dem Herausnehmen aus den Muffeln werden die Gefäße geöffnet,
im Magazin ausgeleert und die Karren auf einer Eisenbahn in die Werkstätten
zurückgebracht, um sie frisch zu füllen.
Man kann auf diese Weise in jeder Muffel in 24 Stunden leicht zwei Verkohlungen
durchführen.
Das beschriebene Fabricationsverfahren beschränkt sich aber nicht auf das erwähnte
Rohmaterial, jene Rückstände; sondern dieser neue Industriezweig veranlaßte die
besondere Verkohlung der Holzabfälle oder der kleinen krumm gewachsenen Reiser,
welche oft nur störend und nutzlos in den Holzungen herumliegen, ferner des
Heidekrauts, des Ginsters etc. Hr. Popelin-Ducarre
verkohlt dieselben seit einiger Zeit, um damit geformte Kohle zu fabriciren.
Die Figuren 41
und 42 zeigen
die Einrichtung des zu dieser Verkohlung dienenden Ofens; dieser von Backsteinen
aufgeführte Ofen ist mit einer dicken Mauer E aus
Bruchsteinen umgeben, und hat im Innern eine Länge von 2,50 Meter; 1,50 Meter Breite
und 2,50 Meter Höhe unter dem Gewölbe; oben wird eine Oeffnung C von 1 Meter Länge und 50 Centimeter Breite durch einen
gußeisernen Rahmen hergestellt, welche mit einem Deckel D von Eisenblech oder Gußeisen nach Belieben verschlossen werden kann;
unten befindet sich in diesem Ofen eine etwa 1 Meter breite und 40 Centimeter hohe
Oeffnung
a, ebenfalls durch einen gußeisernen Rahmen gebildet,
auf welche eine Thür aus gleichem Material paßt.
Dieser Ofen ist einfach oder an andere angebaut, wie der Grundriß (Fig. 43) zeigt.
Die Verkohlung geht auf folgende Weise vor sich. Man läßt das Mauerwerk vorerst
austrocknen, erwärmt es dann allmählich durch Verbrennen der schlechtesten
Holzabfälle im Innern, und reinigt hierauf die Sohle.
Man bringt nun in den Ofen A durch die obere Oeffnung C (Fig. 41) 25 Reisigbüschel
oder Bündel dünner Reiser, von denen jeder 10 Kilogr. wiegt; nur beim erstenmal
wirft man auf diese Reiserbündel eine Schaufel voll glühender Kohlen; es steigt ein
dicker Rauch auf, man lutirt die untere Thür genau und nach drei Stunden, wo der
Rauch schwächer geworden ist, fügt man von Stunde zu Stunde fünf Bündel hinzu, bis
die Zahl von 50 erreicht ist, was einem Gewichte von 500 Kilogr. entspricht. Sobald
der Rauch aufhört oder durch einen schwachen bläulichen Flammenstrahl ersetzt ist,
verschließt man die obere Oeffnung und lutirt sie mit Erde; man öffnet dann die
untere Thür und zieht mittelst einer Scharre die Kohle heraus, welche man in einen
Kohlendämpfer fallen läßt, oder ausbreitet und mit Wasser begießt.
Man beginnt nun eine ähnliche Operation, ohne jedoch glühende Kohle anzuwenden, indem
man je fünf Reiserbündel auf einmal in den Ofen gibt, so daß in 7½ Stunden
deren 50 hineingeworfen werden, um einen Brand vollzumachen, welchen man wie den
ersten herausschafft.
Auf diese Weise macht man in 24 Stunden drei Brände, zu welchen 1500 Kilogr.
trockener Reiser erforderlich sind, die 450 Kilogr. oder 30 Procent Kohlenklein
liefern; vier aneinander stoßende Oefen, wie sie im Grundriß (Fig. 43) zu sehen sind,
würden also täglich 1800 Kilogr. Kohle erzeugen.
Unter gewissen Umständen könnten das Material zu dieser Art von Verkohlung auch junge
Schläge vom Lichten neuer Pflanzungen liefern, vielleicht sogar jährige Pflanzen mit
halbholzigen Stengeln, z. B. die Erdbirnen (knolligen Sonnenblumen). Jedenfalls
verdient diese neue Verwendung derselben als Brennmaterial die Beachtung der
Oekonomen.
Diese Kohle unterscheidet sich von der gewöhnlichen Holzkohle durch ihr Gefüge, weil
sie aus sehr kleinen Stücken und einer dazwischen gelagerten Kohle besteht, welche
letztere ihr eine gewisse Cohäsion ertheilt.
Der hauptsächlichste Unterschied besteht in einer um etwa 33 Proc. größern und
überdieß regelmäßigeren Dichtigkeit.
Die beste Sorte von dieser Art Kohlen bekommt man durch Anwendung 1) des Pulvers von
Kohle aus harten Hölzern, welche das Minimum von Asche enthalten, und 2) einer
starken Portion Theer (bis zu 60 Kilogr. auf 100 Kilogr.); denn der Theer welcher
keine unverbrennliche Materie zurückläßt, liefert ungefähr ¼ seines Gewichts
reinen Kohlenstoff. Die zweite Sorte erhält man durch Anwendung des Kohlenstaubs aus
verschiedenen Magazinen, welcher mit 36–40 Proc. Steinkohlentheer
zusammengeklebt wird; diese Kohle enthält oft größere Mengen von Asche, woran der
Umstand Schuld ist, daß die auf dem Boden der Magazine gesammelten pulverigen
Abfälle großentheils von verkohlten Rinden herrühren, welche der Holzkohle anhingen
und leichter als diese zerfallen; bekanntlich sind in den Rinden die mineralischen
Substanzen in größerer Menge enthalten, als im cylindrischen Holzkörper der Bäume.
Sehr kleines Gezweige (Astwerk) liefert ebenfalls eine Kohle welche mehr Asche
enthält, als diejenige von großen Aesten.
Wir haben oben gesehen, daß man, freilich nur ausnahmsweise, eine geformte Kohle
bereiten kann, welche reiner ist, oder einen geringeren Aschengehalt hat, als die
gewöhnliche Holzkohle; man würde denselben Zweck auch durch Verkohlung des
Schalholzes (des zur Gewinnung der Gerberlohe seiner Rinde beraubten Eichenholzes)
erreichen.
Sind Torfkohlen-Abfälle das Rohmaterial, so wird der Aschengehalt größer und
veränderlicher.
Die erschöpfte Gerberlohe kann auch als Rohmaterial dienen, wo dann der Aschengehalt
der Producte ebenfalls größer wird als in der Holzkohle; überdieß ist eine wohlfeile
Verkohlung der erschöpften Lohe eine zur Zeit noch nicht vollständig gelöste
Aufgabe.
Die geformte Kohle, welche man mit kleinen Kohksabfällen erhält, verbrennt nicht so
leicht wie die Holzkohlen, aber viel leichter als die Kohks selbst, und noch
leichter als die pulverigen Rückstände der Kohks.
Jedenfalls kann die Entzündung dieser verschiedenen geformten Kohlen befördert
werden, indem man ihnen einige Procente gewöhnlicher Holzohle beigibt oder solche
unter sie hinunterbringt.
Man kann auch die Temperatur welche die geformten Kohlen beim Verbrennen entwickeln,
durch Verstärkung des Zugs erhöhen; in diesem Fall läßt man eine größere Luftmenge hindurchziehen,
welche mehr Kohlenstoff verbrennt, also in derselben Zeit und demselben Raum mehr
Wärme hervorbringt; folglich wird hierdurch die Temperatur erhöht, wenn anders der
Verlust um den Feuerraum herum derselbe bleibt. Endlich wird es einleuchten, daß der
Luftstrom, welcher die Asche mitreißt oder schmilzt, das Hinderniß verringert,
welches diese mineralischen Substanzen der Verbrennung entgegensetzen.
Anwendungen. — Diese geformten Kohlen sind zum
Heizen bei allen Verrichtungen in der Küche und dem Laboratorium anwendbar; in Folge
ihrer in der Regel langsameren und regelmäßigeren Verbrennung ist der Verbrauch im
Vergleich mit gewöhnlicher Holzkohle viel geringer.
Namentlich gewährt das Erhitzen mittelst geformter Kohle bei
Elementar-Analysen den Vortheil einer leichter zu regulirenden Temperatur und
einer viel geringeren (den Analytiker sonst so belästigenden) Wärmeausstrahlung.
Kurz, bei den Operationen im Laboratorium sowohl als in den Küchen der Haushaltungen,
gewähren diese Kohlen im Allgemeinen nicht unbedeutende Vortheile; da ihre
Fabrication die Verwendung der kleinen Ueberreste verschiedener Kohlenarten und der
Kohks ermöglicht, so kann man mit dem neuen Brennmaterial je nach den Zwecken, sowie
den Sorten und Preisen desselben, wechseln.
Die Producte dieses neuen Industriezweigs werden bereits in vielen öffentlichen
Anstalten zu Paris, bei Privaten und in Laboratorien angewandt; wir erwähnen von
letztern das Conservatorium für Künste und Gewerbe, die Münze, die pharmaceutische
Schule, die Bergwerksschule etc.
Die Quantitäten, welche davon jährlich bereitet werden könnten, sind beträchtlich,
denn ein Hauptmaterial, der Theer, wird in den Gasanstalten, welche sich in den
meisten Städten Frankreichs verbreiten, in Menge gewonnen.
Die Pariser Gasanstalten, welche allein jeden Abend etwa 100,000 Brenner speisen,
liefern beiläufig 5 Millionen Kilogr. Theer, welche zur Fabrication von wenigstens
12 Millionen Kilogr. Kohle hinreichen würden.
Eine einzige in Paris von Hrn. Popelin-Ducarre
errichtete Fabrik erzeugt täglich in vier Oefen mit Doppelmuffeln 150 Hektoliter
Kohle, welche 4950 Kilogr. wiegen, so daß die jährliche Production 1,782,000 Kilogr.
beträgt.
Tafeln
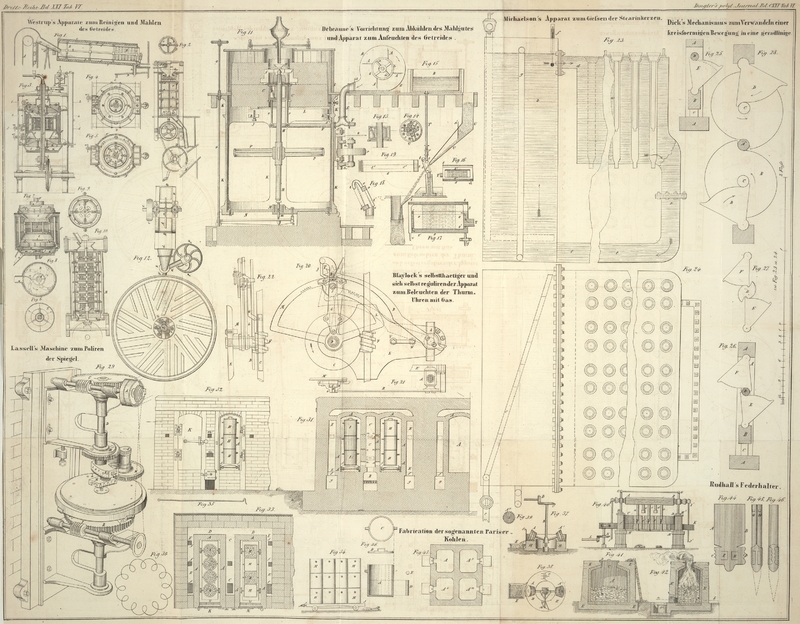