Titel: | Ueber die Verwandlung der vegetabilischen Brennmaterialien in Gas und dessen Benutzung zur Stabeisenfabrication auf der Hütte zu Villotte bei Chatillon an der Seine, im Goldküstendepartement; von Hrn. L. Cailletet. |
Fundstelle: | Band 143, Jahrgang 1857, Nr. XCVIII., S. 415 |
Download: | XML |
XCVIII.
Ueber die Verwandlung der vegetabilischen
Brennmaterialien in Gas und dessen Benutzung zur Stabeisenfabrication auf der Hütte zu
Villotte bei Chatillon an der Seine, im Goldküstendepartement; von Hrn. L. Cailletet.Hr. Cailletet
ließ sich diese Verfahrungsarten im J. 1854 für Frankreich patentiren.
Aus dem Bulletin de la Société de l'Industrie
minérale, T. I p. 473.
Mit Abbildungen auf Tab.
VI.
Cailletet, über die Verwandlung der vegetabilischen
Brennmaterialien in Gas zur Stabeisenfabrication.
Man hat in der letzten Zeit viele Versuche in der Absicht angestellt, die
vegetabilischen oder die mineralischen Brennmaterialien behufs ihrer Verwendung in
Gas zu verwandeln und dieses dann in geeigneten metallurgischen Apparaten zu
verbrennen. Diese Versuche haben wenigstens in Frankreich noch zu keinem ganz
praktischen Resultat geführt; in einigen Waldbezirken Deutschlands sind hingegen mehrere Gashütten
seit einer Reihe von Jahren in regelmäßigem Betriebe.
Diese Gründe haben mich zur Wiederaufnahme jener Versuche veranlaßt, wobei ich mich
aber ausschließlich auf das Holz beschränkte. Mein Zweck war, die hohe Temperatur,
welche die durch Destillation des Holzes entwickelten Gase, nachdem sie vorher von
den flüssigen Producten als Wasser, Theer etc., befreit wurden, bei ihrer
Verbrennung erzeugen können, zur Stabeisenfabrication zu benutzen.
Einige Proben überzeugten mich von den praktischen Schwierigkeiten, die flüssigen
Producte der Destillation des grünen (oder nur lufttrocknen) Holzes zu verdichten.
Das saure und theerhaltige Wasser wirkt auf die blechernen Canäle ein, welche die
Abkühlung erleichtern müssen, zerstört und verstopft sie; die durch die Dämpfe
entwickelte latente Wärme erhöht in kurzer Zeit die Temperatur der ganzen Leitung
und verhindert eine vollständige Condensation; endlich kann man auch die fühlbare
Wärme, welche die Gase bei ihrem Ausströmen aus dem Generator haben, nicht mehr
benutzen.
Diese Gründe veranlaßten mich statt des ungetrockneten Holzes vollständig
getrocknetes zu vergasen. Ich benutzte bei diesem Theile meiner Versuche die
treffliche Abhandlung Leplay's,Grundsätze, welche die Eisenhüttenwerke mit Holzbetrieb und die Waldbesitzer
befolgen müssen um den Kampf gegen die Hütten mit Steinkohlenbetrieb
erfolgreich führen zu können. Deutsch von E. Hartmann. Freiberg 1854. über die mit Gasen aus gedörrtem Holz (sogenanntem Holzstoff, ligneux) betriebenen Puddel-
und Schweißöfen zu Lippitzbach in Kärnthen.
Die Trocken- oder Darrkammern, welche ich im Folgenden beschreiben werde, sind
nicht ganz nach den theoretischen und ökonomischen Grundsätzen Leplay's eingerichtet. Mein Zweck war übrigens, diese Apparate möglichst
zu vereinfachen. Die Kosten für das Brennmaterial brauchte ich nicht zu
berücksichtigen, da ich meine Trockenkammern mit den aus dem Puddelofen als
Ueberhitze entweichenden Gasen heizte.
Die zu Villotte angewendeten Apparate bestehen:
1) aus Trockenkammern;
2) aus einem Gasgenerator;
3) aus einem Puddelofen und einem Verbrennungsapparat.
Um Wiederholungen zu vermeiden, verweise ich auf die detaillirte Beschreibung der
Apparate am Ende dieser Abhandlung.
Die Dörr- oder Trockenkammern. – Das Holz
wird auf mit Ochsen bespannten Wagen, aus den etwa 5 Kilometer (5/7 deutsche Meilen)
von der Hütte entfernten Hauen herbeigeschafft. Es wird auf dem Boden in 2 bis 3
Meter hohen Haufen aufgeklaftert und bleibt den atmosphärischen Einflüssen so lange
ausgesetzt bis man es wegnimmt; man ladet es alsdann in Wagen, welche in die
Dörrkammern eingefahren werden. Diese Arbeit verrichten zwei Frauen leicht und
schnell, indem sie den Wagen mittelst eines Hakens aus den Kammern herausziehen,
dann beladen und wieder hineinschieben, worauf die Kammer mit einer Thür von starkem
Blech verschlossen wird. Die Zeit des Verweilens der Wagen in den Dörrkammern hängt
nothwendig von dem Feuchtigkeitsgrade des Holzes ab und ist nach den Jahreszeiten
verschieden. Im Sommer reichen 28 bis 30 Stunden hin, während im Winter wenigstens
48 Stunden erforderlich sind. Das angewendete Holz, welches von dem vorjährigen
Abtriebe herrührt, enthält, nach einigen im Januar 1856 angestellten Versuchen, etwa
30 Proc. Wasser, als Durchschnitt verschiedener Stücke, die von verschiedenen
Punkten des Haufens genommen worden waren.
Da der Holzstoff ein sehr pyrophorisches Product ist, so mußte man alle möglichen
Maßregeln ergreifen, um seine Entzündung zu vermeiden, weil dadurch traurige Folgen
herbeigeführt werden könnten. Es wurde daher jeder Wagen von dem andern unabhängig
gemacht, die Kammern erhielten mehrere, durch Scheider von einander getrennte
Abtheilungen, damit sich das Feuer, wenn ein Wagen in Brand geräth, keinem Wagen in
einer andern Abtheilung mittheilen kann. Ereignet sich nun, was jedoch selten
vorkommt, eine Entzündung, so beeilt sich der die Dörrkammern bedienende Arbeiter,
den entzündeten Wagen herauszuziehen und das Feuer mit Wasser zu löschen.
Gleichzeitig vermindert der Puddler die Wärme in der Kammer dadurch, daß er einen
Theil der verbrannten Gase in die Esse entweichen läßt. Beim regelmäßigen Betriebe
der Dörrkammern steigt die Temperatur vom Augenblick des Einbringens des Holzes bis
zu dem des Herausnehmens) sie beträgt alsdann 120 bis 130° C.
Die Arbeiter erkennen den zweckmäßigen Grad des Dörrens an der Farbe des Holzstoffes,
die ins Gelbliche gehen muß, an der Volumverminderung des Holzes und endlich an der
Leichtigkeit womit es zerbrochen werden kann.
Der auf diese Weise präparirte Holzstoff ist nicht ganz wasserfrei. Fünf aus
verschiedenen Kammern und von verschiedenen Stellen weggenommene Stücke gaben, nach
vollständigem Austrocknen in einem Strom trockener Luft von 120° C., in 100
Grammen:
Nr.
1.
3,25
Gr. Wasser
Nr. 2.
6,00
„
Nr. 3.
2,75
„
Nr. 4.
4,12
„
Nr. 5.
4,13
„
Der durchschnittliche Wassergehalt des Holzstoffes in dem Augenblick wo er aus der
Dörrkammer kommt, beträgt daher 4 Proc. Es ist sogar wahrscheinlich, daß diese
Quantität wegen der zu großen Neigung des Holzstoffes die Feuchtigkeit aus der Luft
zu absorbiren, zunimmt. Auch haben wir solche Apparate vorgezogen, die den
Faserstoff nach Maaßgabe seines Verbrauchs liefern, statt solche anzuwenden, die
große Mengen von diesem Product auf einmal liefern, welche man alsdann aufbewahren
muß. Das benutzte Holz besteht gewöhnlich aus:
1/2 Eichenholz,
1/3 Buchenholz,
1/6 Lindenholz und verschiedene andere Sorten.
Man erhält nahezu einen Störe Holzstoff aus einem Störe grünen Holzes.Der Störe der Hüttenbesitzer in der Bourgogne ist ein Prisma von 1 Met. Höhe,
1,50 Met. Länge und 0,66 Met. Breite; es sind dieß die Dimensionen des
Holzes in den Schlägen. Der Störe entspricht übrigens genau dem Volum von 1
Kubikmeter. Die erwähnte Volumverminderung ist zu gering und zu wenig constant, als daß
ich sie schätzen konnte.
Die Gestehungskosten von einem Störe Holzstoff lassen sich wie folgt feststellen:
Ankaufspreis von 1 Störe Holz auf dem
Stamm
3,10 Fr.
Hauerlöhne, im Durchschnitt
0,75 „
Aufklaftern im Walde
0,20 „
Anfuhr im Durchschnitt auf 5
Kilometer
1,25 „
Das Beladen und Entladen der Wagen
0,35 „
Das spalten der dicken Scheite
0,10 „
––––––
Durchschnittskosten auf 1 Störe
Holzstoff
5,75 Fr.
Der Störe Holz wiegt im Mittel 380 Kilogr. und gibt 278 Kil. Holzstoff, also 73
Procent.
Die Gezähereparaturkosten und die Zinsen vom Capital sind auf die Productionskosten
des Roheisens übertragen.
Diese betrugen im Januar 1856 5,75 Fr. Es ist dieß ein Maximum, denn nach dem
Durchschnitt einer Reihe von Jahren nehmen der Ankaufspreis des Holzes und die
Arbeitslöhne merklich ab.
Der Gasgenerator. – Aus den Dörrkammern wird der
Holzstoff auf den Gichtboden des Gasgenerators geschafft, um dort sofort benutzt zu
werden.
Dieser Apparat hat die Form eines Prismas mit länglich viereckiger Basis, welches
nach unten zu etwas zusammengezogen ist. Die Dicke der Brennmaterialschicht beträgt
vom Rost bis zur Oeffnung, durch welche sich das Gas entwickelt, 1,70 Meter.
Nach der Theorie sollte man die Höhe dieses Apparates wesentlich vermindern können;
die vom verewigten Ebelmen mit einem Schachtofen
angestellten Versuche ergaben auch für das 0,44 Met. über der Form aufgefangene Gas
folgende Zusammensetzung:
Kohlensäure
0,31
Kohlenoxyd
41,59
Wasserstoff
1,42
Stickstoff
56,68
Sauerstoff
0,00
––––––––––––
100,00 Volume.
Man ersieht hieraus, daß der Sauerstoff der Luft, nachdem er eine nur 0,44 Met. hohe
Schicht glühender Holzkohlen durchströmte, fast gänzlich in Kohlenoxydgas verwandelt
ist. In unserm Apparat haben wir die Brennmaterialschicht weit stärker gemacht, um
den obern Schichten zu gestatten vor dem Verbrennen alle Feuchtigkeit abzugeben.
Bei ihrem Ausströmen aus dem Generator behalten die Gase eine hinreichend hohe
Temperatur, welche dazu beiträgt, die Verbrennungswärme auf dem Ofenherde zu
steigern. Ihre Temperatur, mit einem Quecksilberthermometer gemessen, welches mit
einer metallenen Hülse umgeben war, betrug:
nach eintägigem Betriebe
285°
C.
nach zweitägigem
Betriebe
300
„
nach fünftägigem Betriebe
265
„
Diese Unterschiede rühren wahrscheinlich von kleinen Wassermengen her, die in dem
Holzstoff enthalten sind und welche durch ihre Verdampfung die Temperatur des Gases
vermindern.
Es war von Interesse, durch Versuche zu ermitteln, ob die Gase bei ihrem Ausströmen
aus dem Generator noch beträchtliche Mengen von Wasser und Kohlensäure enthalten.
Nachdem der Generator seit zehn Tagen im Betriebe war, lieferte mir 1 Liter
trockenen Gasts von 0° und 0,760 Met. Druck:
Kohlensäure
1,077
Gr.
Wasser und
Theer
0,132
„
Diese Zahlen weichen wenig von denen ab, welche man bei der Analyse der Producte von
der Destillation des Holzes in geschlossenem Gefäße erhält; sie zeigen ferner, daß
in unserm Apparat nur ein sehr unbedeutender Theil des Kohlenstoffs in ein für die
Verbrennung unnützes Gas umgewandelt wird.
Die Verbrennung wird durch einen Strom kalter Luft unterhalten, die ein Zweigrohr des
Ventilators liefert, welcher den Puddelofen speist.
Das Einladen des Holzstoffes geschieht mit Hülfe eines Kastens, welcher über dem
Generator angebracht ist; ein Arbeiter füllt ihn mit gedörrtem Holz, schließt den
Deckel und zieht mit Hülfe eines Hebels die Bodenplatte zurück, worauf das
Brennmaterial niederfällt. Man sieht, daß bei diesem Apparat während des Chargirens
nur geringe, etwa dem Volum des Kastens gleiche Gasmengen verloren gehen können. Man
chargirt alle acht Minuten; übrigens kann man sich von der Höhe des Holzstoffes im
Generator überzeugen, indem man den Schieber etwas öffnet, so daß man mit einer
hölzernen Stange die obere Seite der letzten Charge berühren kann. Wenn man
Reisigbündel anwendet, so packt man sie auf den Boden des gußeisernen Kastens, und
bedeckt sie mit einer gleichen Gewichtsmenge Holzstoff, um ihren Niedergang zu
erleichtern.
Aus dem Generator strömen die Gase abwärts durch einen Canal, der aus einer dicken
Ziegelsteinmauerung besteht, damit Wärmeverluste vermieden werden. Sie gelangen auf
diese Weise zum Fuß des Puddelofens, in eine Kammer oder einen Canal, dessen
Querschnitt doppelt so groß ist wie der des Canals durch welchen sie einströmen. In
dieser Kammer, wo sie ihre Geschwindigkeit verloren haben, hinterlassen sie den
Staub, welchen sie mit sich führten; durch eine mit Ziegelsteinmauerung
verschlossene Oeffnung reinigt man diesen Raum alle vierzehn Tage.
Der Puddelofen. – Dieser ist nach Art der in der
Champagne üblichen construirt; er hat nur eine Arbeitsthür, allein auf den
Arbeitsherb folgt ein zweiter, auf welchem das Roheisen vorgewärmt wird; der
Verbrennungsapparat, welcher den Rost ersetzt, gibt dem Ofen ein von den
gewöhnlichen abweichendes Ansehen.
Letzterer Theil des Ofens ist so eingerichtet, daß der Gasstrom sich genau mit den
dünnen Strömen warmer Luft, welche durch die Formen eingeführt werden, vermischt.
Dieß ist bekanntlich eine nothwendige Bedingung, um das Maximum der Temperatur
hervorzubringen. Die Luft erwärmt sich in zwei gußeisernen Röhren, welche eine
Heizoberfläche von zwei Quadratmetern haben und hinter dem Vorwärmeherde angebracht
sind; an den Formen gemessen, zeigt die Gebläseluft eine Temperatur von 170 bis 200° C. Es würde
aber vortheilhaft seyn, diese Temperatur auf 250 oder 280° C. erhöhen zu
können.
Die Pressung des durch den Ventilator eingeblasenen Windes, in der Nähe der Formen
gemessen, beträgt nur einige Centimeter Wassersäule. Das Volum der einströmenden
Luft regulirt der Puddler sehr leicht durch ein Register, so daß er in jedem
Augenblick die höchste Wärme hervorbringen kann, indem er in den Ofen die zur
Verbrennung der Gase genau erforderliche Luftmenge einführt.
Die Form besteht aus einem gußeisernen Cylinder, welcher mit blechernen Mäulern
versehen ist, die senkrecht auf der Hauptachse stehen. Nach mehreren Versuchen sind
wir bei dieser schon auf dem Harze angewendeten Gestalt der Form stehen geblieben;
sie gestattet den Strömen warmer Luft und dem Gase, sich in geringer Entfernung von
der Form zu vermischen.
Wenn man den Apparat in Betrieb setzt, so erwärmt man ihn, indem man den Generator
mit grünem Holze chargirt; der Puddelofen füllt sich mit schwarzem Rauch an, der
sehr scharf ist und Wasser auf allen kalten Gegenständen absetzt; man gibt etwas
Wind und das Gas entzündet sich, indem man brennende Späne in den Ofen wirft.
Mit grünem Holz kann man jedoch die Ofenwärme nicht über die Kirschrothhitze bringen;
alsdann chargirt man aber mit Holzstoff, worauf der Ofen schnell weißglühend wird.
Es sind im Durchschnitt zehn bis zwölf Stunden erforderlich, um den Ofen auf die
hinreichende Temperatur zu bringen. Die Flamme ist weiß, die Ofenwände sind blendend
und man kann in kurzer Zeit die auf der Arbeitssohle liegenden Eisenstückchen
zusammenschweißen.
Alsdann wird die bereits auf dem hintern Ofenherd vorgewärmte Roheisencharge
eingesetzt; sie besteht aus 175 Kilogr. oder 350 Zollpfund weißem und grauem
Roheisen. Dasselbe schmilzt in kurzer Zeit nieder und wird dann, wie bei dem
gewöhnlichen Puddelproceß, zerschlagen und umgerührt. Die Puddler haben
hauptsächlich darauf zu sehen, daß die Temperatur während dieser ersten
Betriebsperiode nicht zu sehr gesteigert wird.
Während dieser Zeit blähet sich das Roheisen in Folge der Gasentwickelung auf; hört
diese Volumzunahme auf, so sagt man, daß das Eisen gestiegen sey und es beginnt
alsdann die Arbeit mit einer scharfen Brechstange; in dieser Periode bilden sich
auch Eisentheilchen, die man durch ihre weiße Farbe unterscheiden kann.
Man muß die Eisenmasse zwei- oder dreimal durcharbeiten, d.h. sie mit der
Brechstange heben, um die mit der Sohle in Berührung gebliebenen Theilchen, die minder warm als
die übrigen sind, der Einwirkung der Hitze auszusetzen.
In diesem Zeitpunkt des Betriebes muß der Ofen auf die höchste Temperatur gebracht
werden, wozu es erforderlich ist, den Rost des Generators zu reinigen und recht viel
Luft unter denselben einströmen zu lassen; das Zusammenschweißen der Luppen
geschieht in dem Maaß als das Zängen ausgeführt wird, welches unter einem
Aufwerfhammer geschieht.
Wir stellen hier die verschiedenen Perioden des Puddelns zusammen:
das Chargiren des Roheisens
5 Minuten
das Erhitzen und Zerbrechen
desselben
15 „
die Arbeit mit dem Haken
35 „
die Arbeit mit der Brechstange
15 „
Temperatursteigerung und Zängen
15 „
–––––––––––––––––
1 Stunde
25 Minuten.
Bei dieser Uebersicht sind jedoch weder vorkommende Betriebsstörungen noch
Ofenreparaturen berücksichtigt.
Durchschnittlich macht man in zwölf Stunden acht bis zehn Chargen, wobei man ein
Gemenge von weißem und grauem Roheisen benutzt, welche mit Holzkohlen und kalter
Luft erblasen worden sind.
Das in dem Hohofen zu Villotte benutzte Erz ist ein ziemlich feinkörniger
Brauneisenstein, sogen. Bohnerz aus dem Oxfordthon (Kelloway-Gestein) und man
unterscheidet zwei Varietäten. Das graue Erz, welches Versteinerungen enthält und
phosphorhaltig ist, wird in der Nähe der Hütte gegraben; das rothe Erz wird in
Gruben gewonnen und ist sehr rein. Als Zuschlag und zur Sättigung des kalkigen Erzes
wendet man ein feinkörniges, durch eine kieselige Gangart verbundenes Erz aus dem
Aube-Departement an.
Der Roheisenverbrauch ist fast derselbe wie bei dem gewöhnlichen Puddeln mit
Steinkohlenflamme. Das erzeugte Stabeisen ist wesentlich besser als das in den
Bourgogne'schen Frischfeuern zu Villotte aus demselben Roheisen dargestellte. Die
Producte des Gasofens haben außerdem den wesentlichen Vorzug einer sehr regelmäßigen
Qualität, welche bei den Frischfeuern niemals erzielt wird. Die
Brennmaterialersparung ist bedeutend, wenn man die Kohlenmenge, welche 2,55 Stören
Holzstoff entspricht und zu 1000 Kilogr. Luppeneisen oder Masseln erforderlich ist,
mit der Kohlenmenge vergleicht, welche in Comtéfeuern verbrannt wird, in
denen man nur Luppenstücke erzeugt. Man wird die Vortheile, welche der Holzstoff
gegen die Holzkohlen gewährt, leicht begreifen, wenn man die Zusammensetzung des
grünen Holzes in Betracht zieht, welche folgende ist:
Kohle und
Asche
17,5
Gase
26,6
flüssige Producte
55,9
–––––
100,0
Man sieht, daß man bei der Benutzung des Holzstoffes die Wärme gewinnt, welche die
Verbrennung der Gase liefert, die in der Kohle nicht mehr vorhanden sind.
Der Generator wird entweder mit Holzstoff allein oder zur Hälfte mit diesem und zur
Hälfte mit Reisigbündeln gespeist. Die Erfahrung hat gezeigt, daß sich gleiche
Gewichtstheile von dem einen oder dem andern ersetzen können.
Die Productionskosten für 1000 Kil, Luppenstücke betragen in beiden Fällen:
RoheisenDieser geringe Roheisenabgang rührt daher, daß das Luppeneisen nach
dem Zangen noch sehr viel Schlacken enthält, daher der
Schweißofenabgang sehr bedeutend ist. 1020 Kil. à 195 Fr. die 1000
Kil.
198,90 Fr.
Holzstoff. 2,55
Stère à 5,75 Fr.
14,65 „
2 Puddler à 1,50 Fr.
3,00 „
2 Gehülfen à 1,25 Fr.
2,50 „
2 Roheisenzerschläger à 1,10 Fr.
2,20 „
Diese
Arbeiter werden auf die 1000 Kilogr. gelohnt.
2 Tagelöhner zur Bedienung des Generators
à 1,50 Fr.
3,00 „
Gezäheunterhaltung
0,60 „
unvorhergesehene Kosten
1,75 „
nimmt man an. daß täglich 3000 Kil.
Luppenstücke fabricirt werden, so hat
man auf 1000 Kil. ein Drittel der
obigen Kosten mit
1,80 „
auf Amortisation der Anlagekosten
0,75 „
Zinsen vom Betriebscapitale
3,25 „
––––––––
Es kommen daher 1000 Kil. Luppenstücke zu
stehen auf
227,05 Fr.
Wenn man Reisig und andere zu Bündeln vereinigte
Holzabgänge benutzt, so ersetzt man die Hälfte des Holzstoffes durch 80 Bündel, von
denen 100,2 Fr. statt 7,30 Fr. kosten. Die Brennmaterialkosten betragen alsdann im
Ganzen nur 9,30 Fr. auf 1000 Kil. Luppenstücke und die Kosten auf dieselben
vermindern sich alsdann auf 221,70 Francs.
Das mit Gasen gepuddelte Eisen ist dicht, fadig, sehr fest und läßt sich gleich gut
in der Hitze und kalt verarbeiten. Es muß natürlich besser seyn, als das mit
Steinkohlen dargestellte, weil man die Einwirkung der geschwefelten Gase vermeidet,
welche bei dieser Temperatur eine große Neigung haben sich mit dem Eisen zu
verbinden. Aber auch Flugasche und Kohlenschiefern, welche in das Roheisenbad gelangen,
verringern die Güte des Eisens.
Zu Villotte wird das im Gasofen erzeugte Puddeleisen ausschließlich zur Fabrication
weichen Bleches angewendet. Die Luppenstücke werden zu zweien übereinander gelegt,
ausgeschweißt, kommen dann zum Zangen unter einen Stempelhammer und werden zu 0,14
Met. breiten Stürzen ausgewalzt, welche man mittelst der Schere zu Stücken von
zweckmäßiger Länge zerschneidet. Das daraus dargestellte Blech ist weit besser als
das aus Herdfrischeisen dargestellte.
Besondere Güte und Gleichartigkeit sind die wesentlichen und sehr schätzbaren
Eigenschaften des mit Holzgasen erzeugten Eisens, während, wie jeder Hüttenmann
weiß, das Herdfrischeisen im Allgemeinen ungleichartig ist. Ein anderer Vortheil
welchen diese Methode gewährt, ist der, daß man dabei die Abfälle in den Hauen
benutzen kann, welche nur den Fuhrlohn nach der Hütte tosten.
Beschreibung der Abbildungen.
Dörrkammern und Wagen zum Dörren des Holzes (Fig. 7 bis 9).
Fig. 7
horizontaler Durchschnitt der Dörrkammern.
Fig. 8
senkrechter Durchschnitt derselben nach der Linie XY der Fig. 7, nebst der Seitenansicht eines Wagens, der mit grünem Holze
beladen in die Kammer eingefahren und mit dem gedörrten herausgefahren und entladen
wird.
Fig. 9
Endansicht des Wagens.
A, A die aus rothen Ziegelsteinen erbaueten Dörrkammern;
die Scheidewände H, H bestehen aus auf die hohe Kante
gestellten Ziegelsteinen und theilen die Kammer in 14 Abtheilungen, von denen jede
einen Wagen aufnimmt.
C, C Schließkeile von Walzeisen, welche durch die Enden
der runden Ankerstangen B, B und die Gewölbe
zusammenhalten.
F, F flacheiserne Stäbe, welche die Bekleidungen der
blechernen Thüren bilden.
R, R auf die hohe Kante gestellte Eisenstäbe, welche als
Schienen dienen; jeder Stab ist einerseits in das Mauerwerk eingelassen und wird
anderseits außerhalb desselben mittelst Keilen in einem hölzernen Schwell r, r festgehalten.
G, G gußeiserne Röhren, durch welche die als Ueberhitze
aus dem Ofen entweichenden Gase strömen um Wärme abzugeben.
H, H Scheidewände, welche aus auf die hohe Kante
gestellten Ziegelsteinen aufgeführt sind und verhindern, daß die Entzündung eines
Wagens sich den folgenden Wagen mittheilt.
P Esse von 12 Meter Höhe; sie saugt die verbrannten
Gase, nachdem dieselben den Apparat verlassen haben, an und verhindert deren
Ausströmen durch die Arbeitsthür des Puddelofens.
U, U eiserner Wagen, auf welchen das grüne, zu dörrende
Holz geladen wird; bloß die Räder des Wagens sind von Gußeisen. Jede Kammer ist mit
einem solchen Wagen versehen, dessen Gewicht 47 Kil. beträgt. – Die aus den
Hauen angefahrenen Holzscheite sind 0,66 Met. lang.
Gasgenerator (Fig. 10 und 11).
Fig. 10
senkrechter Durchschnitt des Generators und des Puddelofens nach der Linie X'Y' der Fig. 7.
Fig. 11
senkrechter Durchschnitt von dem obersten Theil des Generators nach der Linie I, II
der Fig.
7.
h, h die Wände des Generators, aus rothen Ziegelsteinen
aufgeführt und inwendig mit feuerfesten Ziegelsteinen bekleidet.
m, n gußeiserne Träger für den aus Flächen Stäben
bestehenden Rost.
t Aschenfall mit einer blechernen Thür. Man verschließt
diese Thür und läßt durch die Röhre s Gebläsewind
einströmen, sobald die Temperatur im Puddelofen gesteigert werden soll.
n, n länglich-viereckiger gußeiserner Kasten zum
Einführen des gedörrten Holzes in den Generator.
f blecherner Deckel, welchen man im Augenblick des
Chargirens verschließt.
l auf Leisten verschiebbare gußeiserne Platte, wodurch
man den Kasten n, n unten verschließen und öffnen
kann.
g eiserner Hebel, womit die Platte l gehandhabt wird.
j, j gußeiserne Deckplatte der obern Seite des
Generators, auf welcher der Kasten n, n steht.
K Canal, durch welchen die brennbaren Gase in den
Puddelofen gelangen; dieser Canal mündet an der Basis des Puddelofens in den
Behälter oder die Kammer W aus, mit der er durch die
Oeffnung z, z in Verbindung steht.
Puddelofen (Fig. 7 und 12).
Fig. 12
senkrechter Durchschnitt desselben nach der Linie III, IV der Fig. 7.
z, z Eintritt der Gase in den Puddelofen.
L Behälter von größerm Querschnitt als z, z; die Gase setzen darin den Staub und die anderen
mitgerissenen Substanzen ab.
M gußeiserne, um ihre Achse drehbare Form; zur
Erleichterung dieser Bewegung tritt die Röhre N, welche
die erwärmte Gebläseluft herbeiführt, nur durch Reibung in die Oeffnung der
Form.
o, o, o sieben conische Formmäuler aus starkem Blech;
sie sind zur Verhinderung ihrer Oxydation mit Lehm beschlagen, und man kann sie
leicht auswechseln, da sie nur durch Reibung in der Form M befestigt sind.
p, q, x, y vorderer Theil des Ofens, wo die brennbaren
Gase mit der Gebläseluft vermischt werden.
O Canal, durch welchen Luft zur Abkühlung des Mauerwerks
strömt.
Q große Feuerbrücke, durch eine senkrecht gestellte
dicke gußeiserne Platte gebildet.
J kleine Feuerbrücke, aus Ziegelsteinen bestehend.
E, E gußeiserne Herdplatte, auf welcher die Arbeitssohle
aus Eisenoxyd hergestellt wird.
D gußeiserne Arbeitsthür des Ofens, auf der inneren
Fläche mit feuerfesten Ziegelsteinen bekleidet.
E', E' Sohle des hintern Ofens zum Vorwärmen des
Roheisens.
D' Arbeitsthür dieses Ofens.
k, k gußeiserne Röhren zum Erwärmen der durch die Formen
einströmenden Gebläseluft.
Die von einem Ventilator gelieferte Luft erhitzt sich in den Röhren k, k und wird dann durch die blecherne, mit Lehm
beschlagene Röhre N in die Form geleitet.
Tafeln
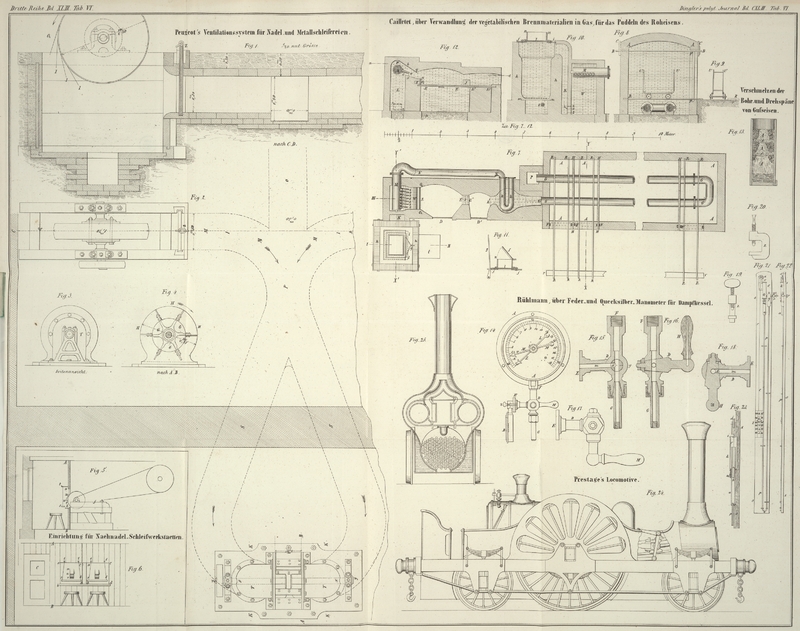