Titel: | Rauchverzehrender Herd mit ununterbrochener Selbstschürung, von Hrn. Tenbrinck, Ingenieur bei der französischen Ostbahn. |
Fundstelle: | Band 150, Jahrgang 1858, Nr. LI., S. 188 |
Download: | XML |
LI.
Rauchverzehrender Herd mit ununterbrochener
Selbstschürung, von Hrn. Tenbrinck, Ingenieur bei der französischen Ostbahn.
Aus den Annales des Mines, 1858, t. XIII p.
175.
Mit Abbildungen auf Tab.
IV.
Tenbrinck's rauchverzehrender Herd mit ununterbrochener
Selbstschürung.
Die ursprüngliche Idee oder der Ausgangspunkt bei dem vorliegenden Ofen oder Herd ist
die Anwendung eines hinreichend geneigten Rostes, daß das Brennmaterial durch sein
eigenes Gewicht abwärts geht und die Schürung eine ununterbrochene wird.
Diese Anordnung ist alt und bekannt, auch öfters benutzt worden; ich habe sie
angenommen und vervollständigt, um zu einer rationellen und rauchfreien Verbrennung
zu gelangen.
Der in Fig. 7
bis 10
dargestellte Apparat ist an einem von den beiden Kesseln der vierpferdigen
Dampfmaschine angebracht, welche eine Pumpe zum Speisen des großen Wasserbehälters
auf dem Bahnhofe zu Metz betreibt. Der Apparat und der Herd sind zwischen zwei
Wänden von feuerfesten Ziegelsteinen angeordnet, die am vordern Theil des Ofens
hervortreten. Das Brennmaterial schürt sich selbst ein und sinkt auch von selbst in
den geneigten Aufschütter A, A hinab, welcher über dem
Rost C, C und in der Verlängerung desselben angebracht
ist.
Die Dicke der in den Herd niedergehenden Brennmaterialschicht hängt von der Oeffnung
oder von der Entfernung der Wände f, f und d, d des Aufschütters ab. Das Ziegelsteingewölbe B, B begränzt den Herd an seinem obern Theil.
Die hintere Seite des Aufschütters ist von der Ofenwand so weit entfernt, daß ein
freier Raum D, D bleibt, welcher für den Zutritt der
Luft hinreicht.
Eine Oeffnung b, welche sich über die ganze Breite des
Herdes erstreckt, läßt die Luft parallel mit dem Aufschütter einströmen und bringt
sie in unmittelbare Berührung mit dem frischen Brennmaterial im Augenblick seiner
Entzündung; diese Oeffnung ist mit einer Klappe c
versehen, welche das Volum der einströmenden Luft nach Belieben zu reguliren
gestattet.
Die massive Wand f, f, auf welcher das Brennmaterial
hinabgleitet, reicht weiter hinab als der Scheider d, d,
welcher das Brennmaterial von der Luft trennt.
In Folge dieser Anordnungen entzündet sich der Vordertheil der in den Herd
niedersinkenden Brennmaterialschicht bei ihrem Austritt aus dem Aufschütter mit
Beihülfe der durch den Canal b zuströmenden Luft. Hinter
der entzündeten Schicht k, k destillirt die Kohle unter
dem Einfluß der Wärme. Die durch die Destillation erzeugten Gase verbinden sich mit
dem Sauerstoff der durch den Zug der Esse angesaugten Luft; dieses, mit
Kohlentheilchen, welche den Hauptbestandtheil des Rauchs bilden, beladene Gemisch
durchströmt die Schicht k, k, welche mit einer hohen
Temperatur verbrennt; die Gase entzünden sich alsdann und die Kohlentheilchen
verschwinden, indem sie entweder mechanisch zurückgehalten oder verbrannt werden.
Die Destillation dauert fort und schreitet als unterwärts gehende vor, die Kohle
verliert ihren Zusammenhang und läßt ihre gasförmigen Theile fahren; letztere können
aber nicht anders als die Schicht k, k oder das glühende
Brennmaterial durchstreichend, entweichen, und dieses läßt nur vollkommen reine und
rauchfreie, entzündete Gase hindurch.
Weiter unten fährt das, fast allen Kohlenwasserstoffes beraubte Brennmaterial mit
Hülfe des Sauerstoffes der durch den Rost einströmenden Luft zu brennen fort. Der
feste Theil, die Kohks, vermindern sich immer mehr bis zum Fuße des Rosts, wo man
keine anderen Rückstände als Asche, Schiefer und Schlacken findet. Diese Rückstände,
welche sich unter dem Rost angehäuft haben, entfernt man sehr leicht durch den
freien Raum M, M.
Die Linie mn bezeichnet annähernd die Trennung der
destillirenden Kohle von derjenigen, welche, weil sie schon rothglühend ist, die
rauchbildenden Elemente abgegeben hat; über dieser Linie erfolgt die Destillation
und unter ihr die Verzehrung des Brennmaterials.
Wenn die durch die Klappe c in den Herd einströmende Luft
kalt ist, so vermindert man die Oeffnung der Klappe der Art, daß nur etwas mehr Luft
einzieht, als zur Entzündung der Fläche k, k der
Brennmaterialschicht erforderlich ist. Läßt man die Klappe c zu weit herab, oder verschließt man sie, so fehlt es an Luft und es erscheint sofort
Rauch, das sichere Zeichen einer schlechten Verbrennung.
In dem Kesselofen, mit welchem die Versuche angestellt wurden, wendet man warme Luft
an; man fängt sie vor dem Rost auf, wo sie schon erwärmt ist und Canäle h, h, h führen sie dann in die Wände des Herdes, wo sie
sich immer mehr erhitzt. Von da wird sie durch zwei Kniee P,
P in den verschlossenen Raum D geleitet, aus
welchem sie durch die Klappe c in den Ofen gelangt. Im
Vergleich mit der Anwendung kalter Luft gewährt die warme einen wesentlichen
Vortheil, welcher aber noch viel größer wäre, wenn man die Luft noch stärker
erwärmen würde. Während meiner Versuche betrug die mittlere Temperatur der Luft
230° C.
Die Roststäbe und der Scheider f, f sind an der Traverse
J, J befestigt. Dreht man die Schrauben, welche
letztere tragen, so wird die Wand f, f von dem Scheider
d, d entfernt oder ihm genähert und dadurch die
Dicke der Brennmaterialschicht, welche in den Herd hinabgeht, vergrößert oder
vermindert. Der Zustand und die Qualität der Steinkohlen, als Stück-,
Würfel- oder kleine Kohlen, als fette oder magere Kohlen, so wie der stärkere
oder schwächere Zug der Esse, bedingen eine verschiedene Dicke der
Brennmaterialschicht, um den besten Effect zu erzielen. Bei gutem Zuge verbrennt man
Stückkohlen sehr gut in Schichten von 20 bis 25 Centimet. (8 bis 10 Zoll); während
man bei kleinen Kohlen die Schicht nicht dicker als 6 bis 8 Centimet. (2 1/2 bis 3
Zoll) machen darf.
Die Luft, welche die Verbrennung unterhält, gelangt vor den Rost, indem sie in den
Kasten L, L einströmt, welcher den Wärmeverlust durch
das Ausstrahlen des Herdes verhütet und die Luft bei ihrem Durchströmen zu erwärmen
beginnt. Die Klappe l, l unten am Kasten dient weniger
dazu, den Eintritt der Luft zu reguliren, als deren Zutritt zu verhindern, wenn man
den Gang des Ofens aufhält. Der Kasten L, L ist an zwei
Ketten aufgehängt, die mit Gegengewichten versehen sind; man läßt ihn nieder, um den
Rost zu untersuchen und zu reinigen, und man zieht ihn auf, wenn die Asche nebst
anderen Rückständen aus dem Aschenraum entfernt werden soll.
Der Gang des Herdes wird einzig und allein durch das Register regulirt; dieses
einfache Mittel ist in allen Fällen ausreichend.
Mit unbedeutenden Abänderungen der Anordnung läßt sich dieses System auch für die
Kessel der Locomotiven und Schiffsdampfmaschinen anwenden.
Es wurden mit beiden Kesseln der erwähnten Dampfmaschine vergleichende Versuche
angestellt. Da diese Maschine eine Pumpe betreibt, welche das Wasser in einen
Behälter hebt, so ist der Widerstand constant, wenn die Geschwindigkeit sich nicht
ändert.
Beide Kessel sind einander ganz gleich, der eine wird mit meinem Apparat geheizt, der
andere mit einer gewöhnlichen Rostfeuerung, die sich in gutem Zustande befindet.
Die beiden Oefen gemeinschaftliche Esse hat einen innern Durchmesser von 0,40 Meter
und eine Höhe von 12 Meter.
Jeder Kessel ist mit nur einer Siederöhre versehen.
Die Räumlichkeit eines solchen Kessels
beträgt
1,246 K. M.
die Heizfläche beträgt
4,835 Q. M.
der gewöhnliche Rost hat eine Fläche von
0,036 „
diejenige des rauchverzehrenden Herdes ist
0,325 „
Die Speisepumpe saugte das Wasser aus einem geaichten Behälter an, daher man im
Stande war, die Menge des verdampften Wassers zu bestimmen, indem man von einem
festen Punkte des gläsernen Wasserstandszeigers ausging.
Die Steinkohlen von Saarbrücken sind sogenannte Förderkohlen, d.h. ein Gemenge von
Stück- und Kleinkohlen; eine Separation, um mit jenen allein zu feuern, hielt
ich nicht für zweckmäßig; man würde aber dadurch offenbar eine günstigere
Verdampfung erlangt haben.
Bei dem gewöhnlichen Ofen blieb das Register fast immer vollständig geöffnet;
dasjenige des rauchverbrennenden Ofens war fast immer nur um ein Sechstel seines
Durchschnittes geöffnet.
Man verbrannte auf dem Quadratdecimeter Rostfläche nachstehende
Steinkohlenmengen:
1. Reihe.
2. Reihe.
3. Reihe.
Rauchverzehrender Ofen
1,04 Kil.
0,83 Kil.
8,88 Kil.
gewöhnlicher Ofen
1,19 „
0,88 „
–
Vergleichende Uebersicht der
Versuchsresultate.
Textabbildung Bd. 150, S. 192
Nummern der Versuchsreihe; Daten;
Dauer des Ganges der Maschine; Anzahl der Umgänge der Maschine in einer Minute;
Gesammtmenge der verbrannten Kohle; Rauchverzehrender Herd; Gewöhnlicher Herd;
Menge des verdampften Wassers; Menge des per Kilogr.
Steinkohle verdampften Wassers; Bemerkungen; April; Mittel; Stund.; Umg.; Kil.;
Liter
(a) Angewendete Steinkohlen
2/3 Kleinkohlen1/3 Stückkohlen zu Saarbrücken.
von der Grube v. d. Heydt
Temperatur des Speisewassers, 5° C.
Dicke der Steinkohlenschicht in dem rauchverzehrenden Herde, 65 Millimeter.
Die am 6. verbrauchte Kleinkohle war etwas besser als die vorhergehende, sie enthielt
etwas Stückkohlen.
Schwacher Rauch während 20 Minuten beim Anfeuern des rauchverzehrenden Ofens.
Deßgleichen schwacher Rauch während des Reinigens des Rostes, welches täglich dreimal
vorgenommen wurde. – Zu der übrigen Zeit gar keine Rauchbildung.
(b) Steinkohlen
2/3 Stückkohlen von der Heinitzgrube bei Saarbrücken.1/3 alte
Kleinkohle.
Am 14. April gehinderter Betrieb, die Speisepumpe gab nicht genug Wasser, daher man
am Ende des Tages den Wasserstand im Kessel nicht unterhalten konnte.
Temperatur des Speisewassers, Dicke der Steinkohlenschicht und Rauch wie bei den
vorhergehenden Versuchen.
Am 12., 13. und 14. hatte man den ganzen Tag über nicht nöthig den Rost zu reinigen;
die Verbrennung war ganz rauchfrei.
(c) Steinkolhen
2/3 Stückkohlen von der Heinitzgrube.1/3 alte Kleinkohlen.
Dicke der Kohlenschicht, 120 Millimeter.
Uebrigens dieselben Beobachtungen.
Bis jetzt betrug die lebhafteste Verbrennung des neuen Herdes 1,50 Kilogr.
Steinkohlen per Quadratdecimeter in der Stunde.
Da die zweite Versuchsreihe kein so günstiges Resultat für den neuen Ofen ergab als
die erste, und mit Grund zu glauben ist, daß die Brennmaterialschicht nicht
hinreichend dick war, so wurden zwei neue Versuche mit derselben Steinkohle
angestellt, dabei aber die Dicke der Schicht von 65 auf 120 Millimeter gebracht. Die
Verdampfung stieg dann von 6,154 auf 6,275 Kilogr. per
Kilogramm Steinkohle. Bei einem aus 2/3 Stück- und 1/3 Kleinkohlen
bestehenden Brennmaterial dürfte die Dicke der Schicht mit Vortheil auf 0,15 Meter
gebracht werden; bei Anwendung von Stückkohlen allein müßte man sie zur Erlangung
besserer Resultate noch stärker machen. Die erste Versuchsreihe wurde mit sehr
schlechten Kleinkohlen, wie man sie im Handel gar nicht findet, ausgeführt, weil
damals keine anderen Kohlen verfügbar waren.
Im Mittel betrug der Vortheil, welchen mein Herd gegen den andern gewährte, 17,2
Proc.; ich muß aber bemerken, daß der gewöhnliche Herd, mit welchem ich zu
concurriren hatte, von ausgezeichneter Beschaffenheit war, sein Ergebniß in der
zweiten Versuchsreihe (5,225 Kil. Wasser per Kilogr.
Steinkohle verdampft) ist wahrhaft außerordentlich.
Das Resultat von 6,214 Kilogr. Wasser per Kilogr.
Steinkohle verdampft, welches sich als Mittel von den mit gewöhnlichen Saarbrücker
Kohlen angestellten Versuchen herausstellte, ist meines Wissens bisher mit keinem
andern Ofen erreicht worden.
Der in Fig. 7
bis 10 im
Grundriß, Aufriß und in mehreren Durchschnitten dargestellte Apparat ist von Eisen
und Blech construirt; die neueren Apparate werden hingegen fast gänzlich aus
Gußeisen bestehen, einfacher und leichter aufzustellen seyn.
Der Gang dieses Herdes regulirt sich mit der größten Leichtigkeit; nachdem die mit
seiner Prüfung beauftragte Commission ihn mehrere Tage im Betriebe gesehen hatte,
erklärte sie in ihrem Berichte, daß die Leitung des Feuers eben so leicht wie bei
den gewöhnlichen Rosten ist.
Es werden gegenwärtig mehrere Oefen dieser Art ausgeführt, einer davon für eine
Locomotive.
Tafeln
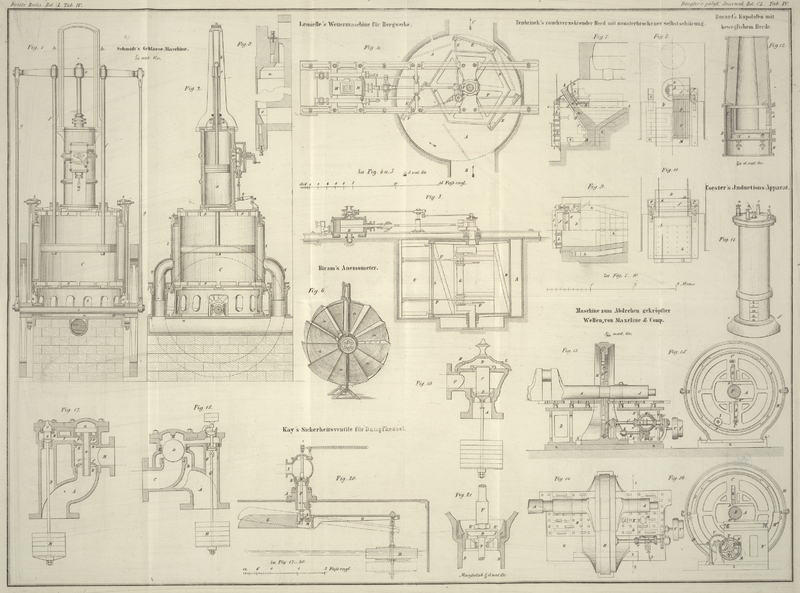