Titel: | Ueber den Brand der Stückkohlen in Locomotiven, über Kohlenwäsche und Herstellung von Kohlenpreßziegeln, sogenannten Briquetts oder Peras; vom Eisenbahnbau-Inspector Reder. |
Fundstelle: | Band 159, Jahrgang 1861, Nr. VIII., S. 28 |
Download: | XML |
VIII.
Ueber den Brand der Stückkohlen in Locomotiven,
über Kohlenwäsche und Herstellung von Kohlenpreßziegeln, sogenannten Briquetts oder
Peras; vom Eisenbahnbau-Inspector Reder.
Aus der Zeitschrift des hannoverschen Architekten- und
Ingenieur-Vereins, 1860, Bd. VI S. 161.
Mit Abbildungen auf Tab.
I.
Reder, über Herstellung von Kohlenpreßziegeln, sogenannten
Briquetts oder Peras.
Bekanntlich hängt die Ausbeute an Kohks sowohl vom Kohlenstoffgehalte der
Steinkohlen, wie von der Construction der Kohksöfen ab, und sind im großen
Durchschnitt die Productionsverhältnisse als sehr günstig
anzusehen, bei denen sich eine Kohksausbeute von 75 Procent herausstellt.
Der durch den Verkohkungsproceß, und zwar in Folge des Entweichens der flüchtigen
Bestandtheile der Kohlen, unvermeidlich auftretende Verlust beträgt demnach etwa 25
Procent des Gewichts der Kohlen, und begründet dieser Verlust vorzüglich den höhern
Preis der Kohks.
Vom Mehrpreise der Kohks gegen Kohlen kommen auf den Gewichtsverlust 90 bis 93
Procent, auf Arbeitslöhne 2 bis 3 Procent und endlich auf Insgemeinkosten, als
Oefen- und Geräthe-Reparaturen, Aufsichtskosten und Verzinsung des
Baucapitals der Rest von 5 bis 6 Procent.
Abgesehen von dem durch zweckmäßige Ofenconstructionen und gute Aufsicht zu
vermeidenden Verluste, welcher durch Verflüchtigung eines Theiles des Kohlenstoffes
bei zu großer Gluth der Oefen eintritt, entweichen bei dem gewöhnlichen
Kohksprocesse mit den schädlichen zugleich auch nützliche Gase (Kohlenwasserstoff
und ölbildendes Gas), welche, wenn sie in den Kohks verblieben, den Heizeffect
erhöhen würden.
In besonderer Würdigung dieser mit der Verkohkung untrennbar verbundenen Mißstände
ist die rohe Kohle als Heizmaterial für stehende Maschinen schon immer angewandt,
während einer gleichen Verwendung derselben für Locomotiven die Befürchtung
entgegenstand, daß durch die schwefligen Gase der Kohlen das innere Werk der
Maschinen (namentlich die Röste und die Siederohre) unzuträglich stark angegriffen
würde.
Erst im Laufe der letzteren Jahre sind Versuche im größeren Maaßstabe mit dem Brande der Kohlen in Locomotiven mit Erfolg
gemacht, und haben dieselben das überraschende Resultat ergeben, daß der schädliche
Einfluß jener Gase, wenn überall bemerkbar, doch sehr gering ist, und derselbe gegen die
bedeutenden Ersparungen, die der Kohlenbrand mit sich bringt, nicht in Anrechnung
gezogen werden kann.
Nachdem es endlich jetzt gelungen ist, den lästigen, mit der Kohlenheizung
verbundenen Rauch durch einfache rauchverzehrende Vorrichtungen fast ganz zu
beseitigen, sind die Kohlen als ein vorzügliches Brennmaterial für Locomotiven
anzusehen und finden als solches gegenwärtig die ausgedehnteste Verwendung.
Wie bedeutend die durch Kohlenfeuerung zu erzielenden Ersparungen sind, ergibt die
Thatsache, daß vorzüglich in Folge der Verwendung der Kohlen, und zwar nur eines
verhältnißmäßig geringen Quantums (etwa 1/3 Kohlen gegen 2/3 Kohks) beim Betriebe
der königlich hannoverschen Eisenbahnen die Kosten für Brennmaterial der Locomotiven
um circa 20 Procent gegen früher herabgedrückt sind.
Backende Kohlen eignen sich zum Brande in Locomotiven besonders deßhalb, weil während
ihres Verbrennens in Folge des eingeleiteten Verkohkungsprocesses ein Zusammenbacken
der einzelnen Kohlentheile stattfindet und dadurch das Durchreißen unverbrannter
Masse durch die Siederohre verhindert wird.
Den Sinterkohlen, mehr aber noch den Anthracitkohlen geht diese Eigenschaft des
Zusammenbackens ab; sie behalten während des Verbrennens nicht allein ihre frühere
geringe Consistenz bei, sondern werden noch durch Ausdehnung des eingeschlossenen
Wassers zersprengt. Diese Kohlenstückchen lagern sich dann entweder auf dem Roste
ab, befördern dort Schlackenbildung und behindern den Luftzug, oder sie werden unverbrannt durch die Siederohre gerissen und fallen in
der Rauchkammer nieder.
Obgleich einige Kohlensorten angenäßt selbst als Feinkohlen in Locomotiven gebrannt werden können, so ist doch allgemein
anzunehmen, daß Stückkohlen die vortheilhaftesten
Resultate geben, und die meisten Kohlen überall nur als Stücke sich zu jenem Brande
eignen.
Leider werden nun aber die Kohlen nur in den wenigsten Gruben als Stücke angehauen,
sie fallen vielmehr zum größten Theile als Grus und nur zum geringeren Theile als
Stücke. Um aus dem Gemisch von Grus und Stückkohlen letztere zu erhalten, muß die
ganze Masse gesiebt (gerostet) werden.
In Folge dieses Siebens häufen sich große Quantitäten Feinkohle neben den Zechen an,
deren Beseitigung und Verwerthung allein durch Briquettirung, d. i. Pressung
derselben zu Kohlenziegeln, zu erreichen ist.
Die Formung von Kohlenziegeln aus der trotz ihres großen Kohlenstoffgehaltes fast
werthlosen Anthracitfeinkohle ist schon sehr alt, und besteht darin, daß der Grus mit Lehm
oder Kalkbrei gemengt und zu handgroßen Stücken, s. g. Kluten geformt wird.
Diese Kluten geben nach ihrer Trocknung an der Sonne ein allerdings billiges, aber
auch schlechtes und, je nachdem Lehm oder Kalk dem Gruse zugesetzt war, ein sehr
stark stäubendes oder sehr stark schlackendes Brennmaterial.
Bei der eigentlichen Briquettirung, welche gleichzeitig von französischen und
englischen Ingenieuren erfunden seyn soll, wird der Feinkohle als Bindemittel
entweder Goudron oder eingedickter Theer zugesetzt, und das Gemisch einem Drucke von
100 Atmosphären unterworfen.
Man unterscheidet drei verschiedene Arten von Briquettpressen:
1) die Stempelpresse von Walschaerts in Brüssel,
2) die Tangential- oder Rad-Presse von Fischer in Brüssel, und
3) die Horizontal- oder Cylinder-Presse von Evrard in Chazotte.Ueber Evrard's Horizontalpresse wurde bereits ein
Bericht im polytechn. Journal Bd. CLIV S.
336 mitgetheilt.A. d. Red.
Die erstere ist eine gewöhnliche Kniehebelpresse. Jedes
Kolbenspiel preßt aus der eingefüllten Mischung ein fertiges Briquett, dessen
Entfernung aus der Form ähnlich wie bei Ziegelpressen beschafft wird. Diese
Briquetts haben eine parallelepipedische Form und wiegen pro Stück 14 Pfd. Die Maschine preßt in der Minute 11 Stück derselben.
Die Tangentialpresse besteht aus zwei in einer Verticalfläche stehenden und auf halber Höhe sich
berührenden, eisernen rotirenden Rädern von 12 bis 16 Fuß Durchmesser, in deren 12
bis 14 Zoll breitem Umfange 20 bis 30 Leeren von der Form der herzustellenden
Briquetts, vertieft ausgespart sind.
Im Scheitel jedes Rades fällt die Briquettmasse durch Rinnen in die einzelnen Leeren,
füllt sie aus, und erfolgt die Pressung in der Berührungsstelle beider Räder. Die
gepreßten Briquetts lösen sich dann wegen ihrer conischen Form bei weiterem
Hinabgange und fallen auf ein untergespanntes, rotirendes Tuch ohne Ende, welches
sie den abnehmenden Arbeitern zuführt. In der Minute werden 38 solcher conischen
Briquetts, jedes 10 Pfd. schwer, hergestellt.
Dem Verfasser war es leider nicht gelungen, sich Eingang in die Briquettfabriken zu
Charleroi und Gosselies, welche mit obengenannten Maschinen arbeiten, zu
verschaffen, und hat derselbe nur eine bei den Maschinenfabrikanten Hallôt und Cail zu
Brüssel im Bau begriffene, aber noch nicht montirte Tangentialpresse oberflächlich
besichtigen können. Dahingegen bot sich Gelegenheit, die dritte Art der Pressen, die
Horizontalpresse zu
Brandeisl in Böhmen, im Betriebe zu sehen, die
hauptsächlichsten Dimensionen aufzumessen und die Details der Briquettfabrication zu
studiren.
Da die Briquettfabrik zu Brandeisl, einer Station der Bahn
von Prag nach Kladno, welche bei Kralup aus der Dresden-Prager Bahn abzweigt,
den Briquettirungsproceß vom Beginne der Kohlengewinnung bis zur Ablieferung der
fertigen Briquetts im fortlaufenden Bilde zeigt, mehrere Besonderheiten der dortigen
Verhältnisse aber auf den Gang der Fabrication nicht ohne Einfluß sind, so dürfte es
sich empfehlen, der eigentlichen Beschreibung der Briquettmaschine etc. eine
Mittheilung der in Brandeisl vorgefundenen Bau- und Betriebsanlagen kurz
voranzuschicken.
Neben Brandeisl wird seitens der k. k. privilegirten
Staats-Eisenbahngesellschaft ein Kohlenwerk, die Zeche Michael, mit täglich
4000 Scheffel Förderung betrieben. Das drei Lachter mächtige, in voller Höhe
abgebaute Flötz liefert eine durchaus magere Kohle, die zum dritten Theile als
Stückkohle und zu 2/3 als Staubkohle und Grus fällt.
Die Kohle ist sehr unrein und enthält 50 Procent Berge, die nicht, wie bei anderen
Kohlenflötzen, compacte Mittel oder wenigstens Schnüre zwischen der guten Kohle
bilden, sondern fein in der ganzen Kohlenmasse eingesprengt sind.
Diese unreine Beschaffenheit der Kohle bedingt eine sehr starke Wäsche, die jedoch,
eben wegen der innigen Mengung beider Stoffe, nur höchstens 33 Proc. Berge entfernen
kann; es bleiben mithin immer noch 17 Proc. Aschentheile in den gewaschenen Kohlen
zurück.
Da die Wäsche um so vollständiger wirkt, je feiner die Kohlen sind, und bei der
Briquettirung die größten Kohlenstückchen nur Erbsengröße haben dürfen, so muß der
Kohlengrus vor weiterer Verwendung noch zerquetscht werden.
Der Gang dieser und der einleitenden Operationen ist folgender:
Die mit gemischten Kohlen beladenen Hunde werden vom Schachte auf Laufbrücken nach
den Sortirplätzen gefördert, dort vermittelst einer Kippvorrichtung über Sieben
entleert und in Stücke und Grus sortirt.
Die Stückkohlen werden zur Versendung nach den Locomotivstationen auf Bahnwagen
verladen, während der zur Briquett-Fabrication bestimmte Grus in Hunden auf
schmalspurigen Bahnen zum Quetschwerke gefördert wird.
Das Quetschwerk befindet sich mit den Wäschen in einem
Gebäude, auf dessen zweiten Stock die mit Grus beladenen Hunde durch einen
Schachtaufzug gewöhnlicher Construction gehoben und dort vermittelst der in Fig. 5 verzeichneten
Kippvorrichtung in den Rumpf c über dem Quetschwerke
entleert werden.
a ist der feste Bock der Kippvorrichtung, auf dessen
Querriegel die Lager für die Kippräder (zwischen welche der Hund b geschoben wird) befestigt sind.
Das Quetschwerk besteht aus zwei vertical unter einander liegenden Walzenpaaren,
welche durch die 16 Pferdekräfte starke Dampfmaschine der Wäschen vermittelst des
Kammrades f in schnelle drehende Bewegung gesetzt
werden.
Die Walzen des oberen Paares d haben eine grob gekörnte
Oberfläche und liegen 1 Zoll im Lichten aus einander, während die unteren,
horizontal geriffelten Walzen d' nur 1/2 Zoll
Zwischenraum von einander haben.
Um das Einklemmen ganz fester Schiefer zwischen den Walzen und somit eine Stockung
des Betriebes, ja den Bruch der Walzen zu vermeiden, ist nur die eine Walze jedes Paares fest, während die andere durch
starke, einem größeren Drucke nachgebende Federn in der richtigen Entfernung von der
ersteren gehalten wird.
Die Feder und ihre Befestigung ist in Fig. 5 mit e, und das Gleitlager der Walzen mit e' bezeichnet.Auf vielen Zechen und Kohkereien werden statt der Walzenquetschwerke sog.
Kohlenmühlen verwandt. – Ein kleinerer geriffelter Conus dreht sich,
ähnlich wie bei den gewöhnlichen Kaffeemühlen, in einem größeren. Der
Zwischenraum zwischen beiden Kegeln am unteren Ende beträgt nur 1/2 Zoll, am
oberen aber 6 bis 8 Zoll.In diesen Quetschwerken können auch Grobkohlen vermahlen werden, wobei die
größeren, eben nur in die obere Oeffnung passenden Stücke bei ihrem
Niedergange erst allmählich zerkleinert werden und unten als Staub
herausfallen.In Folge der größeren Pressung der Kohlen unter sich, wie der größeren
Reibung und Walzung derselben an den geriffelten Wänden der Mühle ist das
Korn des in Kohlenmühlen vermahlenen Kohlenstaubes feiner und gleichmäßiger,
wie das der Walzenquetschen, und gibt man deßhalb der Kohlenmühle auf großen
Werken, wie unter anderen auf der de Wendel'schen
Anlage, unbedingt den Vorzug.
Die beim Durchgange durch die Walzen zerkleinerten Kohlen fallen auf ein Sieb g mit 3/8 Zoll Maschenweite und werden durch die
stoßweise Vor- und Rückwärtsbewegung desselben in nußgroße Kohlen, welche zur
Heizung der stehenden Maschinen benutzt werden, und in den zur Briquettirung zu
verwendenden Kohlenstaub sortirt. Letztere Masse wird nun durch ein Paternosterwerk
h wieder in die zweite Etage des Gebäudes gehoben,
dort in einen Trog i entleert und unter starkem
Wasserzuflusse in vier verschiedenen, 8 Zoll weiten Abfallröhren k auf die vier Wäschen gefördert.
Jede Wäsche besteht aus einem großen viereckigen Wasserbehälter, in welchem sich auf
2/3 seiner Höhe ein 6 Fuß langes und 4 Fuß breites Metallsieb o neben einem aus 4zölligen Eichenbohlen hergestellten 20 und 48
Quadratzoll weiten Kasten befindet.
In diesem Kasten wird durch Uebertragung der Kurbelbewegung obengenannter stehenden
Maschine in eine geradlinige, ein enganschließender Kolben m auf- und niederbewegt, und hierdurch ein stoßweises Durchdringen
und Zurückgehen eines Theiles des im Raume n
befindlichen Wassers durch das Sieb hervorgerufen.Theils durch mechanische Einwirkung, mehr aber durch Säuerung des Wassers
beim Waschen einzelner Kohlensorten werden die Metallsiebe der Wäschen so
angegriffen, daß sie binnen kurzer Zeit erneuert werden müssen.Nach vielfachen Versuchen ist es auf der Kohkerei zu Osnabrück gelungen,
einen passenden Ersatz der Metallsiebe in den Glassieben zu schaffen.Gewöhnliches Fensterglas wird in 1 1/2 Zoll breite Streifen geschnitten, und
diese mit den zum Durchlassen des Wassers erforderlichen Zwischenräumen
neben einander hochkantig in den Rahmen gelegt.Während Metallsiebe beim Waschen von Ibbenbürener Kohlen nur höchstens sechs
Wochen halten, sind die Glassiebe schon neun Monate in unausgesetztem
Gebrauche, ohne irgend welche Abnutzung zu zeigen, und kosten dabei nur 2/3
des Preises der Metallsiebe.
Durch Lösung der an der Kolbenstange befestigten Klaue 1 kann die Verbindung mit dem
Motor aufgehoben und die Wäsche außer Betrieb gesetzt werden.
Das auf dem Siebe gelagerte Gemisch von Kohlen und Bergen wird in Folge des
wechselnden Wasserspiegels in eine lebhafte Bewegung versetzt und lagern sich dabei
die Berge wegen ihres größeren Gewichtes unten auf dem Siebe ab, während die
specifisch leichtere reine Kohle obenauf schwimmt, und über den vordern niedern Rand
der Wäsche mit dem überschüssigen Wasser abfließt. Durch das Sieb p wird dieses Wasser entfernt und gelangen dann die
Kohlen in den überdachten Raum vor der Preßmaschine.
Die Berge werden durch Arbeiter fortwährend vom Siebe entfernt.
Die durch die Maschen des Kohlensiebes beim Waschen mit durchdringende Kohlenschlempe
wird durch Oeffnen des am Boden des Bottichs befindlichen Schüttes q entfernt, fließt in große Bassins, klärt sich dort
durch Verdunsten und Einsickern des Wassers ab und wird, wenn wenig Schwefelkiese
enthaltend, zur Briquettfabrication mit verwandt.Bei einer zweiten Art der Kohlenwäsche wird ebenfalls der Unterschied im
spec. Gewichte der Kohlen und Berge zur Trennung beider benutzt.Das specifische Gewicht der Kohlen schwankt zwischen 1,2 bis 1,6, während das
der Schiefer ± 2,6 beträgt. Schüttet man nun in eine Mutterlauge, die
etwas schwerer wie Kohlen und leichter wie Schiefer ist, die zu waschende
Kohle, so sinken die Bergeunter, während die reine Kohle obenauf schwimmt
und leicht abgezogen werden kann. Diese Wäsche dürfte sich dort empfehlen,
wo passende Mutterlange billig zu haben ist, und Kohlen gewaschen werden
müssen, deren Staub (wie beim Piesberger Gruse) so fein ist, daß er durch
die Siebe der anderen Wäschen durchgeht; sie ist aber ganz unanwendbar, wenn
der Schiefer innig den Kohlen eingesprengt ist, wodurch die Verschiedenheit
der specifischen Gewichte beider aufgehoben wird.Die Eisenhütte Porta Westphalica hat aus diesem Grunde und wegen des theureu
Preises der Mutterlauge eine derartige mit einem großen Baucapitale
hergestellte großartige Waschanlage wieder aufgeben müssen.A. d. Verf.
Das der Kohlenmasse behufs ihrer Briquettirung zuzusetzende Bindemittel ist
eingedickter Theer (Bray genannt), welcher, wo er nicht, wie in Norddeutschland aus
den Hydrocarbürefabriken, als Handelsartikel zu beziehen ist, aus dem Theere durch
Abdestillirung der schlüpfrigen Oele dargestellt werden muß.
Zu diesem Zwecke wird in Brandeisl der aus den Gasanstalten von Prag, Dresden und
Wien bezogene Theer in große mit einander communicirende Gruben abgelassen, aus
welchen er mit einer Theerpumpe nach Bedarf in die Destillirkessel gefördert
wird.
Vier solcher Destillirkessel sind vorhanden, mit welchen in 48 Stunden 240 Centner
Theer, durch Abdestillirung von 40 Procent Oelen, zu 144 Centn. Bray verdickt werden
können.
Der Destillirapparat besteht aus Kesseln, Vorlagen und Kühlfässern gewöhnlicher
Construction.
Nachdem circa 40 Proc. Oele abdestillirt sind, wird die
Consistenz des Theers probirt, und die Operation geschlossen, wenn die Masse zähe
und fadenziehend erscheint.
Dieser Bray wird in zwei große Cisternen abgelassen, worin er bei längerem Stehen
erhärtet.
Die abgezogenen Oele werden in einer eigenen abgelegenen Fabrik weiter verarbeitet
und daraus 6 Proc. Hydrocarbüre gewonnen.
––––––––––
Die Briquettfabrication zerfällt in drei Theile:
1) Erwärmung der Kohlen,
2) Mischung der Kohlen mit erwärmtem Bray, und
3) Pressung der Kohlen zu Briquetts.
1) Die Erwärmung der Kohlen geschieht in dem in Fig. 1 in der
Ansicht, und in Fig.
3 und 4 im Quer- und Längendurchschnitt gezeichneten Heizapparate.
Derselbe besteht aus zwei übereinander liegenden, durch Herdfeuerung erhitzten
Cylindern a und a' von 2 Fuß
11 Zoll Durchmesser und 15 Fuß Länge, in welchen sich eiserne, die Spindel in 7 ganzen Umdrehungen
umlaufende Schnecken sehr langsam (1 Umdrehung in 1 1/2 Minuten) drehen.
Ein Paternosterwerk fördert die Kohlen aus der Halle vermittelst eines Rumpfes in den
oberen Cylinder, wo sie durch die Schnecke erfaßt und nach dem, am anderen Ende
zwischen beiden Cylindern angebrachten Halse c geschoben
werden. Vermittelst dieser Oeffnung gelangen die Kohlen in den unteren Cylinder,
werden nun durch die rückgängige Bewegung der unteren Schnecke zur Vorderwand des
Heizapparates zurückgeschoben und fallen aus einer Oeffnung d auf den Fußboden des Preßgebäudes.
Während des im Ganzen 20 Minuten dauernden Durchgangs der Kohlen durch die
Heizcylinder werden dieselben unter Verdampfung des noch aus den Wäschen
beibehaltenen Wassers auf 72° R. erwärmt.
Die frühere Art der Erwärmung der Kohlen durch heiße, in die Cylinder gelassene
Wasserdämpfe ist deßhalb aufgegeben, weil durch das condensirte Wasser der Dämpfe
die Kohlen sehr feucht wurden.
Dieser hohe Feuchtigkeitsgrad der Kohlen bedingte die spätere Trocknung der fertigen
Briquetts in eigenen Trockenräumen – eine Arbeit, die besondere Kosten
verursachte und sehr feuergefährlich war.Bei Anwendung des Goudron statt des Bray als Bindemittel müssen die Kohlen
bis 80 Procent Wassergehalt haben, in Folge dessen eine Trocknung der
Briquetts durch 24stündiges Stehen in einem auf 300° R. erwärmten
Heizraume erforderlich wird.A. d. Verf.
Die verschiedenen Theile des Heizapparates sind in den Zeichnungen folgendermaßen
bezeichnet:
a oberer Heizcylinder. – a' unterer Heizcylinder. – b Rumpf oder
Füllöffnung. – c Verbindungsrohr oder Hals
zwischen beiden Cylindern. – d Auslaßöffnung der
Kohlen. – e Herdfeuerung mit Treppenrost.
– f Feuercanäle. – g Paternosterwerk. – h Kammräder der
Schnecke und i die durch Transmissionsvorrichtungen
bewegte Riemscheibe.
2) Mischung der Kohlen mit Bray. Die Mengung des
Kohlengruses mit dem Bray geschieht in der in Fig. 1 verzeichneten
Mischtrommel, welche auf dem Boden über der Preßmaschine steht. Die Mischtrommel l ist ein oben offener Halbcylinder von 2 Fuß
Durchmesser und 12 Fuß Länge, dessen eiserne doppelte Wandungen zur Vermeidung des
Kaltwerdens der Kohlen mit Dampf erhitzt werden.
In dieser Trommel dreht sich eine Schnecke m, welche die
durch ein Paternosterwerk k heraufgeförderten warmen
Kohlen langsam der Preßmaschine zuschiebt.
Auf 4 Fuß Entfernung vom Anfange der Schnecke fließt der erwärmte Bray zu, und mischt sich durch
die Wälzungen der Schnecke mit den Kohlen.
Das Quantum des zuzusetzenden Bray hängt vorzüglich von der chemischen
Zusammensetzung der Kohlen ab; bei sehr fetten Kohlen genügt ein Brayzusatz von 2
bis 3 Procent, während magere Kohlen bis zu 10 Procent desselben verlangen.
Dieses Mischungsverhältniß ist aber auch bei ein und denselben Kohlen nicht constant,
sondern richtet sich nach den verschiedenen Feuchtigkeitsgraden derselben,
vorzüglich aber nach der wechselnden klebrigen Beschaffenheit des Bray.
Die richtige Beurtheilung dieser Verhältnisse ist der schwierigste Punkt der ganzen
Fabrication und bedingt längere praktische Erfahrungen.
Um nun je nach Bedarf größere oder geringere Quantitäten Bray den Kohlen zuführen zu
können, befindet sich in dem neben der Mischtrommel stehenden Kessel, worin der Bray
vermittelst einer besonderen Feuerung bis zur Siedehitze erwärmt wird, eine eigene,
sehr sinnreiche Schöpfvorrichtung.
Ueber dem Braykessel dreht sich auf festen Lagern – die in Fig. 1 weggelassen sind,
da sie die hinterliegenden Constructionstheile decken – eine gekröpfte Achse
n, an deren 6 Kurbeln 6 lange eiserne Stäbe o auf etwa 1/4 ihrer Länge aufgehängt sind.
Das ihrem Drehpunkte (einer Welle im Braykessel) entgegengesetzte, zu einer Gabel
ausgearbeitete Ende dieser Stäbe erhält durch die Drehung der gekröpften Achse eine
auf- und niedersteigende Bewegung. Zwischen den Gabeln sind die Schöpfkästen
p eingehängt, welche, durch ein Gegengewicht in
verticaler Lage gehalten, beim Niedergange in die flüssige Braymasse tauchen, und
den so geschöpften Inhalt in die Abflußrinne entleeren, wenn eine Hemmung r, wohinter die Nase q des
Kastens faßt, vorgeschoben und dadurch eine Drehung des Schöpfkastens um seine Achse
bewirkt wird. Je nach dem An- und Abrücken der verschiedenen Hemmungen kann
die Zahl der wirkenden Schöpfkästen und somit der Brayabfluß vermehrt oder
vermindert werden.
3) Die Preßmaschine. Die in Fig. 1 im Durchschnitt und
in Fig. 2 im
Grundriß verzeichnete Preßmaschine ist vom Gruben-Ingenieur Evrard zu Chazotte bei St. Etienne construirt, das Patent
aber durch Kauf an Gebrüder Hénin, Besitzer großer
Briquettfabriken bei Charleroi, übergegangen.
Die in der Mischtrommel vorgemengten Kohlen fallen am Ende der Schnecke in einen
verticalen, oben und unten offenen Cylinder A von 3 Fuß Durchmesser und 5
Fuß Höhe. Auch die Wandungen dieses Cylinders sind doppelt und mit Wasserdampf
erhitzt.
Im Cylinder wird nun die innigste Mengung der Kohlen mit dem Bray, durch auf der
rotirenden Hauptwelle befestigte Messer (ähnlich wie bei den gewöhnlichen
Thonmühlen) hervorgebracht.
In 5 Zoll Abstand vom unteren Rande des Mischcylinders befindet sich ein Tisch mit
überstehendem Rande B, der ebenfalls an der Hauptwelle
befestigt ist und durch diese in drehende Bewegung gesetzt wird. Auf diesen Tisch
stützt sich die im Mischcylinder vorhandene Masse.
Durch 4 Messer C, welche vermittelst einer aus Fig. 1
ersichtlichen, an den 4 Säulen S angebrachten
Stellvorrichtung je nach Bedürfniß weniger oder weiter auf diesen Tisch greifend, zu
stellen sind, wird die entsprechende Masse des Gemisches abgestrichen und fällt
vermittelst der 4 Abfallrohre D auf eine ebenfalls
rotirende Ringfläche E.
Auf diese Fläche greifen 16 über den Einfallröhren der 16 Preßcylinder angebrachte
Messer.
Je 4 solcher Messer bilden zwischen je 2 Abfallröhren einen Satz. Die einzelnen Messer jedes Satzes sind zum Zweck der
Abstreifung einer gleichen Masse der Mischung verschieden weit auf die Ringfläche
E greifend gestellt, so zwar, daß das erste nur auf
1/4, das zweite auf 1/2, das dritte auf 3/4 und das vierte endlich auf die ganze
Breite derselben faßt.
Durch Zurückschlagen der an ihrer Stützsäule drehbaren Messer können ohne
Beeinträchtigung des Fortganges des ganzen Preßprocesses einzelne Preßcylinder
ausgeschaltet werden.
Die Preßcylinder G liegen radial um die Hauptwelle und
sind an dem, auch die Hauptwelle umfassenden und haltenden Rahmen H in unverrückbarer Lage befestigt und mit dem
Mauerwerke verbolzt. Die Länge des Theiles des Cylinders, woselbst die eigentliche
Pressung stattfindet, muß so bemessen werden, daß dem Austritte der Briquettmasse
eine Reibung entgegengesetzt wird, die der verlangten Compression entspricht.
Die Seele der Preßcylinder hat einen Durchmesser von 5 Zoll, die Wandstärke beträgt 2
Zoll.
Um die Reibung und somit den Druck in den Preßcylindern reguliren zu können, ist
jeder Cylinder auf die Länge von 9 Zoll von seinem Kopfe horizontal aufgeschnitten,
und aus der oberen abzunehmenden Hälfte ein am Mundloche 1 1/2 Linien dicker und
nach hinten verlaufender Keil herausgenommen, wodurch der Kopf des Preßcylinders
eine schwach verjüngte conische Form erhält.
Vermittelst starker auf diesen losen Theil aufgesetzter Klemmen i wird derselbe höher und niedriger gestellt, wodurch der
Querschnitt der Briquetts etwas unter die Kreisform gedrückt wird.
In die Preßcylinder greifen die Preßkolben K, welche
vermittelst einer Gabelführung K¹ an einem, um
ein Excentric der Hauptwelle beweglichen, starken Ringe befestigt sind.
Die Excentricität beträgt 8 Zoll und darnach die Hubhöhe des Kolbens 10 1/2 Zoll.
Die zu pressende Masse, welche in Folge des durchlaufenen Weges auf + 30 bis
40° R. (den passenden Wärmegrad zur Pressung) erkaltet ist, wird nun, wie
oben gesagt, durch das Messer F von der Ringfläche E abgestrichen, fällt in die darunter befindliche 4
Quadratzoll weite Oeffnung des Preßcylinders und wird durch den Kolben gegen den,
den vorderen Theil des Cylinders ausfüllenden Briquettkörper geschoben und mit
diesem zusammengepreßt.
Beim Anfange der Operation, oder der Wiederinbetriebsetzung eines reparirten
Cylinders, wird zur erstmaligen Herstellung dieses Widerlagers eine an einem langen
Hebel befestigte Scheibe, deren Klaue hinter den oberen Rand des Cylinders greift,
vor das Mundloch gedrückt, gegen welche sich die eingelassene und nicht entweichen
könnende Briquettmasse preßt. Nachdem der erforderliche Grad der Pressung auf diese
Weise erreicht ist, wird die Scheibe entfernt und genügt die, nöthigenfalls durch
Niederstellung des oberen Mundstückes des Cylinders noch zu vermehrende Reibung des
Briquettkörpers an den Seitenwandungen des Cylinders, um den erlangten Härtegrad der
Briquetts fortwährend beizubehalten.
Die Welle des Excentrics macht in einer Minute 40 Umdrehungen, in Folge deren durch
jeden Preßkolben ein Briquettende von 23 Zoll Länge vorgeschoben wird. Jeder
Kolbenstoß preßt mithin 23/40 Zoll, oder alle 16 Cylinder per Minute rund 31 laufende Fuß fertige Briquetts.
Das aus dem Preßcylinder austretende Briquett schiebt sich auf einer 4 Zoll breiten,
horizontalen Scheide M fort. Auf dieser Scheide ist, 14
Zoll vom Mundloche entfernt, ein Quersteg genietet, gegen welchen das Briquett bei
seinem weiteren Vorgange faßt und dadurch die Scheide vorschiebt, bis eine, sie in
horizontaler Lage haltende Sperrstange sich auslöst.
Das Briquett verliert durch dieses Nachgeben der Scheide seine Unterstützung, bricht
in Folge des eigenen Gewichtes ab und fällt auf einen, um die ganze Preßmaschine
rotirenden, eine Kreisfläche bildenden Tisch N, von
welchem Arbeiter dasselbe abnehmen und als vollkommen fertiges Fabrikat zum Versandt
in Eisenbahnwagen laden.
Die Scheide springt nach dem Niederfallen des Briquetts, in Folge eines Gegengewichts
und des Druckes einer auf ihrer Gleitstange angebrachten Spiralfeder in ihre
ursprüngliche Lage zurück, und hakt dabei die Sperrstange wieder hinter den
Ansatz.
Die Hauptwelle der Preßmaschine besteht aus zwei Theilen, dem oberen, woran der Tisch
B und die Ringfläche E
befestigt ist, und dem unteren stärkeren, durch den das Preßwerk bewegt wird.
Diese Trennung der Hauptwelle in zwei von einander unabhängige Theile wird durch die
verschiedenen Umdrehungsgeschwindigkeiten beider (der obere Theil macht nur 1/4 der
Umdrehungen des unteren) bedingt.
Der Motor aller im Preßgebäude aufgestellten Maschinen und Apparate ist eine
Dampfmaschine von 40 Pferdekräften, die vermittelst der conischen Räder O und P den untern Theil der
Presse in drehende Bewegung versetzt. Auf dieser Achse befindet sich ferner das
Kammrad T, welches in die Zahnstange des Tisches N greift und die Rotirung desselben veranlaßt.
Das Rad Q auf der Achse des obern Theiles der
Preßmaschine greift in das mit der stehenden Dampfmaschine verbundene Rad R ein.
In einer 12stündigen Arbeitsschicht werden 600 bis 700 Cntr. Briquetts hergestellt;
man kann aber durch Vergrößerung der Anlage und Vermehrung der Preßcylinder die
Productionsfähigkeit solcher Fabriken sehr steigern, und finden sich in Frankreich
und Belgien mehrere, die täglich 150,000 bis 180,000 Kilogr. = 3000 bis 3600 Cntr.
Briquetts pressen.
Das specifische Gewicht guter Briquetts ist dem der Kohlen, woraus sie hergestellt
werden, fast gleich, und beträgt durchschnittlich 1,3; dahingegen ist der Heizeffect
der Briquetts größer als der der Kohlen, einmal weil der Brennstoff des Bray mit zur
Wirkung kommt, und dann durch den Bray eine leichtere Fortpflanzung des Feuers
stattfindet, wodurch das Bedingniß eines stärkeren, stets auf Erkaltung wirkenden
Zuges wegfällt.
Zur Ermittelung des wirklichen Brennwerthes der Briquetts wurden vor zwei Jahren von
Belgien 400 Cntr. derselben, welche aus Kohlen, die den hannoverschen sehr ähnlich
seyn sollen, dargestellt waren, bezogen, und haben die damit in Lingen vorgenommenen
Heizversuche folgende Resultate ergeben.
Es wurden verbraucht pro Locomotivmeile:
bei
einer
Mischung
von
1/2
Briquetts
und
1/2 Kohks
= 172,09 Pfd.
Brennmaterial,
„
„
„
„
3/5
„
„
2/5 „
= 180,18 „
„
„
„
„
„
2/3
„
„
1/3 „
= 189,86 „
„
Da nun dieselbe Maschine, mit Kohks allein geheizt, pro
Meile 204,81 Pfd. Kohks verbraucht, so ergibt sich, daß 100 Pfd. Briquetts im ersten
Falle 137,8 Pfd. Kohks, im zweiten 122,8 Pfd., und endlich im ungünstigsten Falle
noch immer 112,1 Pfd. Kohks ersetzen.
Das Mischungsverhältniß von 1/2 Briquetts und 1/2 Kohks erscheint demnach als das
günstigste.
Nach Beschreibung der wesentlichsten Operationen der Briquett-Fabrication, so
wie der einzelnen Theile und Constructionsverhältnisse der dazu erforderlichen
Maschinen, endlich nach Darlegung der großen Brauchbarkeit der Briquetts als
Heizmaterial der Locomotiven, muß nun noch die finanzielle Seite der Frage näher
betrachtet werden.
Den nachstehenden deßfallsigen Berechnungen sind, um schließlich durch Zahlen die
besonderen Vortheile nachweisen zu können, die speciell für unseren Eisenbahnbetrieb
aus der Verwendung der Briquetts erwachsen werden, die hannoverschen
Anschaffungspreise und sonstigen Verhältnisse zu Grunde gelegt.
a. Baukosten
einer Briquettfabrik mit einer Production von täglich 700 Centner
Briquetts.
1)
Eine nach Hénin's Principe
construirte Briquettpresse mit 16 Preßcylindern,fertig geliefert und
aufgestellt, incl. der Mischtrommel, aus
zollvereinsländischenFabriken bezogen, wird kosten
8,200 Rthlr.
2)
Die dazu gehörige Dampfmaschine von 40 Pferdekräften mit
Kesseln und denverschiedenen Verbindungstheilen, ebendaher
bezogen
5,000 „
3)
Für den Erwärmungsapparat, die Paternosterwerke und
Nebentheile sind zurechnen
1,800 „
4)
Das Preß- und Maschinengebäude und die
Fundamentirungen der Maschinekosten pprt.
8,500 „
––––––––––
Summe der Baukosten der eigentlichen Briquettfabrik
23,500 Rthlr.
Da der Bray bei uns als Handelsartikel zu beziehen ist, so kommen Kosten für die
Theerdestillationsanstalt nicht in Anrechnung.
b. Betriebskosten.
Zur Bedienung der Heizvorrichtung des Braykessels und der Presse ist bei einer
12stündigen Arbeitsschicht folgendes Personal erforderlich:
1 Arbeiter zum Anbringen der Kohlen aus der Halde, 1 Arbeiter zum Füllen der
Paternosterschaufeln des Heizapparates, 1 Arbeiter zu deßgleichen der Mischtrommel,
1 Arbeiter zum Einfüllen des Bray in den Braykessel, Heizen desselben und der
Heizvorrichtung, 2 Arbeiter zum Abholen und Beseitigen der fertigen Briquetts, 1
Vormann, 1 Hülfsjunge und 1 Aufseher.
Dafür sind an Arbeitslöhnen und Gehalten monatlich zu
bezahlen
120 Rthlr.
Die Reparaturkosten an den Maschinen berechnen sich pro Monat auf
16 „
Für Schmier- und Putzmaterial sind monatlich
aufzuwenden
26 „
Für Heizmaterial des Braykessels und des Heizapparates
deßgleichen
14 „
Für Brennmaterial der großen Dampfmaschine, Oel, Schmiere
und Löhne des Heizers und des
Maschinenwärters
180 „
––––––––––
1) Summe der monatlichen Ausgaben für Handarbeiten und
Betrieb der Briquettpresse
356 Rthlr.
macht pro
Jahr
4,272 Rthlr.
Im Laufe eines Betriebsjahres, dasselbe zu 300
Arbeitstagen gerechnet, werden 300 × 700 = 210,000 Cntr. Briquetts
hergestellt; auf einen Centner Briquetts kommen mithin an vorgenannten Ausgaben
0,61 Ngr.
2) Eine passende Mischung zur
Herstellung der Briquetts besteht, wiedeßfallsige Proben ergeben haben,
aus 1/3 Piesberger und 2/3 IbbenbürenerKohlen, und verlangt dieselbe
einen Zusatz von 5 Proc. Bray.
Bei dem Preise von 25 Ngr.
für den Centner Bray kostet mithin der Zusatzzu 1 Centner
Briquetts
1,25 „
3) In Belgien nimmt man an,
daß gute Briquetts nicht mehr als 6 bis 7Proc. Aschengehalt haben
dürfen.
Die Piesberger Feinkohle
enthält 9 bis 10 Proc. Berge, deren Entfernungdurch Wäschen, wegen der
staubförmigen Beschaffenheit der Kohlen, sehrschwer zu beschaffen
ist.
Aus der Ibbenbürener Kohle,
welche roh 8 Proc. Berge besitzt, lassensich bei gehöriger
Zerkleinerung der Kohlen die Berge bis auf 3 Proc.durch Waschen
entfernen.
Das Gemisch von 1/3
Piesberger Kohle (mit 11 Proc. Berge) und 2/3Ibbenbürener Kohlen (mit 3
Proc. Berge) hat mithin nur einen Gesammt-Aschengehalt von 5 2/3
Proc., und kann demnach als sich vollkommen zurBriquettfabrication
eignend angesehen werden.
Das Quetschen und Waschen der
zu 1 Cntr. Bray erforderlichen Kohlenkostet an Arbeitslöhnen,
Unterhaltung der Maschinen, 5 procentigerVerzinsung und 5procent.
Amortisation der Baukosten zusammen 0,9 Ngr.Da nun 1/3 der Masse nicht
zerkleint und gewaschen wird, so kommen nurzur Berechnung 2/3 .
0,9
0,60 „
4) Die Verzinsung des
obenstehend zur Summe von 23,500 Rthlr.ermittelten Baucapitales der
eigentlichen Briquettmaschinen und dieAmortisation desselben ebenfalls
mit 5 Proc. erfordert eine jährlicheAbschreibung von 2350 Rthlr.
Diese Summe auf die
Gesammtproduction eines Jahres (210,000 Cntr.Briquetts) vertheilt,
ergibt für den Centner fertiger Briquetts
0,34 „
5) Zu 1 Cntr. Briquetts werden
verbraucht:
2/3 Cntr. Ibbenbürener Gruskohle
à 4,8 Gr. = 3,2 Gr. 1/3 Cntr.
Anthracitkohle des Piesbergs à 1,8 „ =
0,6 „
––––––––––––––––––––
zusammen
3,80 „
–––––––––––––––––––
Kosten eines
Centners Briquetts
6,6 Ngr.
Der Centner Ibbenbürener Stückkohlen verrechnet sich bei einem Grubenpreise von 5,5
Groschen für den Scheffel gemischter Kohlen ebenfalls auf
6,6 Groschen, die Briquetts sind mithin nicht theurer als jene, und werden noch
billiger zu stehen kommen, wenn spätere Versuche die Zulässigkeit eines größeren
Zusatzes von Piesberger Kohlen ergeben.
Der Preis der aus Ibbenbürener und Oeseder Kohlen hergestellten Kohks beträgt 10 1/2
Ngr. pro Centner; dieselben sind mithin 40 Proc. theurer
als die Briquetts.
Zum Nachweise der Richtigkeit oben ausgeführter Kostenberechnungen möge hier erwähnt werden, daß
die belgische Regierung, in Folge eingeleiteter Submission, den Bedarf der auf den
Staatsbahnen erforderlichen Briquetts von Hénin
Söhne zu Charleroi zum Preise von 15,75 Frcs. pro Tonne
à 1000 Kilogr. (macht pro Zollcentner rund 6 Ngr.) bezogen hat, während die Lieferung der Kohks
die Tonne mit 25,25 Frcs. (pro Centner rund 10 Ngr.)
verdungen wurde.
Ebengenannter, im Jahre 1859 gezahlter Preis für die Briquetts soll durch größere
Concurrenz im Jahre 1858 noch um 1,5 Frcs. per Tonne
gedrückt und dennoch das Geschäft der Briquettfabrication ein sehr rentables seyn,
wie sich aus dem Umstande ergibt, daß sehr glaubwürdiger Mittheilung zufolge, eine
derartige, mit einem Baucapitale von 100,000 Frcs. hergestellte Fabrikanlage sich im
ersten Jahre des Betriebes vollständig frei gearbeitet, also 100 Proc. Zinsen
eingetragen hat.
Die vor einem Jahre in den öffentlichen Blättern aufgetauchten Gerüchte, daß in
Belgien der Brand der Briquetts in Locomotiven, wegen des starken lästigen Rauches
derselben, wieder aufgegeben sey, haben sich nicht bewahrheitet und besteht nach wie
vor auf den dortigen Staatsbahnen das
Locomotivbrennmaterial aus 2/3 Kohks und 1/3 Briquetts; während die Privatbahnen entweder Briquetts allein oder in einer
Mischung von 2/3 zu 1/3 Kohks verfeuern.
Auch in Oesterreich, woselbst jener Industriezweig durch die oben mitgetheilten
localen Verhältnisse vielfach beeinträchtigt wird, beabsichtigt man noch mehrere
Briquettfabriken in Ungarn und Mähren einzurichten, und dürfte dieses ein
sprechendes Zeugniß mehr für die großen, aus jener Fabrication zu erzielenden
pecuniären Vortheile seyn.
Zum Schlusse dieses Aufsatzes möge noch erwähnt werden, daß die Herstellung einer
Briquettfabrik in Osnabrück in naher Aussicht steht, und der Betrieb derselben dem
Referenten Gelegenheit geben wird, weitere Mittheilungen über diesen, für die
Kohlenbergwerke so wie für die Bahnverwaltungen gleich wichtigen Industriezweig zu
machen.
Tafeln
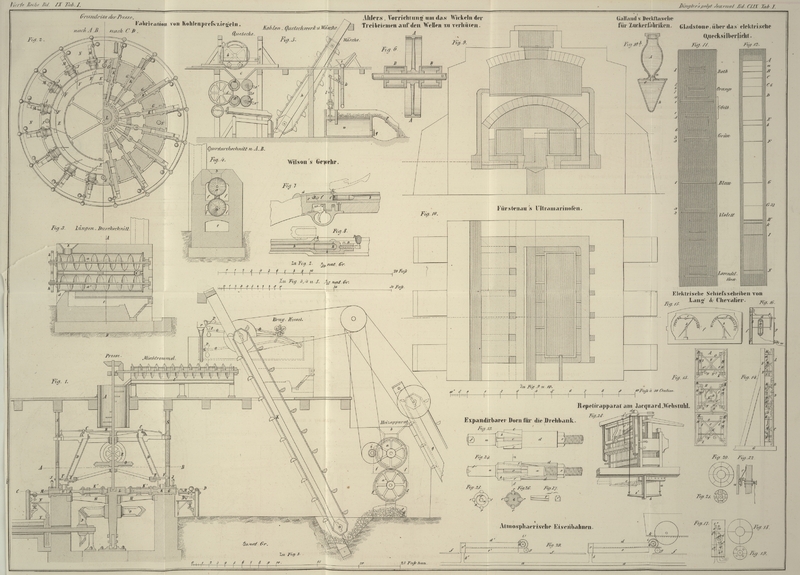