Titel: | Ueber den Nutzeffect und die Construction von Oefen für metallurgische und technische Zwecke; von C. Schinz. |
Autor: | C. Schinz |
Fundstelle: | Band 159, Jahrgang 1861, Nr. LXXIX., S. 282 |
Download: | XML |
LXXIX.
Ueber den Nutzeffect und die Construction von
Oefen für metallurgische und technische Zwecke; von C. Schinz.
(Schluß von S.
209 des vorhergehenden Heftes.)
Mit Abbildungen auf Tab.
IV.
Schinz, über den Nutzeffect und die Construction von Oefen für
metallurgische und technische Zwecke.
Für die Praxis weit wichtiger wäre eine genaue Kenntniß der Leitungsfähigkeit der zu schmelzenden oder zu erhitzenden Körper, da diese
eigentlich die Zeit bedingt, in welcher der gewünschte Effect erreicht werden
kann.
Leider sind unsere Erfahrungen noch zu mangelhaft, um diese Effecte aus der
Leitungsfähigkeit jener Körper a priori berechnen zu
können, und die mit
wissenschaftlicher Schärfe ausgeführten Untersuchungen von Peclet über die Leitungsfähigkeit verschiedener Materialien lassen sich
für den vorliegenden Fall bloß zur Vergleichung, nicht zur Bestimmung absoluter
Werthe benutzen.
Als Beitrag zu dem, was auf diesem Felde noch zu thun ist, will ich hier eine
Erfahrung mittheilen.
In einem Ofen wurden in 17 Stunden 1800 Pfd. Glas mit einem Aufwande von 0,9917 Pfd.
Holz per 1 Pfd. Glas geschmolzen; in einem andern Ofen
wurden 5000 Pfd. Glas in 18 Stunden mit einem Aufwand von 1,4111 Pfd. Holz per 1 Pfd. Glas geschmolzen, also mit einem Mehraufwand
von 29,7 Proc., und doch war die Wärme transmittirende Wandfläche des ersten Ofens
um 23 Proc. im Verhältniß zum Inhalte des Ofens größer, so daß der zweite Ofen
nothwendig gegen den ersten eine wesentliche Ersparniß statt eines Mehrverbrauchs
hätte geben sollen.
Der Eigenthümer des zweiten Ofens behauptete mit der größten Bestimmtheit, daß sein
Glassatz nicht im geringsten strengflüssiger sey, als der im ersten Ofen angewandte,
und es wurde daher von ihm die Erfüllung des Contractes bezüglich der in Aussicht
gestellten Ersparniß bestritten.
Der Glassatz, welcher im ersten Ofen verwendet wurde, bestand aus:
100 reinem Sand 25 gepulvertem
Kalkstein 12 1/2 Potasche 12 1/2
kohlensaurem Natron;
CaO, 3 SiO³ + NaO, 2 SiO³ +
KaO, SiO³.
derjenige des zweiten Ofens bestand aus:
100 Sand (eigentlich 125,
wovon 1/5 kohlens.
Kalk) 54 Kalkstein (wovon 25 in
125 Sand
enthalten), 9 kohlensaurem
Natron.
2 CaO, 3 SiO³ + NaO, 3
SiO³.
Das Verhältniß des Sauerstoffs der Basen zu demjenigen der Kieselsäure war im ersten
Satze 1 : 7, und im zweiten Satze 1 : 5. Hiernach sollte man allerdings vermuthen,
daß dem ersten Satze eine geringere Schmelzbarkeit zukäme. Aber die Erfahrung im
ersten Ofen mit einem Glassatze von 100 Sand, 18,5 Kalkstein und 14,6 Soda, dessen
Sauerstoffverhältniß 1 : 6 ist, ergab schon eine sehr bedeutende Verlängerung der
Schmelzzeit; ferner ist nach Plattner's Untersuchungen
der Schmelzpunkt von Kalkschlacken um 100° höher als derjenige gewöhnlichen
weißen Glases, woraus
hervorgeht, daß wenigstens der Schmelzpunkt eines kalkreichen Glases höher liegen
muß. Uebrigens erklärt ein höherer Schmelzpunkt noch keineswegs die bedeutende
beobachtete Differenz in der Schmelzbarkeit, da ein um 100° höherer
Schmelzpunkt nur 13 Proc. und ein um 50° höherer nur 6 Proc. mehr
Holzverbrauch veranlassen würde, während dieser Mehrverbrauch im zweiten Ofen
effectiv 30 Proc. betrug.
Ich bin endlich zu einer mit den Thatsachen sehr genau übereinstimmenden Erklärung
des verschiedenen Verhaltens dieser beiden Glassätze gelangt. Es ist die den
Materialien des Glassatzes zukommende Leitungsfähigkeit für die Wärme, welche dessen
geringere oder größere Schmelzbarkeit bedingt.
Die Leitungsfähigkeit des fein gepulverten Kalksteins ist 0,0618; diejenige des
Quarzsandes ist 0,162 und diejenige der gepulverten kohlensauren Alkalien 0,084;
sobald aber die letzteren Rothglühhitze angenommen haben, schmelzen dieselben und
bilden also eine zusammenhangende Masse, so daß deren Leitungsfähigkeit nun 0,7
wird. Da nun das Schmelzgut nach seinem Einfüllen in die Häfen sehr bald auf
Rothglühhitze gebracht ist, während der Schmelzdauer aber für den größeren Theil der
Zeit die geringere Temperaturdifferenz zwischen dem Feuer und dem Schmelzgute
stattfindet, so machen wir nur einen sehr kleinen Fehler indem wir die
Leitungsfähigkeit der Alkalien gleich 0,7 setzen.
Dann wird die Leitungsfähigkeit des Glassatzes für den ersten Ofen:
100 Sand × 0,162
= 16,200
25 Kalkstein × 0,0618
= 1,545
25 Alkalien × 0,7
= 17,500
––––
–––––––
150
= 35,245
und die mittlere Leitungsfähigkeit ist 35,245/150 =
0,2350.
Der Glassatz für den zweiten Ofen gibt:
100 Sand × 0,162
= 16,2000
54 Kalkstein × 0,0618
= 3,3372
9 Soda × 0,7
= 6,3000
––––
–––––––––
163
= 25,8372
und die mittlere Leitungsfähigkeit ist 25,8372/163 =
0,1585.
Wenn daher ersterer Glassatz in 17 Stunden den Schmelzproceß vollendet, so wird
letzterer bei gleicher Intensität der Ofenhitze oder des Feuers 0,1585 : 0,235 = 17
: x = 27,14 Stunden brauchen.
Würde daher dieser Glassatz im ersten Ofen bei gleicher Intensität des Feuers
geschmolzen worden seyn, so wäre der Verbrauch pro 1
Pfd. Glas gewesen (27,14 . 105)/1800 = 1,5832 Pfd. Holz, während bei dem ersten
Glassatz dieser Verbrauch nur 0,9917 Pfd. war; es ist folglich die Schmelzbarkeit
des zweiten Satzes um 37 Proc. geringer als diejenige des ersten.
Da aber 27 Stunden Schmelzzeit nicht bloß wegen der Transmission der Ofenwände,
sondern auch wegen der Arbeitsvertheilung in der Glasfabrication höchst ungünstig
sind, so mußte durch einen größern Holzverbrauch und damit hervorgebrachte höhere
Ofentemperatur die Schmelzzeit verkürzt werden.
Folgende Schemen zeigen am besten wie dieser Zweck erreicht wurde.
Im ersten Ofen wurden in der Stunde (Zeiteinheit)
consumirt 105 Pfd. Holz à 3877
= 407,085 W. E.
––––––––––––––
vom Glase absorbirt (Pfd. 1800 . 0,2 . 1300)/17
Stunden
= 27,529
von 64 Quadratfuß Ofen-Wandfläche transmittirt bei
1400° Ofen-Temperatur à 1740
= 111,360
mit den Verbrennungsproducten entfernt Pfd. 105 . 1,8108
. 1412°
= 268,196
––––––––––––––
407,085
Die kleinste Temperatur-Differenz zwischen Glas und Verbrennungsproducten war
also 1412° – 1300° = 112°.
Im zweiten Ofen mit dem schwerschmelzbaren Satze war
die Schmelzzeit 18 Stunden und der
Holzverbrauch 392 Pfd. per St. = 392 × 3877
= 1,519,784 W. E.
––––––––––––––
vom Glase absorbirt (Pfd. 5000 . 0,2 . 1350°)/18
Stunden
= 75,000
von 136 Quadratfuß Wandfläche bei 1450° Ofentemperatur
à 1003 transmittirt
= 258,808
mit den Verbrennungsproducten entfernt Pfd. 392 . 1,8108
. 1670
= 1,185,976
––––––––––––––
1,519,784 W. E.
es war also die nöthige Temperatur-Differenz im
Minimum, um in 18 Stunden zu schmelzen = 1670° – 1350° =
320°, wobei der Schmelzpunkt des Glases um 50° höher angenommen ist
als im ersten Ofen.
Wäre nun in diesem zweiten Ofen der Satz des ersten geschmolzen worden, so wäre der
Holzverbrauch gewesen:
Pfd. 234 × 3877
= 907,418 W. E.
–––––––––––––
vom Glase absorbirt (Pfd. 5000 . 0,2 . 1300°)/17
Stunden
= 76,471
von 136 Quadratfuß transmittirt bei 1400° à 1740
= 236,640
durch die Verbrennungsproducte entführt Pfd. 234 . 1,8108
. 1412°
= 594,307
–––––––––––––
= 907,418 W. E.
Der Holzverbrauch pro 1 Pfd. Glas ist:
a) im ersten Ofen für leicht
schmelzbaren Satz (17 . 105)/1800
= 0,9917 Pfd.
b) in demselben mit dem schwer
schmelzbaren Satz (27,14 . 105)/1800
= 1,5832 „
c) im zweiten Ofen mit dem leicht
schmelzbaren Satz (17 . 234)/5000
= 0,7816 „
d) in demselben mit dem schwer
schmelzbaren Satz (18 . 392)/5000
= 1,4111 „
Vergleichen wir den Holzverbrauch a mit c so ergibt sich ein Unterschied von 21 Proc. zu Gunsten
von c, welche also das günstigere Flächenverhältniß des
letztern Ofens bestimmen; vergleichen wir c mit d, so ist der Unterschied 37 Proc., welcher den
Unterschied der Schmelzbarkeit der beiden Sätze bestimmt; vergleichen wir endlich
a mit d, so ergibt sich
ein Unterschied von 30 Proc., welcher den effectiven Mehrverbrauch an Holz
bezeichnet, der den Streit veranlaßte. Dieser Mehrverbrauch beruht aber auf der um
37 Proc. geringeren Schmelzbarkeit des Glassatzes.
Addiren wir zu dem effectiven Mehrverbrauch = 30 Proc., für verminderte
Ofenwandfläche 21 Proc., 30 + 21 = 51, so bleibt eine Differenz von 51 – 37 =
14 Proc., welche der Ofen wirklich mehr consumirte; diese 14 Proc. dürften wohl
daher rühren, daß in Folge der Steigerung des Holzverbrauchs die Gasentwickelung
weniger stetig ist.
Da in beiden Oefen die Hafenoberfläche, durch welche hindurch die Wärme an das Glas
treten mußte, nahezu die gleiche war, so konnte diese keinen Einfluß ausüben; sonst
aber wird allerdings bei der Bestimmung der Leitungsfähigkeit noch der Factor der
mehr oder weniger dicken Schichte, durch welche die Wärme einziehen muß, mit in
Betracht kommen.
Was nun den Schmelzpunkt der zu schmelzenden Substanz
betrifft, so haben wir bereits gesehen welchen Einfluß derselbe ausübt, und die oben
mitgetheilte Tabelle über den Nutzeffect der Brennstoffe für Temperaturen von 1000°,
1100° bis 1500°, zeigt diesen Einfluß sehr übersichtlich.
Bei der Construction der Oefen kommt nun, wie ebenfalls
bereits ersichtlich geworden, sehr viel darauf an, daß die Ausdehnung der Ofenwände auf das zulässige Minimum beschränkt wird, da
diese Flächen weit mehr Wärme zerstreuen als der zu erhitzende oder zu schmelzende
Körper aufnimmt.
Die specifische Wärme des Materials, woraus diese Wände
bestehen, ist von geringem Einfluß, wenn der Ofen, wie beim Schmelzen von Glas oder
beim Puddeln von Eisen, in fortdauerndem oder fast fortdauerndem Betriebe ist. Wenn
aber der Betrieb ein periodischer ist, oder gar eine völlige Abkühlung des Ofens
zwischen jeder Operation stattfinden muß, wie beim Brennen von Thonwaaren, so hat
die specifische Wärme des Ofenmaterials, oder mit anderen Worten die Wärmecapacität
der Ofenwände, einen sehr bedeutenden Einfluß auf den Nutzeffect des Ofens.
Der gebrannte Thon, welcher fast ausschließlich zum Ofenbaue verwendet wird, verhält
sich bezüglich seiner specifischen Wärme verschieden, dieselbe variirt zwischen
0,1890 und 0,2410; man könnte aber diese Werthe, welche per Kubikfuß eine Capacität von 184 bis 233 W. E. ergeben, sehr
beträchtlich vermindern, indem man die Steine entweder hohl oder porös machte, so
daß eine viel kleinere Masse zu erhitzen wäre.
Von überwiegendem Einfluß auf die Oekonomie beim Betriebe pyrotechnischer Apparate
für hohe Temperaturen ist hingegen die Leitungssähigkeit des
Materials woraus die Ofenwände bestehen.
Peclet hat die Leitungsfähigkeit von zwei Sorten
gebrannten Thones zu 0,306 und 0,414 bestimmt. Da aber die Zusammensetzung des Thons
von verschiedenen Fundorten sehr variirt, so können uns diese Zahlen nur ein
beiläufiges Maaß der Grenzen geben, innerhalb welcher die Leitungsfähigkeit des
gebrannten Thones liegt. Die erste Bestimmung ergibt für 1 Quadratfuß Ofenwand bei
1500° Temperaturdifferenz zwischen der inneren Ofenfläche und der äußeren
Luft: 1500 × 0,306 = 459 W. E., und die zweite ergibt 1500 × 0,414 =
621 W. E.; es ist daher leicht einzusehen, daß solche Angaben zu einer genauen
Berechnungsweise nicht dienen können.
Eine genaue Kenntniß der Leitungsfähigkeit der für den Ofenbau dienenden Materialien
ist aber besonders deßhalb wichtig, weil, wie wir schon im Vorhergehenden gesehen
haben, die durch die Ofenwände zerstreute Wärme je nach der Temperatur der Oefen, 22
bis 33 Proc. der producirten Wärme betragen kann; und da von der im Ofen abgegebenen
Wärme auch eine entsprechende Menge mit den Verbrennungsproducten abzieht, so beträgt in
Wirklichkeit der Wärmeverbrauch für den Ofen selbst 60 bis 90 Proc. der Production,
während der eigentliche Nutzeffect, nämlich die Wärme welche dem zu schmelzenden
oder zu erhitzenden Körper mitgetheilt wird, nicht mehr als 5 bis 7 Proc., und mit
Hinzuziehung der abgeführten Verbrennungsproducte 10 bis 40 Proc. ausmacht.
Ich sah mich daher veranlaßt, alle Bedingungen zu prüfen, welche geeignet sind den
großen Wärmeverlust durch die Ofenwände zu vermindern.
In meiner „Wärme-Meßkunst“ habe ich (Artikel 240 und
folgende) die allgemeinen Werthe sowie die Formeln angegeben, nach welchen die
Transmission der Wärme durch mehr oder weniger dicke Wände zu berechnen ist. Ich
habe nur hinzuzufügen, daß wenn die äußere Temperatur = t' einer etwas dicken Wand 60° C. übersteigt, alsdann die
Transmission nicht mehr dieser Temperatur proportional berechnet werden darf,
sondern eine solche Fläche ist als eine constante Wärmequelle zu betrachten, welche
ihre Wärme an die sie umgebende Luft in progressiver Menge nach dem Gesetze von Dulong abgibt, also nach der Formel Sm (at – 1) + Lnt
b, worin L und
S die Leitungs- und Strahlungscoefficienten
für die wärmeabgebende Fläche sind, m und n constante Größen, ebenso a
und b, während t die
Temperaturdifferenz zwischen der wärmeaufnehmenden Luft und der wärmeabgebenden
Fläche bezeichnet.
Da nun die Temperatur der Wandfläche abhängt:
1) von dem Strahlungscoefficient der Wandfläche = S
2) von der Form der Wand = L
3) von der Dicke der Wand = e
4) von der innern Temperatur = t
5) von der äußeren Temperatur = t''
6) von der Leitungsfähigkeit ihres Materials = C
so müssen alle diese Factoren berücksichtigt werden, wenn man
die Bedingungen untersucht, unter denen diese Temperatur beschränkt wird, und darauf
kommt es eigentlich an, da ja gerade diese Temperatur in der oben angeführten Formel
von Dulong allein bestimmend ist.
Um diese Untersuchung möglichst einfach und dadurch übersichtlicher zu machen, habe
ich für S, L, t'' und t
mittlere Werthe angenommen, welche für die in Rede stehenden Oefen annähernd
passen.
Ich habe gesetzt
S = 0,648
L = 0,4383
t'' = 0
t = 1500°, folglich t ± t'' auch
= 1500°.
Die Werthe von e (Wanddicke) habe ich gesteigert von 5''
bis auf 30'' und endlich C auf drei Werthe gesetzt,
nämlich: 0,084; 0,31 und 0,5; dabei habe ich auch noch die Wärmeleitungsfähigkeit der Luft = 0,024 in
Ansatz gebracht, um den Einfluß von Luftschichten nachzuweisen, wenn man solche
zwischen den Ofenwänden einschließt.
Da ich noch nicht dazu gekommen bin, die Werthe von C
durch genaue Versuche zu bestimmen, so habe ich dafür diejenigen gewählt, welche mit
meinen Erfahrungen an ausgeführten Apparaten am besten übereinstimmen; demnach
gilt
0,5 für gewöhnliche Backsteine, hart gebrannt und mit erheblichem
Gehalt an Eisenoxyd;
0,31 für feuerfeste Steine von ziemlich feinem Korne;
0,084 für ähnliche Massen, welche aber durch organische Stoffe
porös gemacht wurden.
Mit diesen Factoren habe ich eine große Anzahl von Berechnungen durchgeführt und
deren Resultat in den Figuren 1, 2 und 5 graphisch
dargestellt.
Die verticalen Linien in diesen Figuren geben die Wanddicke = e in Zollen = 0,03 Meter an; die horizontalen Linien, welche die Curven
berühren, geben die Wärme-Einheiten an, welche pro 1 Quadratfuß und pro Stunde von der
äußeren Wandfläche an die umgebende Luft transmittirt werden.
Die Curve A, Fig. 1, ist bestimmt durch
die erhaltenen Rechnungsresultate für C = 0,5, und e bei 5'' anfangend und bei 30'' endend;
die Curve B, Fig. 1, ist bestimmt für
C = 0,31, und e bei 5''
anfangend und bei 30'' endend;
die Curve C, Fig. 1, für C = 0,084, und e bei 5''
anfangend und bei 30'' endend;
die Curve D, Fig. 2, für C = 0,31, und e = 5'', dann
C' = 0,5, und e' bei 1''
anfangend und bei 24'' endend; das heißt, die Wand hat gegen das Innere des Ofens
eine 8'' dicke Fütterung von feuerfesten Steinen, die dann in zunehmender Dicke mit
gewöhnlichen Backsteinen (deren Leitungsfähigkeit = 0,5) umkleidet sind.
Die Curve E, Fig. 2, ist basirt auf
eine innere Mauer von feuerfesten Steinen, nämlich C =
0,31 und e = 8''; diese ist mit einem lufterfüllten
Raume von 3'' umgeben, d.h. C' = 0,024 und e' = 3''; endlich besteht die äußere Umhüllung aus
gewöhnlichen Backsteinen, wofür C'' = 0,5 und e'' von 1'' bis 19''.
Die Curve F, Fig. 2, endlich ist
gebildet durch die Berechnung für eine innere Schicht C
= 0,084 und e = 8'', eine Luftschicht C' = 0,024 und e' = 3'',
dann eine äußere Umhüllung C'' = 0,31 und e'' = 1'' bis 19''.
Diese Curven zeigen nun, daß der Einfluß der Leitungsfähigkeit des Materiales weit
bedeutender ist als derjenige der Dicke der Wände, und daß namentlich mit Luft
erfüllte Zwischenräume und hohle oder poröse Steine am meisten dazu beitragen die
Wärmetransmission herabzudrücken; dieser Einfluß macht sich um so mehr geltend, als
bei zunehmender Wanddicke auch die Oberfläche der Wand eine größere wird, wodurch
auch wieder mehr Wärme zerstreut wird.
Um über dieses Verhältniß ins Klare zu kommen, habe ich, wie in den Figuren 3 und 4 im
Längen- und Querschnitte dargestellt ist, die für jeden Zoll zunehmender
Wanddicke entstehende Fläche berechnet und diese Flächen mit dem für je einen
Quadratfuß erhaltenen Werthe multiplicirt; dadurch sind die Curven der Fig. 5
entstanden, welche ebenfalls A bis F benannt sind und den gleichnamigen Curven in den Figuren 1 und
2
entsprechen. Diese zeigen, daß bei gut leitendem Material selbst 3 Fuß dicke Mauern
stets die Transmission vermindern, während bei schlecht leitendem Material durch
dicke Mauern, wegen der vermehrten Oberfläche, dieselbe zunimmt.
In der Wand eingeschlossene Luftschichten oder poröse Steine führen zu demselben
Ziele und sind als analog zu betrachten, denn der poröse Stein enthält ebenfalls
eingeschlossene Luft, welche dieselbe Wirkung hervorbringen muß als wenn sie in
besonderen Räumen enthalten wäre. Da in unseren Berechnungen nur die Factoren C und e veränderlich sind,
und die Endresultate bloß von dem Gliede e/C + e'/C' (siehe Artikel 245 meiner Wärme-Meßkunst)
abhängen, so können wir diese Annahme leicht prüfen.
In der Wand E haben wir 13'' feuerfeste Steinmasse und
3'' Luft, in der Wand C 16'' porösen Stein; wäre nun in
letzteren das Aequivalent von 3'' Luft eingeschlossen, so müßten wir 1,3/0,31 +
0,3/0,024 = 16,7 haben wie für die Wand E; wir haben
aber 1,6/0,084 = 19,0, daher das Material der Wand C
einer Schicht von 3,6'' Luft und 12,4'' Thon gleichkommt, welche gibt: 1,24/0,31 +
0,36/0,024 = 19,0, und ein Kubikfuß dieses porösen Steins würde dann, das
specifische Gewicht des Thons = 1,8 angenommen, wiegen Pfd. 75,33 + 0,016 = 75,346
Pfd., während dieselbe Masse ohne Poren 97,2 Pfd. wiegt, oder das spec. Gewicht der
porösen Masse wäre 1,3953.
Da es möglich ist, poröse Steine von spec. Gewicht 0,7 zu machen, so könnte auch das
Leitungsvermögen C auf 0,0374 heruntergebracht
werden.
Führen wir mit diesem Werthe von C die Rechnung für eine
8'' und 16'' dicke Wand aus, so erhalten wir pro
Quadratfuß 92 und 42 W. E., und für die diesen Wanddicken nach Fig. 4 und 5 entsprechenden
Außenflächen 6624 und 4410 W. E. Fassen wir nun die Ergebnisse für diese beiden
Wanddicken zusammen, so haben wir:
Curve.
Leitungsquotienten.
pro1
QuadratfußW. E.
proOfenflächeW.
E.
–
1,600/0,0374
42
4410
C
1,600/0,084
98
10300
F
0,8/0,31 + 0,3/0,024 + 0,5/0,31 = 1,6/0,098
122
12810
E
0,8/0,31 + 0,3/0,024 + 0,5/0,5 = 1,6/0,1
127
13335
B
1,6/0,31
596
62580
D
0,8/0,31 +
0,8/0,5 =
1,6/0,382
840
88200
A
1,6/0,5
1360
142800
=======
==========
========
–
0,8/0,0374
92
6624
C
0,8/0,084
250
18000
B
0,8/0,31
2071
149112
A
0,8/0,5
6260
440720
Die Aequivalente an trockenem Holze für letztere Zahlen ergeben pro
16'' Wanddicke,
intensive Feuerung,
Pfd. 18;
41;
51;
54;
251;
354
u. 573
8'' Wanddicke,
„
Pfd. 27;
72;
–
–
599;
–
1770
16'' Wanddicke,
Gasfeuerung,
Pfd. 3,8;
9;
11;
11,5;
54;
77;
124
8'' Wanddicke,
„
Pfd. 5,7;
15,6;
–
–
129;
–
382.
Aus dieser Zusammenstellung der erhaltenen Resultate ersieht man, von wie großem
Belang das Durchleitungsvermögen des Materiales der Ofenwände ist, und zugleich
welche bedeutende Brennstoffersparniß durch gehörige Berücksichtigung dieser
Eigenschaft erreicht werden könnte.
Es wird eine Zeit kommen, wo der Hüttenmann eben so gut sein Ofenbaumaterial auf
dessen Leitungsfähigkeit untersuchen wird, als er jetzt seine Erze der chemischen
Analyse unterzieht.
Tafeln
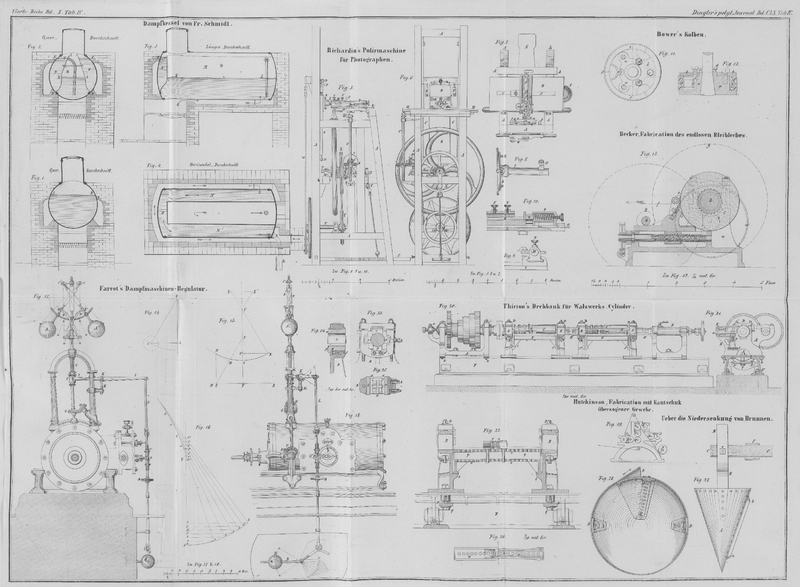