Titel: | Verbesserungen in der Eisen- und Stahlfabrication, von G. Parry auf dem Ebbw-Vale Eisenwerk in Monmouthshire. |
Fundstelle: | Band 166, Jahrgang 1862, Nr. XXIX., S. 127 |
Download: | XML |
XXIX.
Verbesserungen in der Eisen- und
Stahlfabrication, von G.
Parry auf dem Ebbw-Vale Eisenwerk in Monmouthshire.
Aus dem London Journal of arts, August 1862, S.
60.
Mit Abbildungen auf Tab.
III.
Parry's Verbesserungen in der Eisen- und
Stahlfabrication.
Diese Verbesserungen (patentirt in England am 18.
November 1861) beziehen sich auf die Erzeugung eines besseren
Stab- oder Schmiedeeisens, als dasjenige ist, welches bei der gewöhnlichen
Fabrication erhalten wird, sowie auf die Erzeugung von Gußstahl in großen Massen und
von besserer Qualität, als der durch directe Entkohlung von Roheisen wie gewöhnlich
erzielte.
Zu diesem Zweck verwendet der Patentträger Schmiedeeisen, welches vorher dem
Puddelproceß unterworfen wurde und also durch Abscheidung des größeren Theils des
noch darin enthaltenen Schwefels und Phosphors gereinigt worden ist, und bringt
dasselbe mit Kohks in einen mit Gebläse versehenen Schachtofen, welcher dem
gewöhnlich zum Umschmelzen des Roheisens angewendeten ähnlich, aber in Bezug auf die
Formen so eingerichtet ist, daß darin eine viel höhere, als die zum bloßen Schmelzen
des Eisens erforderliche Temperatur unterhalten wird. Auf diese Weise wird die
schnelle und ökonomische Kohlung des angewandten Schmiedeeisens bewirkt. Nach
Beendigung derselben wird das Eisen aus dem Umwandlungsofen in jede beliebige Form
ausgegossen und dann dem Puddelproceß unterworfen, wodurch ein weiterer Antheil
Schwefel und Phosphor entfernt und folglich ein besseres Eisen erhalten wird.
Fig. 17 zeigt
in theilweisem senkrechtem Durchschnitt den zum Kohlen des Schmiedeeisens dienenden
sogenannten Umwandlungsofen. A, A sind die Ofenwände,
B ist eine horizontal blasende Form, C ist eine engere Form, welche unter einen Winkel von
30–45° geneigt ist; D, D sind Formen in
der Nähe der Ofensohle, welche bei der Stahlbereitung zum Durchblasen von Wind durch
das Metall dienen; E, E sind Windkästen zum Speisen der
Formen D, D, welche mit dem Gebläse durch die Röhren F, F in Verbindung stehen.
Beim Kohlen des Schmiedeeisens empfiehlt der Patentträger dasselbe etwa 2 Proc.
Kohlenstoff aus den Kohks aufnehmen zu lassen, worauf es zum nachfolgenden Puddeln
gehörig vorbereitet ist, durch welche Operation es in das „gereinigte
Schmiedeeisen“ verwandelt werden muß.
Nachdem der Umwandlungsofen mit der zum Anheizen hinreichenden Brennmaterialmenge
versehen worden ist, wird er mit etwa 7 Ctr. Kohks (mit hinreichendem Kalkzusatz zum
Schmelzen der Kohksasche) auf jede Tonne Schmiedeeisen beschickt; die einzelnen
Chargen bestehen aus 1 1/4–1 1/2 Ctr. Kohks und 4 Ctr. Eisen (welches am
besten in 4–6 Zoll langen Schienen angewandt wird). Ist der Ofen gefüllt und
das Gebläse angelassen, so muß derselbe während der Dauer der Operation fast voll
erhalten werden, weil sonst das Eisen nicht hinreichend Kohlen aufnimmt und nachher
kein Erfolg durch das Puddeln zu erzielen ist, indem ohne eine gewisse Menge
Kohlenstoff im Eisen das zum Frischen nothwendige „Aufkochen“
nicht stattfinden kann.
Mit einem kleinen Ofen, 2 1/2 Fuß im Quadrat, an den Ecken abgerundet und 10 bis 15
Fuß hoch, welcher mit einer horizontalen Form versehen ist, deren Düse 2 1/2 Zoll
Durchmesser hat, und mit einer geneigten Form von 1 1/4 Zoll Durchmesser, kann man
mit einer Windpressung von 2 1/2–3 Pfd. per
Quadratzoll beiläufig 1 Tonne Eisen stündlich kohlen und abstechen. Bei diesem Theil
des Verfahrens bläst man am besten durch eine oder mehrere Formen C in das Eisen hinab und benutzt dabei die unteren
Formen D, D nicht.
G ist das Schlackenloch am Hinteren Theil des Ofens, H das Stichloch.
Nachdem die Beschickung von gepuddeltem Eisen hinreichende Zeit lang dem Gebläse
ausgesetzt worden ist, um etwa eine Tonne gekohltes Eisen abstechen zu können, so
wird das Stichloch geöffnet und das Metall in Formen gegossen, worauf man es in
gewöhnlicher Weise dem Puddeln unterwirft, wobei die beim ersten Puddeln
zurückgebliebenen Unreinigkeiten entfernt werden.
Das nach diesem Puddeln erhaltene „gereinigte Schmiedeeisen“
kann zu Stäben
ausgewalzt und so in den Handel gebracht, oder auf folgende Weise in Gußstahl verwandelt werden.
Bei der Fabrication von Gußstahl aus Schmiedeeisen wird der beschriebene
Umwandlungsofen ebenfalls angewandt, um das höher gekohlte Eisen darzustellen; aber
die Kohksmenge wird auf beiläufig 5 Ctr. für jede angewandte Tonne Schmiedeeisens
vermindert, wenn man einen harten Stahl zu erzeugen beabsichtigt, und auf beiläufig
4 Ctr. für weichen Stahl. Bei der Fabrication von hartem
Stahl wendet man am besten die Formen B, C
(Fig. 17)
an, ohne die Formen D, D zu benutzen; aber die Düse der
niederblasenden Form C wird vergrößert, indem man ihr 1
1/2 bis 1 3/4 Zoll Durchmesser gibt, um mehr Wind in das Metall am Boden des Ofens
einzuführen, als bei der Darstellung des für den Puddelproceß bestimmten gekohlten
Schmiedeeisens erforderlich ist. Wenn nämlich zu wenig Wind hinabgeblasen wird,
findet man, daß später der Stahl nicht hinreichend flüssig wird.
Zur Darstellung weichen Gußstahls werden zwei der Formen
D, D nebst der gewöhnlichen Form B des Umwandlungsofens angewandt, mit oder ohne die Form
C. Da sich die Formen D,
D unter der Oberfläche des flüssigen starkgekohlten Schmiedeeisens oder
geschmolzenen Stahls befinden, so müssen sie mit Wind von hinreichender Pressung
gespeist werden; 3 Pfd. Druck per Quadratzoll sind für
je 6 Zoll Höhe der Metallschicht ausreichend. Den Zustand des Metalls am Boden des
Ofens kann man theilweise dadurch beurtheilen, daß man durch die Form C einen Eisenstab einführt, oder genauer durch Abstechen
einer Probe desselben. Ist es zu hart, so muß die Windpressung an der Form B vermindert, an den anderen Formen aber entweder
unverändert beibehalten oder etwas verstärkt werden. Ist es hingegen zu weich, so
führt man eine Portion harten Stahl, oder reines Roheisen, oder gekohltes
Schmiedeeisen durch die Form C ein; ebendaselbst kann
man eine geeignete manganhaltige Legirung zusetzen, indem man das Blasrohr gerade
vor dem Abstechen des Ofens zurückbewegt.
Anstatt weichen Stahl im Umwandlungsofen zu bereiten, wie es eben beschrieben wurde,
ist es vorzuziehen, denselben in zwei Operationen zu erzeugen. Man stellt nämlich
zuerst harten Stahl in diesem Ofen dar, und sticht ihn dann in einen andern Ofen
oder Recipient ab, worin man ihn auf den gewünschten Grad von Weichheit zurückführt,
indem man durch das flüssige Metall von unten einen Luftstrom treibt; sollte der so
erzeugte Stahl für die beabsichtigte Anwendung zu weich befunden werden, so versetzt
man ihn mit der geeigneten Quantität harten Stahls in flüssigem Zustande, welchen
man dem Umwandlungsofen entnimmt.
Fig. 18
stellt im senkrechten Längendurchschnitt den Ofen oder Recipient dar, in welchen man
den harten Stahl aus dem Umwandlungsofen abzieht. E, E
sind zwei Windkästen, deren mehrere um den Ofen herum angebracht sind: sie sind
entweder cylindrisch, so daß jeder nur eine Form aufnimmt, oder erweitert zum
Einführen mehrerer Formen. G, G ist das Hauptblasrohr,
welches um den Ofen herumgeht und die Windkästen durch die Röhren F, F speist; D, D sind zwei
der Formen, um Wind durch das geschmolzene Metall zu blasen; H ist das Stichloch zum Entleeren des Ofens, nachdem der Stahl auf den
erforderlichen Grad von Weichheit gebracht ist. Dieser Ofen oder Recipient kann aus
zwei abgestumpften, an ihrer Basis verbundenen Kegeln von Eisenblech hergestellt
werden, oder man gibt ihm noch besser eine parabolische Form, wie die Abbildung
zeigt; er wird mit feuerfestem Material gefüttert, welches man bei I, I, I sieht. Die Charge von hartem Stahl wird in
geschmolzenem Zustand in diesen Ofen durch die oben befindliche Oeffnung J eingelassen, nachdem man das Gebläse abgestellt
hat.
Man kann den Ofen oder Recipient auch durch ein Gasgebläse erhitzen, welches Fig. 19 im
verticalen Durchschnitt zeigt. A ist die
Brennmaterialkammer, welche bis zur Linie D mit kleinen
Kohksstücken gefüllt ist, denen die zum Verschlacken der Asche nöthige Kalkmenge
zugesetzt wurde; die gebildete Schlacke wird am Schlackenloch G abgezogen. B ist ein Blasrohr zur Erzeugung
der Gase, und H ein solches um die Verbrennung der Gase
zu bewerkstelligen, während sie durch das Rohr I in den
Ofen Fig. 18
abziehen; der Gebläsewind zum Verbrennen der Gase kann aber auch an der Oeffnung K direct in das Rohr I
eingeführt werden. Dieser Gasofen ist mit feuerfesten Steinen gefüttert und wird
entweder mit einem Deckel L aus feuerfestem Thon
geschlossen, oder man bringt auf ihm einen Rumpf zum Beschicken mit Brennmaterial
an. Auch das Rohr I ist mit einem schlechten Wärmeleiter
gefüttert. Das Gasgebläse steht auf Rädern, um es leicht vom Ofen Fig. 18 entfernen zu
können. – Nachdem das Einblasen in den Recipient einige Minuten gedauert hat
– die erforderliche Zeit kann der Arbeiter nach kurzer Erfahrung sehr genau
bestimmen – ist der Stahl hinreichend weich geworden, um ihn abstechen und in
Formen gießen zu können. Vor dem Abstechen des Stahls kann man noch geeignete
Legirungen durch die Oeffnung im Deckel J einbringen.
Auch kann man ihm, wenn er zu weich geworden ist harten Stahl, oder reines Roheisen,
oder gekohltes Schmiedeeisen durch dieselbe Oeffnung zusetzen.
Durch dieses Verfahren der Gußstahlfabrication mittelst Schmiedeeisen, welches zuerst
(um den größeren Antheil des darin noch enthaltenen Schwefels und Phosphors
abzuscheiden) gepuddelt und dann mit Kohlenstoff verbunden wurde, wird fast alles
aus englischem Roheisen erzeugte Stabeisen zur Gußstahlbereitung verwendbar.
Tafeln
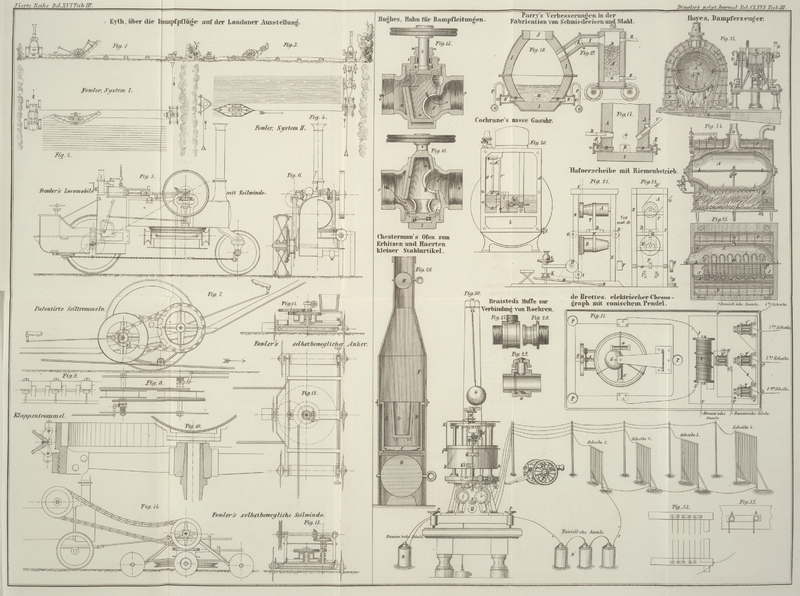