Titel: | Der Gerstenhöfer'sche Röstofen. |
Fundstelle: | Band 193, Jahrgang 1869, Nr. CI., S. 385 |
Download: | XML |
CI.
Der Gerstenhöfer'sche
Röstofen.
Mit Abbildungen auf Tab.
VII.
Gerstenhöfer'scher Röstofen.
Der Gerstenhöfer'sche Röstofen, welcher zuerst 1863 bei
Freiberg versuchsweise angewendet wurde, hat in kurzer Zeit eine weite Verbreitung
gefunden. Indem durch ihn die Verwendung der schwefelhaltigen Erze zur Schwefelsäurefabrication wesentlich erleichtert, in
vielen Fällen aber zuerst möglich gemacht ist, hat er für diesen Zweig der
Metallurgie eine große Bedeutung erlangt, so daß er nicht mit Unrecht als
„epochemachend“ bezeichnet worden ist. Wir geben im
Nachstehenden eine Beschreibung dieses Ofens, wie er auf der Eckardthütte bei
Leimbach im Mandsfeldschen im Betrieb ist.
Der Ofen ist in Fig.
1 – 18 in zwei Durchschnitten
und Details dargestellt. Er besteht aus einem Röstraume A von 4 Fuß 6 Zoll (1,4 Met.) Breite und 12 Fuß (3,77 Met.) Höhe. B ist der Abzug für die flüchtigen Röstproducte (Fig. 3, 4 und 5). In dem
Röstraume A befinden sich außer den drei obersten
Erzvertheilern 15 Reihen Erzträger aus Meißener Thon, jede abwechselnd mit sechs und
sieben Stück (Fig.
13), zusammen 100 Stück. Diese Träger legen sich mit entsprechenden
Ausschnitten auf Vorsprünge der Lagersteine B und D (Fig. 15) an der
Border- und Hinterwand auf, zwischen denen sich die Steine A (Fig. 12 und 15) befinden.
Die Steine C sind an D
angefügt (Fig.
12 und 15). Die Röstgase aus A gelangen durch den
Fuchs e (Fig. 3), den Abzugscanal
B und den Canal g in die
Flugstaubkammern C und E,
und von da in Schwefelsäurekammern. D ist ein
überwölbter Gang durch die Flugstaubkammern E, in
welchem man zu den Ventilen im Windkasten m (Fig. 5) kommen
kann, mittelst deren der Windzutritt in den Ofen durch den Canal l und die Oeffnung a (Fig. 1 und 3) regulirt
wird; n ist das Windleitungsrohr. Der sich in B ansetzende Flugstaub kann durch Oeffnungen q im Gewölbe mittelst langer Spieße beseitigt werden
(Fig.
1).
d, d (Fig. 1 und 3) sind
Erzzuführungsschlitze, b (Fig. 3 und 14) Canäle in der Vorderwand mit
gußeisernen Beobachtungsbüchsen c, welche eine
gewöhnlich mit einem feuerfesten Thonpfropfen f (Fig. 16)
verschlossene Durchbohrung e in ihrer Vorderwand g haben. Die Vorderplatte g
springt gegen die Wände des Hinterkastens h allseitig um
1/8 Zoll (3 Millim) vor, damit die Büchse nach dem Einschieben in das Mauerwerk
besser schließt. Jeder Träger correspondirt mit einer Büchse, und mittelst eines
durch die Durchbohrung e eingebrachten Spießes lassen
sich Ansätze vom Träger entfernen. Außerdem ist s (Fig. 2 und 3) eine größere
Räumöffnung, r ein Rost. h
und i sind Canäle zur Benutzung bei Inbetriebsetzung des
Ofens, k die Ausziehöffnung, p,
p (Fig.
2 und 3) ist die Verankerung des Ofens.
Zur Einführung des Erzes durch die Schlitze d auf die
obersten drei Vertheilungsträger dient die darüber angebrachte Schüttvorrichtung
(Fig. 6
bis 10). Fig. 6 und 9 zeigen, daß
auf der Plattform des Ofens ein gußeiserner, 1 Fuß (0,31 Met.) hoher Kasten a mit 3 Zoll (80 Millim.) breiten Füßen steht, dessen
rechte und linke Wand gerade (Fig. 6), die vordere und
hintere eingeknickt ist (Fig. 9). Nach Aufstellung
desselben wird zunächst die feuerfeste Mauerung innerhalb der Wände noch bis 3 Zoll
(80 Millim.) unter seine obere Kante unter Offenerhaltung der Schlitzräume weiter
geführt, und die rechts von jedem Schlitz entstehende Kante so verbrochen gehalten,
daß eine gekrümmte gußeiserne Platte b (Fig. 6 und 10), welche das Erz nach
den Schüttwalzen leitet, sowohl in der Mauerung, als auch auf Ansätzen des Kastens
eine Unterlage findet. Aus Fig. 17 und 18 ergibt sich
die Art der Befestigung, wo a die Kastenwand, b die Platte und c ein
Winkeleisen bezeichnet, dessen einer Schenkel mit der Platte durch zwei Schrauben
mit versenkten Köpfen und dessen anderer Schenkel mit dem Kasten verschraubt ist.
Nachdem diese Leitplatten gelegt und befestigt sind, werden die Schüttwalzen c durch die in der Vorderseite des Kastens befindlichen
3 1/2 Zoll (90 Millim.) weiten Löcher d (Fig. 7) an die gegenüber
liegenden Lager f (Fig. 8 und 9) geschoben, an der
Vorderwand mit Verschluß g (Fig. 7 und 9) angeschraubt, und das
Zahnrad h mittelst Splintkeiles an die aus dem
Schüttkasten ragende Walzenachse getrieben. Mittelst des Verschlusses g bezweckt man, bei vorkommenden Walzenbrüchen das mit
dem Zahnrad verbunden gebliebene Stück besser heraus nehmen und bequem eine neue
Walze einführen zu können. Aus Vorsorge für dieselbe Eventualität ist auch die
Verbindung des Zahnrades mit der Walze lösbar gemacht, damit man nicht nöthig hat,
bei jedem Bruche auch ein neues Rad mit gießen zu lassen. Zum Schutz der Walzenlager
vor directer Berührung mit der feinen Masse der Beschickung, und um den
Schlitzdeckeln h' (Fig. 6, 8
und 9) ein hinreichendes
Auflager zu gewähren, sind noch über jedes Walzenlager zwei gußeiserne Stücke i (Fig. 6, 8, 9 und 17) gelegt, welche
theilweise in einer Aussparung des Mauerwerkes (Fig. 6), theilweise mit
einem dreiseitig prismatischen Ansatze auf der Platte b
ruhen. Die Schlitzdeckel h' haben zwei Handgriffe; sie
verhindern den directen Abfluß der Beschickung in die Zuführungsschlitze und
bewirken, daß die Beschickung nur allein zwischen Schüttwalze und Leitplatte
hindurch in den Röstschacht gelangen kann, wodurch es möglich ist, daß die
Beschickung per Zeiteinheit stets in gleicher Menge und
nicht über eine gewisse Grenze hinaus in den Röstofen gelangt.
Die zwei Ansätze k (Fig. 7, 8 und 9), an die Vorderwand des
Kastens a angeschraubt, tragen je ein Lager l für eine Welle, an welcher gehörigen Ortes drei
Schrauben ohne Ende sitzen, deren Windungen in die Zähne der Räder h eingreifen. Die Schrauben sind mit einem Stift auf die
Welle gekeilt, welcher im Querschnitt zum Theil in einer Nuth der Welle, zum Theil
in der Nabe der Schraube sitzt. Die auf der einen Seite über das Lager l hinaus ragende Welle trägt hier noch die Scheibe m (Fig. 7 und 9) für einen Laufriemen,
welcher die Kraft auf die Welle überträgt und die Bewegung der Schüttwalzen durch
die Schrauben und die Räder h vermittelt.
Ein auf den eisernen Kasten a aufgesetzter hölzerner
Rumpf n (Fig. 6) versieht, wenn
gefüllt, längere Zeit die Schüttvorrichtung. Das früher vorhandene Sieb o zur Abhaltung gröberer Theile ist beseitigt, weil man
hoffte, die Walzen würden solche Theile zerkleinern, was sich indeß nicht bewährt
hat. Die Schüttwalzen haben in den Rippen einen Durchmesser von 3 Zoll (80 Millim.),
im Walzenkörper einen solchen von 2 Zoll (52 Millim.), bei 3/8 Zoll (10 Millim.)
breiter Walzenrippe.
Behufs Inbetriebsetzung des Ofens bringt man durch die mittlere Oeffnung i (Fig. 2 und 3) 15 bis 16 Roststäbe r ein, verschließt i mit
Ziegelsteinen und Lehm, füllt die Lücken zwischen den einzelnen Roststäben an der
Außenseite mit Gestübbe, bringt durch h Braunkohlen auf
den Rost und entzündet dieselben durch ein Holzfeuer von unten, während die oberen
Oeffnungen a mit Eisenplatten dicht verschlossen werden,
k aber offen bleibt. Damit die Erzträger nicht
springen, muß der Ofen während etwa drei Wochen ganz allmählich in Weißgluth
versetzt werden, wobei man die Feuergase nach Verschließung des Canales g nicht in die Bleikammern, sondern durch einen
seitlichen Canal in eine Esse leitet. Man erhält die Träger zwei Tage in Weißgluth,
und läßt dann die Schüttwalzen langsam an, so daß sie etwa in 5 Minuten einen Umgang
machen. Schon mit dem
Beginne des Anwärmens hat man die Schüttvorrichtung gefüllt, um zu verhindern daß
die Feuergase durch die Schlitze d entweichen. Durch die
Bewegung der Walzen füllen die Erzträger sich allmählich mit der Beschickung bis zum
natürlichen Böschungswinkel derselben, und man feuert noch so lange fort, bis man
durch die Büchsen c beobachtet hat, daß ungefähr die
vierte Querreihe der Träger von unten sich zu füllen beginnt. Alsdann wird ein
Roststab nach dem anderen heraus gezogen, und die entstandene Lücke durch Stein und
Mörtel verschlossen, bis die provisorische Oeffnung i
gänzlich geschlossen ist. Der Aschenraum wird sodann gereinigt, hierauf geschlossen,
und das Ventil m (Fig. 5) behufs der
Windzuführung durch a geöffnet. Das Füllen mit
Beschickung dauert bei dem obigen Walzenumgange etwa 6 2/3 Stunden. Nach Anlassung
der Windes läßt man die flüchtigen Röstproducte noch einige Schichten durch die Esse
abziehen; erst dann öffnet man die Oeffnung g und
verschließt die zur Esse führende Oeffnung. Wie aus Vorstehendem erhellt, fällt die
Röstmasse durch die Schlitze d zunächst auf die Träger,
und sammelt sich auf denselben so lange an, bis sich der der Röstmasse zukommende
natürliche Böschungswinkel hergestellt hat; dann rutschen die weiter ankommenden
Theilchen der Beschickung auf den schiefen Ebenen der Böschung ab, füllen die Träger
der nächst folgenden Reihe, bis der natürliche Böschungswinkel entstanden ist
u.s.f.
Was die Gleichmäßigkeit der Abröstung betrifft, so steht der Gerstenhöfer'sche Ofen den anderen Schachtöfen und besonders auch den
Muffelöfen weit voraus, indem sich, wie dieß bei anderen Oefen nicht der Fall ist,
in allen Horizontalschnitten des Röstraumes gleich viel Beschickung in derselben
Zeit aufhält. Es muß die Beschickung in hinreichend feiner Form aufgegeben werden,
damit in der kurzen Zeit die Abröstung vor sich gehen und die nöthige Hitze zur
weiteren Röstung durch Oxydation des Schwefels entwickelt werden kann.
Während des regelmäßigen Betriebes wird die staubtrockene Beschickung von Rohstein in
Mehl- oder Granalienform mit Schaufeln in den Rumpf der Schüttvorrichtung
geworfen, und mittelst Menschenkraft von einer Kurbel mit Vorgelege mittelst Riemen
die Bewegung bis zu den Schrauben ohne Ende übertragen, welche in die Zahnräder h (Fig. 7) eingreifen. Man
beabsichtigt, die Schüttwalzen später durch eine kleine Dampfmaschine zu bewegen und
dadurch auch dem Siebe im Rumpfe eine stoßende Bewegung zu ertheilen. Da der
Rohstein leicht röstet, so hat man den anfangs erhitzt angewendeten Ventilatorwind
durch kalte, neuerdings sogar durch einfache Zugluft ersetzen können; für einfache,
durch Hitze schwerer zu zerlegende Schwefelmetalle (Zinkblende, Halbschwefelkupfer,
Bleiglanz) dürfte
jedoch heißer Wind beizubehalten seyn. Bei einem Durchsetzquantum von 100 Ctrn. in
24 Stunden hat man durchschnittlich 19 Pfd. atmosphärische Luft per Minute zuzuführen, wornach das Gebläse einzurichten
ist.
Als Gezähe verwendet man zwei Schürhaken von 1/2 Zoll (13 Millim.) Dicke und etwa 5
Fuß (1,57 Met.) Länge zum Aufräumen versetzter Zwischenräume zwischen zwei Trägern
durch die Büchsendurchbohrung e (Fig. 17) hindurch, und
zum Entleeren des Sammelraumes in unter die Oeffnung k
gefahrene Wagen eine Kratze mit eisernem Helme von 4 Fuß (1,25 Met.) Länge. Zum
Reinigen des Abzuges B durch q hindurch dient ein längerer Haken.
In einer 12stündigen Schicht arbeiten vier Mann vor einem Ofen, welche aber auch
gleichzeitig mehrere Oefen bedienen können. Der Sammelraum wird bei einem
Durchsetzquantum von 50 Ctrn. zwei Mal in 12 Stunden geleert, wobei zur Verhütung
der Abkühlung die Oeffnung k mit einem Eisenbleche
versetzt ist, durch dessen schmale Oeffnung die Kratze eingeführt wird, wo dann das
Ausgezogene auf schiefer Ebene in die Wagen gleitet. Das Aufräumen der Zwischenräume
zwischen den Trägern geschieht in 12 Stunden etwa vier Mal; auch wird in jeder
Schicht der Flugstaub in der Höhe des Ofens durch die beiden seitlichen Büchsen mit
dem Haken weggestoßen.
Der Canal nach der Esse wird alle drei Tage von Flugstaub gereinigt. Mittelst einer
fahrbaren Bühne kann man zu den oberen Büchsen gelangen. Das Resultat der Röstung
hängt wesentlich von der Geschicklichkeit und Aufmerksamkeit des mit dem Räumen der
Erzträger-Zwischenräume betrauten Arbeiters ab.
Die höchste Temperatur im Ofen befindet sich bei einem Durchsetzquantum von 100 Ctrn.
in 24 Stunden – womit sich die Geschwindigkeit der Schüttwalzen und die dem
Ofen per Minute zugeführte Beschickung bestimmt –
ziemlich in der Mitte des Schachtes; nach oben hin geht sie in schwache Rothgluth
über, während die untersten Träger gar keine Gluth mehr zeigen. Bei Zutritt von zu
viel kalter Luft rückt die Gluth aufwärts; bei zu wenig Wind sinkt sie abwärts; der
Ofen geht im ersteren Falle zu kalt, im letzteren zu heiß. Bei normalem Gange muß
sich in der heißesten Zone beinahe Weißgluth befinden, wornach man bei eintretenden
Unregelmäßigkeiten entweder Wind absperrt oder die Schüttwalzen sich schneller
drehen läßt. Das Durchsetzquantum ist so zu normiren, daß die in der Zeiteinheit
entwickelte Wärme gerade ausreicht, um die neu in den Ofen tretende Beschickung
abzurosten. Auf Eckardthütte hat sich per 24 Stunden ein
Quantum von 100 Ctr. Rohstein am besten bewährt, wofür 4 Thlr. Löhne im Gedinge
gegeben werden. Tritt durch zu schnelle Oxydation, z.B. bei gemahlenen
Concentrationssteinen, eine Sinterung ein, so muß man die rohen Materialien mit
bereits gerösteten versetzen. Das Anlagecapital für einen Ofen beträgt etwa 1000 bis
1200 Thlr. außer der Entschädigung des Patentinhabers, mit Einschluß der
Dampfmaschine für drei Oefen rund 3600 Thlr.
Wir bemerken zum Schluß noch, daß nach J. R. Wagner's
„Technologischen Studien auf der allgemeinen Kunst- und
Industrieausstellung in Paris im Jahre 1867“ auf Eckardthütte und
Kupferkammer (bei Hettstädt) durch Rösten des Kupfersteines im Gerstenhöfer'schen Ofen eine jährliche Production von 6300 Ctrn.
Schwefelsäure möglich gemacht ist.Hr. Hüttenfactor Nauwerck berichtigt diese Angabe
dahin, daß im Jahre 1867 auf Eckardthütte allein 8069 Ctr. Schwefelsäure
gewonnen sind, während die Fabrik auf Kupferkammer mit Gerstenhöfer'schen Oefen noch keine Schwefelsäure darstellte. Auf
letzterer Hütte waren indessen die Muffelöfen der bisherigen kleinen
Schwefelsäurefabrik mit den Kammern in Verbindung gebracht, und sind in
dieser Fabrik auch 5059 Ctr. Schwefelsäure dargestellt, so daß sich das
ganze producirte Quantum Schwefelsäure der Mansfelder Hütten auf 13128 Ctr.
berechnet. (Zeitschrift des Vereines deutscher Ingenieure, Bd. XIII S.
35.) Ferner ergibt sich aus dem Geschäftsbericht der Mansfeldschen Kupferschiefer
bauenden Gewerkschaft, daß auf den genannten Hütten ein Gerstenhöfer'scher Röstofen so viel Schwefligsäure-Gas erzeugte,
daß der Kammerraum nicht ausreichte, die Umwandlung in Schwefelsäure möglichst
vollständig zu bewirken. Man ist bis zu circa 32 Proc.
Schwefelsäurefall zu 50° Baumé im Maximo gelangt, während circa 40 Proc. hätten erlangt werden können, wenn
größere Kammern vorhanden wären. Die Leistung eines Ofens per Tag hat sich bis circa 200 Ctr. Rohstein
erhöht, während früher auf Grund der in anderen Bezirken gemachten Erfahrungen das
passende Schüttungsquantum nur zu 60 bis 80 Ctr. täglich angenommen werden konnte.
Das Röstmehl war trotz der starken Schüttung so hoch abgeröstet, daß man beim Spuren
Kupferausscheidungen bemerkte, und zur Verhütung derselben, sowie zur Bildung von
circa 65procentigen Spursteinen bis 25 Proc.
ungerösteten Rohstein zuschlagen mußte. Bei dieser Art zu rösten konnte durchaus
nicht constatirt werden, daß in dem Röstmehle mehr Vitriol gebildet war, als bei
schwacher Schüttung. Bedingung des Gelingens sind Zuführung genügender
Oxydationsluft in die Röstöfen und Verwendung trockener, durch Erwärmung von ihrem
Wasser befreiter Granalien.
Dagegen haben nach einer Mittheilung des Hrn. C. Trainer
an den Verfasser die Gerstenhöfer'schen Röstöfen in
Swansea zur Röstung von
Zinkblende sich nicht bewährt, indem sich zu viel Zinkvitriol bildete. (Zeitschrift
für das Berg-, Hütten- und Salinenwesen in dem preußischen Staate, Bd.
XIV, Lief. 1; Zeitschrift des Vereines deutscher Ingenieure, Bd. XII S. 681.)
Tafeln
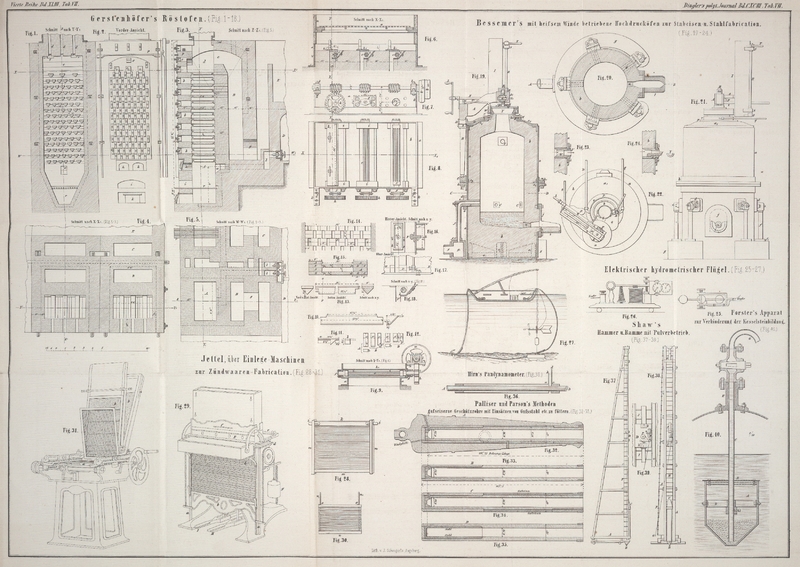