Titel: | Maschine zum Anlassen und Blaumachen von Uhrfedern und Stahlbändern; von Montandon und Söhne, Fabrikanten in Paris. |
Fundstelle: | Band 196, Jahrgang 1870, Nr. VIII., S. 19 |
Download: | XML |
VIII.
Maschine zum Anlassen und Blaumachen von
Uhrfedern und Stahlbändern; von Montandon und Söhne, Fabrikanten in
Paris.
Nach Armengaud's Génie industriel, Januar 1870, S.
44.
Mit Abbildungen auf Tab.
I.
Montandon's Maschine zum Anlassen der Uhrfedern.
Vor einiger Zeit berichtete Armengaud's
Génie industriel in sehr ausführlicher Weise über
die Fabrication von Uhrfedern der Gebrüder
Montandon.Der im Jahrgang 1867 des Génie industriel
enthaltene Bericht über die Uhrfedern-Fabrication der Gebrüder Montandon erscheint dem Referenten noch
jetzt der Mittheilung werth.Welchen Aufschwung diese Fabrik genommen, zeigen am deutlichsten nachstehende
Ziffern.Im Jahre1844erzeugte sie 40,000Stück Pendeluhr und 6,000Dtzd. Taschenuhr-Federn „ „1849 „
„ 70,000 „ „ „ 20,000 „
„
„ „ „1851 „
„ 80,000 „ „ „ 80,000 „
„
„ „ „1855 „
„160,000 „ „ „ 72,000 „
„
„ „ „1862 „
„280,000 „ „ „130,000 „
„
„ „ „1866 „
„800,000 „ „ „180,000 „
„
„Der Verbrauch an Stahl belief sichim Jahre1862auf25,000Kilogrm. „ „1866„58,000„Von den 58,000 Kilogrm. waren 22,000 Kil. englischer Gußstahl und 36,000 Kil.
französischer Stahl.Was den Vertrieb anbelangt, so gingen 3/4 der Erzeugung nach England, Amerika
und Deutschland, 1/4 nach Frankreich, Holland, Spanien und Italien.Bis zu ihrer Vollendung werden bei Taschenuhrfedern 60 und bei Federn für
Pendeluhren 45 aufeinander folgende Operationen vorgenommen.Darstellung des Fabricationsganges.Material. Die Federn für die Kleinuhrmacherei
werden nur aus Gußstahl in Barren, für Großuhrmacherei aus Gerbstahl in
Barren hergestellt. Diese Barren haben gewöhnlich 15 bis 20 Millimeter Dicke
und 1,40 Meter Länge.Walzen der Barren. Die Stahlbarren werden bis auf
1 auch 2 Millimeter heiß, dann aber bis auf die erforderlichen Dicken von
1/10, 1/15, 1/20, 1/30 Millimeter kalt
ausgewalzt; dabei wird das Walzgut 15 bis 20mal ausgeglüht. Die erzeugten
Bänder haben eine Länge von 30, 40 bis 50 Meter und werden nach Breite,
Länge und Dicke sortirt. Der Durchmesser der Walzen beträgt 0,15, die Länge
0,20 Meter.Theilen der Stahlbänder. Für Kleinuhrmacherei
werden 50 verschiedene Breiten geliefert, welche je um 1/15 Millimeter von
einander abweichen; rücksichtlich der Länge (auch Durchmesser: diamètre benannt) sind 22 Abstufungen, im
Ganzen also 1100 Varietäten von Federn.Für Großuhrmacherei sind 60 je um 1/4 Millimeter verschiedene Breiten; die
Länge variirt von 0,75 bis 4,80 Meter, so daß 2131 verschiedene Abstufungen
entstehen.Abgesehen von den Unterschieden in Länge und Breite ist noch die Gestalt der
Federn für einzelne Arten und für verschiedene Absatzquellen
veränderlich.Man schneidet die Stahlbänder mittelst Handscheren oder auf mechanischen
Vorrichtungen.Abschleifen der Federn. Um die Oberfläche wegen
dem nachfolgenden Härten metallisch rein zu machen, werden die Flächen und
Kanten der Federn mit Schmirgelwalzen abgeschliffen; erstere erhalten dabei
eine Längsverschiebung, während letztere sich rasch umdrehen.Härten der Federn. Von allen Arbeiten ist das
Härten jene, welche die größte Sorgfalt beansprucht, weßhalb derselben stets
der Fabrikleiter beiwohnt.Um die Federn zu dieser wichtigen Operation vorzubereiten, werden dieselben
entsprechend gewunden, um das gleichmäßige Durchdringen der Hitze, sowie die
gleichmäßige Abkühlung beim Härten zu erleichtern.Auf einer rotirenden Scheibe von 0,40 Meter Durchmesser lassen sich mittelst
kleiner Keile 11 Blechkämme mit 25 bis 30 Zähnen in verticaler und radialer
Stellung befestigen. Zwischen die Zähne werden die Federn derart gewunden
und mit Draht umschnürt, daß jede Windung von der nächsten getrennt ist.Der Glühofen ist aus feuerfesten Ziegeln mit 3 Quadratmeter Fläche
hergestellt.Für Großuhrfedern ist der Rost des Ofens vertical und ringförmig; das
Brennmaterial (Kohle) liegt außen ringsherum.Wenn der Glühraum eine gleichmäßige Temperatur erreicht hat, so werden die
einzelnen Federpackete in denselben gebracht.Der Ofen für kleine Federn ist dem geschilderten ähnlich; doch ist der Rost
durch eine Glocke von 0,90 bis 1 Meter Durchmesser und 0,30 Meter Höhe
ersetzt; seitlich ist eine durch einen Schieber verschlossene Oeffnung. Als
Brennmaterial wird Holzkohle verwendet.Als Härtebad verwendet man Rüböl mit einer geringen Beimengung von Seife.Anlassen der gehärteten Federn. Die gehärteten
Packete werden aus dem Härtebad genommen, losgebunden und von den Kämmen
befreit.Zur Vorbereitung werden die Federn gescheuert und blank geschliffen. Man
bindet je 12 Stück circa 0,20 Meter vom Ende
entfernt zusammen und erweicht beide Enden durch Ausglühen auf 2 bis 3
Centimeter Länge. Um nun die beim Härten schwarz gewordenen Oberflächen ganz
rein und blank zu machen, folgt ein Abschleifen, jedoch mit großer Vorsicht,
da die Federn hart sind. Man faßt das eine Ende mit einem Feilkloben, breitet
das andere fächerförmig aus, und führt die Federn sanft zwischen zwei mit
feinem Schmirgel überzogene Stücke von weichem Fichtenholz.Das Anlassen selbst, eine Operation welche
bezweckt der Feder die Härte bis auf einen zweckmäßigen Grad (Federhärte) zu
benehmen, erfordert große Uebung, da hiervon die Qualität der Federn
wesentlich abhängt. Zuerst werden 5 bis 6 Streifen mit nahe verschiedenen
Anlauffarben versuchsweise angelassen, z.B.
violett bis dunkelblau, um genau die richtige Farbe für die verwendete
Stahlqualität zu finden.Ist die Farbe bestimmt, so faßt man ein Bündel von je 6 Federn an beiden
Enden mittelst Feilkloben, welche an beweglichen Hülsen befestigt sind.
Diese verschieben sich längs einer schwach gekrümmten Stahlstange, welche
sich gerad zu richten sucht und dadurch die Federn anspannt.Die gespannten Federn werden über ein von unten auf die nöthige Temperatur
erhitztes Eisenstück geführt und hierbei (wenn auch vorher gekrümmt) völlig
gerade.Abrichten und Schleifen der angelassenen Federn.
Da die Kanten der Federn nicht völlig gerade sind, so werden dieselben
abgerichtet. Zwei festliegende Schraubzangen oder Kloben fassen die
hochkantig gespannten und durch Führungswälzchen vor Verrückung gesicherten
Federn. Rotirende, hin- und herbewegte Schleifwalzen bearbeiten die
Kanten.Die kleinen Federn passiren zwei mit je 3 Paar Schleifwalzen versehene
Maschinen, die großen 12 Schleifmaschinen mit je 2 Schleifwalzen. Der
Schmirgelüberzug wird allmählich feiner und feiner, um zu schleifen,
glätten, endlich zu poliren.Rectification der Dicke und Poliren. Die
Cylinderfedern (für Uhren ohne Schnecke und mit Cylinderhemmung) nehmen in
der Dicke von Außen nach Innen hin zu. Wie nun die Dicke beschaffen seyn
mag, werden die in Schraubzangen eingespannten Federn ähnlich wie vorhin auf
Maschinen behandelt, bei welchen der Abstand der Schleifwalzen regulirt
wird.Man prüft jede Feder mittelst eigener Lehren und polirt sie in ähnlichen Maschinen, in welchen die Schleifwalzen
durch Polirwalzen ersetzt sind.Sortiren und Blaumachen. Sind die Federn der
Breite und Dicke nach geprüft, so werden sie mit Hülfe eines
Proportionalmaaßstabes entsprechend der Länge nach getheilt. Hierauf werden
die Enden durch Ausglühen erweicht und mittelst eines Durchschlages mit
viereckigen Löchern zum Einhängen in das Federhaus und an den Federstift
versehen, abgerundet, abgeschliffen, und nochmals polirt, um den durch das
Glühen verlorenen Glanz wieder herzustellen.Nachdem die Federn sorgfältig abgewischt wurden, gibt man ihnen die gelbe,
violette oder blaue Farbe (Blaumachen) auf eine
ähnliche Weise wie dieß vorher beim Anlassen erwähnt wurde.Winden der Federn. Nachdem die erforderliche
Farbe gegeben ist, folgt das Biegen oder Winden der Federn mittelst des
Federwinders. Laßt man die gewundene Feder wieder los, so wickelt sie sich
entsprechend auf. Man prüft die Entfernung der einzelnen Windungen, und wenn
diese die erwünschte Gleichförmigkeit haben, so werden schließlich die eng
gewundenen Federn mit einem Ring von Draht umlegt und sind zum Verkaufe
fertig.
Nachstehend ist ein kürzlich für Montandon und Söhne patentirter Apparat beschrieben, mit welchem das
Anlassen und Blaumachen
der Uhrfedern, überhaupt von Stahlbändern verrichtet wird. Gleichzeitig werden die
angelassenen oder blaugemachten Federn gewunden und es
läßt sich die Geschwindigkeit des Federwinders in der Art reguliren, daß beide
Operationen (Anlassen und Aufwinden) gleichen Schritt halten. Das Princip des
Anlassens der gehärteten Federn ist ein bekanntes, da das Band einfach über eine
erhitzte Eisenplatte streicht, welche auf einem kleinen Ofen liegt.
Montandon's Maschine ist in Figur 11 und 12 in der
Längsansicht, theilweise im Schnitt und im Grundriß dargestellt.
Auf dem Ofen J ruht das gußeiserne Stück K, welches direct von den Flammen bestrichen wird. Die
anzulassende Feder ist auf der Rolle N aufgewickelt,
welche bequem ausgehoben und durch eine frisch bewickelte ersetzt werden kann.
Die Feder streicht über die Eisenplatte K und wird durch
die Presse k niedergedrückt. Um dieß leicht zu
bewerkstelligen, ist der Preßbacken k mit einem Rahmen
l, l¹, und l² in Verbindung, welcher unterhalb halb durch den belasteten Hebel
L nach abwärts gezogen wird. Wenn es erforderlich
ist, wird der Druck der Presse durch Niedertreten der Pedals p aufgehoben.
Die Leitrolle H zwingt das Stahlband der gekrümmten
Oberfläche des Gußstückes K entlang zu streichen und es
gelangt alsdann unmittelbar zur Aufwickelung auf die Spule E, welche auf der Welle D sitzt.
Während die Spule E aufgewickelt wird und deßhalb
– Feder und Nuth mit der Welle D verbunden
– sich umdreht, liefert die benachbarte Rolle E¹ das vorher aufgenommene Stahlband auf die Spule E²,
fest auf der Welle e. Ist nun die Rolle E voll
gewickelt, so wird sie in die punktirt gezeichnete Lage, E¹ aber an die Stelle von E gerückt,
wodurch die Rolle E außer, E¹ hingegen in feste Verbindung mit der Welle D gebracht wird. Alsdann wickelt E¹ neuerdings auf, die Rolle E hingegen
gibt die Feder an die Spule E³ ab. Durch diese
Anordnung findet die Operation des Anlassens und Windens fast ununterbrochen statt.
Die letzten Rollen E² und E³ lassen sich auf der Welle e
verschieben, drehen sich aber stets mit derselben. Die Welle ist beweglich gelagert,
um ohne großen Aufenthalt gehoben zu werden, wenn eine bewickelte Rolle durch eine
frische ersetzt werden muß.
Die Bewegung geht von der Antriebsscheibe P aus, neben
welcher die Leerscheibe P' befindlich ist. Der
Conusriementrieb t treibt die Welle A und diese durch die Zahnräder a, b, c und d die Welle D; von dieser geht die Bewegung mittelst des gekreuzten Riemens g auf die hintere Winderwelle e.
Eine in den Figuren nicht ersichtlich gemachte, verstellbare Riemenleitung verschiebt
zur Veränderung der Aufwindungsgeschwindigkeit den Riemen t. Um auch den Apparat mit der Hand in Bewegung setzen zu können, ist an
der Welle A eine Kurbel M
aufsteckbar. Zu bemerken ist noch die Kuppelung f,
welche mit einem Ausrückhebel verstellt, es möglich macht, die Welle e für eine kurze Zeit (während der Auswechselung der
Rollen E² und E³) in ihrer Drehung zu unterbrechen.
J. Z.
Tafeln
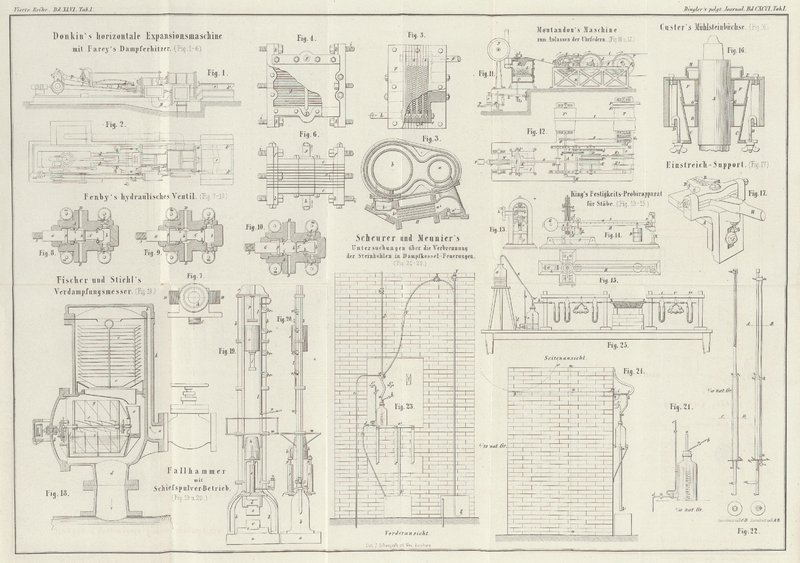