Titel: | Beschreibung der Kupfergewinnung aus Kies-Abbränden im Tyne-District; von Dr. Georg Lunge. |
Autor: | Georg Lunge [GND] |
Fundstelle: | Band 204, Jahrgang 1872, Nr. LXXX., S. 289 |
Download: | XML |
LXXX.
Beschreibung der Kupfergewinnung aus
Kies-Abbränden im Tyne-District; von Dr. Georg Lunge.
Mit Abbildungen auf Tab.
VI.
Lunge, Beschreibung der Kupfergewinnung aus Kiesabbränden im
Tyne-District.
Von wie entscheidender Wichtigkeit für die ganze chemische Groß-Industrie,
wenigstens in England, die Verbindung derselben mit der Gewinnung von Kupfer aus den
Kies-Abbränden von der Schwefelsäurefabrication geworden ist, weiß wohl jeder
chemische Techniker.
Die enorme Steigerung der Sodaproduction in den letzten Jahren wäre vermuthlich ganz
unmöglich gewesen ohne die Einführung der spanischen, portugiesischen und (zum
geringeren Theile) norwegischen Kupfererze, welche ihrerseits nur durch die
Verhüttung auf nassem Wege ermöglicht wurde, weil bei ihrem geringen Gehalte an
Kupfer (2 bis 4 Proc.) die Verhüttung durch den Schmelzproceß in vielen Fällen gar
nicht rentiren würde. Es
war ganz naturgemäß, daß man dann bald dazu schritt, das Erz nicht nach dem weit
entlegenen Swansea zur Verhüttung zu schicken, sondern die Fabriken zur Extraction
des Kupfers in die Nähe der großen Sodafabriken selbst zu verlegen, und so finden
sich denn auch beide meist in zwei großen Gruppen concentrirt, nämlich in
Süd-Lancashire und im Tyne-Districte sin der Nähe von Newcastle).
Im vorigen Jahre hat Clapham einige werthvolle
Mittheilungen über diese verhältnißmäßig ganz neue Industrie gemacht (man s. dieses
Journal Bd. CXCIX S. 302); doch sind seine
Angaben meist nur statistischer Natur und enthalten über den Fabricationsproceß
selbst nur spärliche Notizen. Dieser letztere wird überhaupt selbst an seinen
Ursprungsorten noch häufig in einem gewissen Dunkel erhalten, und es dürfte daher
vielleicht nicht unwillkommen seyn, die Beschreibung des Processes in einer der
größten Fabriken der Art, welche es überhaupt gibt, den Bede
Metal Works zu Jarrow, mit einiger Ausführlichkeit zu
geben, einer Fabrik welche wöchentlich 1000 Tonnen, also jährlich eine Million
Centner Kies-Abbrände verarbeitet und über 500 Arbeiter beschäftigt.
Vorausschicken will ich noch, daß ich die Besichtigung und Erklärung der Fabrik dem
weiter unten vielfach zu nennenden Hrn. Gibb verdanke,
welcher mich auch ermächtigt hat, sein Verfahren mit allen Erläuterungen zu
publiciren, da er für England durch Patente gesichert ist, und vorläufig diese
Industrie auf dieses Land allein beschränkt ist. Auch kann ich seine in der
allerletzten Zeit an die Newcastle Chemical Society
erfolgten, aber noch nicht in allgemeineren Kreisen bekannt gewordenen Mittheilungen
über den Ofen mit Drehherd und seine Analysen im Zusammenhange mit seiner
Kupferfällungsmethode benutzen zur Ergänzung der aus eigener Anschauung gewonnenen
Kenntniß. Es wird daraus ersichtlich werden daß Hr. Gibb,
wenn er auch kein wesentlich neues Princip entdeckt hat, doch verschiedene
Reactionen in ganz neuer, und entschieden höchst zweckmäßiger Weise zu einem im
Großen und Ganzen neuen Verfahren combinirt hat, welches man für einen wesentlichen
Fortschritt in der Technik ansehen muß. Ich muß auch gleich von vornherein bemerken,
daß es sich hier nicht um ein lediglich am Schreibtisch ersonnenes und im
Laboratorium ausgeführtes Verfahren handelt, sondern daß der Fabricationsproceß im
allergrößten Maaßstabe im besten Gange begriffen ist, wie ich dieß vor mir sehen
konnte.
Es wird vielleicht zweckmäßig seyn, der speciellen Beschreibung zunächst einige Worte
über das Princip der nassen Kupferextraction vorauszuschicken, gleichsam das Skelett
welches dann durch die Specialitäten zu einem Körper ausgefüllt werden soll. Das Rohmaterial der
Fabrication bilden die Kies-Abbrände welche diejenigen Schwefelsäure-
(resp. Soda-) fabriken liefern, die mit kupferhaltigen Erzen arbeiten. Es ist
wesentlich daß in solchen Abbränden ein dem Kupfer äquivalenter Antheil Schwefel
zurückbleibe (gleichgültig ob als Sulfat oder Sulfid), eine Bedingung welcher auch
von den bestgeleiteten Schwefelsäurefabriken ganz unwillkürlich immer mehr als
entsprochen wird. Man mahlt die Abbrände zu feinem Pulver, mischt sie mit einer dem
vorhandenen Schwefel entsprechenden Menge von Kochsalz, und röstet das Gemenge bei
so niedriger Temperatur daß das Kupfersulfür möglichst vollständig zu schwefelsaurem
Salz oxydirt wird, während doch kein Eisensulfat entsteht oder bestehen bleibt.
Bekanntlich ist das Kupfersulfat viel beständiger als das Eisensulfat; eine
vollständige Trennung läßt sich aber nur durch die Röstung in Mischung mit Kochsalz
erreichen, indem hierdurch ein großer Theil oder alles entstehende Kupfersulfat sich
gleich mit dem Chlornatrium zu Kupferchlorid (manchmal mit etwas Chlorür) und
Natriumsulfat umsetzt, und man dann nur bedacht seyn muß, möglichst wenig
Kupferchlorid zu verflüchtigen. Dieß sey ausdrücklich bemerkt, weil Henderson früher vorgeschlagen hatte, im Gegensatze dazu,
alles Kupferchlorid zu verflüchtigen und zu condensiren,Man vergl. dieses Journal Bd. CXCIX S.
303 Anm. was aber selbst in den unter seiner Controlle stehenden Fabriken längst
aufgegeben wurde (wenn es je zur fabrikmäßigen Ausführung gekommen ist). Durch bloße
Röstung, ohne Kochsalz, ist es erfahrungsgemäß nicht möglich, alles Kupfer in
löslichen Zustand zu bringen. Gossage's Verfahren (in
diesem Journal Bd. CLIV S. 395) ist ganz
abweichend, und ebenfalls längst aufgegeben; ebenso Longmaid's (dieses Journal Bd. CXXVI S.
156); das oben angedeutete Verfahren der Röstung mit Kochsalz bis zur
Verwandlung (aber nicht Verflüchtigung) allen Kupfers in Chlorid, ist heut zu Tage
das einzige in England gebräuchliche.
Die beim Calciniren entweichenden Gase, welche viel freie Salzsäure (durch Einwirkung
der Schwefelsäure des Eisensulfates auf das Kochsalz), und daneben auch immer etwas
Kupferchlorid enthalten, werden durch einen, den in Sodafabriken gebräuchlichen ganz
ähnlichen Condensationsthurm geleitet, und die condensirte Flüssigkeit wird mit zum
Auslaugen des calcinirten Gemenges verwendet, wobei ihre freie Säure wesentliche
Dienste leistet zur Auflösung namentlich des Kupfers, welches als Chlorür oder Oxyd
vorhanden ist.
Die Auslaugungsflüssigkeit wird dann mit metallischem Eisen, entweder in der Form von Brucheisen oder
von reducirtem Eisenschwamm, behandelt, das metallisch ausgefällte Kupfer gewaschen
und verschmolzen, und die überstehende Mutterlauge fortlaufen gelassen, weil das
Natriumsulfat darin mit zu vielen als Verunreinigung zu betrachtenden Salzen,
namentlich Kochsalz, vermischt ist, um verwendbar zu seyn. In der zu beschreibenden
Fabrik sind jedoch durch Gibb und Gelstharp hierin völlig durchgreifende Verbesserungen angebracht worden,
indem einmal durch Einführung des Ofens mit Drehherd die Röstung und Chlorirung so
vervollkommnet wurden, daß man nicht mit Ueberschuß an Kochsalz zu arbeiten braucht,
und mithin ein reines Natriumsulfat erhält, und zweitens indem das Kupfer als
Schwefelkupfer gefällt wird, in der Weise daß man das eben erwähnte Natriumsulfat zu
Sulfid reducirt, das letztere auslaugt, mit Kohlensäure behandelt und den
entweichenden Schwefelwasserstoff in die Kupferlösung leitet, während man dabei eine
Lösung von kohlensaurem Natron als kostenloses Nebenproduct erhält, und dieselbe
durch Eindampfen und Calciniren auf Soda verarbeitet. Man erspart so nicht nur die
Kosten für das Eisen, sondern erhält auch durch die als Nebenproduct gewonnene
calcinirte Soda noch einen ansehnlichen Gewinn nach Abzug sämmtlicher Unkosten für
die Entwickelung des Schwefelwasserstoffes.
Der Vorschlag von H. Wagner (dieses Journal Bd. CLXXXIII S. 388), Kupfer aus schwachen
Lösungen mit Schwefelwasserstoff zu fällen, welcher aus Schwefelbarium dargestellt
wird, ist in England nie zur Ausführung gekommen, und hat gegenüber dem Gibb'schen Verfahren nicht die mindeste Aussicht auf
Verwirklichung. Dasselbe darf man auch von dem Kopp'schen
Verfahren (dieses Journal Bd. CXCIX S. 400)
sagen, so geistreich auch sonst das letztere ist, und noch viel weniger ist irgend
eine der vielen in Percy's Metallurgie erwähnten Methoden
zur nassen Verhüttung des Kupfers als lebensfähig erkannt worden.
Die chemischen (Soda-) Fabriken senden den Kupferhütten am Ufer des Tyne die
Kies-Abbrände fast sämmtlich per Wasser in
Lichtern zu, und das erste Stadium der Arbeit ist mithin das Entladen der Lichter,
durch einen Dampfkrahn, in Waggons, welche dann auf einer durch Drahtseil und
Trommel betriebenen Bahn über den ziemlich steilen Abhang des Ufers hinausgezogen
und direct in den Raum entladen werden, in welchem die Quetschwalzen stehen. Der
erwähnte Abhang des Ufers gestattet hier, wie in den meisten Fabriken im
Tyne-Districte, die Niveau Unterschiede bei Anlage der Fabriken zu benutzen
und bedeutende Ersparnisse an Hebekosten und Apparaten zu machen. Die Zerkleinerung
der Abbrände geschieht
durch Walzen unter bedeutendem Drucke. Was durch die Walzen hindurchpassirt, wird
durch ein Paternosterwerk in den Oberstock gehoben, und vermittelst eines
Cylindersiebes das Feine von dem Groben gesondert. Die Maschen des Drahtgewebes
haben 8 Oeffnungen per Linear-Zoll. Das Feine
bleibt im Oberstock und entladet sich sofort in eiserne Wagen welche auf einer
Eisenbahn stehen und über die Calciniröfen hinlaufen; das Grobe läuft beständig in
einer eisenblechenen Röhre in den Unterstock zurück und zwischen den Quetschwalzen
durch, so lange bis eine Charge ganz durchgemahlen ist. Dieß ist um so nothwendiger
als schon während dieses Mahlprocesses, zur Erzielung einer recht innigen Mischung,
die erforderliche Menge Kochsalz zugesetzt wird, und mithin jede Charge für sich
allein behandelt werden muß, damit man deren Zusammensetzung genau kennt. Der
Salzzusatz beträgt regelmäßig 7 1/2 Procent vom Gewicht der Abbrände, was für den in
diesen durchschnittlich vorkommenden Gehalt an Schwefel vollkommen genügend ist. Es
wird später noch erwähnt werden, daß bei den mechanischen Oefen (mit Drehherd) kein
weiterer Salzzusatz erforderlich ist, während bei den durch Handarbeit betriebenen
Calciniröfen meist noch ein weiteres Quantum von bis 5 Procent Salz zugesetzt werden
muß. In anderen Kupferextractionsfabriken setzt man sogar 20 Proc. Salz. zu, was
aber viel mehr als nöthig ist.
Das gemahlene Gemisch von Erz und Kochsalz wird durch ein System von Eisenbahnen und
Drehscheiben über jeden einzelnen der Calciniröfen gebracht, und vermittelst eines
eisernen, durch ein horizontales Register verschlossenen Rumpfes nach Bedarf in die
Oefen eingestürzt. Die Anzahl der Calciniröfen beträgt 24, nämlich eine Doppelreihe
von 12 Handöfen (wie ich der Kürze halber in der Folge die durch Handarbeit
betriebenen Oefen nennen will), und eine zweite Doppelreihe von 12 mechanischen
Oefen (d.h. solchen mit Drehherd, wie sie unten beschrieben werden sollen). Die
Oefen sind so gebaut daß immer zwei mit den Fuchs-Enden zusammenstoßen, und
mithin eine Gruppe von der doppelten Länge eines Ofens bilden, bei welcher die
Einfeuerungen an den entgegengesetzten Schmalenden liegen, während die
Arbeitsöffnungen (resp. die Drehmaschinerie) auf derselben Längsseite sich befinden,
und die Füchse in der Mitte zusammentreffen, nur durch eine Scheidewand von einander
getrennt. Sie münden hier abwärts in einen Canal welcher die 6 Gruppen jedes der
Ofensysteme rechtwinkelig unter der Hüttensohle durchkreuzt; die Canäle der beiden
Ofensysteme führen dann in aus Chamottesteinen errichtete Condensationsthürme,
welche ganz genau wie die Thürme für Ofensäure in der Glaubersalzfabrication gebaut
sind, mit einer Füllung
unten von Chamottesteinen und darüber von Kohks. Der Leitungscanal ist einfach aus
Chamottesteinen mit feuerfestem Thon als Bindemittel gebaut, da das Gas viel
trockener als in der Glaubersalzfabrication ist, und eine Condensation und
zerstörende Einwirkung auf den Thon in dem Leitungscanale nicht zu befürchten
steht.
Die Handöfen sind etwa 20 Fuß lang und 9 Fuß breit. Die Feuerungen sind bedeutend
schmäler und die Roststäbe gehen, sowie der Aschenfall, quer über von einer
Längsseite zur anderen ganz durch, so daß von beiden Seiten geschürt werden kann.
Die Kohlen werden durch offene, nur durch sie selbst verschlossen gehaltene
Feuerlöcher nachgefüllt. Von Arbeitslöchern sind für jeden Ofen vier vorhanden, mit
eisernen Rahmen ausgefüttert, und mit eisernen Thüren, im Lichten 10 Zoll breit und
7 Zoll hoch. Die Oefen sind eine eigenthümliche Combination von Muffel- und
Flammöfen, indem sich ein inneres Schutzgewölbe (curtain
arch) unter dem eigentlichen Deckgewölbe von der Feuerbrücke aus durch die
Hälfte des Arbeitsraumes erstreckt; die Flamme wirkt also auf die vordere (der
Feuerbrücke zunächst liegende) Hälfte des Arbeitsraumes nur mittelbar durch das
Schutzgewölbe hindurch, ist dagegen in unmittelbarer Berührung mit der hinteren
Ofenhälfte. Man vermeidet dadurch daß das der Feuerbrücke zunächst liegende Erz
überhitzt wird; in der That kann man deutlich bemerken daß die hintere Ofenhälfte,
wo die Flamme direct wirkt, viel heißer als die vordere, zunächst der Feuerbrücke
gelegene, ist. Eine Ueberhitzung zu vermeiden ist durchaus nothwendig, wenn man
nicht zu viel Kupfer im unlöslichen Zustande behalten will, und aus diesem Grunde
sind von den „Handöfen“ die nach der eben beschriebenen Art
gebauten den ganz offenen Flammöfen vorzuziehen; ganz geschlossene Muffelöfen
verursachen zu viel Kohlenverschwendung, und sind wieder abgekommen wo sie zuerst im
Gebrauche waren. Im Uebrigen stehen auch die besten Handöfen hinter den mechanischen
Oefen so weit zurück, daß man sie wohl auf den Aussterbe-Etat gesetzt
betrachten kann.
Die Hitze in den Oefen ist nicht bedeutend. Das Erz in der hinteren, direct vom Feuer
bestrichenen Hälfte ist nur eben rothglühend, während dasjenige welches unter dem
Schutzgewölbe liegt, bei Tage gar keine deutliche Gluth zeigt. Das Erz wird in
Chargen von 28 Centnern durch einen eisernen Rumpf, wie oben angegeben, in den Ofen
und zwar in dessen hinteren Theil eingestürzt; später wird es nach dem vorderen
Theile zu bewegt, und es befinden sich somit immer je 2 Chargen von 28 Centnern im
Ofen. Es scheint nicht ganz rationell, das frische Erz in den heißesten Theil des
Ofens einzubringen, und dann nach dem kälteren Theile hinzubewegen, aber vermuthlich bewog zu
diesem Verfahren die größere Leichtigkeit der Chargirung in dem offenen Theile des
Ofens, und hat man wohl auch bei Errichtung der Oefen nicht voraus gesehen daß deren
hintere Hälfte heißer als die vordere seyn würde. Selbstredend wird das Röstgut aus
den beiden vorderen Arbeitslöchern herausgezogen, und zwar wiederum in auf
Eisenbahnen gehende Wagen von Eisenblech. Das Abrösten einer Charge dauert etwa 8
Stunden, eher mehr, so daß man in einem Ofen durchschnittlich etwa 40 Tonnen per Woche von 6 (eigentlich nur 5 1/2) Arbeitstagen
fertig machen kann, oder, mit Einrechnung der Stillstände für Reparaturen einzelner
Oefen, 400 Tonnen in allen 12 Oefen. Dazu gebraucht man 3 Arbeiter, welche sich in
Schichten von je 8 Stunden ablösen, so daß also nur ein Arbeiter auf einmal den Ofen
bedient. Die Bedienung dieser Oefen erfordert (im Gegensatze zu den mechanischen
Oefen) eine bedeutende Geschicklichkeit von Seite des Arbeiters, um Ueberröstung zu
verhindern. Die Beendigung der Röstung beurtheilt man in jedem einzelnen Falle durch
Probiren, wobei die Farbenreaction mit Ammoniak angewendet wird, wie später noch
genauer beschrieben werden soll.
Die Beschreibung der mechanischen Röstöfen will ich zunächst mit Gibb's eigenen Worten (in Uebersetzung) geben und meine
Bemerkungen am Schlusse daran anknüpfen.
„Bei dem sogenannten „nassen“
Kupferextractionsverfahren wird die der Auflösung des Kupfers vorhergehende
Röstung der Erze mit Kochsalz bewirkt, indem man die Mischung in einer
oxydirenden Atmosphäre bei dunkler Rothgluth erhitzt, wobei ihre Oberfläche von
Zeit zu Zeit, gewöhnlich durch Handarbeit, erneuert wird. Die Oefen in welchen
diese Operation ausgeführt wird, lassen sich unter drei Classen bringen:
1) Flammöfen, in welchen das Erz direct durch den von der Feuerung kommenden
Luftstrom erhitzt wird;
2) Muffelöfen, in welchen die Hitze durch Mauerwerk zugeleitet wird;
3) aus beiden combinirte Oefen. Dahin gehören Oefen in denen die Flamme zuerst
unter Platten welche die Sohle bilden, geht, und dann durch den Ofen selbst
streicht, und solche welche von dem Flammofen nur dadurch abweichen daß sie ein
„Schutzgewölbe“ von der Feuerbrücke bis zur halben
Ofenlänge haben, welches das der Feuerbrücke zunächst liegende Erz vor
Ueberhitzung bewahrt.“
„Eine Modification des Flammofens deren Zweck der Ersatz der Handarbeit
durch Maschinerie, ferner auch gleichmäßigere Erhitzung und vollkommene Röstung
des Erzes ist, wurde vor Kurzem von Gibb und Gelstharp eingeführt und ist in den Figuren 15 bis 18
gezeichnet:
Fig. 15
ist ein verticaler Querschnitt,
Fig. 16
ein Horizontalschnitt,
Fig. 17
ein verticaler Längsschnitt und
Fig. 18
ein Seiten Aufriß.“
„Der Ofen ist im Wesentlichen ein Flammofen dessen Sohle von einer
kreisförmigen horizontalen Pfanne a, 16 Fuß im
Durchmesser, aus Kesselblech mit Chamotteziegeln gefüttert, gebildet ist. Diese
Pfanne wird von radialen schmiedeeisernen Girders b
getragen, welche auf einer centralen gußeisernen stehenden Welle c befestigt sind.“
„Diese geht in einen Spurzapfen aus und wird in senkrechter Stellung durch
ein Lager e gehalten, in welchem ein oberer Zapfen
der Welle c geht, und welches durch die
röhrenförmigen gußeisernen Arme d getragen wird.
Diese Pfanne a rotirt auf dem centralen Spurzapfen
in ihrer eigenen Ebene, vermittelst einer endlosen Kette f, welche um eine Scheibe g geht, die
unter dem Boden der Pfanne angebracht ist; die Kette wird von einer horizontalen
Welle durch eine Arbeitsscheibe h in Bewegung
gesetzt, und passirt von da über die Leitrollen i, i
zu der horizontalen Scheibe g. Die Ofensohle wird
von einem gußeisernen Pfluge p bearbeitet, welcher
durch den mit dem Querhaupt r verbundenen
schmiedeeisernen Arm o in radialer Richtung in
hin- und hergehende Bewegung versetzt wird. Die Bewegung dieses
Querhauptes ist gleich dem Radius der Ofensohle, und leitet sich von der
Treibwelle ab durch die endlose Schraube k und die
Zahnräder l; das größere der letzteren gibt,
vermittelst der Kurbelwarze und Bleuelstange m, dem
Hebel n eine hin- und hergehende Bewegung,
und das obere gabelförmige Ende von n bewegt
vermittelst in Coulissen gehender Zapfen das Querhaupt r mit der Pflugstange und dem Pfluge. Die Geschwindigkeiten der
kreisförmigen Ofensohle und des Pfluges sind so angeordnet, daß der Pflug
während eines Umganges der Pfanne nicht mehr als um seine eigene Breite
vorrückt, so daß jeder Theil der Ofensohle von dem Pfluge in seinem Hin-
oder Hergange bearbeitet wird. Der Ofen wird vermittelst des Rumpfes s beschickt und er wird ausgeräumt durch die
parallelen Eisenplatten t, welche in schiefer
Richtung über einer radialen Linie auf der dem Pfluge entgegengesetzten Seite
der Ofensohle angebracht sind. Diese Platten sind oben und unten unbeweglich mit
einander verbunden und an einer Kette aufgehängt, so daß sie durch die Decke des
Ofens aus demselben herausgehoben oder in ihn versenkt werden können. Die
Platten sind in Fig. 15 und 16 in der Stellung
zum Ausräumen gezeichnet, wobei sie an eine in der Arbeitsöffnung befestigte
Platte u anstreichen. Wenn die
Ausräumungs-Platten t in dieser Stellung
sind, so wirft eine jede das ihr durch die Umdrehung des Herdes zugeführte Erz
gegen die Peripherie hin in den Pfad der zunächst nach außen stehenden Platte,
von welcher es bei der nächsten Umdrehung wieder weiter nach außen geworfen
wird, bis es schließlich an der Platte u in der
Arbeitsöffnung ankommt, und aus dem Herdrande hinaus auf eine Rinne v geworfen wird, durch welche es auf den Boden
außerhalb des Ofens fällt. Wenn der Ofen in Arbeit ist, werden die Platten durch
die Decke emporgezogen und die Oeffnung durch welche sie passiren wird durch
einen Schieber verschlossen (Fig. 17).“
„Die Arbeit in dem Ofen geschieht folgendermaßen, angefangen damit wenn er
für eine neue Charge fertig ist. Der Herd wird in beständiger Rotation gehalten,
und die Charge (5 Tonnen pulverisirtes Erz mit der nöthigen Menge Salz gemischt)
wird aus dem Rumpf in den Ofen einlaufen gelassen; zu gleicher Zeit wird sie
ausgebreitet, indem man die Ausräumungs-Platten etwa 8 Zoll über dem Herd
aufgehängt hält. Die Platten werden dann aufgezogen und die Ofendecke
geschlossen. Der Herd rotirt zweimal per Minute, und
der Pflug legt seinen Weg nach einer Richtung in 7 1/2 Minuten zurück, wobei er
die Oberfläche des Erzes in einer spiraligen Furche zurückläßt. Die Bewegungen
sind so adjustirt, daß der Pflug bei seinem Rückwege zwischen den bei seinem
Hinwege beschriebenen Linien hingeht, gerade über den erhabenen Stellen, so daß
bei jedem Wege die Furchen an eine andere Stelle kommen und eine neue Oberfläche
der oxydirenden Wirkung der heißen Feuergase ausgesetzt wird. Wenn das Erz
hinreichend geröstet ist, wovon man sich durch Probeziehen versichert, das heißt
in der Regel (wenn Erzrückstände von der unten anzugebenden Zusammensetzung
angewendet werden) in etwa 9 Stunden nach dem Chargiren, werden die
Ausräum-Platten herabgelassen bis sie in Berührung mit dem rotirenden
Herd kommen, und werfen dann das Erz in einem schnellen Strome über die Rinne
hinaus.“
„Die einzige Handarbeit besteht im Feuern und im Adjustiren des Apparates
zum Beschicken und Ausräumen. Ein Mann bedient zwei Oefen, und braucht weiter
keine Erfahrung als im Feuern zu besitzen.“
„Um die chemischen Resultate der mechanischen und manuellen Röstung
vergleichen zu können, wurden Erzmuster wie sie dem Ofen zugeführt wurden und
geröstetes Erz, wie es herauskam, aus zwölf mechanisch und zwölf von Hand
betriebenen Oefen während einer Woche entnommen. Diese Muster wurden erhalten
indem man eine kleine Menge von jedem Erzkarren nahm sowie er die
Zerkleinerungs-Mühle verließ, und ähnliche Mengen von jedem Karren
calcinirten Erzes auf seinem Wege nach den Auslaugkufen. Die Handofen waren von
der unter 3) beschriebenen Art, nämlich mit einem
„Schutzgewölbe“ versehen. Beide Arten Oefen wurden mit
derselben Mischung von Erz und Salz beschickt. Das Erz war gerösteter Kies, und
das Verhältniß des Kochsalzes 7 1/2 Proc. vom Gewichte des ersteren. Wenn man
diese Mischung in dem mechanischen Ofen behandelt, so ist ein fernerer Zusatz
von Salz niemals nöthig; aber in dem Handofen muß man noch Salz zusetzen, mehr
oder weniger je nach der Menge von Schwefel in dem Erze. Im Durchschnitt beträgt
dieser fernere Zusatz an Salz 5 Proc. vom Gewichte des Erzes.“
„Eine vollständige Analyse des Kiesöfen-Rückstandes wurde nicht für
nothwendig gehalten. Die folgende Analyse eines Durchschnittsmusters von einer
sehr großen Quantität ähnlichen Erzes kann als seine allgemeine Zusammensetzung
repräsentirend angenommen werden:
Kupfer
1,78
Eisen
4,88
Schwefel
4,63
Kupferoxyd
2,75
Bleioxyd
0,84
Zinkoxyd
0,47
Kalk
0,28
Eisenoxyd
76,88
Schwefelsäure
5,35
Arsensäure
0,25
Unlösliches
1,40
–––––
99,51
„Kobalt, Wismuth, Silber und Gold sind in kleinen Quantitäten
gegenwärtig.“
„Da der Zweck der Röstung die Oxydation der Sulfüre und die Production von
löslichen Kupferverbindungen war, so wurden die unten angeführten Proben gemacht
als die im Ofen geschehene Arbeit indicirend, und sie sind, zur Vergleichung,
mit denselben Proben zusammengestellt wie sie aus der eben angeführten Analyse
resultiren:
Proben nach derobigen Analyse
Erz- und Salz-Mischung8. bis 15.
Jan. 1872
Kupfer, löslich in Wasser
1,65
1,19
„
löslich in Salzsäure
0,55
0,65
„
unlöslich
1,78
1,31
Schwefelsäure
5,35
5,13
Schwefel
4,63
4,07
Chlornatrium
7,46
„Die Muster von Erz nach der Röstung wurden nicht vollständig analysirt,
sondern mit Wasser und mit verdünnter Salzsäure gewaschen und die Lösungen jede für
sich analysirt, um die Resultate so darzustellen, wie sie beim Oxydiren im
großen Maaßstabe erhalten werden würden:
Mechanischer OfenErz
HandofenErz
Löslich in Wasser
Kupfer Proc.
Kupfer Proc.
Kupferchlorid
4,16
1,96
3,81
1,82
Kupferchlorür
keines
0,19
0,12
Kupfersulfat
1,83
0,81
keines
Eisenprotosulfat
0,15
keines
Eisenpersulfat
0,75
keines
Zinksulfat
2,01
1,95
Kalksulfat
1,29
1,39
Natriumsulfat
9,17
11,13
Chlornatrium
keines
2,64
Löslich in verdünnter
Salzsäure
Kupferchlorür
0,015
0,1
0,33
0,21
Kupferoxyd
0,225
0,18
1,01
0,81
Bleisulfat
Eisenperoxyd
nicht bestimmt
nicht bestimmt
Rückstand
(durch Differenz)
80,40
0,8
77,55
0,11
––––––––––––––––––––––––––––––––––––
sogen, purple oreWesentlich Eisenoxyd, außerdem
Kieselsäure etc. (G. L.)
100,00
3,04
100,00
3,07
Chlornatrium
äquivalent den
Natriumsalzenwie oben
7,56
11,81
„Die folgende Tabelle des Kupfergehaltes in dem verwendeten Kiesrückstande
und beider Varietäten des calcinirten Erzes stellt die Resultate in ihrem
Einflusse auf die Kupferextraction dar. Die Zahlen geben den Totalgehalt an
Kupfer in den verschiedenen Mustern an, welches durch Waschen mit Wasser und mit
verdünnter Säure gewinnbar ist, und den Antheil von Kupfer, welcher im großen
Maaßstabe nicht gewinnbar ist:
Geröstetes Erz
Geröstetes Erz
Kiesrückstand
Mechanische Oefen
Handöfen
Kupfer, löslich in Wasser
37,8
91,1
63,2
„ in verd.
Salzsäure
20,6
6,3
33,2
„ unlöslich
41,6
2,6
3,6
––––––––––––––––––––––––––––––––––––––––––
100,0
100,0
100,0
„Der verhältnißmäßig sehr geringe Antheil von Kupferchlorür und Kupferoxyd
in dem mechanischen Ofen rührt wahrscheinlich von der gleichmäßigen Erhitzung und
der gründlichen Wirkung des Pfluges zum Mischen der Beschickung und zur häufigen
Erneuerung der den Feuergasen ausgesetzten Oberfläche her. Die Gegenwart von
Eisen- und Kupfersulfat in erheblichen Mengen rührt augenscheinlich
daher, daß kein Theil des Erzes in irgend welchem Moment auf längere Zeit in der
Nähe der Feuerbrücke oder der Wirkung der Flamme ausgesetzt bleibt. In dem
Handofen kann die Beschickung von 2 1/2 bis 3 Tonnen Erz selbst von dem besten
Arbeiter nicht mehr als einmal per Stunde umgewendet
werden, und dann ist es auch kaum wahrscheinlich, daß dieß mit annähernd der
Vollständigkeit geschehen würde, mit welcher der Pflug seine Charge von 5 Tonnen
in 7 1/2 Minuten umwendet.“
„Die Resultate wie sie in den Analysen gezeigt sind, beweisen die
verhältnißmäßige Unvollkommenheit der Handarbeit. Die angewendete Menge von
Salz, 11,81 Procent, sollte durch die vollständige Oxydation von 3,23 Procent
Schwefel zersetzt werden, und doch, nach der Röstung in Mischung mit Erz welches
2,05 Proc. Schwefel als Schwefelsäure und 4,07 Proc. Schwefel als Sulfüre
enthält, welche letzteren während der Operation in Gegenwart von Salz und einem
Ueberschusse von erhitzter Luft beinahe ganz und gar oxydirt werden, finden wir
beinahe ein Viertel des Salzes unzersetzt. Hinwiederum, während die 9,17 Procent
zersetzten Salzes äquivalent mit 5 Procent Kupfer sind, finden wir nur 2,15
Procent chlorürt, und 0,81 als Oxyde, aber kein Sulfat. Auf der anderen Seite
finden wir in dem mechanischen Ofen die 7 1/2 Proc. Salz welche angewandt
wurden, vollkommen zersetzt und 2,77 Proc. des Kupfers chlorürt und sulfatisirt,
mit nur 0,18 Proc. als Oxyd. Die Abwesenheit von Sulfaten und Anwesenheit einer
verhältnißmäßig großen Menge von Kupferchlorür in Erz von Handöfen, scheint auf
übermäßige Erhitzung in einem späteren Stadium der Operation
hinzuweisen.“
„Die verhältnißmäßig lange Zeit welche das Erz auf der Oberfläche der
Beschickung der Flammenwirkung ausgesetzt ist, ohne umgewendet zu werden, läßt
es in dem Handofen stärker erhitzt werden, selbst wenn die wirkliche Hitze nicht
größer als in dem mechanischen Ofen ist, in welchem, da die Oberfläche des Erzes
fortwährend wechselt und es nie auf längere Zeit der Feuerbrücke nahe ist, es
kaum möglich ist daß irgend ein Theil der Beschickung überhitzt wird. Bei keiner
möglichen Form des Handofens kann man die Arbeit mit der für Fabrikoperationen
nöthigen Schnelligkeit ausführen und zu gleicher Zeit übermäßige Erhitzung von
einzelnen Stellen des Ofens vermeiden.“
„Daß nur ein verhältnißmäßig kleiner Antheil von Kupfer in dem Röstproduct
von dem mechanischen Ofen Säure zu seiner Lösung beansprucht, ist wichtig, weniger wegen
der leichteren Auslaugung als wegen der Verminderung der zur Auslaugung
erforderlichen Säuremenge. Die Ersparniß an Säure ist nicht von Wichtigkeit an
und für sich, da ja eine hinreichende Menge verdünnter Säure bei der
Condensirung der Gase von den Calciniröfen erhalten wird; aber da diese Gase von
Wismuth- und Arsenchlorür begleitet werden, welche sich bei der
Calcination verflüchtigen, so ergeben sie eine unreine Säure, welche in die
Lösungen eine verhältnißmäßig große Menge dieser Metalle zur Fällung mit dem
Kupfer zurückführt. Das Verhältniß in welchem Arsen und Wismuth zu dem
gewinnbaren Kupfer in den hier betrachteten Erzen stehen, wird am besten gezeigt
wenn man es in Procenten des Kupfers ausdrückt:
Kupfer
2,96 Proc. =
100
Arsen
0,16
5,4
Wismuth
0,01
0,3
„Nicht die ganze Menge dieses Arsens und Wismuthes wird condensirt und in
die Lösungen zurückgeführt; aber wenn man bedenkt daß ein sehr geringer Gehalt
an diesen Körpern die Qualität des Kupfers ernstlich afficirt, und daß die
Gegenwart von nur einem Zehntel der angeführten Menge Arsen in raffinirtem
Kupfer es für die allergewöhnlichsten Verwendungen untauglich machen würde, so
wird es sehr klar, wie wünschenswerth es ist, die kleinst mögliche Menge solcher
Säure in der Auslaugung zu verwenden.“
Zwar wird man, wenn man nicht die ganze Quantität der aus den Rostöfen
gewonnenen schwachen Säure in der Auslaugung des Röstproductes verwendet,
das in dem weglaufenden Antheil enthaltene Kupferchlorid verlieren; aber die
sich mit der Säure verflüchtigende Menge desselben ist so gering, daß ihre
Berücksichtigung sich kaum der Mühe lohnt. (G. L.)
„Die Verminderung der Quantität des Salzes in dem mechanischen Ofen hat,
außer der Ersparung des Salzes selbst, ein noch wichtigeres Resultat in dem
Umstande, daß die bei der Auslaugung des gerösteten Erzes erhaltenen Lösungen
frei von Kochsalz sind, und daß es mithin möglich ist, aus den rückständigen
Lösungen (nach der Fällung des Kupfers G. L.) ein Natriumsulfat zu gewinnen,
welches hinreichend rein zur Sodafabrication ist. Der Unterschied wird
deutlicher, wenn wir betrachten aus was die Salzmischung aus dem Handofen
bestehen würde, nämlich:
Procente des Erzes
Salzmasse = 100
schwefelsaures Natron
11,13
80,8
Chlornatrium
2,64
19,2
––––––––
––––––––
13,77
100,0
„Mit anderen Worten, das reinste Sulfat welches durch irgend welche
einfache Behandlung der rückständigen Lösungen erhalten werden könnte, würde
volle 19 Procent Chlornatrium enthalten.“
Soweit der Bericht des Hrn. Gibb, welchem ich die
folgenden Bemerkungen theils aus seinen weiteren persönlichen Angaben, theils aus
meiner eigenen Anschauung beifügen will.
Der ganze Ofen ist überwölbt, so daß die Seitenwände sich in einem Abstande von einem
Zoll von dem Rande des Drehherdes befinden. Das Mauerwerk reicht bis ganz auf den
Boden, und die unter dem Herde selbst befindliche Maschinerie ist nur durch eine
eiserne, für gewöhnlich verschlossene Thür zugänglich, wodurch sie vor dem (sehr
stark auftretenden) Kohlen- und Erzstaub gesichert wird. Immerhin ist der
letztere noch so bedeutend, daß man von der Anwendung von Zahnrädern zur
Uebertragung der Bewegung auf den Herd abgesehen und dieselben durch eine endlose
Kette ersetzt hat, bei welcher der Staub nicht schadet. Alle Theile der Maschinerie,
namentlich auch die zur Hin- und Herbewegung des Pfluges dienenden, sind
außerordentlich stark gearbeitet, und haben dadurch schon seit 18 Monaten ohne
Reparaturen ausgehalten. Eine Abnutzung findet wesentlich (abgesehen von dem Pfluge)
nur für die Kette statt, welche aus 3/8zölligem Eisen gemacht ist; sie würde auch
für den Spurzapfen der stehenden Welle e sehr stark
seyn, wenn dieser nicht aus bestem gehärteten Stahle gemacht wäre; zur Vorsicht ist
er auch (aus der Zeichnung nicht ersichtlich) so angebracht, daß man ihn leicht
auswechseln kann. Geschmiert wird er durch einen Ueberschuß von Oel, welches durch
eine, von der Hauptwelle getriebene kleine hydraulische Presse bei jedem Umgange des
Herdes in das Spurlager gedrückt wird, und oben wieder in sein Reservoir
zurückfließt. Der (gußeiserne) Pflug muß alle 14 Tage ausgewechselt werden, was
immerhin viel weniger kostet als das in den Handöfen zu Grunde gehende Gezähe. Die
den Pflug hin und her bewegende Maschinerie sieht ziemlich complicirt aus; aber in
Folge ihrer Stärke und ihrer speciellen Einrichtung leidet sie eben nicht. Die
Bewegung geschieht vermittelst der Bleuelstange, welche den oben gabelförmigen Hebel
n treibt; zwischen den Armen der Gabel ist eine sie
quer verbindende Rolle, welche in einer Coulisse wirkt und bei der Umdrehung der
Treibräder vermittelst der Coulisse ein Querhaupt r auf
einer Gleitbahn hin und her bewegt. Dieß ist freilich complicirter als eine einfache
Zahnstange mit Trieb seyn würde; aber wenn man nicht der Maschinerie einen ganz
unmäßigen Raum gönnen wollte, so könnte man nicht vermeiden die Zahnstange in den
Ofen hineingehen zu lassen, wenn der Pflug sich am ferneren Ende seiner Bahn
befindet, und in diesem
Falle würden die Zähne der Zahnstange durch Erzstaub und Oxydation in sehr kurzer
Zeit unbrauchbar werden. Ein weiterer Grund warum sich die Bewegungsmaschinerie des
Pfluges so dauerhaft zeigt, ist der, daß die Bewegung eine so langsame ist (einmal
in 7 1/2 Minuten). Eine Dichtung des Pfannen- (Herd) Randes gegen die
Ofenwände findet in keiner Weise statt; der oben erwähnte Zwischenraum von 1 Zoll
ist vollkommen offen; trotzdem aber schlägt die Flamme nicht über den Rand der
Pfanne, weil umgekehrt fortwährender Zug einen Luftstrom von außen in den Ofenraum
hineinführt. Dieß mag auch dazu beitragen, daß die Maschinerie unter der Pfanne und
diese selbst kälter gehalten und mithin geschont werden; es hat aber den Nachtheil,
einen zu großen Ueberschuß an Luft einzulassen (welche außerdem um die für den Pflug
dienende Arbeitsöffnung reichlich eintritt) und dadurch erklärt es sich auch wohl,
warum der Kohlenverbrauch in den mechanischen Oefen, trotz ihrer größeren
Leistungsfähigkeit (55 Tonnen per Woche gegenüber 40),
doch demjenigen in den Handöfen gleich kommt. Dagegen ist die Ersparniß an
Arbeitslohn sehr bedeutend; ein Arbeiter versieht zwei Oefen, und mithin rösten 2
Arbeiter, in zwölfstündigen Schichten, 110 Tonnen per
Woche, während die 3 Arbeiter des Handofens nur 40 Tonnen fertig bringen. Die
Gesammtproduction aller 12 Oefen, mit Einrechnung der Zeit für Reparaturen, ist 600
Tonnen per Woche. Außerdem ist auch zur Bedienung der
mechanischen Oefen ganz und gar keine Geschicklichkeit, als eine solche im Feuern,
erforderlich, und auch dieß wird fortfallen, wenn, wie dieß beabsichtigt ist,
Gasfeuerung eingeführt wird.
Die Ausräumungsplatten sind von sehr starkem (mindestens 1/20zölligem) Blech
angefertigt und werden vermittelst einer Kette und eines Handkrahnes eingelassen und
ausgehoben; sie sind oben und unten durch starke Schienen unverrückbar mit einander
verbunden, und werden außerdem beim Gebrauche noch durch eine rechtwinkelig durch
sie durchgesteckte, aus beiden Enden des Ofens durchgehende und dort festgehakte
Eisenstange an ihrer Stelle gehalten; dieß fand sich nöthig, weil das Bestreben der
Erzcharge, beim Umgange des Herdes die Platten zu verschieben, statt selbst
ausgeworfen zu werden, bedeutenden Widerstand leistet. Die Platten leiden nicht sehr
stark durch Oxydation, weil sie nur sehr kurze Zeit der Flamme ausgesetzt sind, was
den Gibb'schen Ofen sehr vortheilhaft von Brunton's und von Parkes'
mechanischen Ofeneinrichtungen unterscheidet. Der Spalt im Ofengewölbe, durch
welchen die Platten eingelassen werden, und welcher nur bis zum Centrum reichen
würde, setzt sich ganz querüber fort, um den Beschickungs-Rumpf aufzunehmen
und eine
anderweitige Unterbrechung des Ofengewölbes zu vermeiden.
Die erforderliche Triebkraft wird durch zwei Dampfmaschinen von je 18 Pferdestärken
für alle 12 Oefen geleistet, und es hat sich herausgestellt daß viel schwächere
Maschinen für den Zweck hinreichend gewesen seyn würden. Die Hitze in den Oefen ist
nicht so groß um das Erz am Tage deutlich rothglühend erscheinen zu lassen (nach
eigener Beobachtung). Für bedeutend stärkere Hitzegrade ist es wohl noch
zweifelhaft, ob die Oefen brauchbar seyn würden und ob nicht die Maschinerie unter
dem Herde dann den Dienst versagen würde. Dieß ist zwar für den Kupferproceß
gleichgültig, soll aber demnächst durch Versuche für andere Zwecke entschieden
werden.
Auch bei dem mechanischen Ofen geht man nicht nach der Zeit (welche im Durchschnitt 9
Stunden betragen soll), um die Beendigung der Röstung zu ermitteln, sondern zieht
Proben, wäscht sie mit Wasser und verdünnter Salzsäure (ganz wie im Großen), kocht
den Rückstand dann mit Königswasser, übersättigt mit Ammoniak und läßt absetzen;
indem man immer Probelöffel von demselben Inhalt und Absetzgläser von gleicher Größe
und Gestalt anwendet, erhält man eine für die praktische Arbeit vollkommen
hinreichend genaue Farbenreaction.
Von den beiden Producten welche in den Calciniröfen erzeugt werden, dem festen und
dem gasförmigen, ist über das letztere weiter nichts zu sagen als daß die Gase, wie
schon früher bemerkt, sämmtlich durch Condensationsthürme gehen, bevor sie in den
Schornstein gelangen, und daß die entstehende schwache Salzsäure, welche auch ein
wenig Kupferchlorid (Arsenchlorid etc.) enthält, beim Auslaugen des Röstgutes mit
verwendet wird. Wir wenden uns also gleich zu dem Röstgute selbst, welches in
eisernen Wagen vermittelst schmalspuriger Eisenbahnen und Drehscheiben direct von
den Oefen über jeden der Auslaugbehälter gebracht und von oben in dieselben entleert
werden kann. Das Local in welchem die letzteren stehen, ist um so viel tiefer
belegen daß man natürlichen Fall dafür hat.
Die Auslaugungsbottiche sind inwendig 11 Fuß im Gevierte und 4 Fuß tief, und bestehen
aus starken Holzbohlen welche durch Schraubenbolzen von oben nach unten und seitlich
zusammengehalten werden. Die billigeren Metalle sind für eine so saure Flüssigkeit
selbstredend ausgeschlossen, selbst Blei ist ganz unanwendbar, da es heißer
Salzsäure nicht widersteht; Steinplatten lassen sich aber auch nicht anwenden, weil
dieselben beim Einschütten rothglühender Masse zu leicht springen würden, und
Asphalt etc. würde der letzteren auch nicht widerstehen. Man ist also eben auf Holz angewiesen,
und da es unmöglich ist, solche große Gefäße, bei der rauhen Behandlung welcher sie
ausgesetzt werden müssen, auf die Länge dicht gegen die heiße, saure Lauge zu
halten, so hat man in der beschriebenen Fabrik davon ganz abgesehen und das ganze
Local, unter und zwischen den Bottichen, mit einer dicken Schicht Asphalt überzogen,
die sich nach einem Sammelbrunnen hinsenkt, in welchem alle aus den Fugen der
Bottiche entweichenden kupferhaltigen Laugen sich sammeln und wieder zurückgepumpt
werden können. Man kann in diesem Falle nicht die Bottiche nach der in England für
Sodafabriken ganz allgemeinen Shanks'schen Methode
verbinden, wobei jede Kufe durch ein unter ihren falschen Boden reichendes und in
die nächste Kufe seitlich oben einmündendes Rohr verbunden ist, und eine
selbstwirkende Circulation der Flüssigkeit bei ruhender Masse, durch die
Verschiedenheit in dem specifischen Gewicht zwischen stärkeren und schwächeren
Laugen entsteht. Diese, an sich einfachste und vollkommenste Auslaugungsmethode läßt
sich nur bei porösen Massen, ähnlich der rohen Soda, anwenden, aber nicht bei
dichten und schweren Massen, wie dem hier in Frage kommenden Röstgute. Man ist also
darauf angewiesen, die schwachen Laugen in Sammelbrunnen abzulassen und auf frisches
Röstgut zu pumpen, um sie anzureichern. Das Pumpen (wozu Metallpumpen aber auch
nicht verwendbar sind) geschieht vermittelst eines Druckapparates, im Princip ganz
gleich den bei der Schwefelsäurefabrication angewendeten,Ein solcher ist z.B. von mir im Jahrg. 1871 dieses Journals, Bd. CCI S. 349, beschrieben. wo man durch eine Luftpumpe comprimirte Luft auf die Oberfläche der Säure in
einem geschlossenen Gefäße wirken läßt, und dadurch die Flüssigkeit in einem
Steigrohre in die Höhe treibt – genau dasselbe Princip wie in der
Spritzflasche des Chemikers. Freilich ist man auch für das Druckgefäß wieder auf
Holz angewiesen, und kann daher den Apparat nur für geringe Druckhöhen anwenden;
mehr ist aber auch hier nicht erforderlich. Die Apparate, von denen in den Bede
Metal Works mehrere vorhanden sind, halten immerhin
einen Druck von 30 Pfund per Zoll aus. Man könnte wohl
auch thönerne (Steingut-) Gefäße hier anwenden, aber unmöglich von solcher
Größe wie sie für einen so bedeutenden Fabrikbetrieb nothwendig sind. Für
Leitungsröhren wendet man Thon und Kautschuk an.
Das Auslaugen beginnt mit schwacher Lauge von einer vorhergehenden Operation, welche
sich durch das Einschütten der heißen Masse erwärmt, wird dann fortgesetzt, zunächst
mit heißem Wasser, und schließlich mit der schwachen Säure von den
Condensationsthürmen, welche durch eine Rohrleitung von Kautschuk, mit durch Quetschhähne
verschlossenen Abzweigungen nach jedem Bottiche, überall hingeführt wird wo sie
erforderlich ist. Man macht natürlich die Auslaugung so gründlich wie möglich, und
reichert doch auf der anderen Seite die Laugen thunlichst an; die Laugerei nimmt
daher eine bedeutende Anzahl von Gefäßen und großen Raum in Anspruch. Meist erreicht
man eine Grädigkeit der Lauge von 1,100 spec. Gewicht; ihre Zusammensetzung wird
weiter unten gegeben werden. Der Laugungsrückstand, bekannt unter dem Namen purple ore, besteht im Wesentlichen aus Eisenoxyd,
vollkommen frei von Schwefel, aber gemischt mit allen ursprünglichen (kieseligen
etc.) Verunreinigungen des verwendeten Kieses. Früher hatte man für diesen Artikel
so gut wie gar keine Verwendung, und derselbe häufte sich in enormen Halden in der
Nähe der Kupferextractionsfabriken an; heutzutage aber bildet gerade das purple ore einen wesentlichen Factor der Rentabilität
solcher Fabriken, seitdem es nicht nur als „fettling“ (Futtermaterial) in den Puddelöfen, sondern auch
direct in den Hohöfen angewendet wird. So viel mir bekannt, hat Hr. Berkley, Dirigent der Palmer'schen Hohöfen in Jarrow-on-Tyne, das Verdienst die
directe Anwendung des purple ore in Hohöfen zuerst
durchgesetzt zu haben. Für diesen Zweck wird das purple
ore um so mehr geschätzt, je freier es von kieseliger Gangart ist, und aus
diesem Grunde wird das aus spanischem und portugiesischem Kies stammende Erz dem aus
Norwegen stammenden vorgezogen. Uebrigens wird ein Theil des purple ore in den Kupferfabriken selbst zu Eisenschwamm reducirt, um zur
Fällung des Kupfers zu dienen (s. weiter unten).
Um uns nun zu der Kupferlauge selbst zu wenden, will ich
mich zunächst wieder auf Gibb's Mittheilungen beziehen.
Nach diesem gibt J. A. Phillips die folgende Tabelle für
die durchschnittliche Zusammensetzung der Kupferlauge in den nach gewöhnlicher Weise
mit Handöfen betriebenen Fabriken, in Grains per Gallon
(dessen Inhalt 70000 Grains Wasser entspricht):
Natriumsulfat
10092
Natriumchlorid
4474
Chlor in Verbindung mit schweren Metallen
4630
Kupfer
3700
(davon 405 Grains als
Kupferchlorür)
Zink
480
Blei
40
Eisen
32
Calcium
52
Silber
3,06
Wenn man das Kupfer aus einer Lösung dieser Art durch metallisches Eisen
niederschlägt, so werden die Chloride des Kupfers durch Eisenchlorür substituirt,
und wenn man die von dem metallischen Kupfer abgehende Lauge eindampft, calcinirt
und bei Luftzutritt erhitzt, so wird das Eisenchlorür in Eisenoxyd verwandelt, von
welchem man dann das Natriumsulfat durch Auslaugen trennen kann, selbstredend jedoch
zugleich mit dem Natriumchlorid. Aus einer Lauge von obiger Zusammensetzung z.B.
würde man schließlich ein Salzgemenge erhalten, welches in 100 Thln. 69
Natriumsulfat und 31 Natriumchlorid enthalten würde. Ein solches Salzgemisch, dessen
Gewinnung einigermaßen erhebliche Kosten verursachen würde, ist technisch nicht
verwerthbar, und wesentlich aus diesem Grunde hatte man früher allgemein und hat man
noch jetzt in fast allen Fabriken von seiner Gewinnung überhaupt abgesehen.
Ganz anders stellt es sich dar, wenn man die Laugen betrachtet, welche aus dem mit
„mechanischen“ Oefen erhaltenen Röstgute resultiren, da man
in diesen keinen Ueberschuß an Chlornatrium zu nehmen braucht, und nach der Röstung
dasselbe vollkommen verschwunden ist, wie aus den Gibb'schen Angaben über den Drehherd hervorgeht. Im Gegentheil, ein nicht
unbedeutender Theil des Kupfers befindet sich darin als Sulfat, so daß man, wenn man
die Producte beider Arten Oefen zusammenmischt, das in den Handöfen zurückbleibende
Chlornatrium noch größtentheils umsetzt, und Laugen von folgender Zusammensetzung
erhält (Durchschnitt aus mehrere Tage hindurch genommenen Fabricationsproben, nach
Gibb):
Gramme per Liter
Kupferchlorid
53,2
Kupferchlorür
0,8
Bleisulfat
0,8
Eisenprotosulfat
4,2
Zinksulfat
10,1
Calciumsulfat
5,0
Natriumsulfat
110,9
Natriumchlorid
4,1
Wenn man sämmtliche Natriumsalze = 100 setzt, so würde diese Lösung ergeben:
Natriumsulfat
96,4
Natriumchlorid
3,6
–––––
100,0
Ein solches Gemenge ist zur Sodafabrication vollkommen tauglich, und man sieht daraus
mit einem Blick den enormen Vortheil welchen es gewährt, wenn auch nur die Hälfte der Calciniröfen
„mechanische“ sind, wo dann, wie man aus den oben gemachten
Angaben entnehmen kann, das Verhältniß von mit Handarbeit geröstetem Erz zu dem
mechanisch gerösteten wie 4 : 6 ist. Den vollen Vortheil erhält man freilich erst,
wenn die Fällung des Kupfers nicht mit metallischem Eisen, sondern mit
Schwefelwasserstoff geschieht, nach Gibb und Gelstharp's gleich zu beschreibendem Verfahren.
Die irgendwie erhaltenen Kupferlaugen werden nun zur Abscheidung des Kupfers
behandelt. In allen übrigen Fabriken geschieht dieß vermittelst metallischen Eisens,
und auch in der beschriebenen Fabrik noch theilweise, weil sie noch nicht ganz nach
dem Gibb'schen System umgeändert ist. Manche Fabriken
bedienen sich zur Kupferfällung des Brucheisens, besonders der Abfälle von
Kesselblech; in den größten Fabriken ist dieses jedoch schon längst durch den aus
purple ore reducirten Eisenschwamm ersetzt worden.
Zwar fällt dabei das Kupfer mit allen Verunreinigungen des Eisenschwammes gemengt
aus, aber der doppelte Vortheil des ungemein billigeren Kostenpreises von
Eisenschwamm gegenüber dem Brucheisen, und der fast augenblicklichen Wirksamkeit des
ersteren, überwiegt doch bei weitem. Zur Darstellung des schwammförmigen Eisens
dienen in verschiedenen Fabriken sehr verschiedene Oefen. Man hat früher Muffelöfen
für die besten gehalten, doch ist die zur Reduction des Eisens erforderliche Hitze
so groß, daß nicht nur eine sehr erhebliche Kohlenverschwendung dabei stattfindet,
sondern auch das innere Gewölbe (die eigentliche Muffel) sehr schnell arbeitsunfähig
wird; daher zieht man jetzt Flammöfen vor, bei denen jedoch die Luft durch eine
ziemlich tiefe Kohlenschicht in der Feuerung ihres Sauerstoffes möglichst beraubt
seyn muß; auch müssen sämmtliche Arbeits- (Eintragungs-) Oeffnungen
auf das Sorgfältigste verschlossen und verschmiert seyn. Man nimmt auch in der
Beschickung einen Ueberschuß an Reductionsmittel, nämlich 30 Theile Kohlen auf 100
Theile Eisenoxyd (purple ore). Der Reductionsofen in
jener Fabrik ist auf hohen Pfeilern errichtet, aber mit solcher Benutzung der
Niveau-Verhältnisse, daß die Arbeitsseite viel höher gelegen ist und die
Arbeitsthüren sich mithin in bequemer Höhe befinden, während auf der
entgegengesetzten Seite das Niveau so tief liegt, daß man die Entladungskästen
zwischen den Pfeilern hindurch unter den Ofen selbst einfahren kann. Die Flamme geht
zunächst über die auf der Ofensohle liegende Charge hin, und dann kehrt sie in
Zugcanälen unter der Ofensohle, welche aus Chamotteplatten besteht, zurück. Ein
Entleerungsrohr führt von dem inneren Ofenraume durch den unteren Zugcanal nach
unten, und ist durch einen Eisendeckel in der Art verschlossen, daß es nach Beendigung der Arbeit
durch eines der Arbeitslöcher leicht geöffnet werden kann. Diese Art des Ausräumens
ist von G. Bischof angegeben worden, welcher jedoch
einfache Flammöfen, ohne Zugcanäle unter der Sohle, anwendete. Man schiebt die
Entleerungskästen gerade darunter und läßt die reducirte Masse hineinfallen. Die
Kästen sind viereckig, mit beweglichem, aufklappbarem, aber zunächst festgekeiltem
Boden, im Deckel nur mit einer 6 Zoll weiten Oeffnung versehen, welche sogleich nach
dem Einfüllen des Eisenschwammes durch einen besonderen Deckel verschlossen und
dicht verstrichen wird, um Luftzutritt, und damit Wieder-Oxydation des
Eisenschwammes zu verhindern. Der letztere bleibt in den Kästen bis er kalk genug
geworden ist, um ohne Schaden entfernt werden zu können, und wird dann ausgeräumt
indem man den Keil löst und den beweglichen Boden zurückklappt.
Vor dem Gebrauche wird der Eisenschwamm unter einem Kollergange gemahlen, und dann in
die Kupferlauge eingetragen und darin umgerührt (am besten durch ein mechanisches
Rührwerk), wobei er fast augenblicklich wirkt. Das präcipitirte Kupfer wird dann
ausgewaschen, und geht zu den Schmelzöfen.
Die Fällung geschieht in vier flachen Holzbottichen von elf Fuß im Geviert, welche
für die ganze Fabrik ausreichen würden, auch wenn dieselbe nicht schon großentheils
zur Fällung mit Schwefelwasserstoff umgeändert wäre, nach Gibb und Gelstharp's Verfahren, zu dessen
Beschreibung, wie ich es selbst beobachtet habe, ich nun übergehen will.
Das Princip des Verfahrens ist, zur Fällung des Kupfers
Schwefelwasserstoff zu verwenden, welchen man gewinnt, indem man zu
gleicher Zeit die von dem gefällten Kupfer abgehenden Laugen auf kohlensaures Natron
verarbeitet. Der Einfachheit wegen will ich zunächst die Fällung des Kupfers als
geschehen annehmen, und die davon abgelassene Lauge weiter verfolgen, deren
Zusammensetzung man aus der zuletzt gegebenen Analyse der Kupferlauge mit
Leichtigkeit entnehmen kann. Es versteht sich von selbst, daß man an der Stelle der
Kupfer- und Bleisalze darin freie Säure haben wird; der einzig werthvolle
Bestandtheil darin ist jedoch das Natriumsulfat (Glaubersalz), welches bei Anwendung
der Drehherde eben hinreichend frei von Chlorid ist. Der erste Schritt ist das
Eindampfen der Lauge zur Trockniß, was freilich gleich solche Schwierigkeiten
darbot, daß weniger muthige Techniker davor zurückgeschreckt wären. Nach vielen
Versuchen gelang es jedoch, die große Schwierigkeit, so saure Laugen zur Trockniß zu
bringen, in folgender Weise zu überwinden. Das Eindampfen geschieht in einem
Flammofen, dessen Sohle aus einem umgekehrten Gewölbe besteht. Der ganze innere Raum zwischen dem
Fundamente und der Sohle ist mit „puddle“ (eingesumpftem, geschlagenem und dicht eingestampftem
fetten Thon oder Lehm) gefüllt, so daß er ganz dicht gegen Wasser wird. Darüber ist
dann ein umgekehrtes flaches Gewölbe von Chamottesteinen trocken gelegt, wobei man
die Steine so dicht wie möglich neben einander legt, und die unumgänglichen Fugen
mit trockenem Chamottethon ausfüllt. Dieß verhindert die unmittelbare Berührung
einer bedeutenden Säuremenge und das Wenige was seinen Weg bis zu dem Lehmschlage
findet, wird dort zurückgehalten. Man muß jedoch Sorge tragen daß die Ofensohle nie
ganz trocken wird, sonst entstehen Risse welche sich nur sehr schwer wieder dicht
machen lassen. In diesem Ofen wird die Eindampfung der Lauge fortgesetzt bis sie in
einen dicken Brei verwandelt ist, welchen man mit Schaufeln herausnehmen und in
diesem Zustande nun in einem Calcinirofen gewöhnlicher Construction zur vollkommenen
Trockniß bringen kann. Es ist kaum nöthig zu erwähnen daß die entweichenden Gase,
welche sammtliche freie Säure enthalten, nicht direct in den Schornstein abziehen,
sondern erst durch einen Condensationsthurm gehen. Die calcinirte Masse, welche im
Wesentlichen aus Natriumsulfat (calcinirtem Glaubersalz) besteht (natürlich
verunreinigt mit etwas Kochsalz und den nicht durch Schwefelwasserstoff
präcipitirten Metallen), wird nun zu Schwefelnatrium reducirt. Dieß geschieht in
einem Flammofen mit zwei Arbeitsbetten, ganz ähnlich einem gewöhnlichen Sodaofen.
Man muß natürlich den Luftzutritt durch die Arbeitsthüren etc. möglichst
beschränken, doch braucht man darin durchaus nicht so ängstlich zu seyn als bei der
Herstellung des schwammförmigen Eisens. Man muß sich hüten so stark zu feuern daß
die Masse zum Schmelzen käme. Jede Charge besteht aus 10 Centner Sulfat und 7
Centner Kohlenklein; die Zeit jeder Reduction beträgt drei Stunden, wornach die
gefrittete Masse in einen eisernen Wagen ausgezogen wird, der groß genug ist, um sie
ganz auszunehmen, und dann sogleich mit Sand bedeckt wird, bis sie an die Reihe
kommt in die Auslauggefäße chargirt zu werden. Dieß ist in diesem Falle noch besser
als die bei dem schwammförmigen Eisen angeführten Ausleerungskästen, und der Sand
schadet gar nicht. Eine Durchschnittsprobe aus einer Anzahl Fritten ergab folgendes
Resultat:
Procentigkeitvom ganzenNatrongehalte
Schwefelnatrium
34,86
Natriumcarbonat
2,40
Natriumsilicat
1,64
Natriumaluminat
0,15
–––––
Natron in diesen Salzen, verwerthbar
als Handelswaare
29,90
89,71
–––––
Natriumhyposulfit
0,80
Natriumsulfat
0,66
Natriumchlorid
2,45
Natriumsulfocyanid
0,30
–––––
Natron in diesen Salzen, nicht verwerthbar
2,08
6,22
–––––
Rückstand (tank waste) durch
Differenz
56,74
–––––
100,00
Natron, unlöslich in Wasser
1,36
4,07
–––––––––––
100,00
Das Auslaugen der Masse erfolgt in einem Systeme von vier Eisenblech-Gefäßen,
welche nach Shanks' Methode verbunden und den in
Sodafabriten für die rohe Soda gebräuchlichen ganz ähnlich sind, nur sind sie zur
Verhütung von Oxydation dicht bedeckt. Sie haben Mannlöcher im Deckel und gerade
über dem falschen Siebboden, das letztere zum Ausräumen und theilweisen Einfüllen.
Die mittlere Zusammensetzung des Auslaugungs-Rückstandes wird durch folgende
Analyse repräsentirt:
Schwefeleisen (FeS)
5,26
Schwefelzink
9,00
Schwefelcalcium
4,26
Thonerde
2,22
Kieselsäure
5,16
Natron
2,39
Magnesia
1,24
Kohle
69,70
–––––
99,23
Derselbe wird vor der Hand nicht nützlich verwendet, obwohl der Zinkgehalt desselben
möglicher Weise einmal Veranlassung dazu geben dürfte.
Die resultirende Lauge, deren wesentlichster Bestandtheil Schwefelnatrium ist, darf nicht stärker als von
1,20 spec. Gewicht gemacht werden, weil sie sonst Krystalle auszuscheiden anfängt,
welche die Löcher in den gleich zu erwähnenden Siebböden der
Carbonatirungs-Gefäße verstopfen; sie setzt sich erst in bedeckten Klärkästen
ab, und wird dann in eine Reihe von dicht geschlossenen eisernen Kästen gepumpt,
worin sie mit Kohlensäure behandelt wird. Die Kohlensäure
wird auf die folgende, ganz eigenthümliche Weise erhalten. In einem stehenden, einem
Kupolofen ähnlichen Cylinder von starkem Eisenblech mit Chamottefütterung befindet
sich eine Schicht glühender Kohks von sechs Fuß Höhe. Eine doppeltwirkende
Gebläsemaschine treibt Luft mit einem Drucke von 7 Pfd. per Quadratzoll durch die Kohks, welche in Folge ihrer tiefen Schichtung
die anfangs gebildete Kohlensäure fast vollständig als Kohlenoxyd oben auslassen.
Dasselbe (mit dem Stickstoff der Luft) wird durch ein eisernes Rohr herab und
seitlich in den Boden eines dem ersten ganz ähnlichen Kupolofens geführt, welcher
mit Kalkstein gefüllt ist. Dicht vor dem Eintritte des Gases wird ihm atmosphärische
Luft beigemischt, jedoch in nicht ganz hinreichender Menge um alles Kohlenoxyd zu
verbrennen, so daß nur die Hauptmenge des letzteren in Kohlensäure übergeht, und bei
regelrechtem Betriebe gar kein freier Sauerstoff übrig bleibt. Die an und für sich
heißen, und durch die Verbrennung des Kohlenoxydes noch viel mehr erhitzten Gase
zersetzen den Kalkstein und reichern sich bedeutend mit Kohlensäure an, nämlich von
15 oder 16 auf 21 Volumprocente. Das oben austretende Gemisch von Kohlensäure, etwas
Kohlenoxyd und Stickstoff, wird in einer 2 Fuß weiten Röhre abgeleitet und zunächst
durch einen Wasserbehälter geführt, um gekühlt und gewaschen zu worden. Von da geht
es nun, noch immer unter dem Druck der Gebläsemaschine, zu den die
Schwefelnatriumlauge enthaltenden Eisengefäßen. Die jetzt auf 6 Zoll
zusammengezogene Rohrleitung ist derartig eingerichtet, daß man das Gas nicht nur
beliebig in jedes einzelne Gefäß, sondern auch in jede beliebige Combination der
(fünf) Gefäße leiten kann; ebenso kann man mit dem austretenden Gemisch von
Kohlensäure und Schwefelwasserstoff, oder fast reinem Schwefelwasserstoff (vom
Stickstoff abgesehen) verfahren, und dasselbe entweder in jedes einzelne, oder
mehrere Gefäße einleiten, oder in das zu den Kupferfällungsgefäßen gehende Hauptrohr
ableiten. Es läßt sich wohl denken daß dieß eine ziemlich complicirte Einrichtung
erfordert, und in der That hat es sich auch unmöglich gezeigt, den Zweck mit weniger
als vier Absperrventilen für jedes der fünf Gefäße, im Ganzen also 20, zu erreichen
(wie sogleich zu beschreiben). Die sechszölligen Ventile sind durch Zahnstangen
bewegte senkrechte Schieberventile, wie sie vielfach in Gasfabriken für die
Hauptleitungen angewendet werden. Die Arbeit wird so geführt daß das frische Gas immer zuerst durch
einen Behälter geht dessen Inhalt schon nahezu umgesetzt ist, und darauf durch einen
frisch gefüllten; alsdann ist es hinreichend mit Schwefelwasserstoff gesättigt, und
mehr als zwei Kästen in einer Reihe braucht man nicht anzuwenden. Es bleibt dann in
dem Gase nur 1 Proc. Kohlensäure zurück, also 5 Proc. von der ganzen ursprünglich
vorhandenen Menge desselben.
Das Gas wird durch ein Rohr auf den Boden jedes Kastens geführt, unterhalb eines
falschen Siebbodens welcher den einzigen Zweck hat es in feine Blasen zu zertheilen.
Das Gas tritt dann oben aus, und in den zweiten Kasten ebenfalls unter dem Siebboden
ein. In dem horizontalen Haupt-Zuleitungsrohre (für Kohlensäure) ist je ein
Ventil für jeden Kasten enthalten (zwischen je zwei Kästen), dann ein senkrecht
absteigender Zweig mit Ventil Nr. 2, sich bis unter den Siebboden fortsetzend; dann
ein Ausführungsrohr, welches sich in zwei Theile spaltet, und einen Zweig (mit
Ventil Nr. 3) in das Zuleitungs-Hauptrohr und einen anderen (mit Ventil Nr.
4) in das Ableitungs-Hauptrohr (für Schwefelwasserstoff) absendet. Beide
Hauptrohre enden nicht blind, sondern kehren in sich selbst zurück, und auf diesem
Wege ist es eben möglich, die Gase nach Belieben zu hanthieren und einen Kreislauf
wie oben beschrieben eintreten zu lassen. Einen Geruch von Schwefelwasserstoff
konnte ich nirgends, auch nicht unmittelbar auf den Kästen, verspüren; dieß kann
auch nicht Wunder nehmen, da alle Gefäße vollkommen dicht selbst gegen Druck seyn
müssen, bis zu den Kupferfällungs-Gefäßen hin, und die Bewegung der Gase
durch das ganze System nur durch den anfänglichen Druck der Gebläsemaschine
erfolgt.
Die Wirkung des Gases auf die Schwefelnatriumlösung ist im Wesentlichen die, daß
dasselbe in kohlensaures Natron umgesetzt wird. Nur 1/4 Proc. des Natrons setzt sich
in unterschwefligsaures Salz um, weil doch Berührung mit Luft nicht absolut
ausschließbar ist, und etwa 2 Proc. bleiben als Sulfür zurück. Die umgesetzte Lauge,
welche schwach nach Schwefelwasserstoff riecht, wird in Klärgefäße abgelassen und
dann in Pfannen mit oberschlächtigem Feuer bis zur Breiconsistenz eingedampft, in
eiserne Filter herausgezogen und das abgetropfte Salz in Calciniröfen getrocknet;
Alles in Apparaten und nach dem Verfahren genau eben so wie in den Sodafabriken des
Districtes. Aus eigener Anschauung konnte ich mich überzeugen, daß die erhaltene
calcinirte Soda ihrer Farbe oder sonstigem Aussehen nach vollkommen mit dem Producte
gewöhnlicher Sodafabriken concurriren kann; ihre Zusammensetzung ist nach Gibb die folgende (bei regelrechter Entwickelung der
Kohlensäure, wie oben beschrieben):
Natrium-Carbonat
„ Hydrat
„ Silicat
„ Aluminat
„ Sulfit
86,120,000,550,100,26
VerwerthbaresNatron51,48 Proc.
„ Sulfür
0,00
„ Sulfat
7,23
„ Chlorid
4,38
Calciumcarbonat
0,06
Eisenoxyd
0,05
Unlöslich
0,88
–––––
99,63
Wir verfolgen jetzt den Schwefelwasserstoff auf seinem Wege. Er trifft mit der vom
purple ore abfließenden Kupferlauge zusammen, in
hölzernen Gefäßen von 11 Fuß im Quadrat, vier an der Zahl, welche dicht bedeckt
sind, weil das Gas noch immer unter etwas Druck steht, von dem Gebläse herrührend;
doch findet dieß immer nur in dem ersten der zwei zusammenwirkenden Gefäße statt;
aus dem zweiten entweicht das Gas in's Freie. Dem Princip nach sind diese Gefäße
genau so angeordnet wie die Eisenkästen für Schwefelnatriumlauge, nämlich so daß man
das Gas in jede beliebige Combination von Gefäßen einleiten und aus ihnen ausleiten
kann; auch hier arbeiten immer zwei Gefäße zusammen. Die eisernen Zweigrohre mit
Ventilen sind aber hier durch weite Kautschukröhren mit Quetschhähnen ersetzt. Auch
ist kein Abführungsrohr erforderlich, sondern jedes Gefäß hat ein hölzernes, durch
das Dach gehendes Abführungsrohr für sich. Der Schwefelwasserstoff ist nach dem
Passiren einmal durch schon halb gefällte und dann durch frische Lauge so
ausgenutzt, daß man in dem Abführungsrohre durch den Geruch nichts mehr davon
wahrnehmen kann.
Nach beendigter Fällung wird die ganze Masse, Flüssigkeit und Niederschlag zusammen,
in unterstehende Kufen abgelassen, und dann durch einen hölzernen Luftdruckapparat
(monte-jus) wie oben beschrieben in die
Filter gepreßt. Das Filtriren des zarten Schwefelkupferschlammes verursachte anfangs
große Schwierigkeiten, wird aber jetzt durch die sogen. Needham'schen Filter auf die folg ende Weise bewirkt. Jeder der beiden im
Gebrauch befindlichen Filtrirapparate besteht aus 24 Platten von etwa 8 Fuß Länge
und 2 Fuß Höhe, welche auf der schmalen Längskante stehen, und so zusammengesetzt
sind daß das Ganze einen Block von etwa 8 Fuß im Quadrat und 2 Fuß Höhe bildet. Jede
Platte ist mit dicht neben einander liegenden Furchen von oben nach unten versehen
(welche also der schmäleren Dimension parallel laufen), und außerdem stehen der obere und die beiden
Seitenränder etwas vor, so daß beim Zusammenfügen der Platten nur diese Ränder
zusammenpassen und ein gewisser Raum auch zwischen den erhabenen Theilen der Furchen
bleibt; dieser freie Raum beträgt etwa einen Zoll. Außerdem sind Vorrichtungen
angebracht um die Platten nach dem Zusammensetzen durch Schrauben zusammenzupressen
und in ihrer Stellung zu erhalten. Ehe sie aber zusammengefügt werden, kommt
zwischen je zwei Platten ein Flanellsack welcher über den ganzen inneren Raum
weggeht. Er ist nur oben geschlossen, und dort in seiner Mitte mit einer Röhre
versehen, welche aus einem in den oberen Leisten der Platten ausgesparten Loche der
Platten herausragt; an den Seiten und der Unterkante ist der Sack offen, wird aber
durch mehrfaches Uebereinanderfalten der Kanten temporär geschlossen. Dieß
geschieht, indem die eine Platte horizontal liegt; sie wird dann mit dem Sacke an
ihre verticale Stelle gebracht, ein neuer Sack auf die nächste Platte gelegt,
gleichfalls neben der vorigen aufgerichtet, und so fort. Wenn das Ganze
zusammengefügt ist, so ragen die 24 Rühren alle oben heraus, und werden nun durch
Kautschukschläuche mit ebenso vielen Zweigen eines Druckrohres verbunden, welches
von dem eben erwähnten hölzernen monte-jus
herkommt. Sobald der letztere in Thätigkeit gesetzt wird, wird der
Schwefelkupferschlamm in alle 24 Filtersäcke hineingepreßt, bis diese vollkommen
damit ausgefüllt und in die senkrechten Furchen der Platten hineingepreßt sind. Die
Flüssigkeit (saure Lösung von Natriumsulfat etc.) läuft unten ab, wo ja die Ränder
der Platten einen Zwischenraum zwischen einander lassen, und wird auf dem
asphaltirten, nach einer Seite abschüssigen Boden in einen Sumpf geleitet, aus
welchem sie in den oben beschriebenen Abdampfofen mit Lehmschlag kommt, um als
Rohmaterial für Glaubersalz-, Schwefelnatrium- und
Soda-Darstellung zu dienen. Wenn nichts mehr abläuft, werden die Schrauben
gelöst, die Platten eine nach der anderen weggenommen, waagrecht hingelegt, die
Flanellsäcke auseinander gefaltet, der Schwefelkupferschlamm mit Schaufeln
ausgehoben, und die Säcke sofort wieder in derselben Weise zusammengefaltet, so daß
die Platten und Säcke augenblicklich wieder bereit sind, zur neuen Instandsetzung
des Apparates senkrecht neben einander gestellt zu werden. Zur Bedienung der beiden
Filter, welche die ganze Arbeit der Fabrik besorgen, sind vier Mann erforderlich.
Der Kupferschlamm enthält natürlich noch immer etwas Mutterlauge eingeschlossen,
welche man jedenfalls besser auswaschen würde (z.B. durch Aufrühren mit Wasser und
erneutes Filtriren); vor der Hand geschieht dieß aber nicht (so daß man darin 15
Proc. des Glaubersalzes verliert); vielmehr kommt der Schlamm sofort in die
Kupferöfen. Die Needham'schen Filter leisten nicht alles
Wünschenswerthe, und Gibb ist beschäftigt sie durch
geschlossene Holzkästen von 11 Fuß im Quadrat zu ersetzen, mit falschem Boden, in
welchen über dem Doppelboden ein Druck von 50 Pfund per
Zoll ausgeübt werden soll, um den Schlamm möglichst von Mutterlauge zu befreien. Die
Herstellung von Holzgefäßen, welche einem solchen Drucke widerstehen, ist natürlich
sehr schwierig. Die Kupferöfen sind genau dieselben wie sie in Swansea üblich und
z.B. durch Percy's Metallurgie allgemein bekannt geworden
sind.
In dem ersten Bande des erwähnten Werkes (deutsche Ausgabe, bearbeitet von Dr. Fr. Knapp, S. 384 ff.)
finden sich ausführliche Zeichnungen und Beschreibungen der Kupferöfen und der
Arbeit nach dem Swansea'schen Verfahren. Es sey also nur erwähnt daß man aus dem
rohen Schlamme in dem ersten Ofen auf Stein schmilzt, dann in dem zweiten Ofen den
Stein in Rohkupfer (blister copper) und in dem dritten
auf Garkupfer (refined copper) verarbeitet. Das Kupfer
verläßt die Fabrik entweder in diesem Zustande, oder wird durch Walzwerke zu Blech
oder Stangen verarbeitet. Das Blech erhält in Folge des beim Auswalzen nöthigen
Ausglühens einen stahlgrauen Ueberzug von Oxyd, welchen man leicht durch Beizen
entfernen könnte, wornach die rein rothe Farbe des Kupfers hervortreten würde. Im
Handel (wenigstens in England) wird aber nicht diese rein rothe Farbe, sondern eine
eigenthümlich fleckige, schillernde Oberfläche verlangt, und man erhält diese indem
man die Bleche in Urin wäscht, in einem Flammofen kurze Zeit erhitzt, beim Ausziehen
in Wasser ablöscht und die Bleche in aufrechter Stellung an den Ofen gelehnt
trocknen läßt. Der Urin wirkt vermuthlich theilweise durch den bei seiner Fäulniß
entstehenden Ammoniakgehalt zur Auflösung des Oxydes, theils durch seine organische
Substanz zur Reduction desselben im Flammofen, was aber nicht ganz gleichmäßig vor
sich geht und durch Uebrigbleiben einer dünnen Oxydulhaut das Schillern
verursacht.
Ehe ich von dem Gibb'schen Verfahren scheide, will ich
anführen daß bei demselben der Verbrauch an Kohlen zur Reduction von Schwefelnatrium
etc. geringer als bei Anwendung von Eisenschwamm ist, und die Soda einen reinen
Gewinn darstellt.
Ich will schließlich noch als bemerkenswerth erwähnen daß die Fabrik eine große Menge
von Blech in Form von kreisrunden Stücken (9 Zoll, 12 Zoll und darüber im
Durchmesser), in Stößen zusammengebunden, zum Export nach Indien verschickt, wo die
einheimischen Kupferschmiede es in die vielen im Orient so beliebten Formen von
Kupfergefäßen treiben können, ohne Abschnitzel zu haben. Zur Herstellung dieser
kreisförmigen Bleche dient eine Circularschere (ganz ähnlich den in der
Maschinenpapier-Fabrication gebräuchlichen), welche auf einer Bank befestigt ist. Auf
derselben Bank ist eine horizontal rotirende Scheibe angebracht, jedoch auf einer
Laufschiene, so daß man sie in beliebiger Entfernung von der Kreisschere durch
Schrauben feststellen kann. Das in viereckige Stücke roh vorgeschnittene Blech wird
auf die Drehscheibe gelegt, und während deren Rotation von der Circularschere
beschnitten, so daß es in Form eines Kreises herauskommt. Die Abschnitzel werden
natürlich immer wieder eingeschmolzen und ausgewalzt.
Tafeln
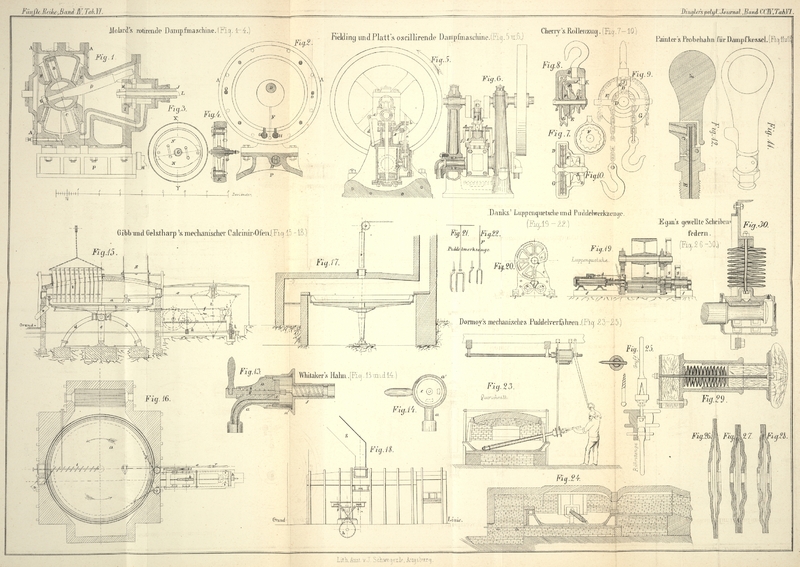