Titel: | Notizen aus der Wiener Weltausstellung 1873; mitgetheilt von Johann Zeman. |
Fundstelle: | Band 213, Jahrgang 1874, Nr. LXX., S. 286 |
Download: | XML |
LXX.
Notizen aus der Wiener Weltausstellung 1873;
mitgetheilt von Johann
Zeman.
Mit Holzschnitten und Abbildungen auf Tab. IV.
(Fortsetzung von S. 28 des vorhergehenden Bandes.)
Zeman, Notizen aus der Wiener Weltausstellung.
77. Dampfhammer von B. und S. Massey,
Openshaw, Manchester. (Figur 9 bis 13.)
Unter den Dampfhämmern kleineren und mittleren Kalibers, welche auf der Wiener
Weltausstellung vertreten waren, muß in Rücksicht auf Einfachheit, Dauerhaftigkeit
und Präcision der Steuerung der Dampfhammer von B. und S. Massey in Manchester mit in erster Reihe genannt werden. Diese Hämmer
gehören in England zu den verbreiterten und auch auf dem Continente ist das Original
stark vertreten, sowie es auch von verschiedenen Maschinenfabriken schon nachgebaut
wird. Der Massey-Hammer gehört zu den
Schnellschlägern – 200 bis 400 Hübe pro Minute;
er ist mit Hand- und Selbststeuerung versehen, für Oberdampf eingerichtet,
und das Gerüst war ein einseitiges.
Die Steuerung erscheint in Fig. 9 bis 13 in verschiedenen
Ansichten dargestellt und ist daraus sehr leicht zu verstehen. Bei Aufgang des
Hammers stößt die Rolle a gegen den Winkelhebel bb', welcher hinten zwischen den beiden
Seitenwänden des Gerüstes gelagert und mit dem Vertheilungsschieber A in Verbindung gebracht ist. Es wird somit der Schieber
A gehoben, der Dampfraum unter dem Kolben im
Dampfcylinder mit dem
Abzugsrohr A' in Verbindung gesetzt, frischer Dampf
dagegen aus dem Schiebergehäuse über den Dampfkolben geleitet und der Hammer abwärts
getrieben. Sowie die Rolle a den Steuerungshebel bb' verläßt, kehrt letzterer wegen der Spiralfeder
c in seine frühere Stellung zurück. Je nachdem man
die Position des Steuerungshebels bb' verändert
– und zwar mit Hilfe des Stellarmes mit Sperrquadrant d – wird die Hubhöhe des Hammers verschieden. Wenn man den
Winkelhebel ganz zurückzieht, so läßt sich der Hammer nach Belieben von Hand durch
den Griff f dirigiren.
Die nähere Einrichtung des bekannten Napier-Schiebers erkennt man ohne nähere Erklärung aus den Abbildungen.
Figur 10
gibt einen Horizontalschnitt durch das Schiebergehäuse; Figur 11 und 12 den
entlasteten Kolbenschieber für die Dampfvertheilung im Vertical- und
Horizontalschnitt und Figur 13 einen Schnitt
durch den Sitz des Kolbenschiebers.
Der Absperrschieber war bei dem ausgestellten 5 Centner-Dampfhammer durch
Handgriff e und Zugstange verstellbar; bei den kleinen
Massey-Hämmern (1/2 Centner Bärgewicht) ist
ein Fußtritt zur Stellung des Absperrschiebers vorhanden. – In der Ansicht
(Figur 9)
erscheint die Steuerungsschieberstange mit einer am Dampfcylinder angeschraubten
Führung versehen. Wenn ich mich aber recht entsinne, hat Massey diese Stange gerade herabgeführt und den Handsteuerhebel f etwas weiter links gesetzt; die Verbindung der
Schieberstange mit dem Winkelhebel gewährte hinlänglich Spielraum.
Die gangbaren Größen der Massey-Hämmer sind
folgende:
Daten
Gewicht des Hämmerbäres in Centner
0,5
1,5
3
5
7
10
15
Durchmesser des Cylinders. (Millimeter)
114
152
190
229
254
305
340
Fallhöhe (Millimeter)
280
330
432
533
610
686
762
Gewicht ohne Chabotte. (Centner)
13
24
32
48
60
80
130
Gewicht der Chabotte. (Centner)
5
12
24
40
56
80
120
Mittlere Hubzahl bei Selbststeuerung pro
Min.
400
350
300
250
200
200
200
Mittlere Dicke des Arbeitstückes, das in
einer Hitze ausgeschmiedet werden kann.
(Mm.)
50
76
102
152
178
203
229
78. Dampf-Preßhammer von B. und
S. Massey, Openshaw, Manchester. (Mit Holzschnitten.)
Weniger bekannt aber ebenso beachtenswerth wie die Dampfhämmer der oben genannten
Firma erscheinen dem Referent die Massey'schen
Dampfpreßhämmer, mit deren Hilfe eine große Zahl von Schmiedestücken wie sie im nachstehenden Tableau
zusammengestellt sind, rasch und in scharfen Formen hergestellt werden können.
Textabbildung Bd. 213, S. 288
Die Disposition des Preßhammers erhellt zur Genüge aus nebenstehendem Holzschnitt.
Der Steuerungs- und Absperrschieber hat die beim Dampfhammer besprochene
Einrichtung. Wenn der Absperrschieber geöffnet wird, tritt Dampf unter den Kolben
und hebt den Oberstempel. Hat man das Eisen im Untergesenk eingelegt, so wird ein
Fußtritt niedergetreten und dadurch der Dampfschieber so umgestellt, daß die untere
Cylinderhälfte mit der Atmosphäre in Verbindung tritt, über den Kolben aber frischer
Dampf gelangt, welcher den Stempel mit einem kräftigen Schlag auf das Untergesenk
hinabtreibt. Sofort erhebt sich der Stempel – wenn der Fußtritt nicht
absichtlich niedergehalten wird – und das gepreßte Schmiedestück kann durch
Schlag auf einen Hebel aus dem Untergesenk herausgeschoben werden.
Die kräftige Spiralfeder am oberen Verbindungs-Querstück der verticalen als
Buffer für den aufsteigenden Dampfkolben, der im Innern des Cylinders gegen die
Bufferspindel anstößt, welche durch die obere Stopfbüchse hindurchgeführt ist.
Nachstehend folgen die Hauptgrößen der Massey'schen
Dampfpreßhämmer:
Daten
Gewicht des Preßstempels in Centner
1/2
1 1/2
3
5
7
10
Durchmesser des Cylinders. (Mm.)
127
178
229
254
279
305
Fallhöhe. (Mm.)
280
330
432
533
610
686
Totalgewicht. (Centner)
12
30
40
50
62
80
Textabbildung Bd. 213, S. 289
79. Ganzzeug-Holländer von Debie,
Granger und Pasquier. (Figur 14.)
Auf dem Gebiete der Papier-IndustrieReferent verweist bei dieser Gelegenheit auf die inzwischen erschienenen
Specialberichte und zwar: „Officieller Ausstellungsbericht über
Papier-Industrie“; von Emil Twerdy, Ingenieur und Papierfabrikant in Bielitz. Heft 38. 35 S.
in gr. 8. Preis 40 Neukreuzer Druck und Verlag der k. k. Hof- und
Staatsdruckerei in Wien 1873. – Ferner „Die
Papier-Industrie“; von Professor Dr. Rud. Weber in
Berlin. Autorisirter Abdruck aus dem Amtlichen Berichte über die Wiener
Weltausstellung im J. 1873. Bd. I, Hft. 7. 56 S. in 8. Pr. 1 Mark. Friedr.
Vieweg und Sohn in
Braunschweig 1874. fanden sich in Wien eine Reihe von Novitäten vor, welche in diesen Notizen
nicht fehlen dürfen. Die eingehendste Beachtung verdient zunächst der von der Karolinenthaler
Maschinenfabrik (vorm. Lüsse,
Märky und Bernard) in Prag ausgestellter
Ganzzeug-Holländer (System Debie, Granger und Pasquier). Mit Bezug auf die in Figur 14 beigegebene
Skizze lasse ich die Beschreibung nach Rudel's
Centralblatt für deutsche Papierfabrikation hier folgen.
Alle Papierfabrikanten haben sicher die Ueberzeugung gewonnen, daß
die bis jetzt noch allgemein gebräuchliche Maschine zur Bearbeitung des Ganzstoffes
eine ihrem Zwecke sehr mangelhaft entsprechende ist. Wenn man sich die Aufgabe,
welche die Operation der Umwandlung von Geweben in feinstgetheilte Fasern, die in
der Papierfabrikation mit dem Namen „Ganzstoff“ bezeichnet
werden, klar vorstellt, so kann man das Trennen der verschiedenen Gewebearten durch
die Hand der Sortirerinnen und Verkleinern der Stücke auf dem Sortirtisch mit
Vor- und Nachsortirung, das Schneiden auf dem Hadernschneider, das Entfasern
der Hadern durch die Halbstoff-Mühle als durchaus zweckmäßige und
systematisch richtig aus einander folgende Arbeiten bezeichnen, für welche kaum
jemals bessere Verfahrungsweisen gefunden werden dürften, weil die Zwischenarbeiten
der Reinigung durch das Stäuben (Wolfen), Kochen, Waschen und Bleichen nur in dem
Stadium richtig erfolgen können, in welchem sich die Gewebe und Fasern in dem
jeweiligen Grade ihrer Bearbeitung befinden. Bis zum Halbstoff muß eben die
Zerlegung der Gewebe bis zu Fasern durch das Schneiden, das Auflockern des
Gespinnstes und die Extraction der in den Fasern mehr oder weniger enthaltenen
Substanzen durch das Kochen, die Reinigung derselben für die darauf folgende
Bleichung durch das Waschen geschehen, und kann nur einerseits in der Form des klein
geschnittenen Gewebes, andererseits in der Form der Faser stattfinden.
Ganz anders ist die Aufgabe bei der Umwandlung des Halbstoffes in
Ganzstoff. Der Ganzstoff soll nicht allein eine fein getheilte, sondern auch
zertheilte Faser sein, d.h. er soll eine Spaltung der ursprünglichen Dicke der Faser
in auch der Länge nach feineren Fäserchen sein. Denn diese Zertheilung ist es,
welche die feine Verfilzung des Papierblattes und damit die Festigkeit desselben,
seine bessere Qualität, seine Reinheit in der Durchsicht und gute Leimung zu einem
guten Theile mit bedingt. Für die Operation der Spaltung der Halbstoff-Fasern
in feinere Fasern kann kaum eine schlechter dazu geeignete Vorrichtung gefunden
werden, als es die deutsche, durch die Holländer verbesserte Cylindermühle ist.
Nicht allein daß durch die gering dargebotenen Flächen an den Schienen des Cylinders
und Grundwerkes, wo allein die Spaltung durch Reibung und Druck erfolgen kann, die
Arbeit unendlich verzögert wird, so geschieht dies auf Kosten der gleichmäßigen
Zertheilung noch mehr durch die überwiegend große Menge hohler Räume zwischen den
Schienen, in welche der Stoff beliebig schlüpfen und sich der Operation des Mahlens
entziehen kann; es ist kein Zwang sondern nur ein Zufall, welche und wie viel Fasern
dabei zur Bearbeitung gelangen und daraus muß ganz natürlicher Weise eine
außerordentliche Ungleichheit der Faserlängen und Feinheilen, aber auch eine
ungehörige Zeitverschwendung hervorgehen.
Die geringe Leistungsfähigkeit einer Cylindermühle war es, welche
die HHrn. E. Debie, Granger und Pasquier zur Construction ihres vervollkommneten Systemes geführt hat.
Dieses Holländersystem hat seit den fünf Jahren seines Bestehens eine solche
Ausbildung erfahren, daß die Kenntniß desselben nunmehr für jeden Papierfabrikanten
von Wichtigkeit ist. Die von den Professoren Lespermont
und Sagebien am 12. September 1872 in der Papierfabrik zu
Wizernes an einer Cylindermühle von 1 Meter Walzendurchmesser, 0,70 Meter Breite,
1000 Kilogrm. wiegend,
bei 180 Touren per Minute angestellten Bremsversuche
ergaben, daß zum Mahlen von Stroh und chemischem Holzstoff sechs Pferdekraft, zum
Mahlen feste Hadernstoffs acht und bei Füllung des Troges
voll mit Wasser ohne Stoff zehn Pferdekraft nöthig waren.
Der kolossale Aufwand an Kraft zur Bewegung des Stoffes ist ganz erklärlich, da die
Schienen der Walze die Function des Rades eines Dampfschiffes haben, welches mit
Schnelligkeit große Lasten im Wasser bewegt – mit dem Unterschiede, daß hier
die Last, dort aber die flüssige Masse bewegt wird. Bei Dampfschiffen ist
bekanntlich ein großer Kraftverbrauch und nur bis 25 Procent Nutzeffect. Die
Schaufeln tauchen höchstens nur mit dem achten Theile des Radumfanges ein, während
die Walze mit den Schienen fast bis zur Hälfte eintaucht, den Stoff in die Höhe
schleudert und ihn wieder nach vorn nimmt; denn der kleinste Theil des von den
Schienen gefaßten Stoffes geht über den Kropf oder Sattel und von da weiter im Troge
herum.
Die bei der neuen Stoffmühle ausgeführten Verbesserungen haben zum
Hauptzwecke: eine große Ersparniß an Kraft in der Anwendung der Walze, bei voller
Beibehaltung derselben Art der Wirksamkeit dieses Werkzeuges als Mahlapparat.
Die erste dieser Verbesserungen gründet sich auf die Beobachtung,
daß bei dem alten Verfahren die Walze zwei unterschiedene Functionen auszuführen
hat, welche für ein gutes Ergebniß der Triebkraft, geradezu entgegengesetzte
Bedingungen der Geschwindigkeit erheischen. Diese Functionen sind die Speisung der
mahlenden Flächen und die Mahlung selbst. Die erstere besteht in der Ertheilung
einer regelmäßigen und gleichmäßigen Bewegung der im Troge befindlichen Stoffmenge
und wird durch eine sehr geringe Geschwindigkeit erlangt. Die zweite hat die
allmälige Verminderung der Faserlängen während des Durchganges über das Grundwerk
zum Zweck und verlangt dagegen eine sehr große Geschwindigkeit. Untersucht man die
für jede dieser beiden Functionen aufgewendete Menge an Triebkraft, so findet man,
daß in der älteren Stoffmühle diese Triebkraft im Verhältniß der Speisung zur
nutzbar gemachten Arbeit beträchtlich ist.
In der neuen Stoffmühle werden die beiden Functionen der Speisung
und Mahlung durch zwei verschiedene Mechanismen ausgeführt: die erstere durch eine
neue Vorrichtung, Elevator genannt, die zweite durch die alte Vorrichtung, die
Walze. Die Walze ist auf dem oberen Theil des Troges mit dem Grundwerke erhoben und
dieses etwas geneigt und vor der Walze derartig angebracht, daß der Stoff in den
Trog zurückfällt, ohne gegen die Haube geworfen zu werden. Um dabei das absolute
Freiwerden der Walzschienen zu sichern, steht der obere Theil des Grundwerkes um
mehrere Centimeter über das Niveau des Stoffes heraus. Aufsteigend vor dem
Grundwerke ist eine stark gebogene Fläche, welcher der durch die specielle
Vorrichtung, die man Elevator nennt, aufgeführte Stoff regelmäßig folgt. Der vor
dieser gebogenen, steil aufsteigenden Fläche befindliche Elevator besteht aus einem
Rade mit Schaufeln von 1,2 Meter Durchmesser und derselben Breite wie die Walze,
macht nur 1 1/4 Umdrehungen per Minute wegen des tiefen
Eintauchens der Schaufeln, welche nach der Bewegungsrichtung des Stoffes hin stark
gebogen sind. Die Uebertragung der Bewegung erfolgt von der Walzenwelle aus, damit
die relativen Bewegungen dieser beiden Theile des Apparates mit einander
wechselseitig in Verbindung stehen.
Gleichmäßig durch diesen Apparat hinaufgezogen, kommt der Stoff
von selbst oben an und gelangt auf natürliche Weise zwischen die Schienen der Walze
und des Grundwerkes, um da wie in den älteren Mühlen gemahlen zu werden. Da die Walze nicht mehr den
Zugang des Stoffes zu bewirken hat, so ist es nicht mehr nöthig, daß die Schienen so
stark wie früher hervorragen; dies ist auf fünf bis sechs Millimeter verringert. Der
durch den Stoff der Walzenbewegung bereitete Widerstand ist demnach auf das
Geringste reducirt und kann diese Ersparniß je nach dem Rauminhalt der Stoffmühlen
und den verschiedenen Bedingungen der Aufstellung 20 bis 30 Procent betragen.
Die zweite Verbesserung, welche kein geringes Interesse bietet,
besteht in der neuen Anordnung des Bodens der Stoffmühle. Betrachtet man die
gewöhnliche Form der Stoffmühl-Tröge, so bemerkt man, daß die dem Boden
zunächst liegenden Stoffschichten eine viel langsamere Bewegung als die höheren
Schichten haben, so daß die letzteren viel öfter die Walze passiren als die
ersteren. Die einzige Hilfe gegen diesen unangenehmen Vorgang ist das Aufrühren, und
ist dieses nur ein sehr mangelhaftes Mittel. Besonders unregelmäßig ist die
Geschwindigkeit der Stoffschichten am Boden und der Oberfläche, am aufsteigenden
Theile des Kropfes, welchen der Stoff zu ersteigen genöthigt ist, um das Niveau zu
erreichen, wo in den älteren Mühlen durch die Walze die Aufschleuderung stattfindet.
Indem man diesen Kropf beseitigt und den Elevator bis auf den Boden des Troges
eintauchen läßt, erreicht man eine fast absolute Gleichartigkeit der
Geschwindigkeiten aller Stofflagen. Die Reibung am Boden kann allein noch den Gang
der untersten Lagen ein wenig verlangsamen. Um diesen Uebelstand zu beheben, erhält
der ganze Boden des Troges eine ununterbrochene Neigung vom Austritte den Stoffes
unter der Walze an bis zu dem Punkte, wo der Elevator ihn von neuem erfaßt. Es
bestand noch eine Ungleichheit des Mahlens durch die sehr verschiedenen Bewegungen,
welchen mit einer ziemlich gleichen Geschwindigkeit die Stoffschichten nahe an der
Mittelwand und der Außenwand folgen. Um diese Unregelmäßigkeit zu überwinden, wird
das Uebermaß von Stoff benützt, welchen der Elevator beständig vor die Walze bringt.
Dieses Zuviel wird durch einen Canal an den äußeren Rand der inneren Mittelwand
geführt, und findet somit in ununterbrochener Weise und während der ganzen Zeit des
Mahlens ein Querabfluß an verschiedenen Theilen des Troges statt, welcher die
vollkommene Vermischung sichert. Diese beiden letzteren Anordnungen liefern die
wirkliche Lösung des Rührers, ohne jede Mithilfe eines mechanischen Werkzeuges.
Die ökonomischen Ergebnisse bestehen in einer beträchtlichen
Beschleunigung des Mahlens, daher Zeitersparniß und auch einem geringeren
Kraftverbrauch, welcher fast nur 50 Procent von dem bei älteren Stoffmühlen
benöthigten ausmacht.
Die neuen Anordnungen bieten jedoch auch noch andere Vortheile von
großer Wichtigkeit. Seit mehreren Jahren hat sich die Anwendung von Grundwerken mit
Schienen ohne zugeschliffene Schneide allgemein eingebürgert und ist diese auch
überdies durch den Vortheil einer großen Regelmäßigkeit der Fabrikation, der
Vermeidung des Schärfens u.s.w. gerechtfertigt. Dieselbe Anordnung bei den
Walzenschienen zu treffen, war daher folgerichtig; aber die Dicke von 3 bis 5
Millimeter im Maximum, welche sie am besten haben mußten, und das nothwendige
Vorstehen derselben, um das Ergreifen des Stoffes zu bewirken, gaben ihnen bei der
alten Construction nicht die gehörige Festigkeit. Bei der neuen hingegen, wo das
Vorstehen dieser Schienen auf 5 bis 6 Millimeter und mehr vermindert ist, dürfen die
Schienen ohneweiters ohne Schärfe und ganz dünn sein. Da der Elevator die Walze von
der Arbeit der Speisung enthebt, so wird der Durchmesser der Walze von der Größe des
Troges ganz unabhängig. Bei einer Vermehrung des Fassungsraumes ist man nicht mehr
wie bisher genöthigt, auch den Durchmesser der Walze und damit ihr Gewicht zu vergrößern. Bei
Vergrößerung der Stoffmühle bleibt der Walzen-Durchmesser derselbe, nur
erhält die Walze eine größere Länge, um dadurch verhältnißmäßig die Production zu
vermehren. Die Walzen erhalten demnach die möglichst kleinen Durchmesser, um sie
weniger kostspielig zu machen.
Der von der Karolinenthaler
Maschinenbau-Gesellschaft (vormals Lüsse,
Märky und Bernard) in Prag ausgestellte
Holländer hatte einen aus Cement gebauten Trog; doch werden diese auch in Gußeisen
ausgeführt. Nähere Mittheilungen hierüber ertheilen H. Everling in Paris (26, rue cadet), Dr. Alwin Rudel in Dresden
und die genannte Karolinenthaler Maschinenbau-Gesellschaft. Von diesen
Holländern sind bereits 60 Stück im Betriebe – und zwar in 17 Fabriken
Frankreichs, in 2 belgischen, 1 bayerischen, 3 preußischen, 3 österreichischen, 1
italienischen und 1 russischen Papierfabrik.
80. Rotirender Knotenfänger von Henry
Watson in Newcastle. (Figur 15.)
Der schon im zweiten Juliheft, 1873 Bd. CCIX S. 81 erwähnte rotirende Knotenfänger
von Watson wurde bis zum Schluß der Ausstellung nicht in
completten Zustand versetzt; es sei demnach nur auf die einfache Skizze in Figur 15
verwiesen, welche diesen Knotenfänger im Längenschnitt andeutet. In der
Wirkungsweise mag derselbe mit dem Bertram'schen
Knotenfänger (a. a. O. S. 84) übereinstimmen; er unterscheidet sich in der
Ausführung zunächst durch den achteckigen Querschnitt, vielleicht um eine größere
wirksame Fläche der Knotenplatten zu erzielen. Um ferner ein Ansetzen von dickerem
Stoff um den Cylinder zu verhüten, ist um denselben herum eine – ebenfalls
mit Knotenspalten versehene – Schiene (etwa 20 Millimeter hoch)
schraubenförmig herumgelegt, welche den Stoff auch in der Längenrichtung der Bütte
in Bewegung erhält. Das Einsaugen des Zeuges und dessen Weiterbeförderung durch ein
Abflußventil a zur Papiermaschine scheint wie bei Bertram durch eine rasch bewegte Pumpe zu erfolgen.
81. Werkzeug zum Abschneiden von
Stehbolzen. (Figur 16 bis 18.)
In dem Pavillon der Kaiser Ferdinands-Nordbahn
(vergl. dies Journal, 1873 Bd. CCX S. 250) befand sich auch ein nettes Werkzeug zum
Abschneiden von Stehbolzen. Um nämlich gleichmäßige Nietköpfe zu erzielen, müssen
die vorstehenden Enden der in Stehkesseln eingeschraubten Stehbolzen auf gleiche
Höhe abgeschnitten werden, was mit diesem Werkzeuge ein Arbeiter bei bis zu 26
Millimeter starken Bolzen aus Kupfer, Eisen und selbst Stahl rasch und exact
ausführen kann.
Das Werkzeug wird mit seiner Oeffnung über den abzuschneidenden Stehbolzen
aufgesteckt und die oben sechskantig auslaufende Büchse a mit Hilfe eines Schlüssels gedreht, welcher in Figur 18 in kleinerem
Maßstab skizzirt ist. Dabei legt sich das Werkzeug mit dem Schwanz b₁ der Grundplatte b
gegen einen benachbarten Bolzen an.
Die Büchse a ist drehbar zwischen die Grundplatte b und die Deckplatte c
eingefügt; sie nimmt den excentrisch eingesetzten
stählernen Schneidring d auf, welcher nach etwaiger
Abnützung leicht wieder ausgewechselt werden kann. Zur Verbindung der Büchse a und des Schneidringes d
dient die Niete e.
Die Grundplatte ist von Schmiedeisen; die den abzuschneidenden Stehbolzen umfassende
Oeffnung ist aber der Dauerhaftigkeit halber mit einem Stahlring armirt, wie dies
durch die Schraffirung hervorgehoben wurde.
82. Sauerbrey's Salzmühle. (Figur 19 und
20).
Die zweckmäßige Construction dieser von der Staßfurter
Maschinen- und Dampfkesselfabrik ausgestellt gewesenen Mühle zum
Mahlen von Stein-, Kali- oder Düngesalz, ferner aber auch von Zucker,
Chamotte, Phosphorite u.s.w. erhellt zur Genüge aus den beigegebenen zwei Ansichten
in Figur 19
und 20.
Der Läufer, Mahlrumpf und die Mahlkränze sind aus Hartguß. Leistung pro 10 Stunden je nach Größe der Mühle 250 bis 800 und
1000 Centner hartes Mahlgut (Steinsalz etc.), beziehentlich 300 bis 1000 Ctr. poröse
Masse (Düngesalz u.a.).
Um ein bequemes Demontiren zu gestatten, sitzt das Triebrad auf der horizontalen
Welle nicht direct auf, sondern auf einem auf der Welle aufgekeilten conischen
Futter, auf welchem das Rad durch Schrauben und Keil befestigt ist. Ein Abziehen
dieses Rades kann nun sehr leicht erfolgen, wenn es auch – was bei solchen
Mühlen nicht zu vermeiden ist – stark verrostet wäre. Man lüftet die
Schrauben, stößt das Rad von der conischen Büchse ab, nimmt die Lagerdeckel der
Welle weg, worauf die Welle sammt Büchse herausgezogen wird, während das Rad in der
Fundamentgrube bleibt. Dann kann das Rad herausgenommen und im Falle eines Bruches
oder drgl. durch ein neues ersetzt werden. – Ein unmittelbar auf der Welle
aufgekeiltes und auf dieser festgerostetes Zahnrad würde nur mit großen
Schwierigkeiten abgezogen werden können; deshalb die Einschaltung der conischen
Büchse.
Tafeln
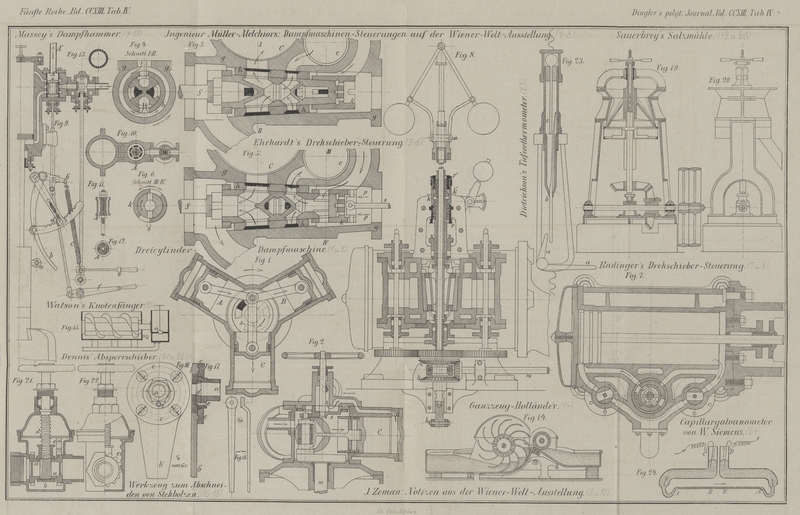