Titel: | Die Fabrikation des Cementes und dessen Anwendung für Soolenleitungen in Ischl; von Oberbergverwalter August Aigner. |
Fundstelle: | Band 215, Jahrgang 1875, S. 420 |
Download: | XML |
Die Fabrikation des Cementes und dessen Anwendung
für Soolenleitungen in Ischl; von Oberbergverwalter August Aigner.
Aus dem Berg- und Hüttenmännischen Jahrbuch,
1874 S. 134.
Mit Abbildungen auf Taf.
X [c.d/3].
Aigner, über die Fabrikation des Cementes und Herstellung von
Cementröhren.
Unter den Objecten, welche die verschiedenen Zweige der Bautechnik dem Beschauer des
Weltausstellungsraumes in Wien darboten, spielten die Cemente eine hervorragende
Rolle, deren mannigfaltige Verwendung in allen Gebieten des Bauwesens im
fortwährenden Steigen ist und deren Wichtigkeit sich wohl auch danach bemessen läßt,
daß auf 49 Aussteller 4 Fortschritts-, 18 Verdienstmedaillen und 22
Anerkennungsdiplome entfielen; es erregte die Betrachtung der in dieser Branche der
Technik erreichten hohen Vollendung ein um so größeres Interesse, als die
ausgedehnte Literatur, welche sich seit nahe einem halben Jahrhunderte über den
Gegenstand entwickelt hat, hier gewissermaßen ihren sichtbaren Ausdruck fand.
Bis zum J. 1756 bediente man sich, wie bekannt, des Trasses und der Puzzolanerde,
deren Silicate schon durch vulkanische Processe aufgeschlossen sind, welche also die
Kieselsäure in löslicher Form enthalten und zur Herstellung des hydraulischen
Mörtels erst einer Zugabe von Luftkalk bedürfen. Smeaton
war der Erste, welcher mit der Trennung des Thonrückstandes beim Auflösen eines
Mergels von Glamorganshire in Salpetersäure die erste Bahn für die wissenschaftliche
Forschung eröffnete; Parker brannte zuerst die Thonnieren
von Sheppy (natürlicher hydraulischer Kalk) und nahm 1796 auf Romancement ein
Patent; 1824 wurde Joseph Aspdin der Erfinder des
künstlichen oder Portlandcementes, indem er gebrannten Kalk mit gleichen Theilen
Thon mittels Maschinen mengte und abermals brannte; 1836 begründete Pasley (1831 41 154) die
eigentliche Portlandcement-Fabrikation, indem er zwei Theile des
Medoway-Thones (0,75CaO + 14,8Fe₂O₃ +
11,6Al₂O₃
+ 68,65SiO₃ + 1,9KO +
2,1NaO) mit Kreide mengte und brannte; 1838 erschien
sein erstes wissenschaftliches Werk.
Aber schon im J. 1828 wurde Prof. Fuchs in München der
eigentliche Schöpfer der ersten Theorie, welche bis zum heutigen Tage die Grundlage
für jede weitere Forschung bietet: „Durch das Brennen wird der kohlensaure
Kalk ätzend und wirkt als solcher derart auf den Thon ein, daß die Kieselsäure
durch den Aetzkalk die Freiheit erlangt und sich in späterer Berührung mit
Wasser mit dem Kalke zu einer bestimmten chemischen Verbindung (Hydrosilicat)
vereinigt, wobei die Anwesenheit von Alkalien durch ihre Substitution in der
Glühhitze diese Bildung begünstigt.“
Die weiteren, in verschiedenen Zeitschriften und selbständigen Werken
veröffentlichten Studien und Controversen, an welchen sich die Namen: Vicat 1841, Kuhlmann 1848, v.
Pettenkofer 1849, Schafhäutel 1851, Grathe 1854, Winkler 1855 bis 1865, Feichtinger 1859 bis 1865, v. Kripp 1865, Frémy 1865, Held 1865,
Michaelis 1869 knüpfen, haben über die chemischen
Vorgänge bei den Cementen die wissenschaftliche Grundlage klargestellt, welche kurz
in dem Satze gipfelt, daß die Cemente die Eigenschaft des Erhärtens in Wesenheit den
in Folge Einwirkung des Feuers gebildeten Kalksilicaten und Kalkaluminaten
verdanken.
Die Fabrikation des Cementes spaltete sich daher schon frühzeitig in zwei Arten,
nämlich in die vorzüglich in Deutschland und England betriebene Fabrikation von
künstlichem Portlandcement und die Anfertigung von natürlichem hydraulischem Kalk,
welche in späterer Zeit in den nördlichen Abhängen der Alpen von Bayern und Tirol
ein dem Portlandcement nahezu gleichwerthiges Product erzielte und, wie es scheint,
durch ein glückliches Zusammentreffen günstiger Umstände, nämlich beste Qualität und
billige Gewinnung des Rohmaterials, directes Brennen und entsprechende
Communicationsmittel, der künstlichen Erzeugung des Portlandcementes ein immer
größeres Terrain abgewinnt.
In dem bayerisch-tirolischen Hochgebirge in der Umgebung
von Kufstein erfolgt die Fabrikation des Cementes aus den natürlichen, der unteren
Tertiärformation angehörenden, großen Mergellagern, von denen einige Schichten eine
dem Portlandcement (nach Michaelis: 60CaO + 1,17MgO + 7,5Al₂O₃ +
3,34Fe₂O₃
+ 0,74NaO + 29,31SiO₃) nahezu gleichwerthige Zusammensetzung zeigen.
Dieses Material für hydraulischen Kalk wird am Tage gewonnen und
mittels Bahnen und Absturzvorrichtungen zu den Oefen gebracht; diese, den
Eisenhohöfen ähnlich, sind für continuirlichen Betrieb mit Steinkohlenklein
eingerichtet, haben in der Regel eine Höhe von 28 bis 30 Fuß (8,9 bis 9,5 M.), eine
Gichtweite von 9 Fuß (2,8 M.), stehen meistens zu mehreren (3 bis 6) in einer Reihe
mit gemeinschaftlicher Futtermauerung basteiartig nebeneinander und werden auf ihrer
Gicht von einem Heizer bedient, welcher den auf der Bahn zugeführten Mergel und das
Kohlenklein abwechselnd aufschüttet. Der Ofen ist am Boden auf 7 Fuß (2,2 M.)
angezogen und besitzt vorn ein Gewölbe, durch welches ein zweiter Arbeiter das
gebrannte Product auszieht. Dies erfolgt mittels sechs 2 bis 3 Zoll (5 bis 8
Centim.) dicker Eisenroststäbe, welche einfach gerüttelt werden. Die Erzeugung per
Tag beträgt bei jedem Ofen circa 400 Zollcentner. Die Räumung wird nach jeder halben
Stunde vorgenommen; die Feuerzone befindet sich ungefähr in der Mitte der Ofenhöhe.
Die Menge des Brennstoffes (Kohlenkleins) ist gleich 1 zu 4 Th. Mergel.
Die Oefen sind mit behauenen Stücken von buntem Sandstein
gefüttert und werden gegen die nahe stehende Futtermauer etwas hohl gestellt. Das
gebrannte Product wird direct per Bahn in die Mühlen geschafft; diese zeigen
verschiedene Einrichtungen; meist haben sie drei Stockwerke. In dem Souterrain
befindet sich eine Turbine, deren verticale Achse mittels Getriebe die Bewegung auf
die Mühlsteine und von da in den zweiten und dritten Stock überträgt. Im ersten
Stock befinden sich zwei Mahlgänge, welche das aus dem dritten Stock herabfallende
Mahlgut verarbeiten; dieses fällt von den Mühlsteinen direct in die untergestellten
Fässer und wird in letzteren durch eine hebelartige Prellvorrichtung möglichst
compact zusammengeschüttelt. Die Mühlsteine stammen aus Belgien und werden jede
Woche, für die Portlandcement-Erzeugung jeden zweiten Tag, behauen. Im
zweiten Stock befindet sich ein Quetschwerk, bestehend aus zwei langen cannelirten
Stahlwalzen, welche das aus dem dritten Stock in eine Gosse gestürzte, von den Oefen
kommende Rohmaterial aufnehmen. Das gequetschte Material wird behufs besserer
gleichförmiger Zertheilung im dritten Stock mittels Elevatoren aufgezogen und fällt
erst durch eine Vertheilungslutte in den ersten Stock auf die Mahlgänge. Durch
Quetschung wird die Größe einer Bohne erzielt. Bisweilen geschieht die Verarbeitung
einfacher. Von einer Turbine wird eine horizontale Achse in Bewegung gesetzt, um
welche drei Paare Koller (stehende Walzen zu 40 Ctr.) rotiren. Die Mehle fallen aus
den gußeisernen durchbrochenen Kollerschalen in eine gemeinschaftliche Gosse, werden
mittels Elevatoren gehoben und gelangen auf Sortirsiebe, wobei das Grobe wieder in
die Schalen zurückfällt, oder auf Mahlgängen vermahlen wird.
Bei jeder Fabrik von hydraulischem Kalk befindet sich eine
Werkstätte zur Herstellung der Fässer; dieselbe enthält eine Boden- und eine
Circularsäge für Dauben, eine Hobelmaschine zum Säumen der Dauben und eine
Circularsäge zum Beschneiden der Dauben und Erzeugung des Frosches; die Bodenbreter
werden zuerst aus drei Stücken zusammengefügt und dann durch die Bodensäge rund
geschnitten; sämmtliche Bestandtheile kommen hierauf in die Binderei und werden
mittels Haselgurten (200 Stück zu 2 fl. ö. W.) gebunden. Der Umstand, daß die
Abnehmer des hydraulischen Kalkes denselben nur in Fässern wünschen, macht die
Emballage theuer (13 kr. per Zollcentner). Die Gestehungskosten sind für die
Erzeugung des hydraulischen Kalkes per Ctr. bei Dampfmaschinenbetrieb 45 kr., bei
Wasserkraft 40 kr.; dabei entfallen auf:
Emballage
13 kr.
Mahlen
4 „
Rohmaterial-Beischaffung
1 „
Regie, Zinsen des Anlagecapitals,
Fuhrlöhne
18 „
Brennstoff
4 „
––––
zusammen:
40 kr.
Schon Feichtinger wies darauf hin, daß
noch an mehreren Orten der Alpen Mergel gefunden werden dürften, welche sich ebenso
wie der Perlmooser Cement zur Portlandcement-Fabrikation eignen. Obwohl dies
bis jetzt nicht der Fall war, so ist doch das Vorkommen von Mergeln minderer
Qualität in den Alpen und insbesondere in den Hangendschichten der Salzreviere nicht
unbedeutend, und obgleich die Anwendung der Cemente im Salinenfache –
beispielsweise zur Herstellung der Soolenreservoirs (vergl. 1867 185 244), zur Verhinderung des Blähens der Ulmen u.s.w.
von Grubenstrecken, zum Schutze gegen Rost bei
Eisenröhren (vergl. 1874
214 494) – nicht neu ist, so glaube ich doch ein
Genre der Cementfabrikation beleuchten zu müssen, welches, wie die Fabrikate der
Wiener Weltausstellung beweisen, eine immer größere Verbreitung findet.
Wenn ich hierbei in erster Linie auf die Erzeugnisse aus dem
Perlmooser Cemente und aus die Röhrengarnituren von Dickeroff und Widmann mit 24 bis 6 Zoll (63 bis
16 Cm.) Durchmesser [erstere mit 4 Zoll (10 Cm.) Fleischstärke] hinweise, so wäre
die Erreichung dieser Fabrikate mit den Mergeln der Salzreviere allerdings
unmöglich, denn dieselben sind in der Regel von minderer Güte, erhärten langsam,
liefern jedoch bei sorgfältiger Behandlung im Brennen, schneller Verarbeitung und
bei größerer Röhrenstärke ein Fabrikat, welches für das praktische Bedürfniß der
Salinen vollkommen ausreicht.
Das Material für den hydraulischen Kalk am Ischler Salzberg gehört
zur Neocombildung, nimmt das Hangende des Salzlagers ein und enthält nach Patera:
In Salzsäure unlöslichen Rückstand (Al₂O₃,
SiO₃)
37,00
kohlensaures Eisenoxydul
10,51
kohlensaure Kalkerde
48,80
kohlensaure Talkerde
2,42
–––––
zusammen:
98,73.
Das Brennen dieses Mergels geschieht in gewöhnlichen Kalköfen,
intermittirend mittels Holzfeuerung, und es kostet die Herstellung eines Wiener
Centners (56 Kilogrm.) des fertigen Productes 47 kr. ö. W.
Es soll nun die Herstellung der Cementröhren, wie sie am
Salzberge bei Ischl ausgeführt wird, geschildert werden. Als Material für diese
Herstellung dient ein Gemenge von gleichen Volumtheilen gewaschenem und
hydraulischem Sand, welches in einem Rührapparat unter Zusatz der erforderlichen
Menge Wasser gemischt und in die Röhrenform eingegossen wird.
Zum Waschen des Sandes dient der in Fig. 31 und 32
dargestellte Apparat. Er besteht aus einem Wassertrog a,
in welchen der untere Theil der mit einer eisernen Achse b versehenen achteckigen Trommel c eintaucht.
An sieben Seiten dieser Trommel sind innen eiserne Gitter aus Drahtstäben
eingesetzt, durch welche sich der feine Sand und die unreinen erdigen Theile
durchsieben. Eine dieser Seiten bildet eine Thüre, durch welche der zu waschende
Sand eingefüllt wird. An der achten Seite, welche nach dem Waschen jedesmal unten
stehen gelassen wird, befindet sich kein Gitter, da auf dieser Fläche der gewaschene
Sand durch ein an der Stirnwand der Trommel befindliches Thürchen t mittels einer Blechkrücke ausgezogen wird, während man
den im Troge angehäuften Sand durch eine hart am Boden befindliche verschließbare
Seitenöffnung entfernt. Um den gewaschenen Sand ausziehen zu können, wird die
Trommel sammt Achse gehoben, indem man die beiden in verticaler Führung f gehenden Lager g mittels
der Hebel h aufwärts bewegt, sodann unter die Trommel eine flache
Rinne untergeschoben, über welche der gewaschene Sand in ein bereit stehendes Gefäß
oder auf den Fußboden herausgezogen wird. Im Troge muß ein beständiger Zu-
und Abfluß des Wassers stattfinden.
Den Rührapparat für die Röhrenmasse zeigen Fig. 33 und 34. Auf dem
hölzernen Boden A ist die gleichfalls hölzerne
cylindrische Wand B befestigt, welche innen, sowie der
Boden mit Blech gefüttert Wird. An der einen Seite der Wand befindet sich die Lutte
D, die für gewöhnlich durch den Schieber E abgeschlossen ist. Der eigentliche Rührapparat besteht
aus dem Armkreuz F, an welchem 14 windschiefe Schaufeln
g befestigt sind; an die Achse H, welche für Handbetrieb oben eine Kurbel trägt,
schließt sich unten eine eiserne Büchse, welche über den fixen Drehzapfen t gesteckt wird.
Die Röhrenform zeigen Fig. 41 bis 48, und zwar
Fig. 46
und 47 in der
Zusammenstellung. Auf Schwellen, in welche die Zangenhölzer z eingezapft sind, wird das Bodenbret p (Fig. 44 und
45)
gelegt; dann schiebt man die zwei an der Innenseite kantigen hölzernen Seitentheile
t (Fig. 43) ein. Diese
besitzen Ruthen f, in welche die Stoßbreter(Fig. 41 und
42) so
eingeschoben werden, daß deren Vorsprünge k gegen die
Mitte der Röhrenform gekehrt sind; ferner sind an den Seitentheilen und dem Boden
Leisten l, l' (Fig. 43 und 45) befestigt,
so daß an den Enden der fertigen Röhre, wie Fig. 39 zeigt, Falze u entstehen. Nebstdem müssen die Röhrenenden der
Verbindung wegen auf circa 6 Zoll (15 Cm.) Länge cylindrisch sein, was dadurch
erzielt wird, daß man an den einspringenden Kanten der Seitenwände ebenso lange
Holzleisten, welche innen abgerundet sind, festnagelt. Die Stoßbreter werden an der
dem Rohr zugekehrten Seite flach kegelförmig ausgedreht, um dem Stirnende des Rohres
die entsprechende, in Fig. 39 angedeutete, für
die Verbindung zweier Röhren nothwendige Gestalt zu geben. Durch die Oeffnungen der
Stoßbreter wird nun der genau abgedrehte, am besten aus Gußeisen hohl gefertigte
Kolben (Kern) J (Fig. 48)
eingeschoben.
Soll der Guß stattfinden, so werden alle Theile der Form an der Innenfläche
gereinigt, mit trockenem Graphitpulver und Leinwandballen blank gerieben; die hierzu
erforderliche Zeit beträgt 20 Minuten. Hierauf wird der Kolben eingesetzt, das im
Rührapparat gemischte Material einlaufen gelassen und mit einem hölzernen Stößel
festgestampft. Die Menge des Materiales beträgt für ein vierzölliges (10 Cm.) Rohr 1
Kubikfuß (0,3 Kubikmeter) = 58 Pfund (32,5 Kilogrm.) hydraulischen Kalk und 1
Kubikfuß = 100 Pfund (56 Kilogrm.) gewaschenen Sand. Nach beendetem Guß zieht man
die ganze Form mittels der Schraubenzwinge s (Fig. 46) und
Keile so an, daß die Masse überall gleich gut anliegt.
Während des Festwerdens, welches bei langsam erhärtenden Mergeln 24 bis 48 Stunden
dauert, muß der Kern J in den ersten 12 Stunden nach je
einer halben Stunde eine kleine Drehung erhalten. Nach 12 Stunden kann man denselben
ausziehen, was das Austrocknen befördert, und nach 48 Stunden können die
Seitentheile blosgelegt werden, worauf dann die Röhre sammt den Bodenbretern in den
Trockenraum gestellt wird und darin 14 bis 30, selbst 60 Tage verbleibt.
Die Verbindung der Röhren erfolgt durch Vergießen der
Fugen mit Cement. Man bedient sich dazu eines Ledergurtes, welcher um die
zusammenstoßenden Rohrenden herumgelegt wird, welche aus diesem Grunde auf eine
Länge ab (Fig. 39) rund statt kantig geformt sein müssen; die Breite des
Gurtes richtet sich nach der Größe der Röhren. Fig. 37 zeigt die
Außenseite, Fig.
38 die Innenseite des aufgerollten Gurtes a,
Fig. 35
den um die Rohrenden gelegten Gurt, Fig. 40 dessen
Querschnitt in vergrößertem Maßstab. An seiner inneren Seite sind Lederwulste b mit trapezförmigem Querschnitt aufgenäht, an der
äußeren Fläche die eisernen Spangen p (Fig. 37) aufgenietet,
welche bewirken, daß der Gurt seiner Breite nach flach auseinander gehalten wird;
m sind vier Schraubenmuttern, in welche die
Schrauben s (Fig. 35) eingedreht
werden, um einen festen Anschluß der Lederwulste b an
die Rohrwände zu bewirken, was durch die cylindrische äußere Form der Rohrenden
erleichtert wird. Der Lederriemen ist an den Enden bei o
(Fig. 37
und 38) rund
ausgeschnitten, so daß, wenn derselbe um die Rohrenden gelegt ist, eine Oeffnung
bleibt, durch welche das Vergußmaterial eingeschüttet wird. Zur größeren Sicherheit
kann man am Rande der Wulste b Leinwandstücke annähen
und mittels Schnüre um die Röhre anziehen. Damit der Verguß an den Röhren haften
kann, müssen ihre Stoßflächen, wie früher bemerkt, conisch nach außen divergiren
(vergl. Fig.
36 und 39); es wird hierauf bei g eine kleine
Hanfbandage eingedreht, damit der Cement nicht in das Innere der Röhre dringen kann,
und hierauf der Riemen nach Fig. 35 angelegt. Die
größte Distanz der conischen Endflächen soll für fünfzöllige (132 Mm.) Rohre einen
Zoll (26 Mm.) betragen, wofür 8 Pfd. (4,5 Kilogrm.) Vergußmaterial ausreichen wird.
Man braucht wegen langsamer Erhärtung eine größere Anzahl dieser Bandagen, um nicht
bei Herstellung einer Verbindung erst auf das Festwerden einer anderen warten zu
müssen.
Es ist selbstverständlich, daß die Erzeugung nur dann wohlfeil
sein kann, wenn dieselbe fabrikmäßig geschieht, wenn also Sandwasch- und
Rührapparat durch einen Motor (z.B. ein kleines Wasserrad) in Bewegung gesetzt
werden.
Der Sandwaschapparat wird mittels eines Riemens durch eine auf der
Wasserradwelle befindliche Riementrommel und eine auf der Achse des Sandwäschers
befestigte Riemenscheibe bewegt; beim Ausziehen des gewaschenen Sandes wird die
Sandtrommel sammt Achse und Riemenscheibe gehoben, während sich die leere
Riemenscheibe auf einem fixen Achsnagel fortbewegt. Ebenso ist die senkrechte Achse
des Rührapparates wegen des Aushebens in zwei über einander stehenden Lagern nach
aufwärts verschiebbar und außerdem der Länge nach mit einer Nuth versehen, auf
welcher zwei kleine Zahnräder nach auf- und abwärts mittels einer separaten
Stellachse verschiebbar sind und dabei wechselweise in ein horizontales und durch
einen Riemen mit der Wasserradwelle in Verbindung stehendes Zahnrad eingreifen,
wodurch eine Vor- und Rückwärtsbewegung des Mörtelrührapparates erzielt wird.
Bei einem mittleren Stande der Stellachse bleibt der Rührapparat in Ruhe, so daß die
senkrechte Achse mittels eines Wirbelringes gehoben, hierauf die Röhrenform auf
einer Bahn unter den Rührapparat gestellt und aus demselben gefüllt werden kann. Mit
diesem Motor ist gleichzeitig eine Hebevorrichtung in Verbindung, welche die
angetrockneten Röhren in den höher liegenden Trockenraum zu schaffen hat.
Unter Anwendung dieser Vorrichtungen stellen sich die Kosten eines
3 1/2 Fuß langen vierzölligen Rohres, wie folgt. Für Cement (ein Kubikfuß) 29 kr.,
für gewaschenen Sand (ein Kubikfuß) 9 kr., für Graphitpulver 2 kr., für Arbeit 25
kr., für Vergußmaterial 6 kr., zusammen 71 kr., also per Fuß 20 kr. Dem gegenüber
stellt sich der Fuß einer vierzölligen gußeisernen Röhre auf 2 fl. 25 kr., der Fuß
eines aus anderen Fabriken bezogenen Cementrohres auf 83 kr., der Fuß einer
hölzernen Röhre auf 11 kr.; demgemäß können hinsichtlich des Preises mit den
Cementröhren nur die hölzernen concurriren, wobei jedoch bemerkt werden muß, daß die
Verwendung der letzteren bei den steigenden Holzpreisen immer theurer wird, daß es
überhaupt eine nationalökonomische Anforderung ist, dem immer werthvoller werdenden
Bau- und Nutzholze ein dauerhafteres Materiale zu substituiren.
Was die Dauerhaftigkeit der Cementröhren betrifft, so ist sie selbstverständlich in
jenen Orten, wo keine Verschiebung stattfindet, also auf einem festen Boden, eine
fast unbegrenzte; der Cement steht in dieser Beziehung allen anderen oben genannten
Materialien voran. Uebrigens besitzen wir, wie schon Prof. Fuchs zuerst gezeigt hat, in dem Wasserglase
ein äußerst werthvolles Mittel, die Güte des hydraulischen Kalkes zu erhöhen. Das
Wasserglas wird mittels des in Fig. 49 abgebildeten
Wischers zweimal auf die inneren Röhrenwände gestrichen, wodurch sich der Preis
einer Röhre um nicht mehr als 1/2 kr. erhöht.
Die Fabrikation von Cementröhren ist keinesfalls neu, und es wurden beispielsweise in
Dingler's polytechnischem Journal (1854 132 202. 134 136) einfache
Verfahren dazu angegeben, doch basiren sie insgesammt auf der Anwendung schnell
erhärtender Cemente, welche, wie bereits erwähnt, in der Nähe der Salzlager noch
nicht gefunden wurden.
Daß zum Legen der Röhren ein fester Untergrund benöthigt wird und jede Erschütterung
zu vermeiden ist, braucht kaum erwähnt zu werden.
Tafeln
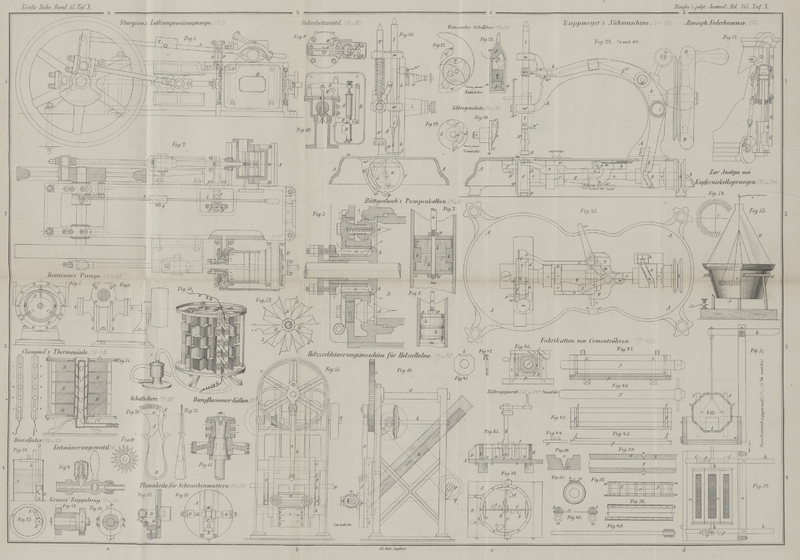