Titel: | Ueber Pohl's Verfahren zur Fabrikation von Kochsalz aus Soolen; von Dr. Georg Lunge (South-Shields). |
Autor: | Georg Lunge [GND] |
Fundstelle: | Band 219, Jahrgang 1876, S. 245 |
Download: | XML |
Ueber Pohl's Verfahren zur Fabrikation von Kochsalz aus
Soolen; von Dr. Georg Lunge
(South-Shields).
Mit Abbildungen auf Taf.
V [a/4].
Lunge, über Pohl's Kochsalzfabrikation aus Soolen.
In meiner Mittheilung über Hargreaves' Verfahren zur
Fabrikation von Sodasulfat (vgl. 1875 218 416) habe ich
beiläufig des Pohl'schen Verfahrens zur Fabrikation von Kochsalz erwähnt (a. a. O.
S. 428). Es scheint über dasselbe noch nichts in die Oeffentlichkeit gedrungen zu
sein; soeben hat jedoch Hr. Pohl (aus Liverpool) eine nur
zur Privatcirculation bestimmte englische Broschüre von 48 Seiten über sein
Verfahren drucken lassen, deren Benützung für die Oeffentlichkeit er mir
freundlichst gestattet hat; ich werde im Folgenden einen kurzen Auszug ihres
wesentlichen Inhaltes geben.
Pohl wurde durch die Kohlentheuerung der Jahre 1872 und
1873, welche ihm als kleinern Salzfabrikanten noch größern Schaden als den großen
Fabrikanten zufügte, veranlaßt, auf Ersparniß an Brennmaterial beim Verdampfen der
Soole zu achten, und kam bald zu dem Resultate, daß das alte Verfahren verlassen
werden müsse, trotzdem das Scheitern aller frühern Versuche in dieser Beziehung
gerade nicht ermuthigend wirkte. Als Präliminarfragen erörtert er die folgenden:
1. Wie viel Salz enthält Soole (d.h. gesättigte)?
2. Wie viel Kohlen werden bei dem jetzigen Verfahren zur
Production von 1t Salz
verbraucht?
3. Wie viel Wasser wird in modernen Dampfkesseln auf 1t Kohlen verdampft?
Durch eine große Anzahl von Versuchen, welche mit großer Sorgfalt ausgeführt wurden,
stellte Pohl fest, daß genau 27 Th. reines Chlornatrium
mit 73 Th. destillirten Wassers 100 Th. einer gesättigten Lösung ergeben, sowohl in
der Hitze als in der Kälte, welche bei 62° F. (16 2/3° C.) das
specifische Gewicht 1,20642 zeigt. Er verbreitet sich ausführlich über die Ursachen,
warum dieses Resultat von früher beobachteten abweicht, stellt aber fest, daß Fuchs und Reichenbach ein mit
dem seinigen praktisch identisches Resultat erhalten haben, nämlich daß 100 Th.
Wasser bei allen Wärmegraden 37 Th. NaCl auflösen (= 27,01 NaCl auf 72,99 Wasser).
Gerlach's Untersuchungen sind Pohl augenscheinlich unbekannt geblieben; nach Gerlach hält eine gesättigte Kochsalzlösung bei 15° 26,395 Proc.
(spec. Gew. 1,20433).
Betreffs der zweiten Frage, des Kohlenverbrauches bei dem alten Verfahren des
Salzsiedens, wurden Pohl sehr abweichende Angaben
gemacht. In Varangeville sagte man ihm, daß man mit 1 Pfd. Kohle 3 1/2 Pfd. Wasser
verdampft, was ihm, nach der Construction der Apparate zu urtheilen, völlig
unglaublich scheint. Zu Inowraclaw, welches die best eingerichtete unter den von ihm
besuchten Salinen ist, sagte man ihm, daß man beim Sieden höchstens 2t Salz auf 1t bester schlesischer Steinkohle erhalte,
und zum Trocknen des Salzes und Betriebe der Maschinen noch ein besonderes Quantum
Kohle verbrauche. Die Schönebecker Resultate, wo ihm Einsicht der Bücher verstattet
wurde, sind nicht maßgebend, weil man dort Braunkohle verwendet. Was England
betrifft, so kam er nach vielen Anfragen und Inspectionen von Geschäftsbüchern zu
dem Resultate, daß man für 1t mittelguter
Kohle erhalte:
30 Ctr. feinkörniges (Butter-) Salz oder
37 Ctr. grobkörniges gewöhnliches Siedesalz.
Dies kommt bei einem Durchschnittsgehalt der Soolen von 26 1/2
Proc. auf eine Wasserverdampfung von
4t,18 für Buttersalz
oder
5t,13 für gewöhnliches
Salz für 1t Kohle heraus.
Es scheint auffallend, daß das Resultat sich günstiger für die Verdampfung bedeutend
unter dem Siedepunkte (wie es bei gewöhnlichem Salze durch
„Soggen“ stattfindet), als für diejenige beim Sieden
(Stören) stellt! dies widerspricht Peclet's Angaben, und
wird von Pohl auf größere Arbeitsverluste beim Darstellen
von Buttersalz zurückgeführt. Die Durchschnittstemperatur der Soole beim Arbeiten
auf Buttersalz ist 107°, die beim Arbeiten auf gewöhnliches Salz 70°.
Die Schornsteintemperatur wurde für gewöhnliches Salz etwa 315°, bei
Buttersalz zwischen 420° und 570° gefunden, und zwar am höchsten, wenn
die Pfannen soeben von Pfannenstein befreit worden waren. Durch diese Operationen,
wobei der oft 6 Zoll (152mm) dicke
Pfannenstein nach dem Entleeren der Pfanne durch gewaltsame Hammerschläge von unten
abgelöst und zersprengt wird, leidet die Vernietung der Pfannen sehr, und wird dadurch Veranlassung
zum Lecken und Zusetzen der Züge und Roste mit Salz gegeben. Bei gewöhnlichem Salz,
wo das Feuer nicht so heftig ist, bildet sich weniger Pfannenstein und findet
weniger Verlust von unbenutzt entweichender Wärme statt.
Lecken der Pfannen und Absatz von Salz an den Feuerzügen nöthigten dazu, dieselben
von viel größerm Querschnitte als eigentlich nöthig zu nehmen; auch die Einrichtung
der Feuerherde und Roste bei den gewöhnlichen Pfannen ist ganz irrationell und führt
einmal zu unvollständiger Ausnützung des Brennmaterials, und zweitens zu schneller
Abnützung des Pfannenbleches.
Was die dritte Frage betrifft, so verbreitet sich Pohl mit
großer Ausführlichkeit über die theoretische Verbrennungswärme und den theoretischen
Heizeffect der Kohle und über die Ursachen, warum die Leistung derselben in der
Praxis hinter der Theorie zurückbleibt; wir wollen ihm darin nicht folgen und nur
erwähnen, daß nach seiner praktischen Erfahrung die Kohle besser ausgenützt wird,
wenn man sie in einem 6 1/2 engl. Fuß (1m,98) hohen Heizraume verbrennt, als wenn derselbe nur 4 1/2 Fuß (1,m37) hoch ist. Er führt an, daß man die
Angabe finde, in den besten Cornischen Kesseln würden bis 11k,8 Wasser vom Siedepunkte mit 1k Kohle verdampft; aber mit großem Rechte
bemerkt er, daß bei diesen auffällig hohen Resultaten das mechanische
Ueberschleudern von Wasser (priming) nicht
berücksichtigt sei. Immerhin kann man behaupten, daß gute Dampfkessel 8 bis selbst
10k Wasser per 1k Kohle verdampfen, und die Frage liegt
nahe, warum die Leistung der Salzpfannen so weit dahinter zurückbleibt, während doch
die Heizfläche und die geringe Spannung des Dampfes zu ihrem Vortheile sprechen
sollten. Alle bisherigen Versuche, diese Sachlage zu ändern, sind fehlgeschlagen,
hauptsächlich weil für einen so billigen und voluminösen Artikel keine
Complicationen des Apparates anwendbar sind. (In Lancashire kostet das gewöhnliche
Soggsalz häufig nur 6 Sh. die Tonne.)
Die erste Idee zu einer bessern Verdampfungsmethode wurde Pohl durch die Pfannen mit oberschlächtigem Feuer gegeben, welche er in
chemischen Fabriken zur Concentrirung von Schwefelsäure (vgl. 1871 201 351) und Sodalaugen angewendet sah, und es fiel ihm
ein, daß sich dieses Verfahren noch verbessern lasse, wenn man die Abdampfpfanne,
statt mit einem Gewölbe, mit einer zweiten Pfanne bedecke. Dabei kann man den
weitern Vortheil erreichen, die Flamme durch einen nur 3 Zoll (76mm) weiten Canal zwischen der
Flüssigkeitsoberfläche in der untern und dem Boden der obern Pfanne durchzupressen,
und somit ihre Hitze fast vollkommen auszunützen. (Vgl. 1875 218 488. D. Red.)
Pohl konnte eine solche Combination nirgends auffinden,
und was Kochsalzfabrikation betrifft, so kann ich meinerseits ebenfalls keine Notiz
davon entdecken; dagegen habe ich für andere Zwecke (z.B. Verdampfung der
gebrauchten Laugen von der Stroh- und Esparto-Papierfabrikation)
dieselbe Combination selbst vor 15 Jahren construirt und vielfach seitdem anderwärts
gesehen; unzweifelhaft ist das auch schon viel länger als 15 Jahre geschehen.
Freilich kann man nicht läugnen, daß gerade in der Salzfabrikation diese Combination
ungemein passend scheint und doch nirgends in Anwendung gekommen ist, bis Pohl sie einführte. Pfannen mit Oberfeuer sind freilich
schon früher vorgeschlagen worden (Pohl erwähnt ein
englisches Patent von Hall und Rosen von 1864), immer aber nur mit einem Gewölbe bedeckt, und haben sich
keinen Eingang verschaffen können. Pohl macht darauf
aufmerksam, daß die Gewölbehöhe bei einer Pfanne von 20 Fuß (6m, 10) Weite mindestens 2 Fuß (610mm) sein müsse, wodurch die Flamme viel zu
entfernt von der Flüssigkeit gehalten wird. Die bedeutend vermehrte Schwierigkeit
des Soggens erwähnt er gar nicht.
Pohl's eigene Construction ist nun in Fig. 33 und 34 skizzenhaft
angedeutet und wird mit Hilfe der nachstehenden Buchstabenerklärungen leicht
verständlich sein.
A Oberpfanne.
B Unterpfanne,
a Feuerstelle, 1m,37 hoch über dem Roste.
b Feuerthür.
c Rost.
d Zugraum zwischen der Soolenoberfläche
in der Unterpfanne und dem Boden der Oberpfanne.
e Säulen, welche auf Bohlen stehen und
die Oberpfanne tragen.
t Rauchsammler.
g Kamin.
h Ziegelgewölbe.
Beim ersten Sieden wurde ein Zwischenraum von 6 Zoll (152mm) bei d
gelassen, und die Gase traten bei f mit einer Temperatur
von über 200° aus. Bei einem zweiten Versuche hielt man die Soole niedriger
und ließ 8 Zoll (203mm) Zwischenraum bei
d; die Temperatur bei f
stieg dann auf 230°. Darauf wurde die Soole in der Unterpfanne wieder höher
gehalten, so daß 4 1/4 Zoll (114mm) bei d blieben; die Temperatur in f war dann 138° und stieg beim stärksten Feuern nicht über
142°. Der zweite Sud beansprucht 16 Tage, während welcher Zeit die
Pfannentemperatur alle 12 Stunden festgestellt wurde. Der Durchschnitt in der
Oberpfanne war 710° in der Nähe der Feuerung, 55 1/2° in der Mitte und
49° am Ende. Die Temperatur der Unterpfanne muß an der Oberfläche constant
107 1/2° gewesen sein, denn nur das feinste Buttersalz fand sich vor. Der Zug
war so stark, daß das Salz gegen das Ende der Pfanne zugetrieben wurde, welches sich
dort bis an die Oberfläche der Soole anhäufte, während der Theil der Pfanne in der
Nähe der Feuerung nicht so voll war. Bei spätern Suden mit reducirter Rostfläche
füllte sich die Pfanne ganz umgekehrt, vorn mehr als hinten. Da weniger Dampf
entwickelt wurde, so war auch der Zug weniger intensiv. Um diese Zeit war die
Temperatur der entweichenden Gase nur 104° und bei langsamem Feuern kam sie
bis 55° herab, wobei Dampfwolken in großen Mengen aus dem Kamin entwichen.
Augenscheinlich ging ein großer Ueberschuß von atmosphärischer Luft mit durch, was
auch durch die Gasanalyse bestätigt wurde, und Pohl
kehrte daher zu größern Rosten zurück.
Das Feuern geschah in folgender Weise. Entlang allen Pfannenöfen und in gleicher Höhe
mit der Oberpfanne läuft ein Schienengleise, auf dem ein kleiner, mit Kohlen
gefüllter Wagen läuft, von welchem eine Kette herabhängt. An der Kette hängt eine
Schaufel, welche 50 Pfd. (= 22k,5) Kohlen
faßte. Die Feuerthüre wird geöffnet, die zusammengebackene Kohle wird nach hinten
geschoben und die Schaufel mit frischen Kohlen auf den leeren Raum im Vordergrunde
ausgeleert. Bei diesem Verfahren entweicht gar kein Rauch aus dem Schornstein, und
es findet sich nur ein wenig Nuß in dem Rauchsammler f
und im Salze selbst vor.
Das Resultat des 16tägigen Sudes einer Soole von 25,27 Proc. Salzgehalt, welcher
57t Kleinkohle von Little Hulton in
Lancashire beanspruchte, war:
82t seines Buttersalz (aus
der Unterpfanne),
49t Soggsalz (aus der
Oberpfanne).
Bei dem alten Verfahren würden diese beansprucht haben:
82t
Buttersalz
54t
13
Ctr.
Kleinkohle
49t
Soggsalz
26t
10
„
„
––––––––
81t
3
„
„
Wirklich verbrannt
57t
0
„
„
––––––––
Ersparniß
24t
3
„
„
Dies war sehr ermuthigend, aber die Qualität des Salzes in der Unterpfanne schien
eine Zeitlang diesem Vortheile die Wage zu halten. Wenn die Unterpfanne beinahe voll
war, wurde die Thür aufgemacht, die Mutterlauge abtropfen lassen und das Salz in
Schubkarren herausgekarrt. Wenn die Arbeiter mit den Spaten in das Salz
hineingruben, so
erschien es als schneeweiße Masse, hier und dort durch schwarze horizontale Streifen
unterbrochen. Ruß bildet sich natürlich durch die bei der niedrigen Temperatur nicht
immer zu vermeidenden unvollkommenen Verbrennung der Feuergase. Soweit er auf der
Oberfläche der Soole entsteht, ist er fast unschädlich, weil er in leichten Flocken
erscheint, welche auf der Oberfläche schwimmen und durch den Zug nach f geführt werden. Was sich dagegen von Ruß am Boden der
Oberpfanne bildet, erscheint in festen Schichten, welche sich durch die Stöße der
Schürkrücken beim Entleeren der Oberpfanne ablösen und in die Unterpfanne fallen, wo
sie wegen ihrer größern Schwere untersinken, die oben erwähnten schwarzen Streifen
bilden und beim Ausleeren das ganze Salz mißfarbig machen. Dies geschah mit einem 4
1/2 Fuß (1m,37) hohen Feuerraum; ein 6 1/2
Fuß (1m,98) hoher Raum gab bessere
Resultate; die Verbrennung der Gase geschieht dann schon vollständig im Feuerraum
selbst, und keine leuchtende Flamme tritt über die Soole, so daß sich kein Nuß
abscheiden kann. Andere Mittel der Rauchverbrennung, z.B. Einführen von erhitzter
Luft in den Feuerraum, schlugen fehl und führten nur zu größerm Kohlenverbrauch.
Das Salz aus den Unterpfannen, wie es mit Ruß verunreinigt war, war freilich sehr
schwer verkäuflich, da es für die Sodafabriken zu feinkörnig ist; diesem Uebelstande
ist jetzt dadurch abgeholfen, daß bei dem Hargreaves'schen Verfahren gerade solches
feinkörniges Salz (Buttersalz) viel geeigneter zur Sulfatfabrikation als das
grobkörnige Soggsalz ist, und der beigemengte Ruß ist ebenfalls völlig unschädlich,
da er einfach in den Cylindern verbrennt.
Pohl versuchte auch, die Ausleerung der Unterpfanne auf
mechanischem Wege zu bewerkstelligen, und zwar durch Riemen ohne Ende, welche unter
der Oberfläche der Soole hingingen, mußte aber die Maschinerie als nutzlos aufgeben
und zur Handarbeit zurückkehren. Dagegen gelang es ihm, noch eine Verbesserung
dadurch anzubringen, daß er die Oberpfanne da, wo die Feuergase zwischen die Pfannen
treten und den größten Widerstand erfahren, bis auf 6 Zoll (152mm) Abstand hob und weiter hinten auf 3
Zoll (76mm) herabließ. Diese Aenderung
zeigte sich als sehr vortheilhaft; die Temperatur in der Oberpfanne betrug
93° vorn (bis auf 98° steigend), 82° in der Mitte, 71°
hinten, und die Pfanne füllte sich ganz gleichmäßig von vorn nach hinten.
Das Mittelresultat einer ganzen Reihe von Suden ist 3t Salz auf 1t Steinkohlen.
Pohl behauptet, daß fein Verfahren folgende Vortheile
erziele:
1. Ersparniß von einem Drittel der Kohle.
2. Hervorbringung eines künstlichen Zuges ohne Kosten, nämlich
durch den aus der Unterpfanne entweichenden Dampf.
3. Möglichkeit der Erhaltung eines intensiven Feuers ohne
Schaden für die Pfannen.
4. Fast gänzliche Abwesenheit von Pfannenstein in der
Oberpfanne, mithin von Leckwerden und schneller Abnützung derselben.
5. Unmöglichkeit, daß ausleckende Soole Salz in den Zügen
absetzt und den Zug behindert, daher die Möglichkeit, mit einem Zugraum von nur
3 Zoll (76mm) Tiefe zu arbeiten.
6. Ersparniß von Arbeit zum Feuern, ein Drittel.
7. Ersparniß an Bodenrente, indem mehr Salz als früher auf
demselben Raume gemacht wird und die Unterpfanne zugleich als Lagerraum dient.
Das Salz tropft in 24 Stunden hinreichend ab, um direct von der Unterpfanne weg
verschifft werden zu können (die Fabriken in Cheshire liegen meist an Canälen
oder schiffbaren Flußarmen), und, da die Unterpfanne, wenn voll, eine ganze
Schiffsladung hält, so erspart man doppeltes Handhaben des Salzes.
8. Bildung einer gewissen Quantität Sodasulfat in der
Unterpfanne durch Verbrennung des Schwefels in der Kohle und entsprechende
Wertherhöhung des Salzes für chemische Zwecke. (Dies dürfte in der Praxis nicht
nennenswerth sein. G. L.)
9. Vermeidung von Rauch in Folge der vollkommenen
Verbrennung.
Die Kohle wird zunächst so vollkommen wie möglich verbrannt und dann die
Verbrennungsproducte gezwungen, alle praktisch disponible Hitze als Arbeitsleistung
abzugeben; sie entweichen nur 104° heiß. Dabei ist das Verfahren einfach und
selbst billiger als das alte; die Rauchcanäle sind von Holz, und Pohl will in Zukunft selbst die Schornsteine aus diesem
Material machen. Weiter kann man doch nicht gehen.
Allerdings ist vorläufig das Verfahren noch nicht hinreichend vervollkommnet, um das
Salz aus der Unterpfanne anders als für chemische Zwecke verwendbar zu machen; aber
da gegenwärtig in England 500000t jährlich
für diesen Zweck gebraucht werden, und man bei deren Fabrikation mit offenem Feuer
noch 250000t gewöhnliches Soggsalz aus den
Oberpfannen erhalten würde, so würde dies die Hälfte der ganzen Salzproduction von
Winsford und Northwich decken, welche nach den letzten Regierungsausweisen 1 1/4
Million Tonnen pro Jahr beträgt. Dies würde einen ganz erheblichen Minderverbrauch
von Kohlen bedeuten.
Ich muß für meinen Theil freilich auf Folgendes hinweisen. Wie Pohl selbst bemerkt (s. o.), wird das feinkörnige (Butter-) Salz
aus den Unterpfannen von
den Sodafabriken gewöhnlicher Art nicht verwendet, sondern vorläufig nur für
Hargreaves' Sulfatverfahren. Ich kann auch nicht absehen, daß dies für die
Sulfatfabrikation in Kesseln, wie sie in der großen Mehrzahl der Sodafabriken
geschieht, je anders werden wird; denn die Vorzüge des gröber krystallisirten und
doch sehr leicht auflöslichen Salzes vor dem feinkörnigen, sich fest
zusammensetzenden und an den Kesseln und Gezähen fest anhängende Buttersalze sind
ganz in die Augen springend und würden nur durch einen bedeutend niedrigern Preis
ausgeglichen werden können, wozu aber wiederum bei dem so niedrigen Grundpreise des
Cheshire-Salzes kein Raum zu sein scheint. Die größere Verbreitung von Pohl's
Salz in England dürfte also großentheils von derjenigen des Hargreaves'schen
Sulfatverfahrens abhängig sein, für welches es freilich ein ganz ausgezeichnetes
Rohmaterial abgibt. Hargreaves' Verfahren, was man noch nicht als billiger oder auch
nur eben so billig als das alte Verfahren hinstellen kann, erwartet in diesem
Augenblicke noch größere Bewährung und Vervollkommnung, ehe an eine Verdrängung des
alten Verfahrens durch dasselbe zu denken ist; es wird allerdings mit Erfolg in
einer Reihe von Fabriken ausgeübt, und der Einwand des größern Kohlenverbrauches ist
mehr und mehr überwunden worden (vgl. 1875 218 416); aber
ich höre Klagen, daß es, wie viele andere pneumatische Processe, mit
Unregelmäßigkeit arbeitet und sehr viel schlechtes Sulfat neben ganz ausgezeichnetem
herauskommt. Vorläufig, d.h. für einige Jahre, wird dadurch kein sehr bedeutender
Bruchtheil der Salzproduction von Cheshire consumirt werden, und wird sich mithin
Pohl's Salzfabrikationsverfahren auch nur mäßig ausbreiten können. In Deutschland,
wo die chemischen Fabriken ohnehin an ein viel feinkörnigeres Fabriksalz als das Cheshire common salt gewöhnt sind, dürfte Pohl's
Verfahren vielleicht beachtenswerth sein, wo Steinsalz nicht billiger bezogen werden
kann.
Tafeln
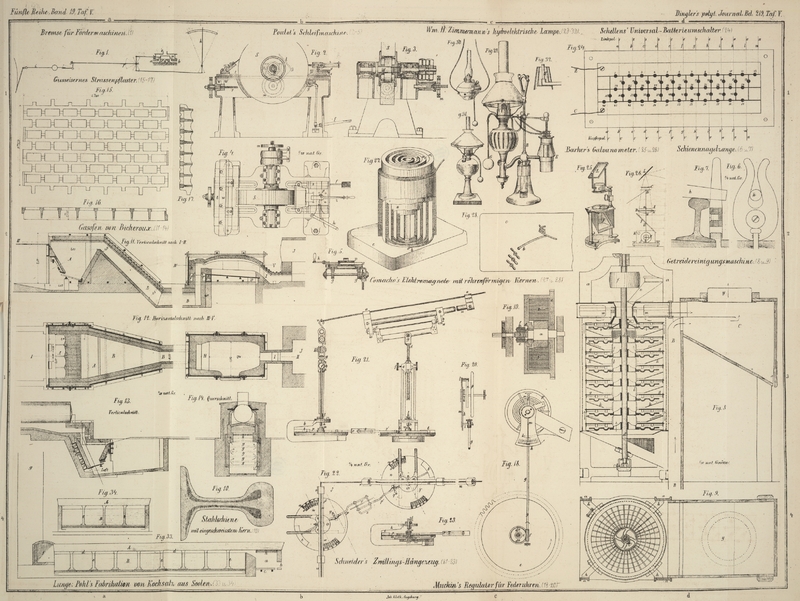