Titel: | Notizen zur hydrometallurgischen Kupfergewinnung; von Dr. Georg Lunge (South-Schields). |
Autor: | Georg Lunge [GND] |
Fundstelle: | Band 219, Jahrgang 1876, S. 323 |
Download: | XML |
Notizen zur hydrometallurgischen Kupfergewinnung;
von Dr. Georg Lunge
(South-Schields).
Mit Abbildungen auf Taf.
VI [c/1].
Lunge, Notizen zur hydrometallurgischen
Kupfergewinnung.
1. Zur Verwerthung des abfälligen
Natriumsulfates.
Bekanntlich entsteht bei der in England so großartig betriebenen chlorirenden Röstung
der Abbrände von kupferhaltigem Schwefelkies eine gewisse Menge Natriumsulfat, genau
entsprechend derjenigen des in den Abbränden zurückgebliebenen Schwefels. Je nach
der Beschaffenheit des Erzes und der Sorgfalt der Schwefelsäure-Fabrikanten
schwankt der Schwefelgehalt der Abbrände, so wie sie in die Kupferhütte geliefert
werden, von 3 bis 7 Proc., manchmal mehr, woraus dann beim Rösten mit Kochsalz die
äquivalente Menge Natriumsulfat entsteht, d.h. von 13 bis 31 Proc. der Abbrände. Bis
jetzt geht in allen englischen Kupferhütten sämmtliches Sulfat verloren; es findet
sich in den sauren Laugen, welche vom Ausfällen des Kupfers zurückbleiben und wird
mit denselben fortlaufen gelassen. In einer frühern Mittheilung (1872 204 308) habe ich das ungemein sinnreiche Verfahren von
Gibb beschrieben, durch welches das Sulfat, und zwar
in Gestalt von Soda, verwerthet wurde. Leider habe ich später (1874 214 467) berichten müssen, daß Gibb's Verfahren wieder
aufgegeben worden ist, und obwohl die Gründe dafür mehr localer Natur waren, so ist
doch bei der großen Kostspieligkeit der Anlage keine Aussicht auf Wiederaufnahme des
Verfahrens vorhanden. Es wird mithin am Platze sein, ein anderes bisher nicht
veröffentlichtes Verfahren ganz kurz zu beschreiben, nach welchem in einer andern
großen Kupferhütte eine Zeitlang das Sulfat als solches gewonnen wurde, neben
Eisenoxyd im Zustande solcher Feinheit und Reinheit, daß es der besten Eisenmennige
gleich kam und dann auch im Großen als solche verkauft wurde. Das Sulfat wurde in
feinkörniger Form und ebenfalls im Zustande sehr großer Reinheit gewonnen, nämlich
nur 1/10 bis 1/4 Proc. Kochsalz und nie eine Spur Eisen enthaltend; es wurde auch
factisch zur Glasfabrikation verwendet. Das Verfahren war folgendes.
Die saure Mutterlauge von der Kupferfällung wurde in einem Ofen mit Ziegelsohle zur
Trockne eingedampft, die resultirende Masse, welche aus Natrium-Sulfat und
-Chlorid und Eisensalzen bestand, in einem andern Ofen schwach geglüht und
unter aufrechten Mühlsteinen sehr fein gemahlen; die Masse wurde darauf in einem
Muffelofen ganz derselben Art, wie sie zum chlorirenden Rösten angewendet werden,
sorgfältig calcinirt, bis sämmtliche Eisensalze auf die höhere Oxydationsstufe
gebracht waren. Nach dem Calciniren wurde das Product in einem mit Rührwerk
versehenen Cylinder mit Hilfe von Dampf in Wasser gelöst und die Lösung dem Klären
überlassen; das Eisenoxyd setzte sich ab und bedurfte nur des Auswaschens, um reine
Eisenmennige darzustellen und in den Handel zu gehen.
Die Lösung (wesentlich Na₂SO₄ und NaCl haltend) wurde in Dampfpfannen
concentrirt. Dieselben waren cylindrisch, 10 Fuß engl. (3m,05) im Durchmesser, 6 Fuß (1m,83) hoch, geheizt durch Dampf von 40 Pfd.
(2at,72) Ueberdruck, welcher in einer
in 5 oder 6 Wendungen um den Umfang der Pfannen herumgehenden und 2 oder 3 Zoll (51
oder 76mm) von derselben abstehenden
Schlange circulirte. Das beim Concentriren sich abscheidende Salz wurde durch ein
Rührwerk gehindert, sich an dem Boden und den Seiten der Pfanne und um die Schlange
herum in Krusten abzusetzen. Das Rührwerk bestand aus einer stehenden, in einem
Zapfenlager am Boden der Pfanne rotirenden Welle mit sechs horizontalen Armen. Die
Concentrirung wurde bis auf 1,37 bis 1,40 spec. Gew. der Flüssigkeit, je nach deren
Zusammensetzung, fortgesetzt; es fand sich dann, daß fast sämmtliches Sulfat
ausgeschieden war; die Flüssigkeit mit dem suspendirten Salze wurde in einen
Abtropfkasten mit falschem Siebboden abgelassen, das Salz mit etwas kochendem Wasser
gewaschen, um die Mutterlauge zu entfernen, und dann in einem Ofen getrocknet, wobei
es ein Product von oben angegebener Reinheit ergab.
Dieses Verfahren, welches augenscheinlich ziemlich erheblichen Aufwand an Kohlen
erfordert, machte sich natürlicherweise nicht bezahlt, als vor einigen Jahren der
Preis der Kohlen auf so enorme Weise stieg, und wurde deshalb aufgegeben. Es ist zur
Zeit auch noch nicht wieder aufgenommen worden, dürfte aber Beachtung für solche
Fälle verdienen, wo Brennmaterial billig und reines Sulfat und Eisenmennige
werthvoll sind. Uebrigens dürfte gerade der erste, mit Gibb's Verfahren
gemeinschaftliche Schritt, nämlich das Abdampfen der sauren Laugen in einem Ofen mit
Ziegelsohle, meiner Ansicht nach zu den technisch schwierigsten Aufgaben gehören,
deren Ueberwindung durch eine verbesserte Construction der Ofensohlen ein großes
Desideratum darstellt.
2. Ueber schwammförmiges Eisen.
(Taf. VI [c/1] Fig. 13 bis 15)
Dieses Product, welches nicht nur bekanntermaßen große Wichtigkeit in der
Hydrometallurgie des Kupfers hat, sondern auch in der Metallurgie des Eisens und
Stahles selbst vielleicht noch eine große Rolle zu spielen bestimmt ist, und
neuerdings auch zur Reinigung von Trinkwasser (nach G. Bischof, vgl. 1871 200 419. 1873 210 46) verwendet wird, verdient wohl eine nähere
Besprechung. Schon im J. 1837 und 1840 wurden englische Patente auf seine
Darstellung (an N. Clay, Vgl. 1838 67 229. 1839 71 52. 415. 1840 76 304. 1841 82 40) verliehen,
und eine ganze Reihe von spätern Erfindern beschäftigte sich mit demselben
Gegenstande und thut es noch jetzt, obwohl bisher alle Versuche, schmiedbares Eisen
in ökonomisch vortheilhafter Weise auf diesem Wege darzustellen, erfolglos gewesen
sind. Am bekanntesten und zugleich am großartigsten in dieser Hinsicht sind die
Versuche von C. W. Siemens (vgl. 1873 209 1. 1875 217 69), denen ein
schließlicher Erfolg sicherlich zu wünschen ist. Siemens
hat es in der That so weit gebracht, daß die Reduction des Eisens und die darauf
folgende Zusammenschweißung desselben mit einem mäßigen Aufwande von Kohlen und
Arbeit vor sich gehen; es scheint aber, als ob der fein vertheilte Zustand des
Eisens dahin geführt hätte, daß es zu viel Schwefel aus den Feuergasen und der
Reductionskohle absorbirte und dadurch für Schmiedeisen und Stahl zu unrein
wurde.
Ohne mich weiter mit demjenigen Theile dieses Gegenstandes zu beschäftigen, welcher
sich auf die Gewinnung von Schmiedeisen und Stahl bezieht, will ich nur auf den
Gebrauch des schwammförmigen Eisens zur Reduction von Cementkupfer eingehen, und
zwar theilweise nach Angaben von Thomas Gibb, welchem ich
schon früher so werthvolle Mittheilungen für meine Publicationen über die nasse
Kupferextraction verdanke, theilweise nach sonstigen Erkundigungen und eigener
Anschauung.
De Bronac und Deherrypon nahmen
1859 ein belgisches Patent (1860 157 342) für die
Verwendung von schwammförmigem Eisen in der Reduction von Schwefelmetallen auf
trockenem Wege. In demselben Jahre patentirte W. Gossage
(vgl. 1859 154 395) die Verwendung von schwammförmigem
Eisen, dargestellt durch Reduction von Pyritabbränden in Muffelöfen, zur
Präcipitirung von Kupfer aus dessen Lösungen. 1862 patentirte G. Bischof (1863 169 474. 1864
172 463) die Fabrikation und Anwendung von
schwammförmigem Eisen für die Kupfercementation; sein Verfahren und Material ist im
wesentlichen dasselbe wie Gossage's. Im J. 1863
patentirte G. Bischof dann noch eine specielle
Ofenconstruction und einen dahingehörigen Apparat für diesen Zweck. Eine ganze Reihe
von Ofenconstructionen wurde 1863 und 1867 von Henderson,
und ein dem Gerstenhöfer'schen Kiesschlichofen ähnlicher Ofen 1869 von Snelus patentirt; aber keine einzige dieser
Constructionen hat sich Eingang in der Praxis verschafft; übrigens hatten die auf G.
Bischof folgenden Erfindungen meistens als Hauptzweck
die Darstellung von Eisenschwamm zur Schmiedeisen- und Stahlfabrikation,
welche eben bis jetzt, namentlich wegen der bedeutenden Absorption von Schwefel aus
den Ofengasen, noch nicht erfolgreich gewesen ist. Der cylindrische rotirende Ofen
von C. W. Siemens reducirt schnell und billig, und auch
ein verticaler Retortenofen ist neuerdings von Blair
(1875 216 304) vorgeschlagen worden. Letzterer überwindet
die große Schwierigkeit, den Inhalt anderer als sehr enger Retorten gleichmäßig zu
erhitzen, dadurch, daß er einen Schacht von 4 Fuß engl. (1m,22) Durchmesser mit einem von oben
hineinhängenden Cylinder versieht, welcher nur einen ringförmigen Raum von 3 bis 4
Zoll (76 bis 102mm) Weite für die zu
reducirende Charge läßt; der weite Schacht wird von außen, der Cylinder von innen
durch Gas geheizt, und die Masse wird dadurch leicht und schnell rothglühend. Der
Apparat verlängert sich nach unten in einen Abkühlungsschacht, aus welchem der
Eisenschwamm von Zeit zu Zeit herausgezogen wird, während frische Mischung von Erz
und Holzkohlenpulver in den ringförmigen Raum von oben eingefüllt wird.
In der Praxis der Kupferextraction wird nur eine einzige Art Ofen zur Darstellung des
zum Präcipitiren dienenden Eisens angewendet. Dies ist ein Flammofen von der Art,
daß die Feuergase, nachdem sie direct über die Charge gegangen sind, unter der
Herdsohle wieder zurückkehren und dieselbe indirect heizen. Die Figuren 13 bis 15 zeigen die
Construction des Ofens in allen wesentlichen Einzelnheiten. Die Gesammtlänge des
Ofens ist 28 Fuß 9 Zoll (8m,753) in der
Zeichnung, oder bis 30 Fuß (19m, 144). Die
Dimension der Arbeitssohle ist 22 bis 23 Fuß (6,695 bis 7m) lang und 8 Fuß (2m,438) breit; sie ist durch niedrige, 9
Zoll (229mm) hohe Mauern in drei
Abtheilungen getheilt, welche auf der einen Seite je zwei Arbeitsthüren haben (oder
auch die der Feuerbrücke nächste Abtheilung nur eine Thür). Jede Abtheilung wird für
sich bestellt, und fertig gemacht; ein Hinüberschaffen von einer in die andere
findet nicht statt. Die gußeisernen Arbeitsthüren müssen luftdicht schließen, zu
welchem Zwecke sie in Nuthen laufen; ganz dasselbe ist der Fall mit der Feuerthür.
Der Feuerraum ist darauf eingerichtet, eine reducirende Flamme zu erzeugen; die
Rostfläche ist 4 × 3 Fuß (1m,219
× 0m,914) und die Träger sind 3 Fuß
4 Zoll (1m,016), neuerdings sogar 4 Fuß 8 Zoll (1m,422), unter der Feuerbrücke angebracht,
so daß man eine sehr tiefe Schicht des Brennmaterials erhält, welche es nicht
gestattet, daß freier Sauerstoff in das Innere des Ofens gelangt. Die Ofensohle wird
von Chamotteplatten gebildet, von 4 Zoll (102mm) Dicke und mit in einander gefalzten Rändern; sie ruhen theilweise auf
Mauern, welche zugleich die Wände der untern Zugcanäle bilden, und theilweise auf
Eisenschienen. Die Flamme welche durch die untern Züge gestrichen ist, steigt dann
in einem senkrechten Schachte entlang der Feuerbrücke hinab, und von dort geht sie
nach dem Schornstein. Ein Register von Chamottemasse befindet sich in dem abgehenden
Zuge; es muß jedesmal geschlossen werden, ehe eine Arbeits- oder Feuerthür
geöffnet wird. Ueber das (9 zöllige = 229mm) Ofengewölbe erstreckt sich eine flache gußeiserne Schale, welche von
kurzen Säulchen und Trägern unterstützt wird. Sie dient dazu, das Erz zu trocknen
und mit Kohle zu mischen; die Mischung wird von dort nach dem Innern des Ofens
chargirt, zu welchem Zwecke gußeiserne Röhren, 6 Zoll (152mm) im Durchmesser, durch das Gewölbe
hindurch geführt sind. Der ganze Ofen ruht auf Mauerpfeilern, und die Hüttensohle
auf der Arbeitsseite muß hinreichend über derjenigen auf der Abfuhrseite erhöht
sein, damit man auf der letztern die Entleerungskästen zwischen den Tragpfeilern
unter den Ofen selbst schieben kann. Die Entleerung erfolgt durch eiserne (6 zöllige
= 152mm) Röhren, welche gerade vor den
Arbeitsthüren in jeder Ofenabtheilung von der Ofensohle durch die Züge durch nach
unten hin gehen. Die Entleerungskästen sind von Eisen, von rectangulärem Querschnitt
und kegelförmig sich nach oben verjüngend. Der Deckel ist fest, und hat in seiner
Mitte eine 6 Zoll (152mm) weite Oeffnung
mit aufstehender Flansche, durch welche der Kasten mit der Entleerungsröhre
verbunden wird. Der Boden des Kastens ist beweglich und dreht sich an der einen
Seite um Angeln, während die andere mit Bolzen und Vorsteckern zur Befestigung
versehen ist. Die Oeffnung im Deckel ist durch eine gußeiserne Platte leicht
verschließbar. Das Ganze läuft auf vier Rädern derart, daß sie die Bewegung des
Bodens nicht hindern. Der Inhalt jedes Kastens ist 12 Cubikfuß (0cbm,340).
Wenn der Ofen hellrothglühend ist, kann er beschickt werden. Die Beschickung besteht
für jede Abtheilung aus 20 Ctr. (1016k)
trockenem „purple ore“ (von der
Kupferextraction zurückbleibendes, mehr oder weniger unreines Eisenoxyd) und 6 Ctr.
(305k) Steinkohlen, welche durch ein
Sieb von 8 Maschen pro Linearzoll (ca. 32 Maschen pro 10cm) passirt ist. Wie schon oben erwähnt,
geschieht die Beschickung von der gußeisernen Schale über dem Ofengewölbe aus. Die
Feuer- und Arbeitschüren werden verschlossen, so daß die Luft einzig und
allein durch die Kohlen auf dem Roste eintritt, wobei man dafür sorgt, daß die
brennende Masse nicht hohl wird, wodurch unconsumirter Sauerstoff in das Ofeninnere
gelangen könnte. Die Reductionszeit in der ersten (der Feuerbrücke zunächst
liegenden) Abtheilung beträgt 9 bis 12 Stunden; in der zweiten Abtheilung 18 Stunden
und in der dritten 24 Stunden. Die Dicke der Schicht auf der Ofensohle beträgt etwa
6 Zoll (152mm). Man muß während der
Reductionszeit jede Abtheilung zwei oder selbst dreimal mit Gezähen umarbeiten.
Trotzdem man dabei den Schieber zumacht, kommt doch etwas Luft in den Ofen; aber das
Umarbeiten ist ganz unvermeidlich, weil die Masse sonst zusammenbacken würde. Die
oben angegebene Zeit bezieht sich auf helle Rothglut; man kann auch bei sehr
schwacher Rothglut arbeiten, und das dabei gewonnene Eisen ist sogar viel besser für
Kupferpräcipitirung; aber da man in diesem Falle um so viel längere Zeit zur
Reduction braucht (bis 60 Stunden), so ist es nicht vortheilhaft, in dieser Weise zu
arbeiten. Bei der großen Tiefe der Feuerung braucht man nur 2 oder 3 mal alle zwölf
Stunden frische Kohlen aufzuwerfen (ca. 15 Ctr. pro 20 Ctr. Erz).
Das Ende der Reduction wird durch Probiren festgestellt. Man nimmt eine kleine Probe,
bedeckt sie auf einer Eisenplatte mit einem Ziegelstein, bis sie erkaltet ist, und
probirt von dem Mittlern (unoxydirten) Theile 1g mit einer Kupfervitriollösung von bekanntem Gehalte, welche aus einer
Bürette unter Umrühren auf den Eisenschwamm laufen gelassen wird; von Zeit zu Zeit
nimmt man einen Tropfen heraus und sieht, ob er noch einen Flecken auf einer blanken
Messerklinge hervorbringt oder nicht; im letztern Falle ist der Proceß beendigt.
Nach Beendigung der Reaction in irgend einer der drei Abtheilungen wird der Schieber
geschlossen; zwei der Entleerungskästen werden unter den Ofen gefahren und ihre
Oeffnungen mit den Ausleerungsröhren durch einen eisernen Reifen und Lehmlutirung
verbunden, und die Charge dann möglichst schnell von den Arbeitschüren aus in sie
hinabgestürzt. Die Kästen werden dann mit dem losen Deckel verschlossen, abgefahren
und 48 Stunden dem Erkalten überlassen. Sie werden darauf mit einem Krahn gehoben
und die Vorstecker losgeschlagen, worauf der Boden sich um die Angeln dreht und die
ganze Masse des reducirten Eisens wegen der nach oben verjüngten Form des Kastens
mit Leichtigkeit herausfällt. Der Schwamm wird darauf in einem schweren Kollergange
mit 6 Fuß (1m,83) im Durchmesser haltenden
Läufern fein gemahlen und durch ein Sieb mit 50 Maschen pro Linearzoll (etwa 20 pro 1cm) gesiebt, worauf es zur Verwendung für
die Kupferpräcipitation fertig ist.
Zwei verschiedene Rohmaterialien sind für die Fabrikation des in der Kupferextraction
verwendeten Eisenschwamms vorgeschlagen worden, nämlich Pyritabbrände, so wie sie
aus den Schwefelsäurefabriken kommen, und das „purple ore“ der Kupferhütten selbst. Folgendes sind
Analysen von Durchschnittsmustern beider Materialien (vgl. auch 1875 215 229 und 231).
Abbrände.
Purple ore.
Eisenoxyd
78,15
95,10
Eisen
3,76
–
Kupfer
1,55
0,18
Schwefel
3,62
0,07
Kupferoxyd
2,70
–
Zinkoxyd
0,47
–
Bleioxyd
0,84
0,96
Calciumoxyd
0,28
0,20
Natriumoxyd
–
0,13
Schwefelsäure
5,80
0,78
Arsensäure
0,25
–
Kieseliger Rückstand
1,85
2,13
–––––––––––––––––––
99,27
99,55.
Sowohl G. Bischof als Gossage
schlugen den Gebrauch der Abbrände direct vor, auf Grund des in die Augen
springenden Vortheiles, daß man dabei deren Kupfergehalt ohne die vorherige Mühe der
nassen Extraction verwerthet. Leider aber enthielten die Abbrände eine merkliche
Quantität Arsenik, wie aus obiger Analyse hervorgeht, und dieses Metall bleibt in
dem Eisenschwamm, mischt sichstch dem Cementkupfer bei und verschlechtert die Qualität des schließlich
daraus gewonnenen Feinkupfers ganz bedeutend. G. Bischof
sagt zwar in seinem Patente von 1862, daß Arsenik und Blei sich bei der Reduction
verflüchtigen. Dies ist aber in der That nur mit dem Blei zum großen Theil der Fall;
das Arsen existirt in den Erzen wesentlich in Form von arsensaurem Eisen und Kupfer,
welche zu beständigen Arsenmetallen reducirt werden, und in der That enthält das aus
Abbränden gewonnene schwammförmige Eisen eine derjenigen der Abbrände selbst fast
genau entsprechende Quantität Arsen. Auf der andern Seite bleibt im „purple ore“ nur die unbedeutendste Spur
Arsen zurück, und es wird jetzt ausschließlich für Eisenschwamm angewendet. Die
folgende Analyse zeigt die Zusammensetzung des daraus in dem oben beschriebenen Ofen
auf die beschriebene Weise gewonnenen schwammförmigen Eisens:
Eisenoxyd
8,15
Eisenoxydul
2,40
Metallisches Eisen
70,40
Kupfer
0,24
Blei
0,27
Kohlenstoff
7,60
Schwefel
1,07
Thonerde
0,19
Zink
0,30
Kieseliger Rückstand
9,00
–––––
99,62.
Wenn man schwammförmiges Eisen zur Kupferpräcipitirung anwendet, so thut man dieses
unter fortwährendem Umrühren. In manchen Fabriken geschieht dies durch mechanische
Rührwerke, in andern durch Handarbeit, in Gibb's Fabrik durch ein Gebläse, welches
durch einen Kautschukschlauch in dem Bottich hin und her geführt wird. Am besten
dürfte sich dazu ein Körting'sches Gebläse (1875 218 287)
eignen. Man erhält auf diese Weise eine sehr vollkommene Mischung, und das
präcipitirte Kupfer enthält nur 1 Proc. metallisches Eisen, mit sehr großer
Ersparniß an Raum, Apparaten und Arbeit gegenüber der Arbeit mit Brucheisen. Der
größern Billigkeit des Materials und der Behandlung bei Anwendung von Eisenschwamm
steht freilich eine größere Verunreinigung des Kupfers durch unreducirte Eisenoxyde
und Kohlenstoff gegenüber; aber die große Annehmlichkeit, statt des voluminösen und
große Apparate erforderlichen Brucheisens mit einem Material zu arbeiten, welches in
der Fabrik selbst abfällt und so viel weniger Zeit zur Wirkung verlangt, scheint der
Anwendung des schwammförmigen Eisens wenigstens für die Massenproduction den Vorzug
zu geben.
Nach G. Bischof soll bei der Anwendung von schwammförmigem
Eisen das Arsen erst nach einigen Stunden präcipitirt werden, während alles Kupfer
viel früher ausgefällt und somit nicht arsenhaltig wird. Gibb dagegen behauptet, nach langjähriger Erfahrung im größten Maßstabe,
daß mit Eisen in beliebiger Form oder Kupferlösungen beliebiger Art er nie die
geringste Spur Arsen in Lösung gefunden habe, sobald sämmtliches Kupfer ausgefällt
ist.
Tafeln
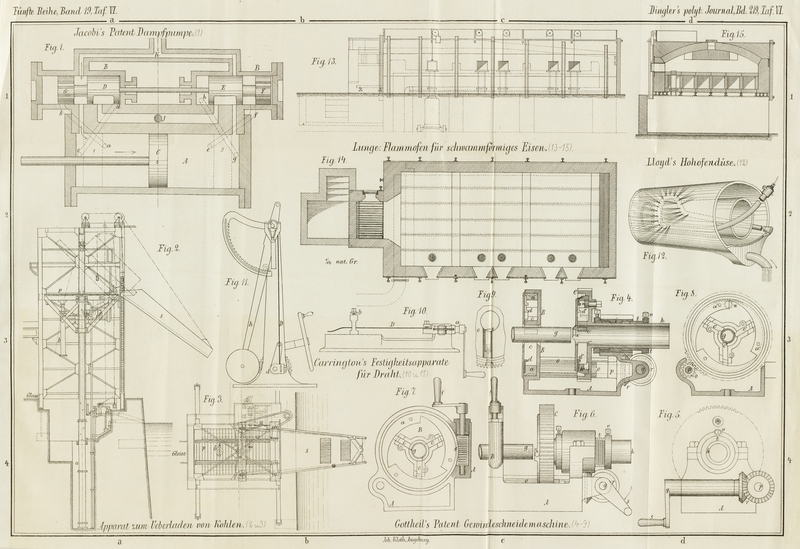