Titel: | Notizen von der Weltausstellung in Philadelphia 1876; von Ingenieur Müller-Melchiors. |
Fundstelle: | Band 223, Jahrgang 1877, S. 445 |
Download: | XML |
Notizen von der Weltausstellung in Philadelphia
1876; von Ingenieur Müller-Melchiors.
Mit Abbildungen im Text und auf Tafel XI.
(Fortsetzung von S. 30 dieses Bandes.)
Müller-Melchiors, Notizen von der Weltausstellung in
Philadelphia 1876.
63) Kegelräder-Fräsmaschine
von E. Grube.
(Mit Holzschnitt und Fig. 1 bis 3 [a. b/1].)
Zwei Werkzeugmaschinen zum Bearbeiten der Zahnform eiserner Kegelräder waren in
Philadelphia ausgestellt. Die eine in kolossalen Dimensionen, um Kegelräder bis zu
3m Durchmesser zu hobeln, ausgeführt
von dem berühmten Maschinenfabrikanten G. H. Corliß in
Providence – die zweite, kaum von der Größe einer Nähmaschine, zum Fräsen von
Kegelrädern bis 140mm Durchmesser, erfunden
und patentirt von einem Deutschen, E. Grube.
Von der letztern, deren Arbeitsprincip vollkommen neu ist, während die Corliß-Fräsmaschine bei wunderbaren
Detailausführungen in ihrem Grundgedanken doch schon wiederholt von Andern
verkörpert worden war, möge es uns gestattet sein, zunächst zu berichten.
Die Zahnform wird hier mittels eines Fräsers hergestellt und könnte in Folge dessen
bekanntermaßen nur dann vollkommen genau werden, wenn es möglich wäre, die Contour
des Fräsers selbst beim Vorwärtsschreiten gegen die Kegelspitze gleichmäßig zu
verjüngen. Nachdem dies praktisch unausführbar ist, begnügte man sich bei der bisher
üblichen Fräsmethode conischer Räder, dem Fräser die Zahncontour des äußern
Theilkreises, die Weite der innern Zahnlücke zu geben, denselben schief gegen das
Zahnmittel einzustellen und nun zunächst die eine Seite sämmtlicher Zähne, bei
nochmaligem Durchgang des Rades und Umstellung des Fräsers die andere Seite der
Zähne abzufräsen.
Bei der Grube'schen Fräsmaschine wird selbstverständlich
der principielle Mangel des Fräsens conischer Räder nicht behoben, und auch hier
werden die Erzeugenden der Zahnflanken parallel zu einander, während sie correcter Weise alle zur
Kegelspitze convergiren sollten; dagegen wird das Einstellen der Maschine wesentlich
vereinfacht, die Symmetrie der beiden Seiten jedes Zahnes unter allen Umständen
gesichert und das ganze Rad bei nur einem Umgang, also
nahezu in der halben Zeit, fertig geschnitten.
Das Mittel, alle diese Vortheile zu erreichen und der ingeniöse Grundgedanke der
ganzen Construction besteht darin, dem auf gewöhnliche Art hergestellten Fräser
außer seiner längs der Zahnflanke fortschreitenden Bewegung noch eine Querbewegung
zu ertheilen. Mittels derselben rückt der Fräser auf der einen Seite der Zahnlücke
vor, geht längs der andern Seite gleichfalls schneidend zurück und die Zahnlücke ist
vollendet, wenn man nicht vorzieht, den Fräser nochmals durchpassiren zu lassen,
wobei er nun längs der zuletzt geschnittenen Seite hinauf- und längs der erst
geschnittenen zurückgeht, bis er außer Eingriff kommt, worauf das zu schneidende Rad
um eine Theilung verdreht und die neue Zahnlücke in gleicher Weise ausgefräst
wird.
Textabbildung Bd. 223, S. 446
Die praktische Ausführung dieses Arbeitsprincipes ist in vorstehendem Holzschnitt,
welcher die Ausstellungsmaschine darstellt, ersichtlich; seitdem ist die Maschine in
den Details verbessert und speciell der Antrieb des Fräsers constructiver angeordnet
worden, wie dies in den Skizzen Fig. 1 bis 3 in zwei Ansichten und im
Grundriß (letzterer bei niedergedrehtem Frässupport b)
dargestellt ist. Hier sind auf dem Ständer der Maschine die zwei Haupttheile, die
Einspannvorrichtung a und der Frässupport b angebracht.
Erstere trägt ein Schneckenrad, auf dessen verticale Welle das zu fräsende Rad
aufgespannt wird. Durch eine Schnecke, deren Kurbel k
auf eine Theilscheibe t einspielt, wird die Verstellung
des Arbeitsstückes um je eine Theilung von Hand bewerkstelligt.
Der Frässupport b muß zunächst in den entsprechenden
Winkel des Theilkreisconus eingestellt werden und außerdem, je nach der Größe des zu
fräsenden Rades, gegen dasselbe zu verschieben sein. Aus letzterm Grunde ist der
Frässupport nicht direct an dem Ständer befestigt, sondern mittels einer
Schlittenführung durch das Handrad h einer Längsbewegung
gegen die Einspannvorrichtung zu fähig. Auf diesem Schlitten ist der Frässupport b um die Zapfen z, z'
drehbar und kann mittels der Schraube s innerhalb eines
Ausschlagewinkels von 90° beliebig verdreht und eingestellt werden. Die
Schraube s ist mit ihrem untern Ende in einem drehbaren
Hals mit dem Schlitten verbunden und greift in eine Mutter ein, die im schwingenden
Support drehbar gelagert ist (Fig. 2); ein Ansatz der
Mutter wird in der geschlitztem Scale, die am untern Halslager der Schraube
befestigt ist, geführt und zeigt mittels eines Indexstriches den Neigungswinkel des
Supportes an.
Mittels dieser zwei Bewegungen kann der Support derart eingestellt werden, daß der
Boden der Zahnlücke die richtige Neigung und die innere Zahnlücke die richtige Weite
erhält. Es wird nämlich der den Fräser tragende Werkzeughalter w auf einer Führungsspindel c geführt, deren Mittellinie die Drehungsachse zz' des schwingenden Supportes schneidet und mit demselben mittels der
Schraube s in den entsprechenden Neigungswinkel gestellt
werden kann. Die Vorrückung des Werkzeughalters w
erfolgt durch die Schraube d, welche zur Führungsspindel
c parallel läuft und, wie in Figur 2 angedeutet, mit
ihrem obern Ende im Support b, am andern Ende in einem
auf der Spindel c befestigten Arm gelagert ist.
Zum Antrieb des Fräsers trägt der Werkzeughalter w hinter
der in Spitzen gelagerten Frässpindel x eine zweite
Welle y, welche mit x durch
Stirnräder verbunden ist. Anderseits erfolgt der Maschinenantrieb auf die mit
Fest- und Losscheibe versehene Welle e und von
dieser mittels eines auf der Drehungsachse z lose
aufsitzenden Stirnrades auf die Welle f, die in einem
Arme gelagert ist, welcher, auf der Drehungsspindel z
befestigt, sich gleichzeitig mit dem schwingenden Support b verdreht. Von der Welle f endlich geht die
Bewegung auf die Welle y des Werkzeughalters über;
nachdem aber dieser sowohl eine hin und her gehende, als auch eine später zu
besprechende Querbewegung ausführt, so ist eine feste Kupplung selbstverständlich
nicht anwendbar. Es wurde daher bei der ältern, im Holzschnitt dargestellten
Ausführung die Welle f
oberhalb der
Drehungsachse zz' angeordnet und von dieser aus mittels
einer Gliederkette auf die Welle y übergegangen;
neuerdings aber wird an f und y je ein Universalgelenk angebracht, mit demselben eine zweitheilige
Zwischenwelle verbunden, die sich verlängern und verkürzen kann, und derart in
soliderer Weise die Bewegung auf den Fräser übertragen.
Die bis jetzt beschriebenen Theile sind, wie oben bemerkt, nur im Stande den Boden
der Zahnlücke eines Kegelrades zu schneiden, genügen dagegen vollkommen zum
Ausfräsen von Stirnrädern. Dazu wird der schwingende
Support b sammt der darin gelagerten Spindel c und Schraube d vertical
gestellt und der Werkzeughalter w mit dem continuirlich
rotirenden Fräser längs des auf der Schneckenradwelle aufgesetzten Stirnrades auf
und nieder geführt. Die vor- und rückgängige Bewegung der Schraube d, sowie die Verstellung des zu schneidenden Rades
erfolgt von Hand; erstere mittels des auf s angebrachten
Griffrädchens, letztere durch die Kurbel k.
Sollen Stirnräder mit schiefen Zähnen geschnitten werden, wie sie gewöhnlich als Schneckenräder Verwendung finden, so kann bei
unveränderter verticaler Stellung des schwingenden Supportes b der gewünschte schiefe Schnitt dadurch erzielt werden, daß die
Führungsspindel c und mit ihr die Schraube d nicht fest gelagert, sondern am obern Ende in
Kugellagern beweglich sind, während das untere Ende von c, wie dies speciell aus dem Holzschnitt und der Figur 1 klar ersichtlich
ist, innerhalb des Supportrahmens b auf einem
Quersupport m in der Längsrichtung der Drehungsachse zz' verschoben werden kann. Da die Schraube d an diesem Ende von der Führungsspindel c getragen wird, folgt sie selbstverständlich der
Bewegung der letztern. Der Quersupport m ist dann in der
erforderlichen Stellung festzuklemmen und das Schneckenrad genau so wie ein Stirnrad
zu schneiden; der größte zulässige Durchmesser von Schnecken- und
Stirnrädern, welche die hier vorliegende Maschine noch aufnimmt, beträgt 400mm.
Nach dem Vorausgegangenen wird nun die Herstellung von Kegelrädern auf der
Grube'schen Maschine leicht verständlich. Die richtige Einstellung des schwingenden Supportes b ist
schon früher erörtert worden, die Möglichkeit einer Querbewegung beim Schneiden der Schneckenräder dargestellt; es handelt
sich somit nur mehr darum, wie diese Querbewegung zur Herstellung der Zahnlücke des
Kegelrades benutzt wird. Um dies zu erreichen, muß mit dem Rückgang des Fräsers von der Kegelspitze der Quersupport m rechts oder links aus
seiner Mittelstellung bewegt werden, je nachdem die rechte oder linke Zahnflanke bearbeitet wird; beim
Aufgang des Fräsers dagegen muß sich der Quersupport entsprechend seiner
Mittelstellung nähern.
Beides geschieht automatisch durch die Maschine, so daß der Arbeiter nur die
Verdrehung des Arbeitsstückes um je eine Theilung vorzunehmen hat. Der Quersupport
m trägt am einen Ende ein Auge, in das die Zugstange
r eingreift, deren anderes Ende mittels eines
Gleitbackens in der Kurbelscheibe g radial verstellbar
ist; diese erhält durch Kegelradübersetzung von der Antriebswelle e eine langsam rotirende Bewegung mitgetheilt. Hierdurch
wird der Quersupport m und damit das untere Ende der
Spindel c und der Schraube d
innerhalb des Supportes b hin- und herbewegt.
Gleichzeitig kommt das auf d befestigte Sperrrad v abwechselnd mit zwei in den Skizzen nicht ersichtlich
gemachten Sperrklinken in Eingriff und setzt dadurch die Schraube d abwechselnd in rechts- und linksgängige
Bewegung, so daß beim Ausgange des Quersupportes mit der
Mittelstellung der Werkzeughalter stets zurückgeschraubt
wird, während er beim Rückgange des Quersupportes zur
Mittelstellung gegen die Kegelspitze vorrückt. Dadurch
entsteht die eingangs beschriebene Arbeitsweise, welche bei einmaligem Vor-
und Rückgange die Zahnlücke fertig herstellt.
Die Einstellung des Quersupportes auf den erforderlichen Hub ist sehr einfach zu
bewerkstelligen derart, daß der Fräser in seiner untern Stellung bei einer halben
Umdrehung der Kurbelscheibe g und ausgelöster Vorrückung
grade die volle Zahnlücke des äußern Theilkreises bestreicht. Dann wird die
hierdurch erzielte Zahnform die genaueste, welche sich überhaupt mit Anwendung eines
Fräsers erzielen läßt, und für alle kleinen Räder vollkommen genügend.
Die Maschine ist einfach, wirksam und leicht zu bedienen und die ganze Anordnung so
„echt amerikanisch“, daß es wohl manchen Enthusiasten,
welche nur jenseits des Oceans mechanisches Genie
entdecken, schwer fallen dürfte, zu glauben, daß sie eine landsmännische Erfindung
vor sich haben.
Die Vertretung von Grube's Kegelräder-Fräsmaschine
hat die Firma Kahlke und Detlefsen in Hamburg, Rödingsmarkt 34, übernommen.
64) Kegelräder-Hobelmaschine
von G. H. Corliß.
(Mit Holzschnitt und Fig. 4 bis 7 [a. b/3].)
Der berühmte Erfinder der modernen Dampfmaschinen-Steuerungen, G. H. Corliß, hat im gleichen Jahre mit seinem ersten
Dampfmaschinen-Patente 1849 eine Kegelräderhobelmaschine patentirt und
hiernach eine Maschine
construirt, die noch heute in der Fabrik der Corliß-Company zu Providence (Rhode Island) arbeiten soll. Die
Ausstellungsmaschine ist in ähnlicher Weise construirt und arbeitet nach demselben
Arbeitsprincipe, das in der Wesenheit darin besteht, die Zahnform mittels eines
Hobelmessers zu bearbeiten, dessen Schnittlinie nach einem Modellzahne (Schablone)
veränderlich, unter allen Umständen aber nach der Spitze des Theilkreisconus
gerichtet ist.
Es leuchtet ein, daß dasselbe Princip allen Kegelräder-Hobelmaschinen, welche
correcte Zahnstanken erzielen wollen, zu Grunde liegen muß, und es ist wohl denkbar,
daß selbst die Priorität des ersten Patentes von G. H. Corliß von andern Constructeuren angefochten werden könnteVgl. 1873 209 241 Note 73.; die Kegelräder-Hobelmaschine, welche durch die Maschinenfabrik von
L. A. Riedinger auf der Wiener Weltausstellung 1873
allgemein bekannt geworden ist, arbeitet genau nach demselben Systeme und dürfte
zudem für gleiche Arbeitsstücke bedeutend billiger herzustellen sein, als die von
Corliß in Philadelphia ausgestellte Arbeitsmaschine.
Dennoch beansprucht dieselbe außerordentliches Interesse zunächst durch ihre
kolossalen Dimensionen, da sie Kegelräder bis zu 3m Durchmesser aufzunehmen vermag, besonders
aber durch die geniale Ausführung aller Details, welche einen ungewöhnlich hohen
Grad von Genauigkeit verbürgen.
Die Figuren 4
und 5 zeigen
die Maschine in den beiden Ansichten, erstere im theilweisen Schnitt durch den
Antriebsmechanismus; der beigegebene Holzschnitt gibt ein perspectivisches Bild nach
einer Photographie hergestellt. Dasselbe zeigt das zu bearbeitende Rad (dessen Zähne
entweder roh gegossen, vorgefräst oder auch auf der Corliß-Maschine aus dem
vollen gehobelt werden müssen, ehe die genaue Zahnform gegeben wird), aufgespannt
auf einer horizontalen Hohlwelle H, die in einem langen
Halse des Gestelles A gelagert ist und am hintern Ende
das große Theilungsrad D (4m,900 Durchmesser) aufgeklemmt trägt;
dasselbe wird, wie aus Figur 5 ersichtlich, durch
Einlegkeile stets an der Lauffläche des Lagerhalses gehalten, während die Welle H je nach der Größe des Arbeitsstückes vor und zurück
geschoben werden kann. Auf dem abgedrehten Umfang des Theilungsrades werden
verschiedene Reihen genau äquidistanter Löcher eingebohrt, um die erforderlichen
Eintheilungen bewirken zu können; die Verdrehung des Rades geschieht durch ein
Getriebe, welches an der verzahnten Seite des Umfanges angreift und von Hand je um
eine Theilung verdreht wird, sobald der Schnitt vollendet ist. Die ganze Anordnung
des Mechanismus zum Einstellen und Festklemmen des Theilungsrades ist äußerst praktisch und compact,
würde uns aber in der Beschreibung wohl zu weit führen; wesentlich ist der große
Umfang des Theilungsrades D, welcher einen immerhin
möglichen Genauigkeitsfehler der Eintheilung erst mehrfach verkleinert auf das
Arbeitsstück überträgt.
Textabbildung Bd. 223, S. 451
In gleicher Weise ist der Modellzahn zwei bis drei Mal weiter als das Hobelmesser von
der Kegelspitze entfernt und im selben Maße gegenüber der Zahnflanke vergrößert.
Derselbe liegt auf der Peripherie des zu einem Kreisquadranten ansteigenden
Maschinengestelles A in dem Bügel b eingespannt; an seine Kante wird durch ein Gewicht mittels der Schnur
s der schwingende Support S mit einem Führungsstifte angepreßt, während derselbe gleichzeitig nach
jedem Schnitte weiter nach abwärts verstellt wird; das Eigengewicht des Supportes
ist dabei durch ein zweites, unter dem Fußboden angebrachtes Gewicht aufgehoben,
welches auf S mittels der Schnur s' einwirkt.
Im Support S gleitet der eigentliche Werkzeugträger w (Fig. 5), der durch
Zahnstange und Getriebe von einer Welle p auf und nieder
bewegt wird und beim Niedergange schneidet. Nachdem somit das Arbeitsstück feststeht und das
Messer bewegt wird, wäre die Maschine richtiger mit
„Shaping“- oder „Feilmaschine“ zu
bezeichnen.
Die Welle p, im Schnittpunkt der Achse xx und yy (Fig. 5), ist in
der zweiten Hälfte B des Maschinengestelles gelagert,
welches zur Lagerung der Hohlwelle H und zum Quadranten
A der Supportführung genau rechtwinklig steht. Der
Antriebsmechanismus ist in Figur 4 im Schnitt
dargestellt, und man ersieht, daß die Zahnradübersetzung, Riemenantrieb mit
verschiedenen Geschwindigkeiten für Vor- und Rückgang, Umsteuerung der
Maschine durch stellbare Anschläge mittels des Supportes w, in ähnlicher Weise wie die Tischbewegung einer Hobelmaschine angeordnet
sind; überraschend ist dabei, gegenüber den andern Dimensionen der Maschine, die
geringe Breite des Antriebsriemens von 32mm, welche deutliches Zeugniß der vollendeten Ausführung und rationellen
Arbeitsweise der Maschine ablegt.
In demselben Theile B des Maschinengestelles ist über der
Welle p eine Hohlwelle gelagert (Fig. 4), welche einen
Zapfen T angegossen trägt, welchen man passend mit
„Supportträger“ bezeichnen kann. Auf demselben ist nämlich
der Support S mittels einer langen Nabe drehbar
aufgesetzt und erhält hierdurch einerseits, indem er sich mit dem Supportträger T um die Achse p dreht, die Einstellung auf den entsprechenden
Neigungswinkel, sowie den Vorschub vom Zahnkopf zum Zahnfuß, während anderseits,
durch Drehung des Supportes S um T, demselben ermöglicht wird, der Contour des Modellzahnes zu folgen. Die
mit dem Werkzeughalter w verbundene Zahnstange ist im
Support S in dessen Verlängerung nach abwärts geführt
(Fig. 5)
und wird von dem auf der Welle p aufgeschnittenen
Getriebe auf und nieder bewegt; damit aber bei Verdrehung des Supportes um T kein Klemmen der Zähne erfolgt, sind die Zähne der
Zahnstange einzeln um je einen Zapfen drehbar in dieselbe eingesetzt, wie dies im
Schnitte aus Figur
4 ersichtlich ist.
Ueber das Getriebe hervorragend und dasselbe in der Ansicht Figur 5 verdeckend, ist
eine Scheibe angebracht, die sich in einem an S
angeschraubten Arme frei beweglich drehen kann. An derselben sind zwei Hebel
befestigt, der eine, nach aufwärts gerichtet, in Verbindung mit der Zugstange z, der andere, nach abwärts gerichtete, mit einer
Frictionsrolle in der Ruth n einspielend, die in Figur 7 in
Ansicht und Grundriß gezeichnet ist. Diese Vorrichtung dient als
Umsteuerungsmechanismus, indem die Zugstange z mit
Anschlägen versehen ist, durch welche sie am Ende des Hubes vom Werkzeugträger w mitgenommen wird. Dadurch schwingt der untere Arm nach
rechts oder links, schiebt hierbei die Ruth n vorwärts
oder rückwärts und verändert gleichzeitig, da sie durch eine Zugstange mit den Riemengabeln
verbunden ist, die Stellung der Antriebsriemen.
Es erübrigt nunmehr noch die Darstellung der Vorrückung und Seitwärtsbewegung des
Supportes S; dieselbe geschieht am obern Ende des
Supportes, welches in Figur 6 in vergrößertem
Maßstabe und mit Weglassung des Quadranten A
herausgezeichnet ist. Hier bedeutet wie früher w den
Werkzeugträger, S den Support, an welchen der Ansatz L geschraubt ist, s' die
Schnur zu dem ausbalancirenden Gegenwicht und z die vom
Werkzeugträger bewegte Zugstange, deren Function zum Umsteuern bereits beschrieben
wurde, und welche gleichzeitig zum Abwärtssteuern des Supportes längs des am
Quadranten A festgeklemmten Zahnsegmentes Z dient. Die Bewegungsübertragung mittels Zugstange,
Ratsche und Räderübersetzung auf das Getriebe g ist aus
der Zeichnung klar ersichtlich und hiermit die Abwärtssteuerung des Hobelmessers in
der Richtung des Pfeiles der Figur 6 gegeben.
Gleichzeitig soll sich jedoch dasselbe auch seitlich, normal gegen die
Zeichnungsebene, verschieben, damit die Zahnflanke nicht geradlinig, sondern nach
der erforderlichen Curve geschnitten wird.
Zu diesem Zwecke ist das Getriebe g breiter als die
Zahnstange Z und gestattet eine Seitenbewegung des
Supportes S um den Zapfen des Supportträgers T. Hervorgebracht wird dieselbe durch den Stift t, welcher mit dem an S
befestigten Ansatze L verbunden ist und mittels des im
festgeklemmten Bügel b gelagerten, von der Schnur s normal gegen die Bildebene angezogenen Hebels h an die im Bügel b
eingespannte Zahnschablone angepreßt wird. Indem somit der Stift t unter der Wirkung des Getriebes g und dem Drucke des Hebels h längs der Kante
αβ des Modellzahnes herabgeführt
wird, erhält die Schneidlinie des Hobelmessers, deren Verlängerung mit der Achse von
t zusammenfällt, bei jedem successiven Schnitt eine
andere Neigung gegen die Bildebene der Figuren 5 und 6, so daß die
genaue Copie des Modellzahnes auf dem Arbeitsstücke hergestellt wird.
Um dabei während des Aufwärtsganges, wo der Stahl nicht schneidet, die Messerspitze
von der Schnittfläche zu entfernen, ist der Führungsstift t nicht fest mit dem Ansatze L verbunden,
sondern im Bolzen q drehbar gelagert. Unterhalb des
Bolzens ist der Stift t keilförmig verlängert und stemmt
sich hier gegen einen zweiten Keil k, welcher beim
schneidenden Niedergange des Messers zurückgezogen ist und dabei den Stift t arretirt, als ob er fest mit L verbunden wäre. Sobald jedoch der Werkzeugträger w bei seinem Niedergange an den untern Anschlag der Zugstange z anstößt und hierdurch die Umsteuerung der
Antriebswelle p
bewirkt, wird auch
gleichzeitig durch das andere Ende der Zugstange z der
Keil k nach aufwärts bewegt und verdreht hierdurch t um den Zapfen q, so daß,
nachdem die Kante von t an der festen Zahnschablone
anliegt, der Support S aus der Bildebene heraus und das
Hobelmesser von der Schnittfläche abgehoben wird. Sobald der hiernach erfolgende
Aufgang des Werkzeugträgers w vollendet ist, wird die
Zugstange z neuerdings verstellt, und dabei gleichzeitig
mit der Umsteuerung der Antriebswelle und der Abwärtssteuerung des Supportes der
Keil k zurückgezogen und der Stift t wieder in die Schneidlinie des Hobelmessers
zurückgebracht.
Der Vorgang beim Schneiden eines Kegelrades ist demnach folgender. Das
vorgeschnittene und überdrehte Arbeitsstück wird auf der Welle H eingespannt und sammt derselben im Ständer A verschoben, bis die Spitze des Kegelmantels in den
Durchschnittspunkt der Hohlwelle H und der Antriebswelle
p fällt, worauf die Welle H wieder fest mit dem Theilungsrade D
verbunden wird.
Hierauf wird der Bügel b losgeklemmt und längs des
Quadranten A verschoben, bis der Supportarm S, der von b mittels der
eingreifenden Zähne von g mitgenommen wird, den
richtigen Neigungswinkel erreicht hat. Dies findet dann statt, wenn das Hobelmesser,
dessen Abstand von dem Werkzeugträger mittels Lehre bestimmt wird, genau die
Oberfläche des überdrehten Arbeitsstückes bestreicht, während das Getriebe g vollständig zurückgezogen ist (in der Stellung der
Figur 6)
und der Stift t am Ende α des Modellzahnes anliegt.
Sobald dies erreicht ist, wird der Bügel b festgeklemmt,
das Theilungsrad D sammt dem Arbeitsstücke so weit
verdreht, daß die entsprechende Spanstärke genommen wird, und hierauf der
Theilungsmechanismus auf die entsprechende Reihe der Theilkreislöcher eingestellt.
Nachdem sodann eine Zahnflanke in der oben beschriebenen Weise gehobelt ist, wird
das Arbeitsstück um eine Theilung verdreht und so fort, bis im ganzen Umkreise
sämmtliche Zähne auf einer Seite behobelt sind.
Hierauf wird das Hobelmesser zum Bearbeiten der andern Zahnseiten umgespannt und der
Stift t an die andere Seite des Modellzahnes angedrückt
dadurch, daß die belastete Schnur s mit einem zweiten
Hebel h verbunden wird, welcher dem in Fig. 6 ersichtlichen
gegenüber steht.
Auf diese Weise wird das Rad bei zweimaligem Durchgange vollendet – mit einer
Genauigkeit, wie sie durch keine andere Maschine erzielbar ist und nur durch die
Abnutzung des Hobelmessers in minimaler Weise beeinträchtigt werden könnte. Auch
dies kann man unschädlich machen, wenn man beim zweiten Durchgange des Rades beim
zuletzt geschnittenen
Zahne zu hobeln anfängt und das Rad in entgegengesetzter Richtung herumführt.
Die hierdurch erzielbare Vollkommenheit im Eingriffe von Kegelrädern wurde durch die
nahezu geräuschlose Functionirung der großen Transmissionsräder in der
Maschinenhalle zu Philadelphia aufs glänzendste dargethan.
65. Der „Groosokat“. (Fig. 8 bis 10 [c/4].)
So genannt wird ein transportabler Laufkrahn, welcher in der russischen Abtheilung zu
sehen war und den Zweck hat, zum Transport von Lasten auf geringe Distanzen zu
dienen. Er besteht aus einer Laufbahn, die aus Blechen und Winkeleisen
zusammengenietet wird (Fig. 8 bis 10) und dem Wagen,
welcher hier so angeordnet ist, daß die beiden Laufrollen auf getrennten Zapfen
geführt sind, so daß sie einen freien Zwischenraum in der Längsachse des Trägers
lassen. Dadurch ist es ermöglicht, die Laufbahn an den aus der Zeichnung
ersichtlichen Haken aufzuhängen, ohne den Weg des Wagens zu beschränken.
Diese Vorrichtung soll speciell zum Ausladen von Schiffen in die Magazinsräume
geeignet und zu diesem Zwecke schon seit mehrern Jahren im
Artillerie-Departement zu Kronstadt in Gebrauch sein. Es wird hier die
Laufbahn auf leichten Dreifüßen von etwa 6m
Höhe aufgehängt derart, daß das eine Ende, welches einen Flaschenzug trägt, auf dem
Deck des zu entladenden Schiffes gestützt wird. Am andern Ende wird die Laufbahn
durch einfache Laschenverbindungen angestückelt, bis sie den Laderaum erreicht, und
in den entsprechenden Distanzen an Dreifüßen aufgehängt. Die Last, welche bis 800k betragen kann, wird mittels des
Flaschenzuges ausgehoben, am Wagen befestigt und rollt dann bei geringer Neigung der
Laufbahn dem Magazine zu.
(Fortsetzung folgt.)
Tafeln
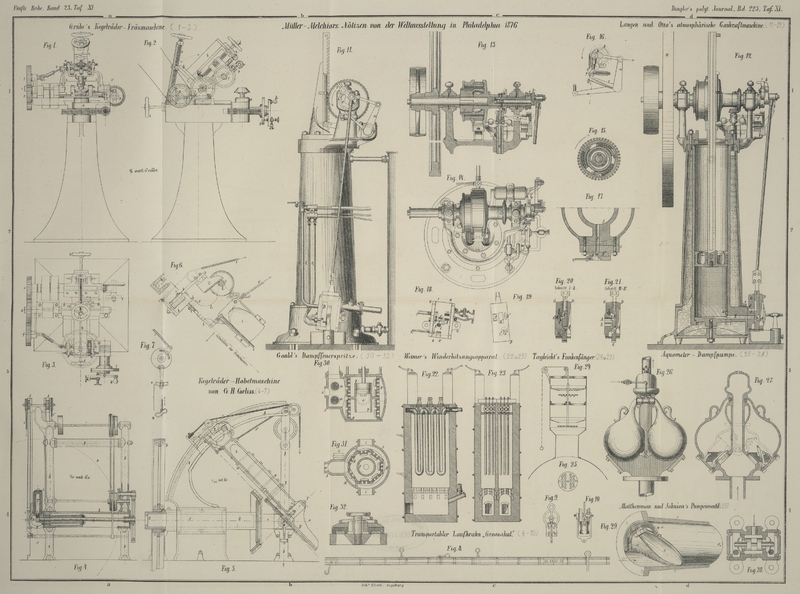