Titel: | Zur chemischen Technologie der Alkalien. |
Fundstelle: | Band 231, Jahrgang 1879, S. 153 |
Download: | XML |
Zur chemischen Technologie der
Alkalien.
Mit Abbildungen auf Tafel 13.
(Fortsetzung von S. 68 dieses Bandes.)
Zur chemischen Technologie der Alkalien.
Rotirende Zersetzungspfanne für Kalium-
und Natriumsulfat; von H. F. Pease, W. Jones und J. Walsh in Middlesbrough.
Bekanntlich führten im J. 1875 die beiden Letztgenannten das Verfahren ein, die
Chloralkalien mit Schwefelsäure in einer einzigen Pfanne zu zersetzen und zu
calciniren (* 1876 220 232). Die Pfanne war mit rotirenden Rührern und einem
gewölbten Deckel versehen, unter welchem die erforderliche Hitze zugeführt wurde.
Nach den neuesten Vorschlägen (* D. R. P. Nr. 1125 vom 20. October 1877. Englisches
Patent Nr. 1760 vom 5. Mai 1877) wird eine rotirende Pfanne und ein unbeweglicher
Rührer verwendet.
Die neue Pfanne, von welcher Taf. 13 Fig. 12 die
Draufsicht, Fig. 13
einen Durchnitt zeigt, ruht unten auf einem Zapfen C,
der durch die Mitte der Pfanne hindurchgeht und oben mit den Trägern des Daches in
Verbindung stehen kann. Ein Kragen, welcher einen Theil der Pfanne bildet, legt sich
um den centralen Zapfen und verhindert, daſs die Chemikalien in das Lager
überlaufen, welches von unten oder von oben durch eine Röhre, die durch den Zapfen
hinunterführt, geschmiert werden kann. Rings um die äuſsere Kante der Pfanne ist ein
Kranz E angebracht, der in einen an dem Mauerwerk
befestigten ringförmigen Kanal hineinragt, welcher, mit feinem Sand gefüllt, den
Zutritt der Luft zu den Gasen in der Pfanne verhindert. Die Pfanne wird durch das
Zahnrad H in Eingriff mit dem Zahnkranz G in Umdrehung versetzt. Neben dem Zahnkranz befindet
sich die ringförmige Schiene I, welche auf den
Tragrollen J ruht, wodurch die Pfanne im Gleichgewicht
gehalten wird.
In der aus Ziegeln oder anderem Material aufgebauten Kammer K ist eine Oeffnung für die heiſsen Ofengase gelassen, während eine
ähnliche Oeffnung auf der anderen Seite die Dämpfe ableitet. Diese beiden Oeffnungen
werden gewöhnlich mit einer Klappe versehen.
Auf der der Ofenöffnung entgegengesetzten Seite reichen zwei radiale Schienen L von dem Mittel zapfen nach der Seitenwand und sitzen
in dieser fest. Diese beiden Schienen bilden einen Winkel von ungefährungefähär 60° mit einander und sind mit Schaufeln B
oder Pflügen M versehen und derart angebracht, daſs die
Schaufeln der einen Schiene die umzurührende Masse in die Bahn der Schaufeln der
anderen Schiene schieben.
Gewöhnlich wird die Pfanne aus Schmiedeisen construirt, welches die
Temperaturschwankungen besser erträgt, und mit Guſseisen gefüttert, da dieses
weniger von den Chemikalien angegriffen wird. Soll sie ganz aus Guſseisen
hergestellt werden, so wird sie in der Regel aus Segmenten P zusammengesetzt, wie in Fig. 14 und
15 Taf. 13 gezeigt ist. Die Verbindung dieser Segmente geschieht mittels
äuſserer Flanschen Q, welche senkrecht abstehen und
durch Bolzen oder Nieten festgehalten werden. An diese wird eine zweite L-förmige,
parallel mit der Pfanne laufende Flansche R für jede
der ersteren Flanschen befestigt, so daſs dieselben zusammen eine an der Auſsenseite
der Pfanne herlaufende T-förmige Flansche bilden. An diese werden zwei gleichwinklig
gebogene Schienen s aus Schmiedeisen oder Stahl derart
befestigt, daſs die langen Flügel derselben mit ihrer Rückseite einander gegenüber
liegend, aber durch eine Leiste t von einander
getrennt, nach abwärts reichen und mit Hilfe der letztern durch Bolzen oder Nieten
mit einander verbunden sind. Die gebogenen Platten und auch in einem gewissen
Umfange die beiden Hälften des guſseisernen T-Stückes folgen der Expansion oder
Contraction der Pfanne, halten diese aber stets völlig wasserdicht verschlossen.
Wenn die guſseisernen Flanschen durch Bolzen mit einander verbunden sind, so
erhalten letztere federnde Unterlagsscheiben.
Sulfatöfen. Um zu verhindern, daſs Salzsäuregas durch
das Mauerwerk der Muffel in den Rauchkanal tritt, preſst E.
K. Muspratt (Englisches Patent Nr. 1733 vom 4. Mai 1877. Vgl. * 1871 202
80. 1875 218 303) in den Muffelofen atmosphärische Luft ein, so daſs hier ein etwas
stärkerer Gasdruck herrscht als in der Muffel selbst.
Storr Best und R. Morris
(Englisches Patent Nr. 1402 vom 10. April 1877) wollen zur Herstellung von Natrium-
und Kaliumsulfat eine Lösung von Chlorkalium oder Chlornatrium mit Pyritröstgasen
behandeln, welche in einem Thurme den herunterrieselnden Salzlösungen
entgegengeführt werden.
Entwässerung von Natriumsulfat; von A. R. Pechiney und Comp.
in Paris. Um das Glaubersalz auf billigere Weise zu entwässern als bisher,
haben A. R. Pechiney und Comp. in Paris (* D. R. P. Nr.
1842 vom 12. Januar 1878) vorgeschlagen, dasselbe in einem mit Rührwerk versehenen
Gefäſs aus Eisenblech oder Holz zu erwärmen, bis die ganze Masse flüssig geworden
ist, was schon bei 33° geschieht. Nun fügt man auf 100 Th. Glaubersalz 16 bis 20 Th.
Kochsalz oder 45 Th. gemischtes Salinensalz (bestehend aus 45 Th. Kochsalz und 45
Th. Magnesiumsulfat) hinzu und erwärmt auf 40 bis 50°. Es scheidet sich bald fast
alles Natriumsulfat wasserfrei (als Thenardit) aus. Man bringt nun die Masse in
einen Kübel mit doppeltem Boden, läſst die Lauge abfliesen und entfernt die letzten
Reste derselben durch Abschleudern.
Herstellung von Kaliumsulfat aus Kieserit. Um die
lösende Wirkung des bei der Umsetzung von schwefelsaurem Magnesium und Chlorkalium
gebildeten Chlormagnesiums auf das entstandene schwefelsaure Kalium aufzuheben, fügt
F. Brünjes in Leopoldshall (D. R. P. Nr. 11 vom 19.
Juli 1877) den Salzlösungen Alkohol zu. Es wird ein Gemisch von 1,5 bis 2 Aeq. Clorkalium und 1
Aeq. Kieserit oder Kainit in möglichst wenig Wasser gelöst, dann 25 bis 50
Vol.-Proc. Alkohol zugefügt. Mit dem schwefelsauren Kalium scheidet sich ein Theil
des überschüssig angewendeten Chlorkaliums aus, in Folge dessen das Kaliumsulfat
leichter auswaschbar ist. Wird beim Abdestilliren des Alkoholes die Lösung auf 1,26
sp. G. gebracht, so scheidet sich reines Chlorkalium, bei 1,33 sp. Gr. dagegen
Carnallit aus.
G. Barsche in Leopoldshall (D. R. P. Nr. 2173 vom 25.
September 1877) schlägt dagegen folgendes Verfahren vor. Es werden 447k Chlorkalium (6 Aeq.) und 492k Bittersalz (4 Aeq.) viermal hinter einander mit
je 300k Wasser ausgelaugt. Fast reines
Kaliumsulfat bleibt zurück, während die erste Lauge namentlich das schädliche
Chlormagnesium enthält, so daſs sich die späteren Laugen zu einer neuen Umsetzung
eignen. Bezeichnet man die nach einander in Arbeit genommenen Salzgemische mit A bis D, so verfährt man
also in folgender Weise. Die erste Lauge von A wird
verdampft und auf Carnallit verarbeitet; die zweite geht nach B und wird dann verdampft; mit der dritten wird erst
B, dann C behandelt,
worauf sie ebenfalls verdampft wird, während der vierte Auszug zunächst auf B, C und dann auf D
gebracht, ehe sie verdampft wird. Nun ist A fertig, B wird mit 300k
Wasser behandelt, die Lauge geht nach C, D, E u.s.f.
Man hat demnach für je 939k Salzgemisch nur 300k Wasser nöthig, während bei vorheriger Lösung des
Chlorkaliums und Bittersalzes 1800k erforderlich
waren.
Leblanc'scher Sodaproceſs. Nach J. Mactear in St. Rollox wird die Bildung von Cyanverbindungen in der
Sodaschmelze dadurch verhütet, daſs man auf 100 Th, Sulfat nicht mehr als 29 Th.
Kohle und 70 Th. kohlensaures Calcium zusetzt (vgl. 1877 224 201). Zur Erreichung
einer leichter ausziehbaren Masse fügt man kurz vor Beendigung der Schmelze noch
etwas gebrannten Kalk zu. – Pechiney setzt statt dessen
etwas schwefelsaures Natrium hinzu, um die bei dem gewöhnlichen Schmelzverfahren
gebildeten Cyanverbindungen am Ende des Schmelzprocesses zu oxydiren. (Nach Chemical News, 1878 Bd. 38 S. 130.)
Nach W. Weldon (Chemical News, 1878 Bd. 38 S. 137) wird
die Bildung von Cyanverbindungen durch eine niedere Ofentemperatur begünstigt, da
z.B. Handöfen im Allgemeinen eine an diesen Verbindungen ärmere Schmelze geben, als
die mit geringeren Temperaturen arbeitenden Drehöfen. Solange Sulfat vorhanden ist,
bildet sich kein Cyan.
Stirling Newall in Durham (Englisches Patent Nr. 4066
vom 1. November 1877) schlägt vor, den kohlensauren Kalk vorzuwärmen und mit Kohle
und Sulfat gemischt auf einmal (vgl. 1877 224 199) in den rotirenden Sodaofen zu
bringen.
Tafeln
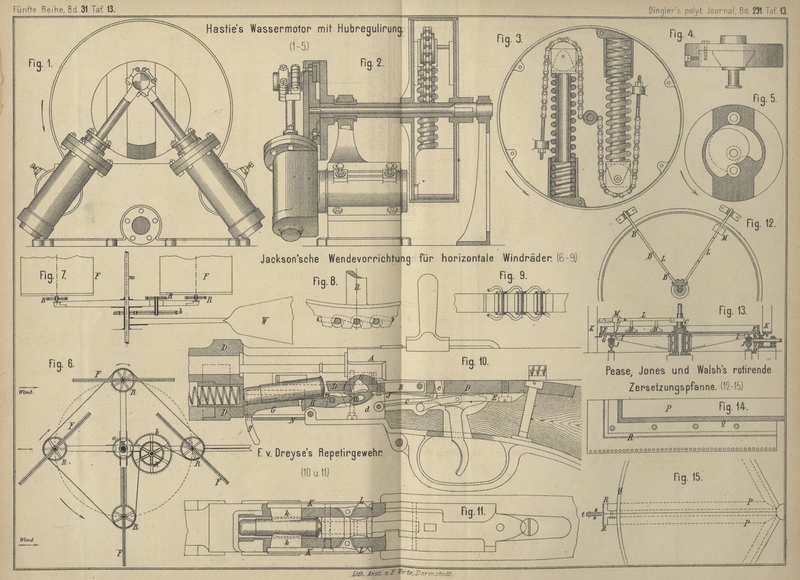