Titel: | Zur chemischen Technologie des Glases. |
Fundstelle: | Band 232, Jahrgang 1879, S. 522 |
Download: | XML |
Zur chemischen Technologie des
Glases.
(Fortsetzung des Berichtes S. 348 dieses
Bandes.)
Mit Abbildungen auf Tafel 45.
Zur chemischen Technologie des Glases.
Glasschmelzöfen. Während die Glasschmelzöfen mit
Holzfeuerung (vgl. 1838 69 155. 1862 164 347), auch die mit directer Steinkohlenfeuerung, wie
sie z.B. von Bagon (* 1840 77 44), Guinand (* 1841 80 36), Bessemer (* 1842 86 182), Crosfield (* 1842
86 424), Chance (* 1848
110 336) und Pilkington
(* 1861 162 109) beschrieben wurden, immer mehr
zurücktreten, finden die Schmelzöfen mit Gasfeuerung mehr und mehr Beifall.
Derartige Oefen wurden in D. p. J. bereits beschrieben von Bellford (* 1855 136 105), White (* 1858 149 176), Schinz (1858 150 332), Venini (* 1861 159 422),
dann von Boëtius (* 1870 197
498), Nehse (* 1876 220
427), Platenka (* 1876 222
322) und Dillinger (1877 224
520), namentlich aber von Friedr. Siemens (* 1872 203 11), dessen Ofen in Deutschland die weiteste
Verbreitung gefunden hat (vgl. 1878 228 92). Zwar
versuchte Schinz (* 1862 166
270. 1863 167 439. 1866 182
216) durch Rechnung nachzuweisen, daſs die Siemens'schen Oefen unpraktisch seien,
und auch Pütsch (1866 180
127 und 489) hatte Manches daran auszusetzen, betonte aber Schinz gegenüber die Vortheile der Generatorgasfeuerung (1867 183 25). Boëtius (* 1863 167 283) und F. Siemens
(1866 180 322) zeigten die Haltlosigkeit dieser Einwürfe
(vgl. 1871 202 417).
Inzwischen hat nun Friedr. Siemens
in Dresden (* D. R. P. Nr. 2955 vom 18. October 1877) seine continuirlich arbeitende
Glasschmelzwanne noch verbessert. Auf Taf. 45 zeigt Fig. 1 einen
Längsschnitt nach I-IV durch die Wanne und einen
Regenerator, Fig. 2 einen
Horizontalschnitt nach V-VI durch die Wanne und Fig.
3 einen Querschnitt nach VII-VIII durch den
ganzen Ofen, Fig. 4 den
Durchschnitt einer Arbeitsstelle. Die vier Regeneratoren R1 bis R4 liegen jetzt dicht neben einander und bilden bei
gleicher Länge ein zusammenhängendes Ganze mit dem Ofen, wodurch der Wärmeverlust
durch Leitung und Strahlung geringer wird als früher. Der gröſsere Theil A der Regeneratoren ist wieder mit Chamottesteinen
ausgesetzt, der durch die Mauer m davon getrennte
kleinere Theil B nicht. Dieser der Einlegestelle
zunächst liegende Theil nimmt die mechanisch fortgeführten Bestandtheile des
Glassatzes auf, so daſs die ausgesetzten Regeneratoren A rein bleiben; diese sind übrigens von der Rösche C aus, die Theile B von den Wechselklappen
W aus leicht zugänglich.
Die Wanne selbst ist nicht mehr durch Zwischenwände in verschiedene Räume getheilt
(vgl. * 1872 203 11 und 14. * 204 190), sondern bildet ein Ganzes, in Folge dessen Reparaturen seltener
werden. In der geschmolzenen Glasmasse U schwimmen an
dem den Arbeitsstellen
a des Ofens zugewendeten Ende Thonkränze oder Ringe k, während durch den oberen Theil O des Ofens die Flamme streicht, so daſs das Schmelzen
des Glases nur von der Oberfläche aus erfolgt. Der Boden b und die Wände w der Wanne sind wie früher
mit Luftkühlungen e umgeben, in denen mittels der
Schornsteine s eine lebhafte Bewegung kalter Luft
unterhalten wird. Neben Erzielung einer längeren Haltbarkeit des Wannenmaterials
wird dadurch verhindert, daſs das Glas durch die Fugen in die darunter liegenden
Regeneratoren dringen kann.
Das bei c eingelegte Glasgemenge wird nach
vorgeschrittener Schmelzung auf den Boden sinken, verdrängt dadurch eine andere
Menge Glas, welche durch die Bodenkühlung steifer und damit specifisch leichter
geworden ist, nach oben. Diese wird wieder, nachdem sie eine Zeit lang an der
Oberfläche der Hitze ausgesetzt war und ordentlich durchgeschmolzen ist, specifisch
schwerer als die darunter befindlichen Schichten und muſs in Folge dessen nach unten
sinken. Dieses durch die Unterschiede im specifischen Gewicht bedingte Verhalten des
Glases in Verbindung mit dem beim Ausarbeiten desselben durch die auf der Bühne M stehenden Glasmacher auftretenden hydrostatischen
Druck in der Pfeilrichtung nach den Arbeitsstellen hin ruft eine schlängelnde
Bewegung der Glasmasse hervor. Die im Glase schwimmenden, durch die Bewegung
desselben in der Richtung nach den Arbeitsstellen hin dicht zusammen und gegen die
Wandung w der Wanne gedrängten Kränze k verhindern, daſs noch nicht gehörig durchgeschmolzene
Glasmassetheilchen direct zu den Arbeitsstellen hingeführt werden; dieselben werden
vielmehr an oder in den Kränzen je nach fortgeschrittener Schmelzung aufgehalten.
Durch Einwirkung der Hitze durchgeschmolzen, sinken sie alsdann zu Boden und
verdrängen andere specifisch leichtere Glasmassen nach oben in die Nächstliegenden
Kränze, worauf das Spiel von neuem beginnt. Dieses Auf- und Niedersteigen und
ununterbrochene Fortschreiten verursacht ein jedesmaliges Durchschmelzen des Glases,
bis die Glastheilchen vollkommen geläutert zur Verarbeitung gelangen. Da die Kränze
ziemlich tief eintauchen, so muſs das Glas immer fast bis unten hin untersinken,
wodurch Stauung und daraus folgende Entglasung vermieden wird.
Generatorgase und Luft treten getrennt durch die über einander liegenden Kanäle g und l ein, die Flamme
streicht quer durch den Ofen, die Verbrennungsproducte entweichen durch die
gegenüber liegenden Kanäle zu den Regeneratoren und gelangen durch die zu den
Wechselklappen führenden Kanäle x zum Schornstein.
Durch diese Anordnung der Kanäle g und l erhält das Glas im freien Raum der Wanne vor den
Kränzen, welche man mit dem Schmelzraum der früheren Construction vergleichen
könnte, die gröſste Hitze, während sich in dem übrigen Theile des Ofens nach den
Arbeitsstellen zu die Zahl der Kanäle verringert und somit die Hitze abnimmt. Zur
Mäſsigung der Hitze im
vorderen Theile der Wanne wird der Schornsteinzug so geregelt, daſs aus den
Arbeitslöchern die Flamme heraustritt.
Jeder Theil der Wanne ist durch die Luft- und Gaskanäle nach dem Aufheben der
Chamotteplatten p leicht zugänglich. Die von dem Glase
angegriffenen Kränze werden durch die Oeffnung d
ausgewechselt; zum Anwärmen stellt man sie vorher in der Oeffnung auf.
Wo es sich um Massendarstellung namentlich gewöhnlicher Flaschen handelt, leistet
dieser Ofen Vorzügliches. Versuche, welche Referent über die Ausnutzung der
Brennstoffe (vgl. 1876 220 255) in denselben gemacht hat,
sollen nächstens mitgetheilt werden.
Um in gewöhnlichen und anderen Glasschmelz-Wannenöfen fortdauernd
schmelzen und arbeiten zu können, schlägt F. Siemens in
Dresden (* D. R. P. Nr. 925 vom 3. Juli 1877) ferner vor, ein mit Boden versehenes
zweitheiliges Schiffchen, wie die beiden Schnitte Fig. 5 und
6 Taf. 45 zeigen, auf dem Glase schwimmen zu lassen. An jeder
Arbeitsöffnung des Wannenofens schwimmt eines derselben auf dem Glase und der
Glasmacher entnimmt das zu verarbeitende Glas aus der der Ofenöffnung zugekehrten
Arbeitsabtheilung A, während die andere abgekehrte
Abtheilung B das Glas durch die Oeffnungen r aus der Wanne empfängt und durch die im Stege s befindlichen Oeffnungen a in die Abtheilung A übertreten läſst. Die
Löcher r sind in der Auſsenwand in solcher Höhe
angebracht, daſs das Glas aus der Wanne direct unter der Oberfläche des Glases
geschöpft wird. Alle Unreinigkeiten, welche auf der Oberfläche des Glases schwimmen,
bleiben also zurück und das eingetretene Glas wird, indem sich dasselbe über die
Oberfläche der Abtheilung B verbreitet, unter der
Einwirkung der Hitze raffinirt und sinkt nach unten in dem Maſse, wie durch das
erhöhte specifische Gewicht des Glases bestimmt wird und neues Glas durch die
Oeffnungen r eintritt. Die Löcher a sind fast am Boden des Schiffchens angebracht und
vermitteln den Eintritt des durch sein vergröſsertes specifisches Gewicht gesunkenen
raffinirten Glases von B nach A. Das geläuterte Glas tritt also in den unteren Theil der Abtheilung A ein, um an der Oberfläche derselben Abtheilung vom
Glasmacher, ähnlich wie aus einem gewöhnlichen Arbeitsringe, gesammelt und
verarbeitet zu werden. Die Gröſse der Schiffchen richtet sich nach der Menge des aus
einem Arbeitsloche zu verarbeitenden Glases, nach der Schmelzfähigkeit des
Wannenofens und nach der angewendeten Hitze; doch dürfte 1m Länge bei 0m,5
Breite und 0m,25 Tiefe meist genügen.
Um die Temperatur des Glases in der Abtheilung A etwas
zu mäſsigen, ist es zuweilen zweckmäſsig, durch Erhöhung des Steges s eine Schutzwand gegen die Ofenhitze herzustellen,
welche, wie die Durchschnitte Fig. 7 und
8 Taf. 45 zeigen, zu einer völligen Bedeckung der Arbeitsabtheilung
ausgedehnt werden kann (vgl. * 1852 153 23. * 1872 204 193).
Rickman in London (Engineer, 1878 Bd. 45 S. 457) geht bei seinem
Glasschmelzofen wieder zur Halbgasfeuerung zurück, wie Verticalschnitt I-II und Horizontalschnitt III-IV
Fig.
9 und 10 Taf. 45
zeigen. Die Kohlen werden durch die Oeffnung F in den
Behälter A eingefüllt, vergasen in dem Generator B, während die gebildete Koke auf dem steilen Roste C verbrennt. Zu beiden Seiten der Generatoren liegen
Luftkanäle E. Die durch dieselben zugeführte heiſse
Luft mischt sich mit den aus den beiden Generatoren in den gemeinschaftlichen
Verbrennungsraum D eintretenden Gasen, die Flamme
schlägt durch die 6 Oeffnungen G, umspült die 6
gedeckten Häfen H, worauf die Rauchgase durch die
Kanäle K und dem Sammelkanal L in den Schornstein S entweichen. Ein in der
Glasfabrik von Pellat und Comp. in London befindlicher
Ofen soll sehr befriedigend arbeiten; eine so gute Ausnutzung der Brennstoffe als
durch Regenerativfeuerung kann mit demselben natürlich nicht erreicht werden.
Im Anschluſs hieran möge nach der Glashütte, 1878 S. 33 auch der Ofen von Boëtius kurz beschrieben werden (vgl. * 1870 197 498), welcher in Deutschland nächst dem Siemens'schen die weiteste
Verbreitung gefunden hat. Wie Längsschnitt und Querschnitt in Fig. 11 und
12 Taf. 45 zeigen, liegen unter dem Herde meist zwei Generatoren A, welche entweder in ganzer Höhe oder nach Fig.
11 nur theilweise getrennt sind. Die Generatoren werden durch geneigte
Ebenen C, schräg liegende Roste D und nach oben sich verengende Seitenwände N
gebildet. Die bei B eingefüllten Kohlen vergasen, die
Koke verbrennt auf dem Rost D, so daſs die Gase bereits
mit hoher Temperatur in den Flammenkanal K eintreten.
Die durch die Seitenkanäle F zugeleitete atmosphärische
Luft erwärmt sich an den Seitenwänden N des Generators
und den horizontalen Kanälen H, tritt aus einer Anzahl
seitlicher Oeffnungen in den Gasstrom ein, die Flamme umspült die Häfen G, während die Rauchgase durch kleine Kamine m entweichen.
A. Pütsch in Berlin (* D. R. P. Nr.
1034 vom 1. November 1877) verwendet eine vereinfachte Regenerativfeuerung, welche
in Fig. 13 und 14 Taf. 45
in Verticalschnitt I-II und Horizontalschnitt III-IV dargestellt ist. Die Gase werden in dem dicht an
den Ofen gebauten Generator A erzeugt, treffen bei B mit der aus dem Spalt a
strömenden, stark vorgewärmten Luft zusammen, die Flamme umspült die Häfen H, während die abziehenden Feuergase durch den Spalt
b nach der Steuerkammer D gelangen. Diese enthält zwei Oeffnungen d1 und d2, welche zu den beiden Regeneratoren E1 und E2 führen und
abwechselnd durch einen aus feuerfestem Material hergestellten Schieber geöffnet und
geschlossen werden können. In Fig. 14
hält der Schieber die Oeffnung d2 verschlossen, die abgehenden Feuergase ziehen
daher durch die Oeffnung d1 in den Regenerator E1 und geben ihre Wärme an die gitterförmig aufgestellten
Steine ab, worauf sie durch den Kanal c bei der aus dem
Grundriſs ersichtlichen Stellung der Luftklappe F in
den Schornsteinkanal e gelangen.
Inzwischen tritt atmosphärische Luft durch das mit einem Regulirschieber versehene
Luftloch f auf die andere Seite der Luftklappe F und von dort in den Kanal c2, durchstreicht den durch vorherigen
Betrieb erhitzten Regenerator E2 und verläſst denselben stark erwärmt durch die
Oeffnung g2, welche zu
einer zweiten der ersten entsprechenden Steuerkammer G
führt. Je nach der Schieberstellung steht diese durch die Oeffnungen g1 und g2 abwechselnd mit
einem der beiden Regeneratoren in Verbindung. Aus der Kammer G tritt dann die heiſse Luft in den Kanal a.
Nach einer gewissen Zeit wird die Stellung der beiden Schieber sowie der Luftklappe
gewechselt. Der Weg der Feuergase geht dann durch die jetzt freiliegende Oeffnung
d2 nach dem
abgekühlten Regenerator E2 und hierauf durch den Kanal c2 nach dem Schornsteinkanal e; die durch das Luftloch einziehende atmosphärische Luft dagegen tritt
durch Kanal c1 in den
heiſsen Regenerator E1
und von dort durch die Oeffnung g1 in die Steuerkammer G. Für beide Fälle der Schieber- und Luftklappenstellung ist die
Zugrichtung nur in den Regeneratoren und den Kanälen bis zur Luftklappe eine
verschiedene; im Ofen selbst bleibt sie unverändert.
E. H. Siebert in Berlin (* D. R. P.
Hr. 3647 vom 7. Mai 1878) hat einen Glasschmelzofen mit Regenerativfeuerung
construirt, von welcher Fig. 15 bis
18 Taf. 45 den senkrechten Längsschnitt I-II, den Horizontalschnitt III-IV, die
Schnitte V-VI und VII-VIII
veranschaulichen.
Das durch den Kanal a zugeführte Generatorgas geht bei
der in Fig. 16
gezeichneten Stellung des Gaswechselventiles B' durch
den Kanal b zum Regenerator C' und tritt durch die Oeffnung d in den
Verbrennungskanal D'. Die atmosphärische Luft tritt
durch o ein und gelangt bei der angenommenen Stellung
der Wechselklappe B durch den Kanal c' in den Regenerator C
und durch die Oeffnung d' ebenfalls in den Feuerraum
D', um die Verbrennung des Gases zu unterhalten.
Die Verbrennungsproducte entweichen durch den zweiten Verbrennungskanal D und theilen sich hier, indem ein Theil durch den
Regenerator F', den Kanal b', zur Wechselklappe B' und von hier durch
den Kanal f', der zweite durch den Regenerator F und die Kanäle c und f zum Schornstein gelangt. Nach entsprechender Drehung
der Wechselklappen durchziehen die bei a und o eintretenden Gase den Ofen in umgekehrter
Richtung.
Um die unangenehmen Wirkungen der abwechselnd von der einen und der anderen Seite
kommenden Flamme auf die Häfen zu beseitigen, sind im Oberofen zwischen je zwei
Häfen die Oeffnungen k angebracht, welche in die
horizontalen Sammelkanäle m münden, die ihrerseits wieder mit den
senkrechten Kanälen g und h verbunden sind. Die von hier abgezweigten Kanäle l, l' laufen unter den Luftzuführungskanälen c,
c' und nur durch Thonplatten von diesen getrennt der ganzen Länge nach hin
bis p, wo sie sich zu dem einen Kanal x vereinigen, der zum Schornstein führt. Während des
Schmelzprocesses arbeitet der Ofen mit einer wechselnden Flamme. Sobald es nöthig
wird, Theile des Ofens in ihrer Temperatur zu steigern, wird der Schornsteinschieber
3 gezogen. Hierdurch wird ein Theil der Flamme
genöthigt, seinen Ausweg durch die Oeffnungen k zu
nehmen, wodurch den Häfen an der der Flammenrichtung abgekehrten Seite Wärme
zugeführt wird. Durch Schlieſsen und Oeffnen der kleinen Abzugsöffnungen k mittels eingelegter Steine hat man es in der Gewalt,
die Menge der Wärme, welche nach einem bestimmten Theile des Ofens gezogen werden
soll, zu regeln. Die durch k abgeführten Gase sollen
ihre Wärme an die Luftkanäle abgeben.
Um bei der Ausarbeitung des Glases eine gleichmäſsige Hitze zu erzielen, schlieſst
man die Schornsteinschieber 1 und 2, so daſs der Rückgang des Feuers durch die
Regeneratorsysteme aufhört; hierauf werden sowohl Gaswechsel B', als auch Luftwechsel B zur Mitte
gestellt, so daſs die Klappen derselben die punktirten Stellungen annehmen. Hierbei
theilt sich sowohl der Gas-, als auch der Luftstrom in zwei Theile. Durch die
Regeneratorsysteme C' und F' gehen jetzt Ströme Gas und durch die Regeneratorsysteme C und F Ströme Luft,
welche sich in den Verbrennungskanälen D' und D vereinigen und zwei Flammen bilden, wodurch das Feuer
im Ofen selbst gleichmäſsig vertheilt wird. Durch Stellung der Klappen der
Wechselventile kann man jede dieser beiden Flammen verstärken oder schwächen.
Damit nun die Flammen ihren Ausweg nicht durch die Arbeitslöcher nehmen und hier die
Arbeiter stören, wird der Schornsteinschieber 3
gezogen. Hierdurch wird das abgehende Feuer gezwungen, um die Häfen herum seinen
Ausweg durch die Oeffnungen k zu nehmen. Durch Zufluſs
von Gas und Luft und durch Stellung des Schornstein-Schiebers 3 hat man es in der Gewalt, den Inhalt der Häfen auf
der gewünschten Temperatur zu erhalten und auch aus den Arbeitslöchern nur so viel
Flammen austreten zu lassen, als erforderlich ist.
Tafeln
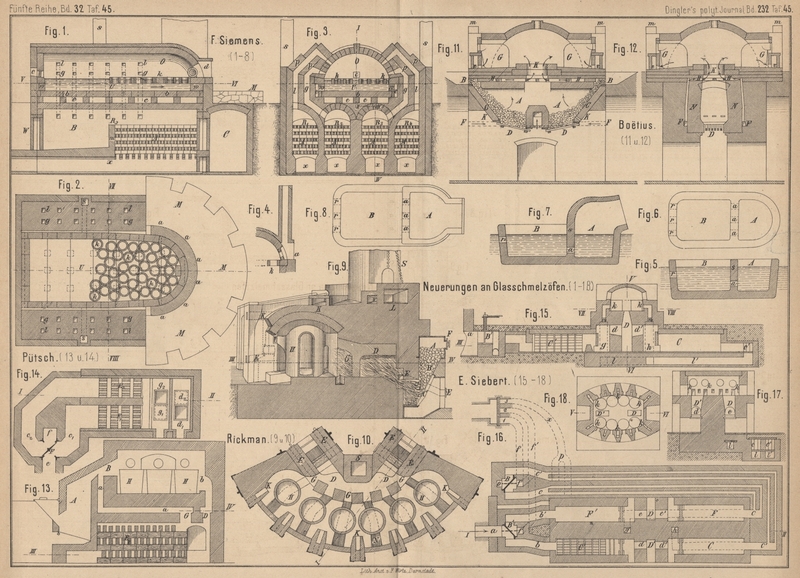