Titel: | Neuerungen an Holzbearbeitungsmaschinen und Apparaten der Chemnitzer Werkzeugmaschinen-Fabrik, vormals Joh. Zimmermann in Chemnitz. |
Autor: | J. P. |
Fundstelle: | Band 235, Jahrgang 1880, S. 338 |
Download: | XML |
Neuerungen an Holzbearbeitungsmaschinen und
Apparaten der Chemnitzer Werkzeugmaschinen-Fabrik, vormals Joh. Zimmermann in
Chemnitz.
Mit Abbildungen im Text und auf Tafel 34.
Holzbearbeitungsmaschinen der Chemnitzer
Werkzeugmaschinenfabrik.
Die mit Rücksicht auf ihre stetige Vervollkommnung (*
1876 222 305. 220 33. 1873 209 6. * 1869 193 177) wiederholt behandelte Zinkenfräsmaschine wurde neuerdings noch dahin
verbessert (vgl. * D. R. P. Nr. 7071 vom 8. April 1879), daſs nun mittels derselben
sowohl die beistehend in Fig. 4 veranschaulichten gewöhnlichen, als auch verdeckte Zinken hergestellt werden können, wie sie die Textfiguren 2 und
3 zeigen.
Fig. 1., Bd. 235, S. 337
Fig. 2., Bd. 235, S. 337
Fig. 3., Bd. 235, S. 337
Fig. 4., Bd. 235, S. 337
Die Maschine hat wie früher vier Frässpindeln, nämlich je zwei auf den beiden
horizontal verschiebbaren Supporten, welche mit ihren Schlitten gemeinschaftlich die
in bekannter Weise eingeleitete verticale Aufwärts- und Abwärtsbewegung vollführen.
Hiermit ist aber auch noch eine seitliche Bewegung der Frässpindeln verbunden, indem
sich die Supporte an den den verticalen Ständerarmen zugekehrten Seiten mit Nasen
gegen angeschraubte Schablonen anlegen, wobei sie durch belastete Hebel angedrückt
werden. Die seitliche Bewegung der Supporte entspricht der Form der Schablonen, und
es ist leicht einzusehen, daſs dieser Mechanismus, sobald entsprechend anders
geformte Schablonen benutzt werden, auch zur Herstellung gewöhnlicher Verzinkungen
und anderer Zinkenformen geeignet ist.
Beim Fräsen verdeckter Zinken werden die Zapfen und
Zinken gleichzeitig gefräst, indem die beiden Bretter, wie Textfigur 1 zeigt, rechtwinklig zusammengespannt gleichzeitig der
Anarbeitung unterzogen werden. Bei jedem Auf- und Niedergang der Frässpindeln werden
demnach vier Zapfen und vier Zinken, nämlich so viele, als Frässpindeln vorhanden
sind, gleichzeitig fertig. Bezüglich der Leistungsfähigkeit der so verbesserten
Zinkenfräsmaschine mag angeführt werden, daſs mittels derselben je 15 gewöhnliche
Zinkenzapfen, je 30 gewöhnliche Zinkenschlitze, oder je 9 verdeckte Zinkenzapfen und
Schlitze gleichzeitig, in einer Minute hergestellt werden können, wobei die
Frässpindeln ungefähr 5000 Umdrehungen in der Minute machen. Diese Maschine ist
sonach jetzt nicht nur zur Kistenfabrikation, sondern auch für die Möbeltischlerei
sehr zu empfehlen.
Neuerdings ist auſser dieser für Massenfabrikation geeigneten Maschine ein einfacher,
billigerer und doch leistungsfähiger Zinkenfräsapparat
(Textfigur 5 und 6) zur Patentirung eingereicht worden; derselbe eignet sich für
jede Tischlerei, kann auf jeder Fräsmaschine angebracht werden und gestattet sowohl
offene, als auch verdeckte Zinken schnell und genau herzustellen, indem man einfach
den Apparat mit der Hand der rasch rotirenden Fräse zuführt.
Fig. 5., Bd. 235, S. 338
Fig. 6., Bd. 235, S. 338
Die Ein Spannung des zu bearbeitenden Holzes erfolgt durch
Schienen, welche mittels Endschrauben festgespannt und beim Lüften durch Federn vom
Holze abgedrückt
werden, so daſs letzteres leicht nach dem Fräsen entfernt werden kann. Die Bretter
werden dabei so eingespannt, daſs sie einen rechten Winkel bilden. Unter der Platte
dieses Einspannapparates wird die Schablone befestigt, welche der herzustellenden
Verzinkung entsprechend geformt ist, nämlich auf der ganzen Länge regelmäſsige
Vertiefungen hat, die man als Zähne bezeichnen kann, und welche in Form und Theilung
den herzustellenden Zapfen und Schlitzen entspricht. – Schiebt man den Apparat an
die Fräse heran, so wird letzterer an der Schablone hingleiten und beim Hin- und
Herschieben die Zinkenschlitze oder Zapfen herstellen.
Bezüglich der Leistungsfähigkeit ist zu unterscheiden, ob bei der
offenen Verzinkung auch, wie bei der verdeckten, abgerundete Zinken und Schlitze
zulässig sind; dann kann man verdeckte und offene Zinken von gleicher Theilung mit
einerlei Schablonen und einerlei Fräsen anfertigen, bei beiden Zinkenarten in der
Minute 16 Zapfen und 16 Schlitze. Wenn hingegen bei offener Verzinkung die Zapfen
eckig gewünscht werden, so ist eine zweite Schablone und eine zweite Fräse extra
nöthig; die Leistungsfähigkeit beträgt dann die Hälfte.
Die Zinken können mittels dieses Apparates in beliebigen
Theilungen angefertigt werden, man braucht nur zu jeder Theilung andere Schablonen.
Man kann mit dem Apparat Bretter bis 500mm breit
und 25mm stark verzinken; dieselben können auch
ungleich dick sein. Der Preis ist 200 M., worin eine Fräse und eine Schablone
inbegriffen ist.
Ein besonderer Zinkenfräsen-Schärfapparat ermöglicht es, die Fräsen für die
Zinkenfräsmaschine und für den Zinkenfräsapparat so genau zu schärfen, wie dies aus
freier Hand, selbst bei groſser Geschicklichkeit, kaum möglich ist.
Die Handhabung desselben ist eine ganz einfache. Die zu
schleifende Fräse wird in die Hauptspindel des Apparates gesteckt und mittels
Schraube darin festgehalten. Auf dieser Spindel befinden sich mehrere
Schraubengänge, deren Steigungen den Steigungen der zu schärfenden
Fräsen-Schneidkanten entsprechen, und es hat der Arbeiter nur nöthig, den
Führungsstift in die betreffende Nuth einzustellen. Beim Schärfen der übrigen
Schneiden der Fräse ist die Spindel mit derselben so viel zu drehen, bis die nächste
Schneidkante vor der Schmirgelscheibe steht. Beide Einstellungen kann der Arbeiter
ablesen; auch wird die letztere noch durch Einschnappen in eine Theilscheibe
besonders gesichert. Während des Schleifens hat der Arbeiter die Spindel mit der
Fräse hin und her zu schieben und so auf die ganze Länge der Schneidkante an der
Schleifscheibe vorbei zu führen. Ein Führungsbogen bewirkt hierbei die Verschiebung
des die Fräse tragenden Supportes senkrecht zur Achse der Schleifscheibe
entsprechend dem Fräsenprofil.
Für Cigarrenkisten- und Jalousie-Fabriken von besonderer
Wichtigkeit ist die patentirte Holzhobelmaschine für
Cigarren- und Jalousiebrettchen zum gleichzeitigen Hobeln mehrerer ungleich
dicker Hölzer (vgl. * D. R. P. Nr. 8564 vom 10. August 1879). Mittels
derselben ist man im Stande, 6mm und mehr in der
Dicke verschiedene Hölzer neben einander so zu hobeln, daſs von allen diesen Hölzern
nur ein gleich schwacher Span weggenommen wird, also sämmtliche Brettchen in
entsprechend verschiedenen Dicken aus der Maschine hervorgehen. Die Brettchen werden
hierbei auf einer Seite gehobelt, wobei die Spandicke beliebig regulirt werden kann.
In Fig. 1 und 2 Taf. 34
ist diese Maschine in zwei Ansichten dargestellt; Fig. 3 zeigt
dieselbe im Durchschnitt.
Der Vorschub des Holzes geschieht durch die im Gestell C gelagerten Walzen A und
B, sowie durch ein doppeltes Rädervorgelege D nebst Stufenscheibe
E. Die Messerwelle F ist
ebenfalls im Gestell C festgelagert und wird von der
Riemenrolle G betrieben. Vor und hinter der Messerwelle
werden die vertical verstellbaren Tische H und J geführt. Oberhalb der Walzen A und B befinden sich, über deren Breite
vertheilt, je sechs Druckrollen K, welche durch
Gewichte L und mittels der Hebel M das zuzuführende Holz auf die Walzen A und B drücken. Die
Gewichtshebel M haben ihren Drehbezieh. Aufhängepunkt
in den Schienen N, welche je sechs Druckstücke O tragen, bezieh. auf welchen sich die Druckstücke
vertical bewegen können. Diese Schienen N sind auf
jeder Seite in einen gemeinschaftlichen Rahmen P
gelagert. Beide Rahmen sind sammt den Schienen und den darauf befindlichen
Druckstücken im Gestell vertical durch die Schrauben Q
verstellbar.
In jeder dieser Stellungen haben die Druckstücke auf den Schienen
N so viel Verticalbewegung, als die Löcher in den
Druckstücken höher sind wie die Schienen selbst. Zu gleicher Zeit haben aber die
Druckrollen K an den Gewichtshebeln M mindestens ebenso viel Verticalbewegung. In Folge
dessen können die Hölzer, welche neben einander gehobelt werden, in der Dicke um
ebenso viel von einander verschieden sein, als obige Verticalbewegung der
Druckstücke und Druckrollen es zuläſst.
Die Zahl der neben einander zu hobelnden Hölzer richtet sich nach
der Zahl der Druckstücke und Gewichtshebel; dieselbe ist zu sechs für die
vorliegende Breite gewählt worden.
Um die Messer von der Messerwelle F
wegnehmen bezieh. leicht und genau einstellen zu können, kann der ganze Druckapparat
in zwei Theilen rechts und links auf dem Tisch aus dem Wege geschoben werden,
nachdem die Stifte R (Fig. 2)
entfernt sind.
Beim Hobeln von stärkeren Hölzern wird der Druck durch Auflegen
der Gewichte S auf die Druckstücke O vergröſsert.
Die Kraft, mit welcher überhaupt die Hölzer vorgeschoben werden,
resultirt aus dem oben erwähnten Gewichtshebeldruck und aus dem Druck, welchen die
Gewichtshebel T nebst Gewichten U hervorbringen, indem dieselben die Vorschubwalzen A und B senkrecht nach
oben drücken. Dieser verticale Hub der Walzen wird durch die Stellschrauben v begrenzt; die Walzen können daher über den Tisch nur
so viel vorstehen, als diese Stellschrauben es gestatten.
Die Tische H und J sind in schräg liegender Führung verstellbar mittels
Schrauben w und w1; letztere regelt die wegzunehmende Spandicke.
Um die Maschine zum Hobeln von gleichen
Dicken umzustellen, werden die Druckstücke O
durch die Schrauben X auf die Schienen N festgebremst und die Gewichtshebel M jederseits durch einen Bolzen unter einander
verbunden, welcher durch das Loch z am Ende jedes
Hebels gesteckt wird. Beim Hobeln gleicher Dicken steht also bei dieser Maschine die
Druckvorrichtung fest, dagegen ist der Tisch H leicht
beweglich. Die Gröſse der Bewegung desselben richtet sich nach der Dicke des Holzes,
welches gehobelt wird, und diese Bewegungsgröſse gibt gleichzeitig die Spanstärke
an, welche von den Hölzern weggenommen wird. Um diese Tischbewegung zu erzielen,
sind die Kegelräder abzunehmen und die Spindel w1 ist etwas vorwärts zu schrauben. Der gelöste Tisch
H bewegt sich dann durch einen Hebel Z und ein aufgestecktes Gewicht nach oben und preſst
das zu hobelnde Holz an die Druckvorrichtung. Damit sich jedoch der Tisch H nicht zu hoch bewegt, wird unten bei b ein Anschlag befestigt, welcher zur rechten Zeit an
die Führung anstöſst. Auf den Rahmen P sind auf beiden
Seiten Zeiger c angebracht, welche auf der Scale d am Gestell C anzeigen,
wie dick das gehobelte Holz wird.
Will man das gehobelte Holz dicker oder dünner haben, so stellt
man die ganze Druckvorrichtung durch die Schrauben Q
höher oder tiefer.
Im Anschlüsse an die Mittheilungen über Schärfapparate für Bandsägeblätter (* 1879
233 96) bringen wir in Fig. 4 bis
6 Taf. 34 einen Apparat zur Darstellung, für welchen die Chemnitzer Werkzeugmaschinen-Fabrik das deutsche Patent
nachgesucht hat. Derselbe dient zum mechanischen Schärfen von Bandsägeblättern und
hat sich auſserordentlich gut bewährt, da er nicht nur die Arbeit weit rascher und genauer verrichtet, als
dies durch gewöhnliche Handarbeit mit der Feile möglich ist, sondern auch durch
jeden Arbeiter, selbst einen Knaben, bedient werden kann.
Das Schärfen geschieht durch eine Stahlfräse A, welche auf der im Bügel C zwischen Körnerspitzen gelagerten Spindel B
aufgekeilt wird, wie in Fig. 4
ersichtlich. Der Bügel C kann durch die Schraube D um Achse E gedreht
werden, um die Fräse dem Sägeblatt entsprechend anzustellen, und wird durch Anziehen
der Schraube E im Tische F
in geneigter Lage festgehalten. In dem Bügel C befindet
sich auſser D noch eine Schraube G, welche mit dem Tisch F
in Verbindung steht und eine federnde Unterlagscheibe H
aus Gummi, die zwischen dem Kopf dieser Schraube und dem Tisch F angebracht ist, zwingt, die Fräse beständig auf den
Zahn der Säge zu drücken. Hierdurch wird eine gleichmäſsige Arbeit der Fräse auf
ihrem ganzen Umfang erzielt. Der Tisch F ist mit dem
Träger J durch die Schraube K verbunden und in einem Schlitze senkrecht verstellbar. Diese Anordnung
läſst es zu, daſs der Tisch F und somit auch die Fräse
A gemäſs der Neigung der Zähne schief gestellt
werden kann.
Als Auflage dient dem Sägeblatt die in einem Schlitze verstellbare
Platte N; die Feder O hält
das Blatt aufrecht. Bei einer Umdrehung des Schwungrades hat die Fräse einen Zahn
geschärft. Der Apparat hat dabei nun noch die Aufgabe, das Sägeblatt um einen Zahn
weiter zu rücken; es geschieht dies dadurch, daſs der am Schwungrad P befestigte Bogen Q beim
Drehen gegen eine Knagge R des Stückes S drückt, Letzteres ist auf einer durch zwei Ansätze
des Bügels C gehenden Achse befestigt und trägt auf der
der Knagge entgegengesetzten Seite einen Arm mit der in einer Hülse befindlichen
Klinke T. Wenn daher der Bogen Q auf die Knagge R wirkt, bringt derselbe
eine Bewegung der Klinke T in horizontaler Richtung
hervor und hierdurch den Vorschub des Sägeblattes um einen Zahn; dabei wird die
Klinke T durch die Schraube U fest gehalten und durch die Feder V
beständig auf den Zahngrund gedrückt. Die Gröſse des Vorschubes richtet sich nach
der Zahntheilung und wird durch Einstellung der Schraube W am Stücke S bewirkt, indem diese auf den
Bügel C früher oder später aufstöſst. Die Rückbewegung
der Klinke nebst Vorschubhebel geschieht durch eine passend eingelegte Feder.
Damit sich jedoch die Fräse während der Dauer des Vorschubes nicht
dreht, hat man an beiden Kegelrädern, welche die Drehbewegung vom Schwungrad P auf die Spindel B
übertragen, eine Anzahl Zähne ausgelassen. Diese Räder sind also auf die Dauer des
Verschiebens des Blattes auſser Thätigkeit gesetzt, indem das eine an dem anderen
vorbeigleitet. Damit ein Verschieben des Blattes überhaupt möglich ist, hat die
Fräse A an einer Stelle des Umfanges eine Nuth, durch
welche das Sägeblatt während des Stillstandes der Fräse gleitet.
Wie aus den Textfiguren 7 und 8 (in Ansicht und Grundriſs, mit
Weglassung der Führungsrollen links und rechts) ersichtlich ist, liefert die
genannte Fabrik diesen selbstthätigen Schärfapparat auch combinirt mit ihrem
Schränkapparat (vgl. 1877 224 551) und ist hierdurch ein vollkommenes Werkzeug zum
Schärfen und Schränken von Bandsägeblättern geboten.
In Fig. 7 bis
15 Taf. 34 ist ein zweckmäſsig construirter selbstthätiger Schränkapparat für Kreissägeblätter dargestellt, für
welchen die Chemnitzer Werkzeugmaschinen-Fabrik
gleichfalls ein deutsches Patent nachgesucht hat und der sich, nach vorgenommener
Umstellung, auch als selbstthätiger Schränkapparat für Bandsägeblätter verwenden
läſst.
Im Gestell A ist eine Welle B gelagert, auf welche ein Excenter C aufgekeilt ist, das an seinen beiden Enden je eine
Schraubenfläche besitzt. Beim Drehen des Handrades ertheilen die Endflächen des
Excenters den beiden Schränkhebeln D eine schwingende
Bewegung, so daſs sich dieselben mit ihren oberen Enden gegen einander bewegen; die
Rückbewegung erfolgt durch eine Feder E und wird
begrenzt durch ein Paar Gummieinsätze F, welche in den
Schränkhebeln selbst befestigt sind.
Fig. 7., Bd. 235, S. 342
Fig. 8., Bd. 235, S. 342
In jedem der letzteren befindet sich ein Schränkbacken G, welcher durch die Schrauben H und J, sowie durch je ein Untertheil c und je einen Keil a so
eingestellt und gehalten wird, als nothwendig ist, damit die eigentliche
Schränkfläche o von jedem der beiden Backen G je eine Zahnspitze des auf dem Bolzen W drehbaren Sägeblattes drückt und dabei schränkt. Wie
viel die eine Zahnspitze rechts und die andere gleich viel links geschränkt wird,
hängt ebenfalls von obiger Einstellung ab.
Um die nächstfolgenden zwei Zähne schränken zu können, muſs das
Sägeblatt entsprechend gedreht werden. Dies geschieht selbstthätig, indem beim
Weiterdrehen des Handrades das Excenter C den Stift O nach auswärts, mithin das obere Hebelende P nach einwärts derart verschiebt, daſs die in das
Sägeblatt eingreifende Klinke Q das Blatt um 2 Zähne
weiter dreht. Die Kraft hierzu ist gering und kann durch Nachziehen der Klemmbacken
auf dem Bolzen W geregelt werden. Das Zurückgehen des
Stiftes O sowie des Hebels P nebst Klinke Q geschieht durch eine Feder
R; die Gröſse dieses Rückganges, mithin auch die
Gröſse des damit zusammenhängenden Vorschubes vom Sägeblatt, richtet sich nach der
doppelten Zahntheilung des Blattes, nach welcher die Stellschraube S einzustellen ist.
Wie dieser Apparat zum selbstthätigen Schränken von
Bandsägeblättern umgeändert wird, kann aus Fig. 14 und
15 Taf. 34 ersehen werden. Man setzt ein Paar andere Schränkbacken ein, ebenso eine
anders geformte Sperrklinke V, nachdem die Sperrklinke
Q nebst Feder entfernt worden ist; der letztere ist
für diesen Zweck überflüssig, da die Klinke hierbei durch ihr eigenes Gewicht in den
Spielraum zwischen je 2 Zähne fällt. Damit die Zahnspitzen in die richtige Höhenlage
zu den Schränkflächen o gebracht und erhalten werden
können – was bei der Verwendung für Kreissägeblätter durch verticales Verstellen des
Bolzens W erfolgt – wird hierfür eine senkrecht
verstellbare Unterlage T verwendet, welche an ihren
beiden Enden durch die verstellbaren Hebel U gehalten
wird, deren Köpfe die seitliche Führung für das Blatt abgeben.
Hierzu sei noch erwähnt, daſs dieser Apparat in zwei verschiedenen
Gröſsen gebaut wird und zwar AAV für Kreissägeblätter bis 350mm Durchmesser bei 1¼mm Blattdicke und AAW für solche bis 600mm Durchmesser bei 2¼mm Blattdicke.
Eine für den Wagenbau äuſsert zweckmäſsige Maschine, für welche
die Chemnitzer Werkzeugmaschinen-Fabrik allein das
Recht der Ausführung und des Vertriebes erworben hat, ist die in Fig. 16 bis
19 Taf. 34 dargestellte Radnaben-Bohrmaschine, Patent K. L. Lasch (*
D. R. P. Nr. 7475 vom 16. April 1879).
Das allgemein gebräuchliche Verfahren, Radbüchsen durch Aufbohren
mit conischen Löffelbohrern in die Wagenräder einzulassen, hat den Nachtheil, daſs
das gebohrte Loch fast nie centrisch zum Rad ist und in den meisten Fällen nicht
genau dem Conus der Büchse entspricht. Es macht sich daher ein Eintreiben schwacher
Holzkeile zwischen Nabenwandung und Radbüchse nothwendig.
Abgesehen davon, daſs das erforderliche Abrichten der Räder eine
zeitraubende Arbeit ist und sehr geübte Leute dazu nöthig sind, wird eine derartig
einseitig durch Keile gehaltene Radbüchse bei Belastung des Wagens nie so fest
sitzen, als wenn das Loch der Radnabe genau centrisch gebohrt ist und sich dem Conus
der Radbüchse anschlieſst. Letzteres wird nun durch die vorliegende Maschine
erreicht, und zwar bei etwa viermal gröſserer Leistung als durch Handarbeit, wobei
ein sehr leichter Gang der Maschine dadurch erzielt wird, daſs das Kreuz, auf
welches das Rad aufgespannt ist, auf Rollen läuft. Auch ist dadurch das
Büchsen-Einlassen bei den schwersten Rädern ermöglicht. Die Maschine besteht in
ihren Haupttheilen aus der Grundplatte mit angegossenen Bohrspindellagern, der
Bohrspindel, dem Aufspannkreuz mit Lager und dem Schaltzeug.
An der Grundplatte a sind zwei zur
Aufnahme der stählernen Bohrspindel B bestimmte Lager
angegossen. Am vorderen Theil der Platte ist der seitlich im Kreis verstellbare, mit
segmentartigem Fuſs versehene Ring C angeschraubt,
welcher mittels zweier Laufrollen D und der
bogenförmigen Leiste E zur Lagerung des dreiarmigen
Aufspannkreuzes F dient. Die Achse der einen Laufrolle
ist durch eine mit Kugelgelenk (Fig. 19)
angekuppelte Welle h durch das Getriebe J mit den Rädern des Schaltzeuges verbunden. Die
Schaltung wird hervorgebracht, indem das Rad J in das
auf der Warze des Spindellagers laufende Doppelrad K
greift und dann mittels des Zwischenrades l den inneren
Zahnkranz m bewegt, dessen Warze durch das Lager der
Bohrspindel hindurch reicht und zur Befestigung der Kammmutter n dient, welche sich durch Excenter bequem in das
Gewinde der Bohrspindel ein- und auslegen läſst.
Die Maschine ist eingerichtet, um auf jeder Werkbank aufgeschraubt
werden zu können; es kann dieselbe aber auch durch einen an die Grundplatte
anzugieſsenden Fuſs freistehend eingerichtet werden.
Das Einlassen der Radbüchsen geschieht in folgender Weise: Das bis
auf das Einlassen der Büchsen fertige Wagenrad wird an dem dreiarmigen Kreuz F aufgespannt. Je nach der conischen Beschaffenheit der
Radbüchse wird der das Kreuz tragende Ring in der auf der Platte eingegossenen Nuth
verschoben. Eine auf der Grundplatte angebrachte Scale P erleichtert die Schrägstellung des Rades. Nach Stellung des in die Spindel eingeklemmten
Bohrmessers und Einlegen der Kammmutter n bewegt der
Arbeiter entweder durch Eingreifen in die Radspeichen, oder durch einen in das Kreuz
F eingeschraubten Drehung das aufgespannte Rad. Das
Schaltzeug, welches durch die Laufrolle D in Bewegung
gesetzt wird, schiebt die Bohrspindel durch die zu bohrende Radnabe. Zuletzt wird
die Kammmutter ausgerückt und die Spindel durch Eingreifen in den am Ende derselben
eingeschraubten Ring zurückgezogen. Ein zweimaliges Durchdrehen der Bohrspindel
genügt, um das Loch fertig zu bohren.
Das Einfräsen der Verstärkung der Radbüchse, sowie der
Stoſsscheiben geschieht mit gröſster Leichtigkeit.
J. P.
Tafeln
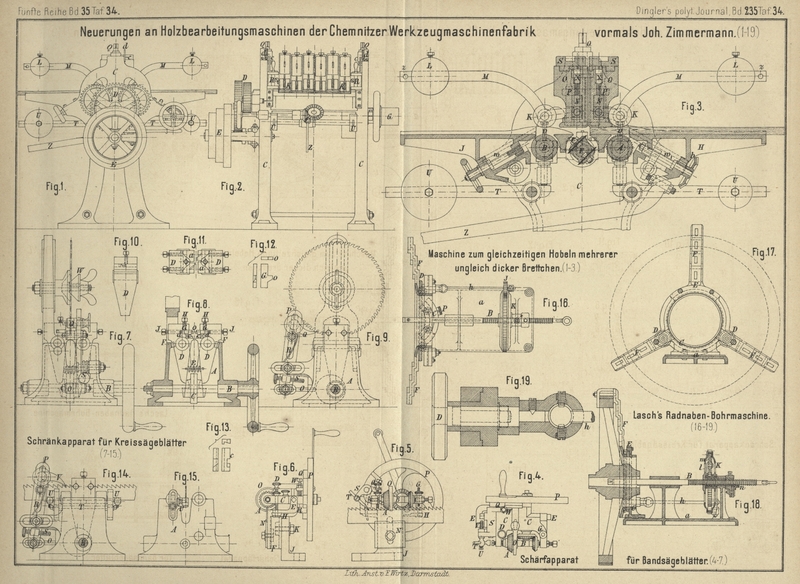