Titel: | Zur chemischen Technologie des Glases. |
Fundstelle: | Band 240, Jahrgang 1881, S. 115 |
Download: | XML |
Zur chemischen Technologie des
Glases.
Mit Abbildungen auf Tafel 11.
(Patentklasse 32. Fortsetzung des Berichtes S. 366
Bd. 239.)
Zur chemischen Technologie des Glases.
Flaschenverschluſs nebst Schere zur Herstellung des
Flaschenmundstückes von H. Hering in Berlin (*
D. R. P. Kl. 64 Nr. 5664 vom 17. März 1878). Das Flaschenmundstück hat, wie aus Fig.
1 Taf. 11 zu entnehmen, an der inneren Seite zwei Vorsprünge oder Ansätze
a, welche entweder, wie hier, direct am oberen
Rande oder ganz im Innern des Flaschenmundstückes angebracht sind. Der Pfropfen
(Fig. 2) besteht aus dem mit zwei seitlichen Nasen b versehenen Bolzen c, an den sich oben der
beliebig geformte, hier sechskantige Kopf d
anschlieſst. Beim Verschlieſsen bringt man den Bolzen c
in die Flaschenöffnung ein, bis die Nasen b beim
Herumdrehen des Kopfes d unter die Ansätze a der Flasche greifen und der Verschluſs durch das
feste Anpressen der Gummischeibe f durch Kopf d an den oberen Flaschenrand bewirkt wird. Beim
Pfropfen Fig. 3 ist
ein Gummiring f in eine entsprechende Nuth einer losen
Unterlegscheibe g gelegt; letztere soll verhindern,
daſs beim Drehen des Kopfes d derselbe auf dem Gummi
gleitet bezieh. reibt,
was eine starke Abnutzung zur Folge hätte, und bewirken, daſs der Kopf d nur auf der losen Scheibe g gleitet und so die Lage der letzteren zur Gummischeibe und Flaschenrand
unverändert bleibt.
Die zur Herstellung dieses Flachenmundstückes erforderliche Schere (Fig. 4 bis
6 Taf. 11) besteht aus dem gabelartig federnden Stück R, an dessen Enden die Rollenträger h angeschraubt sind. Der punktirt gezeichnete Schlitz
b des Querstückes n
gestattet eine Bewegung der Rollenträger h und der mit
ihnen fest verbundenen Gabelenden. Die auf h
befindlichen losen Rollen i, welche bei geschlossener
Schere (Fig. 4) die
äuſsere Form des Flaschenmundstückes umschlieſsen, werden in ihrer Lage festgehalten
einerseits durch den Ansatz k, andererseits durch die
Unterlegscheibe und Mutter l. Die innere Form des
Flaschenmundstückes wird gebildet durch den unbeweglichen conischen Dorn m und durch das auf der Dornachse sitzende, drehbare,
prismatische Stück w, dessen Querschnitt Fig.
6 zeigt.
Ist die Flasche bis auf das Mundstück fertig, so wird sie erwärmt, und, nachdem der
Bund herumgelegt ist, der Dorn der geöffneten Schere in die Flaschenöffnung
geschoben, bis der obere Flaschenrand gegen das Querstück stöſst. Dann dreht man die
geschlossene Schere herum und es werden dabei die Rollen i die äuſsere Form der Flasche bilden, das Querstück n den oberen glatten Rand und der Dorn m die innere Rundung und richtige Weite der Flasche
unterhalb der Ansätze a (Fig. 1). Das
bewegliche prismatische Stück w wird an dieser Drehung
nicht theilnehmen, sondern stehen bleiben und die Lappen bezieh. Ansätze a bilden.
Bei der Flaschenschere von Const. Richter in Hamburg (*
D. R. P. Kl. 64 Nr. 10151 vom 21. October 1879) wird die Flasche zum Rollen auf den
Dorn i (Fig. 7 Taf.
11) gesteckt und durch Zusammenpressen der federnden Arme g ein Hervortreten der Theile j bewirkt,
welche in dem Flaschenhalse entsprechende Eindrücke c
(Fig. 8) hervorbringen, in welche dann der Stopfen eingreift.
Um ein scharfes Ausformen der in Formen
geblasenen Glasgegenstände zu erreichen, verwendet J. Riedel in Maxdorf bei Reichenberg, Böhmen (* D. R. P. Nr. 10873 vom 5.
December 1879) auf 5 bis 6at Ueberdruck gepreſste
Luft an. Zu diesem Zweck wird der mittels des Schlauches B (Fig. 9 Taf.
11) mit dem Vorrathsbehälter für gepreſste Luft verbundene Ventilkasten A an einem Gestelle etwa 0m,6 über der zu benutzenden Metallform frei aufgehängt, damit der
Glasbläser, nachdem er die Glasmasse in gewöhnlicher Weise in die Metallform
geblasen hat, den Ansatz a schnell auf die Kegelspitze
der Pfeife setzen kann. Der Arbeiter drückt dann auf den Knopf h und entfernt so den die Oeffnung c verschlieſsenden Schieber. Die nun eintretende
gepreſste Luft treibt das Glas bis in die zartesten Theile der Hohlform.
Formtretwerk mit Vorrichtung zum Verstellen und mit
Preſsboden für Glasbläserei von M. Mäsch in
Steele a. d. Ruhr (* D. R. P. Nr. 6316 vom 5. December 1878). Auf den vier Stempeln
des Untersgestelles ruht der guſseiserne Rahmen g (Fig.
10 und 11 Taf.
11), in dessen schwalbenschwanzförmiger Führung die jeweilig erforderliche Form mit
an dieselbe befestigtem Schlitten s eingeschoben wird.
Um den Führungsarm zwischen Hebel und Form für alle aufzusetzenden Formen verwendbar
zu machen, ist derselbe in zwei Theile zerlegt, welche durch den Regulirmuff p mit rechts und links eingeschnittenem Gewinde
verbunden sind, wodurch die Längenunterschiede zwischen Arm und der betreffenden
Form nach Erforderniſs ausgeglichen werden können. Der während des Gebrauches durch
die Erhitzung verursachten Ausdehnung der Form wird dadurch Rechnung getragen, daſs
der Drehbolzen b nach unten zu conisch geformt ist und
auf der Stellschraube c ruht. Damit kann man den Bolzen
b heben oder senken und hierdurch den Gang des
Apparates von den Temperaturunterschieden unabhängig machen. Der Apparat hat den
Vorzug, daſs zu den Formen für Medicingläser von 5 bis 500cc Inhalt nur ein Gestell erforderlich ist.
Skelettformen für geblasene, sogen, gedrehte Gläser hat
M. Herrmann in Dresden (* D. R. P. Kl. 32 Nr. 8096
vom 11. Juni 1879) angegeben. Da sich die bisher angewendeten Metallformen bei
raschem Arbeiten zu sehr erhitzen, dadurch sich rasch abnutzen und die angewendete
Einlage oder Schmiere verkohlen, so daſs durch die kohligen Ansätze Streifen in das
Glas kommen, so empfiehlt Herrmann die Anwendung
durchbrochener oder entsprechend zusammengesetzter Formen für solche Gläser, welche
während des Einblasens in die Form gedreht werden. Fig. 12 bis
15 Taf. 11 zeigen z.B. eine derartige Skelettform für eine
Bordeauxflasche. Hierfür empfiehlt sich eine Theilung der Form in der Weise, daſs
sich der gröſste Theil des Cylinders der Flasche in dem mittels Flanschen f befestigten Formtheil d
befindet, der aus einem Stück besteht, in welches der Einstich e eingesetzt ist. Der kleinere Theil des Cylinders der
Flasche, Hals und Brust, befinden sich in den beiden beweglichen Form theilen g. Der geschlossene Cylinder d enthält Einschnitte c, welche der Luft
ungehinderten Eintritt zum Forminnnern verschaffen, gleichviel ob die Form offen
oder geschlossen ist. Diese Durchbrechungen c sind
gegen die Drehungsachse der Form geneigt, um als Abstreifer bei dem Drehen der
Flasche zu wirken. In ähnlicher Weise ist der Einstich e durchbrochen, während die beweglichen Theile g nur je 3 Einschnitte i haben. Durch diese
Vorrichtung soll die Form besser gekühlt, organische Substanz aber völlig verbrannt
werden, ohne Kohle abzusetzen.
H. Feurhake und W. Peck in
Pittsburg, Pensylvanien (* D. R. P. Nr. 9639 vom 21. September 1879) wollen die
Oberfläche der Preſsformen mittels des Sandgebläses oder durch Aetzen körnen, damit
die Gläser ebenfalls
eine entsprechend gekörnte Oberfläche erhalten. Um etwaige Figuren in die Formen
einzuätzen, wird die Zeichnung zunächst mit einer Farbe aus 1 Rindstalg, 1 Wachs, 2
Colophonium, 1 Asphalt, ½ Lampenrufs auf trockenes Abziehpapier gedruckt, welches
erhalten wird, indem man 500g Stärke und 6 bis
7g Glycerin in Wasser kocht und mit der Lösung
Flieſspapier tränkt. Das bedruckte Papier wird mit der Druckseite auf die zu ätzende
Fläche gelegt, an dieselbe gedrückt, leicht befeuchtet und abgezogen. Die Zeichnung
auf der Form wird dann mit einem Pulver aus 1 Th. Asphalt und 1 Th. Colophonium
bestäubt und das Pulver vorsichtig mittels des Fingers mit der Farbe verrieben. Die
Form wird dann leicht erwärmt, so daſs das Pulver gerade festschmilzt, ohne zu
verlaufen. Darauf wird die Zeichnung wieder bestäubt und wie vorhin behandelt.
Dieser Proceſs wird so lange fortgesetzt, bis ein hinreichender Körper für die
Zeichnung erzielt ist. Für grobe Körnungen wird ein Säuregemisch empfohlen von 5 Th.
Holzessigsäure, 1 Th. Alkohol und 1 Th. Salpetersäure, für feinere Körnungen eine
Mischung von Salpetersäure und Fluſssäure.
Um bei der Herstellung doppelwandiger
Glaskuppeln in dem äuſseren Mantel genügenden Raum für das Stück b (Fig. 16
Taf. 11) des von unten mittels Gegenform einzudrückenden inneren Mantels zu
schaffen, wird von O. Schumann in Hamburg (* D. R. P.
Nr. 9667 vom 24. August 1879) der äuſsere Mantel der Kuppel in der entsprechenden
Form mit Hinzufügung eines besonderen Arbeitstückes a
geblasen, welches nach vollzogenem Durchdruck des inneren Mantels an geeigneter
Stelle bei c abgeschnitten wird. Nachdem dann die
inneren Flächen versilbert sind, wird die Oeffnung bei c durch einen Blechring geschlossen.
Um geblasene, noch warme Glaswalzen
an ihrem vorderen Ende durch Einschlagen eines Stiftes zu
lochen, haben W. Westmeyer, D. Schweppe und
R Schlicker in Witten a. d. Ruhr (* D. R. P. Nr.
11503 vom 18. März 1880) die in Fig. 17
Taf. 11 abgebildete Vorrichtung angegeben. An dem Ofen ist eine beiderseits durch
Deckel geschlossene Hülse a befestigt, welche den
Bolzen e umschlieſst; dieser trägt die durch die
Hülsendeckel tretenden Stifte b und c. Ueber den ersteren ist eine Spiralfeder geschoben,
welche sich gegen den hinteren Hülsendeckel und gegen den Bolzen e stützt; der letztere bildet den Schlagstift. Ein auf
der Hülse aufgesteckter Trichter g dient der Walze als
Stütze und Mittelführung, wenn sie vor den Schlagstift gebracht wird. Das
Einschlagen dieses Stiftes in die Walze wird dann durch Niedertreten des Trittes h bewirkt; hierbei wird durch Vermittelung des
Zwischenhebels i und zweier Verbindungsstangen der
Hebel k gegen die im geschlitzten Bolzen e drehbare und nur im Rücken anliegende Nase o gedrückt, die Bolzenfeder also gespannt, bis endlich
der Hebel k von der Nase o
abschnappt. Die Feder treibt dann den Bolzen nach vorn und der Schlagstift dringt in die Walze ein.
Nach dem Loslassen des Trittes bringt das Gewicht l die
ganze Hebelvorrichtung in die ursprüngliche Lage zurück. Der Hebel k kann hierbei die Klinke o mit Rücksicht auf ihre Beweglichkeit nach vorn ungehindert passiren.
Zur Verfertigung von Broschen, Knöpfen u.
dgl. aus Glasmosaik stellt man nach J. Wagner
in Görlitz (* D. R. P. Nr. 9125 vom 1. August 1879) zunächst die Hauptkörper a (Fig. 18 und
19 Taf. 11) aus Preſsglas her. Man belegt dann die Vertiefung e mit gemusterten Glasplättchen, welche wie der sogen,
venetianische Kuchengrund durch Ausziehen eines Bündels farbiger Glasstäbe,
Zerschneiden des Stabes in heiſsem Zustande mit der Schere und Abschleifen der
einzelnen Stücke erhalten und noch naſs, mit dem als Schleifmittel verwendeten
weiſsen Compositionsschlamm behaftet, in die Form eingesetzt werden. Nach dem
Austrocknen werden die so vorbereiteten Gegenstände auf eine mit gebranntem Gyps
überstreute, ganz ebene Thonplatte gelegt und darauf in einer Muffel die Plättchen
an der Form festgeschmolzen. Nachdem die Gegenstände langsam ausgekühlt sind, werden
die Lücken zwischen den Plättchen mit in Wasser fein geriebener weiſser oder
farbiger Mischung ausgefüllt und das Glühen bezieh. Schmelzen bis zum gleichen
Hitzegrad in der Muffel nochmals vorgenommen. Sollte, nachdem das Ganze langsam
abgekühlt ist, die Mischung die Lücken nicht in ganzer Höhe ausfüllen, so muſs das
Stück nochmals damit überstrichen und aufs neue dem Schmelzproceſs unterworfen
werden. Die so vorbereiteten Stücke werden oben abgeschliffen, wodurch die
Masaikmuster hervortreten. Die betreffende krystallweiſse Mischung besteht aus:
10k
Mennige
10k
gereinigtem weiſsem Kiessand,
0k,5
Borax und
10g
blauem Kobaltoxyd.
Dieses Gemenge wird gut unter einander
gerührt und in einem Tiegel bis zur Dünnflüssigkeit geschmolzen, dann
pulverisirt.
Um in Bündeln oder Büscheln zusammengelegte Glasfäden zu
Flechten, Borden u. dgl. verarbeiten zu können, soll man sie nach Friese und Fayenz in
Hamburg (D. R. P. Nr. 11298 vom 18. Februar 1880) mit feinem versilbertem oder
vergoldetem Kupferdraht umspinnen.
F. Siemens in Dresden (D. R. P. Nr. 11055 vom 6.
December 1879) bespricht eingehend ein Verfahren, um gröſsere unregelmäſsig geformte
Glaskörper namentlich Eisenbahnschwellen, Mühlsteine u.
dgl. möglichst haltbar herzustellen und zu kühlen. Die
betreffenden Gegenstände werden in Metall- oder Sandformen gegossen, dann in Sand
gebettet, wieder gewärmt und nun mit dem Sande zusammen derart gekühlt, daſs die
Glasstücke möglichst nur von den parallelen Flächen aus und zwar thunlichst
gleichmäſsig gekühlt werden. Nach einem Berichte von
Wood im Engineering, 1879
Bd. 28 S. 271 zeichnen sich derartig hergestellte Eisenbahnschwellen durch groſse
Festigkeit aus.
F. O. Hirsch und E. Hirche
in Radeberg, Sachsen (* D. R. P. Nr. 9703 vom 22. Juli 1879) empfehlen einen
drehbaren Glaskühlofen, welcher in 4 Abtheilungen A bis D (Fig. 20
Taf. 11) je drei Blechkästen enthält, die von der stehenden guſseisernen Welle a unten durch Speichen und oben durch Halter getragen
werden. Die Glasmacher stellen die geblasene Waare sofort in die Kühlgefäſse der
ersten Abtheilung A, welche sich in dem oben bedeckten
und mit einer entsprechenden Gasheizung versehenen Räume r befindet. Sind die 3 Kästen gefüllt, so dreht man die Vorrichtung um
90°, so daſs nun die Kästen der Abtheilung D besetzt
werden, während die der ersten Abtheilung langsam in den Raum n, dann bei weiterer Drehung an freier Luft kühlen und
schlieſslich entleert werden.
F. B. A. Royer de la Bastie in Richemont (* D. R. P.
Zusatz Nr. 5410 vom 27. Februar 1878) macht weitere Mittheilungen über sein Härteverfahren (1879 233 *
314). Der in Fig. 21 bis
23 Taf. 11 dargestellte Muffelofen dient namentlich zum Härten kleiner
Gegenstände. Die Muffel A aus feuerfestem Stein ruht
auf Backsteinen e und steht mit dem Kessel durch eine
Oeffnung c in Verbindung. Die Flamme geht vom Herd m aus unter der Muffel her, dann in der Richtung der
Pfeile in den Schornstein s. In dem durch eine
seitliche Feuerung geheizten Kessel B, welcher die
Kühlflüssigkeit enthält, befindet sich eine doppelte Kette, die über vierkantigen
Kettenhaspel mittels einer Kurbel h bewegt wird und
kleine Becher w trägt, welche zur Aufnahme der zu
härtenden Gegenstände dienen. Sobald das Thermometer t
den richtigen Hitzegrad zeigt, bringt der Arbeiter die zu härtenden Gegenstände
durch die Oeffnungen x ein, stöſst sie in die Muffel
A und dann durch das Loch c in die Becher w. Jeder Becher kann ein oder
mehrere Stücke aufnehmen; zur Entleerung derselben öffnet man den Deckel n.
Zum Härten flacher Gegenstände dient der Ofen Fig. 24 und
25 Taf. 11. Die Flamme des Herdes h heizt
den Ofen A direct, dann den Vorwärmer B und geht in den Schornstein s. Der Boden a des Ofens aus feuerfestem
geschliffenem Stein ist mit einem guſseisernen Mechanismus n verbunden, der auf Schneiden o durch eine
Trittvorrichtung t bewegt wird. Die Glastafel wird in
den Vorwärmer B gebracht, erhitzt sich nach und nach
und wird dann in den Arbeitsofen A auf die Wage a geschoben. Sobald das Glas genügend erhitzt ist, wird
diese gedreht und die Glastafel gleitet in ein Bad oder in den Kessel auf dem Wagen
C mit verschiedenen Abtheilungen für die einzelnen
Platten. Sobald eine Abtheilung gefüllt ist, zieht man den Wagen zurück und füllt
die zweite und darauf die anderen; sind alle Abtheilungen voll, so wird der ganze
Apparat durch einen frischen ersetzt.
J. M. A. Deherrypon in Paris (* D. R. P. Nr. 9930 vom
23. September und Zusatz Nr. 10514 vom 31. October 1879) will Glas enthärten oder auch härten durch entsprechende
Behandlung mit gepreſster erwärmter Luft. Als neu wird
die Anwendung von mit Steinen ausgesetzten Kammern zwischen Feuerung und Wärmeofen,
sogen. Wärmeaccumulatoren, bezeichnet.
Die Theorie der Glashärtung (vgl.
1875 216 * 75. 288. 1879 233 314) bespricht eingehend O.
Schott in den Verhandlungen des Vereines zur
Beförderung des Gewerbfleiſses, 1879 S. 273.
Der Glasschmelzofen von H. Krigar in Hannover (* D. R. P. Nr. 11728 vom 11.
December 1879) besteht aus einem Schacht a (Fig.
26 Taf. 11), in welchen von der Gicht b aus
der zu schmelzende Glassatz mit den Brennstoffen eingefüllt wird. Die erforderliche
atmosphärische Luft wird durch das mit Drosselklappe versehene Windrohr e, den Windkasten c und
die Düse f eingeblasen. Das geschmolzene Glas sammelt
sich im Schmelzherd g, flieſst in den Hauptkanal h und zwei seitlich von letzterem gelegene Nebenkanäle,
denen es durch entsprechende Arbeitsöffnungen entnommen wird. Um das Glas flüssig zu
erhalten, ist eine Nebenfeuerung l angebracht, deren
Gase gleichmäſsig über das in den drei Kanälen befindliche Glas hinwegstreichen und
in dem gemeinsamen Schornstein m zugleich mit den Gasen
des Schachtofes abziehen.
P. Richarme in Rive de Gire, Loire (* D. R. P. Nr. 8100
vom 26. November 1878) legt durch den ganzen Kühlofen eine endlose Fahrbahn. Auf
diese werden die fertigen Gegenstände gestellt und am entgegengesetzten Ofenende
nach beendeter Kühlung von derselben wieder abgenommen. (Eine ganz ähnliche
Vorrichtung hat Referent übrigens schon früher in der Stolberger Glashütte
gesehen.)
Der Glaskühlofen von M. Epstein in Sosnowice, R.-Polen (* D. R. P. Nr. 11785
vom 4. März 1880) besteht aus drei mittels eiserner Schützen getrennten Räumen,
durch welche eine Schienenbahn führt, die sich um den Ofen herumzieht. Der mittlere
Raum des Ofens f (Fig. 27 bis
29 Taf. 11) wird durch Gas, Kohle oder Holz geheizt. Der bei e vorgewärmte Kühlwagen wird in den Raum f gestoſsen, dort durch die Oeffnung h mit dem abzukühlenden Glase gefüllt, der Deckel
zugemacht und durch zwei Haken, die sich auf die am unteren Theile des Deckels
befindlichen seitlichen Vorsprünge legen, geschlossen. Mittels einer eisernen
Hakenstange wird dann der Wagen aus dem Raum f nach g auf die Drehscheibe b
gezogen. Während des Einlegens in den ersten Wagen wird ein zweiter Wagen in den
Raum e geschoben, welcher, wenn der erste gefüllt,
bereits so weit vorgewärmt ist, daſs er sofort nach f
gestoſsen und gefüllt werden kann. Nachdem der erste Wagen etwa 10 Minuten in der
bei der unmittelbaren Nähe des heiſsen Raumes etwas erwärmten Kammer g
zugebracht hat, wird er über die Drehscheibe b auf das
andere Geleis gebracht und hier um etwa eine Wagenlänge vorgerückt. Der Wagen
gelangt so allmählich über die Drehscheiben c und d in die Sortirstube, wird hier entleert und, ohne daſs
er das Geleis verläſst, durch die Drehscheiben d und
a wieder in den Vorwärmraum e zurückgeführt. (Vgl. Hirsch 1879 233 * 219.)
Tafeln
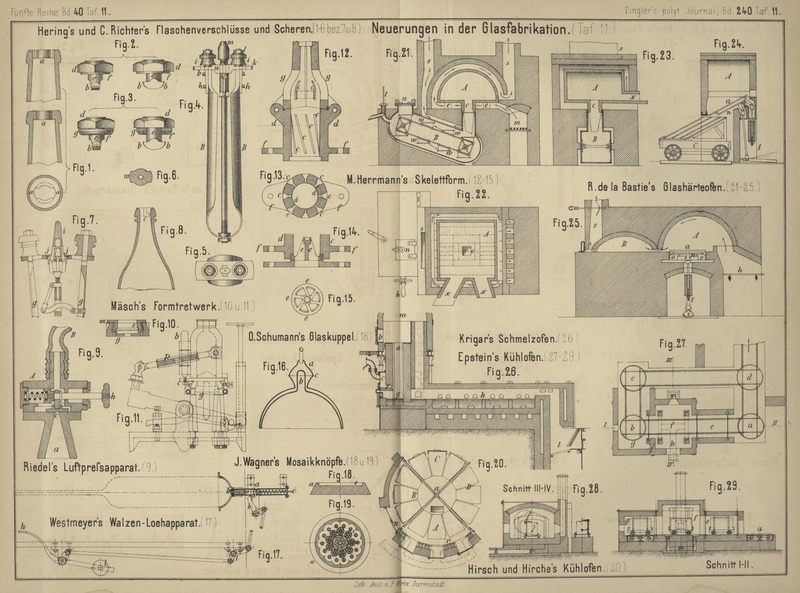