Titel: | Ueber die Herstellung und Verwendung von Leuchtgas. |
Fundstelle: | Band 240, Jahrgang 1881, S. 293 |
Download: | XML |
Ueber die Herstellung und Verwendung von
Leuchtgas.
Mit Abbildungen auf Tafel 25.
(Patentklasse 26. Fortsetzung des Berichtes von S.
324 Bd. 238).
Zur Herstellung und Verwendung von Leuchtgas.
Die Generatoröfen der Münchener
Gasanstalt (vgl. 1880 235 * 209) sind nach N. H.
Schilling (Journal für Gasbeleuchtung, 1880 S.
180) jetzt dahin geändert, daſs statt der Zickzackförmigen Führung der Gase die
geradlinige bei einer doppelt so groſsen Anzahl von Kanälen zur Anwendung kommt und
die Kanäle in senkrechter Richtung abwechseln. In Fig. 1 bis
3 Taf. 25 bezeichnen 1 bis 6 die jetzigen Luftkanäle, n bis t die Rauchgaskanäle. Die kalte Luft
tritt bei L in den Kanal 1
an der Vorderwand unmittelbar über der Sohle des unteren Raumes n ein, geht nach rückwärts, tritt in den Kanal 2 über, kommt in diesem wieder nach vorn, geht durch
3 zum zweiten Male nach rückwärts, tritt nach 4 über und seht wieder nach vorwärts, hierauf senkrecht aufwärts in
den Ofen nach 5, hier rückwärts und tritt dann über
nach 6, wo sie die Schlitze findet, welche sie mit den
Generatorgasen zusammenführt. Die Rauchgase dagegen, welche unter der tiefsten
Flügelretorte nach rückwärts ziehen, gelangen bei n
abwärts nach o, ziehen hier der Luft entgegen nach
vorn, in p nach hinten, in q nach vorwärts, nehmen von hier aus einen Umweg durch die Kanäle t und r, welche unter dem
Dampferzeuger v liegen, und gehen in s nach rückwärts zum Rauchkanal hinaus. Der früher
zwischen dem Ofen und der Regeneration befindliche Rauchgasschieber ist jetzt
hinunter verlegt, so daſs er auch den Zug in der Regeneration mit regelt.
Um den früher durch das Rohr e zugeführten Dampf
kostenfrei zu erzeugen, wurde in dem unteren Theil des Generators ein Wasserkasten
v mit Zufluſsrohr w
eingesetzt und gehen die Rauchgase aus der Regeneration, bevor diese in den letzten
Kanal eintreten, wie erwähnt, unter den Kasten vor und zurück. Bei der
ursprünglichen Anlage gingen die Rauchgase, deren Volumen durch die eingesaugte Luft
etwa wie 100 : 170 vergröſsert war, noch mit 800° aus der Regeneration ab; nach der
beschriebenen Abänderung hörte dieser Volumenzuwachs auf und die Temperatur der
abziehenden Rauchgase erreichte nicht mehr die früheren 800°. So lange böhmische
Kohlen in 3stündiger Beschickung verwendet wurden, genügte zur Erzeugung von 570k Wasserdampf in 24 Stunden (1k Wasser für 2k
Kohlenstoff) der anfängliche Kasten von 1qm,46
Heizfläche; als aber Saarbrücker Kohlen in 4stündiger Beschickung zur Verwendung
gelangten, der Wasserdampfbedarf sich daher auf 0k,7 für 1k Kohlenstoff steigerte, stellte es
sich als nothwendig heraus, die Heizfläche des Wasserkastens zu vergröſsern, und es
wurde in Folge dessen nicht nur der Wasserkasten selbst nach rückwärts verlängert,
sondern auch noch ein Rohr B zum Durchzug für die
Rauchgase in demselben angebracht, so daſs die gesammte Heizfläche jetzt 2qm,8 beträgt. Um die Luft möglichst in der Mitte
des Generators und nicht an den Wänden desselben eintreten zu lassen, wurde über dem
Wasserkasten ein Blech eingeschoben, das an den Auflageschienen des Mundstückes
abschlieſst und die Luft zwingt, über der Wasserfläche hinweg nach dem Rostraume zu
ziehen. Eine Regulirung des Luftzutrittes wird ferner dadurch erreicht, daſs man vor
das schräge Blech noch ein zweites vorlegt, in welchem sich ein Schieber von etwa
12cm Breite befindet, der auf ein bestimmtes
Maſs, in der Regel zwischen 2 und 3cm eingestellt
wird, so daſs also die Luft durch eine Oeffnung von 12cm Länge und 2,5 bis 3cm Breite in den
Rostraum zieht.
Die Oefen sind 21 Monate im Betrieb und seit 1 Jahr fast ausschlieſslich mit
Saarbrücker Kohlen (mit einem Zusatz bis zu 10 Proc. böhmischer Plattenkohlen)
beschickt worden. Im Spätsommer 1879 ergab sich der Anstand, daſs sich nicht nur die
Aufsteigröhren in lästiger Weise verstopften, sondern daſs auch die Theerverdickung
in der Vorlage und im Ableitungsrohre zur Condensation in bedenklicher Weise zunahm.
Wenn der gewonnene Theer kalt geworden war, so bildete er eine so zähe Masse, daſs
er nicht mehr auslief, und die Verwerthung desselben stieſs auf ernstliche
Schwierigkeiten. Zugleich zeigte sich eine starke Bildung von Naphtalin, welche
allerdings auf der Fabrik nur zum geringsten Theile zum Vorschein kam, aber bald in
den Röhrenleitungen der Stadt, und zwar zum Theil an ziemlich entfernten Punkten und
in gröſseren Röhren gefunden wurde. Die Temperatur der Oefen war zu jener Zeit eine
sehr hohe und es wurden bei 3stündiger Beschickung von jeder Retorte in 24 Stunden
gegen 300cbm Gas gemacht. Nachdem die Temperatur
in den Oefen daraufhin ermäſsigt worden, zeigten sich die Uebelstände sofort wieder
beseitigt und es wurde nun der Betrieb dahin geändert, daſs die Gasausbeute für die
Retorte in 24 Stunden auf 250 bis 260cbm
festgestellt und die Temperatur so gehalten wurde, daſs die Kohlen gerade noch
vollständig ausgasten. Dabei stellte es sich heraus, daſs es ökonomisch vortheilhaft
war, von der 3stündigen Beschickung wieder auf eine 4stündige überzugehen, und in
dieser Weise ist nun der Betrieb den ganzen Winter hindurch ohne den geringsten
Anstand fortgeführt worden.
Folgende Zahlen sind die Mittelwerthe, die sich aus den vom 7. bis
18. Januar 1880 fortgesetzten Erhebungen ergeben haben bei ausschlieſslicher
Verwendung von Saarbrücker (Heinitz-Dechen-) Kohlen ohne Zusatz von Plattenkohlen.
Es betrug:
Gasausbeute für die Retorte in 24
Stunden
258cbm
Gasausbeute für den Ofen in 24
Stunden
2066cbm
Gewicht der vergasten Kohlen für 1 Retorte
in 24 Stunden
861k
Dasselbe für jeden Ofen in 24
Stunden
6887k
Gasausbeute für 100k Kohlen
30cbm
Heizmaterialverbrauch an Kokes für den
Ofen in 24 Stunden
953k
Dasselbe für 100k vergaster Kohle
14k
In den Tagen vom 20. bis 27. Februar brauchte ein Ofen
im Durchschnitt für 24 Stunden 939k Kokes, in den
Tagen vom 29. Februar bis 5. März 909k Kokes bei
einer gleichzeitigen Wasserzufuhr von im Mittel 73 Procent der verheizten Kokes.
Vergleicht man diese Betriebsresultate mit den früheren, so ist die im Ofen gewonnene
Gasmenge beim jetzigen Betriebe um etwa 5 Proc. geringer als früher; dabei ist aber
der Verbrauch an Heizmaterial jetzt um 20 bis 26 Proc. geringer als früher. Der
erste Umstand ist zur Vermeidung von Betriebsstörungen durch Herabminderung der
Ofentemperatur absichtlich herbeigeführt, den zweiten verdankt man der verbesserten
Vorwärmung der Luft. Die Untersuchungen der Anlage ergaben:
Mittlere Zusammensetzung der Heizgase im
Gas- kanal unmittelbar neben dem Generator
CO2COHN
9,1 Proc.19,8 „13,9 „57,2 „
Zugeführtes Wasser für 1k Kohlenstoff
0,72k
Mittlere Temperatur der Heizgase im Gaskanal
unmittelbar neben dem Generator
1100°
Mittlere Temperatur der vorgewärmten Luft beim
Eintritt vom Kanal 5 in Kanal 6
1090°
Mittlere Temperatur in den Kanälen 4
620°
„ „ „
„ „ 3
500°
„ „ „
„ „ 2
370°
„ „ „
„ „ 1
Nicht zugängl.
„ „ beim Eintritt hinter
dem Luftschieber im Kanal 1
35°
„ „ der Rauchgase beim
Austritt aus dem Ofen bei n
1250°
Mittlere Temp. in den Kanälen o
Nicht zugängl.
„ „ „ „ „ p
1100°
„ „ „ „ „ q
Nicht zugängl.
„ „ „ „ „ t unter dem Wassergefäſs
600°
„ „ „ „ „ r desgleichen
520°
„ „ „ „ „ s
500°
Zusammensetzung der Verbrennungsgase
beim Austritt aus dem Ofen bei n
CO2COON
18,6 Proc. – „ 1,2 „80,2 „
Zusammensetzung der Verbrennungsgase
beim Austritt aus der Regeneration bei t
CO2COON
17,2 „ – „ 2,8 „80,0 „
Zug
unter dem Generator-Rost
2,5mm
im Heizgaskanal hinter dem Generatorschacht
4,0
im Heizgaskanal am Ende
2,5
im Ofen oberhalb der Schlitze bei a
1,5
im Ofen bei c
2,5
in den Rauchgaskanälen
bei n p q t s
3,5 4,5 7,010,515,0
in den Luftkanälen
bei 1 2 3 4/5 5/6
3,0 1,0 0,75 0,0 2,5
Die Luft, welche früher nur bis auf etwa 600° vorgewärmt wurde, erreicht demnach
jetzt eine Temperatur bis gegen 1100°. Die Verbrennungsgase, welche früher mit 1100°
aus dem Ofen austraten und in der Regeneration bis auf etwa 800° abgekühlt wurden,
treten jetzt mit einer höheren Temperatur von etwa 1250° aus dem Ofen und verlassen
die Regeneration mit etwa 500°. Die Vorwärmung der Luft durch Ausnutzung der mit den
Verbrennungsgasen aus dem Ofen abziehenden Wärme ist somit um ein Wesentliches
erhöht worden. Auch der Arbeitslohn stellt sich jetzt noch bedeutend günstiger als
früher. Beim Betriebe von 7 Generatoröfen beträgt derselbe gegenwärtig M. 82,80 für
24 Stunden, nämlich:
Für 1 Partieführer in 12 Stunden
3,50
M.
„ 2 Zieher zu 3,45
6,90
„ 1 Heizer
3,10
„ 9 Arbeiter (Kohlenführer zu 3,10)
27,90
––––––––––
„ 12 Stunden
41,40
M.
Für 24 Stunden
82,80
M.
Mithin für 1 Ofen in 24 Stunden auf
11,83
M.
Bei einer Produktion von 2066cbm in 24 Stunden
stellt sich somit der Arbeitslohn für 100cbm Gas
auf 57,26 Pf. gegen früher 80,3 Pf.
An den Generatoren sind bis jetzt noch keinerlei Ausbesserungen vorzunehmen gewesen;
das Mauerwerk ist vollständig tadellos und an der Innenseite nirgends abgeschmolzen,
oder ausgefressen. Gegenüber dem Gaskanal ist ein gröſserer feuerfester Schaudübel
eingesetzt worden, um den Gaskanal besehen und nöthigen Falles reinigen zu können.
Auf die Füllöffnungen sind statt der ersten guſseisernen Abschluſsdeckel solche aus
feuerfestem Material aufgesetzt worden, die sich vorzüglich bewähren. Auch am
Mauerwerk der Regeneration ist bis jetzt noch nicht die mindeste Ausbesserung
vorzunehmen gewesen; sämmtliche Kanäle waren staubfrei und die Kanten der Steine
noch vollständig scharf. Bei den von Anfang in Betrieb gewesenen Oefen haben im
vorigen Sommer die Retorten ausgewechselt werden müssen. Dieselben waren einer sehr
hohen Temperatur ausgesetzt gewesen, die Oefen hatten schwächere Vorder- und
Rückwände und die Retorten waren auſser vorn und hinten nur noch 3 mal unterstützt.
Beim Ausbrechen zeigte sich, daſs die Schlitzplatten vollständig gut erhalten, daſs
dagegen die unteren Tragsteine der mittleren Retorten geschmolzen waren und daſs auf
diese Weise der innere Einbau seinen Halt verloren und das Zerreiſsen der Retorten
veranlaſst hatte. Im gegenwärtigen Einbau sind 4 Tragsteine, die Vorderwand hat nach
auſsen 1 Stein Stärke, dann 8cm Isolirschicht und
dahinter wieder ½ Stein Mauerwerk. Die Rückwand ist zwei Stein stark und neuerdings
versuchsweise, wie schon eingangs erwähnt, an einigen Oefen durch eine vorgesetzte ½
Stein starke Mauer mit Isolirschicht verstärkt worden. Bis jetzt kann man weder an
den Retorten, noch sonst im Einbau einen Mangel bemerken, die Vorder- und Rückwände
sind nicht, wie früher, nach auſsen getrieben, sondern in ihrer ersten Lage stehen
geblieben. Der Graphitansatz ist so gering, daſs er alle 2 bis 3 Monate innerhalb 2
Stunden ausgebrannt werden kann. Die Tauchung wird auf 20mm gehalten.
Bei dem in Fig. 4 bis
6 Taf. 25 dargestellten Retortenofen von A. Klönne in Dortmund (* D. R. P. Nr. 10400 vom 16. Mai
1879) liegt der Generator K in der Mitte unter dem
Ofen, ist möglichst weit nach oben in den Retortenofen hineingedrückt und deshalb
mit einem spitzen oder parabelförmigen Gewölbe oder mit Façonsteinen abgeschlossen.
Die unteren Retorten sind deshalb aus einander geschoben und die untersten Füchse
L ganz nach den Auſsenwänden des Ofens hin verlegt.
Auf diese Weise entsteht auſser einem groſsen Verbrennungsraum zwischen den unteren
Retorten so viel Raum, daſs der Scheitel des Generatorgewölbes über der Ofensohle zu liegen kommt
und sich die Füllöffnung M in der Vorderwand des
Generators anbringen läſst. Um das Abschluſsgewölbe der Luftzufuhröffnung vor der
Zerstörung zu schützen, ist an der Innenseite des Gewölbes ein Metallrohr O angebracht, durch welches Wasser oder auch Luft und
Dampf hindurchgeführt wird. Das erzeugte Kohlenoxyd tritt durch die Oeffnungen P in den eigentlichen Retortenofen und trifft dort mit
der durch die Kanäle h zugeführten atmosphärischen Luft
zusammen. Diese strömt von auſsen in die Kanäle a und
d ein, geht auf der einen Seite durch die Kanäle
b und c, auf der
anderen durch die Kanäle f und g, um schlieſslich mittels der erwähnten Zweigkanäle h den einzelnen Verbrennungspunkten des Generatorgases
zugeführt zu werden. Durch die Anordnung, daſs auf der einen Seite des Ofens ein
horizontaler Kanal mehr vorhanden ist als auf der anderen, wird der Vortheil
erzielt, daſs alle Verbrennungspunkte eine möglichst gleich groſse Menge von Luft
erhalten. Die in den Kanälen a, b, c und d, f, g schon vorgewärmte Luft wird in den im Innern
des Verbrennungsraumes angeordneten Zweigkanälen h,
welche aus besonders geformten, dünnen, feuerfesten Ziegeln hergestellt wurden, noch
weiter erhitzt. In Folge der hohen Temperatur, mit welcher die Luft demnach mit dem
Gas zusammentrifft, soll nach Klönne die bei der
Verbrennung entwickelte Hitze eine auſserordentlich hohe sein – eine Annahme, welche
nicht ganz richtig ist, da doch die an die Luft in den Kanälen h abgegebene Wärme der Flamme selbst entnommen
wird.
Die Reinigung der Zugöffnung N des Generators von
Schlacke wird von dem Arbeitsraum R aus vorgenommen,
welcher durch Klappthüren verschlossen werden kann, die mit Gegengewichten versehen
sind, um sie leicht handhaben zu können. Durch diese Einrichtung wird die Anlage
eines besonders überwölbten Kellers unnöthig gemacht und läſst sich die Schlacke
leicht herauswerfen. Auch behält der bedienende Arbeiter den Kopf über der
Arbeitssohle und ist somit vor der Einathmung schädlicher Gase und vor übermäſsiger
Wärme besser geschützt (vgl. F. Fischer 1879 232
528).
In Beziehung auf die äuſsere Form des Ofens soll noch hervorgehoben werden, daſs
dieser unten durch ein umgekehrtes Gewölbe abgeschlossen werden kann, um einem
etwaigen Andränge von Grundwasser zu begegnen. Auch die geringe Tiefenlage des
Generators ist für den Fall eines nassen wie eines felsigen Baugrundes von
wesentlichem Vortheil. Nach oben ist der Ofen durch ein elliptisches Gewölbe
abgeschlossen, welches sich am besten der besonderen Anordnung der Retorten
anschlieſst. Bei 8 und 9 Retorten ist es u.a. zweckmäſsig, zwei Reihen von
Brennöffnungen P anzuwenden, zwischen denen dann noch
Luftzuführungskanäle liegen, bei 12 Retorten drei Reihen, während bei 3 bis 7
Retorten eine Reihe genügt.
Bei den Dresdener Generatoröfen ist nach Hasse (Journal für
Gasbeleuchtung, 1880 S. 411) die Füllöffnung des Generators mit einem
kugelartig gestaltetem Verschluſs versehen (Fig. 7 Taf.
25), welcher eine Ausgleichung mit dem Ofenhausfuſsboden gestattet. Zur
Dampfentwicklung ist unter dem Kanal für das nach dem Schornstein ziehende Feuer im
Ofen ein schmaler und niedriger, 7 bis 14cm hoher
Kanal angebracht, in diesen ein einmal zurück und wieder vorwärts führendes
schmiedeisernes Rohr eingelegt und letzteres in seiner Verlängerung nochmals in
einer neben dem Feuerkanal zwischen diesem und dem Ofenpfeiler belassenen Oeffnung
hinter- und vorgeführt, das eine Ende auf der einen Seite mit einem Wasserbehälter
verbunden und auf der anderen Seite bis unter die Wangensteine z (Fig. 8) des
Generators geführt, wo es mehrere Abgänge e erhält.
Sowohl am Eintritt, als am Austritt vom Ofen besitzt das Rohr einen Regulirungshahn;
die Dampfentwicklung ist eine ununterbrochene. Eine Ersparniſs an Feuerungsmaterial
ist hierbei nicht zu erkennen; dagegen genügt dieser Dampf, um ein Mürbewerden und
eine theilweise Umwandlung der Schlacke in Asche zu bewirken, das Schlacken somit zu
erleichtern, auſserdem aber den Schlackenüberzug an den Wangensteinen zu befördern,
so daſs, im Fall die Wasserzuführung in die schmalen Rinnen w an der Sohle des Generators vernachlässigt werden sollte, dieser Dampf
durch seine Einwirkung auf die Verschlackung immer noch genügt, das Verbrennen der
Wangensteine zu verhindern.
Die Generatoröfen von C. Haupt (vgl. 1880 235 * 208) in der Gasanstalt zu
Brieg haben sich nach L. Link (Journal für Gasbeleuchtung, 1880 S. 250) seit October 1880 gut bewährt.
Wegen geringer Tiefe des Retortenhauses konnten nur sehr kurze Retorten vom
Normalformat I bei 2m,18 lichter Ofentiefe zur
Verwendung kommen. Zur Vergasung kamen Kleinkohle aus Königin-Louise-Grube bei
Zabrze, Oberschlesien, zur Aufbesserung des Gases gemischt mit Stückkohle aus
Orzesche, welche zwar nicht mehr, aber weit besseres Gas gibt als erstere Kohle, die
Kokes sind aber weniger gut als von Zabrze-Kohle allein.
Mit einem Ofen zu 8 Retorten wurden vom 28. November bis 2.
December 1879 in 5 Tagen und 6 Stunden bei 4stündigem Beschicken der Retorten von
35t,6 Kohlen 10002cbm Gas gezogen, also von 100k 28cbm,1 und für die Retorte und Tag 243cbm. An Kokes wurden dazu verfeuert 5030k,5 oder für 100k Kohlen 14k,13 und für 100cbm Gas 50k,3.
In 6 Tagen und 18 Stunden wurden ferner erhalten von 44t Kohlen 12498cbm Gas, also für 100k 28cbm,4 und
für die Retorte und Tag 231cbm. Verfeuert wurden
dazu 6118k Kokes, somit für 100k Kohlen 13k,9
und für 100cbm Gas 48k,95. Dabei waren beide Nachbaröfen kalt. Im Januar 1880 wurden in 3½
Tagen von 21t,6 Kohlen 6413cbm Gas, somit von 100k Kohlen 29cbm,68 und für die Retorte
täglich 229cbm Gas erzeugt. Verfeuert wurden
3123k Kokes oder für 100k Kohlen 14k,46
und für 100cbm Gas 48k,7 Kokes. Die abziehenden Gase waren etwa 400° warm.
Am 31. December 1879 waren in Deutschland vorhanden 370 Oefen mit
zusammen 2469
Retorten mit Generatorfeuerung, davon 237 Oefen mit 1875 Retorten in Betrieb. Zur
Heizung- der 370 Oefen dienten 296 Generatoren, von denen 100 vor, 59 hinter, 117
unter den Oefen, 20 entfernt, 259 unter und nur 37 über Flur liegen. Es liegt
demnach nur der 5. Theil sämmtlicher Generatoren hinter den Oefen, der 15. entfernt
und der 8. über Flur und geht daraus wohl zur Genüge hervor, daſs die natürlichste
und zweckmäſsigste Lage des Generators entweder unmittelbar vor, oder unter dem Ofen
und unter Flur ist; 211 haben gleichbleibende Schütthöhe, nur 85 variable und nur 73
Dampfzuführung, 94 einen Schlitz unten, 93 seitlich, 53 einen schrägliegenden, 56
einen horizontalen Rost; bei 261 wird die Verbrennungsluft durch die abgehenden
Rauchgase erwärmt und nur bei 35 nicht. Im Ganzen arbeiten 92 Anstalten mit
Generatorfeuerung. (Vgl. Wagner's Jahresbericht, 1880
S. 888.)
Die Gasretortenvorlage von Th. v. d. Linden in Oberhausen (* D. R. P. Nr. 10600
vom 9. December 1879) besteht aus dem guſseisernen Vorlegekopf A (Fig. 9 und
10 Taf. 25) mit Ring D und Vertiefungen g. An seinem weiteren Ende schlieſst sich derselbe
der Form der Retorte an, an seinem engeren Ende ist er abgerundet. Der
Dichtungsdeckel B ist kapselförmig und mit abgehobeltem
Ring r und erhabenen Schraubenwindungen f versehen, welche in die Vertiefungen g genau eingreifen.
F. W. Lürmann in Osnabrück (* D. R. P. Nr. 9062 vom 27.
Juli 1879) macht den Vorschlag, Gasretorten aus hochkantigen, feuerfesten Steinen
gewöhnlichen Formates, deren Querfugen durch Zwischenmauern gestützt sind,
aufzumauern.
Vorrichtungen zum Füllen und Entleeren der Gasretorten
wurden bereits von Holden und Best (1870 196 266), Foulis (1876 220 * 221),
A. v. Löhr in Wien (* D. R. P. Kl. 24 Nr. 4499 vom
12. März 1878) und A. Q. Roſs in Cincinnati (* D. R. P. Nr. 8075 und 8076 vom 18. Januar 1879)
angegeben. – A. Longsdon in London (* D. R. P. Nr. 8543
vom 28. Juni 1879) hat auf einem längs den Ofenreihen eines Retortenhauses
verschiebbaren Wagen E und G (Fig. 11 bis
13 Taf. 25) den verschiedenen Höhenlagen der Retorten entsprechend
verstellbare Laufschienen A angebracht, auf welchen ein
kleiner Karren in der Richtung der Längenachse der Retorten hin- und hergefahren
werden kann. Der Karren B läuft mittels vier Rädern auf
der Laufschiene A. Die Achse a für die oberen Räder ist auf dem Karrengestell r drehbar, während die Achse b für die beiden
unteren Räder an zwei Zugschienen bq hängt, welche
mittels des Hebels pq mit der zweiten auf dem
Karrengestell r drehbar gelagerten Achse p verbunden sind. Auf dieser Achse p ist ferner ein Hebel op
befestigt, durch dessen Drehung um einen kleinen Winkel die Achse b und damit die darauf befestigten unteren Laufräder
des Karrens B gehoben und gesenkt werden können. Auf
dem Karrengestell r ist ein Zieheisen c befestigt, welches an seinem Ende d eine um diesen Punkt drehbare Klappe e trägt, deren Form dem unteren Retortenquerschnitt
entspricht. Unterhalb des Zieheisens c ist um k drehbar ein Arm ik
befestigt, von dessen Angriffspunkt l aus eine
Zahnstange lo die Verbindung mit der Achse p herstellt. Hat dieser Hebel die in den Fig. 11 und
12 angegebene, nach rechts geneigte (Anfang- bezieh. Mittel-) Stellung,
so ist der Hebel pq und damit die Achse b gehoben; befindet er sich jedoch in der in Fig.
13 gezeichneten nach links geneigten (End-) Stellung, so ist pq und damit die Achse b
gesenkt.
In der ersten Stellung bei dem Einfahren wird der Karren B von den vier Laufrädern völlig getragen, während bei dem Ausfahren die
unteren Laufräder ausgerückt sind und das vordere Ende des Zieheisens c mit seiner Klappe e auf
dem Boden der Retorte schleifen muſs. Zur Bewirkung der Drehung der Klappe e ist auf das Zieheisen c
eine mit dem Hebel ik in l
verbundene Stange t gelegt, welche mittels einer
kleinen Lenkstange gh die Klappe e in die besprochenen Stellungen bringt. Damit jedoch
bei der in Fig. 13
gezeichneten Lage des Hebels ih die Klappe e in der senkrechten Stellung festgehalten wird, ist
eine Sperrklinke nmu angebracht, deren Ende u sich gegen eine an dem Zieheisen c angebrachte Nase s legt,
wenn der Hebel nach links ausgeschlagen ist. Ist der Hebel nach rechts ausgelegt, so
ist die Sperrklinke der Verschiebung von t auf c nicht hinderlich.
Der Karren fährt in der in Fig. 11
angegebenen Stellung die eine umgekehrte Mulde mit offenem Boden bildende Klappe e in die Retorte hinein; da die Laufräder auf der Achse
b gehoben sind, so geht die Mulde, ohne Widerstand
zu finden, über die Kokesschicht oben an der Decke der Retorte hinweg, bis sie in
die Stellung der Fig. 12
gelangt. Während des Ueberganges aus dieser Stellung in jene der Fig. 13
findet nun nicht nur ein Umklappen der Klappe c aus der
horizontalen in die verticale Stellung statt, sondern der Karren B verliert auch gleichzeitig seine Unterstützung auf
den Laufrädern der Achse b. Diese Umstellung des Hebels
erfolgt selbstthätig dadurch, daſs derselbe durch den Bolzen H, welcher in einem Bock C eingelegt ist, der
zweitheilig an der Wange G des Wagens befestigt ist,
auf die andere Seite nach links gedrückt wird. Verschiedene Einkerbungen F auf den beiden Schenkeln des Bockes C ermöglichen das Einlegen des Bolzens H an verschiedenen Stellen, so daſs das Umklappen des
Hebels verschiedenen Weglängen des Karrens B
entsprechend erfolgen kann. Durch das Umklappen des Hebels wird nun die Klappe e umgeschlagen, die Sperrklinke nmu hinter die Nase s eingeklinkt und dadurch
die Klappe c in der verticalen Stellung festgehalten.
Ferner senkt sich dadurch die Achse b und die Klappe
e ruht mit dem halben Gewicht des ganzen
beweglichen Apparates auf dem Boden der Retorte und zieht dadurch bei der
Zurückbewegung des Wagens B die Koke aus der Retorte
heraus. Die Flügelbleche f bedecken die Koke auch von
oben und hindern somit ein Zurückgleiten derselben.
Ein zweiter Bock D an der Wange E des Wagens stellt durch die Fläche I zuerst der Sperrklinke nmu und dann dem Hebel ih ein Hinderniſs
entgegen. Infolge dessen wird die Sperrklinke bei u aus
der Nase s gehoben und der Hebel nach rechts
herumgeworfen. Dadurch aber wird die Stange t
vorgeschoben und die Klappe e mittels des Gliedes gh horizontal gestellt, zugleich aber die Achse b und damit das Ende d des
Zieheisens c gehoben, also der Apparat wieder in seine
erste Stellung (Fig. 11)
zurückgebracht.
Nach dem Bericht über den Betrieb der
städtischen Gaswerke in Köln betrug die Gesammtmenge des dort dargestellten
Leuchtgases für das Betriebsjahr 1879/80 12833 610cbm. Davon wurden abgegeben an Private 8457 869cbm, öffentliche Beleuchtung 1985 113cbm, selbst verbraucht an Leuchtgas 182945cbm und zur Unterfeuerung 1517714cbm,
zusammen nutzbar 12143641cbm, somit ergibt sich
ein Gasverlust von 682069cbm oder 5,3 Proc.
1000k Kohlen lieferten:
1879/80
1878/79
Gas
300,46cbm
gegen
303,52cbm
Nutzbares Gas
284,31
„
274,81
Verkäufliche Kokes
535k
„
496k
Theer
44,23
„
40,40
Schwefelsaures Ammoniak
9,92
„
9,60
Für 100cbm Nutzgas stellten sich im genannten
Betriebsjahr die Ausgaben und Einnahmen folgendermaſsen:
An Kohlen
2,985
M.
„ Stocherlöhne
0,596
„ Reinigung
0,088
„ Unterhaltung der Gasöfen
0,243
„ „ „ Dampfmaschinen und
Exhaustoren
0,166
„ Ausbesserungen
0,302
„ Unterhaltung des Röhrensystemes
0,125
„ „ der öffentlichen Beleuchtung
0,336
„ „ „ Eisenbahn
0,008
„ Gehälter
0,455
„ Unkosten
0,448
„ Gasmesserreparaturen
0,125
––––––––––
Zusammen
5,877
M.
Zinsen
3,264Amortisation 0,885Abschreibungen 4,730
8,879
M.
––––––––––
Gesammtausgabe
14,756
M.
––––––––––
Für Gas
10,808
M.
„ Kokes
2,169
„ Theer
0,526
„ Ammoniak
0,842
„ Verschiedene Producte
0,017
„ Privatanlage
0,076
„ Gasmessermiethe
0,309
„ Pacht
0,009
––––––––––
Gesammteinnahme
14,756
M.
Zieht man von der Brutto-Betriebsausgabe
= 5,877
M.
die Einnahme für Nebenproducte u. dgl.
= 3,948
––––––––––
so erhält man als Brutto-Fabrikationskosten für 100cbm
= 1,929
M.
Demnach kostet 1cbm Nutzgas
nur 1,929 Pf. in der eigentlichen Fabrikation, einschlieſslich der Ausgaben für
öffentliche Beleuchtung.
Tafeln
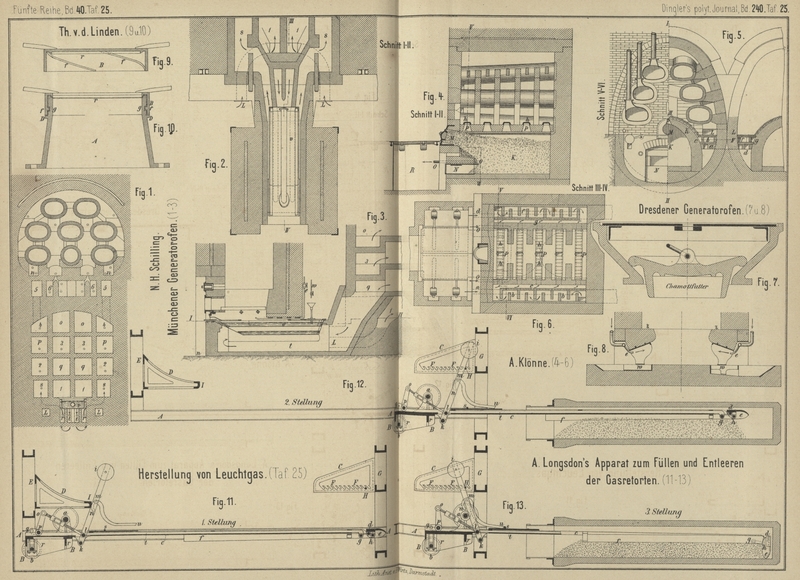