Titel: | Neuerungen im Eisenhüttenwesen. |
Autor: | St. |
Fundstelle: | Band 241, Jahrgang 1881, S. 291 |
Download: | XML |
Neuerungen im Eisenhüttenwesen.
(Patentklasse 18. Fortsetzung des Berichtes S. 304
Bd. 240.)
Mit Abbildungen auf Tafel 23.
Ueber Neuerungen im Eisenhüttenwesen.
Westman's Röstofen für
Eisenerze (Fig. 1 bis
4 Taf. 23), welcher in Schweden allgemein Anwendung findet, verwerthet
als Brennmaterial die Gichtgase des Hochofens. Er hat einen 9m,5 hohen Schacht, einen unteren Durchmesser von
3m und eine Gicht von 1,5 bis 2m Weite. 4 kleinere, seitlich angebrachte Essen
n führen die Verbrennungsproducte ab und vereinigen
sich in einer gewissen Höhe zu einem einzigen Schornsteine. Die Mitte der Gicht wird
dadurch behufs Einstürzung der Beschickung frei gehalten. Das Begichten geschieht
selbstthätig mittels eines Wagens m, welcher auf einer
schiefen Ebene läuft und durch ein über eine Seilscheibe gelegtes Zugseil bewegt
wird. Bei Ankunft des Wagens m auf der Gicht trifft
derselbe auf einen Hebel i und öffnet dadurch den
Gichtverschluſs. Die Beschickung entleert sich in den Schacht, der Gichtdeckel
schlieſst sich und der Wagen kehrt wieder zur Hüttensohle zurück. Die Bewegung des
Seiles geschieht von der Welle der Gebläsemaschine aus durch eine geeignete
Transmission.
Der Schacht hat zwei Hemden: Die innere Ausmauerung besteht aus feuerfestem Material;
dann kommt gewöhnliches Mauerwerk und auſsen ein Blechmantel mit Verstärkungsringen.
Die Ausziehöffnungen b liegen im untersten Theile des
Ofens, dicht über dem Boden und dienen gleichzeitig zum Eintritt der Luft, so daſs
letztere sich an den in den Ausziehöffnungen liegenden heiſsen Erzen erhitzt, diese
aber abkühlt. Die vom Hochofen entnommenen Gichtgase treten in ein rund um den Ofen
gelegtes, auf einem Mauervorsprung ruhendes Rohr c und
gelangen durch 16 Düsen e und die Oeffnungen f in das Ofeninnere, wo sie auf die Luft treffen und
verbrannt werden. Ueber den Oeffnungen f liegen noch
zwei Reihen Schürlöcher h und i, welche dazu dienen, das Schachtinnere zu beobachten, Versetzungen
aufzuheben und, wenn nöthig, Luft einzulassen. Wie ersichtlich, ist der Theil über
den Ausziehöffnungen durch einen Ring g mit Wasserrohr
gekühlt. Behufs Inbetriebsetzung des Ofens füllt man seinen unteren Theil und die
Ausziehöffnungen mit Reisigbündeln und verstopft die über den Gasdüsen liegenden
Oeffnungen mittels nach innen vorstehender Holzklötze, damit das in die Gicht von einer Höhe von 8
bis 9m herabgestürzte Erz nicht die unteren Kanten
jener Oeffnungen und damit die innere Schachtausmauerung zerstöre. Nachdem der Ofen
auf diese Weise bis über die Höhe der Gasdüsen mit Holz vollgestopft ist, füllt man
ihn mit Erz, entzündet das Holz und läſst die Gichtgase hinzutreten.
Handelt es sich darum, einen nur zeitweise auſser Betrieb gesetzten Ofen wieder in
Gang zu bringen, so läſst man das geröstete Erz im unteren Ofentheile bis zur Höhe
der Gasdüsen stehen, füllt dann den Schacht mit Holz bis zu einer gewissen Höhe und
begichtet hierauf mit rohem Erz. Man legt dadurch einfach das Feuer höher und kratzt
je nach dem Fortgange der Röstung das schon geröstete Erz unten aus.
Die einzige Schwierigkeit beim Betriebe dieses Ofens liegt in der Regulirung der
Temperatur, da dieselbe leicht so hoch steigen kann, daſs sich, besonders bei
Verwendung von kieseligen Erzen, diese verschlaken. Auſserdem kommen – wie bei allen
mit Hochofengasen geheizten hüttenmännischen Apparaten – Explosionen vor; man kann
dieselben jedoch leicht durch Anbringung von Sicherheitsklappen in den Gasröhren und
oberen Ofentheilen unschädlich machen. Würde man den ganzen Ofen höher legen und die
Sohlen der Ausziehöffnungen nach unten geneigt herstellen, wie es z.B. bei den Oefen
in Cleveland der Fall ist, so würde ein selbstthätiges Entleeren des Ofens
stattfinden und der Arbeiter nur ein Oeffnen und Schlieſsen der die Ausziehöffnungen
versperrenden Thüre nöthig haben.
Ein solcher Westman'scher Ofen von obigen Dimensionen
ist im Stande, 40t Erz in 24 Stunden zu rösten.
Die Kosten sind, da man keines besonderen Brennmaterials bedarf, geriög. Er hat
endlich den groſsen Vortheil, daſs das Vermengen der Brennmaterialasche mit den zu
röstenden Erzen umgangen wird. Letztere Eigenschaft läſst ihn sogar da ökonomische
Verwendung finden, wo man keine Hochofengase zur Verfügung hat und schlechtes
billiges Brennmaterial in Generatoren vergasen muſs. (Nach dem Génie civil, 1881 Bd. 1 S. 145.)
Ueber die Rettung eines beinahe
vollständig eingefrorenen Hochofens Büttgenbach'schen Systemes (mit frei
stehendem Schacht und Gestell) auf der Neusser Hütte berichtet Büttgenbach selbst in einer Versammlung des Vereines
deutscher Ingenieure (vgl. Wochenschrift, 1881 S.
23.)
Der Gestell- und Rastraum waren bis auf eine Höhe von 4m über dem Bodenstein vollständig zugeblasen und mit einer kalten Masse
gefüllt und war es unmöglich, Wind in den Ofen einzuführen. Dabei waren die
Gestellwände bis auf 150 bis 200mm Dicke
weggebrannt, die Gebläseformen lagen 4m über dem
Bodenstein und hatten kein Feuer mehr, während der untere Theil des Gestelles von
Rissen bis zu 10cm Breite zerklüftet war.
Um den Ofen wieder in Gang zu setzen, wurden die Formen aus dem Ofen genommen, alle
Oeffnungen zugestopft, die Gicht zugedeckt und der Ofen sich 4 Tage selbst
überlassen. Gleichzeitig stellte man durch Anbohren des Schachtes über dem Tragringe
fest, daſs ersterer nicht gelitten. Man entfernte nun allmählich die Gestellwände
zwischen den einzelnen Formgewölben, kratzte die fast kalte Masse, soweit es zur
Aufführung eines neuen Gestelles nothwendig war, aus und brach endlich den noch
stehen gebliebenen mittleren Pfeiler, welcher die sich in der Mitte der Rast
gebildet habende Decke trug, weg. Da letztere erkaltet war, trug sie die ganze im
Ofen noch befindliche Beschickungssäule. Nachdem mit dem Fortschritt dieser Arbeiten
das neue Gestell wieder fertig gebaut und über jedem Formloch ein Raum für eine
Kühlform ausgespart worden, füllte man das Gestell mit 20t Kokes und 2500k glasiger saurer Schlacke, deckte die Gicht ab, füllte die um den Raum
von etwa 4 Ladungen niedergesunkene Beschickungssäule bis zum Rande der Gicht auf
und entzündete das auf dem Boden liegende Holz. Nach 12 Stunden hatte die
Kokesfüllung unter Einwirkung von nur geringem Winddruck Feuer gefangen, die Formen
wurden auf ihre normale Höhe gelegt und frisch geblasen. Nach 9 Stunden wurde die
Schlacke abgelassen und 6 Stunden später ein regelrechter Eisenabstich erzielt.
Die ausgekratzten kalkigen Massen wogen 30 und dauerte die ganze Operation 14 Tage.
(Vgl. Witherbee 1881 239
468.)
Die Anwendung von Hochofen- und
Bessemerschlacken als Versatz in Bergwerken. Die Zeitschrift für das Berg-, Hütten- und Salinenwesen, 1881 S. 67 bringt
einen Aufsatz über einen Schlackenversatz auf Zeche Gräfin Laura, welche theils
neben der Alvenslebener Hütte liegt, theils sich unter derselben erstreckt. Die
hierbei verwendete Schlacke wird vom Hochofen in guſseiserne Wagen abgestochen und
nach dem Erkalten die Kastenwände der letzteren abgehoben. Die Blöcke gelangen dann
auf Abkühlungsbänke und werden zuletzt mit dem Fäustel zerschlagen. Die Schlacken
von 6 Hochöfen, ihrer Beschaffenheit nach Singulo- bis Bisilicate und je nach dem
Ofengang dicht, d.h. glasig oder steinig, in welchem Falle sie auſserordentlich fest
sind oder porös, so daſs sie vollständig zerbröckeln, werden durch dicht neben der
Hochofen- bezieh. Bessemeranlage liegende Duckel in die Grube gestürzt und durch
Pferde- oder Bremsbergbetrieb an den Ort ihrer Verwendung gebracht.
Die Erfahrung im Betriebsjahr 1879/80 hat erwiesen, daſs die Holzkosten (Stempel u.
dgl.) für 100k Kohlen bei dem gewöhnlichen
Abbaubetriebe 1,85 Pf., bei dem Betriebe mit Schlackenversatz nur 1,02 Pf.
ausmachen. Dabei betrug die Mehrförderung der in Folge von Schlackenversatz
gewonnenen Kohlen im letzten Vierteljahr 17686t
und die Selbstkosten dafür 30305,53 M., so daſs sich dieselben für den Centner auf 8,59 Pf., gegen
13,55 Pf. beim gewöhnlichen Betrieb stellten. 100cbm loser Schlacke liefern 80cbm
Versatzmaterial, welches sich sofort fest zusammensetzt und alsdann dem etwa
entstehenden Druck des hangenden Gebirges Widerstand zu leisten vermag. Eine
nachträgliche Volumenverminderung findet in einem Zeiträume eines Jahres um 0,5
Proc. statt. Neben der Ersparung der Kosten des oft weiten Transportes der Schlacke
zu den ausgedehnten theueren Haldenplätzen hat der Schlackenversatz für den Bergbau
die Vortheile, daſs eine groſse Anzahl neuer Gewinnungspunkte für die Kohlen
gewonnen werden, zugleich aber dadurch eine Ermäſsigung der für Tagebrüche zu
zahlenden Grundentschädigungen herbeigeführt wird.
Auſserdem werden Grubenbrände, da keine Kohle mehr stehen bleibt, vermieden; Klüfte
können durch das geringe Niedersetzen des Deckgebirges nicht mehr so leicht
entstehen und wird dadurch eine Verbindung des alten Mannes mit der Atmosphäre
aufgehoben. Endlich kann das Hereinbrechen von Wasser, welches beim Bruchbau oft in
groſsen Massen auftritt, nicht mehr so leicht eintreten. Es muſs jedoch dabei
bemerkt werden, daſs sich der Schlackenversatz nur da ökonomisch erweisen wird, wo
Hütte und Bergwerk sich gegenseitig in die Hände arbeiten können. Trotzdem aber
verdient der Gegenstand alle Aufmerksamkeit.
Ein Puddelproceſs, bei welchem als
Nebenproducte, unter rationellster Ausnutzung des Brennmaterials,
Kieselfluorwasserstoffsäure und Phosphorsäure gewonnen werden und welcher in
New-York von James Henderson ausgeführt wird, ist im
Engineer, 1880 Bd. 50 S. 312 beschrieben. Das Eisen
wird in einem Herde gepuddelt, dessen Boden aus gemahlenem Fluſsspath, dessen Seiten
aber aus Walzsinter oder einer anderen reichen Oxydationsstufe des Eisens bestehen.
Dabei verflüchtigt der Fluſsspath das im Eisen befindliche Silicium und den Phosphor
als Gas, anstatt dieselben in das Endproduct oder in die Schlacke überzuführen. Der
Ofen, in welchem der Proceſs ausgeführt wird, besitzt eine Gasfeuerung, und zwar
wird sowohl der Generator zur Erzeugung des Gases, als der Ofen zur Verbrennung
dieses Gases mit Gebläseluft gespeist. Um nun aber ohne weitere Beaufsichtigung und
Regulirung des Zuges genau so viel Luft in den Generator einzuführen, wie zur
Erzeugung einer gewissen Menge Gases nothwendig ist, und ebenso dem Ofen nicht mehr
Luft zuzuführen, als zur Verbrennung dieses Gases erforderlich ist, besitzt die
Gebläsemaschine zwei gekuppelte Cylinder verschiedener Gröſse, wovon der eine eine
ganz bestimmte Luftmenge für den Generator, der andere eine ebensolche für die
Feuerung liefert. Die beiden Gebläsecylinder können entweder eine gemeinsame,
durchgehende Kolbenstange besitzen und kann diese direct mit der des Dampfcylinders
verbunden werden, oder es können an ihre Stelle zwei Roots-Gebläse von bestimmtem
Wirkungsgrad treten.
Verbrennt man im Generator Kokes ohne Wasserstoffgehalt, so sind die erforderlichen
Luftmengen gleich.
Der Herd, in welchem das Gas verbrannt wird, besitzt eine runde Gestalt und rotirt,
ähnlich dem Pernot'schen Ofen, um eine verticale Achse.
Aus diesem Herde treten die verbrannten Gase in eine zweite Kammer, welche dem
Puddelraum ähnelt, und schmelzen hier das Roheisen für die folgende Beschickung.
Sodann gehen die Gase durch die Feuerrohre eines Kessels und umspülen, auf 150°
abgekühlt, die Windleitungsröhren, welche zum Generator führen, um endlich durch ein
in ein Wasserbecken tauchendes Rohr in die Atmosphäre zu entweichen. In dem Wasser
werden alle festen und condensirbaren Theile zurückgehalten.
Die Ausführung des Processes ist folgende: Während des Stillstandes des Ofens wird
der Herd mit Fluſsspath und Eisenerz behufs Raffination des Eisens bedeckt; sodann
wird Roheisen eingebracht und der Ofen in die höchste erreichbare Temperatur
versetzt. Nachdem das Eisen geschmolzen, wird die Temperatur heruntergedrückt und
während 20 Minuten auf der der Kochperiode des gewöhnlichen Puddelprocesses
gehalten. Sodann wird die Hitze wieder gesteigert und Erzklumpen, Eisenabfälle u.
dgl. eingeführt, bis der gewünschte Kohlenstoffgehalt erreicht und das Product
abgestochen werden kann.
Hat das graue Roheisen einen Gehalt von 3 Proc. Kohlenstoff, so ist die Umwandlung in
einer Stunde, vom Augenblicke der Einführung des geschmolzenen Roheisens aus dem
Vorherde an gerechnet, bewerkstelligt, so daſs jede 1½ Stunde 1 Hitze gemacht und
bei einem Durchmesser des Herdes von 3m,1 100t Schmiedeisen in einem Tage erzeugt werden
können. Die kurze Dauer des Processes rührt von der Heftigkeit her, mit welcher sich
das Fluor mit dem Silicium und dem Phosphor unter Erzeugung einer groſsen Wärmemenge
verbindet und von der Möglichkeit, binnen kürzester Zeit im Ofen die höchsten
Temperaturen hervorrufen zu können. Das mit den Feuergasen entweichende
Fluorsilicium und Phosphorfluorid zersetzt sich bei Berührung mit Wasser in
Kieselfluorwasserstoffsäure und Kieselsäure einerseits und Phosphorsäure und
Fluorwasserstoff andererseits. Die Waschvorrichtung kann natürlich jede Gestalt,
z.B. die bei Hochöfen gebräuchliche haben.
Die als Nebenproduct gewonnene Kieselfluorwasserstoffsäure soll zur Gewinnung des
Kaliums aus den Zuckermelassen und aus den Salzsoolen der Salzbergwerke als
Kieselfluorkalium benutzt werden.
Ph. Ant. Fauler in Freiburg, Baden (* D. R. P. Nr. 12
563 vom 9. April 1880) setzt den Schacht von Cupolöfen
aus einer Anzahl von auf einander gestellten auswechselbaren Ringen zusammen.
Dieselben bestehen aus einem kurzen Blechmantel, welcher an der äuſseren Seite oben mit einem ⌜-Eisen,
unten mit einem ⊥-Eisen versehen ist. Der nach innen vorspringende horizontale
Schenkel des letzteren hat die Aufgabe, das im Mantel eingemauerte Mauerwerk zu
tragen; der äuſsere horizontale Schenkel jedoch legt sich über den horizontalen
Schenkel des Winkeleisens des nächst unteren Ringes und wird mit diesem verschraubt.
Behufs Auswechselung eines Ringes, dessen Ausmauerung weggebrannt ist, werden, wie
es scheint, die über ihm befindlichen Ringe an die feste Gicht mittels Ketten
aufgehängt, der einer Ausbesserung bedürftige Ring herausgenommen und durch einen
neuen, in Vorrath gehaltenen Ring ersetzt. Als weitere Neuerung ist patentirt eine
ringförmige Windeinführung, bestehend aus einem hohlen Guſsring.
Wie weit die Amerikaner in den Dimensionen der Cupolöfen für Bessemerwerke gehen, zeigen nach Engineering, 1880 Bd. 30 S. 592 die Fig. 5 und
6 Taf. 23, welche einen Schmelzofen für graues Roheisen der Albany and Rensselaer Iron and Steel Works in Troy
darstellen. 3 solcher Oefen, 8m,8 über der
Hüttensohle aufgestellt, versorgen zwei dicht neben einander stehende Birnen mit
grauem Eisen. Sie besitzen einen herunterklappbaren Boden, einen besonderen
Schlackenabstich und 8 Düsen mit einer Mundöffnung von 13mm Höhe und 20mm
Breite. (Die Zeichnung stellt eine ältere Construction dar.) Sie werden mit 65 Proc.
hartem Anthracit und 35 Proc. Kokes beschickt. Das Innere ist nahezu cylindrisch und
wird die eigentliche Rast mit feuerfestem Material ausgestampft und da die
Ausfütterung nur geringe Dimensionen hat, durch Schlangenrohre gekühlt. Zwei
zusammen arbeitende Oefen sind im Stande, in 24 Stunden 500t Eisen niederzuschmelzen.
Vor jedem Ofen steht auf einer Wage eine Kipppfanne mit einem Fassungsraum von 15t; in dieselbe wird das Eisen abgestochen, wenn
ein Aufenthalt im Blasen eintritt, der Cupolöfen aber abgestochen werden muſs.
Neuerungen an einem Universalwalzwerk von Wilh. Wenström zu Orebro, Schweden (* D. R. P. Nr.
12860 vom 28. Juli 1880). In Fig. 7 bis
9 Taf. 23 bedeuten A die obere, B die untere Walze, C und
D die Seitenwalzen, welche gegen die Kanten des zu
walzenden Eisens drücken. Die obere Walze A ist in
einem Querstück E gelagert, welches zwischen den
Walzenständern vertical verschiebbar ist. Das Einstellen desselben geschieht wie
gewöhnlich durch die Stellschrauben F und die Zahnräder
G und Handrad H. Die
untere Walze B behält stets ein und dieselbe Höhenlage,
kann indessen auf einem Schlitten J, in welchem sie
gelagert ist, in der Richtung ihrer Achse verschoben werden. Das Einstellen dieser
Walze geschieht durch die Stellschraube K mittels der
Kegelräder L und des Handrades M. Die Walze C ist nach keiner Richtung hin
verschiebbar, gestattet vielmehr nur eine einfache Drehung um ihre Achse. Ihr
Lagergestell kann deshalb mit dem Walzengerüst fest verbunden werden. Dagegen muſs die Walze
D der oberen Walze A
folgen können, wenn diese gehoben und gesenkt, sowie der unteren Walze B, wenn diese seitwärts verschoben wird. Diese
zweifache Bewegung wird dadurch bewirkt, daſs das Lagergestell O der Walze eine horizontale Geradführung P an dem Lagerstück E und
eine verticale Führung Q an dem Lagerschlitten J hat. Die Dicke des zu
walzenden Eisens wird demnach durch die Höhenlage der oberen Walze A, die Breite desselben durch die Rechts- oder
Linksverschiebung der unteren Walze B bestimmt. Diese
beiden Gröſsen werden in 4facher Vergröſserung auf einem Maſsstabe angegeben,
welcher durch das um die Achse jedes Handrades angebrachte Gewinde verschoben wird
und hierbei das betreffende Kaliber bezeichnet.
Die Walzen können entweder mittels langer Kuppelwellen, die das Einstellen der Walzen
in verschiedene Lagen ohne zu groſse Spannung gestatten, in Umdrehung versetzt
werden; es kann dies auch durch vier in der Weise angeordnete Getriebe geschehen,
daſs die Räder S und T
fortdauernd ihre ursprüngliche Stellung innehalten, während das Getriebe U der oberen Walze durch S
in Umdrehung versetzt, gehoben oder gesenkt werden kann, ohne daſs die
Angriffsflächen der Kuppelung sehr erheblich verändert werden. Dabei kann das
Getriebe V der unteren Walze, welches durch die
Kupplung T getrieben wird, während des vollen Ganges
zwischen den Zähnen des Getriebes T, also in seiner
Achsrichtung, hin- und hergeschoben werden. Die Rollen C und D drehen sich beim Walzen infolge der
Reibung des durch die Ober- und Unterwalze A und B gegen ihre Mantelfläche gequetschten Eisens. Behufs
Einführung des zu walzenden Stückes zwischen die Walzen bezieh. Abführung des die
Walzen verlassenden Stückes dienen Leitbahnen. Auf der Seite des beweglichen
Lagergestelles O der Walze D sind beide Bahnen mit Seitenrändern Y
versehen, während das Walzeisen auf der anderen Seite von den am Walzengerüst
befestigten Führungsrändern Z geführt wird. Will man
obere Leitbahnen anwenden, so werden dieselben an dem Lagerstück E befestigt und mit der Oberwalze A gehoben oder gesenkt.
Natürlich ist das ganze System nur für Fertigwalzen bestimmt.
St.
Tafeln
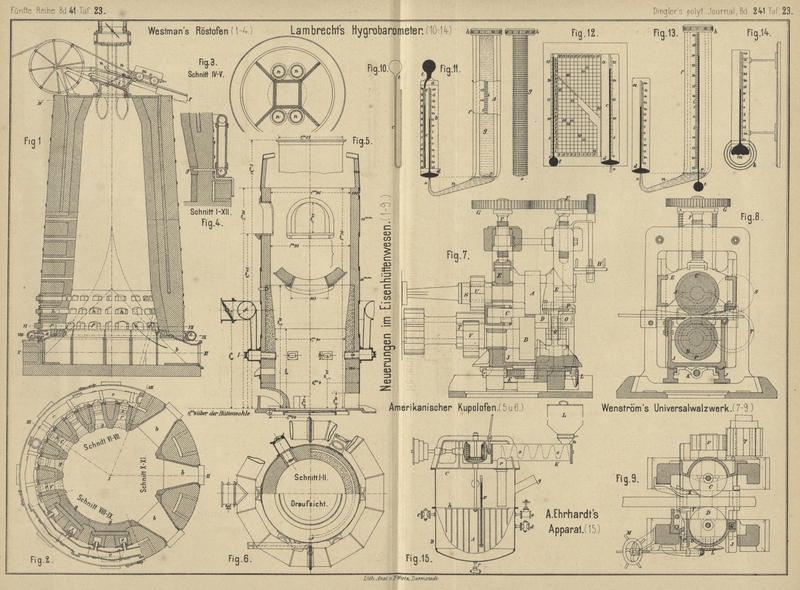