Titel: | Neuerungen im Mühlenwesen; von Prof. Friedr. Kick. |
Fundstelle: | Band 242, Jahrgang 1881, S. 181 |
Download: | XML |
Neuerungen im Mühlenwesen; von Prof. Friedr. Kick.
Mit Abbildungen auf Tafel 16.
(Patentklasse 50. Fortsetzung des Berichtes S. 195
Bd. 237.)
F. Kick, über Neuerungen im Mühlenwesen.
1) Reinigungs- und Schälmaschinen.
Die neueren Maschinen dieser Gruppe sind constructive Abänderungen der bekannten
Einrichtungen und weisen einerseits das berechtigte Bestreben nach Vervollkommnung
einzelner Details, andererseits die weniger empfehlenswerthe Verbindung von oft
getrennt ausgeführten Arbeiten, z.B. Scheuern und Ausblasen (Verbindung von
„Schälmaschine“ und Aspirator) oder Spitzen und Bürsten (Spitzgang und
Bürstmaschine) o. dgl., auf.
Unter den Detailverbesserungen
verdient das neuartige gestanzte Blech der Gebrüder Seck in
Dresden (* D. R. P. Nr. 13347 vom 4.
Juli 1880) erwähnt zu werden, welches als Mantelblech für Reinigungs- und Schälmaschinen recht gute Dienste leisten
mag. Fig. 1 Taf. 16 stellt dasselbe in Schnitt und Ansicht dar und es läſst
sich leicht erkennen, daſs die aufgebogenen scharfen Ränder der Schnitte die darüber
hingetriebenen Getreidekörner kräftiger bearbeiten als die Ränder der gewöhnlichen
Längsschlitze; ebenso ist es ersichtlich, daſs die abgestoſsenen Schalentheilchen
leichter nach auſsen gelangen, als dies bei den sonst verwendeten Reibblechen der
Fall ist. – Daſs die scharfen Ränder sich bei den Seck'schen Blechen auch nach einiger Zeit abstumpfen werden, ist wohl natürlich; hierdurch wird
aber der letzterwähnte Vortheil nicht beeinträchtigt.
Da bei vielen Reinigungs-, Schäl- und Bürstenmaschinen die
allmähliche Abnutzung der arbeitenden Steine, Bürsten u.a. eine Verkleinerung des Durchmessers des Mantels, welcher oft
aus Wellenblech besteht, erfordert, so sind von mehreren Constructeuren
Verbesserungen in der Anordnung des Mantels zum Zwecke der gleichförmigen leichten
Verkleinerung des Durchmessers eingeführt worden. So haben sich E. H. Vonhof in Sachsenburg i. Th. und Aug. und Bernh. Landgraf in Frankenhausen (Erl. * D. R.
P. Nr. 10480 vom 30. September 1879) eine Reinigungs- und Schälmaschine patentiren
lassen, welche mit einem an einer horizontalen Achse angeordneten conischen Läufer
gegen einen Reibblechmantel arbeitet und bei welcher das Neue darin besteht, daſs
die beiden Endscheiben mehrere concentrische Nuthen
enthalten, in welche, entsprechend der Steinabnutzung, die Mantelbleche eingesetzt
werden können.
Ernst
Garbe in Berlin (* D. R. P. Nr. 12896 vom 25. August 1880) ordnet bei
Bürstenmaschinen an beiden Enden des Mantels „Regulirungsringe“ an, welche
bei engster Mantelstellung einen geschlossenen Ring bilden, bei weitester Stellung
die Form Fig. 2 Taf.
16 aufweisen. Diese Regulirungsringe werden durch mehrere radial liegende
Stellschrauben, welche durch Schlitze der Ringe gehen, concentrisch zur verticalen
Bürstentrommel eingestellt und später nachgezogen. Die Mantelbleche sind in
geeigneter Weise mit den Regulirungsringen verbunden und wird jener
Verticalblechstreifen, welcher die Ringlücken (die klaffende Stelle) deckt, bei der
Zusammenziehung ausgewechselt.
Was nun die erwähnten Combinationen zweier Zwecke oder zweier oft getrennter
Mechanismen betrifft, so ist zunächst zu bemerken, daſs mit scheuernd oder arbeitend
wirkenden Theilen auch bisher häufig und mit vollem Rechte die reinigende Wirkung
bewegter Luft, also Ventilation verbunden war; denn hierdurch werden die
abgeriebenen Theilchen theilweise sogleich weggeführt.
Wenn daher K. F. Müller in Neustadt a. d. Haardt (* D. R. P. Nr. 11587 vom 16. April
1880) in seinem Patente sowohl beim Erlauf, als im Reinigungscylinder und
beim Auslauf ventilirt, so fügt er zu der schon mehrseitig gebräuchlichen
Luftwirkung im Reinigungscylinder und beim Auslauf (Eureka-Maschine, Puhlmann u.a.) noch jene beim Einlauf bei, welche
natürlich nichts schadet, aber auch nicht wesentlich nothwendig oder auch nur
förderlich ist.
H. M.
Hesse in Lehndorf, Sachsen-Altenburg
(* D. R. P. Nr. 12623 vom 26. Juni 1880) combinirt einen
Spitzgang mit dem Bürstenapparat und einem Aspirator. Die Bürsten sind am Läufer so
angebracht, daſs sie theils gegen die Wand, theils gegen den Boden der Zarge wirken
und, indem sie die
gespitzten Körner herumtreiben, endlich zum Ableitungsrohre führen, welches mit
einem Saugventilator in Verbindung steht. Gegen diese Combination lieſse sich
bemerken, daſs die Frucht, sowie sie den Spitzgang verläſst, ausgeblasen werden
sollte. Theilweise ist dies wohl der Fall; denn die den Spitzgang verlassenden
Theilchen fallen auf ein den Oberboden der Zarge bildendes ringförmiges Sieb, unter
welchem sich ein Hohlraum befindet, welcher gleichfalls mit dem Ventilator in
Verbindung steht. Es ist nur zu fürchten, daſs sich dieser niedrige Hohlraum bald
mit Spitzabfällen füllt und dieser Theil der Aspiration dann seine Wirkung verliert;
hiernach werden aber die Bürsten den Staub in die Spalte des Weizens einreiben und
eher nachtheilig als förderlich wirken.
Joh.
Kubon in Dresden (* D. R. P. Zusatz Nr. 9497 vom 19. Juni 1879) combinirt einen
Aspirator mit einem unterläufigen Spitzgang. Die
Construction ist wohl eigenartig, namentlich durch die Beifügung eines Regulators,
welcher auf die Stellung einer Saugklappe einwirkt, aber wesentliche Vorzüge sind
nicht aufzufinden; übrigens sind Zeichnung und Beschreibung unvollkommen.
Bei der namentlich zum Schälen von Roggen in Verwendung stehenden
Schälmaschine von Vinc. Till in Brück a. d. M. rotirt
(laut Angabe des Directors der Müllerschule in Brück) mit 350 bis 380 Touren in der
Minute eine gröſsere Zahl an einer Welle befestigter Eisenscheiben von 60mm Durchmesser in einem mit 8 bis 15 Touren sich
drehenden Siebcylinder von 650mm Weite. Die
Eisenscheiben, mit Schmirgel oder Sand bekleidet, tauchen an der Einlaufseite nahe
300mm tief in das Getreide, während diese
Schicht an der Auslaufseite nur etwa 100mm hoch
ist; sie stehen von einander 80 bis 100mm ab und
müssen nach 4 bis 6 Tagen bei einer täglichen Leistung von angeblich 10t neu mit Schmirgel bekleidet werden. Die ganze
Maschine ist von einem Holzmantel umgeben, aus welchem die Luft sammt dem Schälstaub
durch einen Ventilator in eine Staubkammer getrieben wird. Der geschälte Roggen geht
dann durch einen Tarar oder eine Bürstmaschine.
2) Neuerungen an Mahlgängen. Es
gehören hierher Verbesserungen an Details, unter
welchen namentlich die bei der Aspiration der Mahlgänge gebräuchlichen
Abklopfvorrichtungen mehrseitig den Stoff zu neuen Constructionen geboten haben, und
der ziemlich eigenartig construirte Mahlgang von C. W.
Raase. Mit Recht führt sich die von Jaacks und
Behrns in Lübeck zuerst in rationeller Weise gelöste Aspiration oder
Ventilation der Mahlgänge immer allgemeiner ein. Dieselbe besteht bekanntlich darin
(vgl. 1877 226 * 427), daſs die Luft aus dem Innern eines
in der erhöhten Mühlsteinzarge (oder Bütte) hängenden Stoffnlters durch einen
Saugventilator abgezogen wird. Die nachtretende Luft nimmt ihren Weg durch das
Läuferauge und zwischen den Mahlflächen und befördert so das Auswerfen des
Mahlgutes. Natürlich setzt sich Mehlstaub an die Filterflächen an; soll daher das
Filter für die Luft durchgängig bleiben, muſs es von Zeit zu Zeit abgeklopft werden,
wobei die im Saugrohr befindliche Klappe zu schlieſsen ist. In einfachster Weise
kann dies durch die Hand des Arbeiters alle 15 bis 30 Minuten geschehen. Die Abklopfvorrichtungen besorgen diese Arbeit
selbstthätig; daſs hier der Phantasie des Constructeurs ein weites Feld geboten ist,
ohne daſs dessen Anbau besonders wichtige Früchte zeitigen könnte, ist begreiflich.
Unter den diesbezüglichen neueren Constructionen seien erwähnt: die Aspirations- und
Abklopfvorrichtung von Ferd. Kraus in Neuſs a. Rh. (* D. R. P. Nr. 8954 vom 22. Mai
1879). Die Auslösung zur Abklopfvorrichtung kann gleichzeitig auf mehrere
Mahlgänge einwirken und die Luftabführung aus dem Filter ist in Folge Anwendung
eines in dem Filterraum passend angebrachten Zinkschirmes eine centrale; zudem ist
die Filtergröſse durch Befestigung an der Zargenwand eine vergröſserte. Die Abklopf
Vorrichtung von Jaacks und Behrns in
Lübeck (* D. R. P. Nr. 11877 vom 25.
April 1880) zeichnet sich durch besondere Einfachheit aus; bei ihr wird
durch ein endloses bewegtes Band, welches durch Mitnehmer auf die an den einzelnen
Mahlgängen befindlichen Apparate einwirkt, die Aufgabe gelöst.
P.
Schneitier in Berlin (* D. R. P. Nr. 12069 vom 13. Juli 1880) hat in constructiv
sehr einfacher, hübscher Weise die Aufgabe gelöst, die Länge der Zeiträume, nach
welchen jedesmal das Schlieſsen der Klappe im Saugrohr und das Abklopfen des Filters
ausgeführt wird, nach Bedarf abzuändern. Wenn es auch möglich ist, die
Zwischenzeiten für das Abklopfen ein- für allemal so zu wählen, daſs dieselben für
die gewöhnliche Mahlarbeit entsprechen, so läſst sich doch nicht läugnen, daſs
verschiedenes Mahlgut, namentlich bei verschiedenem Wassergehalt desselben, das
Filter früher oder später in seiner Wirksamkeit beeinträchtigt. Kann aber die Luft
allzu schwer hindurchtreten, so erhöht sich ziemlich rasch die Vermahlungstemperatur
und die vortheilhafte Wirkung der Ventilation wird wesentlich beeinträchtigt. Die
Aufgabe ist dadurch gelöst, daſs ein oscillirender Hebel, welcher mit einer
Reibungsschiebklaue auf eine Triebscheibe des Apparates einwirkt, in der Gröſse
seines Ausschlages leicht verändert werden kann. Diese Aenderung des Ausschlages
wird erzielt, indem der Verbindungspunkt einer von einer Kurbel angetriebenen
Schubstange an dem Hebel längs desselben versetzt wird. Zudem kann auch der
Kurbelradius vergröſsert oder verkleinert werden.
J. G. E.
Reichard in Stuttgart (* D. R. P. Nr. 13226 vom 17. September 1880) hat eine
Aspirationseinrichtung mit Abklopfapparat angegeben, bei welcher düten- oder trichterförmige Filter
in einem Zwischendeckel der Zarge so angebracht sind, daſs sie umgestülpt und
hierbei abgebeutelt werden können. Dadurch wird die Fläche der Filter
auſserordentlich vermindert, so daſs diese Anordnung schon aus diesem Grunde allein,
von anderen Bedenken abgesehen, sich nicht empfiehlt.
Ed. Borgward's Aspirationseinrichtung (* D. R. P. Nr.
11981 vom 18. April 1880) wird nicht in der Zarge des Mahlganges angebracht, sondern
es bildet der Staubfänger einen Apparat für sich, welcher auf der Zarge angebracht werden kann. Hierdurch wird auch das Filtermehl
gesondert gewonnen, obwohl dies nicht Gegenstand dieses, sondern des Seck'schen Patentes Nr. 6317 ist, welches wir Bd. 237
S. 202 erwähnten. – Der gleichfalls ventilirte Mahlgang von Georg
Milbank in Chillicothe, Nordamerika (*
D. R. P. Nr. 11988 vom 16. Mai 1880) mit seinen 18
Patentansprüchen, seiner Abführung des Mehlstaubes und seiner naiven Construction
ist einer mechanischen Miſsgeburt des vorigen Jahrhunderts gleichzuachten.
Unter den Verbesserungen anderer Mahlgangdetails sei die Steinstellung von Gust. Lucas in
Dresden (* D. R. P. Nr. 10431 vom 13.
Januar 1880) erwähnt, bei welcher von einem vertical verstellbaren Rahmen
sowohl das Spurlager der Mühlspindel, als das Vorgelege sammt seinen Lagern getragen
wird. Auf der Vorgelegewelle sitzt die Antriebsriemenscheibe, die Leerscheibe und
ein Kegelrad, welches auf ein kleineres an der Mühlspindel die Bewegung überträgt.
Indem alle diese Theile die Verticalbewegung mit dem Rahmen gleichzeitig mitmachen,
bleibt natürlich der Eingriff der Kegelräder stets richtig, aber die ganze Anordnung
wird umständlicher und die Steinstellung erfordert mehr Kraft.
Von den verbesserten Hauen sei
zunächst die „Mühlsteinhaue mit Universalgelenk“ von Aug. H.
Martin in Neustadt a. d. Haardt (* D. R. P. Nr. 7301 vom 27. April 1879) erwähnt, welche aus
den beiden Fig. 3 und
4 Taf. 16 zur Genüge erkannt werden kann (die gleichen Theile sind mit
denselben Buchstaben bezeichnet). Indem hier die Drehzapfen weiter aus dem Mittel
gelegt sind, als dies gewöhnlich der Fall ist, so kann beim Gang ein Klemmen nicht
eintreten und das Balanciren bleibt ein weit freieres.
Die feste dreiflügelige Haue von
J.
Hayn in Stettin (* D. R. P. Nr. 9390 vom 19. October 1879) ist durch den
Verticalschnitt Fig. 5 Taf.
16 charakterisirt. Jeder Flügel der Haue ruht auf einem Kautschukcylinder und wird
von einer Schraube gegen denselben gepreſst. Durch die drei Schrauben wird der
Läufer leicht horizontal gestellt. Die in der Verlängerung der Mühlspindel
angeordnete Schraube s gestattet, wenn sie angezogen
wird, ein leichtes Abheben der Haue von der Mühlspindel, wodurch das bei festen Hauen sonst
schwierige Abheben des Läufers beseitigt ist. Die Kautschukcylinder i bedingen eine kleine, wenn auch sehr beschränkte
Beweglichkeit des Läufers gegen die Haue, daher derselbe nicht vollkommen starr mit
der Mühlspindel verbunden ist. Natürlich braucht ein solcher Stein, um die
Unterlehne zu behaupten, keine mit der Mühlspindel zusammenfallende freie Achse zu
haben; ist der Stein im Material ungleich, so werden daher schädliche Lagerdrücke
entstehen, deren Vorhandensein man erst durch zu rasche Abnutzung der Pfanne gewahr
wird. Die übrigen Mängel, welche man gemeiniglich den festen Hauen vorwirft, sind
jedoch in anscheinend recht glücklicher Art behoben.
H. C.
Fricke in Bielefeld (* D. R. P. Nr. 9202 vom 31. August 1879) lieſs sich eine
Vorrichtung zum centrischen Anziehen der Lagerklötze an
Steinbüchsen patentiren, durch welche beabsichtigt ist, während des Ganges die Mühlspindel stets in richtiger
Lagerung zu erhalten. Wie bei den gewöhnlichen Steinbüchsen sind drei Backen, deren
Mittellinien unter 120° zu einander liegen, in der Steinbüchse gelagert. Diese
Backen werden durch Keile gegen die Mühlspindel gedrückt, welche mit nach unten
verlängerten Zapfen bei der einen Ausführungsweise auf einer horizontalen Platte
aufstehen, deren Heben (Emporschrauben) auch ein Steigen der drei Keile und ein
Andrücken der drei Backen zur Folge hat. Bei einer zweiten Construction stehen die
drei Zapfen auf drei geneigten Flächen einer Kreisscheibe auf, durch deren
entsprechende Drehung das Heben oder Senken der Keile erzielt wird. – Ist auch das
Bedürfniſs, die Büchse während des Ganges des Mahlganges anzuziehen, kein groſses,
so ist die Anordnung Fricke's für den Gebrauch
jedenfalls bequemer als die der gewöhnlich verwendeten Büchsen.
Daſs für jeden Mahlgang oder Walzenstuhl eine gleichmäſsig
wirkende Zuführung ein Bedürfniſs ist, weil von
derselben die Gleichförmigkeit des Productes und die Leistungsfähigkeit bedingt ist,
braucht nicht erst bewiesen zu werden; mit der Zuführung aber eine
selbstregistrirende Meſstrommel zu verbinden, welche auch noch die Menge des
Einlaufes für jeden Mahlgang oder Walzenstuhl angibt, scheint mir – von
Versuchsapparaten etwa abgesehen – kein dringendes Bedürfniſs zu sein. – Ludw. Ed.
Mühlau in Würzen, Sachsen (* D. R. P. Nr. 10408 vom 15. Januar 1880) hat sich diese
Aufgabe trotzdem gestellt und gelöst. Zudem signalisirt sein Apparat durch
Glockenzeichen, falls nicht hinreichende Mahlgutmengen zulaufen, und er gestattet
eine doppelte Regulirung, einerseits durch Veränderung der Höhe der zulaufenden
Getreideschicht, andererseits durch vom Hauptschieber seitlich angebrachte kleine
Schieber eine Veränderung der Breite des Getreidestromes.
Eine selbstthätige, mechanische Abstell- und Alarmvorrichtung
für Walzenstühle wurde von Gust. Heinr. Pfefferkorn in
Chemnitz (* D. R. P. Nr. 13917 vom
29. Juni 1880) angegeben.
Die Aus- und Einrückvorrichtung für
Mahlgänge von Nestor Reinicke in Langensalza (Erl. * D.
R. P. Nr. 10703 vom 9. Januar 1880) ist zwar originell, aber viel zu umständlich und
gebrechlich, um praktisch zu sein. Die Idee ist in Kürze folgende: Die im Läufer
angebrachte Haue kann durch eine Combination einer Reibungs- und Klauenkupplung mit
der Mühlspindel verbunden werden. Diese Verbindung wird gelöst, indem man einen
Ring, welcher den Läufer umgibt und der im Innern der Zarge oder Bütte liegt, hebt
und hierdurch auch den Läufer, welcher mit vier Rollen auf diesem Ringe ruht,
lüftet. Durch Senken des Laufringes wird die Kupplung eingerückt.
Anton
Emele in Mittelsteine bei Glatz (*
D. R. P. Nr. 11056 vom 7. December 1879) hat einen
elektrischen Controlapparat für Mahlgänge
patentiren lassen, bei welchem durch den Strom des zuflieſsenden Mahlgutes ein Hebel
in solcher Lage erhalten wird, daſs das Läutewerk schweigt, während es zum Spiel
kommt, wenn der Zufluſs des Mahlgutes aufhört. Man brauchte nur die bei
Hoteltelegraphen gebräuchliche Vorrichtung hiermit zu combiniren und es würde auch
die Nummer jenes Mahlganges oder sonstigen Müllereimaschine signalisirt werden
können, bei welcher der Zufluſs unterbrochen ist. Dies ist aber keine neue
Erfindung; Aehnliches kann somit übergangen werden.
Weit einschneidender in den bisherigen Gebrauch ist C. W.
Haase in Breslau (* D. R. P. Nr. 13472 vom 1. September 1880) bei seinem
Mahlgang vorgegangen, indem er das Läuferauge oder die Hohlen so weit vergröſserte,
daſs von den Steinen nur zwei Mahlkränze von etwa 20cm Breite übrig blieben. Die Mühlsteinstücke, welche diese Kränze bilden,
vergieſst er in sogen. Kapselringen, von welchen der obere mit Haue und Treiber in
eigenthümlicher Weise verbunden ist. Die Fig. 6Dieselbe ist nicht der Patentzeichnung, sondern einer späteren
Veröffentlichung Haase's
nachgebildet. Taf. 16 zeigt einen Verticalschnitt durch die
wichtigsten Theile des Mahlganges: m ist der Mahlkranz,
r der Kapselring, h
die Haue, t der gleichfalls vierflügelige Treiber, o ist der mit der Haue verbundene Streuteller, s die Mühlspindel. Die Flügel der Haue sind in Schuhen
n durch Blei eingegossen, welche Schuhe an den
Kränzen k vertical verstellbar sind, wenn die
guſseisernen Zwischenstücke z entsprechend dem
erfolgten Abmahlen des Steines entfernt werden. Die erforderliche Belastung des
Läufers erfolgt durch Einlegen guſseiserner, entsprechend geformter Gewichte in die
Kästchen r1 des
Kapselringes. Am Treiber sind Abstreichcurven a behufs
ausgiebiger Zuführung des Mahlgutes zu den Mahlkränzen angebracht.
Haase behauptet wohl mit Recht, durch diese Anordnung
eine gröſsere Leistung bei gleichem Kraftverbrauche zu erzielen und kühler zu
mahlen; irrig ist aber seine Anschauung, hierdurch den Walzen Concurrenz machen zu
können; denn jener die Schale so sehr schonende Angriff, wie ihn die Walzen
zulassen, kann auch durch den besten Mahlgang nicht erreicht werden. Das
Anwendungsfeld der Mahlgänge wird bei Weizen Vermahlung in einer rationellen
Kunstmühle doch nur im Spitzen, im Abmahlen von Schalen und Kleie und dem Ausmahlen
der Dünste, namentlich der ordinären Sorten derselben, bestehen. Auch die
Ventilation der Mahlgänge durch diese Construction für die Vermahlung von Roggen
überflüssig zu machen, wird darum nicht gelingen, weil durch die Ventilation die
feuchte Luft ohne Mehlverlust abgeführt wird und dadurch das Mahlgut trockener in
die Mahlcylinder kommt, was für diese von nicht zu unterschätzendem Werthe ist.
Nicht für eigentliche Müllereizwecke, wohl aber zum
Schroten von Viehfutter kann mit Vortheil die von der Maschinenbau-Actiengesellschafl Humboldt in Kalk bei
Köln gewählte Anordnung dienen, mit welcher wir die Schrotmaschinen beginnen wollen.
3) Schrot- und
Weizenschneidmaschinen. Die Schrotmaschinen oder Schrotstühle bezwecken
entweder eine grobe Verkleinerung der Getreidearten zu Zwecken der Viehfütterung,
oder die Vorverkleinerung bei der Hochmüllerei. Nur im letzteren Falle soll das
Brechen der Körner mit möglichst geringer Beimengung von Mehl geschehen. Zu der
ersteren Gruppe von Schrotstühlen gehört der unterläufige Mahlgang (Erl. * D. R. P.
Nr. 10091 vom 11. October 1879) der eben genannten Maschinenfabrik, welchen wir
seiner constructiv guten und einfachen Anordnung wegen in Fig. 7 Taf.
16 wiedergeben. Dieselbe bedarf keiner näheren Erklärung; wohl aber muſs
hervorgehoben werden, daſs sowohl der Mahlkörper a, als
der kegelförmige Läufer b aus Guſseisen hergestellt
sind und daſs diese Körper in verschiedener Höhe Nuthen eingegossen haben derart,
daſs, sobald die erste oberste Nuthreihe durch den allmählichen Verschleiſs des
Eisens abgerieben ist, sofort die zweite, endlich eine dritte zur Wirkung kommt, wie
dies m
Fig.
8 dargestellt ist. – Die Verwendung von Hartguſs macht derlei Vorkehrungen
überflüssig. Ob die Richtung der Furchen mit Rücksicht auf die Bewegungsrichtung des
Läufers den für die Hauschläge unterläufiger Mahlgänge aufgestellten Grundsätzen
entspricht, läſst sich aus der Patentbeschreibung nicht erkennen, ist jedoch
wichtig, wenn sich ganze Körner ins Schrot gelangen sollen.
A. Millot's sogenannte Schrotmaschine mit gezahnten
Scheiben (* D. R. P. Zusatz Nr. 12457 vom 4. November 1879) ist eigentlich weniger
zum Schroten, sondern zum Abmahlen von 4. bis 5. Schrot bestimmt und wird bei den
Desintegratoren besprochen.
Daſs durch die Getreideschneidmaschine von Reuter und Straube in
Halle a. d. S. (* D. R. P. Nr. 11920
vom 23. März 1880) zu gleicher Zeit ein Zerschneiden, Reiſsen und Mahlen
des Getreides unter Anwendung von Messern stattfinden soll, beruht auf dem
Miſsverständniſs der Aufgabe des Schrotens für Mahlzwecke, bezieh. der
Schneidwerke.
Zu der zweiten Gruppe von Schrotgängen gehört die
Getreidespaltmaschine von Th. Markurth in
Hamburg (* D. R. P. Nr. 9073 vom 7.
Juni 1879). Es arbeiten zwei Kreissägensysteme zusammen, ähnlich wie bei
bekannten Schrotstühlen, z.B. jenem von A. Zipser (1878
228 * 407). Neu ist,
daſs die Getreidezuführung nicht direct zwischen die Schneide walzen erfolgt,
sondern das Getreide zuerst in den Raum a (Fig.
9 Taf. 16) tritt, aus demselben unter dem Kreisschieber s vorbei gegen die Sägewalze w1 gelangen soll, welche die Aufgabe hat,
dasselbe zu erfassen und in Zusammenwirkung mit der zweiten Sägewalze w zu spalten. Es heiſst in der Patentbeschreibung,
„daſs das Getreide von unten (in der Richtung des Pfeiles) den Kreissägen
zugeführt wird, bei welcher Gelegenheit die schweren Verunreinigungen bei m liegen bleiben und nicht mit aufsteigen, also
auch die Sägeblätter nicht beschädigen können.“ – Dies ist jedoch unrichtig, denn bei ruhig stehendem Gehäuse wird das
Getreide nach seinem natürlichen Böschungswinkel unter dem Schieber gegen die Walze
abrollen und Steinchen werden ebenso gut an dieselbe gelangen als das Getreide; nur
dann, wenn das Gehäuse gerüttelt würde, wäre ein Grund vorhanden, daſs sich die
Steinchen allmählich bei m ablagern könnten. Diese
Maschine ist eher patentirt, als erprobt worden.
Ludw.
Hottmann in Grunbach, Württemberg (*
D. R. P. Nr. 14348 vom 11. August 1880 und Nr. 14369 vom 8.
Mai 1880) hat zwei Schrotgänge construirt, bei welchen durch angebrachte
Siebe die gebildeten Griese von den noch weiter zu schrotenden gröberen Theilen in
der Schrotmaschine selbst abgeschieden werden. Die eine dieser Maschinen besitzt
vier an einer verticalen Welle befestigte Scheiben, je mit einem geriffelten
Hartguſskranz besetzt, welcher gegen einen ebensolchen darüber befindlichen, aber
festen einstellbaren Kranz arbeitet. Das ausgeworfene Schrot fliegt gegen Siebe,
welche kurze Mantelstücke bilden und die Griese durchlassen sollen, während die
gröberen Theilchen über conischen Gleitflächen der nächsten Etage zugeführt werden.
Der zweite Schrotgang ist dem bekannten Conus oder Rubber nachgebildet. Der
rotirende Kegel ist aus geriffelten Hartguſssegmenten gebildet, der Mantel theils
aus Hartguſs, theils aus Siebsegmenten. Bei beiden Constructionen werden die durch
die Siebe entfernten feineren Theilchen nach Etagen der Maschine gesondert gewonnen.
Hottmann will hierdurch schärfere Griese und
weniger Schrotmehl erzielen. Verglichen mit den ganz vorzüglichen
Schrotwalzenstühlen mit Riffelwalzen kann der Erfolg kein vorzüglicherer sein; betrachtet man
jedoch diese Maschinen für sich, so ist klar, daſs durch die Anbringung der Siebe
weniger Mehl und schärferer Gries gewonnen werden muſs als ohne dieselben.
Die Schrotwalzenstühle sind durch
neuere Varitäten vertreten. Diesbezüglich sei der Schrotwalzenstuhl des Freisinger Vorschuſsvereines (* D. R. P. Nr. 10689 vom
20. December 1879) erwähnt, bei welchem die Hartguſsriffelwalzen schräg über
einander liegen. Die constructive Durchführung ist zu loben. Es läſst sich in
einfacher Weise der Minimalabstand der Walzen reguliren. Ueberflüssig ist die
besondere Belastung der oberen Walze, indem das Walzengewicht allein genügt, den
Mahlgutwiderstand auszuhalten.
Oscar
Oexle in Augsburg (* D. R. P. Nr. 9881 vom 29. November 1879) hat einen
Walzenstuhl mit geriffelten Walzen patentirt, bei welchem sich die Walzenoberflächen
an der Arbeitstelle in entgegengesetzter Richtung und zwar die eine im Sinne des
Durchganges sehr rasch, die zweite im entgegengesetzten Sinne sehr langsam bewegen.
Es soll durch die langsamere Aufwärtsbewegung der einen Walze die gleichmäſsigere
Vertheilung des Mahlgutes gefördert werden. Hierfür hat wohl in erster Linie die
gute Zuführung (Speisevorrichtung) zu sorgen.
Von neuerer Form sind die Schrotwalzen der Gebrüder
Peugeot in Valentigney, Frankreich (*
D. R. P. Nr. 12771 vom 2. Juni 1880), welche für die
Vermahlung ölhaltiger Früchte und Samen bestimmt sind
und eigentlich eher Mahlwalzen als Schrotwalzen heiſsen sollten, da sie das
ölhaltige Material zu einem Breie verreiben. Die Walzen haben ungleiche Tourenzahl,
sind unten mit Abstreichern versehen und zeigen die in Fig. 10
Taf. 16 dargestellte Form.
Endlich ist A. Millot's Walzenstuhl
(System Dost) seiner einfachen und rationellen
Construction wegen hervorzuheben. Fig. 11
Taf. 16 zeigt, daſs die obere Walze fix gelagert ist und die untere durch den Hebel
h entsprechend eingestellt werden kann; die Feder
f gestattet das Ausweichen der unteren Walze, falls
Eisentheile zwischen die Walzen kämen; sie wirkt aber nur bei Anwendung glatter
Walzen als elastischer Andruck, in welchem Falle sie durch die Mutter m schärfer gespannt werden kann. Der Antrieb beider
Walzen erfolgt durch Riemen.
Einer neuen Idee endlich begegnet man in dem Quetschwalzwerk der F. Wühlerischen Maschinenbauanstalt
und Eisengieſserei-Actiengesellschafl in
Berlin (* D. R. P. Nr. 13861 vom 4.
December 1880), bei welchem Quetschwalzwerk, bestimmt für groſskörnige
Cerealien, die von den gewöhnlichen Walzen schlecht erfaſst werden, z.B. Mais, eine
Walze und ein eiserner Ring zusammenarbeiten, durch welche Anordnung ein kleinerer
Klemmungswinkel resultirt; d.h. jener Winkel, welchen die Tangenten an Walze und
Ring in den Berührungspunkten mit dem zu quetschenden Korn einschlieſsen, ist
bedeutend kleiner als bei der gebräuchlichen Anordnung. Der Ring r läuft auf Reibungswalzen f,
f1 und ist f1 durch eine Feder gegen den Ring bezieh.
die Walze w gedrückt (vgl. Fig. 12
Taf. 16). Die Art der Mahlgut-Zuführung und Abführung ist nicht näher beschrieben. –
Der beabsichtigte Zweck könnte übrigens auch recht wohl durch Fink's Scheibenmühle sowie durch gröber geriffelte
Schrotwalzen erreicht werden, daher ein Bedürfniſs für diese etwas sonderbare
Anordnung wohl kaum besteht. Die Fink'sche Scheibenmühle, deren Horizontal schnitt
und Grundriſs in Fig. 13
Taf. 16 nach den Verhandlungen des Vereines für
Gewerbefleiſs, 1880 S. 247 dargestellt ist, arbeitet mit Klemmungswinkeln,
wie dieselben Walzen von etwa 4m Durchmesser
entsprechen würden (vgl. auch S. 194).
4) Walzenstühle. Als Material der
Walzen steht Hartguſs und Porzellan in vorherrschender Verwendung. Zuweilen finden
sich wohl auch Steinwalzen; dieselben haben sich aber in groſsen Mühlen nicht Bahn
brechen können und Versuche mit Granitwalzen, welche im Vorjahre in Pest
stattfanden, haben zu dem Resultate geführt, daſs die Walzen zu bald ihre feine
gleichförmige Oberfläche verlieren und durch Ausbröckeln von Theilchen stark rauh
und endlich auch unrund werden. Der kräftigsten Inanspruchnahme hält der Hartguſs
bisher am besten Stand und dies ist der Grund seiner, namentlich in groſsen Mühlen,
vorherrschenden Anwendung, wenn auch nicht bezweifelt werden kann, daſs die Dünste,
namentlich von mildem Weizen, auf Porzellanwalzen leichter (bei weniger Druck)
aufgelöst (ausgemahlen) werden.
Die Neuerungen bei den Walzenstühlen beschränken sich, wie
begreiflich, vorherrschend auf Einzelverbesserungen, zumeist ziemlich
untergeordneter Bedeutung, zuweilen untermischt mit Anordnungen, welche nur gemacht
scheinen, um ein Patent zu erlangen. Ueber die letzteren kann ohne Beeinträchtigung
des Lesers hinweggegangen werden; von den ersteren sei zunächst Friedr. Wegmann's Einlaufvorrichtung (* D. R. P. Nr.
10304 vom 4. December 1879) erwähnt, welche den Zweck hat, solche Materialien –
milde Dünste –, welche sich beim Einlaufe leicht zu Klümpchen ballen, zu isoliren,
so daſs sie in möglichst gleichförmiger Vertheilung zwischen die Walzen gelangen.
Dieser Aufgabe ist dadurch entsprochen, daſs neben die gewöhnliche geriffelte
Speisewalze s (Fig. 14
Taf. 16) die weit rascher bewegte „Förderwalze“
w gelegt ist, welche das Mahlgut aus der unter den
Walzen liegenden Blechmulde m herausschleudert und
hierbei vertheilt. Die Fig. 15 und
16 geben über die Verbindung der beiden Walzen s und w durch die Arme a, a1 und über den
Antrieb von w durch das innen verzahnte Rad r, sowie endlich darüber Aufschluſs, daſs die Förderwalze von dem Handrade
o aus durch Vermittlung der Schraube o1 und des verzahnten
Segmentes z nach Bedarf gehoben und gesenkt werden
kann. Ueber die Beschaffenheit der Förderwalze ist zwar in der Patentbeschreibung
nichts gesagt; nach Selnick's Mühlenberichten, 1881 Nr.
2 S. 15 aber soll dieselbe aus Porzellan hergestellt sein. Statt des Hebens der
Förderwalze kann auch die Mulde stellbar gemacht werden; in ihr sollen sich auch
specifisch schwerere Theilchen (Sand, Eisenstückchen) ansammeln können.
Die gleichmäſsige und ununterbrochene Zuführung des Mahlgutes
unter Verhinderung des Festsitzens desselben suchte F. Göbel
in Ratibor (* D. R. P. Nr. 12494 vom 17.
Juli 1880) durch einen über die Speisewalze gelagerten Rührer zu
erreichen.
Moritz
Martin in Bitterfeld (* D. R. P. Nr. 9832 vom 26. August 1879 und Zusätze Nr. 10344 vom
18. December 1879 und Nr. 12086 vom 30. Juni 1880) hat
Walzenstuhlanordnungen angegeben, durch welche eine besonders scharfe Einstellung
der Minimalentfernung der Walzen erreicht werden soll. Zu diesem Zwecke wird bei den
beiden letztgenannten Patenten zwischen die Walzenlager der beiden in gleicher Höhe
befindlichen horizontalen Mahlwalzen ein Keil eingedrückt und dadurch der Abstand
festgestellt. Ein besonderer Vortheil kann jedoch in dieser Anordnung gegenüber
anderen dem gleichen Zwecke dienenden nicht gefunden werden.
Andreas
Mechwart in Budapest (* D. R. P. Kl. 47 Zusatz Nr. 10634 vom 31. Januar 1880) lieſs
sich die Einschaltung von Zwischenrollen patentiren, um bei einer geraden Anzahl von
Walzen gleichfalls seinen bekannten, die Lager entlastenden Ring (vgl. 1879 231 * 99) anwenden zu können, welcher sich für
Ausmahlstühle vorzüglich bewährt hat.
Zu den in ihrer Construction von den sonst gebräuchlichen Anordnungen am meisten
abweichenden Neuerungen sind die Patente von Beyer in
Paris und Hermsdorf in Chemnitz zu rechnen.
Der Walzenstuhl von Friedr. L. Hermsdorf
in Chemnitz (* D. R. P. Nr. 14021 vom 25.
August 1880) ist für eine sehr kräftige, die Schale nicht schonende Getreideverkleinerung, mit geringen
Abänderungen laut Patentschrift auch zur Raffinirung von Holz- und Strohstoff
verwendbar. Es sind, wie die Skizze Fig. 17
Taf. 16 darstellt, zwei Paare Riffelwalzen und zwischen diesen zwei geriffelte
Sättel c, c1
angeordnet, welche sich gegen einander entsprechend einstellen lassen. Der Weg des
Mahlgutes ist durch die eingezeichneten Pfeile genügend dargestellt. Hermsdorf verbindet mit dem Walzenstuhl ein Rüttelsieb
zur Absonderung „der groben Kleie“.
Noch origineller, dabei aber constructiv (so weit es die etwas undeutlichen
Patentzeichnungen erkennen lassen) gut durchgeführt, ist der Porzellan-Walzenstuhl von
Aug.
Friedr. und Adolf G. Beyer in Paris
(* D. R. P. Nr. 13912 vom 9. Januar 1880). Die hohlen
Porzellancylinder laufen lose auf den festen Achsen; es sind daher nicht die Achsen, sondern
die Cylinder auf den Achsen angetrieben. Fig. 18
Taf. 16 zeigt den Längsschnitt durch einen Cylinder sammt seiner eisernen Armatur.
Die lange Röhre r muſs natürlich von innen geschmiert
sein, was auch eine eigenthümliche Anordnung bedingt. Zum Zwecke möglichst
gleichförmiger Vertheilung des Mahlgutes hat Beyer das
Ende der Gosse direct auf die eine Walze aufgesetzt und läſst durch entsprechende
Einstellung des mit einem Kamme oder einem Leder besetzten Halbcylinders h (Fig. 19)
das Mahlgut gegen die Vermahlungsstelle gleiten. Nebst der rotirenden Bewegung
erhält auch hier die Porzellanwalze eine Längsbewegung, wie dies schon an einem
früheren Stuhle derselben Firma (vgl. 1880 237 111) der
Fall war. Endlich ist noch zu erwähnen, daſs mit dem Obertheile des die Walzen
deckenden Kastens Saugröhren „zum Abführen der Kleie“ vorhanden sind, eine deshalb bedenkliche
Anordnung, weil durch dieselbe ja auch Mehltheilchen mitgerissen werden müssen und
es jedenfalls besser ist, das Abscheiden der Kleie in gesondertem Processe zu
vollziehen.
Für die richtige gleichförmige Wirkung jedes Walzenstuhles ist
der genaue Parallelismus der Walzenachsen wesentlich. Um dieser Bedingung für die
Dauer besser entsprechen zu können, hat Fr. Wegmann in
Zürich (* D. R. P. Nr. 9926 vom 19.
Juni 1879) eine Anordnung getroffen, welche darin besteht, daſs jedes der
beiden auf einen Zapfen ruhenden, bezieh. schwingenden Lager der stellbaren Walze
dadurch im verticalen Sinne etwas verstellt werden kann, daſs dieser Zapfen, welcher
excentrisch zu seinen gelagerten Hälsen angearbeitet ist, entsprechend verdreht
wird. Nachdem jene Lager auch eine geringe Seitenbewegung gestatten und durch die
„Pression“ gegen die fix gelagerte zweite Walze gedrückt werden, so
stellt sich die bewegliche Walze zur fest gelagerten richtig ein.
Bei den Walzenstühlen von Lorenz Nemelka in
Simmering bei Wien (* D. R. P. Nr.
11133 vom 27. Juni 1879), welche bereits im letzten Berichte Bd. 237*S.
112 besprochen wurden, ist durch die Lage der Walzenachsen – dieselben befanden sich
ursprünglich nicht in derselben Horizontalebene – auf
die Erhaltung der parallelen Lage hingewirkt; denn die im höheren Horizonte liegende
Walze wird sich durch ihr Eigengewicht stets längs einer Erzeugenden an die untere
Walze anzulegen trachten, wie dies in greller Darstellung aus Fig. 20
Taf. 16 ersichtlich sein dürfte. Aehnliche Anordnungen finden sich auch anderwärts
und es verdient betont zu werden, daſs hierbei ungleiche Lagerabnutzung weniger
nachtheilig auf die Walzenstellung einwirken und auch nicht so leicht eintreten kann
wie bei jenen Walzenstühlen, deren Walzen in derselben Horizontal- oder Verticalebene
gelagert sind. Das hier Gesagte gilt natürlich nur von Ausmahlstühlen, bei welchen
die Walzen nicht auf einen bestimmten Abstand eingestellt werden; ist letzteres der
Fall, dann muſs eine Stellvorrichtung vorhanden sein und durch diese, sowie durch
Lagercorrectionen, wird sich der richtige Parallelismus erreichen lassen.
Dienen Walzenstühle zum Ausmahlen und ist der verwendete Andruck
ein bedeutender, dann findet allerdings auch eine Erwärmung des Mahlgutes statt und,
um diese zu verhindern, hat P. Schneitier in Berlin mit
dem Walzenstuhle eine Aspirationsanordnung verbunden, von welcher Fig. 21
Taf. 16 eine Skizze darstellt: a ist das zum Ventilator
führende Rohr, b die Filterkammer, welche durch c, d mit dem Kasten unter den Walzen in Verbindung
steht. Wir halten diese Anordnung nicht für erforderlich, weil unserer Erfahrung
nach die Erwärmung des Mahlgutes zwischen Walzen die zulässigen Grenzen nicht
übersteigt, ja lange nicht erreicht. Der Vortheil liegt hier vielmehr in der
erhöhten Trockenheit der Mahlproducte, welche bei Exportmehlen allerdings Bedürfniſs ist. Daſs durch die Walzen das Mahlgut
minder ausgetrocknet wird als bei der Steinvermahlung, wurde beim Uebergange von der
Stein- zur Walzenvermahlung mehrorts sehr unangenehm empfunden.
Da mit den Walzenstühlen auch die sogen. Scheibenstühle, welche sich, wie bereits S. 191 hervorgehoben, durch einen
sehr kleinen Klemmungswinkel auszeichnen, nahe verwandt sind, so seien hier auch
einige Bemerkungen über diese Mahlmaschinen beigefügt. Die Einwirkung der conischen
Mahlscheiben auf das Mahlgut wird eine mehr reibende sein als die Einwirkung der
Walzen. Denn bei den letzteren gehen bei gleicher Tourenzahl der Walzen jene
Oberflächenpunkte, welche das Mahlgut klemmen, mit
demselben weiter, wobei sie durch ihre Annäherung stets mehr und mehr drückend
einwirken; bei verschiedener Umfangsgeschwindigkeit findet allerdings eine reibende
Einwirkung statt, aber das Hinschleifen des Mahlgutes erfolgt doch nur über eine
verhältniſsmäſsig geringe Strecke; denn die bei nicht geriffelten Walzen
angewendeten Differenzen der Umfangsgeschwindigkeiten sind gering. Bei den
Scheibenwalzen ist dieses Verhältniſs wesentlich anders. Es beginne im Punkte a (Fig. 22
Taf. 16) die Klemmung des Mahlgutstückchens, so bewegen sich die Oberflächenpunkte
der Scheibe A in der Richtung des Pfeiles 1 und jene
der Scheibe B in der Richtung des Pfeiles 2. Das
Mahlguttheilchen gelangt unter wachsender Pressung, der resultirenden Einwirkung
folgend, nach b, so hat es an der Oberfläche jeder der
beiden Scheiben sich um die Strecke cb hinbewegen
müssen. Findet nun auch ein Brechen des Theilchens statt, so werden die Bruchstücke
bald einer ähnlichen
Einwirkung unterworfen sein, bis sie endlich bei oo1 die engste Stelle passirt haben. Da
nun die äuſsersten Theile des Mahlgutes, auch der
Griese, stets wenigstens zum Theile aus Schalenstückchen bestehen; so findet hier
eine Verkleinerung der Theilchen ohne die bei Walzen vorkommende mögliche Schonung
der Schalentheile statt und das Ergebniſs muſs ein, namentlich bei Hochmüllerei,
auffallend minderwerthiges Mehl sein; daher sind die Scheibenmühlen als Auflös- und
Ausmahlstühle den Walzen nachzusetzen.
Betreffs selbstthätiger Abstell- und Alarmvorrichtungen siehe Seite 187.
(Schluſs folgt.)
Tafeln
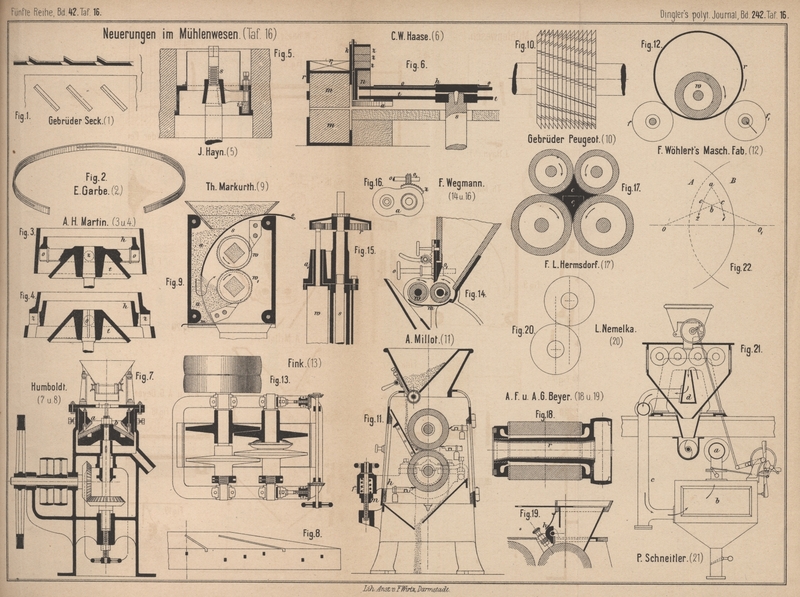