Titel: | Maschinen zur Verarbeitung des Thones und zur Herstellung von Kohlenziegeln. |
Autor: | H. F. |
Fundstelle: | Band 245, Jahrgang 1882, S. 108 |
Download: | XML |
Maschinen zur Verarbeitung des Thones und zur
Herstellung von Kohlenziegeln.
Patentklasse 80. Mit Abbildungen auf Tafel 10.
Maschinen zur Verarbeitung des Thones u. dgl.
In der Maschine zum Pressen der Braunkohlen, Lohe, Sägespäne,
des Torfes u. dgl. von Edm. Geisenberger und Em.
Picard in Brüssel (*D. R. P. Nr. 16768 vom 1. März 1881) bewegen drei über
einander liegende Schnecken das zu pressende Material durch eiserne Röhren, welche
von auſsen durch Feuer bespült werden, allmählich nach unten; die untere Schnecke
hat gleichzeitig die Aufgabe, die erwärmte Masse in die Gestalt eines prismatischen
Stranges aus der Maschine hervorzupressen. Zu dem Ende befindet sich in der
verlängerten Achse der unteren Schnecke eine schlank pyramidenförmige Röhre, welche
die Gestaltung des Stranges zu bewirken hat und, nahe dem Anfange derselben, über
der Schnecke ein Sternrad, dessen Flügel in die Schraubengänge der Schnecke
eingreifen, um zu verhüten, daſs die zu formende Masse an der Drehbewegung der
Schnecke sich betheiligt. Von diesem Sternrad ab wird die Röhre, in welche die
Schnecke ragt, sowie die eigentliche Formröhre, das Mundstück, durch Wasser gekühlt,
um hierdurch eine Kühlung bezieh. Erhärtung des zu bildenden Stranges zu vermitteln.
Das Quertheilen des Stranges soll in folgender Weise stattfinden: Vor dem Mundstück,
über und unter dem gebildeten Strange liegen zwei Wellen, auf welche je ein Paar
Ringe befestigt sind, welche radiale Messer zwischen sich tragen; bei Drehung dieser
Körper treffen je zwei Messer auf einander, so daſs sie den Strang an dieser Stelle
zerlegen. – Bei dieser Anordnung erscheint als besonders bedenklich, daſs die
Drehung der Messerwellen durch den hervorquellenden, zu schneidenden Strang selbst
erfolgen soll.
Die Thonkrugpresse von Jakob
Büchler in Sayn bei Coblenz (*D. R. P. Nr. 16760 vom 3. Juni 1881) hat im
Wesentlichen die in Fig. 1 Taf.
10 veranschaulichte Einrichtung. In dem Cylinder L
befindet sich ein Kolben, welcher den zu bearbeitenden Thon nach oben drückt;
zunächst trifft letzterer auf das aus Stahlmessern gebildete Gitter m, welches Steine und andere gröbere Verunreinigungen
zurückhalten, ferner – nach Ansicht des Erfinders – auch den Thon mischen soll.
Wegen des verhältniſsmäſsig geringen Durchmessers der oberen Mündung des
Zwischenstückes g trifft der Thon hier auf bedeutende
Widerstände; der zu ihrer Ueberwindung erforderliche Druck soll nun die im Thon
eingeschlossene Luft zum Entweichen durch die mit Filz gefüllten Oeffnungen h veranlassen. Der weiter durch die Röhre f sich fortbewegende Thon muſs endlich aus einem
ringförmigen Schlitz entweichen, welcher zwischen dem oberen Rande des im
Wesentlichen trommelförmigen Schiebers a und der
kreisförmigen Platte b – die mit Hilfe der Stange d in ihrer Lage festgehalten wird – frei bleibt; er trifft hierbei auf die
leicht verschiebbare Platte c, welche dem oberen Rande
der sich bildenden Thonröhre als Führung dient. Nachdem diese Röhre in genügender
Länge ausgebildet ist, schiebt man den Ring a nach
unten und führt über dessen oberen Rand einen gespannten Draht hindurch, um den
Thonstrang abzuschneiden, so zwar, daſs zwischen der Platte b und der Schnittfuge die Bodendicke des zu formenden Kruges bleibt. Der
cylindrische Krug wird nunmehr nebst Platte b und
Stange d abgehoben und von der Platte b abgestreift, worauf beide Theile b und d sowie der Ring a an deren frühere Stelle gebracht werden und das
Pressen eines anderen Kruges beginnt.
Die so gefertigten Krüge bedürfen einiger freihändiger Nacharbeit, insbesondere des
Ansetzens des Henkels; die Hohlkehle v, welche nahe dem
oberen Rande des Ringes a sich befindet, soll die
Glättung der Auſsenseite der Krüge vermitteln.
Nachdem der Thoninhalt des Cylinders L verbraucht worden
ist, wird – nach Lösen zweier Klammern – die Halsplatte g nebst den ihr anhängenden Theilen zur Seite geschoben, L aufs Neue gefüllt und nach Bedarf m gereinigt u.s.w.
Der Abschneidetisch für Ziegelsteine von F. H. Hetschold in Nippes bei Köln (*D. R. P. Nr. 16
775 vom 14. Mai 1881) besteht – auſser dem feststehenden Rollentisch – aus einem
beweglichen Rollentisch und dem eigentlichen Abschneidetisch, welche Theile
unabhängig von einander auf Rädern verschiebbar sind. Der Zweck dieser Zergliederung
ist nicht ersichtlich.
Billaris Maschine zum Verfertigen rundlicher
Kohlenziegel ist auf Grund folgender Erwägungen entworfen. Die
gebräuchliche Gestalt und Gröſse der aus (mit etwa 8 Proc. Theer gemischten)
Kohlenklein durch Zusammenballen gefertigter Brennstoffstücke ist unzweckmäſsig,
indem letztere meistens eine Zertrümmerung der Ziegeln erfordern, bevor sie in das
Feuer geworfen werden. Hieraus entsteht ein Arbeitsverlust, auſserdem aber lästiger
Gruſs. Die kantige Gestalt der Stücke führt schon während der Verfrachtung zum
Abstoſsen kleiner Brocken. Man soll daher die Brennstoffstücke rundlich gestalten
und ihre Gröſse so wählen, daſs ein Zerschlagen derselben überflüssig ist.
Zur Zeit erfolgt das Pressen der Kohlenziegel meistens in einer sich wenig
verengenden Röhre, so daſs die Reibung an der Wand der letzteren den nöthigen
Gegendruck liefern muſs. In Folge dessen findet das Ballen der Masse in
verschiedenen Punkten des Querschnittes mit verschiedenem Druck statt, was den
Zusammenhang der geformten Brennstoffstücke schädigt; zweckmäſsiger ist es, die
Pressung in überall geschlossener Form zu vollziehen. Der erforderliche bedeutende
Druck (etwa 0k,5 auf 1qmm) soll im Interesse der Dauer der Maschine nicht stoſsweise, sondern
allmählich anwachsend wirken. Endlich sollen die gröſserer Abnützung
unterworfenen Maschinentheile leicht und rasch durch andere ersetzt und auch die
Untersuchung der Maschine ohne gröſsere Betriebsstörungen möglich sein.
Billan's Maschine ist nach dem Génie civil, 1882 S. 278 in Fig. 2 und
3 Taf. 10 im Grundriſs bezieh. senkrechten Schnitt dargestellt. In A erfolgt die Mischung der vorher erwärmten Stoffe; von
hier wird das Gemisch zwischen die vier Rollen B
geführt. Durch das Zusammenlegen der mit kugelförmigen Vertiefungen versehenen vier
Rollenumfänge entstehen Hohlkugeln, entsprechend der Gestalt und Gröſse der zu
bildenden Brennstoffstücke. Indem nun der aus dem Mischer A niederflieſsende Strang – an die Umfange der Rollen B sich gut anschlieſsende Wände führen denselben – in
die allmählich sich verengenden Hohlräume gezwängt wird, entsteht die erforderliche
Pressung. Die geformten Brennstoffstücke entfallen den Hohlräumen, sobald diese sich
unten öffnen.
Die vier in Fig. 2
erkennbaren Kegelradpaare sichern die genaue gegenseitige Lage der Höhlungen; der
Antrieb erfolgt von der Welle D aus durch
Wurmgetriebe.
Ueber Boulton's Töpferei-Maschinen bringt Engineer, 1881 Bd.
52 S.470 einen bemerkenswerthen Aufsatz; leider sind die beigegebenen Abbildungen
unbefriedigend. W. Boulton in Burslem betreibt die
verschiedenen Maschinen eines Werkes mittels eines endlosen Seiles. Es sind sonach
Vorrichtungen nothwendig, welche eine bequeme Ein- bezieh. Ausrückung und ferner –
wenigstens für einige Maschinen – solche, welche einen raschen Wechsel der
Geschwindigkeit gestatten. Zum Betriebe der Töpferscheiben dient nun folgende
Einrichtung (vgl. 1871 201 * 21). An der in festen Lagern
sich drehenden senkrechten Spindel der Töpferscheibe ist ein einem abgestumpften
Kegel ähnlicher längerer Drehkörper befestigt, dessen Erzeugende ein wenig nach
auſsen gekrümmt ist. Neben derselben ist ein ähnlicher Körper in umgekehrter
Stellung beweglich gelagert, welche mittels einer Seilrolle in gleichförmiger
Drehung erhalten wird. Der Töpfer vermag nun durch den Druck des Fuſses die beiden
Drehkörper in Berührung zu bringen, so daſs durch die entstehende Reibung die
Töpferscheibe gedreht wird. Bei geringem Druck des Fuſses wälzt sich das dünnere
Ende der Antriebsrolle an dem dickeren Ende der mit der Töpferscheibe verbundenen
Rolle ab, so daſs diese sich langsam dreht; bei stärkstem Druck kommt aber das
dickste Ende der ersteren Rolle mit dem dünnsten der letzteren in Berührung, wodurch
eine sehr groſse Geschwindigkeit entsteht. Zwischen diesen beiden Grenzen liegende
Drücke bringen mittlere Geschwindigkeiten hervor, während nach Aufheben des Fuſses
die Töpferscheibe zum Stillstand gelang!.
Eine zweite Maschine, welche in gröſserer Zahl verlangte Gegenstände – z.B. Teller –
selbstständig formt, ist mit drei Töpferscheiben versehen, welche, auſser um ihre
eigene Achse, sich gemeinschaftlich um eine senkrechte Spindel zu drehen vermögen. Eine liegende
Welle, auf der ein nur auf ⅓ des Umfanges verzahntes Kegelrad befestigt ist, dreht
die erwähnte senkrechte Spindel ruckweise jedesmal um 120°, so daſs der Reihe nach
jede der Töpferscheiben unter die zur Ausbildung des Profils dienende Lehre zu
stehen kommt. In dieser Stellung tritt die Schnurrolle der betreffenden
Töpferscheibe mit einem ununterbrochen sich bewegenden Treibseil in Berührung, so
daſs die zugehörige Scheibe in rasche Drehung versetzt wird, während die beiden
anderen Scheiben sich in Ruhe befinden, also der fertige Gegenstand abgehoben,
bezieh. eine frische Thonplatte aufgelegt werden kann. Die Gestalt der
Scheibenoberfläche entspricht dem Hohlraum des zu formenden Gegenstandes; wird daher
die Lehre, deren Profil der Auſsenseite desselben entspricht, langsam
niedergelassen, so wird die Thonplatte an die Form der Töpferscheibe gedrückt und
weiter die sonst noch nöthige Formung der Auſsenseite vollzogen. Zu dem Ende ist ein
Daumen auf der vorhin erwähnten liegenden Welle angebracht, welcher, nachdem
derselbe früher die Lehre gehoben hatte, dieselbe langsam niedersinken läſst. Ein
zweiter Daumen dieser Welle legt rechtzeitig ein Messer an den Umfang der auf der
Töpferscheibe befestigten Form, um den sich bildenden rauhen Rand zu beseitigen.
Nach ⅔ Umdrehung der liegenden Welle ist die Formung des Gegenstandes vollzogen,
worauf das letzte Drittel zum Wechseln der Scheibenstellungen dient.
Einige andere anscheinend sinnreiche Einrichtungen sind nur angedeutet.
Die Mischmaschine und Presse mit Drehtisch zum Formen der
Thonziegel, Träberkuchen u. dgl. von L.
Souchard in Berlin (*D. R. P. Nr. 17844 vom 12. August 1881) unterscheidet
sich durch folgende Einzelnheiten von den bekannten Einrichtungen: Walzwerk und
Thonschneider sind mit einander fest verbunden, können aber um eine Säule gedreht
werden, so daſs die unten befindliche Mündung des Thonschneiders entweder über der
zu füllenden Form des Drehtisches sich befindet, oder diesen behufs Füllung mit der
Hand frei läſst.
Das Aufheben des Formbodens erfolgt durch die in Fig. 4 Taf.
10 dargestellte Einrichtung. Unter der Kopfplatte C,
welche einerseits durch die Säule D festgehalten wird,
andererseits mittels des Bolzens e an den Bock B befestigt ist, befinden sich die beiden verzahnten
Daumen E und F. E dreht
sich um einen an der Grundplatte A gelagerten festen
Bolzen h, F dagegen um einen Bolzen, welcher mit dem
Hebel g auf und nieder zu schwingen vermag. Mittels der
auf m befestigten Kurbel K
und der Lenkstange H werden die beiden Daumen auf
einander abgerollt, so daſs mit jeder Drehung der Welle m ein Heben und Senken des Lenkers g erfolgt;
ersteres tritt unmittelbar nach dem Zeitpunkte ein, in welchem eine gefüllte Form
unter der Platte C angelangt ist, so daſs das Pressen
stattfindet, indem der Stift des Formbodens durch das schwingende Ende des Lenkers g gehoben wird. – Referent kann die vorliegende
Bewegungsübertragung nicht loben, so lange nicht für eine bessere als die
vorliegende Führung des Formbodens gesorgt ist.
Nachdem die rückläufige Bewegung des Daumens F
eingetreten ist, dreht sich der Formtisch G um 90°; der
Stift des Formbodens gleitet auf der eine Schraubenfläche bildenden Schiene L und wird durch diese in dem Maſse gehoben, daſs der
Formboden den gepreſsten Ziegel aus der Form herausschiebt. Die ruckweise Drehung
des Tisches G wird dadurch hervorgebracht, daſs an der
liegenden Welle m ein nur theilweise verzahntes
Kegelrad sich befindet, welches sonach nur zeitweise mit dem Zahnkranz n des Tisches in Eingriff ist. Dieses
Bewegungsverfahren – welches auch von Anderen angewendet wird – halte ich nicht für
empfehlenswerth, indem dasselbe nothwendiger Weise heftige Stöſse im Gefolge haben
muſs und nach einiger Abnutzung nicht mehr zuverlässig wirkt. Während des Pressens
ward der Tisch G durch einen an der Stange s befestigten und an der Säule D geführten Riegel r festgehalten, welcher
zwischen zwei Nasen z des Tisches greift. Der Riegel
wird durch einen am Rade l befindlichen Stift unter
Vermittelung der Hebel u und t sowie des Gegengewichtes w selbstthätig auf
und nieder bewegt.
Ziegelpressen für Handbetrieb sind von C. Schlickeysen in Berlin (*D. R. P. Nr. 16969 vom 31.
März 1881) in gröſserer Zahl construirt Es liegt den vorliegenden Anordnungen die
Absicht zu Grunde, der Hand (auſser dem Einlegen des Thones und Abnehmen des
Ziegels) nur zwei Bewegungen zuzumuthen, indem durch eine derselben die Pressung
vollzogen, durch die andere gleichzeitig der Deckel der Preſsform abgehoben und der
gepreſste Ziegel herausgeschoben wird. Anscheinend lassen die vorgeschlagenen
Mechanismen noch Einiges zu wünschen übrig.
H. F.
Tafeln
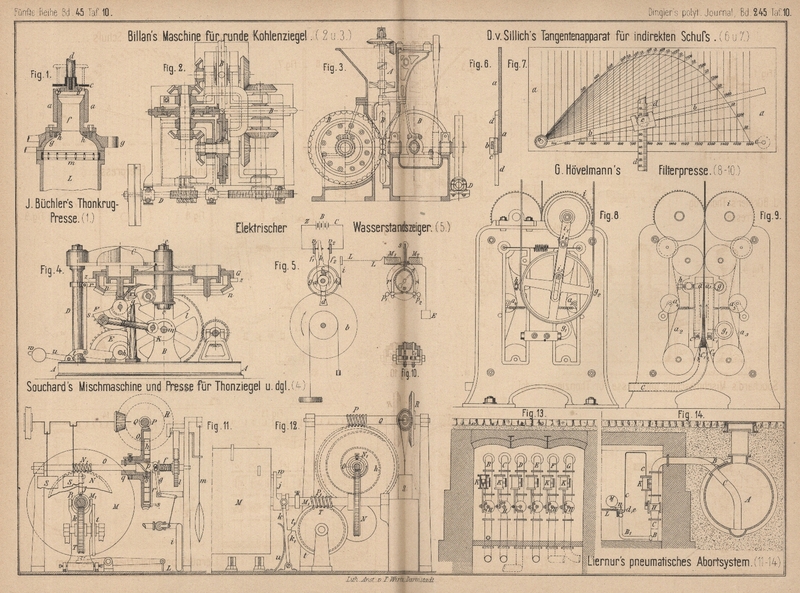