Titel: | Ueber die Herstellung der Sand-Gussformen mittels sogen. Formmaschinen; von Hermann Fischer. |
Autor: | Hermann Fischer |
Fundstelle: | Band 246, Jahrgang 1882, S. 49 |
Download: | XML |
Ueber die Herstellung der Sand-Guſsformen mittels
sogen. Formmaschinen; von Hermann Fischer.
Mit Abbildungen auf Tafel 2.
(Fortsetzung der Abhandlung S. 6 d.
Bd.)
Herm. Fischer, über Herstellung der Sandguſsformen.
So lange das Modell einfach gestaltet ist, läſst sich der nothwendige Anschluſs der
Formplatte verhältniſsmäſsig leicht erreichen; für reicher entwickelte
Grundriſsformen, z.B. Zahnräder, ist es nicht wohl möglich die Gestalt der
Formplattendurchbrechung freihändig genau genug herzustellen. Man macht dann die
Durchbrechung der guſseisernen Platte gröſser als das Modell und gestaltet die
Ränder so, daſs eine Metalllegirung, welche eingegossen wird, nachdem das Modell in
seine richtige Lage gebracht ist, an denselben genügende Anhaftungspunkte findet. So
ist ein genauer Schluſs zwischen Modell und Formplatte ziemlich billig zu schaffen.
Ist die Theilungsfläche des Modelles nicht eben, so muſs die Breite des
Legirungsringes gröſser als bei ebenen Theilungsflächen gewählt werden, um mittels
seiner Oberfläche die Theilungsfläche des Sandes zu gewinnen. Behufs Erzielung der
richtigen Gestalt dieser Theilungsfläche muſs natürlich während des Gieſsens des
Legirungsringes eine passende Form angelegt werden.
Weiter oben wurde im Allgemeinen hervorgehoben, daſs das Feststampfen des Sandes bei
der Handformerei verhältniſsmäſsig wenig Zeit beanspruche. Man sollte daraus
schlieſsen, daſs das Festigen des Sandes mittels mechanischer Mittel weniger häufig
versucht werden würde als die Ausführung anderer mehr Zeit beanspruchender Arbeiten.
Ich muſs jedoch das Gegentheil bestätigen.
Karmarsch erwähnt schon i. J. 1838 (Prechtl's technologische Encyklopädie, Bd. 9 S. 595)
die Benutzung einer schweren, auf dem Sande hin und her zu rollenden Kanonenkugel
zum Festigen des Sandes.
Sinnreich erscheint das an Stewart (Englisches Patent
vom 14. Juli 1846 [Stentz gibt a. a. O. irrthümlich das
Jahr 1847 an]) patentirte Verfahren der Röhrenformerei (vgl. 1847 104 * 245). Eine Blechröhre, welche concentrisch mit dem
kurzen cylindrischen Modell in den senkrecht aufgestellten Formkasten ragt, ist
unten mit schraubenförmig gestalteten Flügeln versehen. Indem nun diese Blechröhre,
während man Sand einwirft, gedreht wird, steigen die genannten Flügel auf den Sand,
drücken ihn zwischen Formkastenwand und Modell fest und heben gleichzeitig, dem
Fortschreiten der Kastenfüllung entsprechend, sowohl die Blechröhre, an welcher sie
befestigt sind, als auch das kurze Modell allmählich nach oben.
Macfarlane (Englisches Patent vom 26. Februar 1857,
vergleiche Practical Mechanics' Journal, November 1857
* S. 202) versieht das kurze, röhrenförmige Modell in der Nähe des oberen Randes
inwendig und auswendig mit solchen Flügeln, so daſs gleichzeitig Kern und Mantel in
der vorhin angegebenen Weise geformt werden. Sheriff
(Practical Mechanical Journal, April 1855 * S. 31, vgl. 1855 137 * 19 und in etwas anderer Art Zeitschrift des Vereins deutscher Ingenieure, 1864 * S. 681) benutzt die
Stewart'sche Formmethode mit der Abänderung, daſs
das Eindrücken des Sandes – statt mittels der Schraubenflügel – durch Rollen erfolgt
und das kurze Modell nicht allein in der von ihm gebildeten Form, sondern vor allem
längs einer in der Achse des Formkastens befindlichen festen Stange geführt wird.
Endlich verwendet D. Elder (Civil-Engineer and
Architects Journal, December 1855 S. 427, Zeitschrift des Vereins deutscher Ingenieure, 1863 S.
171, vgl. 1856 140 272) – neben dem kurzen, allmählich
nach oben bewegten Modell – eine dem Modell concentrische Stampfröhre, deren unterer
Rand geschlitzt ist, so daſs die von der Röhrenwand stehen gebliebenen Stifte
fingerartig in den Sand eingreifen. Die Stampfröhre wird durch einen sinnreichen
Mechanismus gehoben und gesenkt.
Dieses Elder'sche Verfahren ist auch in verschiedene
deutsche Röhrengieſsereien eingeführt worden, aber – meines Wissens – überall wieder
verlassen. Der Grundgedanke desselben – durch fingerartige Stifte bis in die tiefer
liegenden Sandschichten einzudringen, um diese zu festigen – ist aber neuerdings von
E. de Limon (*D. R. P. Nr. 10185 vom 6. Januar
1880, vgl. 1880 238 * 198, Verhandlungen, 1880 * S. 490) wieder aufgenommen, wahrscheinlich auch ohne
Erfolg.
Den hier kurz beschriebenen Aufstampfverfahren Stewart's,
Sheriff's und Elder's ist Anerkennung nicht zu
versagen. Sie erreichen – worauf entschieden Werth gelegt werden muſs – eine groſse
Sanddichte in unmittelbarer Nähe der Modelloberfläche. Ihre Auſsergebrauchsetzung
dürfte deshalb lediglich veranlaſst sein durch die geringe Zeitersparnis, welche sie
hervorbringen, gegenüber dem Aufwand an mechanischer Einrichtung und deren
Ausbesserungsarbeiten, welche sie bedingen. Ich kann mich daher betreffs des Kinniberg'schen Verfahrens (Englisches Patent vom 13.
November 1856, Practical Mechanics' Journal, Juli 1857
* S. 101), bei welchem die Festigung grundsätzlich falsch erfolgt, mit Anführung der
Quellen begnügen.
A. Newton (Englisches Patent vom 5. Oktober 1849, London Journal of Arts, August 1850 * S. 8, vgl. 1850
118 * 352) formt Röhren und andere Gegenstände in
folgender Weise: Jeder Formkasten ist nur an der Seite offen, in welcher die
Hohlräume ausgespart werden sollen; sie haben eine solche Gestalt (vgl. Fig.
11 und 12 Taf. 2),
daſs nach vollzogenem Einformen eine dünne Sandschicht möglichst gleichmäſsiger
Dicke den Formkasten auskleidet. Auf den leeren Formkasten A wird ein Rahmen B gestülpt, welcher den
muldenförmigen Raum so weit vergröſsert, daſs eine für das Formen genügende
Sandmenge im lockeren Zustande darin Platz hat. Derselbe wird alsdann unter den Trichter C geschoben – wobei der Schieber D selbstthätig zur Seite gerückt wird –, füllt sich aus
diesem mit Sand und wird alsdann in Bezug auf die Figur nach links unter das Modell
E gebracht, während der Schieber D die Trichteröffnung selbstthätig schlieſst. Das
Modell E wird nun mittels Krummzapfen und Lenkstange in
den Formkasten eingedrückt, festigt so den Sand und bewegt sich alsdann genau
senkrecht nach oben zurück.
White's Verfahren (Armengaud's
Génie industriell 1859 * S. 14, vgl. 1859 152 *
9) ist gewissermaſsen eine Copie des Newton'schen. Es
unterscheidet sich von diesem nur durch die Art der Kasten Verschiebung. Auch hier
erzielt man die gröſste Sanddichte in unmittelbarer Nähe der gebildeten
Formoberfläche. Schwierigkeiten dürften in so fern entstehen, als die richtige
Sandmenge in der angegebenen Weise nicht gewonnen werden kann; ist der Sand bei dem
Einfüllen locker, so fällt zu wenig ein und die Form wird nicht fest genug; ist er
dagegen wesentlich dichter, als er sein soll, so wird der Sand zu fest gepreſst. Es
kann sogar ein Bruch der Maschine herbeigeführt werden.
Dieser Gefahr wird durch J. Page und Robertson (Practical
Mechanics' Journal, April 1856 * S. 5, vgl. 1856 142 * 184. Polytechnisches Centralblatt, 1856
* S. 984) durch folgendes Verfahren einigermaſsen vorgebeugt: Zunächst wird der
Formkasten ganz mit Sand gefüllt, alsdann der Gestalt und Gröſse des Modelles
entsprechend eine gewisse Sandmenge ausgeschnitten – wozu theilweise recht
sinnreiche Mechanismen Verwendung finden – und nunmehr das Modell eingepreſst, sowie
nach vollzogener Pressung genau zurückgezogen. Das Verfahren ist zu umständlich, als
daſs es Vortheile im Ueberschuſs bieten könnte.
Mehr Anklang hat die bereits erwähnte Brown-Behn'sche
Formmaschine gefunden. Sie wurde namentlich durch Waltjen in Bezug auf die Construction der Maschinentheile für
Röhrenformerei verbessert (vgl. Prechtl's technologische
Encyklopädie, Supplementband 2 * S. 629. Polytechnisches Centralblatt, 1857 S. 1175); ihre grundsätzliche Anordnung
erhielt sie aber bereits i. J. 1854 durch Brown; sie
besteht in Folgendem. Die Formplatte A (Fig. 9 Taf.
2), aus der das Modell B in richtiger Höhe hervorragt
und welche genau passend in dem Formtisch D senkrecht
verschiebbar ist, befindet sich in tieferer Lage als die Oberfläche des Formtisches
D. Man trägt den Sand auf, streicht das
Ueberflüssige mittels einer Lehre ab und befestigt sodann den Formkasten E auf dem Formtisch. Hierauf werden Formplatte A und Modell B
gemeinschaftlich so weit gehoben, daſs die Oberfläche der Formplatte mit derjenigen
des Formtisches D abschneidet. Es erfolgt alsdann – wie
bereits beschrieben – zunächst das Zurückziehen des Modelles B, worauf auch die Formplatte nach unten bewegt und der Formkasten
abgehoben wird.
Die Festigung des Sandes erfolgt sonach bei dem Brown'schen Verfahren genau so wie bei dem älteren Newton'schen; ob die Einpressung des Modelles von oben nach unten oder von unten nach oben
stattfindet, ist für die Wirkung offenbar gleichgültig und hat nur Einfluſs auf die
Anordnung der Maschinentheile. Wichtig ist das oben bereits gewürdigte Zurückziehen
des Modelles, bevor die Formplatte zurückbewegt wird, indem man hiermit die
vollständige Sicherung der Sandkanten C gewinnt.
Howard (Englisches Patent vom 5. Februar 1856, vgl. Practical Mechanics' Journal, August 1857 * S. 124) hat
anscheinend die Gefahr erkannt, welche das Newton-Brown'sche Preſsverfahren in sich birgt, indem der zu pressende
Sand eine verschiedene Dichte hat. Derselbe verwendet deshalb oben und unten offene
Formkasten, setzt einen derselben auf die mit der Maschine verbundene Formplatte, in
deren Durchbrechung das Modell sich befindet, und stampft in gewöhnlicher Weise auf.
Hierauf wird das Modell etwas emporgedrückt, so daſs der Sand, welcher das Modell
berührt, noch mehr verdichtet wird, und dann das Modell in die alte Lage
zurückgezogen. – Was mit diesem Verfahren erreicht werden soll, ist nicht abzusehen;
wahrscheinlich hat man sich bald von der Nutzlosigkeit des Einpressens überzeugt und
in Folge dessen die ganze Einrichtung nur zum genauen Ausziehen des Modelles unter
Zurückhaltung des Sandes benutzt. So dürfte der früher erwähnte Irrthum Stentz's entstanden sein.
Jobson (Mechanics' Magazine, April 1859 * S. 218) wirft
den Sand in den oben offenen Formkasten, schiebt alsdann einen Deckel über denselben
und drückt das Modell, welches durch eine entsprechende Oeffnung des Formtisches
ragt, von unten in den Sand. Um nun eine zu groſse Pressung des Sandes zu verhüten,
läſst derselbe einen Spalt zwischen Modell und Rand der Formtischdurchbrechung frei,
durch welchen ein Theil des Sandes zu entschlüpfen vermag. – Dieses Verfahren kann
in der vorliegenden Ausführung nicht von Erfolg sein, da die Kanten der Sandform
nothwendig unrein ausfallen. Es macht einen günstigeren Eindruck in der
Ausführungsart W. Aikin und W.
Drummond's (*D. R. P. Nr. 5217 und 6479, Verhandlungen, 1880 * S. 188, vgl. 1878 229 *
209). Dieselben befolgen zunächst das Brown-Behn-Waltjen'sche Verfahren in Bezug auf das Pressen und
Zurückziehen der Modelle vollständig, eignen sich daneben aber den erwähnten Jobson'schen Vorschlag in der Weise an, daſs sie den
Deckel des Kastens mit Oeffnungen versehen und hierdurch Abfluſsöffnungen für den zu
stark gepreſsten Sand schaffen. So viel mir über den Nutzen dieser Durchbrechungen
bekannt geworden ist, steht derselbe lediglich auf dem Papiere, so daſs – wenn meine
diesbezüglichen Nachrichten richtig sind – thatsächlich die genannte Maschine nur
betreffs Anordnung der Maschinentheile von der oben näher besprochenen Brown'schen abweicht.
Ich komme nun zu einer Reihe neuerer deutscher Formmaschinen, bei welchen das
Ausziehen der Modelle lediglich genau senkrecht zur Formkastenfläche – Jahn, Lohse –, das Festigen des Sandes aber durch Druck auf der von den
Modellen abgewendeten Seite des Sandes erfolgt. Dem Alter nach reihen sich dieselben
wie folgt an einander: Wertheim (*D. R. P. Nr. 2733 vom
9. April 1878, Verhandlungen, 1880 * S. 184, Sebold und Neff (*D. R. P. Nr. 8390 vom 26. Juli 1879
und Nr. 9089 vom 15. August 1879, Verhandlungen, 1880 *
S. 481, vgl. 1880 236 * 19. 237 * 439. Englisches Patent 1879 Nr. 5327 und 1880 Nr. 5344), Gallas und Aufderheide
(Englisches Patent vom 29. December 1880 Nr. 5469, Iron, 1882 Bd. 19 * S. 158, Glaser's Annalen,
Februar 1882 * S. 95), Laiſsle (*D. R. P. Nr. 18734 vom
8. April 1881, vgl. 1882 243 * 456), W. Ugé (*D. R. P. Nr. 15570 vom 16. Januar 1881, vgl.
1882 243 * 285).
Die Werthheim'sche Maschine besteht aus einer
Preſsvorrichtung, welcher sich links und rechts Aushebevorrichtungen anschlieſsen.
Die Modellplatte befindet sich mit nach oben gerichteten Modellen auf einem Wagen
und zwar zunächst an der Stelle, an welcher das Ausziehen der Modelle stattfindet.
Hier wird ein Formkasten aufgesetzt, ein Rahmen hinzugefügt, um den Rauminhalt des
Kastens der Lockerheit des Sandes entsprechend zu vergröſsern (ebenso wie oben bei
Newton's Verfahren erwähnt), und das Ganze mit Sand
gefüllt. Man legt nunmehr ein Druckbrett auf, dessen Abmessungen der Länge und Weite
des Formkastens entsprechen und dessen Unterfläche annähernd das Spiegelbild der
Modellplatte ist, rollt mit Hilfe des Wagens den Formkasten unter die durch
Reibungsräder angetriebene Schraubenspindel in die Mitte der Maschine, preſst das
Druckbrett um ein gewisses Mais in den Kasten und fährt diesen nach Zurückziehung
der Preſsspindel auf den alten Platz zurück. Hierauf wird das Druckbrett und der
Füllrahmen entfernt, der Rücken des Formkastens – nach Umständen unter Zuhilfenahme
des Handstampfers – geebnet, mit einem Richtscheit abgestrichen und alsdann der
Kasten von der Modellplatte abgehoben. Zu diesem Zwecke hebt man mittels Handhebels
einen senkrecht gut geführten Körper, der oben in vier Stifte ausläuft, welche unter
die überstehenden Ränder des Formkastens greifen; das weitere Abheben und Umwenden
des Kastens erfolgt freihändig. An der entgegengesetzten Seite der Presse befindet
sich ein zweiter Arbeitsplatz mit Aushebevorrichtung, welche zur Herstellung der
anderen Formhälfte dient und zwar in gleicher Weise, wie soeben betreffs der ersten
Formhälfte beschrieben wurde.
Das wesentlich Neue dieses Werthheim'schen
Formverfahrens besteht in dem Pressen des Sandes mittels auf den Rücken des
Formkastens gelegter und zwar mit Relief versehener Druckplatte. Auf die Anpassung
dieses Reliefs an dasjenige der Modellplatte wird besonderer Werth gelegt; von ihr
wird eine gleichmäſsige Festigung des Sandes erwartet. Würde der Sand ein vollkommen
flüssiger Körper sein, sich dem Wasser ähnlich verhalten, so würde allerdings der
seitens der Druckplatte ausgeübte Druck sich überall hin gleichmäſsig vertheilen.
Man will aber, daſs die
Sandtheile möglichst schwer gegen einander sich verschieben, damit sie dem
ungleichmäſsigen Druck des flüssigen Metalles zu widerstehen vermögen, während des
Gieſsens ihre Gestalt nicht verändern. Daraus geht schon hervor, daſs von einem
gleichmäſsigen Verdichten des Sandes mittels des Werthheim'schen Verfahrens nicht die Rede sein kann. Ich mache jedoch noch
aufmerksam auf die Reibung des Sandes an den Kastenwänden, an den Scherwänden und in
sich selbst, um auf die Ursachen hinzuweisen, welche den Druck der Druckplatte nur
geschwächt und zwar sehr ungleichmäſsig geschwächt in die Nähe der Modelle gelangen
lassen. Je niedriger bezieh. dünner die Sandschicht ist, um so geringer fallen die
angezogenen Widerstände gegen die Verschiebung der Sandtheilchen aus, um so
regelmäſsiger erfolgt sonach die Verdichtung des Sandes, so daſs das Werthheim'sche Verfahren um so eher anwendbar ist, je
flacher die Modelle und Kasten sind.
Sebold und Neff benutzen das Werthheim'sche Preſsverfahren einschlieſslich der mit Relief versehenen
Druckplatte, fügen aber eine Neuerung hinzu, welche Blum
(Verhandlungen, 1880 S. 481) besonders hervorhebt. Sie füllen nämlich den
auf die Modellplatte gesetzten Kasten bis zum oberen Rand mit Sand, ebenso den auf
die Druckplatte gesetzten Füllrahmen, schieben über diesen einen dünnen Deckel,
kippen ihn auf den Formkasten und ziehen den Deckel heraus. Es ist somit der Raum
zwischen Modell und Druckplatte vollständig mit Sand gefüllt; man nimmt an, daſs
demzufolge das Zusammendrücken, durch das senkrechte Niedersteigen der Sandtheile
gleichförmig erfolge, übersieht dabei aber die Reibung des Sandes an den
Kastenwänden u.s.w. wie auch an der Oberflache der Modelle. In verhältniſsmäſsig
tiefen Zwischenräumen der Modelle wird in Folge der Reibungsverluste der Druck nur
sehr geschwächt ankommen. Sind solche vorhanden, so dürfte das ursprüngliche Werthheim'sche Verfahren den Vorzug verdienen, indem
dieses über den Vertiefungen mit denselben wachsend den gröſsten Druck erzeugt, also
ein genügender Theil desselben viel eher in die Tiefe zu dringen vermag wie bei der
Sebold und Neff'schen Maschine.
Zwei der oben angeführten Maschinen – jene von Gallas
und Aufderheide, sowie die Laiſsle'sche – benutzen die Druckplatte in der Werthheim'schen Weise, Ugé benutzt eine
gerade Druckplatte, wohl in richtiger Erkenntniſs der Thatsache, daſs das
vorliegende Sandfestigungsverfahren nur für flache Modelle möglich ist. Bei dieser
Gelegenheit erwähne ich noch einer englischen Röhrenformmaschine, nämlich der Cochrane'schen (Engineering, 1868 Bd. 6 * S. 317), welche ebenfalls Druckplatten auf die
von den Modellen abgewendete Sandfläche wirken läſst. Ein weiteres Eingehen auf
Einzelheiten dieser Maschine lohnt sich nicht.
Den erwähnten deutschen Maschinen muſs ich jedoch noch einige Worte widmen.
Früher wurden Mittel genannt, um der Gefahr einer zu groſsen Pressung vorzubeugen.
Sebold und Neff haben eine Anordnung gewählt,
welche anscheinend recht zweckmäſsig ist. Sie lassen nämlich während des Pressens
die Räder des die Modellplatte tragenden Wagens auf Schienenstücke sich stützen,
welche durch belastete Hebel getragen werden, so daſs sie niedersinken, sobald die
Pressung das beabsichtigte Maſs überschreitet. Gallas
und Aufderheide verwenden in gleichem Sinne Federn.
Schon die Sebold und Neff'sche Maschine ist
einigermaſsen zusammengesetzt, diejenige. Gallas und
Aufderheide's scheint aber das Maſs des Zulässigen
zu überschreiten; sie ist nicht allein sehr theuer in der Herstellung, sondern muſs
– wenn man bedenkt, daſs sie in der Formerei benutzt wird, nicht aber in einer
sauberen, Sandstaub freien Werkstatt – auch bedeutende Ausbesserungskosten
erfordern.
Eigenthümlich klingt die Begründung für die Nützlichkeit der Laiſsle'schen Maschine. Es wird nämlich behauptet, daſs bei den älteren
Maschinen dieselben Mechanismen gleichzeitig zum Pressen und Ausheben der Modelle
benutzt würden, in Folge dessen sie wegen der groſsen Abnutzung für letzteren Zweck
bald zu ungenau würden. Thatsächlich ist nun diese Behauptung der Werthheim'schen Maschine gegenüber, wie oben
beschrieben, falsch. Laiſsle kannte doch die Werthheim'sche Maschine, da derselbe das Formverfahren
derselben sich angeeignet hat.
Ugé's Maschine ist einfach und billig herzustellen,
weshalb sie trotz der ihr wie den übrigen anhaftenden grundsätzlichen Mängeln eine
gewisse Anwendungsfähigkeit besitzt.
Ueberblicken wir die Gesammtheit der verschiedenen mechanischen
Sandfestigungsverfahren, so müssen wir gestehen, daſs das Stewart'sche und Elder'sche Verfahren sowie
deren Gefolge grundsätzlich das richtigste treffen, nächst diesen das Newton'sche und namentlich Brown'sche als gut anzuerkennen ist, das Pressen des Sandrückens aber als
das mangelhafteste Verfahren bezeichnet werden muſs. Die erste dieser Gruppen ist so
gut wie vollständig verschwunden; die zweite findet für besondere Fälle Verwendung
und die dritte ist nur für flache Modelle brauchbar. Wenn die betreffenden Maschinen
trotzdem gröſsere Verbreitung finden, so geschieht dies nicht, weil sie auch die
Festigung des Sandes mechanisch vollziehen, sondern weil sie eine gute, die Form
schonende Modellaushebung in sich schlieſsen und manche Constructionsvortheile
besitzen.
In dem Sonderfalle, daſs die Theilungsfläche der Form durch eine ebene Endfläche des
Modelles gelegt werden kann, daſs also der eine Kasten als Formfläche nur eine mit
seinem Rande abschneidende Ebene erhält, ist die gegenseitige Lage der beiden
Formkasten gleichgültig. Sobald jedoch die Theilfläche der Form – einerlei, ob sie
eben oder gekrümmt ist – auch das Modell in zwei Theile zerlegt, ist alle Sorgfalt
darauf zu verwenden, daſs die beiden Formen genau richtig einander gegenüber zu liegen kommen. Dies
erfordert mühevolle Arbeit bei Herstellung der Modellplatten, aber auch Merkmittel,
um demnächst die beiden Formkasten rasch in die richtige Lage bringen zu können. Es
liegt nahe, hierfür die sogen. Schlieſsstifte bezieh. die zugehörigen Oesen zu
verwenden, was thatsächlich in der Regel geschieht. Alsdann muſs man aber verzichten
auf das vielerorts beliebte Zusammenkeilen der Kasten mittels in die hervorragenden
Enden der Schlieſsstifte eingetriebener Splinte, indem hierbei nothwendiger Weise
die Genauigkeit der Schlieſsstifte verloren gehen muſs.
Sebold und Neff (1880 237 *
439) und meines Wissens auch einige Andere benutzen für das genaue Einstellen der
Kasten besondere, an den Kastenrändern angebrachte und genau gebohrte Lappen, in
welche nur während des Zusammenlegens der Kasten genau passende Bolzen geschoben,
alsdann die Splinte in die Schlieſsstifte getrieben und hierauf die erwähnten Bolzen
wieder herausgezogen werden. Die Löcher dieser Lappen stehen natürlich im Einklang
mit Stiften, welche auf der Modellplatte angebracht sind. Zweifellos bleiben diese
nur zum Einstellen der Kasten zur Benutzung kommenden Löcher länger genau als die
Schlieſsstifte, welchen beim Hin- und Herschaffen der Kasten manche Gefahr droht.
Jedoch erfordert dieses Verfahren eine neue Arbeit, ja sogar eine besondere
Maschine, so daſs die Frage ist, ob seine Vortheile überwiegen. Die genaue
Herstellung und Instandhaltung der Kasten bezieh. der an ihnen befindlichen
Einstellungsmarken ist einigermaſsen kostspielig wegen der nöthigen groſsen Zahl der
Kasten. Man hat daher Auswege ersonnen, welche mit weniger Kasten auszukommen
gestatten.
Die sogen. Abschlag-Formkasten bieten in dieser Richtung das weitgehendste Mittel. Es
sind zwei Constructionen derselben bekannt, nämlich die von Gülpen, Lensing und v. Gimborn (* D. R. P.
Nr. 100 und Nr. 2486, Zeitschrift des Vereins deutscher
Ingenieure, 1878 * S. 33, vgl. 1878 229 * 243)
und die anscheinend ältere eines Ungenannten (vgl. 1880 235 * 21). Erstere gestalten ihre Formkasten so, daſs sie im
zusammengelegten Zustande eine abgestumpfte Pyramide bezieh. einen abgestumpften
Kegel bilden, legen auf die kleinere obere Fläche des Oberkastens ein die Oeffnung
desselben ausfüllendes Brett, während die gröſsere untere Fläche des Unterkastens
auf der Hüttensohle ruht, und heben nun, indem sie geeignet gestaltete Hebel auf das
genannte Brett stützen, beide Kasten empor, während die Form an ihrem Orte bleibt.
Die zweite Construction scheint weniger zweckmäſsig zu sein. Jeder Kasten ist –
ähnlich wie viele Formen für verzierte Ziegel – an zwei gegenüber liegenden Ecken
nur durch lösbare Schlösser vereinigt. Nachdem die eingeformten und zusammengelegten
Kasten auf die Hüttensohle gestellt sind, löst man die Schlösser und zieht die
Kastentheile nach links bezieh. rechts von dem Sande ab. In der Regel wird man dem
Sand eine seitliche Stütze durch angestampften Sand gewähren müssen * dies ist bei
der ersten Construction erleichtert, indem sie gestattet, die Formen ziemlich dicht an einander zu
rücken.
Ernst Paul (*D. R. P. Nr. 4814 vom 10. September 1878.
Verhandlungen, 1880 * S. 192) geht weniger weit.
Derselbe benutzt zur Aufnahme der Sandformen schlichte Kasten, welche so lange in
mit Markstiften bezieh. Oesen versehene Rahmen eingeklemmt bleiben, wie es das
Formen und genaue Zusammenlegen der Kasten nöthig macht. Hier ist das nachherige
seitliche Stützen der Formen entbehrlich; freilich wird das Hantiren mit dem durch
die Rahmen beschwerten Kasten anstrengender.
Die Formmaschinen bedingen den Verbrauch gröſserer Sandmengen an einem Orte. Es liegt
nahe, dem entsprechend Anordnungen zu treffen, um den Sand von dem Behälter
desselben bequem in den Formkasten zu bringen. In dieser Beziehung sind
erwähnenswerth die Einrichtungen Aikin und Drummond's,
Sebold und Neff's, Gallas und Aufderheide's sowie Laiſsle's, welche in den
früher genannten Quellen beschrieben werden. Hervorheben will ich, daſs Gallas und Aufderheide
zunächst freien Sand mit Hilfe einer besonderen Vorrichtung auf die Modellplatte
sieben und dann aus einem zweiten Behälter den Kasten füllen.
An die vorliegende Erörterung müſste sich naturgemäſs die Beschreibung und
Besprechung derjenigen Verfahren anreihen, welche zur Herstellung der Kerne dienen.
Auf diesem Gebiete findet sich jedoch – soweit das Ausziehen gestampfter Kerne aus
den Kernkasten mittels den vorhin besprochenen Formmaschinen ähnlicher Vorrichtungen
nicht in Frage kommt – so gut wie nichts Erwähnenswerthes. Ich verzichte deshalb auf
ein weiteres Eingehen in diesen Gegenstand.
Ergiebiger ist die Verfolgung derjenigen Bestrebungen, welche dadurch, daſs sie die
Bewegung der Formkasten für die einzelnen Arbeiten des Formens, Gieſsens und
Ausräumens erleichtern, Ersparungen erreichen wollen. Stentz führt in seiner Arbeit (a. a. O. * S. 344) einige bemerkenswerthe
Beispiele für die Formerei und Gieſserei im Allgemeinen an, bespricht dann (S. 353)
das Formen der Röhren ausführlich, unter Beigabe guter Abbildungen, bei welcher
Gelegenheit zu Tage tritt, daſs jede einzelne Arbeit an einem besondern Orte
ausgeführt wird, indem die Kasten mit Hilfe geeigneter Wagen auf Schienengeleisen
die Hütte durchwandern. Ich habe in mehreren Hütten derartige Anlagen in Betrieb
gesehen, bin aber bald ernüchtert worden, als ich versuchte, eine vergleichende
Kostenrechnung dieses Spazierenführens der theils gewaltigen, bis 4m hohen Formkästen mit dem anderen Verfahren
anzustellen, bei welchen die Formkästen ihren Ort nicht verlassen. Als Fahnenträger
dieses letzteren z. Z. am meisten beliebten Arbeitsverfahrens wird die
Eisengieſserei zu Frouard bei Nancy genannt, über welche Petzeld einen kurzen Bericht in der Zeitschrift
für Berg-, Hütten- und Salinenwesen, 1867 S. 237 veröffentlicht. Eine
Beschreibung mit Abbildungen, welche nicht ganz mit dem Petzeld'schen Berichte übereinstimmen, findet man in Ledebur's Werk: Die Verarbeitung der Metalle auf
mechanischem Wege (Braunschweig 1879). Hier begibt sich der Former behufs
Aufstampfung des Mantels um ein eisernes Modell, die Wärmequelle (jetzt wohl
meistens ein kleiner Ofen) behufs Austrocknung der Form, der Trichter zum Schwärzen
der Form, der Kern und schlieſslich die Gieſspfanne zum Formkasten, dessen eine
Hälfte fest ist, während die andere Hälfte nur so weit zur Seite geschoben wird, als
das Ausziehen der gegossenen Röhre und das Aasleeren des Kastens es nöthig macht. In
sehr hübscher Ausführung findet man dieses Verfahren in der Stühlen'schen Eisengieſserei in Kalk bei Deutz.
Gewissermaſsen ein Zwischenglied zwischen den beiden hier genannten Extremen bildet
ein Drehformgerüst, welches in der Hannover'schen Eisengieſserei seit einer Reihe von Jahren in mehreren
Exemplaren für 80 bis 200mm weite Röhren im
Gebrauch ist, neben der für das Formen und Gieſsen der gröſseren Röhren nach dem
Vorbilde der Frouard'schen Eisengieſserei angeordneten Einrichtung. Ich verdanke dem
Constructeur, technischen Direktor Hammerstein der
Hannover'schen Eisengieſserei, die unter Fig. 13 und
14 Taf. 2 angefügten Abbildungen, welche ich veröffentliche, weil ich
annehme, daſs der Grundgedanke der Anordnung auch für manche andere Guſswaare
Anwendung finden kann.
Zu einem solchen Drehformgerüst gehören 8 Formkasten A,
welche an einem auf Rollen und um die Spindel C
drehbaren Körper B befestigt sind. Die auſsen liegenden
Hälften der Formkasten A sind mit den an B unmittelbar befestigten Hälften einerseits durch
Gelenke, andererseits durch Schlieſskeile verbunden, so daſs erstere ohne
Schwierigkeit zurückgeklappt werden können; die mit B
verbundene Bühne E ist mit entsprechenden Ausschnitten
versehen. Die Bühne E wird durch einen Zahnkranz
umrahmt, welcher mit Hilfe des Vorgeleges F die Drehung
der Formen nebst Zubehör gestattet. Man formt nun der Reihe nach die Mäntel in die
Kasten (die einfache Winde J dient zum Ausziehen der
Modelle), hängt je einen kleinen Trockenofen unter die Formen u.s.w., setzt unten
die besonders geformten Muffenformen an, senkt die Kerne ein – mit Hilfe einer Winde
ähnlich wie J – und gieſst dann der Reihe nach, zu
welchem Zwecke die Gieſspfanne G an einer kleinen,
mittels der Hand zu bedienenden Winde H hängt. Das
Formgerüst läſst sich sehr leicht drehen und augenscheinlich vortheilhaft
verwenden.
Die Ersparungen an Former- bezieh. Arbeitslöhnen, welche durch die bisher
besprochenen Maschinen bezieh. Einrichtungen gegenüber der Handformerei gemacht
werden, sind meistens sehr bedeutend, theils dadurch, daſs der einzelne Arbeiter
viel mehr zu leisten vermag, theils dadurch, daſs man billigere Arbeiter verwenden
kann und trotzdem mindestens ebenso gute Waare erhält als durch den theureren, mit
mangelhaften Werkzeugen ausgerüsteten Arbeiter. Diesen Ersparungen stehen aber die
sehr hohen Einrichtungskosten, die bedeutenden Kosten für Anfertigung der Modelle und die nicht
geringen Ausbesserungskosten der Maschinen gegenüber. Können diese auf zahlreiche
Arbeitstücke vertheilt werden, hat man bestimmte Stücke in groſser Menge zu liefern,
so ist der auf das einzelne Guſsstück entfallende Betrag genügend klein, um von den
oben genannten Ersparungen überwogen zu werden; ist dies nicht der Fall, so ist es
natürlich falsch, sich dieser Formmaschinen bezieh. Form- und Arbeitsverfahren zu
bedienen. Die Beschaffungs- und Unterhaltungskosten der verschiedenen Maschinen und
Einrichtungen sind sehr verschieden, so daſs die Frage der Rentabilität derselben
gewissermaſsen für jede derselben gestellt werden muſs: das eine ist oft noch mit
groſsem Vortheile zu verwenden, während das andere schon Verluste bringen würde.
(Schluß folgt.)
Tafeln
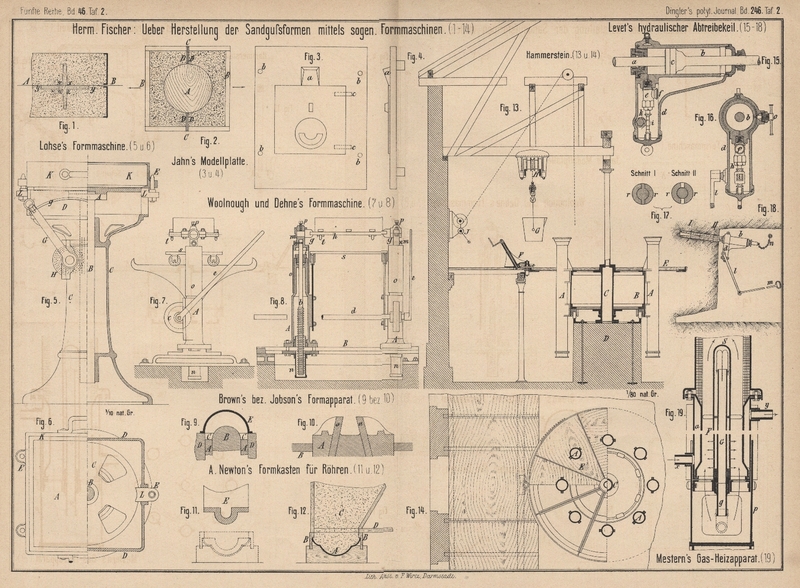