Titel: | Ueber Papierfässer und deren Herstellung. |
Autor: | G. R. |
Fundstelle: | Band 252, Jahrgang 1884, S. 504 |
Download: | XML |
Ueber Papierfässer und deren
Herstellung.
Patentklasse 54. Mit Abbildungen auf Tafel 38.
Ueber Papierfässer und deren Herstellung.
Vor den Fässern aus Holz haben die Papierfässer die Vorzüge, daſs sie leichter und
fester sind, also nicht so leicht zusammenfallen und zudem billiger hergestellt
werden können; diese Vorzüge machen sich besonders geltend, wenn das Faſs als
Transportmittel für pulverige, teigige und dickflüssige Waaren dient. Dabei können
die Papierfässer je nach dem Zwecke, dem sie dienen sollen, passender und handlicher
hergestellt werden, als dies bei Holzfässern je der Fall ist.
Die Papierfässer werden entweder aus über einander geleimten Papier- oder
Pappschichten, oder direkt aus Papiermasse hergestellt und können ebenso wohl eine
mehr oder weniger gewölbte, als auch eine cylindrische oder einseitig verjüngte Form
erhalten.
Papierfässer von cylindrischer Form aus über einander
geleimten Pappdeckelblättern werden von Eugen
Ritter in Ehrenfeld bei Cöln (* D. R. P. Nr. 3958 vom 27. Juni 1878) hergestellt. Die
gebräuchlichste Einrichtung eines solchen Fasses zeigt Fig. 1 Taf.
38. Es ist e der durch Runden einer Papptafel und
Verbinden der Enden derselben erhaltene Rumpf, auf den zum Schütze seiner Ränder die
äuſseren Kopfreifen b von Holz, Eisen o. dgl.
aufgezogen werden. Der Boden a, ebenfalls aus Pappe
oder aus Holz, wird zwischen den beiden inneren Reifen c und d gehalten.
Zur Herstellung der dicken Papptafeln werden eine je nach der gewünschten Stärke bestimmte
Anzahl in gleiche Gröſse geschnittener und auf einer Maschine gleichzeitig auf
beiden Seiten mit dem Klebemittel oder Cemente bestrichener Pappdeckelblätter auf
einander gelegt, wobei das oberste und unterste Blatt auf der äuſseren Seite nicht
bestrichen wird. Mehrere solcher Lagen (gewöhnlich 1000k auf einmal) kommen dann in eine Presse, in welcher sie fest
zusammengedrückt werden, damit der Klebstoff tiefer in die Pappdeckelblätter
eindringt und deren Verbindung eine möglichst dichte wird.
Aus der Presse kommen die durch die unbestrichen gebliebenen Seiten leicht zu
trennenden Papptafeln zum Trocknen in eine Trockenkammer, welche in Fig. 3 Taf.
38 im Durchschnitte skizzirt ist, wobei die Papptafeln vollständig eben bleiben
müssen, sich also weder verziehen, noch in einzelne Lagen loslösen dürfen, um jede
Blasenbildung zu verhüten. Die Papptafeln müssen daher während des Trocknens von
beiden Seiten zusammengehalten werden, zu welchem Zwecke die Trockenkammer die
nachfolgend beschriebene Einrichtung erhält. Ein an einer Stirnseite zugängiger Raum
C mit Doppelwandungen, deren Zwischenräume mit
einem schlechten Wärmeleiter ausgefüllt sind, wird durch einen darunter befindlichen
Ofen A mit den Rauchabzugsrohren b erwärmt* an Stelle dieser direkten Heizung kann auch
eine Dampfheizung treten. Der Boden B des Raumes ist
nur auf einer Hälfte bei S durchbrochen, um der warmen
Luft eine bestimmte Strömung zu geben, welche durch eine in dem Abzugskanale L liegende Klappe regulirt werden kann. An den Seiten
wänden des Raumes sind Knaggen e angebracht, in welche
die Riegel H gelegt werden. Auf diese Riegel H kommen die Papptafeln zu stehen, welche durch die in
Fig. 2 besonders dargestellten Holzrahmen von einander getrennt werden.
Indem die Latten m dieser Rahmen die Papptafeln mit
ihrer schmalen Seite berühren, erlauben sie, da auch die Randleisten n schwächer als die Latten m sind, eine allseitige Berührung der warmen Luft mit den Papptafeln. Wenn
in der ganzen Breite abwechselnd Papptafeln und Rahmen eingelegt sind, wird zuletzt
noch ein Brett eingeschoben und darauf durch die in der Wand angebrachten
Schraubenspindeln s der ganze Pack Papptafeln und
Rahmen festgepreſst. Auf diese Weise werden die Papptafeln während des ganzen
Verlaufes der Trocknung gehalten und können während derselben erforderlichen Falles
die Schrauben s noch nachgezogen werden.
Die aus der Trockenkammer genommenen trockenen Papptafeln sind vollkommen eben und
gerade; dieselben werden nun wasserdicht gemacht und den Kanten, wo sich beim
fertigen Rumpfe die Reifen anlegen, wird durch Eintauchen in eine geeignete
Flüssigkeit eine besondere Härte und Steifheit gegeben. Auf einer Maschine werden
vorher die Papptafeln gerade geschnitten und ihre Kanten, welche später über
einander zu liegen kommen, abgeschrägt. Das Runden der Papptafeln und das Zusammenleimen der
abgeschrägten Kanten unter Anwendung eines besonderen Cementes geschieht auf einer
Maschine, über deren Construction die Patentschrift jedoch nichts angibt. Es ist nur
eine in Fig. 4 Taf.
38 wiedergegebene Zwinge beschrieben, mit deren Hilfe das Zusammenleimen auf der
Maschine erfolgt. Zwei hölzerne Schienen a decken die
Leimfuge des Faſsrumpfes von innen und auſsen und werden durch die eisernen Klammern
c von jeder Kopfseite her fest zusammengezogen. Die
gleichzeitig mit umfaſsten Reifen b werden an ihren
Enden h mit Holzschrauben und kleinen Metallklammern
zusammengehalten.
Das Biegen und Zusammenleimen des Faſsrumpfes soll auf der Maschine sehr schnell
gehen und je nach der Faſsgröſse 1 bis 3 Minuten dauern, so daſs 3 Arbeiter in 10
Stunden im Mittel 300 bis 500 Faſsrümpfe zu leimen vermögen. Mit den Zwingen bleiben
die Rümpfe 5 Stunden liegen, in welcher Zeit der Leim oder Cement der Fuge
vollkommen getrocknet ist. Auch das Einbringen der Innenreifen in den Faſsrumpf soll
nach der Patentschrift auf einer Maschine erfolgen, wobei gleichzeitig die Böden
eingesetzt werden.
Die auf diese Weise erzeugten Papierfässer können anstatt cylindrisch ebenso gut auch
in Form eines abgestumpften Kegels erzeugt werden, so daſs sie für den Versand in
einander geschoben werden können, wobei dann die Böden besonders zu verpacken
sind.
Für manche Zwecke wird der Faſsrumpf innen oder auſsen oder beiderseits mit dünnen
Holzfurnüren belegt; auch können solche zwischen Papptafeln gelegt werden. So stellt
Eng. Richter Versand- und Aufbewahrungsgefäſse für
Pulver o. dgl. (* D. R. P. Kl. 81 Nr. 8907 vom 1.
Mai 1879) her durch Umgeben eines cylindrischen papiernen Rumpfes mit einer
metallenen Hülle, auf welche die Reifen oder wieder ein Papierrumpf gezogen werden.
Die Füllung der Fässer erfolgt vor der Fertigstellung oder durch in einem Boden
angebrachte Verschraubungen.
Im Zusatzpatente Nr. 9036 vom 19. September 1879 sind Papierfässer mit Doppelwandung
angegeben. Auf einen fertigen Rumpf e (Fig. 5 bis
8 Taf. 38) wird eine zweite Papptafel c
gewickelt, auf welche erst die Reifen b kommen. Auf den
inneren Faſsrumpf e legt sich dann der Boden a. In Fig. 5 wird
der Deckel a durch ein Leistenkreuz g gehalten. In Fig. 6 ist
der Deckel a theilbar, so daſs derselbe nach seiner
Einpressung eine sehr feste Lage zwischen dem Faſskörper e und einem eingesetzten Ringe d erhält. In
Fig. 7 und 8 besteht
der Deckel aus drei Lagen. Die innere Lage a wird
gewöhnlich mit dem inneren Rumpfe e1 verleimt; die weiter darüber gelegten Böden a1 werden entweder
durch einen Innenreif d (vgl. Fig. 7),
oder durch einen Winkeleisenring w (vgl. Fig.
8), welcher gleichzeitig den Auſsenreifen bildet, gehalten.
Weitere Anordnungen sind durch das zweite Zusatzpatent * Nr. 10146 vom 23. Januar
1880 geschützt. Bei dem in Fig. 9 Taf.
38 dargestellten Verschlusse kommt auf den Innenreifen c ein
Papierboden a zu liegen, oder wird damit verkittet,
über welchen der starke Holzboden a1 eingesetzt wird. Dabei kann der Papierboden a eine Füll- und Entleerungsöffnung o erhalten, welche durch eine aufgelegte Papierscheibe
t verschlossen wird. In Fig. 10 ist
ein Papierfaſs zur Aufnahme eines Gefäſses k aus Glas,
Thon, oder Metall gezeichnet. Der Zwischenraum zwischen Gefäſs und Faſs wird in den
Ecken mit Ringen r aus elastischem Material ausgefüllt,
so daſs das Gefäſs auf diesen Polsterstreifen vollkommen sicher ruht. In Fig.
11 ist der Verschluſs des Papierfasses durch Auftreiben eines conischen
Reifens h bewirkt. In den inneren Verschluſsreifen d ist mit einem Falze der Boden a eingelassen, wodurch derselbe einen besseren Halt findet und auch die
Dichtung eine vollkommenere wird. In Fig. 12 ist
ein Verschluſs mit Doppelboden und einer besonderen zwischen den abgeschrägten
Rändern der Böden a, a1
liegenden Abdichtungsschnur s dargestellt.
Auch für die Beförderung von Eiern oder Früchten, welche keinen Druck erleiden dürfen, hat Richter geeignete Papierfässer erdacht (vgl. * D. R. P.
Nr. 3959 vom 27. Juni 1878). In der Achse des Fasses befindet sich eine mit den
Böden verschraubte Stange, auf welche Papierscheiben gesteckt werden. In diese sind
dann ausgezackte Löcher eingeschnitten, in welche die Eier o. dgl. zu liegen
kommen.
Papierfässer von gebauchter Form aus über einander gewickelten Rollenpapieren werden nach dem Verfahren
von J. H. Darlington und Ch. E.
Sedore in New York (Erl. * D. R. P. Nr. 8743 vom 14. August 1879) in der
Weise angefertigt, daſs zuerst ein Cylinder aus Papier hergestellt, derselbe dann in
die Fig. 13 Taf. 38 ersichtliche Form gebracht und gleichzeitig getrocknet
wird, worauf die Enden des erhaltenen Rumpfes zum Einbringen der Faſsböden mit einer
Rinne versehen werden, welche drei Arbeiten auf besonderen Maschinen erfolgen.
Die Maschine zum Wickeln des Papiercylinders zeigt Fig. 14
Taf. 38 und die Wickeltrommel B derselben allein Fig.
15. Von der in die Maschine eingehängten und durch die Leiste S gebremsten groſsen Papierrolle J geht das Papier in dem Leimtroge E unter einer der ungleichen Spannung des Papieres
wegen beweglich gemachten Walze e zu einem Paare
Druckwalzen c, d und wird hinter diesen auf einer
Trommel B in gewünschter Stärke aufgewickelt. Das in
dem Troge E von dem Papiere aufgenommene Klebemittel
wird zum gröſsten Theile durch stellbare Schienen a und
b abgestrichen und der noch überschüssige
Klebestoff von den Druckwalzen c, d zurückgehalten. Der
Bremshebel g ist mit einem Bogen s verbunden, von welchem eine Kette k über Rollen nach dem vorderen Ende der Maschine
läuft, so daſs von dort aus die Bremse gehandhabt werden kann. Die Maschine ist noch
mit einer selbstthätigen Ausrückvorrichtung versehen, welche nach einer bestimmten
Anzahl Trommelumdrehungen, wenn also die aufgewickelte Papierschicht die gewünschte Stärke erlangt
hat, zur Wirkung kommt. Um den Papiercylinder leicht von der Trommel abnehmen zu
können, wird dieselbe dann verkleinert. Zu diesem Zwecke ist der Trommelmantel aus
Leisten L (Fig. 15)
gebildet, welche durch die Gelenkstangen G mit der
Trommelachse T verbunden sind. Die Leisten stoſsen
jedoch nicht alle radial zusammen, vielmehr sind einzelne parallel zu ihrem
Mittelradius zusammengepaſst; diese können also zuerst nach der Trommelachse zu
bewegt werden, worauf erst die übrigen Leisten nachfolgen können. Es wird auf diese
Weise eine vollkommen geschlossene Oberfläche der Trommel auch bei deren gröſster
Erweiterung erzielt. Die ersteren Leisten hängen mit den Gelenkstangen d an einer Krone K, welche
durch das Handrad D auf der mit Gewinde versehenen
Büchse C verschoben werden kann; die letzteren Leisten
sind ähnlich durch Gelenkstangen c mit der Büchse C verbunden, welche ihrerseits durch das Handrad H auf der mit Gewinde versehenen Trommelachse
verschiebbar ist. Durch Drehung der Handräder können also nach einander beide Arten
Leisten parallel nach der Trommelachse zu bewegt werden, worauf der noch nasse
Papiercylinder leicht abzuziehen ist. Derselbe kommt nun in die in Fig. 16
Taf. 38 dargestellte hydraulische Presse.
Die den Papiercylinder aufnehmende Form besteht aus zwei Theilen J und J1, von denen der untere gegen den oberen gepreſst
und dann festgestellt wird. Dies geschieht durch die Keile L (Fig. 17),
welche durch ein mittels eines Hebels M bewegtes
Zahnrad N alle gleichzeitig in Löcher der Säulen A der Presse eingeschoben werden. Damit das Faſs an der
Fuge der beiden Formtheile keine Naht bekommt, wird dort ein besonderer Schluſsring
J2 eingelegt (vgl.
Fig. 18). Die beiden Formhälften sind mit Höhlungen für Dampfheizung
versehen. In die Ausbauchung wird der feuchte Papiercylinder unter Benutzung eines
dehnbaren Sackes aus Gummi hineingepreſst, in ähnlicher Weise wie die Formgebung der
Strohhüte u. dgl. erfolgt. Der Sack ist an der oberen Preſsformplatte befestigt und
reicht in denselben hinein ein Block, welcher den Innenraum so weit ausfüllt, daſs
es nur einer sehr geringen Wassermenge bedarf, um den Sack auszudehnen. Unter dem
starken hydraulischen Drucke bleibt der Gummisack, bis der ausgebauchte
Papiercylinder vollkommen trocken ist, was zuweilen schon in 5 Minuten erreicht
ist.
Die Maschine zum Kimmen der Ränder des Faſsrumpfes ist in Fig. 19 und
20 Taf. 38 skizzirt. Eine Rolle R mit einer
Stahlscheibe wird in dem von einem Ringe x gehaltenen
Faſsrumpfe herumgedreht, wobei, neben dem Eindrücken der Kimme durch die
Stahlscheibe zur Aufnahme des Bodens, durch die conische Form der Rollen der Rand
etwas zur leichten Einbringung des Bodens erweitert wird, wie dies in Fig.
13 bei m punktirt angedeutet ist. Die Rolle
R lagert in einem Bügel n, welcher durch ein Gelenkstück p mit der
stehenden Spindel o
verbunden ist; dasselbe
ist der Fall mit den zwei kleinen Rollen R1. Alle drei Rollen sitzen auf dem Theile T, welcher durch ein Kegelräderpaar S in Umdrehung versetzt wird. Die Spindel o stützt sich in dem Spurlager eines Hebels Q, welcher durch den Tritthebel O mit der Rolle L gehalten wird. Wenn der
Hebel O nieder getreten und somit die Spindel o gehoben wird, gehen vermöge der Kniehebelwirkung der
Gelenkstücke p die 3 Rollen R und R1 aus
einander, die letzteren finden ihre Anlage an dem Ringe z und drücken die erstere fest gegen den Faſsrand. Die Feder F bewirkt den Rückgang der Rollen und die Stellschraube
B begrenzt die Tiefe des Eindrückens der Rolle R.
Sind beide Faſsränder derart vorgerichtet, so werden die Böden n (Fig. 13)
eingedrückt und dann durch Auftreiben der Auſsenreifen E die Ränder wieder zusammengezogen; gleichzeitig wird der Innenreifen o eingesetzt, welcher bis an die Kimme reicht und den
Halt des Bodens noch sichert.
Direkt aus Papier auf der Papiermaschine gewickelte
Papierfässer sollen nach H. A. Johnson in Medina, N. Y.
(Nordamerikanisches Patent Nr. 258071, vgl. Papierzeitung, 1883 S. 1244) mittels der in Fig. 25
Taf. 38 gezeichneten Wickelvorrichtung in folgender Weise hergestellt werden. Der in
einem Stoffkasten D laufende Siebcylinder C gibt die aufgenommene Papierschicht an die mit Filz
bezogene untere Fläche der Scheibe B ab. Durch diese um
den Zapfen c drehbare Scheibe B wird der Siebcylinder C in Bewegung gesetzt
und die anhaftende Papierschicht zu der conischen Wickelwalze E getragen, welche gleichzeitig durch die Scheibe B angetrieben wird und die Papierschicht aufnimmt. An
einer um den Zapfen f drehbaren Scheibe sitzen zwei
solche Wickelwalzen E; hat nun die Schicht auf der
oberen Walze die gewünschte Stärke erlangt, so wird das Papier auf der Scheibe B durchgeschnitten und die andere Wickelwalze nach oben
zur Aufnahme des Papieres gedreht. Der von der ersteren Walze E abgezogene etwas conische Papierschlauch wird nun auf
vorher beschriebene Weise weiter behandelt.
Direkt auf der Papiermaschine werden auch Papierfässer nach dem Vorschlage von N. de Wolff in Christiansthal bei Hadersleben (Erl. *
D. R. P. Nr. 4751 vom 7. September 1878) hergestellt. Ein Hohlcylinder aus Blech,
Porzellan, Glas o. dgl. wird auf einer Cylindermaschine mit Stoff aus Stroh, Torf,
Holz, Lumpen u.a. überzogen, indem die vom Cylindersiebe aufgenommene Stoffschicht
sich gleich auf den Cylinder wickelt. Auf letzterem wird dieselbe dann getrocknet
und so ein Papierfaſs erhalten, welches durch das darin bleibende Gefäſs für jeden
aufzunehmenden Inhalt entsprechend widerstandsfähig ist, während durch die umgebende
Stoffschicht dieses Gefäſs selbst vor Beschädigungen geschützt wird. Fig. 24
Taf. 38 zeigt ein solches Papierfaſs, bei welchem das innere Gefäſs aus Blech ist.
Der innere Blechboden b ist eingelöthet und am oberen
Rande hat das Blechgefäſs eine Wulst w, auf welche sich der Deckel d legt, welcher, wie auch der Boden, aus einer inneren
Blech- und einer äuſseren Holzscheibe zusammengesetzt ist. Die Ränder werden noch
durch aufgenagelte Reifen r geschützt.
Von G. W.
Laraway in Hartford, Nordamerika (*
D. R. P. Nr. 20132 vom 18. Januar 1882) ist eine
Presse angegeben, um auch die bisher aus Holz oder über einander geleimtem Papier
bestehenden Faſsböden aus Papierstoff herzustellen. Der
Faſsböden b (Fig. 22
Taf. 38) wird mit verstärktem Rande c gefertigt und
gibt daher eine gröſsere Auflage, also auch eine bessere Dichtung an dem Faſsrumpfe.
Der Boden legt sich auf den bei d abgesetzten Faſsrumpf
a (Fig. 22)
und kann auch mit durch den Auſsenreifen r hindurch
getriebenen Nägeln gehalten werden. Während bisher auch Faſsböden mit umgelegtem
Rande hergestellt wurden, indem die noch feuchten über einander geleimten
Papierschichten in einer runden Form gepreſst wurden, wobei jedoch an den Rändern
oft Brüche vorkamen, wird hier der Faſsböden in einer entsprechenden Form direkt aus
Papiermasse gepreſst.
Die erforderliche Presse zeigt Fig. 21,
die benutzte Form allein Fig. 23.
Der Preſskolben e wird von dem Excenter h mittels Stange g und
Kniehebel d auf und nieder bewegt. Wenn sich der Kolben
in seiner tiefsten Stellung befindet, kann durch die Kanäle j die Papiermasse zutreten. Ueber dem Kolben e wird auf einer Bahn n die Form
eingeschoben, welche sich gegen das Querhaupt f der
Presse legt. Der Kolben ist hohl und auf seiner oberen Fläche mit kleinen Löchern
finden Ablauf des Wassers versehen. Die in Fig. 23
dargestellte Form setzt sich zusammen aus einer runden Platte und einem sie
umgebenden Ringe, welcher aus 4 Theilen besteht, die auf den durch die Gelenke l und die Klammer m
zusammengehaltenen Stücken k und k1 befestigt sind. Für
den Austritt des Wassers hat die runde Formplatte, der Ring und die obere
Kolbenfläche folgende Einrichtung erhalten: Die innere Wand bildet ein feines Sieb
p (Fig. 23),
unter welchem ein wellenförmiges Blech liegt, das mit gröſseren Löchern versehen
ist.
Wenn ein Boden dicht genug gepreſst ist, wird die Form aus der Presse gezogen, der
viertheilige Ring derselben geöffnet, worauf der fertige Boden leicht herausgenommen
werden kann.
G. R.
Tafeln
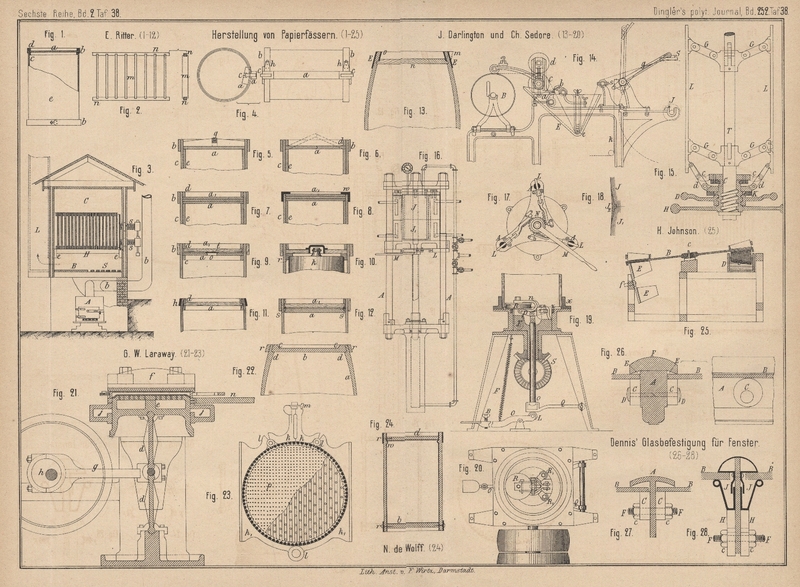