Titel: | Ueber Neuerungen im Eisenhüttenwesen. |
Fundstelle: | Band 253, Jahrgang 1884, S. 117 |
Download: | XML |
Ueber Neuerungen im Eisenhüttenwesen.
(Patentklasse 18. Fortsetzung des Berichtes Bd.
252 S. 243.)
Mit Abbildungen im Texte und auf Tafel 10.
Ueber Neuerungen im Eisenhüttenwesen.
Flammöfen. Die Siemens'sche Regenerativfeuerung will J.
Henderson bei Puddel-, Schweiſs- und
Schmelzöfen durch folgende nach dem Engineering and
Mining Journal, 1883 Bd. 36 S. 285 beschriebene Einrichtung ersetzen. Möglichst nahe an dem
Flammofen C (Fig. 1 und
2 Taf. 10) mit ebenem Drehherde V steht der
Generator A. Die durch den Trichter a aufgegebene Kohle gelangt zuerst in einen eisernen
Cylinder r und wird hier entgast; die Gase durchdringen
die Kohle nach unten und gelangen mit den Generatorgasen in den Abzug B. Die Verbrennungsluft wird dem Generator durch das
Rohr h und die Düsen i
zugeführt und zwar mittels einer Balancier-Gebläsemaschine bei N, von welcher der Wind, nachdem derselbe den
Windregulator P durchzogen hat, mittels des Rohres y zum Generator gelangt. Die Brennmaterialasche wird
durch Zuschlag einer entsprechenden Menge von Kalk geschmolzen und bei d abgezogen. Die Generatorgase mischen sich in dem
Kanale B innig mit senkrecht darauf treffenden heiſsen
Luftströmen und gelangen dann in den Flammofen C. Die
betreffende Gebläseluft gelangt von der Balancier-Gebläsemaschine J nach dem Windregulator K
und dann in das Rohr L. Von hier wird die Luft durch
die Winderhitzungsrohre S geführt, welche zur Seite des
Feuerkanales des Dampfkessels O angeordnet sind. Das
Rohr S mündet in das mit Wärmeschutzmaterial umgebene
und nach dem Kanäle B führende Rohr T.
Durch eine derartige Luftvertheilung hat es der Arbeiter in der Hand, im Ofen C eine neutrale, eine oxydirende oder eine reducirende
Flamme zu erzeugen. In den beiden ersten Fällen gelangen die Abgase ohne weiteres
durch den Fuchs D in den Vorherd E und von hier unter den Dampfkessel O. Im Falle noch unverbrannte Gase in den Abzugsgasen
vorhanden sind, wird bei x erhitzte Luft in den Kanal
D eingeblasen; dieselbe wird durch das Rohr c aus dem Rohre T
entnommen und in den Seitenwänden des Herdes E
erhitzt.
Der Herd V ruht auf einer Drehscheibe, welche durch
Wasserdruck gehoben und gesenkt werden kann. Die Abdichtung des Herdes gegen den
festen Ofenkörper wird durch einen Sandverschluſs bewirkt. Der Herd macht in der
Minute 3 bis 4 Umdrehungen. Die Drehscheibe des Herdes ruht auf einem Zapfen des
Hebekolbens, so daſs, wenn dieser gesenkt wird, bis die Drehscheibe auf 4 Rädern
ruht, diese zur Seite gezogen werden kann.
Ein derartiger Ofen mit einem Fassungsvermögen des Herdes von 2t,5 ist in Belle-Fonte in Betrieb genommen worden
und sollte mit einer Siemens'schen Regenerativanlage in
Vergleich gestellt werden. Der Henderson'sche Ofen
bedurfte zum Anzünden, Anblasen und Begichten mit Gaskohle bis zum Punkte, wo der
Boden des Herdes hergestellt werden konnte, 16 Stunden. Die Herstellung des Bodens,
das Einschmelzen des Einsatzes und das Abstechen nahmen dann noch 28 Stunden in
Anspruch. Der Siemens'sche Regenerativofen dagegen
brauchte allein zur Anheizung 48 Stunden, dann noch 48 bis 72 Stunden zur
Herstellung des Bodens. Um nun eine Post, bestehend aus 50 Proc. Roheisen, 50 Proc.
Schmiedeisen und Abfall, in einen niedrig gekohlten Stahl zu verwandeln, bedarf man
noch 11 bis 12 Stunden. Der Abbrand beim Henderson'schen Ofen soll nur 6 Proc. betragen.
Otto Springer in Hermannshütte (* D. R. P. Nr. 25 368
vom 28. Juni 1883, vgl. auch 1883 247 * 329. 250 234) versieht seinen mit Siemens'scher Regenerativfeuerung arbeitenden Gaspuddelofen (vgl. Fig. 3 und
4 Taf. 10), entsprechend der umwechselbaren Flammenführung, mit zwei
Vorschmelzherden und einem Arbeitsherde. Die Vorschmelzherde A und A1 sind
muldenartig vertieft; die Sohle derselben wird je nach Bedürfniſs aus gepochtem
Kalkstein, Eisenerz, Garschlacke o. dgl. eingestampft. Gegen den Arbeitsherd hin
sind die Vorschmelzherde durch Feuerbrücken a
abgeschlossen; dieselben besitzen rinnenförmige Aussparungen b, welche während des Schmelzens durch Garschlacke o. dgl. geschlossen
erhalten werden. Die Roheisenposten werden in die Vorschmelzherde A und A1 eingesetzt, worin sie geschmolzen und nach
Erforderniſs bis zu einer beliebigen Grenze gefeint werden.
Das Schmelzen geschieht mittels Generatorgase, welche durch die Gaszuleitungskanäle
B und B1 einmal von rechts und das andere Mal von links in
den Ofen treten. C, C1
sind Luftzuleitungskanäle. Sind die eingesetzten Roheisenposten in den Herden A, A1 geschmolzen, so
werden sie durch Oeffnen der Rinnen b in den
Feuerbrücken a in den Arbeitsherd D geleitet, während die Schlacken in den Herden A, A1 zurückbleiben.
Das abgeleitete geschmolzene Eisen wird nun in dem Herde D der gewöhnlichen Puddelarbeit unterzogen, während in die Herde A und A1 neue Posten eingesetzt und geschmolzen werden.
Aehnlich ist der in Fig. 5 Taf.
10 gezeichnete Gasschmelzofen von G. Leuffgen bezieh. G.
Stumpf in Berlin (Englisches Patent, 1883 Nr. 2842). Der Arbeitsherd
besitzt an beiden Enden erhöhte Schmelzherde G, die vom
Mittelherde durch Brücken, über welche das Metall flieſst, getrennt sind und die das
Schmelzmaterial durch je 8 Trichter H erhalten. Die
Generatorgase treten abwechselnd durch die Kanäle A in
die Vorschmelzherde G und von hier durch den Mittel-
und den anderen Vorschmelzherd in die Regeneratorkammern. Die zur Verbrennung der
Gase nothwendige Gebläseluft tritt in den doppelten Boden des Herdes N oder auch der Vorherde G
und von hier durch die Röhren i in die Leitungen C, welche die erhitzte Luft in den Kanal D und von hier zu den Düsenröhren F führen. Je nach der Richtung der durch den Ofen
streichenden Gase müssen die Röhren F einer Seite des
Ofens abgestellt werden. Auſserdem sind noch Einrichtungen vorgesehen, um im
Arbeitsherde Luft in das Metallbad einblasen zu
können.
Der Ofen kann zum Einschmelzen verschiedener Materialien benutzt werden. Der
Hauptzweck ist dabei eine energische Einwirkung der reducirenden oder oxydirenden
Flamme auf das Material, wenn es im geschmolzenen Zustande in dünner Schicht über
die Brücken flieſst, welche die Vorherde G von dem
Mittelherde N trennen.
Während gewöhnlich die Regeneratorkammern der Flammöfen
unter der Erde liegen, um allseitig freien Zutritt zu letzteren zu haben, legen F. W. Dick und J. Riley in
Glasgow (Englisches Patent, 1883 Nr. 1157) dieselben über die Erde direkt auf der Hüttensohle oder auf Säulen, so daſs sie den
Ofen überragen. Die Skizze Fig. 6 Taf.
10 zeigt die erstere Anordnung; dabei sind die 4 Kammern K, zwei für die Luft und zwei für das Gas, gleichmäſsig um den Ofen O vertheilt. Jede Kammer besteht aus einem äuſseren
Eisencylinder mit feuerfestem Futter und Ziegelausfüllung. Durch die Kanäle a wird den Kammern Gas und Luft zugeführt; letztere
erhitzen sich in denselben, vereinigen sich in den Kanälen b und c und treten dann zusammen in den
Arbeitsherd O. Die verbrannten Gase verlassen die
Kammern durch besondere Kanäle. Der Herd besitzt zwischen den Kanälen o, durch welche die Gase ein- bezieh. austreten, zwei
Arbeitsöffnungen. Um die Kammern und den Ofen leicht reinigen und ausbessern zu
können, sind die Gewölbe an Ketten aufgehängt und abnehmbar; sie haben in diesem
Falle die Einrichtung der bekannten abhebbaren Fuchsgewölbe. Liegen die Kammern über
der Hüttensohle, so sind die Verbindungskanäle mit dem Ofen am Boden der ersteren
angebracht.
R. P. Wilson in Cleveland, Nordamerika, ordnet die Vorschmelzherde in seinem englischen Patente, 1883 Nr.
2631 nach Fig. 7 und
8 Taf. 10 an. Wie ersichtlich, stoſsen die Vorschmelzherde A und B in einem spitzen
Winkel zusammen, so daſs die Flammen der beiden Feuerungen zusammen den Arbeitsherd
C, welcher tiefer liegt als die Vorschmelzherde,
bestreichen. Die Verbrennungsluft wird den Flammen durch die Feuerbrücken zugeführt;
dieselbe erhitzt sich vorher, indem sie die Bodenkanäle des Ofens in der
Pfeilrichtung durchzieht. – Derselbe Flammschmelzofen mit zwei Feuerherden ist im
Deutschen Reiche an C. Wetter in London unter * Nr.
26892 vom 2. September 1883 patentirt.
Das englische Patent 1883 Nr. 1619 von J. Imray in
London bezieht sich auf die Kühlung des Puddelherdes
durch Wasser. Die Herdseiten werden aus Guſseisenkästen gebildet, durch welche das
Wasser flieſst. Unter der auswechselbaren Sohlplatte ist ebenfalls ein Kasten
angeordnet, welcher mit den Seitenkästen in Verbindung steht.
Ueber das mechanische Puddeln in Drehöfen
veröffentlichte J. G. Danks, der Sohn des Erfinders des
gleichnamigen Drehpuddelofens im Engineering and Mining
Journal, 1883 Bd. 36 S. 130 einen bemerkenswerthen Aufsatz, welchem
Folgendes entnommen ist.
Der Puddelprozeſs wurde im J. 1780 von Henry Cort in England eingeführt und in einem Sandherde vorgenommen.
Dadurch stieg die Gesammtverarbeitung von Eisen von etwa 12000t im J. 1720 auf 90000t im J. 1780 und auf 400000t im J. 1820.
Die nächste Verbesserung war die Anwendung eiserner Herdwände und die Bekleidung
derselben mit reichen reinen Eisenerzen statt des Sandes durch S. B. Rogers. Seitdem sind wesentliche Verbesserungen
an dem eigentlichen Puddelofen nicht mehr vorgenommen worden. Die ersten Nachrichten
über einen Drehofen mit feuerfestem Futter und mit etwas schrägliegender Achse sind in einem englischen
Patente von Walker und Warren aus dem J. 1853 enthalten. Ob aber dieser Ofen jemals ausgeführt
worden, ist fraglich.
Erst Sam. Danks führte, nachdem ihm
in Amerika ein sich drehender Puddelofen im J. 1856 patentirt worden war, denselben
in der Praxis aus, konnte aber, durch die Zeitumstände gezwungen, keine weiteren
Versuche damit anstellen. Dies war W. Tooth in London
vergönnt, welcher auf den Dowlais-Eisenwerken unter der Leitung von Will. Menelaus einen mit Ganister ausgefütterten
Drehpuddelofen baute. Aber trotzdem noch bis zum J. 1863 von Tooth und Yates verschiedene
Verbesserungspatente auf den Ofen genommen worden waren und die Dowlais-Eisenwerke
nicht weniger wie 2 Mill. Mark damit auf erfolglose Versuche geopfert hatten, konnte
sich der Ofen nicht behaupten und wurde verlassen, hauptsächlich deshalb, weil es an
einem haltbaren Materiale für das Futter fehlte (vgl. Tunner 1872 204 282).
Mittlerweile war S. Danks wieder nach
Amerika zurückgekehrt und baute dort im Mai 1868 in einem alten Werke einen
rotirenden Versuchspuddelofen von nicht ganz 1m
Länge und etwas mehr als 1m Breite für Posten von
etwa 150k Eisen. Die Feuerung besaſs Unter- und
Oberwind. Das Futter dieses Ofens stellte Danks folgendermaſsen her: Zuerst wurde in dem
Drehcylinder eine etwa 2 bis 3cm dicke Schicht von
einem Breie aus Eisenerz und Kalk eingetragen und mittels Holzfeuerung getrocknet.
Dann wurde auf dieser Schicht Hammerschlag eingeschmolzen und durch Drehen des
Cylinders der erste Ueberzug damit vollständig überdeckt. In die geschmolzene
Schlacke wurden sodann feines Erz, ganze Erzstücke und Abfalleisen eingerührt und
dieses Verfahren unter fortwährendem Umdrehen des Cylinders 5 mal wiederholt. Das
Futter hatte dann eine äuſserst feste und für die Oxydation der schädlichen
Beimengungen des Eisens sehr günstige rauhe Oberfläche. Dieser Ofen bewährte sich in
Bezug auf seine Haltbarkeit und sein Ausbringen ausgezeichnet, so daſs man zwei
weitere Oefen mit gleichem Durchmesser, aber 3 mal so groſser Länge baute. Man
beabsichtigte dabei eine selbstthätige Trennung der fertigen Eisenmasse in Luppen
durch in das Innere des Cylinders hervorragende Vorsprünge (vgl. Schneider 1879 232 * 403.
Siemens 1883 249 442).
Dieselben bewiesen sich aber als unpraktisch und wurden bald wieder verlassen. Auch
die auſsergewöhnliche Länge der Oefen bewährte sich nicht, weil ein zu
ungleichförmiges Product erzielt wurde. Bessere Resultate ergaben Oefen mit
Cylindern von 2m Durchmesser und 1m,5 Länge und diese verdrängten dann auf dem
betreffenden Werke alle Handpuddelöfen, ganz besonders als es sich herausstellte,
daſs die Drehöfen einen um 5 bis 8 Proc. geringeren Abbrand ergaben als die alten
Handpuddelöfen.
Bis 1871 besaſsen schon 3 Werke in Amerika nur Drehpuddelöfen. In
Folge dessen gingen bald darauf Engländer mit englischem Roheisen und Futter nach
Amerika und betrieben einen Danks'schen Ofen mit
englischem Materiale (vgl. 1872 203 * 277. 204 216). Die dabei erzielten guten Resultate hatten 1872
den Bau des ersten Dank'schen Ofens in England zur
Folge und zwar auf den Werken von Hopkins, Gilkes und
Comp. in Middlesborough; dieselben stellten im J. 1878 mit 6 Oefen über
10000t Puddeleisen her.
Seitdem versuchte es Adam Spencer
(1872 204 257. 1877 226 63)
mit einem Kolossalofen von über 3m Länge, in
welchem Posten von 1t Eisen verschmolzen wurden –
aber mit keinem Erfolge. Th. Crampton (1871 200 * 358. 1877 226 63. 1880
235 * 126) baute einen sehr langen Ofen und theilte
denselben in 2 Abtheilungen, von welchen die erste als Verbrennungskammer, die
andere als eigentlicher Puddelherd dienen sollte; als Brennmaterial verwendete er
pulverförmige Kohle. C. W. Siemens (1873 209 * 1. 1880 235 * 369. 1881
242 * 123. 1883 249 442)
führte im rotirenden Ofen die direkte Eisendarstellung aus. Will. Sellers (Patent 1872) schloſs ein Ende des rotirenden Cylinders ganz
und lieſs die Feuergase an einem Ende ein- und austreten (vgl. 1878 228 * 41). Dauernde Erfolge hatte aber keine dieser so
genannten Verbesserungen zu verzeichnen. Das nächste Werk, welches im J. 1882 mit
der Einführung der Danks'schen Puddelöfen vorging, war
die Otis Iron and Steel Company in Cleveland. Der
rotirende Cylinder des Ofens hat 2m Länge und
ebenso groſsen Durchmesser und bestellt aus sehr fest zusammengenieteten Stahlplatten.
Der Feuerrost hat eine selbstthätige Aufgebevorrichtung. Der erste Ofen hat während
6 Monaten so gute Betriebsresultate ergeben, daſs zur Zeit weitere errichtet
werden.
Sehr viele Schwierigkeiten machten die Halsringe an den Enden des
rotirenden Cylinders. Da sie einer häufigen Abkühlung und Wiedererhitzung, nebenbei
auch noch der Reibung in ungeschmierten Lagern ausgesetzt waren, so rissen sie
oftmals, was ein Eindringen des durch dieselben flieſsenden Kühlwassers in den Ofen
zur Folge hatte. Zur Beseitigung dieser Uebelstände sind schon 25 verschiedene
Constructionen, sowohl in Schmiedeisen als Guſseisen, ersonnen und versucht worden.
Andererseits machten die beim Aufhören des Betriebes durch Schrumpfen im Futter
entstehenden Risse sehr viel zu schaffen. Als einzigstes Mittel dagegen haben sich
conische Uebergänge an den Enden des Cylinders bewährt. Würden diese nicht
angewendet, so würden beim Wiederbeginne des Betriebes die stärksten Anker und
Bolzen aus einander getrieben.
Alle diese innerhalb 10 Jahren vorgenommenen Verbesserungen haben
es möglich gemacht, mit einem Dänischen Puddelofen direkt vom Hochofen 10 bis 12t Eisen in 12 Stunden zu verarbeiten und zwar zu
einem Eisen von besserer Güte als das in Handpuddelöfen dargestellte. (Vgl. auch Tahon 1873 209 189. Tunner 1874 213 123.)
Böller zum Reinigen der Winderhitzungsapparate. Zur
Beseitigung des Staubes, welcher sich nach und nach in den Durchzügen der Cowper'schen Apparate ablagert, erweist sich am
zweckmäſsigsten die Erregung einer starken Lufterschütterung, welche die Staub- und
Rufsmassen zu Falle bringt. Zu diesem Zwecke werden von Cowper Schüsse aus einem Böller durch eine Seitenöffnung in den Apparat
hineingefeuert. Vortheilhafter erscheint es nach J.
Ellison von den Ebbw Vale Iron Works den
Böller in lothrechter Stellung zur Anwendung zu bringen, weil alsdann der Schuſs in
der Richtung der Luftwege und nicht rechtwinkelig zu denselben erfolgt, wie im
ersten Falle.
Textabbildung Bd. 253, S. 122
Die beigegebene Figur zeigt die Anordnung dieses Apparates. Der Böller selbst ist
aufrecht auf einer Art Laffette befestigt, mit welcher er bequem an Ort und Stelle
gebracht werden kann. Das Abfeuern erfolgt mittels einer von Ch. Wood in Middlesborough angegebenen Zündvorrichtung. Vor dem Zündkegel
a befindet sich ein Rohr b, in welchem ein Bolzen leicht verschiebbar ist. Wird dieser Bolzen durch
kräftiges Einblasen von Luft in das Rohr b durch den
Gummischlauch c nach vorn getrieben, so trifft derselbe
auf das auf den Kegel a aufgesetzte Zündhütchen und
veranlaſst so die Entzündung des Schusses. Die Pulverladung beträgt 140 bis 170g, auf welche ein Besatz von Schlackenwolle kommt.
12 Schüsse aus diesem Apparate sollen dieselbe Wirkung haben als 30 nach der älteren
Weise wagerecht abgefeuerte.
Holzaschenkokes. Bekanntlich wird bei
gleicher Beschickung in einem mit Holzkohlen betriebenen Hochofen ein von Phosphor
und Silicium freieres Eisen hergestellt, als in einem mit Kokes betriebenen
Hochofen. Siegfr. Stein in Bonn (Erl. D. R. P. Nr.
25241 vom 1. März 1883) schreibt dies dem Unterschiede der Aschen von Holzkohlen und
Kokes zu und schlägt deshalb zur Ausgleichung desselben vor, die Aschenbestandtheile
beider Brennmaterialien durch entsprechende Zuschläge gleichwerthig zu machen. Zu
diesem Zwecke muſs zunächst die Menge und dann die Zusammensetzung der in den
betreffenden Kokes enthaltenen Asche durch Analyse bestimmt werden. Durch Rechnung
ist nun festzustellen, ob und wie viel in dieser Asche an Kali, Natron, Kalk und
Magnesia fehlt, bezieh. wie viel von diesen Stoffen durch Baryt ersetzt werden kann.
Den zu verkokenden Kohlen werden dann entsprechende Zusätze hinzugefügt, so daſs die
fertigen Kokes eine Asche ergeben, welche vollkommen der der Holzkohlen gleich ist.
Dabei ist auf möglichste Zerkleinerung und innige Mischung der Steinkohlen und der
Zuschläge Bedacht zu nehmen. Man erreicht dies am besten durch Knetmaschinen,
Schleudermühlen u.s.w. Es ist ferner darauf zu sehen, daſs die Kohlen möglichst rein
und von Asche frei sind, damit man um so kleinere Mengen Zusätze bedarf und in Folge
dessen auch in Bezug auf die Menge der Asche der der Holzkohlen nahe kommt. Die
Alkalien und alkalischen Erden, welche als Zuschläge besonders in Betracht kommen,
werden entweder in Pulverform, oder gelöst den Kohlen zugesetzt, letzteres besonders
bei Anwendung von kohlensaurem Kali und Natron. Kohlensaurer Kalk, Magnesia,
Kalkmagnesia, bezieh. Baryt werden entweder roh, oder gebrannt und gemahlen mit den
Kohlen gemischt. Man kann dieselben jedoch vorher auch ablöschen, oder mit Wasser zu
einem Breie anrühren.
Tafeln
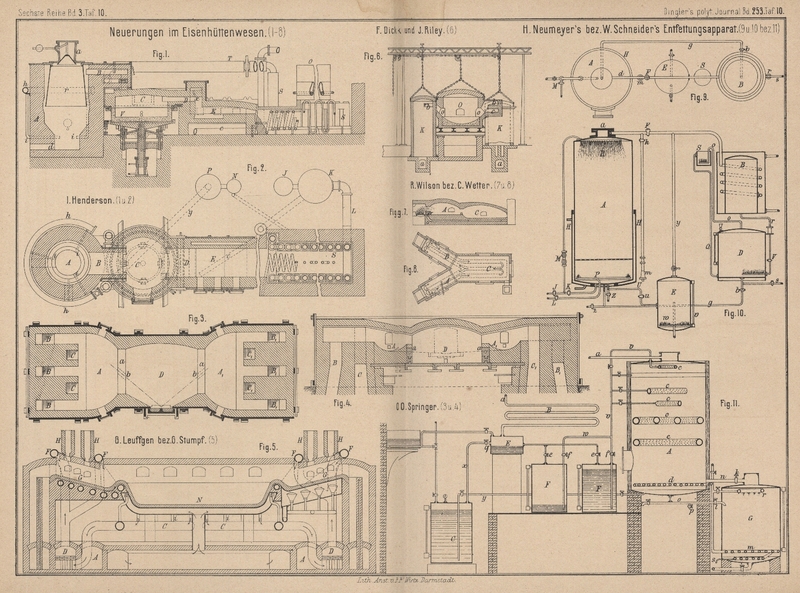