Titel: | Ueber die Herstellung von Leuchtgas. |
Fundstelle: | Band 253, Jahrgang 1884, S. 233 |
Download: | XML |
Ueber die Herstellung von Leuchtgas.
Mit Abbildungen im Texte und auf Tafel 16, 19 ff.
(Patentklasse 26. Fortsetzung des Berichtes S. 202
d. Bd.)
Ueber die Herstellung von Leuchtgas.
Die Bull's Gas, Light and Coke
Company in Liverpool (* D. R. P. Nr. 26093 vom 7. August 1883) schlägt zur
Herstellung von Leuchtgas vor, entschwefeltes Kohlenpulver
in stehenden Retorten zu verwenden. Das in der Mühle N (Fig. 1 bis
3 Taf. 19) zu feinem Pulver gemahlene Kohlenklein gelangt durch den
Trichter C in das von einem Dampfmantel a umgebene Rohr A, worin
sich die Schnecke B dreht und die pulverförmige Kohle
nach dem oberen Ende des Rohres befördert, welches mit einem Abzugsrohre S für die Schwefeldämpfe, sowie mit einem Abfallrohre
b versehen ist. Durch letzteres gelangt die
entschwefelte Kohle in den Mischapparat D. An dem Ende
des Mischgehäuses ist eine Thür t angebracht, durch
welche das entschwefelte und mit Theer gemischte Kohlenpulver in den von Schienen
c getragenen, hin- und herschiebbaren Füllbehälter
E gelangt, worauf die Einfallöffnung e mit einem dicht schlieſsenden Deckel abgesperrt wird;
durch den unteren Schieber s fällt das Kohlenklein in die Retorten.
Durch eine Hebelverbindung h kann der Füllbehälter E gehoben und gesenkt werden. Die Retorten F stehen in zwei parallelen Reihen neben einander, mit
ihrem weiteren Ende nach unten. Jede Retorte ist oben mit einem Halse versehen, in
welchem sich der dicht schlieſsende Schieber s
befindet. Das obere Ende des Halses schlieſst sich beim Füllen dicht an die untere
Oeffnung des Füllbehälters E an und ist am Boden mit
einer Thür v versehen, welche beim Leeren der Retorte
zu öffnen ist, so daſs der Inhalt in den Karren L
fällt. Diese Thür v ist doppelt, so daſs ihre innere
Wand in die Retorte hineinragt, damit die unterste Lage Kohlenpulver in der Retorte
in eine Höhe mit der Sohle des Feuerkanales zu liegen kommt. In jeder Retorte
befindet sich ein Rohr J, welches nach unten verjüngt
zuläuft und mit Löchern für die Aufnahme des sich entwickelnden Leuchtgases versehen
ist. Dasselbe gelangt aus dem oberen Ende der Rohre J
durch Zweigrohre z nach der Hydraulik K.
Die zur Verbrennung des im Generator M erzeugten
Heizgases nöthige Luft strömt durch erhitzte Rohre h,
welche auf beiden Seiten des Ofens durch die nach dem Schornsteine führenden
Feuerkanäle V gelegt sind, so daſs durch die
Verbrennungsgase die einströmende Luft erhitzt wird.
Das als Füllmaterial der Retorte zu benutzende Kohlenklein oder die Grieskohle wird
zuerst, um es so viel wie möglich von Schwefel zu befreien, der Luft ausgesetzt und
wie gewöhnlich gewaschen; dann wird in der Mühle N das
entschwefelte und gewaschene Kohlenklein zu feinem Pulver vermählen. Durch das
Waschen und Pulverisiren der Kohle und das darauf folgende Weiterbefördern derselben
mittels der Schnecke durch das mit dem Dampfmantel a
versehene Rohr A wird das Kohlenpulver gleichzeitig
getrocknet und von Schwefel befreit; letzterer entweicht als Schwefligsäure, so daſs
das Kohlenklein vollkommen trocken und beinahe ohne allen Schwefelgehalt in den
Mischapparat D gelangen soll.
Die so behandelte Retortenfüllung wird nun mit Kohlentheer oder Naphta gemischt und
in luftdicht schlieſsenden Behältern E nach den
stehenden Retorten F gebracht, füllt diese Retorten
vollständig aus und wird daher viel vortheilhafter in Bezug auf die Ausbeute an
Leuchtgas erhitzt, als es in den gewöhnlichen liegenden Retorten geschieht, welche
in der Regel nur zu ⅔ ihres Inhaltes mit Steinkohle gefüllt sind. Wegen des ganz
unbedeutenden Schwefelgehaltes soll das auf diese Art erzeugte Leuchtgas keiner
nachträglichen Reinigung mehr bedürfen und es soll kein Kohlenstoff durch den
Schwefel gebunden, mithin auch die Leuchtkraft des erzeugten Gases nicht durch den
Verlust von Kohlenstoff vermindert werden.
Nach B. Andreae in Wien (* D. R. P. Nr. 26985 vom 5.
August 1883) nimmt zur Erzeugung von Leucht- und
Heizgas der Fülltrichter a (Textfigur
1 bis 3 S. 240 und
241 d. Bd.) die zur Entgasung bestimmten Kohlen auf, welche beim Oeffnen einer
Klappe oder eines Schiebers am unteren Theile desselben in den Vergasungsraum b gelangen, wo dieselben durch die von auſsen
zugeführte Wärme der Destillation unterworfen werden. Die Destillationsproducte
nehmen ihren Weg durch das Knierohr c und die Vorlage
d, wie bei der heutigen Leuchtgasfabrikation, um,
entweder durch entsprechende Kühl- und Reinigungapparate von Theer, Ammoniak,
Kohlensäure u. dgl. befreit, schlieſslich in einen Gasbehälter zu gelangen, oder
auch ohne diese vorherige Reinigung dort aufgesammelt zu werden.
Die gebildete Koke bleibt auf der unter dem Destillationsraume befindlichen
feuerfesten Brücke e so lange liegen, bis dieselbe
mittels eines geeigneten Werkzeuges, welches durch entsprechende Oeffnungen in der
Ofenwand eingeführt werden kann, heruntergestoſsen wird. Um eine Ueberfüllung des
Raumes f mit Koke zu verhüten, kann nun entweder der
überflüssige Theil derselben aus dem Räume f als Koke
gewonnen, oder aber die ganze Koke, welche in diesen Raum gelangt, in Wassergas
übergeführt werden. Durch Einführung von Luft unterhalb des Rostes g, welcher den Feuerraum f
unten abschlieſst, wird ein Theil des Kohlenstoffes der Koke direkt über dem Roste
verbrannt, ein anderer Theil Kohlenstoff in Kohlenoxyd und erst durch eine weitere
Zuführung von Luft, welche direkt über der Kokesschicht in den Raum f eintritt, theilweise noch im Feuerraume f, theilweise aber auch erst im Raume i zur Verbrennung gelangen. Die Asche fällt in den Raum
h und kann durch die halbrunde, in dem Gefäſse A drehbare Schaufel entfernt werden.
Der auf die erwähnte Weise stets sich erneuernde Wärmevorrath in dem Raume f dient dazu, die Destillation im Raume b zu bewerkstelligen; gleichzeitig werden hierdurch die
Steine im Räume i auf möglichst hoher Temperatur
gehalten. Der Ueberschuſs an Wärme entweicht mit den Rauchgasen aus dem Raume i durch die Oeffnungen k
und l; dabei werden die Schieber m, welche die Eingänge zu den Heizräumen n für die Kessel o
sperren, so gestellt, daſs in erster Reihe für eine genügende Dampferzeugung gesorgt
ist und nur der hierzu nicht benöthigte Theil der Rauchgase seinen Weg durch die
Oeffnung l nach den Kanälen p und von da durch die Kanäle q in die Kammer
r nimmt, wohin auch die zur Dampferzeugung bereits
benutzten Rauchgase schlieſslich durch den Kanal S
gelangen, um hier den gröſsten Theil ihrer noch innehabenden Wärme zurückzulassen,
ehe dieselben durch den Kanal t nach dem Schornsteine
ziehen.
Um nun den zur Heizung nicht erforderlichen Theil der nach dem Raume f gelangten Koke in Wassergas und Asche überzuführen,
wird der Betrieb des Ofens mit Luft in regelmäſsigen Zwischenräumen unterbrochen und
die Oeffnungen zum Eintritte derselben in den Ofen, sowie die Oeffnungen zum
Austritte der abziehenden Rauchgase aus dem Raume i durch die Verschlüsse
u und v, sowie C und D gasdicht
verschlossen. Es tritt alsdann Dampf bei w ein,
umstreicht zuerst den Schieber v, gelangt alsdann durch
die Kanäle p bereits vorgewärmt durch die Oeffnung l in den Raum i und von da
stark überhitzt nach der glühenden Kokesschicht in den Raum f. Da nun nur die Oeffnungen x dem Dampfe
einen Ausweg aus dem Ofen gestatten, so muſs derselbe die glühende Kokesschicht in
f durchziehen, wird aber hierbei unter Bildung von
Wassergas zersetzt, welches durch die Oeffnungen x
seinen Ausweg aus dem Ofen findet.
Um ökonomisch arbeiten zu können, sind zwei Gaserzeugungsapparate, wie der hier
beschriebene, mit einander gekuppelt und bilden zusammen ein System. Geht der eine
Gaserzeugungsapparat mit Dampf und liefert also Wassergas, so geht der andere
Apparat mit Luft und die aus demselben abziehenden Rauchgase umspülen die Kessel o und, da zwei Kammern r
unterhalb derselben angebracht sind, von denen stets nur die eine den Rauchgasen
Durchgang gestattet, so kann zur gleichen Zeit die zweite Kammer zum Vorwärmen der
Luft benutzt werden. Die Gebläseluft für den jeweiligen neu aufzublasenden Ofen
tritt in Folge dessen bei E in die durch die Klappen
F vor Eintritt von Rauchgasen geschützte Kammer r, erwärmt sich hier, nimmt alsdann ihren Weg durch die
Kanäle q des Ofens, welcher zu derselben Zeit Wassergas
erzeugt, um schlieſslich durch einen der Kanäle y, das
Rohr z und die Absperrvorrichtungen C und D als überhitzte
Luft in den anderen Ofen einzutreten. Der den Kesseln entnommene Dampf treibt dabei
die zum Betriebe des Gebläses nothwendige Dampfmaschine. Der abgehende Dampf der
Maschine besorgt nach seinem Austritte aus letzterer die Erzeugung des Wassergases.
Die in dem Gaserzeugungsapparate erzeugte Wärme wird in demselben möglichst
aufgespeichert zur jeweiligen nachfolgenden Wassergaserzeugung und besorgt
gleichzeitig die vorherige Destillation des Vergasungsmaterials in einem von der
Verbrennungs- und Feuerstätte abgesonderten Räume.
Die in den Rauchgasen aus dem Gaserzeugungsraume bezieh. dem Feuer- und
Verbrennungsraume abziehende Wärme wird in erster Linie zur Dampferzeugung benutzt
und nur der hierzu nicht benothigte Theil der Wärme zum Ueberhitzen von Dampf und
Luft, welch letzterem Zwecke auch die der Dampferzeugung bereits gedienten Rauchgase
noch ebenfalls zugeführt werden, so daſs auf diese Weise der gröſste Theil der aus
dem Gaserzeugungsraume gelangenden Wärme demselben wieder zurückgegeben wird.
Soll das Wassergas nun auch carburirt werden, so muſs dasselbe als fertiges Wassergas
noch durch einen Ofen gehen, während gleichzeitig über der glühenden Kokesschicht im
Feuerraume die zur Carburirung sich eignenden Stoffe zuflieſsen, so daſs deren
Vergasung im Feuerraume gleichmäſsig erfolgt. Da die Einlassung von Dampf und Luft in einen und
denselben Ofen stets in ganz bestimmten Zwischenräumen zu geschehen hat und dabei
gleichzeitig gewisse Oeffnungen des Ofens geschlossen, andere geöffnet werden
müssen, daher eine Menge Verschlüsse und Vorrichtungen gleichzeitig gehandhabt
werden und dabei noch nebenbei zuverlässig wirken sollen, so ist die Anordnung
getroffen, daſs die Maschine die jeweilige Umsteuerung aller zu einem Wechsel des
Ofens von Luft auf Dampf nothwendigen Vorrichtungen in regelmäſsigen Zwischenräumen
besorgt.
F. C. Glaser in Berlin (* D. R. P. Nr. 26887 vom 8.
August 1883) verwendet zur Destillation von Torf einen
Ofen, welcher aus einem Systeme von lothrechten Schächten A (Textfigur 4 und 5) besteht. Der Raum für
die Verbrennung der unten sich bildenden glühenden Torfkoke ist groſs und besonders
hoch, um der bei dem angewendeten, schwach zu gestaltenden Luftzuge über den Rosten
r sich durch vollständige Verbrennung bildenden
Kohlensäure Zeit zu lassen, im oberen Verbrennungsraume mit der glühenden Torfmasse
sich zu Kohlenoxydgas zu reduciren. Die Zwischenwände der Schächte besitzen ungefähr
in halber Höhe eine Reihe von Schichten, in welchen durch Einfügung von feuerfesten
Hohlsteinen Löcher angebracht sind, die mit einer Absaugevorrichtung a für die dort sich entwickelnden Kohlenoxydgase in
Verbindung gebracht werden können. Die Löcher werden am besten in den Steinen derart
angeordnet, daſs dieselben nach unten gerichtet sind, um das Absaugen der Gase mehr
aus dem unteren als aus dem oberen Theile des Ofens zu ermöglichen und eine
Verstopfung durch den glühenden Torf zu vermeiden.
In dem oberen Theile des Ofens befindet sich eine Oeffnung z, welche mit einer Rohrleitung zum Abzüge der sich entwickelnden Gase
nach dem Kühler und Scrubber verbunden ist. Auſserdem sind die oberen Theile der
Zwischenwände dieser Oefen mit gröſseren Löchern versehen, welche mit einer
Rohrleitung l zur Abführung der von auſsen in diese
Löcher einströmenden und durch die erhitzten Wände selbst vorgewärmten Luft dienen.
Durch diese Einrichtung wird der doppelte Vortheil erreicht, daſs einerseits die
Führung des Betriebes bei niedriger Temperatur hauptsächlich in den oberen Theilen
der Oefen, wo am ehesten eine Zersetzung des Ammoniaks stattfinden könnte, gefördert
und andererseits für die spätere Verwendung der Heizgase eine kostenlos vorerwärmte
Luft erhalten wird.
Die Beschickung dieser Oefen mit Torf muſs in der Weise geschehen, daſs der letztere
nur mit möglichst abgekühlten Gasen in Berührung kommt, und wird zu diesem Zwecke
bei einem irgendwie bedeutenden Steigen der Temperatur ein Abziehen der sich
bildenden Kohlenoxydgase bereits in der Mittelschicht des Ofens durch die hierzu
vorgesehene und vorhin bereits erwähnte Einrichtung bewirkt werden müssen. Auch
muſs, um die Temperatur auf einer niedrigen Stufe zu erhalten, kein höherer als nur
der absolut nöthige Zug in den Verbrennungsgasen vorhanden sein. Nur dann ist es
möglich, die Zersetzung bezieh. ein Zurückschlagen der sich aus dem Torfe
entwickelnden warmfeuchten Gase, bestehend aus Ammoniak, Essigsäure, Holzgeist,
Wasser, Theer u. dgl., zu verhindern. Die Gase, welche die Destillation des Torfes
bewirken, entstehen im unteren Theile des Ofens aus der Verbrennung der bei der
Destillation zurückbleibenden Kohlenstoffverbindung (glühende Torfkoke). Das etwaige
Absaugen des in der mittleren Schicht gebildeten Kohlenoxydgases geschieht in
möglichst heiſsem Zustande des Gases und wird das letztere durch direkte Zuleitung
zur Verbrennungsstelle des gebildeten Gases dort in möglichst heiſsem Zustande
verwerthet. Dieses Absaugen der Kohlenoxyd gase geschieht nur bei einem höheren
Ansteigen der Temperatur in dieser Region; tritt dieses Höhersteigen der Temperatur
nicht ein, so wird durch das langsame Auftreten des Kohlenoxydgases die Destillation
auch in dem oberen Theile des Ofens in gewünschter Weise erfolgen. Auſserdem wird
dieser obere Theil durch die durchströmende Luft der Löcher, wie bereits erwähnt,
gekühlt.
Die Destillationsproducte des Torfes werden aus den obersten Räumen der Schächte der
Destillationsöfen in einen Luftkühler geführt, welcher den Zweck hat, diese Gase so
weit abzukühlen, daſs ein gröſserer Theil des Theeres, des Ammoniakwassers und der
anderen Nebenproducte ausfällt. Dann werden die Gase durch einen Wasserscrubber
geführt, in welchem dieselben mit dem im Luftkühler gewonnenen Ammoniakwasser
behandelt und zum gröſsten Theile von dem Ammoniak befreit werden. Die aus diesen
Wasserscrubbern abströmenden, beinahe vollständig abgekühlten Gase werden direkt mit
einer Leitung an die Verwendungsstelle als Heizgas, sei es, wie in der Zeichnung
angedeutet, zu einem Kessel oder einer anderen, industriellen Zwecken dienenden
Feuerung geführt, wo dieselben in Verbindung mit der in den oberen Theilen der
Destillationsöfen vorgewärmten Luft und den etwa an der Mittelzone dieser Oefen
abgesaugten heiſsen Kohlenoxydgasen verbrannt werden können.
Der praktisch technische Vortheil des ganzen Verfahrens soll hauptsächlich darin
bestehen, daſs die Heizgase hierbei zum mindesten ohne Kosten gewonnen werden
können, da die bei demselben gewonnenen Nebenproducte allein schon an Werth den
Kosten des aufgewendeten Rohmaterials einschlieſslich der Fabrikationskosten,
Kapitalzinsen, Amortisationskosten u. dgl. gleichkommen bezieh. bei richtiger
Betriebsführung die letzteren bedeutend übersteigen sollen.
H. Hirzel in Plagwitz-Leipzig (* D. R. P. Zusatz Nr.
25909 vom 24. April 1883, vgl. 1880 237 * 228) verwendet
zur Herstellung von Oelgas eine Kugelretorte, welche,
wie Fig. 4 Taf. 19 zeigt, nur einen Hals und eine Oeffnung hat. Der
Oeleinlauf durch den Syphon o geht wie bisher vor sich,
während das Gas, statt durch einen besonderen (den hinteren) Hals abzuströmen,
durch den einen vorderen Hals und Kopf C nach D abgeführt wird.
Th. Foucault in Paris (* D. R. P. Nr. 25730 vom 5. Juni
1883) will zur Herstellung von Leuchtgas aus Schieferölen,
Erdöl u. dgl. einen Verdampfapparat verwenden, dessen Heizschacht B (Fig. 5 Taf.
19) zur Aufnahme des Brennmaterials dient; an seinem unteren Ende ist derselbe mit
einem Chamotteringe a zum Schütze gegen Verbrennung
versehen und an seinem oberen Ende wird der Schacht durch einen mittels
Sandverschluſs dicht gehaltenen, lose aufliegenden Deckel verschlossen. Die Löcher
z dienen der entwickelten Kohlensäure als Abzug.
Dieser Heizschacht befindet sich im Inneren eines zweiten Schachtes C aus Guſseisen, welcher die Form einer umgekehrten
Flasche hat und mit seinem unteren engen Theile den Rost umschlieſst. Die
Verbrennungsproducte entweichen in den Schornstein S.
Der Schacht C ist auſserdem an seinem unteren Ende mit
Angüssen c versehen, welche in die ringförmige Rinne
e eintauchen, in der sich die zu verdampfende
Flüssigkeit befindet, und trägt an seinem oberen Ende einen vertieften Kranz b, welcher zur Unterstützung und gasdichten
Abschlieſsung der Glocke d dient. Der Raum zwischen dem
Mantel f und dem Schachte C ist mit Holzkohlenstücken ausgefüllt, welche dazu dienen, die Angüsse
c rothglühend zu erhalten; das durch diese Angüsse
in Folge Verdampfung in der Rinne e erzeugte Gas steigt
durch die Holzkohlenfüllung in die Höhe, geht zwischen f und d wieder herunter und gelangt durch die
Oeffnung i in das Rohr g,
durch welches es dem Regulator zugeführt wird. Das Rohr n leitet das zu verdampfende Material in die Rinne e und das Rohr h regelt die in D befindliche Füllung. Die mit einander verbundenen
Abtheilungen E dienen zur Aufnahme des zur Verwendung
gelangenden Oeles, welches durch ein Rohrsystem n dem
Verdampfapparate zugeführt wird. Zu diesem Zwecke ist über E der Behälter F angeordnet, welcher mit
Wasser gefüllt ist; dieses wird durch ein Rohr m in den
Oelbehälter E geleitet, sinkt hier in Folge seiner
specifischen Schwere nach unten und drückt die Oelschicht nach Maſsgabe deren
Verbrauches nach oben, so daſs dieselbe in der Richtung der eingezeichneten Pfeile
durch das Rohrsystem n dem Verdampfapparate zugeführt
wird. In dem Behälter H befindet sich ebenfalls Wasser,
welches durch Rohr o und Hähne k in das Sammelbecken r und von dort in das
Rohr n gelangt, woselbst es sich mit dem
durchflieſsenden Oele vereinigt, um zur Herstellung von gemischtem Gas oder auch von
armem Gas oder von Wasserstoffgas dem Verdampfapparate zugeführt zu werden. Der
untere Theil des Vertheilers enthält den Ersatzbehälter K und das Sammelbecken L für sämmtliche
Condensationsrückstände; aus diesem letzteren werden die öligen Rückstände durch ein
Rohr in den Behälter M und die wässerigen Rückstände
nach N übergeführt.
Der Regulator G ist zugleich Reinigungsapparat; die
Regulirung
Herstellung von Leuchtgas.
betrifft das rechtzeitige Schlieſsen oder Oeffnen der Ventile
der Rohre o und m zu dem
Zwecke, bei Stillstand des Betriebes den Zufluſs der Oele o. dgl. und des Wassers
zum Verdampfapparate abzustellen bezieh. wieder einzuleiten; sie erfolgt unter dem
Einflüsse eines Hebels, der an seinem einen Ende die Ventilstangen v trägt und an seinem anderen Ende das Gewicht t, welches die Ventile von m und o während des Betriebes geöffnet hält
und durch die in die Höhe gehende Gasometerglocke P
gehoben wird, sobald der Gasverbrauch geringer ist als die Erzeugung. Hierdurch
werden sodann die beiden Ventile geschlossen und die Gaserzeugung unterbrochen. Das
im Verdampfapparate entwickelte Gas gelangt durch Rohr g in den Regulator G in der Richtung der
Pfeile unter die Haube w des durchbrochenen Bodens x, von dort abwärts unter diesen Boden und durch dessen
Durchbrechungen wieder nach oben. Wenn nun das Gas aus g durch den Boden x nach oben tritt, so nimmt
es wie das Wasser in Folge der schraubenförmigen Durchgangsöffnungen in x eine drehende Bewegung an und es werden hierdurch die
Berührungspunkte zwischen Gas und Wasser beständig gewechselt und vervielfältigt,
wodurch eine erhöhte Reinigung erzielt wird. Aus der Glocke gelangt nunmehr das
fertige Gas durch Rohr y an den Ort seiner
Verwendung.
A. Binnie in Maori Hill bei Dunedin, Neu-Seeland (* D.
R. P. Nr. 23854 vom 14. Juli 1882) will ein Gemisch von Fett
und Wasser in eine rothglühende Retorte tropfen lassen, das erzeugte Gas
mit Luft mischen und das Gemenge durch Erhitzen in Leuchtgas überführen. – Der
Apparat macht nicht den Eindruck, als ob er praktisch brauchbar sei.
M. Groſs in New-York (* D. R. P. Nr. 25471 vom 12. Juni
1883) verwendet zur Herstellung von Leuchtgas aus Erdöl und
überhitztem Wasserdampf mit Ausschluſs von atmosphärischer Luft an beiden
Seiten offene Retorten A (Textfig. 6 bis 8), deren
mittlerer Theil der vollen Hitze des Ofens ausgesetzt ist. Derselbe ist mit irgend
einem porösen Stoffe angefüllt und wird stets in Weiſsglut gehalten. In der Mitte
des vorderen Theiles der Retorte ist ein Chamottestück p angebracht, welches mehrere Centimeter nach abwärts reicht und als
Brücke dient, um alle wider dasselbe strömenden Gase nach unten zu leiten. In die
vordere Seite der Retorte ist eine schwere Platte D aus
Guſseisen dicht eingesetzt. Diese Platte hat eine runde Oeffnung o, durch welche alle Gase auf ihrem Wege nach den
Abzugskanälen F, E hindurch müssen. An derselben Platte
ist ein aus starken Eisenstäben hergestellter Korb G
befestigt, welcher zur Aufnahme der porösen Masse dient, durch Rahmen d gehalten wird, falls als solche ein verbrennlicher
Stoff, wie z.B. Koke verwendet wird, welcher alsdann alle 2 oder 3 Monate ersetzt
werden muſs. Wird ein unverbrennlicher poröser Körper verwendet, so ist der Korb G unnöthig.
Wenn Heizgas in einer der Retorten erzeugt werden soll, welches alsdann zum Heizen der Retorten
und des Dampfgenerators dienen kann, wird die Verbindung dieser Retorten mit dem
Abzugsrohre E unterbrochen, indem man das in diesem
Rohre befindliche Ventil H schlieſst und das Gas durch
die am Boden und der Seite des Kanales oder Mundstückes F angebrachten Rohre J bezieh. K nach seinem Bestimmungsorte leitet. Soll das Gas nach
einem Gasometer geleitet werden, so läſst man es durch das Rohr L ziehen.
Durch eine Oeffnung in der Mitte des oberen Theiles der Platte Q geht das Oelrohr r,
während das zur Einführung des Dampfes bestimmte Rohr t
durch eine ähnliche Oeffnung im unteren Theile der Platte Q geht. Das Dampfrohr mündet unter den durchlöcherten Platten n, auf welche das Oel tröpfelt, und das innere Ende
desselben ist nach einer Seite gebogen, so daſs der eintretende Dampf gegen die
Seite der Platte Q anstöſst und sich dann mit den durch
die Berührung des Oeles mit den heiſsen Platten n
gebildeten Kohlenwasserstoffdämpfen mischt. Das innige Gemenge von überhitztem Dampf
und den Kohlenwasserstoffdämpfen wird von einem zwischen dem Condensator und dem
Gasometer befindlichen Sauggebläse durch die Retorte A
und die in dieser befindliche hoch erhitzte, poröse Masse hindurchgezogen, welche
nach ihrer Mitte hin immer heiſser wird. Dadurch soll sich ein beständiges
brennbares Gas bilden, welches hauptsächlich aus schweren Kohlenwasserstoffen der
Aethylenreihe und der Methylenreihe, reinem Wasserstoff, Kohlenoxydgas und einem
gewissen Procentsatze von Theerdämpfen bestehen, dagegen weder Stickstoff, noch
Kohlensäure, noch Ammoniak- oder Schwefelverbindungen enthalten soll.
E. J. Jerzmanowski in New-York (* D. R. P. Nr. 27145 vom
23. Mai 1883) will zur Herstellung von Leuchtgas ein mittels
Kalk erzieltes unreines Wasserstoffgas carburiren. Das in einem Generator
A (Fig. 7 und
8 Taf. 19) erzeugte Heizgas tritt durch Rohre G und K in den mit Kalk gefüllten Ofen B. Durch das Rohr J läſst
man Luft in den Kalkofen B einströmen, um die
Verbrennung des Heizgases darin zu unterhalten. Die Verbrennungsproducte treten
durch das Reinigungsventil t aus. Ist der Kalk glühend,
so wird das Reinigungsventil geschlossen und ein anderes Ventil geöffnet, welches
die Verbindung mit dem Kühler C herstellt. Dann werden
Wasserdampf und Erdöl oder ein anderer flüchtiger Kohlenwasserstoff mit einander
durch den Strahlapparat H eingespritzt. In Folge der
Reaction des heiſsen Kalkes auf den überhitzten Wasserdampf und das Erdöl sollen
sich Wasserstoffgas und Kohlensäure nebst einer sehr geringen Menge von
Kohlenoxydgas, Sumpfgas und anderen Verunreinigungen bilden. Das Gas geht durch das
Rohr d zum Kühler C, wobei
es aber nicht in Berührung mit dem Kühlwasser kommt, sondern durch Röhren
hindurchgeht, welche mittels Wasser gekühlt werden. Von da geht das Gas durch das
Rohr M zum Gasometer D,
dann durch das Rohr N zur ersten Kalkkammer E, von hier durch ein Rohr zur zweiten mit Kalk gefüllten
Kammer und von da aus zum Reiniger P, um das Gas von
der Kohlensäure gründlich zu reinigen.
Um den Kalk wieder ätzend zu machen, wird das Gas zeitweilig durch entsprechende
Ventile durch die anderen Kammern E flieſsen gelassen
und in die Kalk enthaltenden Absorptionskammern durch die Röhren G und R Gas eingeleitet,
sowie Luft durch das Rohr S. Durch das Rohr c soll Dampf eintreten und der Apparat a dazu dienen, das Gas zu entzünden. Ob Dampf
hinzugefügt werden soll oder nicht, hängt von der im Heizgase enthaltenen
Wasserstoffmenge ab. Die Producte dieser Verbrennung entweichen durch die Ventile
v. Dadurch wird das Kalkcarbonat wieder in
ungelöschten Kalk umgewandelt und die Operation kann in den anderen Kalkkammern
wiederholt werden.
Aus dem Waschapparate P geht das Gas zum Carburir- und
Fixirapparate F. Das feuerbeständige Material in
demselben sollte in eben derselben Weise durch Verbrennung des Heizgases mit Luft
erhitzt werden, wie dies bei den Kalkkammern E der Fall
ist; es braucht aber kein Dampf eingelassen zu werden. Wenn eine der Kammern
hinreichend erhitzt worden ist, so läſst man den Wasserstoff durch dieselbe
hindurchflieſsen und gleichzeitig mit diesem ein carburisirendes Mittel, wie etwa
Erdöl o. dgl., durch das Rohr b einflieſsen gelassen.
Dieses wird so in Gegenwart von Wasserstoff verdampft und nachher durch die heiſsen
Theile des feuerfesten Materials vergast. Von da aus geht das Gas durch die Vorlage
O und das Gasrohr V
zum Vertheilungsgasometer.
Will man keinen Generator anwenden, so soll der Kalkofen Fig. 6 Taf.
19 genommen werden. Ist der Kalk in demselben erhitzt, so werden die Ventile in den
Röhren d und e geöffnet,
so daſs Wasserdampf und ein flüssiger Kohlenwasserstoff' eingespritzt werden, welche
durch das Rohr b entweichen. Nachdem der Kalk bis unter
jene Temperatur abgekühlt worden ist, bei welcher noch eine Umwandlung stattfindet,
wird das Ventil im Rohre b geschlossen und im
Schornsteine c ein Ventil geöffnet. Da dann Luft durch
das Rohr f eintreten kann, so wird eine Verbrennung der
Naphta oder anderer Kohlenwasserstoffe stattfinden, wodurch eine hohe Temperatur
entsteht und der Kalk wieder bis zu einem Grade erwärmt wird, bei welchem die
Umwandlung stattfindet. Auf diese Weise kann man somit das beschriebene Verfahren
sehr vereinfachen, vermeidet die Anwendung von Kohle und es wird der zweite
Gasgenerator überflüssig.
Tafeln
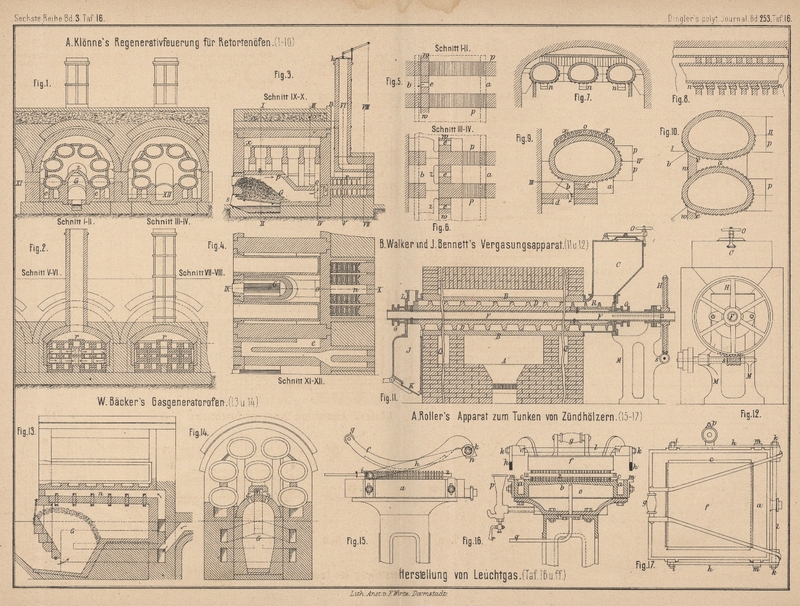