Titel: | Herstellung von Kokes mit Nebenproducten. |
Fundstelle: | Band 254, Jahrgang 1884, S. 31 |
Download: | XML |
Herstellung von Kokes mit
Nebenproducten.
(Patentklasse 10. Fortsetzung des Berichtes Bd.
253 S. 372.)
Mit Abbildungen im Texte und auf Tafel 4.
Herstellung von Kokes mit Nebenproducten.
Nach J.
Jameson in Akenside Hill bei Newcastle-on-Tyne (* D. R. P. Nr. 27694 vom 6.
Juni 1883) werden die zu verkokenden Kohlen mit Theerpech versetzt, welches nach
Gewinnung der nutzbaren Producte des Theeres zurückbleibt. Um den Grad der Absaugung
am Boden des Ofens zu den verschiedenen Zeiten der Kokesbereitung ändern zu können,
werden bei einer gröſseren Anzahl von Oefen A (Fig. 1 und 2 Taf. 4)
mehrere Hauptleitungen c angewendet, in denen
ununterbrochen verschiedene Spannungen herrschen. Jeder Ofen wird dann mit allen
Leitungen durch ein Rohr b und Ventile v so verbunden, daſs man durch Oeffnung eines der
Ventile die erforderliche Saugwirkung am Boden des Ofens herbeiführen und die
Producte somit in verschiedenen Zeiten getrennt absaugen, z.B. eine Vermischung von
armem und reichem Gase, von condensirbaren und nicht verflüssigbaren Producten
vermeiden kann. Ferner kann man an den Kühlapparaten Vorkehrungen treffen, um die
bei verschiedenen Temperaturen flüssig werdenden Producte von einander zu
trennen.
Beim Ablöschen des Ofens will Jameson stark ansaugen, um
so eine beträchtliche Menge Brenngas und Ammoniak zu gewinnen, welches sonst
verloren gehen würde.
Um die nach den Oefen führenden Zweigröhren, sowie die Oeffnungen im Boden des Ofens
von Verstopfungen zu befreien, ist eine besondere Druckleitung vorhanden, mittels
deren gepreſste Luft durch jene Röhren und Oeffnungen geblasen werden kann (vgl.
1884 252 * 284).
Nach H. Herberz in Langendreer (* D. R. P. Zusatz Nr.
27506 vom 21. November 1883, vgl. 1884 252 * 255) werden
die lothrechten Züge über das Gewölbe des Kokesofens hinaus verlängert und die
Seitenwände dieser Verlängerungen zu Kanälen ausgebildet, in denen Luft und Gase
erhitzt werden. Dadurch soll zugleich eine gewisse Abkühlung und damit erhöhte
Dauerhaftigkeit dieser Kanalverlängerungen erzielt werden.
Die Gase werden aus den Rohrleitungen m (Fig. 3 bis 5 Taf. 4) in die kleinen
Röhren n und aus diesen mittels des gemauerten Kanales
p in die einzelnen senkrechten Züge geleitet. Die
atmosphärische Luft strömt durch die Röhren r in die
Heizkanäle s, zunächst in den unteren, dann den
mittleren, endlich in den oberen und aus letzterem in die einzelnen lothrechten
Züge, um hier die Verbrennung der aus den Kanälen p
austretenden Gase zu bewirken. Wenn die Luft unter Druck eingeleitet werden soll,
werden die Röhren r mit einer (in den Figuren
fehlenden) Rohrleitung, welche die Luft von dem Gebläse zuführt, in Verbindung
gesetzt und an den Röhren r Regulirvorrichtungen für
die Zuströmung der Luft zu den einzelnen Gruppen der Heizkanäle s angebracht. Soll die Luft nur durch den Zug des
Kamins angesaugt werden, so fällt die genannte Rohrleitung weg und die
Regulirvorrichtungen werden direkt auf die Röhren r
gesetzt, wie in der Zeichnung angedeutet ist.
Ueber eine im Laufe des vorigen Jahres in. Betrieb gekommene Kokereianlage mit
Gewinnung der Nebenproducte, welche von G. Hoffmann
construirt wurde, berichtet C. Otto in Stahl und Eisen, 1884 S. 396. Das Wesentliche der Construction
besteht in der Verbindung von Siemens'schen Regeneratoren mit gewöhnlichen
Kokesöfen. Dieselbe ist zuerst versuchsweise bei den Schlesischen Kohlen- und Kokeswerken in Gottesberg ausgeführt, ohne Anlage
von Condensationsapparaten für das Gas (vgl. 1884 252 *
254), dann mit sehr vollkommener Verflüssigungseinrichtung an einer Anlage von 20
Kokesöfen auf der Zeche Pluto bei Wanne und an 20 Kokesöfen bei den genannten Werken
in Gottesberg. Die Ergebnisse dieser Anlagen sind so auſserordentlich günstige, daſs
nach derselben Einrichtung mit Gewinnung der Nebenproducte in Deutschland im
Augenblicke bereits 120 Kokesöfen im Baue begriffen sind. Nachstehende Textfigur
zeigt die Gesammtanordnung der Kokesöfen und Condensation auf der Zeche Pluto, Fig. 6 bis 11 Taf. 4
veranschaulichen nähere Einzelheiten derselben.
Textabbildung Bd. 254, S. 33
Die Kokesöfen mit lothrechten Zügen in den Seitenwänden (vgl. 1883 248 * 209) sind 9m
lang, haben eine lichte Weite von 0m,6, eine Höhe
von 1m,6 bis zum Widerlager und die Entfernung von
Mitte zu Mitte beträgt 0m,95. Bei den gewöhnlichen
Kokesöfen ohne Theer- und Ammoniakgewinnung sind in den Verkokungsräumen Oeffnungen
vorhanden, durch welche die Gase aus den Verkokungsräumen zuerst in die Seitenwände
und dann in die Sohlkanäle ziehen, um dort mit zugeleiteter Luft zu verbrennen und
durch diese Verbrennung die Verkokungskammer selbst für den Verkokungsprozeſs
genügend zu heizen. Bei dem vorliegenden Ofen fehlt dagegen jede direkte Verbindung
von Verkokungsräum und
Wand; vielmehr hat auſser den Entlade- und den Beschickungsöffnungen, welche während
des Betriebes geschlossen sind, dieser Ofen nur 2 Oeffnungen a im Gewölbe, durch welche die bei dem Verkokungsprozesse entwickelten
Gase aus dem Ofen entweichen können.
In der Seitenwand des Ofens ist unter dem Widerlager ein liegender Kanal m angeordnet, welcher über den sämmtlichen lothrechten
Zügen der Seitenwand hergeht und eine Verbindung derselben ermöglicht. Jeder
Sohlkanal ist in der Längsrichtung des Ofens durch eine Scheidewand in zwei Hälften
s und S getheilt. Jede
dieser Hälften steht in Verbindung mit zwei Regeneratoren, welche neben einander
liegen und von denen g und G zur Erhitzung des zur Verbrennung zu verwendenden Gases, l und L zur Erhitzung der
zur Verbrennung dieses Gases nothwendigen Luft dienen soll. Diese Regeneratoren sind
lange Kanäle, mit Steinen gitterartig ausgesetzt, um eine groſse Oberfläche zu
erzielen. Dieselben gehen unter der ganzen Gruppe her und an deren Ende stehen die
beiden Luftregeneratoren l und L durch eine Wechselklappe entweder mit dem Luftzuströmungsrohre, oder mit
dem Schornsteine in Verbindung; dabei sind die Gasregeneratoren g und G ebenfalls durch
eine besondere Wechselklappe entweder mit dem Gaszuströmungsrohre, oder mit dem
Schornsteine in Verbindung gebracht.
Sind nun die Oefen in Hitze und durch f mit Kohlen
beschickt, so entweichen die Gase der verkokenden Kohlen durch die Oeffnung a in die Steigrohre r und
gehen bei geöffnetem Ventile v in die Vorlage V. Von hier ziehen die Gase zur Condensationsanlage, wo
sie in den Gaskühlern K gekühlt und dann in den
Gaswäschern (sögen. Scrubber) W gewaschen werden (vgl.
Fig. 9 bis
11 Taf.
4). Die Gase werden dann durch das gleiche Gebläse, welches dieselben nach den
Kühlapparaten hingesaugt hat und das überhaupt die ganze Bewegung der Gase
veranlaſst, wieder von der Condensation weg nach den Oefen hingedrückt und zwar je
nach Stellung der Wechselklappe des Gasdruckrohres entweder nach dem auf der einen
Seite liegenden Gasregenerator g, oder nach dem auf der
anderen Seite liegenden Regenerator G.
Nehmen wir an, das Gas gehe zum Gasregenerator g, so
wird die Wechselklappe der Luftregeneratoren so gestellt, daſs die eingeblasene Luft
in den Luftregenerator l tritt. Dieser und der
Gasregenerator g münden bei jedem Ofen durch neben
einander liegende Oeffnungen o und d in den Sohlkanal s. Die
Verbrennung findet theils im Sohlkanale selbst, theils auf dem weiteren Wege statt.
Der gesammte Strom der in Verbrennung begriffenen Gase und der hoch heiſsen
Verbrennungsproducte geht durch die neben einander liegenden Steigkanäle c in den wagerechten Kanal m und von da, durch die lothrechten Züge e
abfallend, in den Sohlkanal S, von wo die nunmehr
sämmtlich als verbrannt anzunehmenden Gase durch den Luftregenerator L und den Gasregenerator G
zum Kamine entweichen und auf diesem Wege ihre Hitze an das Gitterwerk der Regeneratoren abgeben. Nach
einer bestimmten Zeit, etwa 1 Stunde, werden die beiden Wechselklappen umgestellt
und es tritt alsdann der umgekehrte Weg ein. Das Gas tritt aus der Condensation in
den Gasregenerator G, die Luft in den Luftregenerator
L. Die Verbrennung findet im Sohlkanale S statt. Die Stromrichtung des Gases, der Luft und der
Verbrennungsproducte geht durch e nach m und dann durch c nach
s und durch die Regeneratoren l und g zu dem Kamine.
Dies ist die ursprüngliche Einrichtung der Kokesöfen auf Zeche Pluto; es wurde jedoch von Anfang an darauf verzichtet,
das Gas zu regeneriren, so daſs nur die Luft vorgewärmt wird und zwar aus folgenden
Gründen: Das Nebeneinanderliegen der langen Gas- und Luftregeneratoren kann durch
mögliche Undichtigkeiten der Zwischenwände zu einer Vermischung von Gas und Luft
bereits in den Regeneratoren, also zu Schmelzungen in denselben führen, was
Betriebsstörungen zur Folge haben müſste. Ferner geht bei jeder Umstellung der
Wechselklappe ein ganzer Regeneratorinhalt an Gas verloren und dieser ist bei der
Gröſse der Regeneratoren nicht unbedeutend. Zudem kommt das bei der Umstellung
weggehende heiſse Gas zwischen Klappe und Schornstein mit dem Inhalte des heiſsen
Luftregenerators zusammen und es können Explosionen erfolgen. Endlich ist das
Volumen der zur Verbrennung des Gases nothwendigen Luft ungefähr das 6fache des
Gases; es erscheint also bei dieser Zusammensetzung einfacher und wichtiger, die
groſse Masse Verbrennungsluft allein auf eine sehr hohe Temperatur zu bringen, als
auſser der Verbrennungsluft auch noch die kleine Menge Gas zu erhitzen und die
hierzu nöthige Hitze der Verbrennungsluft zu entziehen.
Man benutzt daher beide neben einander liegende Regeneratoren nur für die Luft und
führt das Gas aus dem von der Condensation zurückkommenden Gasdruckrohre je nach
Stellung der Wechselklappe entweder nach dem Rohre n,
oder nach dem auf der anderen Seite der Kokesöfen liegenden Rohre N. An jedem Ofen ist durch eine kleine Gasdüse, welche
mit einem Hahne versehen ist, eine Verbindung zwischen Gasdruckrohr und
Ofensohlkanal hergestellt. Die Klappe im Gasdruckrohre und die Klappe im Ende der
Luftregeneratoren werden entsprechend gestellt. Wenn also das Gas durch die
Gasdruckleitung und deren Düsen in die Sohlkanäle auf der einen Seite tritt, so
streicht auch die Luft durch die auf der gleichen Seite befindlichen Regeneratoren
in dieselben Sohlkanäle und die Verbrennung und der Weg der Verbrenungsproducte ist
der schon dargelegte. Bei der Umstellung findet der umgekehrte Weg statt. Statt der
zwei Regeneratoren auf jeder Seite wendet man überhaupt jetzt nur noch einen
einzigen auf jeder Seite der Batterie an und dienen diese nur zum Wiedererhitzen der
Luft. Durch diese einräumige Lufterhitzung mit wechselnder Zugrichtung kann die
Verbrennungsluft ganz auſserordentlich rasch und hoch erhitzt werden, viel rascher
und höher als durch
diejenigen mehrräumigen Anlagen, welche auf der stetigen Erhitzung der
Verbrennungsluft durch Wände hindurch beruhen, auf deren einer Seite die Abhitze
heizt, während auf der anderen die zuströmende Verbrennungsluft sich erwärmen soll.
Die Luft kommt bei dieser Siemens'schen Regeneration
auf Zeche Pluto auf eine Temperatur von über 1000° und
durch Anwendung einer so hochgradig heiſsen Luft als Verbrennungsluft wird es
ermöglicht, daſs von den aus der Condensation zurückkommenden kalten und durch den
Verlust an Theer weniger heizkräftigen Gasen nur ein gewisser Theil gebraucht wird,
um durch seine Verbrennung den Verkokungsprozeſs im Gange und die Oefen hinreichend
heiſs zu erhalten. Es hat sich beim Betriebe auf Pluto
herausgestellt, daſs man nicht das sämmtliche vorhandene Gas zur Heizung der Oefen
verwenden darf, wenn die betreffenden Verbrennungsstellen u. dgl. nicht zu heiſs
werden sollen, und daſs man also viel mehr Gas hat, als man zur Unterhaltung des
Verkokungsprozesses braucht; es beträgt der Ueberschuſs etwa 100cbm für Ofen und Tag. Die Temperatur in
Sohlkanälen und Seitenwänden ist so hoch, daſs der Verkokungsprozeſs bei normaler
Ladung, der Ofen mit 5750k trockener Kohlen
gerechnet, in 48 Stunden vor sich geht; sehr häufig ist die Garungszeit eine
geringere. Wird die Garungszeit eine geringere, als erwünscht, so braucht man nur
weniger Gas zuzuführen, um durch eine kleine Erniedrigung der Temperatur wieder eine
Garungszeit von 48 Stunden zu bekommen: Man hat überhaupt den Prozeſs ganz
auſserordentlich in der Hand, weil sowohl Gas, als Luft eingeblasen wird und die
Mengen beider genau geregelt werden können. Die Güte der Kokes ist eine ganz
vorzügliche. Das Ausbringen an Kokes ist in Folge des völligen Luftabschlusses um 7
Proc. höher als bei gewöhnlichen Oefen.
Die Temperaturmessungen, welche mit einem Graphitpyrometer von Steinle und Härtung vorgenommen und mit
Metalllegirungen verglichen wurden, ergaben im Sohlkanale 1200 bis 1400°, in den
Seitenwänden 1100 bis 1200°, im Regenerator bei Beginn der Luftzuströmung 1000°, am
Ende derselben 720°, im Kamine 420°.
Die Gaskühler K (Fig. 9 und 10 Taf. 4) sind eiserne
stehende Cylinder, mit im Deckel und Boden derselben befestigten Eisenröhren x. Aus dem Aufsatze w
strömt Wasser durch die Eisenröhren nach unten und kühlt das Gas ab, welches seinen
Weg zwischen diesen Kühlröhren der Richtung des kalten Wassers entgegen nimmt.
Mehrere Gaskühler stehen so mit einander in Verbindung, daſs das Kühlwasser, welches
von dem ersten Gaskühler unten abflieſst, bei dem zweiten oben einflieſst und so
fort, während das Gas den entgegengesetzten Weg macht. Das Gas hat nach seinem
Entweichen aus dem Ofen im Steigrohre eine Temperatur von 600 bis 700°, in der
Vorlage eine solche von 200 bis 400° je nach der Entfernung vom Steigrohre, vor den
Gaskühlern eine Temperatur von 75 bis 120°, hinter denselben von 17 bis 30°. Durch
die Abkühlung
verliert das Gas einen groſsen Theil Theer und Ammoniakwasser und zwar von dem
gesammten Ammoniakwasser, welches die Condensation liefert, etwa 75 Proc.
In den als Gaswascher dienenden stehenden eisernen Cylindern W (Fig.
11 Taf. 4) ist in Abständen von etwa 10cm eine groſse Zahl von gelochten Blechen über einander angebracht. Auf
das oberste Blech tropft fortwährend kaltes Wasser, so daſs von Blech zu Blech ein
Regen von Wassertropfen nieder- und dem Gase entgegenträufelt, welches in der dem
Wasser entgegengesetzten Richtung sich bewegt und seinen Ammoniakgehalt an das
Wasser abgibt. Das Ammoniak haltige Wasser flieſst unten ab und wird, wenn es noch
nicht hinreichend stark an Ammoniak ist, nochmals und weiterhin so oft nach oben und
dem Gase entgegen gepumpt, bis es für den Verkauf genügend reich an Ammoniak ist.
Mehrere Gaswäscher stehen so mit einander in Verbindung, daſs das Gas bei seinem
Durchgange durch dieselben in dem letzten vor seinem Austritte nur mit reinem Wasser
in Berührung kommt und daſs die Anreicherung des Ammoniakwassers in denjenigen
Gaswäschern stattfindet, in welche das Gas zuerst eintritt. Die Gaswäscher entfernen
die in den Gaskühlern noch übrig gebliebenen 25 Procent des Ammoniakgehaltes und
bringen auch zugleich mit dem Ammoniakwasser noch sehr viel Theer zur Ausscheidung.
Die Temperatur des Gases wird bei Anwendung von genügend kaltem Wasser in den
Gaswäschern bis auf 13° heruntergebracht.
Die Trennung des Theeres und Ammoniakwassers findet in Cisternen nach dem
specifischen Gewichte statt. Das Ammoniakwasser wird für den Verbrauch so lange auf
den Gaswäschern angereichert, bis es etwa 3 bis 3,5° B. hat, entsprechend 1,777
Proc. Ammoniak- da nun etwa 14 Proc. 3grädiges Ammoniakwasser entfallen, so stellt
sich die Ausbeute an Ammoniak, auf schwefelsaures Ammoniak gerechnet, auf etwa 1
Procent der trockenen Kohle.
Auf Zeche Pluto wird das Ammoniakwasser nicht auf
schwefelsaures Ammoniak verarbeitet, sondern als Ammoniakwasser nach seinem
Ammoniakgehalte nach Graden Beaumé verkauft. Die Theerausbeute betrug hier im
Durchschnitte des besten Betriebsmonates 3,46 Proc. bezieh. des schlechtesten
Monates 2,78 Procent, auf trockene Kohle gerechnet. Diese Schwankungen des
Ausbringens sind darauf zurückzuführen, daſs man längere Zeit nur unbedeutende
Mengen Kühlwasser zur Verfügung hatte. Der Kühlwasserbedarf ist für jeden Ofen
täglich 5cbm.
Der Gehalt des Theeres an den in Betracht kommenden Stoffen ist nach Untersuchungen
von Knublauch auf wasserfreien Theer berechnet:
Benzol
0,954
bis
1,06
Proc.
vom
Theer,
Naphtalin
4,27
„
5,27
„
„
„
Anthracen
0,575
„
0,64
„
„
„
Pech
etwa 50
„
„
„
Von diesem Peche kann je nach der Menge des unlöslichen
Rückstandes noch ein mehr oder weniger groſser Theil bei fortgesetzter Destillation
übergetrieben werden. Der in concentrirter Essigsäure oder Benzin unlösliche
Rückstand beträgt 10 bis 25 Procent des Theeres.
Wie schon erwähnt, sind bei jedem Ofen 100cbm Gas
übrig, welches folgende Zusammensetzung hat:
Kokereigas
Kölner Leuchtgas
Benzoldampf
0,60
1,54
Aethylen (C2H4)
1,61
1,19
Schwefelwasserstoff
0,42
–
Kohlensäure
1,39
0,87
Kohlenoxyd
6,41
5,40
Wasserstoff
52,69
55,00
Methylwasserstoff (CH4)
35,67
36,00
Wasser
1,21
–
––––––
––––––
100,00
100,00.
Das Gas hat etwa die halbe Leuchtkraft wie das der Kölner Gasanstalt, dessen Analyse
mit angeführt ist. Kleine Mengen dieses Gases verwendet man auf Zeche Pluto als Leuchtgas unter Benutzung gröſserer Brenner.
Das Gas kann aber auch ebenso zur Heizung von Kesseln
oder zu anderen Heizzwecken verwendet werden und es steht demselben hier vor Allem
der groſse Vortheil zur Seite, daſs es als Heizmaterial sehr weit weggeleitet werden
kann. Im Uebrigen kann auch die Abhitze aus den Regeneratoren, welche mit 420° in
den Schornstein entweicht, noch sehr gut zur Kesselheizung verwendet werden, am
besten vielleicht unter gleichzeitigem Verbrennen des überschieſsenden Gases mit
heiſser Luft aus den Kühlkanälen der Kokesöfen, aus Aussparungen in der Umgebung der
Regeneratoren oder aus den Regeneratoren selbst. Eine derartige Verwendung der
Abhitze und des überschieſsenden Gases zur Kesselheizung kommt demnächst auf einer
Kokerei in Westfalen in Betrieb.
Der Geldertrag aus der Gewinnung der Nebenproducte hängt, abgesehen von der
Construction der Kokesöfen und der Condensation, auch abgesehen von der sorgsamen
Führung des Betriebes, wesentlich von der Zusammensetzung der Kohle ab, d.h. von dem
Reichthume an Gas, an Theer und an Ammoniak. Gute Kokeskohlen eignen sich also
jedenfalls vorzugsweise zu einer Verkokung mit gleichzeitiger Gewinnung der
Nebenproducte. Bei Annahme des heutigen Theerpreises von 5,50 M. für 100k stellt sich auf 10k trockene Kohlen der Reinerlös an Theer bei einem Ausbringen von 3,5
Proc. auf 19,25 M. Die Ammoniakausbeute der Kohlen ist in Westfalen allgemein etwa 1
Procent der trockenen Kohlen auf schwefelsaures Ammoniak gerechnet. In Oberschlesien
ist die Kohle meist noch reicher an Ammoniak und geht bis zu 1,37 Procent der
trockenen Kohle auf schwefelsaures Ammoniak berechnet. In Niederschlesien ist der
Gehalt etwa 0,8 bis 0,9 Proc. also niedriger, und im Saarbrücker Bezirk sogar nur
0,7 bis 0,8 Proc. immer auf schwefelsaures Ammoniak und trockene Kohle berechnet.
Bei Annahme des heutigen
Marktpreises von 27 M. für 100k schwefelsaures
Ammoniak und bei Abzug von 5 M. Fabrikationskosten für 100k schwefelsaures Ammoniak stellt sich der
Reinerlös an Ammoniak auf 10t trockene Kohle bei
einem Ausbringen von 1,37 Proc. Ammoniumsulfat auf 30,10 M.
Man kann annehmen, daſs ein Kokesofen, der mit allen Condensationsanlagen zur
Gewinnung der Nebenproducte ausgerüstet ist, das 3 bis 4fache von einem gewöhnlichen
Kokesofen kostet. Wenn also auch das Erträgniſs solcher Anlagen mit Gewinnung von
Nebenproducten ein gutes ist, so werden doch die hohen Anlagekosten einer allzu
raschen Verbreitung solcher Oefen im Wege stehen. Eine langsame und nicht
überstürzte Entwickelung dieses Industriezweiges kann aber für dessen Erträgniſs nur
von Nutzen sein. Da jährlich in
England
etwa
350000t
Theer,
Frankreich
„
55000
Belgien
„
50000
Holland
„
15000
Deutschland
„
62500
–––––––––––––––––––
also zusammen
532500t
Theer
allein zur Destillation gelangen, so üben die von 1000
Kokesofen gelieferten 27000t Theer keinen Einfluſs
auf die Preisverhältnisse. Ferner würden schon zur Deckung der Einfuhr an
Ammoniumsulfat in Deutschland etwa 6000 Kokesofen erforderlich sein.
In Niederschlesien ist eine derartige Anlage in Gottesberg im Beiriebe; in Bau sind
solche auf der Anlage von G. Schulz in Riemke bei
Bochum mit 40 Oefen, ferner auf Zeche Friedenshoffnungsgrube in Hermsdorf bei
Waldenburg und bei E. Friedlander neben den
Porembaschächten in Zabrze.
F. Lürmann (daselbst S. 403) glaubt, daſs in
zweiräumigen Lufterhitzern die Luft auf ebenso hohe Temperatur gebracht werde als in
Siemens'schen Regeneratoren. 20 seiner Oefen auf
der Anlage von Schulz in Riemke liefern keine genügende
Erfolge, weil die Verbrennungsluft nicht vorgewärmt wird. Man wirft dem Ofen ferner
vor, daſs das Gewölbe zu heiſs gehalten würde, daſs dadurch die Theere und Oele, die
auf eine Länge von 2m unter dem Gewölbe des Ofens
im Inneren desselben bis zum Steigrohre hinziehen müssen, feste Producte
ausscheiden, welche Verstopfungen veranlassen und den Betrieb der Oefen stören. Ist
dies richtig, dann müſste derselbe Uebelstand auch in den Retorten der Gasanstalten
eintreten.
Auf den Hüttenwerken in Trzynietz wurde versucht, aus schlecht backender Steinkohle gute, dichte Kokes herzustellen. Nach einem
Berichte in der Oesterreichischen Zeitschrift für Berg- und
Hüttenwesen, 1884 S. 231 und 299 gelang dies weder durch Verwendung sehr
heiſsgehender Oefen, noch durch Zusatz von Theer und Pech als Bindemittel. Die
mittels Schleudermühlen zerkleinerten normalfeuchten Kohlen wurden nun in einen
hölzernen Kasten von gleichem Querschnitte und Länge wie der Kokesofen, mit
abnehmbaren Seiten wänden und einer eisernen Bodenplatte eingestampft. Wurde die
Kohle 1m hoch eingeschüttet und mit hölzernem
Stöſsel niedergestampft, so war eine Verdichtung des Besatzes von 15 Procent der
ursprünglichen Höhe oder eine Verminderung der ursprünglichen Hohlräume von etwa 35
Vol.-Proc. auf 20 Proc. erreichbar; wurde aber dieselbe Menge Kohle in drei gleich
hohe Posten über einander eingestampft, so verminderte sich die Höhe des
ursprünglichen, also nicht gestampften Besatzes um 22 Proc. und die Hohlräume
verkleinerten sich von den ursprünglichen 35 auf 13,5 Vol.-Proc. woraus zu folgern
ist, daſs durch noch vermehrtes Stampfen ein noch gröſserer Erfolg zu erzielen sein
wird, bezieh. daſs die eine Verbackung hindernden Hohlräume der zu verkokenden Kohle
aufs Geringste herabgezogen werden können.
Nachdem der Besatz in dem Kasten eingestampft war, wurden die Wände entfernt und die
Kohlenkuchen mittels der Ausstoſsmaschine und mit Zuhilfenahme eines an dem
Blechboden befestigten Hakens in den Ofen gezogen. Die Kohlenkuchen berührten
anfangs selbstredend nicht die Seitenwände des Kokesofens, lehnten sich aber
allmählich im Laufe der beginnenden Verkokung an dieselben an. Die Verkokung selbst
ist ohne wesentliche Verlangsamung eine gleichmäſsigere, indem die Gasentwickelung
zu Anfang des Prozesses nicht so heftig auftritt, sondern sich mehr über die ganze
Verkokungszeit vertheilt. Nach Beendigung des Kokungsprozesses wurde der Kokeskuchen
jeweilig sammt der früher erwähnten Unterlagsblechplatte ausgestoſsen, wobei die
letztere ganz unbeschädigt aus dem Ofen kam. Die erhaltenen Kokes sind sehr dicht
und gleichmäſsig.
Bei besser backender Kohle genügt es, die Oberfläche des Besatzes im Ofen mittels
eines Hebelwerkes zu stampfen, an dessen einem Ende eine Eisenplatte angebracht ist,
welche in den Ofen eingeführt wird, so daſs man von jeder Seite des Ofens je eine
Hälfte des Besatzes niederzustampfen oder oberflächlich zu verdichten im Stande ist.
Bei gut backender Kohle ist diese Zusammenpressung von entscheidendem Erfolge, weil
die oberen Theile des Kokeskuchens bei gewöhnlichem Ofenbesatze stets mürbe sind.
Bei der Verwendung von magerer Kohle genügt jedoch weder das Einstampfen im Ofen
mittels des genannten Hebelwerkes, noch das Einpressen der Kohle mittels der
Ausstoſsmaschine vor beginnender Verkokung, noch die Ausübung eines Druckes auf den
Ofenbesatz durch eine ruhige Belastung in Folge Auflegens von guſseisernen Platten
oder von feuerfesten Steinen während der Verkokung (vgl. Sachse 1884 250 * 462).
Das Gesammtausbringen an Kokes war nach den bisherigen Versuchen der Verkokung stark
gepreſster Kohle um 3 bis 5 Proc. höher als bei dem gewöhnlichen Kokungsprozesse
ohne vorherige Verdichtung des Besatzes. Die Methode an sich bedingt keine Aenderung
der bestehenden Ofensysteme und ist bei allen liegenden Kokesöfen ohne Unterschied anwendbar. Nach
den gemachten Erfahrungen liegt es nahe, daſs geringe Mengen von reiner Kokeslösche
mit dem Kohlenbesatze gemeinschaftlich eingestampft werden können und daſs auf diese
Weise eine vortheilhafte Zugutebringung der Kokeslösche möglich wird.
Es ist auch die Vermuthung naheliegend, daſs sich aus in der Schleudernmühle
verkleinerter und zusammengepreſster Braunkohle ohne
Anwendung von Bindemitteln brauchbare, dichte, grobstückige Kokes erzielen lieſsen
und daſs dieser Zweck durch Anwendung geringerer Mengen von Bindemitteln (Theer und
Pech) noch wesentlich gefördert werden könnte.
Tafeln
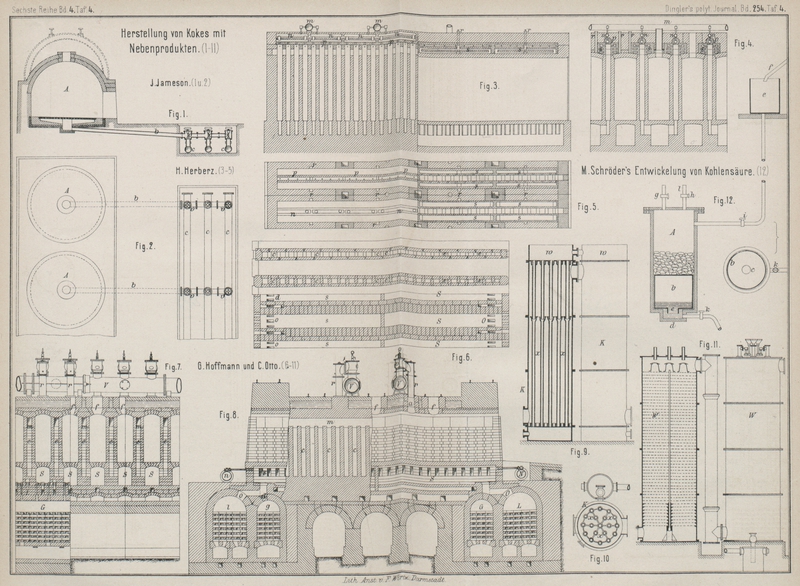