Titel: | Ueber die Verwerthung der Hochofengase. |
Autor: | F. |
Fundstelle: | Band 254, Jahrgang 1884, S. 254 |
Download: | XML |
Ueber die Verwerthung der Hochofengase.Die Ausnutzung der Gichtgase zur Erwärmung des Gebläsewindes bei Hochöfen ist
bereits im J. 1832 durch Faber du Faur in
Wasseralfingen eingeführt worden und die betreffende Anlage in D. p. J. 1834 52 * 100
dargestellt.
Mit Abbildungen im Texte und auf Tafel 19.
Ueber die Verwerthung der Hochofengase.
Nachdem R. Bunsen (1839 72
441) gezeigt hatte, daſs die Hochofengase noch erhebliche Mengen von Kohlenoxyd,
Methan und Wasserstoff enthalten, wurde die allgemeine Aufmerksamkeit auf die
bereits von Aubertot, Curaudau u.a. (vgl. 1837 65 235) empfohlene Verwendung der Hochofengase als
Brennstoff gelenkt. M. Berry (1839 72 * 120) und in ähnlicher Weise Baudelot (1841 79 77) saugten die aus der Gicht
entweichenden Gase durch ein Gebläse ab und führten dieselben in den Hochofen zurück
bezieh. den verschiedenen Feuerstellen zu.
Es folgen nun die Untersuchungen über die
Zusammensetzung und den Brennwerth der Hochofengase von Ebelmen (1842 85 33. 1844 92 297. 1851 119 351), Gruner (1871 202 160. 1872 204 39. 1876 220 247), Kent (1875 218 332), Wolters (1876 222 329), Dürre (1876 220 513. 222 539. 1883 248 122), Jaumain (1882 246 141), J. L. Bell (1882 246 474),
Schellhammer u.a. (vgl. Jahresbericht der chemischen Technologie, 1882 S. 59).
M. Poole (1842 86 * 92)
entnahm die Gase in einiger Entfernung unter der Gicht und führte dieselben den
Puddel- und Schweiſsöfen sowie den Dampfkesseln zu. Das Verfahren rührt von Faber du Faur in Wasseralfingen her und wird von Delesse (vgl. 1843 88 * 264)
eingehend beschrieben. Entsprechende Einrichtungen
werden dann von Pfort (1843 88 * 276), Sire (1843 89 * 119), Budd (1848 109 478), Levi (1850 116 * 363), Darby (1850 116 * 368), Blackwell (1853 127 * 261), Levick und James (1857 146 * 203), Parry (1859 151 * 35), Mauclère (1859 154 * 100),
Turley (1860 156 * 194),
Stein (1860 157 * 438),
Ihme (1861 161 * 350),
Lloyd (1861 161 * 353),
Langen (1862 165 * 25),
J. Jacobi (1870 198 *
131), Sparrow (1873 207 *
313), Buderus (1875 215 *
306), Frew (1878 228 * 326),
Sattler 1878 230 * 411)
bezieh. Schlink (1882 246 *
147) angegeben. Zum Rösten der Eisenerze wurden die
Hochofengase ebenfalls bald verwendet (vgl. 1851 120 237)
und wurden derartige Anlagen namentlich von Houldsworth
(1853 127 * 116) angegeben; Cowper (1860 158 * 104), Whitwell (1870 197 * 315)
u.a. empfehlen sie namentlich zur Winderhitzung.
Die Verbrennung der Hochofengase wird erschwert durch die Gegenwart von Flugstaub,
Wasserdampf und Kohlensäure.
Zur Abscheidung des FlugstaubesVgl. Pattinson 1877 223 * 473. Gruner 1877 225 401. Limbor
1882 245 393. L.
Schneider 1884 252
517. leitet Macco (1884 251 355) die Gase durch Schlacken, Reisig u. dgl. Nach
O. Schrader in Zabrze und
H.
Macco in Siegen (* D. R. P. Kl. 18 Nr. 28003 vom 13. Januar 1884) treten die
aus dem Hochofen entweichenden Gichtgase zunächst in einen weiten Behälter A (Textfig. 1). In Folge
der verringerten Geschwindigkeit fällt die schwere Asche in den Ofen zurück, während
die nur noch leichteren Flugstaub enthaltenden Gichtgase durch das Sammelgefäſs B in das Rohrsystem C und
D treten. Die beiden Rohre C und D sind durch Böden in verschiedene
Kammern a getheilt, welche durch Stutzen e mit einander verbunden sind. Die Gase werden dadurch
gezwungen, eine Schlangenbewegung auszuführen und der mitgerissene Flugstaub setzt
sich in den Aschenfängen der einzelnen Kammern ab. Durch passend angeordnete
Oeffnungen werden die Kammern gereinigt.
Fig. 1., Bd. 254, S. 255
Fig. 2., Bd. 254, S. 255
In Textfig. 2 besteht die Abänderung darin, daſs diese
Rohre in einen Kasten verwandelt sind, der durch neben einander und absatzweise über
einander angeordnete Kammern a den Gasen einen längeren
und mehr gewundenen Weg vorschreibt. Durch Aschenfänge sowie durch
Reinigungsöffnungen ist auch hier für Entfernung der niedersinkenden Flugasche
gesorgt.
K. Möller empfiehlt in der Zeitschrift des Vereins deutscher Ingenieure, 1884 * S. 263 die
Hochofengase durch Schlackenwolle zu filtriren. Ist die
Oberfläche dieser Trockenreiniger so groſs, daſs die Gase auf Temperaturen unter
100° abgekühlt werden, so wird auch ein Theil des Wassers, bei Verwendung von
Steinkohlen auch Theer und Ammoniak abgeschieden; vollständiger geschieht dies durch
gleichzeitige Verwendung von Wasser.Der Vorschlag von Kosmann in der Zeitschrift des Oberschlesischen Berg- und
Hüttenvereins, 1883 S. 156, den Gichtstaub durch Paraffinöl
abzuscheiden, scheint noch nicht versucht zu sein.
Derartige Kühl- und Waschräume für Hochofengase u. dgl.
beschreibt F. W. Lürmann in Stahl und Eisen, 1884 * S. 35. Danach wird auf den Gartsherrie Eisenwerken
in Schottland nach Vorschlägen des Direktors J.
Alexander aus den Gasen zweier Hochöfen täglich etwa 1t schwefelsaures Ammonium gewonnen. In den Gasen
der Kokeshochöfen ist noch kein Ammoniak nachgewiesen.
Die Textfiguren 3 und 4
zeigen solche Kühl- und Waschräume in Ansicht und Grundriſs. Die Hauptgasleitung G führt die Gase von den Hochöfen durch eine der Menge
der Gase und ihrer Temperatur entsprechende Zahl Leitungen g zu den
Kühlräumen K, deren Einrichtung Luft allein als
Kühlmittel voraussetzt. Die Gase streichen durch diese Kühlräume, deren Röhren
abwechselnd oben und unten mit einander in Verbindung stehen, in der Richtung der
Pfeile. Die untere Verbindung der Röhren dient zugleich als Sammelkasten für die
ausgeschiedene Flüssigkeit (Theer und Ammoniakwasser), welche darin in solcher Höhe
stehen bleiben, daſs die nicht bis auf den Boden reichenden Scheidewände s mit der Flüssigkeit einen Abschluſs bilden und so den
Gasen ihren Weg vorschreiben.
Fig. 3., Bd. 254, S. 256
Fig. 4., Bd. 254, S. 256
Durch einen Ueberlauf u wird wie in Leuchtgasfabriken
das Mehr der ausgeschiedenen Nebenproducte in Sammelgruben T abgeführt. Die Gase gelangen dann durch die Rohre z zu den Waschräumen W. In
diesen sind gelochte Böden aus Holz oder Metall in gewisser Entfernung von einander
und so angebracht, daſs dieselben abwechselnd auf der einen und auf der anderen Seite an die Wandungen
des Waschraumes dicht anschlieſsen. Durch und zwischen diesen gelochten Böden
steigen die Gase von unten nach oben. Indem so die Gase oft ihre Richtung wechseln,
gegen die Böden stoſsen und durch die Löcher derselben gehen, scheiden sich die
Theerreste aus. Ferner tritt oben in den Waschraum W
Wasser durch das Rohr w ein, vertheilt sich auf und
durch die gelochten Böden und löst auf seinem Wege und der groſsen, demselben
gebotenen Oberfläche die Reste von Ammoniak aus den Gasen auf.
Durch den Ueberlauf u und v
gelangt der Theer und die Waschflüssigkeit in die Gruben T sowie S, woraus dieselben durch die Pumpe
P so lange wieder gehoben und durch das Rohr w in den Waschräumen W mit
neuen Mengen Gasen in Berührung gebracht werden, bis die gewünschte Anreicherung mit
Ammoniak stattgefunden hat. Die abgekühlten, von Theer und Ammoniak befreiten Gase
werden durch die Rohre x in eine Hauptgasleitung G1 und durch diese bei
Hochöfen zu den Winderhitzern und Kesseln geführt. Soll aus den Hochofengasen nur
der Staub abgeschieden werden, so sind die Waschräume W
entbehrlich; es kann dann aber zweckmäſsig sein, die Gase vor Eintritt in die Kühler
anzufeuchten.
Bei dem von Belani vorgeschlagenen Staubanfeuchter bereitet der nach oben ausströmende
Dampf des Dampfrohres d (Fig. 4 Taf. 19) die
Anfeuchtung des Flugstaubes in dem Gasrohre G vor.
Dieselbe wird dadurch vollendet, daſs der nach unten strömende Dampf das aus dem
Rohre w austretende Wasser zerstäubt. Der nasse Staub
sammelt sich in dem Schlammschiffe A. Der folgende
Kühlraum K ist durch Blechwände in schmale Räume
getheilt. Durch die unten und oben offenen Abtheilungen k steigen die Gase auf; in die oben geschlossenen Abtheilungen h wird das Kühlwasser durch mit zwei Reihen seitlicher
Löcher versehene Röhren w an die Auſsenwände der
Gasdurchzugsräume k gespritzt.
J. Alexander hat ferner die in Fig. 1 bis 3 Taf. 19 in Grundriſs,
Schnitt und Ansicht dargestellten groſsen Kühl- und
Waschräume vorgeschlagen. Jeder Kühlraum K hat
zwei Hauptabtheilungen, mit welchen die Gasleitung G
durch senkrechte Rohre g in Verbindung steht.
Wagerechte Scheidewände s scheiden jeden Hauptraum in 4
Unterabtheilungen, in welche das Gas aus der Rohrleitung g durch die Stutzen a gelangt. In jeder
Unterabtheilung sind querdurch metallene, mit kaltem Wasser gefüllte Kühlräume k und h angebracht, welche
seitlich mit den äuſseren Wandungen dicht vernietet sind. Unter den Kühlräumen k und über h ist der
nöthige Raum für den Durchgang der abzukühlenden Gase gelassen, so daſs diese, durch
die Unterabtheilungen von links nach rechts streichend, abwechselnd unten und oben
die Durchgänge unter k und über h benutzen müssen. Diese Kühlräume k und h sind unter sich durch so viel Röhren r mit
einander verbunden, als für die durchlaufende Menge des Kühlwassers nöthig erachtet
werden. Das Kühlwasser wird durch die Leitung w an der
Seite des Kühlraumes zugeführt, an welcher das abzukühlende Gas diese verläſst,
während das Wasser, nachdem es durch die Kühlräume k
und h geflossen ist, aus der Unterabtheilung an der
entgegengesetzten Seite durch die Leitung z fortgeführt
wird. Auf den Auſsenseiten sind auſserdem Ueberläufe u
angebracht, welche die niedergeschlagenen Flüssigkeiten durch die geneigten Rohre
x zu dem gemeinschaftlichen Fallrohre y und so zu der Hauptableitung führen.
Die gezeichneten zwei Hauptabtheilungen der Kühlräume K
haben etwa 2200qm von Wasser berührter und 500qm nur von Luft berührter Kühlfläche. Die Gase
verlassen die Unterabtheilungen des Kühlraumes K durch
kurze Rohre o, welche in das senkrechte Rohr p münden. Von diesem führt das Rohr q die Gase in einen Waschthurm W, welcher mit gelochten Böden b aus Holz
oder Metall versehen ist. Diese mit Wasser berieselten Böden b lassen abwechselnd auf der einen und anderen Seite des runden Thurmes
für das Gas Durchgänge und bewirken in bekannter Weise die Ausscheidung der
Theerreste durch Stoſs und Oberfläche.
Fig. 5., Bd. 254, S. 258
Fig. 6., Bd. 254, S. 258
Die in Textfig. 5 und 6
gezeichnete rechteckige Form des Waschthurmes hat den
Vorzug, daſs sich der Gasstrom in dem ganzen Raume des Thurmes besser vertheilt,
weil der Durchgang für das Gas in der ganzen Länge der Böden b eine rechteckige Form, also überall denselben Querschnitt hat, was bei
der Form des Durchganges als Kreisabschnitt in dem kreisförmigen Waschthurme nicht
der Fall ist. Das Gas tritt in den unteren Theil des Thurmes W durch das Rohr g unter die gelochten Böden
b und durch die beschriebenen rechteckigen
Durchgänge, welche diese Böden abwechselnd auf der einen und der anderen Seite im
Thurme in der ganzen Breite desselben lassen, langsam in die Höhe. Um die Reinigung
der gelochten Böden b auch ohne Oeffnen der Mannlöcher
vornehmen zu können, ist am Boden des Thurmes ein Rohr d angebracht, durch welches ununterbrochen oder zeitweise Dampf unter die
Böden b geblasen wird. Der Dampf erwärmt zugleich den
etwa auf den Böden angesammelten verdickten Theer, welcher dadurch flüssiger wird
und dann von dem Waschwasser mit fortgeführt werden kann.
Die Reinigungsöffnungen m werden zweckmäſsig zugleich
als Explosionsklappen eingerichtet. In passender Höhe zu jeder Reinigungsöffnung m ist auſsen am Thurme für den Arbeiter eine Bühne t angebracht. Die verschiedenen Bühnen sind durch
Leitern l mit einander verbunden.
Diese bequem eingerichtete Reinigung gestattet, die Zwischenräume zweier Böden von
geringer Höhe zu nehmen, also viel solcher Böden anzuordnen. So wird eine häufigere
Stoſswirkung und eine sehr groſse Oberfläche ermöglicht; diese endlich gestatten
Anwendung verhältniſsmäſsig kleiner Waschthürme für eine groſse zu behandelnde
Gasmenge. Die gelochten Böden sind an drei Seiten mit Winkeleisen an den eisernen
Wandungen des Thurmes befestigt und werden auſserdem durch die 4 Säulen s getragen. Das Wasser wird durch das gelochte Rohr w eingeführt und vertheilt sich so auf den gelochten
Böden b; das aufgebogene Ende des Rohres w dient als Abschluſs gegen den Austritt des Gases.
Dieser Waschthurm hat einen Inhalt von etwa 720cbm
und eine äuſsere Oberfläche von etwa 480qm; die
Fläche der 17 Böden b beträgt zusammen 560qm.
Fig. 7., Bd. 254, S. 259
Fig. 8., Bd. 254, S. 259
Bei dem von Alexander construirten cylindrischen Kühler sind, wie aus Textfigur 7 und 8 zu
entnehmen ist, in dem äuſseren Cylinder K 7 innere
Cylinder k angebracht, welche abwechselnd oben und
unten mit einander in Verbindung stehen, so daſs die Gase, welche in den ersten
dieser Cylinder k durch das Rohr g unten ein-, aus den letzten durch das Rohr G oben austreten. Jeder der Cylinder k enthält wieder 7 Rohre v, welche dadurch, daſs dieselben oben und unten offen sind, mit dem mit
Wasser gefüllten Hauptraume K in Verbindung stehen,
also auch Wasser enthalten. Das kalte Wasser wird dem Kühlraume K durch die Rohrleitungen W zu- und das warme Wasser durch w abgeführt.
Die aus den Gasen abgeschiedenen Flüssigkeiten werden durch die Rohre u und z in die Grube S abgeleitet. Der Kühler hat ungefähr 1700qm durch Wasser und etwa 288qm durch Luft gekühlte Fläche, welch letztere auch noch
mit Wasser gekühlt werden kann, so daſs die erstere dann etwa 200qm betragen würde.
Um bei Steinkohlen-Hochöfen die Ausbeute an Ammoniak zu
erhöhen, soll aus der um den Ofen liegenden Dampfleitung d (Fig.
7 und 8 Taf. 19) den 2 bis 3m unter der
Gichtöffnung angebrachten gelochten Röhren r Dampf
zugeleitet werden. Statt dessen kann auch der Dampf durch ein mittleres Rohr e zugeführt werden, welches passend theilweise in das
Gasabzugsrohr G gelegt wird, um dadurch den Dampf zu
überhitzen.
Bei den nur mit Luftkühlung versehenen Kühlern von Gebrüder Körting in Hannover treten die Gase durch
Stutzen der Rohrleitung G (Fig. 5 und 6 Taf. 19) in die eine
Reihe der 30cm weiten Röhren des Kühlraumes K und des ebenso eingerichteten damit verbundenen
Waschraumes. Zwischen je 5 der 25 in einer Reihe hinter einander angeordneten Röhren
des Kühlraumes K und auch der 25 Röhren des Waschraumes
sind unten oder oben Scheidewände in den Verbindungsröhren v angebracht, so daſs die in eine Rohrreihe eintretenden Gase gezwungen
sind, in den so gebildeten Unterabtheilungen von je 5 der Rohre auf- und
niederzusteigen.
Die gezeichneten 3 Rohrreihen bilden eine Abtheilung der gesammten Kühl- und
Waschräume und die Bewegung der in eine solche Abtheilung eintretenden Gasmenge wird
durch Körting'sche Sauger unterhalten, welche, wenn
nöthig, an verschiedenen Stellen, z.B. zwischen den Kühl- und Waschräumen,
eingeschaltet werden können. Die in jeder Unterabtheilung von 5 Röhren
ausgeschiedenen Flüssigkeiten werden durch Ueberläufer in die Sammelgruben
abgeleitet. Das Ammoniakwasser wird durch Pumpen auf die Höhe der Waschräume gehoben
und fällt in diesen, in seiner Menge begrenzt und zertheilt, nieder. Um den Gasen
und dem Wasser in den Waschräumen groſse Oberflächen zu bieten und eine Stoſswirkung
zu veranlassen, sind die Röhren derselben mit eigens dazu hergestellten Hobelspänen
angefüllt, Jede Rohrreihe kann von der Leitung G durch
Absperrvorrichtungen a abgeschlossen und dann einer
etwaigen besonderen Reinigung unterzogen werden. Die gezeichnete Abtheilung der
Kühl- und Waschräume enthält 450 Röhren von 300mm
lichter Weite und 3m,5 Baulänge und haben diese
mit den Verbindungsröhren v zusammen eine
Kühloberfläche von etwa 1700qm. Diese Kühlräume
haben sich bereits für die Gase der Gasanstalten bewährt.
Young und Beilby nehmen mit ihren groſsen gemauerten
Waschräumen auch auf die zur völligen Ausscheidung der Theernebel erforderliche
Geschwindigkeitsverminderung der Gase Rücksicht.
In den Raum W (Fig. 10 Taf. 19) treten
die Gase durch den Kanals und die Oeffnungen e, welche
durch Bleiglocken n überdeckt sind. Indem die Gase in
dem Räume W aufsteigen, strömt denselben ein feiner
Regen Wasser oder Säure haltiges Wasser oder Säure entgegen, um die Reste Ammoniak
aufzunehmen. Die Gase treten bei G aus. Die
ausgeschiedene Flüssigkeit wird durch einen Ueberlauf u abgeleitet.
Der Inhalt dieses Waschraumes beträgt 500cbm.
Fig. 9 Taf. 19
zeigt mit einander verbundene Waschräume W1 W2 u.s.w. Die Gase
treten durch Rohr g ein, durch G aus und gelangen durch r in den Raum W2
, dann erforderlichenfalls durch Rohr v in den dritten Waschraum u.s.w. bis zum letzten. Das
Wasser oder die Säure haltige Flüssigkeit wird in jeden Waschraum durch Zerstäuber
z in einem feinen Regen eingeführt. Die Anordnung
der Zerstäuber z unten in den Waschräumen und die
höhere Stellung eines jeden der folgenden Räume hat den Vortheil, daſs
Flüssigkeitshebevorrichtungen hier unnöthig werden. Indem die Flüssigkeit vom
letzten Waschräume nach dem ersten (W1) geleitet wird, kommt dieselbe auch nach und nach
mit Gasen zusammen, welche noch reicher an Ammoniak sind, so daſs die Flüssigkeit
sich immer leichter vollständig damit sättigen kann. Jeder der Waschräume hat einen
Inhalt von etwa 300cbm.
Ein Hochofen, welcher in 24 Stunden 75t Kokes verbraucht, liefert etwa 355000cbm Gas oder 4cbm,11 in der Secunde. Die
Geschwindigkeit dieser Gase berechnet sich nach dem Querschnitte der Gasleitung. Ist
derselbe z.B. 1qm,22, gleich demjenigen einer
Leitung von 1m,25 Durchmesser, so ist die
Geschwindigkeit = 4,11 : 1,22 = 3m,36 in der
Secunde. Wenn die Temperatur der Hochofengase nur 215° beträgt und die specifische
Wärme derselben 0,237 ist, dann führen dieselben, bis auf 15° abgekühlt, um die
Nebenproducte zu gewinnen, oder den Staub und die Wasserdämpfe auszuscheiden, dem
Kühlmittel in einer Secunde 5,46 × 200 × 0,237 = 259c, in einer Minute 328 × 200 × 0,237 = 15553c und im Tage 472500 × 200 × 0,237 = 22 × 396 × 500c zu. Dies sind auf 1k der im Tage vergasten Kokes 298,2 oder rund 300c. Wenn die Hochofengase allein durch Wasser auf
15° abgekühlt werden sollen, das Kühlwasser mit 15° zu- und mit 70° abläuft, was zu
ermöglichen sein dürfte, wenn genügende Oberfläche vorhanden ist und das Kühlwasser
in umgekehrter Richtung als das Gas strömt, dann würde man in einer Secunde 259 :
(70 – 15) = 4k,71, in einer Minute 282k,78 und im Tage 407209k oder 407cbm,2
Kühlwasser gebrauchen. Dies wäre auf 1k der im
Tage in einem Hochofen vergasten Kokes 5k,43
Wasser, welche zur Kühlung der Gase erforderlich würden. Je gröſser die Kühlfläche,
um so kleiner ist der Wasserbedarf und umgekehrt. Ist die Beschaffung des Wassers
theuer, dann wird man die Kühlflächen vergröſsern müssen und umgekehrt.
Die Gröſse der Waschräume ist nach den Anforderungen der
Leuchtgasfabrikation so zu bemessen, daſs das Gas 10 bis 12 Minuten in denselben
verweilt, oder daſs für 100cbm der in 24 Stunden
erzeugten Gase mindestens 0cbm,5 Waschraum
vorhanden sind. Groſse Räume, in welchen die abgekühlten Gase zur Ruhe kommen und
Zeit zur Ausscheidung der Theernebel finden, scheinen für vollkommene Gewinnung des
Theers von allergröſster Wichtigkeit.
Während der gröſsere Theil der beschriebenen Waschräume in Eisen construirt gedacht
sind, wird man da, wo Wasser billig ist, oder wo Säuren zur Aufnahme des Ammoniaks
angewendet werden, die Waschräume aus Mauerwerk herstellen und im letzteren Falle
inwendig etwa mit Asphalt verputzen.
J. v. EhrenwerthJ. v. Ehrenwerth: Die Regenerirung der
Hochofengase. (Leipzig 1883. A.
Felix.) empfiehlt die Regenerirung der Hochofengase, wobei Verfasser zunächst die Verhältnisse
der alpinen Holzkohlen-Hochöfen im Auge hat, daher annimmt, daſs die Erze heiſs
gegichtet werden und daſs auch der Zuschlag kein Wasser enthalte, während der Wassergehalt der
atmosphärischen Luft vernachlässigt wird. Verfasser berechnet nun die
Zusammensetzung der Gichtgase eines Hochofens zu:
Gichtgase
Für 100 Roheisen
Für 100 Gichtgase
Kohlenstoff
Kohlensäure
82,10
24,23
5,62
Kohlenoxyd
96,58
20,60
10,59
Kohlenwasserstoff CH4
1,50
0,38
0,28
Wasserstoff
0,82
0,21
–
Stickstoff
217,52
54,58
–
–––––
–––––
–––––
398,52
100,00
16,49.
Die dem Hochofen zuzuführende Menge Wind beträgt 282k,32 oder 218cbm,2 von 0° und 760mm Barometerstand. Im Vergleiche mit
Generatorgasen legt v. Ehrenwerth folgende Werthe für
die Zusammensetzung und den Brennwerth der Gase seinen weiteren Betrachtungen zu
Grunde:
Generatorgase aus
Hochofen-Gichtgase
Kokes
Stein-Kohle
Gewöhn-liche
Voll-kommenregenerirt
Praktischregenerirt
KohlenoxydKohlensäureLeichter
KohlenwasserstoffWasserstoffStickstoff
33,8 1,3 – 0,1 64,8
25,0 6,5 1,5 0,5 66,5
24,23 20,60 0,38 0,21 54,58
42,42 0,00 0,21 0,15 57,22
34,87 8,37 0,28 0,18 56,30
Summe
100
100
100
100
100
1k Gas gibt c
841
920
688
1087
923
Um nun die obigen 20,6 Th. Kohlensäure der Gichtgase wieder in Kohlenoxyd
überzuführen, sind theoretisch 5,62 Th. Kohlenstoff erforderlich, auſserdem aber
auch an Reductionswärme 17613c für je 100k Hochofengase. Es wird nun aber angenommen, daſs
praktich ein Gas gewonnen werde, welches 8,37 Gew.- oder 5,3 Vol.-Proc. Kohlensäure
enthält. Hierzu wären erforderlich 9684°, oder wenn 30 Procent der erzeugten Wärme
verloren gingen, 13834°. Um diese zu erzeugen, müſsten Kohlen ebenfalls im obigen
Verhältnisse CO2 : CO = 0,55 vergast werden, oder
86,7 Proc. zu Kohlenoxyd, 13,3 Proc. zu Kohlensäure, so daſs 1k Kohlenstoff nur 3219c entwickelt. Es sind dann für 100k
Gichtgase erforderlich: für die Regeneration 3k,09, für die Wärmeerzeugung 4k,30
Kohlenstoff oder 9k,24 Kokes.
Zur Ausführung dieser Regeneration sollen Schachtöfen verwendet werden, welche durch
den Gichtverschluſs F (Fig. 11 und 12 Taf. 19)
mit Kokes, Holzkohlen o. dgl. gefüllt werden. Durch die Leitung w und die Formen v wird
Luft eingeblasen; die Gichtgase gelangen durch Leitung g und Formen e in den Ofen, während die
regenerirten Gase bei G entweichen. Soll die Schlacke
bei s durch Abstechen entfernt werden, so werden die
Windformen dem Boden ziemlich nahe gelegt, um die Schlacke flüssig zu erhalten. Die
Gasformen können etwa 10 bis 20cm höher liegen
oder auch wohl unter den Windformen oder neben diesen, in welchem Falle man denselben am besten sehr
breite Querschnitte gibt, so daſs die Einströmung auf einem groſsen Theile des
Umfanges des Regenerators erfolgt.
Will man nicht ununterbrochen arbeiten, was in mancher Richtung Vortheile bietet, so
kann derselbe Regenerator verwendet werden; derselbe wird dann abwechselnd durch
Wind geheizt, wenn der Apparat entsprechend heiſs ist, der Wind bis auf eine sehr
geringe Menge eingestellt und dann durch Durchleiten der Gase deren Regenerirung
bewirkt. Ist der Apparat hierdurch wieder so abgekühlt, daſs die Regenerirung
leidet, so folgt abermals die Heizung u.s.f. Bei unterbrochenem Betriebe müssen
mindestens 2 Regeneratoren vorhanden sein, wovon der eine geheizt wird, während der
andere regenerirt. Es wäre aber zweckmäſsig, mehrere Apparate, etwa 3 bis 4,
anzulegen, wodurch man nebst anderen Vortheilen, an Gleichmäſsigkeit der Gase
gewinnt. Während der Heizung wirkt der Regenerator wie ein gewöhnlicher Generator,
die Gase werden daher auch mit den anderen zusammengeleitet und verwendet.
J. v. Ehrenwerth hält diese Regenerirung besonders
wichtig für solche Anlagen, welche einen Theil der Gichtgase unbenutzt entweichen
lassen, welche also, wie viele alpinen Holzkohlen-Hochöfen Wasser als Betriebskraft
verwenden. Die regenerirten Hochofengase sollen namentlich für das
Siemens-Martin-Verfahren verwendet werden.
Die Angabe, daſs die Regenerirung von 100k
Gichtgasen mit 9k,24 Kokes ausführbar sei, ist
wohl zu niedrig gegriffen. Die Gase der meisten Hochöfen enthalten erhebliche Mengen
Wasserdampf; wird dieser Dampf durch Abkühlung ausgeschieden, so geht damit die
erhebliche Eigenwärme der Gase verloren; wird der Dampf aber mit zur Regeneration
geführt, so erfordert derselbe erheblichen Brennstoffaufwand, welcher nur zum Theile
wieder verwerthbar ist. Immerhin ist dieser Vorschlag der Regenerirung der
Hochofengase bemerkenswerth.
F. Lürmann macht in der Zeitschrift des Vereins deutscher Ingenieure, 1884 S. 323 den Vorschlag,
die regenerirten Hochofengase wieder in den Hochofen einzublasen. Danach hat das
Gemenge der Gase, welches im Hochofen theils durch Einblasen von atmosphärischer
Luft und theils durch Einblasen der Gichtgase entstehen würde, weniger
Stickstoffgehalt als die bisher zur Reduction der Erze benutzten, allein durch
Vergasung von Kohlenstoff mit atmosphärischer Luft entstandenen Gase. Dieses
Gasgemenge mit geringem Stickstoffgehalt nimmt in der Reductionszone des Hochofens
den entsprechenden Sauerstoffgehalt aus den Erzen und weiter Kohlensäure aus der
Beschickung auf und kommt als Gichtgas mit einem noch geringeren Gehalte an
Stickstoff wieder in den Hochofen zurück.
In diesem Kreislaufe soll sich der Stickstoffgehalt der Gichtgase und demzufolge also
der in dem Hochofen zur Reduction benutzten Gase um ein wesentliches, entsprechend
dem Mitverbrauche von Gasen, verringern, die Reductionsfähigkeit derselben sich also
wesentlich erhöhen lassen. Der absolute Brennmaterialverbrauch des Hochofens würde
durch diesen Umstand und durch Wiederbenutzung des in den Hochofengasen enthaltenen
gasförmigen Kohlenstoffes den jeweiligen Verhältnissen entsprechend vermindert
werden können. Ein dem direkt verbrannten Kohlenstoffe entsprechender Antheil
Gichtgase wird nach Lürmann wie bisher zu Zwecken der
Winderhitzung und Dampferzeugung verwendbar bleiben. (Vgl. Schinz 1868 189 513. 1869 191 * 283.)
F.
Tafeln
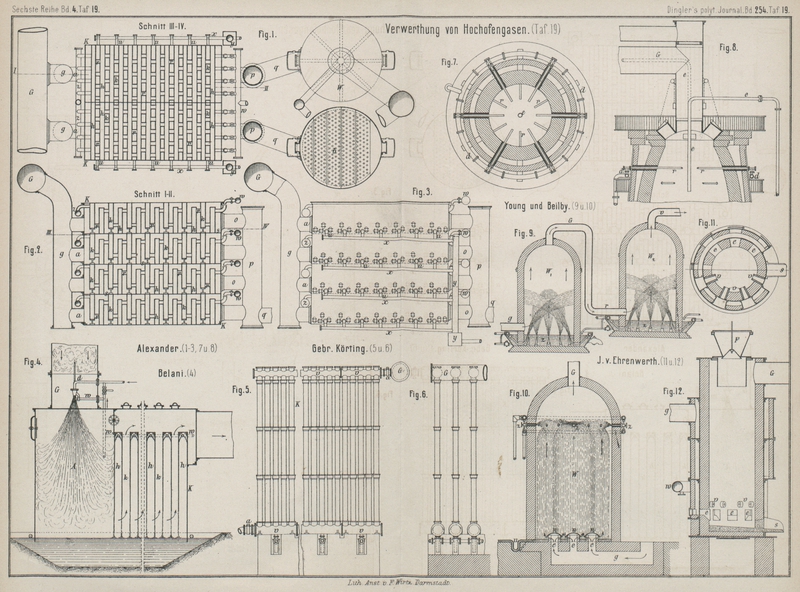