Titel: | Ueber Neuerungen im Hüttenwesen. |
Fundstelle: | Band 256, Jahrgang 1885, S. 317 |
Download: | XML |
Ueber Neuerungen im Hüttenwesen.
(Patentklasse 40. Fortsetzung des Berichtes S. 226
d. Bd.)
Mit Abbildungen auf Tafel
21.
Ueber Neuerungen im Hüttenwesen.
L. Kleemann in Myslowitz (* D. R. P. Zusatz Nr. 28596
vom 14. December 1883, vgl. 1880 236 * 249) hat seine Vorlage an Zinkdestilliröfen, um das Entweichen der
Destillationsproducte an der Vorderseite des Ofens zu verhindern, dahin geändert,
daſs der Kasten b (Fig. 1 bis 3 Taf. 21) durch eine lose
Kapelle s oben ganz geschlossen ist. Der Rost mit der
Aufschüttung ist in ein hinzugekommenes Rostbehältniſs p verlegt und die Hinterwand von b zur
Verbindung von p mit b
weggelassen worden. Die Zinkdämpfe kommen hiernach erst in p unter den Rost, um nach dem Durchziehen der darüber ausgebreiteten
Aufschüttung bei q nach g
und h zu entweichen. Zur Auflage des Rostes ist vorn
eine Eisenschiene h querüber mit den Enden in die Wände
von p gelegt und hinten entweder dieselbe Einrichtung
getroffen, oder wie auf der Zeichnung die Hinterwand von p mit einem Vorsprunge versehen. Der Kasten b
ist zwischen zwei durch Bänder w und z zu einem Gestelle r
verbundenen Platten, welche mittels daran befestigter und mit Thon verstrichener
Rahmen u zugleich die Seitenwände von b bilden, hergestellt; die bereits erwähnte lose Decke
s und ein Vorsetzer t
bilden die beiden anderen Kastenbestandtheile. Diese, wie gewöhnlich vor den
Muffelräumen abgenommen, geben vorn zwischen den Platten den Raum zum Zutritte für
das Abwerfen der Aufschüttung, die Reinigung des Rostes und zugleich für den Abzug
der Muffelraumgase von der Vorlage a nach g und k frei. Die an den
Platten von r sitzenden Rahmen u sind aus Winkeleisen gedacht und dienen noch dazu, daſs davon die
vorderen Seiten zum genauen Anlegen des Vorsetzers t,
die oberen zur Führung und stets gleichen Lage von s
und die hinteren zum genauen Anschluſs von p an b dienen. Zu letzterem tragen die Bügel z auch bei, welche mit den Enden der Seitenplatten
gleichsam einen Muff bilden, in welchen p mit seinem
vorderen Theile eingeschoben wird. Um endlich die Platten von r oben vor möglichem Angriffe von der Flamme der bei
q entweichenden Gase zu schützen, werden
Thonplatten l über s an
die Seiten gestellt.
J.
Garnier in Paris (* D. R. P. Nr. 30418 vom 3. Juli 1884) empfiehlt zur unmittelbaren Gewinnung von Rohkupfer aus Kupfererzen und
Rohsteinen einen kegelförmigen Tiegel, welcher entweder mit solchen Stoffen
ausgefüttert wird,
die weder von Kieselsäure, noch von Basen angegriffen werden, z.B. Chromerz,
Calciumsulfat, Zinksilicat, Calciumphosphat o. dgl., oder aber mit gewöhnlichen
kieselhaltigen, feuerfesten Massen. In letzterem Falle darf die Ausfütterung jedoch
nur so dünn sein, daſs die im Inneren des Apparates an der Wandung befindlichen
geschmolzenen Massen durch einen Wasser- oder Luftstrom, welcher auſsen um die
Wandung flieſst, derart abgekühlt werden, daſs sie unmittelbar an der Wandung
erstarren und somit eine Schutzhülle für den Tiegel bilden.
Der Ofen ist in zwei Zapfen a und b (Fig. 4 Taf. 21) drehbar
gelagert, durch welche gleichzeitig die Luft zugeleitet wird, die zunächst in einen
den unteren Theil des Ofens umgebenden Hohlraum c und
dann durch die Düsen f in das Innere eintritt. Der
Hohlraum c wird von Metallblechen d eingeschlossen, von denen das Innere gleichzeitig die
Auſsenwandung des Ofens bilden kann. Diese Anordnung bietet den Vortheil, daſs
einerseits die Luft vorgewärmt wird, andererseits die Wandung des Ofens eine
entsprechende Abkühlung erleidet und hierdurch noch besser vor zu rascher Zerstörung
bewahrt bleibt. Um übrigens in dieser Hinsicht noch gröſseren Schutz zu erzielen,
kann man, besonders wenn die Ausfütterung aus kieselhaltigen Ziegeln besteht, an
einzelnen Theilen des Mantels noch Wasserkühlung anwenden. In der Auſsenwandung des
Mantelraumes c sind in der Achse der Düsen f Löcher e angeordnet,
welche das Reinigen, Schlieſsen und Wiederöffnen der Düsen f gestatten. Die Schlacke wird bei g, das
Rohkupfer bei k abgestochen. Der untere Theil k des Ofens ist mit einer der oben erwähnten Massen
ausgefüttert, der obere Theil l besitzt eine
gewöhnliche feuerfeste Ausfütterung; zwischen beiden befindet sich eine Schicht m aus feuerfester Masse.
Nachdem der Apparat beschickt und in Betrieb gesetzt ist, sammelt sich der
geschmolzene Kupferstein nach und nach auf dem Boden und steigt immer höher, während
die Schlacken ablaufen. Die Beschickung kann entweder aus Kupfererzen oder
Kupfersteinen, oder einem Gemische beider bestehen. Sobald der geschmolzene
Kupferstein die Düsen erreicht, schlieſst man die Oeffnung für den Abfluſs der
Schlacken, ohne die Windzuführung zu unterbrechen; der geschmolzene Kupferstein
steigt nun höher, so daſs die eingepreſste Luft durch denselben durchdringt, wodurch
dann der im Rohsteine enthaltene Schwefel, sowie auch das Eisen und die anderen,
leichter als Kupfer oxydirbaren Stoffe verbrannt werden.
Die entstehende Schwefligsäure entweicht hierbei mit der überschüssigen Luft, während
sich das Eisenoxyd mit den erdigen Stoffen der Beschickung verbindet, wozu letztere
derart zusammengesetzt sein muſs, daſs sie von vorn herein die zum Binden des
Eisenoxydes erforderliche Menge Kieselsäure enthält. Das zu Boden sinkende Kupfer
enthält nur noch einen geringen Bruchtheil Eisen und sonstiger Unreinigkeiten. Das Feinen schreitet in
dieser Weise ununterbrochen fort, da aus der schmelzenden Beschickung immer wieder
eine entsprechende Menge frischen Schwefelkupfers in das Bad eintritt.
Sobald der gröſsere Widerstand, welchen der Wind beim Durchdringen der geschmolzenen
Masse findet, darauf schlieſsen läſst, daſs die Luft jetzt durch eine dichtere Masse
treten muſs, sticht man die Schlacken ab; dieselben werden noch mehr oder weniger
Kupferstein enthalten, welcher sich jedoch in den Schlackenformen durch Saigerung
von den Schlacken trennt. Das Rohkupfer wird ebenfalls von Zeit zu Zeit abgestochen.
(Vgl. Manhès 1884 254 *
481.)
J. Quaglio in Frankfurt a. M., J. Pintsch in Berlin und A. Lentz in
Stettin (* D. R. P. Nr. 29551 vom 9.
März 1884) wollen in einem Ofen zur Darstellung
oder Schmelzung von Metallen gleichzeitig Kohlenoxyd oder
Schwefelkohlenstoff gewinnen. Zu diesem Zwecke sind zwei Schachtöfen H (Fig. 5 bis 7 Taf. 21) durch Kanal X verbunden, gasdicht mit einem eisernen Mantel A umgeben und an der heiſsesten Stelle mit einem
Wasserkühlringe B versehen. Der untere Theil J ist erweitert, wodurch beim Herabfallen der Füllung
für den Abzug der Gase und das Einblasen der Luft ein freier Raum W sich bildet. Die Thüren C und B dienen zum Ziehen der Asche und
Schlacken, die Oeffnungen z zum Nachstoſsen.
Die beiden Schachtöfen H werden mit Kohle gefüllt, bei
W angeheizt und die Gase bei P abgesaugt; hierdurch tritt die Verbrennungsluft durch
den einen freien Schlitz des Schiebers zu den Kohlen, während durch den mit dem
Muschelschieber G (vgl. Fig. 8) überdeckten
Schlitz aus dem anderen Ofen die Gase abgezogen werden. Man kann gleichzeitig auch
ein Gebläse anbringen, in welchem Falle der obere Theil des Schiebers mit einem
luftdichten Kasten umgeben wird, in welchen das Zuführungsrohr vom Gebläse
einmündet; gleichzeitig mit der Luft kann man auch Dampf einströmen lassen, wodurch
nebst Kohlenoxyd auch Wasserstoffgas gebildet wird. Sobald die. Kohle im ersten
Schachte glühend ist, wird der Schieber nach der anderen Seite verschoben und tritt
nun sofort der umgekehrte Kreislauf ein. Ist auch die Kohle im zweiten Schachte
glühend, so kann mit dem Aufgeben der Erze, mit Kohle gemischt, durch den
Fülltrichter EF begonnen werden.
Die reducirten Metalle, welche flüssig bleiben, sammeln sich im Schöpfherde K. Die dampfförmigen Metalle und Metalloxyde gehen nach
dem zweiten Schachtofen über, in welchem sie vollständig reducirt werden, während
gleichzeitig die etwa noch vorhandene schädliche Kohlensäure zu Kohlenoxyd
verwandelt wird. Die Metalldämpfe werden abgesaugt und gehen durch Rohre M zum Condensator N. Das
Kohlenoxyd oder Wassergas geht durch P nach einem
Gasbehälter, um von dort weiter zu Heizungszwecken
verwendet zu werden. Wird in diesem Ofen die unmittelbare Reduction von Blende mit
Kohle vorgenommen, wobei
Schwefelkohlenstoff gebildet wird, so ist zwischen der Auslaſsöffnung P und dem Sauger ein kräftig wirkender, mit Wasser
gefüllter Kühler einzuschalten.
Bei schwer reducirbaren Erzen, Erzen mit viel Schlacke gebenden Bestandtheilen oder
bei Kohlen von minderer Beschaffenheit ist die Erzeugung von höheren Temperaturen,
als durch die Verbrennung der Kohle zu Kohlenoxyd entsteht, nothwendig. Diese
höheren Temperaturen können erzeugt werden durch Vorerhitzung der Verbrennungsluft
in einem der bekannten Lufterhitzungsapparate, wobei zur Erhitzung ein Theil der
abgesaugten Gase in letzteren Apparaten verbrannt werden kann. Oder man verbrennt
einen Theil der erzeugten Gase in einem in den Schachtofen selbst eingebauten,
geschlossenen, feuerfesten Raum, wodurch dessen Umfassungswände und folglich auch
der umgebende Raum des Schachtofens auf Weiſsglut erhalten wird.
Nach G.
Sehe in Altena, Westfalen (* D. R. P. Nr. 29535 vom 21. Juni 1883) findet das Schmelzen von Zink haltigen Legirungen in Tiegeln T (Fig. 9 und 10 Taf. 21) statt, welche
durch die Decke p des Ofens hindurch auf die
feuerfesten Untersätze f gestellt werden. Zwischen den
Wandungen der Tiegel und denen der Oeffnungen in den feuerfesten Platten p bleibt ein etwa 5mm
weiter Spielraum, um das Anschmelzen beider an einander zu verhindern. Der Herd h fällt von allen Seiten nach der Mitte hin etwas ab,
so daſs, wenn ein Tiegel während des Schmelzens entzwei gehen sollte, das Metall
durch den Abstich s sofort aus dem Ofen entfernt werden
kann.
Wird in solcher Art eingesetzten Tiegeln z.B. Kupfer und Zink zu Messing geschmolzen,
so gibt man zuerst das Kupfer in die Tiegel, welches bei etwa 1050 bis 1200°
schmilzt. Dann gibt man rasch so viel Zink hinzu, als nothwendig ist, im Ganzen in
der Regel etwa die Hälfte bis ein Drittel des Kupfers, und wirft nun so viel Abfälle
von Messing in die flüssige Masse, daſs dieselbe steif wird. Gleichzeitig werden
hierdurch in den oberen Theilen der Tiegel kältere Metallschichten gebildet. Da nun
die Tiegel auſserdem aus dem Ofen hervorragen, so herrscht in den oberen Schichten
der Metalle eine wesentlich geringere Temperatur und wird dieselbe durch die
allmählich mit dem fortschreitenden Schmelzen weiter nachgegebenen kalten
Messingabfälle auf diesem niederen Standpunkt gehalten, welche die sich in den
heiſseren Metallschichten entwickelnden und nach oben aufsteigenden Zinkdämpfe
zwingen, sich in diesen kälteren Schichten zum allergröſsten Theile zu verdichten.
Es sollen auf diese Weise nur geringe Verluste an Zink entstehen und zwar
hauptsächlich beim ersten Eingeben des Zinkes zu dem geschmolzenen Kupfer. Nimmt man
nun, nachdem alles Metall geschmolzen ist, die Tiegel heraus und rührt die
geschmolzene Masse um, so wird eine vollkommen gleichartige guſsfertige Legirung
erzielt. Bilden sich bei dem Umrühren noch Zinkdämpfe, so kühlt man die oberen, nun flüssigen
Metallschichten, welche ohnehin eine geringere Temperatur wie die unteren besitzen
(etwa 900° oben zu 1200° unten), mit Wasser ab und zwingt so auch die zuletzt noch
entwickelten Zinkdämpfe, sich zu verdichten.
Tafeln
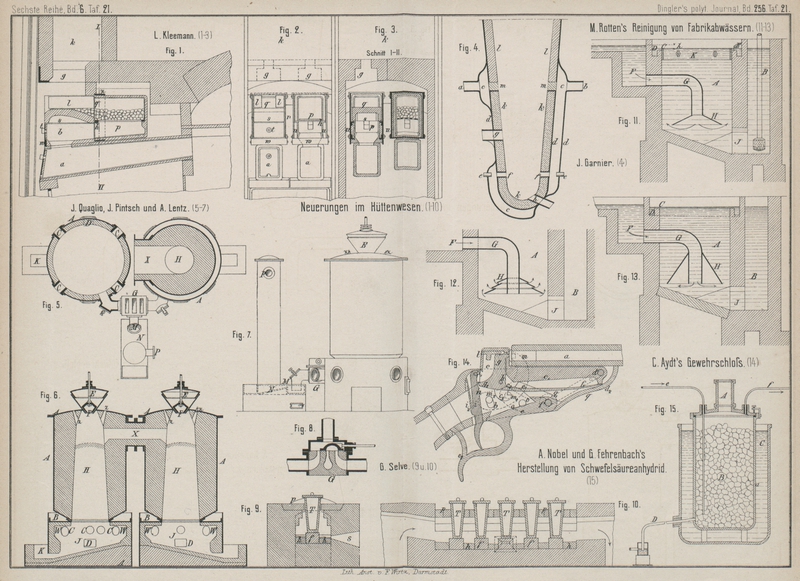