Titel: | Ueber Neuerungen im Eisenhüttenwesen. |
Fundstelle: | Band 259, Jahrgang 1886, S. 361 |
Download: | XML |
Ueber Neuerungen im Eisenhüttenwesen.
(Patentklasse 18. Fortsetzung des Berichtes Bd.
258 S. 443).
Mit Abbildungen im Texte und auf Tafel 24.
Ueber Neuerungen im Eisenhüttenwesen.
Behufs besserer Vertheilung der Beschickung bei Hochöfen
(vgl. Schlink 1882 246 *
147) empfiehlt W. v. Vloten in Dortmund (* D. R. P. Nr.
34162 vom 4. Juli 1885) einen Gichtapparat mit
Doppelkegel, welcher die Beschickung in zwei von einander getrennten Ringen
in den Ofen gleiten läſst. Nach Fig. 1 Taf. 24 wird die
Gicht geschlossen von dem Trichter a, dem Doppelkegel
b und dem Kegel c,
welcher sich an dem in der Ofenmitte eingehängten Gasabzugsrohre G führt und oben mittels eines Wasserverschlusses gegen
dasselbe abgedichtet ist. Der Kegel c ist mit Ketten an
dem doppelarmigen Hebel i aufgehängt und kann dadurch
gehoben und gesenkt werden. Der Doppelkegel b hängt an
Stangen f zwischen a und
c, so daſs er bei geschlossener Gicht von c getragen wird. Die Stangen f gestatten dem Doppelkegel b einen kurzen
Hub nach unten, wobei die Muttern der Stangen sich dann auf Bufferfedern setzen und
den Stoſs auffangen. Die Beschickung wird bei geschlossener Gicht in den Trichter
a gestürzt und dann der Kegel c gesenkt; dabei geht zuerst b mit c herunter, so daſs ein Theil der
Beschickung durch den zwischen a und b entstehenden Spalt in den Ofen gelangt, wobei die
Materialien gegen den äuſseren Ring e prallen und dann
senkrecht herabfallen. Wird das Herabgehen von b durch
die Stangen f begrenzt, so entfernt sich c von b, so daſs der Rest
der Beschickung durch den Spalt zwischen b und c gegen den inneren Ring e1 anprallend in den Ofen fällt. Die
Schlieſsung der Gicht erfolgt in umgekehrter Weise, wobei c zuerst b mitnimmt und dann b gegen a hebt.
Gegen die bekannten Gichtapparate mit sich senkendem Doppelkegel unterscheidet sich
also der vorliegende nur durch Anordnung der Ringe e
und e1, welche
allerdings eine Ablenkung der Materialien von dem Umfange des Schachtes nach dem
Inneren und dadurch eine gleichmäſsigere Vertheilung der Beschickung über den ganzen
Ofenquerschnitt bewirken können.
Ein von H. Macco in Siegen (* D. R. P. Nr. 33329 vom 24.
April 1885) angegebener Winderhitzer soll die Mängel
der Cowper'schen und der Whitwell'schen Apparate beseitigen (vgl. auch 1884 251 354). Bekanntlich gehen bei dem Cowper'schen Winderhitzer (vgl. 1883 248 * 499) die
Gase in einem runden Zuge in die Höhe, vertheilen sich oben im Apparate, um durch
gitterartig zusammengesetztes Mauerwerk nach unten zu ziehen und durch den
Abzugskanal nach dem Schornsteine zu entweichen. Hierbei zeigt sich der Uebelstand,
daſs die Gase vorzugsweise durch den Theil des Apparates nach unten ziehen, durch
welchen sie am schnellsten zu dem Abzugskanale gelangen können. Die Vertheilung der
Gase, welche das Mauerwerk erhitzen sollen, ist daher eine sehr ungleichmäſsige:,
letzteres wird ebenso ungleichmäſsig erwärmt und daher nur ganz unvollständig
ausgenutzt. Ferner wird die Temperatur der Gase dadurch wenig ausgenutzt, daſs
dieselben, nachdem sie in dem kaminartigen Rohre im Apparate aufgestiegen sind,
diesen Weg nur einmal beim Herabgehen wieder zurücklegen und in Folge dessen mit
hoher Temperatur in den Abzugskanal eintreten. Auſserdem ist es durch die bisher
übliche Construction nicht möglich, dieselben genügend zu reinigen, da die Decke der
Apparate vollständig geschlossen ausgeführt werden muſs und in Folge dessen ein
Herunterlassen eiserner Bürsten oder anderer Werkzeuge zum Reinigen der einzelnen
Kanäle unmöglich ist. – Die Whitwell'schen Apparate
(vgl. 1882 245 * 161) vermeiden einen Theil dieser Fehler
dadurch, daſs die Gase mehrfach im Apparate auf- und abgeführt werden, sich dadurch
gleichmäſsig vertheilen und in Folge der Länge des Weges vollständiger ausgenutzt
werden; sie haben indessen gegenüber den Cowper'schen
Apparaten den Nachtheil, daſs sie bei gleichem Inhalte des Apparates an feuerfestem
Material eine bedeutend geringere Heizfläche für Gas und Wind darbieten.
Bei der in Fig.
2 und 3 Taf. 24 veranschaulichten Macco'schen
Anordnung sind die Kammern b und h für den Ein- und Austritt der Gase, wie solche bei
den Whitwell'schen Apparaten ausgeführt sind,
beibehalten; dagegen ist der mittlere Theil des Apparates den Cowper'schen Winderhitzern entsprechend derart
eingerichtet, daſs derselbe in zwei Räumen getheilt wird, in denen die Gase ihre
Wärme an gitterartig in den verschiedensten Formen zusammengesetztes Mauerwerk
abgeben und die zu erwärmende Luft in demselben Mauerwerke erhitzt wird. Die Gase
treten durch den Kanal a ein, gehen in der Abtheilung
b des Apparates in die Höhe, treten bei c in den nächsten gitterartig zusammengesetzten Theil
d, ziehen in demselben nach unten, um sich in der
unteren Kammer e wieder zu vereinigen. Von da treten
die Gase in die zweite gitterförmige Abtheilung f, in
welcher sie nach oben ziehen, um alsdann durch die Oeffnungen g in die letzte Abtheilung h des Apparates zu gelangen, nach unten zu ziehen und durch die Oeffnung
i in den Schornstein zu entweichen. Sowohl gleich
nach dem Eintritte in den Apparat im unteren Theile der Abtheilung b, als auch in der unteren mittleren Abtheilung e wird den Gasen erwärmte Luft zugeführt, um dieselben
vollständig zu verbrennen. Der zu erwärmende Wind macht den umgekehrten Weg. Durch
diese Einrichtung wird also erreicht, daſs Gase und Wind einen möglichst langen Weg
in dem Apparate zurücklegen und hierdurch in die Lage kommen, ihre Temperatur
möglichst vollständig abzugeben bezieh. aufzunehmen. Es wird ferner ermöglicht, daſs
die Gase sich gleichmäſsig im Apparate vertheilen und derselbe dadurch vollständig
ausgenutzt wird. Schlieſslich wird durch die Anwendung der mittleren Abtheilungen
d und f eine groſse
Heizfläche hergestellt und eine hohe Temperatur des zu erwärmenden Windes
hervorgebracht.
Die Reinigung geschieht hier ähnlich wie bei Whitwell'schen Apparaten, indem die im oberen Boden
befindlichen Mannlöcher geöffnet, die in der Decke des Apparates angebrachten
Formsteine entfernt und die einzelnen Theile des Apparates durch eiserne Bürsten
abgekratzt werden. Die heruntergefallenen Unreinigkeiten werden durch die unten
befindlichen Reinigungsöffnungen entfernt, Es ist also möglich, auch den mittleren,
nach dem Cowper'schen Systeme gebauten Theil des
Apparates von oben zu reinigen.
F. W. Lürmann in Osnabrück (* D. R. P. Nr. 31697 vom 26.
August 1884, Zusatz zu * Nr. 31116, vgl. 1885 257 * 236)
gibt weitere Einrichtungen
zur Erhitzung von Verbrennungsluft und Gasen, deren Temperatur geringer
als zur Entzündung nothwendig ist, in Anwendung auf Lufterhitzer und Dampfkesselfeuerungen an.
Diese Einrichtungen unterscheiden sich von den früheren durch eine abgeänderte
Anordnung der Kanäle, der Vorwärm- und Verbrennungsräume. Eine im 2. Zusatzpatente
Nr. 33417 vom 3. April 1885 erläuterte Einrichtung bezweckt eine noch höhere
Erhitzung der Gase und eine noch innigere Mischung derselben. Erstere wird dadurch
erzielt, daſs die Seitenwände der Kammern aus Stein und
Eisen hergestellt werden; letzteres Material gestattet bei gleicher
Festigkeit viel geringere Dicken ab Steinwände. Ebenso stellt man die Schlitze,
welche Gas und Luft in die Kammern führen, aus Eisen her, so daſs die Trennungswände
der einzelnen Schlitze sehr dünn werden und die Anzahl derselben vermehrt werden
kann, was eine innigere Mischung von Gas und Luft zur Folge hat.
Zur gleichzeitigen Entfernung des Schwefels und des Phosphors
aus dem Roheisen schlagen A. Rollet in St.
Etienne und R. M. Daelen in Düsseldorf (* D. R. P. Nr.
33386 vom 20. Mai 1884) einen Apparat vor, welcher aus einem Kupolofen und einem
damit verbundenen Flammofen besteht (vgl. Krupp 1880
235 * 373. Uebersicht 1880 238 416. Rollet 1881 242 220. C. Hoepfner 1885 257 236). Der Kupolofen hat, wie aus Fig. 5 und 6 Taf. 24 zu entnehmen
ist, einen cylindrischen Schacht, dessen Eisenmantel durch äuſsere Wasserberieselung
gekühlt wird. Im mittleren Theile hat der Schacht eine dünne Ausfütterung von
feuerfestem Material; dasselbe bedeckt sich während des Betriebes bald mit einer
Schicht Eisen, welche fest darauf haften bleibt. Der Boden des Ofens ist abgeschrägt
und führt zu einem Kanäle, welcher ansteigend in den Reinigungsofen mündet-
auſserdem ist noch ein besonderer Abstich vorhanden. Der Kupolofen hat mehrere
Reihen Formen, deren Höhenabstand um so gröſser sein soll, je unreiner das Eisen
ist, bezieh. je mehr Zuschläge dasselbe zur Reinigung verlangt. Die unterste
Formenreihe ist stechend angeordnet; die oberen Reihen liegen wagerecht. Die
Windpressung soll 20 bis 60cm Wassersäule, die
Temperatur des Windes 350° betragen. Der Flammofen hat die bekannte Einrichtung.
Je nach dem Phosphor- und Siliciumgehalte des Roheisens besteht die Beschickung für
1000k Roheisen mit Eisenabfällen aus:
Kokes
120
bis
160k
Kalkstein
150
„
450
Fluſsspath
35
„
80
Eisenoxyd
50
„
150
Die entfallende Schlacke soll folgende Zusammensetzung
haben:
SiO2 und P2O5
12
bis
16
Proc.
Al2O3
2
„
3
CaFl2
20
„
28
Fe2O3
1
„
5
Schwefel
1
„
2
Bei der Berechnung der Beschickung wird angenommen, daſs alles Silicium und der Phosphor als
kiesel- und phosphorsaure Verbindungen in die Schlacke gehen. Von dem
Schwefelgehalte behält die Schlacke nur 1 bis 2 Proc. zurück; der Rest, oft mehr als
die Hälfte, soll durch die oxydirende Wirkung des Windes und der Gase des Kupolofens
auf die Schlacken mit dem Rauche verschwinden. Die Menge des Eisenoxydes in der
Beschickung ist für weiſses Schwefel haltiges Roheisen geringer als für graues oder
weiſses weniger Schwefel enthaltendes Roheisen zu nehmen; die Schwefel haltigen
Roheisensorten, welche sich leichter oxydiren als die anderen, erzeugen von selbst
in dem oberen Theil des Kupolofens Eisenoxyd, welches sich dem Eisenoxyde der
Beschickung beimischt und nachher im unteren Theile des Ofens reducirt wird. Das
erhaltene Eisen ist weiſs oder grau; sein Kohlenstoffgehalt ist durch den
Reinigungsprozeſs gestiegen, sein Mangangehalt gefallen. Die Schlacke ist weiſs oder
graugelblich weiſs.
Rollet und Daelen wollen
also in dem Kupolofen eine lange Schmelzzone erzeugen, in welcher das Eisen und die
Zuschläge vollständig geschmolzen in innigste Berührung mit einander kommen. Die
stechende unterste tiefstehende Formenreihe soll das Eisen und die Schlacke so lange
wie möglich dem Einflüsse des Windes aussetzen; andererseits soll eine derartige
Anordnung der Formen eine zu starke Kohlenstoffaufnahme des gereinigten Roheisens
verhüten, was bei der hohen Temperatur und der basischen, an Eisen armen Schlacke
unfehlbar eintreten würde, wenn der Wind weniger stark auf das Eisen einwirkt. In
dem Flammofen wird das Eisen gefrischt. Schlacke kann in Folge der ansteigenden
Richtung des Verbindungskanales in denselben nicht eintreten.In wie weit sich die Hoffnungen auf dieses Verfahren verwirklichen werden,
muſs die Erfahrung lehren. Der Patentanspruch lautet: Zur Roheisenreinigung
und zur Stahlerzeugung die Verwendung eines aus Kalk, Fluorcalcium und
Eisenoxyd bestehenden Zuschlages im Hochofen oder Kupolofen in den nach der
Verunreinigung des Roheisens sich richtenden Mengen behufs Gleichzeitiger Ausscheidung von Schwefel und
Phosphor unter Anwendung eines Hochofens oder Kupolofens, dessen unterste
Formen schräg gestellt sind, in Verbindung mit einem Vorherde, welcher mit
dem Hochofen oder Kupolofen durch einen Kanal verbunden ist.
Ein anderes Verfahren zur gleichzeitigen Entfernung des
Phosphors und des Schwefels aus dem Eisen in der basischen Birne wurde von
R. Schliwa in Luxemburg und L. Gildemeister in Dortmund (D. R. P. Nr. 32589 vom 18. November 1884)
vorgeschlagen. Dasselbe erfordert folgende Führung des basischen Prozesses: Man
setzt, nachdem das Silicium oxydirt worden ist, eine kleine Menge leicht
schmelzbaren basischen Materials zu, so daſs die gebildete Kieselsäure verschlackt
wird; diese Schlacke wird dann abgegossen. Bläst man nun wieder, so findet eine
Verbrennung des Kohlenstoffes statt, welche das Bad auf die erforderliche Temperatur
bringt. Sodann setzt man wieder basisches Material zu und verschlackt unter Aufhebung der
Kohlenstoffverbrennung die Phosphorsäure. Diese Schlacke gieſst man wiederum ab und
verbläst dann das Eisen auf den gewünschten Kohlenstoffgehalt. Die Erfinder gehen
hierbei von der Ansicht aus, daſs das Silicium und der Phosphor bei Anwesenheit
genügender Mengen leicht schmelzbarer Basen eine gröſsere Verwandtschaft zum
Sauerstoffe der Gebläseluft haben, als der Kohlenstoff des Eisens. Das Verfahren
lehnt sich eng an das unter D. R. P. Nr. 14468 (vgl. 1882 244 151) patentirte an und es wird deshalb in der Patentschrift darauf
hingewiesen, daſs es nicht ohne Zustimmung der Besitzer jenes Patentes ausgeführt
werden darf.
Schliwa und Gildemeister
wollen den Schwefel aus dem Eisen dadurch entfernen, daſs sie dem Gebläsewinde
Feuchtigkeit (nicht Dampf) beimengen. Zu diesem Zwecke wird in die Windleitung ein
mit Bimssteinstückchen gefülltes Gefäſs eingeschaltet, in welches man gröſsere oder
geringere Mengen heiſsen Wassers eintröpfeln läſst.
Nach dem Patente des Hörder Vereins (D. R. P. Nr. 12700,
vgl. 1882 244 152) findet die Reduction des in der
basischen Birne entphosphorten Eisens nach dem Abziehen der Schlacke bei gekippter
Birne in der Weise statt, daſs Spiegeleisen oder Ferromangan in die Birne
eingeworfen und dann das Eisen in die Gieſspfanne ausgegossen wird. A. Hansen in Dortmund (D. R. P. Nr. 33262 vom 6.
December 1884) will die dabei immer stattfindende, wenn auch geringe Reduction der
Phosphorsäure aus der Schlacke in der Weise vermeiden, daſs er das Spiegeleisen erst
dann zusetzt, wenn die gekippte Birne nach dem Abziehen der Schlacke wieder in die
Höhe gerichtet worden ist, also wieder ein kurzes Durchblasen des Windes nothwendig
wird. Es soll also das Spiegeleisen sofort innig mit dem entphosphorten Eisen
gemischt werden, anstatt es bei ruhiger Lage des Eisenbades längere Zeit mit der
noch immer auf demselben schwimmenden Schlacke in Berührung zu lassen.
Der Kupolofen von Arthur
Greiner und Th. Erpf in Chisnovoda, Ungarn (*
D. R. P. Nr. 33212 vom 28. März 1885) besitzt, wie aus Fig. 4 Taf. 24 zu ersehen
ist, über den untersten Düsen, welche die Verbrennung der Kokes in Kohlensäure
bewirken, noch 3 Reihen Düsen, welche je nach Umständen die Verbrennung der wieder
zu Kohlenoxyd reducirten Kohlensäure in letztere hervorrufen sollen. Die Eröffnung
der einzelnen Reihen der Düsen durch Zurückziehen der Pfropfen richtet sich nach der
Verbrennlichkeit bezieh. der Dichtigkeit und Gröſse der Kokes. Auſser diesen sind
aber noch zwei höher gelegene Reihen kleinerer Düsen vorhanden, die behufs
Erreichung der Verbrennung des hier vorhandenen Kohlenoxydes zu Kohlensäure mit
heiſsem Wind gespeist werden. Die Temperatur dieses Windes kann durch Stellen der
Schieber V beliebig geregelt werden. A ist ein kleiner Winderhitzer, B ein Druckregeler für den eintretenden kalten Wind. Die vier unteren
Reihen Düsen erhalten nur kalten Wind. Durch die 3 Schieber
V kann man den 2 Düsengruppen auch verschieden
gepreſsten Wind zuführen.
Nach Stahl und Eisen, 1886 * S. 96 ist dieser Ofen
bereits in Oesterreich-Ungarn und Deutschland ausgeführt und mit Erfolg in Betrieb.
Ein von der Oesterreichischen Alpinen
Montan-Gesellschaft erbauter Greiner und Erpf'scher Kupolofen von 0m,8 Durchmesser ergab in 12 nach einander folgenden Schmelzungen, bei
denen je 7 bis 14t,5 im Ganzen 100t Eisen gesetzt worden sind, einen Verbrauch von
5k,01 bester westfälischer Kokes auf 100k Eiseneinsatz und damit eine durchschnittliche
Ersparniſs von 33 Procent gegen dem gewöhnlichen Verbrauche (vgl. F. Fischer 1879 231 38. Ledebur 1885 258 172). An
Fällkokes wurden bei jeder Schmelzung 300k
verwendet, wie dies anderen Oefen von gleichem Durchmesser und gleicher Formhöhe
entspricht. Das geschmolzene Eisen war von befriedigender Güte. Von anderen Seiten
gemachte Angaben über den Kokesverbrauch bei nach dem beschriebenen Systeme
umgebauten Kupolöfen sind: 4,14, 4,0, 5,732 bezieh. 4,5 Procent des Eiseneinsatzes.
Dabei wird die Güte der erhaltenen Guſswaaren gleichwertig mit der vor dem Umbau
erzeugten angegeben und von einer Seite bemerkt, daſs die Leistung des Ofens
gestiegen sei.
Textabbildung Bd. 259, S. 367 Von Jens Hansen in Helsingoer, Dänemark (* D.
R. P. Nr. 33895 vom 29. März 1885) ist ein Kupolofen
angegeben, bei welchem die Schmelzung zum gröſsten Theile durch gasförmiges Brennmaterial bewirkt wird. Auſserdem ist
noch ein besonderer Schmelzraum für Abfalleisen o. dgl. und ein Nacherhitzer
vorhanden. Der Feuerraum A ist mittels eines kurzen
Fuchses mit dem unteren Theile des Schmelzschachtes B
verbunden, so daſs die in A entwickelten Gase in
Verbindung mit den geringen Mengen Kokes, welche zusammen mit dem Roheisen in B eingefüllt werden, letzteres niederschmelzen. Ein
Theil der Gase gelangt aus dem Fuchse durch den Kanal G
in den Schmelzraum E für das Abfalleisen, welcher
hinter dem Schachte B liegt. Aus E gehen dann die Gase durch einen Kanal K wieder in den Schmelzschacht B zurück. Das in B und E schmelzende Eisen tropft durch die Kanäle B und I in den
Nacherhitzer C, welcher in Form eines Ringkanales
angeordnet ist und im oberen Theile mit dem unter E
liegenden Schlackenraume D durch einen Kanal in
Verbindung steht. Der
Ofentheil C wird durch Gase erhitzt, die aus dem
Feuerraume A durch den Kanal H und vier Reihen radialer Kanäle H1 in den Raum C
eintreten und denselben durch einen senkrechten, wieder in den Schacht B führenden Kanal verlassen. Die in den Raum A bei f und F eingeblasene Verbrennungsluft hat eine so starke
Pressung, daſs die durch H und H1 in C
eintretenden Gase das hier befindliche geschmolzene Eisen durchdringen und es in
eine drehende Bewegung versetzen, was die Abscheidung der Schlacke erleichtern soll.
Ist der Raum C mit Eisen gefüllt, so wird dasselbe in
bekannter Weise abgestochen. Die Abführung der Schlacke aus D geschieht ebenfalls durch Abstechen. Die Feuerung von A besitzt statt des Rostes einen oben offenen Topf,
welcher auf Rollen unter der Feuerung fortgefahren, mit Brennmaterial gefüllt und
wieder unter die Feuerung gebracht wird. Unterdessen wird das in A befindliche glühende Brennmaterial durch eine
zwischen Topf und A geschobene Platte unterstützt.
Nachdem man diese wieder fortgezogen hat, wird der Boden des Topfes durch eine
mittels Handkurbel und Zahnräder gedrehte Schraube gehoben und dadurch das in
letzterem befindliche Brennmaterial der Feuerstelle langsam näher gerückt.
Gründe für diese eigenthümliche und umständliche Einrichtung des Kupolofens sind von
Hansen nicht angegeben.
Tafeln
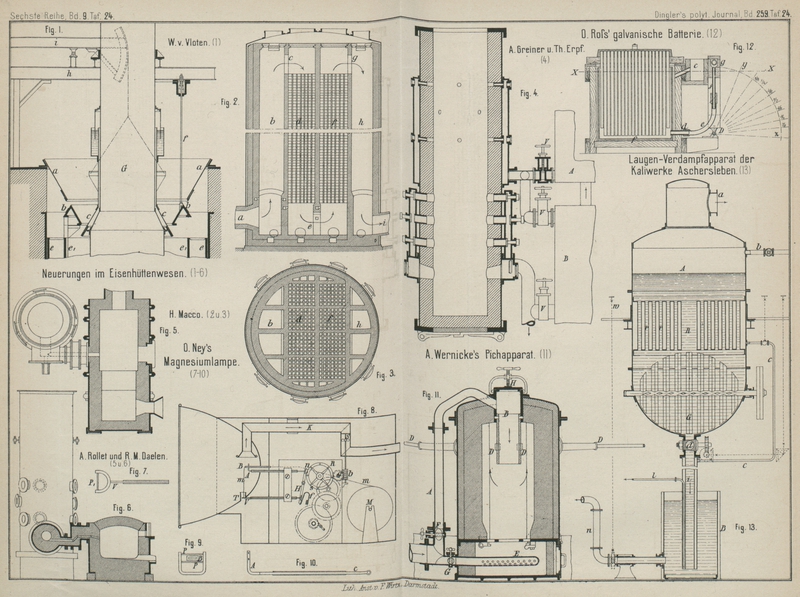