Titel: | Ueber Neuerungen an Pumpen. |
Fundstelle: | Band 259, Jahrgang 1886, S. 477 |
Download: | XML |
Ueber Neuerungen an Pumpen.
(Patentklasse 59. Fortsetzung des Berichtes Bd.
258 S. 469.)
Mit Abbildungen im Texte und auf Tafel 31.
Ueber Neuerungen an Pumpen.
Nach dem Genie civil, 1885 Bd. 7 * S. 285 hat kürzlich
Ch. Tellier in Auteuil bei Paris (vgl. auch * D. R.
P. Kl. 46 Nr. 34749 vom 15. August 1885) der französischen Akademie der
Wissenschaften einen eigenthümlichen Apparat zum Heben von
Flüssigkeiten mittels Ammoniakgas vorgelegt, welches durch die Sonnenwärme verdampft wird. Die Einrichtung, wie sie in
Auteuil praktisch versucht wurde, besteht aus einem unter etwa 45° gegen Süden
geneigten Dache, gebildet aus zwei Kupferplatten, welche in einem geringen Abstande
durch Bolzen mit einander verbunden sind. Dieses Dach dient zur Aufnahme der
Ammoniakflüssigkeit; letztere gibt, wenn sie durch die Sonnenstrahlen erwärmt wird,
Dämpfe ab, welche in einem Behälter gesammelt werden; letzterer steht am Fuſse mit
dem unteren Theile des Daches in Verbindung, so daſs etwa von den Gasen mitgerissene
Flüssigkeit wieder in das Dach zurück flieſsen kann. Die Dämpfe, welche je nach dem
Concentrationsgrade der Ammoniakflüssigkeit einen Druck von 1 bis 3at besitzen, gelangen nun aus dem Behälter durch
ein Rohr in eine im Brunnen, aus welchem das Wasser gehoben werden soll, angeordnete
Hohlkugel, die durch eine Gummischeibe in 2 gleiche Räume getheilt ist. Der untere
Theil der Kugel besitzt ein Saug- und Druckrohr mit den entsprechenden Ventilen.
Angenommen, die Gummischeibe nehme ihre Mittellage ein und der untere Theil der
Kugel sei mit Wasser gefüllt, so wird letzteres in das Druckrohr gedrängt, wenn die
Ammoniakdämpfe auf die Gummischeibe anfangen zu wirken. Um nun die Dämpfe behufs
Ansaugung des Wassers durch die Elasticität der Gummischeibe oder behufs
unmittelbaren Eintrittes des Wassers, wenn die Kugel im Wasser liegt, aus letzterer
zu entfernen, ist mit der Scheibe durch eine Stange ein Schieber verbunden, Welcher
in der tiefsten Stellung den Ausgang für die Dämpfe öffnet. Es hebt sich nun die
Scheibe wieder, worauf in der höchsten Stellung die Umsteuerung des Schiebers
stattfindet. Die Abdämpfe gelangen in einen über Tage stehenden Behälter, durch
welchen mittels einer Kühlschlange kaltes Wasser geleitet wird. Die Dämpfe
verdichten sich hier wieder und wird dann die Ammoniakflüssigkeit von einer kleinen
Pumpe, die mit der Gummischeibe in der Kugel verbunden ist, wieder in das Dach
gedrückt. Nach Tellier soll der in Auteuil aufgestellte
Apparat, welcher für eine Förderung von 500l
Wasser bestimmt ist, 1200l in der Stunde neben.
Die Leistung des Apparates soll aber in heiſsen Ländern bis auf 3000l steigen und sollen dabei Förderhöhen bis zu
20m überwunden werden können.
Eine Dampfpumpe zu Wasserversorgungszwecken von Gordon und Maxwell in Hamilton, Ohio, soll nach dem Techniker, 1885 * S. 206 vielfach in Nordamerika in Anwendung
stehen; sie ist nach dem Zwillingscompoundsysteme, so daſs je zwei aus einem Pumpen-
und zwei Dampfcylindern bestehende Maschinen auf einer Grundplatte ruhen. Die
Pumpencylinder haben je einen nach 2 Seiten wirkenden Tauchkolben. Die beiden
Stopfbüchsen derselben liegen ganz frei, so daſs sie auch während des Betriebes
nachgesehen werden können. Die Ventile sind Gummiring-Klappenventile. Eigenthümlich
ist die Steuerung der Dampfcylinder, welche ein
Durchgehen der Maschine, wenn eines der Hauptwasserleitungsrohre platzt,
verhütet.
Die beiden Schieber des Hoch- und Niederdruckcylinders sind an
einer gemeinsamen Schieberstange befestigt, auf welcher auſserdem noch zwei kleine
Kolben sitzen, von denen der eine in einem kleinen Dampfcylinder und der andere in
einem kleinen Wassercylinder eingeschlossen ist. Ersterer ist mit einem Schieber
versehen, welcher von der Kolbenstange der nebenliegenden Maschine bewegt wird. Die
Verbindung ist eine derartige, daſs kurz, bevor die eine Maschine am Ende ihres
Hubes angelangt ist, der kleine Schieber der anderen Maschine umgesteuert wird. Der
Kolben in dem kleinen Dampfcylinder wird so durch den Dampf von dem einen Ende nach
dem anderen getrieben und steuert somit die beiden groſsen Schieber der dazu
gehörigen Compound-Dampfmaschine um, so daſs diese einen neuen Hub beginnt. Während
diese nun den Hub ausführt, bleibt die andere Maschine stehen, bis jene sie kurz vor
Ende des Hubes wieder umsteuert. Die beiden Einzelmaschinen steuern sich also
gegenseitig um; doch wird der Schieber nicht wie bei den meisten derartigen
Constructionen durch eine mechanische Verbindung, sondern durch Dampfdruck bewegt.
Diese Bewegung ist aber eine langsame; sollte das Pumpengestänge eine zu groſse
Geschwindigkeit annehmen, so wird die Ventilstange wieder zurückgezogen und zwar
gegen den Dampfdruck, welcher auf den Kolben im kleinen Dampfcylinder drückt. Durch
Zurückziehen der Schieber wird der Dampf sogleich wieder vom groſsen Dampfcylinder
abgesperrt und die Maschine beendet ihren Hub ruhig und ohne Stoſs.
Dieses Zurückziehen der Schieber gegen den Dampfdruck in dem
kleinen Dampfcylinder geschieht auf folgende Weise: Auf der Schieberstange sitzt
noch ein zweiter Kolben, welcher in einem kleinen, mit Wasser gefüllten Cylinder
spielt. Die Enden dieses Cylinders stehen durch einen Kanal mit einander in
Verbindung, welcher in der Mitte durch einen Hahn eingeengt ist, so daſs das Wasser
nur langsam von dem einen Ende des Cylinders nach dem anderen flieſsen kann und die
Bewegung der Schieberstange also verzögert wird. Dieser Wassercylinder ist nicht
fest, sondern steht mit der Kolbenstange seiner Maschine durch Hebel so in
Verbindung, daſs derselbe bei jedem Hube auf einer Bahn nach der einen oder anderen
Seite geschoben wird. Diese Verschiebungen sind entgegengesetzt der vorher
stattgehabten Schieberbewegung und gehen bei richtigem Betriebe nur langsam vor
sich, so daſs die Bewegung der Schieberstange verzögert wird. Sollte aber die
Kolbenstange eine gefährliche Geschwindigkeit annehmen, so wird auch der
Wassercylinder schnell verschoben. Der Kolben in demselben muſs dieser schnellen
Bewegung folgen, trotz des Gegendruckes in dem kleinen Dampfcylinder, da das Wasser
in dem Cylinder einen zu groſsen Widerstand bietet. Auf diese Weise ist also die
Maschine vor einer gefährlichen Kolbengeschwindigkeit geschützt.
Zum Speisen von selbstthätigen Feuerlöscheinrichtungen
(vgl. Parmelle bezieh. Grinnell 1882 245 140. 1885 256 * 396. 257 * 220. Oriolle 1883 247 * 45. Gray 1885 256 * 396), welche
in nordamerikanischen Fabriken vielfach in Anwendung stehen, wird nach Engineering, 1885 Bd. 40 * S. 466 verschiedentlich die
Worthington'sche Dampfpumpe (vgl. 1883 250 5) benutzt. Die an
der Decke der Fabrikräume angebrachten Siebrohre oder Brausen stehen dann
unmittelbar mit dem Steigrohre der Dampfpumpe in Verbindung. Schmilzt eines der
Abschluſsventile der Zuleitungsrohre, so tritt Wasser in die Brause. Sind jedoch
alle Ventile geschlossen, so herrscht in dem Steigrohre der Dampfpumpe ein
bestimmter Druck, der sich vom Windkessel der letzteren aus bis in einen kleinen
Cylinder fortsetzt, dessen Kolben unmittelbar mit dem Dampfzuleitungsventile für die
Pumpe verbunden ist. Der kleine Kolben wird nun für gewöhnlich durch eine Feder
niedergehalten, deren Spannung dem erforderlichen Drucke in den Löschleitungen
entspricht. Dadurch wird aber auch das Dampfventil geschlossen gehalten, so daſs die
Pumpe stillsteht. Findet nun in den Löschleitungen bei Oeffnung eines Brauserohres
eine Druck Verminderung statt, so öffnet die Feder das entlastete Dampfventil und
die Pumpe tritt so lange in Thätigkeit, bis das geschmolzene Ventil wieder ersetzt
ist, oder das Steigrohr sonstwie abgeschlossen wird. Damit die Dampfpumpe zu jeder
Zeit sofort in Thätigkeit treten kann, ist die Dampfleitung vor dem Absperrventile
und jedes Ende des Dampfcylinders mit einem Dampfwasserableiter versehen, welcher
das sich in der Leitung niederschlagende Wasser ununterbrochen abführt.
G. Herbst in Bochum (* D. R. P. Nr. 33815 vom 18. April
1885) hat einen Regulator für Dampfpumpen ohne
Hilfsdrehung vorgeschlagen, welcher die Aenderung der Bewegungen des
Pumpenkolbens beim Hubwechsel nur langsam erfolgen läſst und das Durchschlagen des
Kolbens verhindert, für den Fall, daſs im Betriebe der Pumpen eine Störung eintritt.
Zu diesem Zwecke benutzt Herbst die in den Pumpenräumen
entstehenden Druckänderungen zur Bewegung eines Regulatorkolbens, welcher
unmittelbar mit dem Drosselventile des Dampfcylinders verbunden ist. Der in Fig. 1 und 2 Taf. 31
dargestellte Regulator ist für eine Pumpe mit 2 Tauchkolben von entgegengesetzter
Bewegungs-i'ichtung bestimmt. Durch die Rohrstutzen a1 und a2 steht je eine Seite des in dem Cylinder C beweglichen Regulatorkolbens K mit je einem Arbeitsraume (dem Raume zwischen Druck- und Saugventil) der
Pumpe in Verbindung. Sobald in beiden Arbeitsräumen und somit auf beiden Seiten des
Kolbens K gleicher Druck herrscht, wird derselbe durch
die federn f1 und f2 in seiner
Mittelstellung erhalten. Der Kolben K wirkt auf ein
Drosselventil V, welches in die zur Dampfmaschine
führende Leitung D eingeschaltet ist. Dieses Ventil
schlieſst nie ganz ab, so daſs selbst bei der Mittelstellung von K noch eine Bewegung des Pumpenkolbens möglich bleibt,
dieselbe aber nur sehr langsam erfolgen kann. Da nun bei jedem Kolbenwechsel die
Umsteuerung, welche vom Regulator gar nicht beeinfluſst wird, erfolgt, so muſs eine
Druckänderung in den Arbeitsräumen eintreten; dadurch ist aber bedingt, daſs die
Druckwirkungen in denselben in einem Punkte gleich sein müssen und somit K seine Mittelstellung einnehmen muſs. Hieraus folgt,
daſs bei jedem Hubwechsel durch den Regulator eine Drosselung des Dampfes erfolgt. Erst, wenn in
beiden Arbeitsräumen der richtige Druckunterschied eingetreten ist, kann die
Bewegung ungehindert vor sich gehen.
Tritt nun irgend eine Störung im Gange der Pumpe ein, ist z.B. beim Hub Wechsel
irgend eines der Ventile offen geblieben, so ist in beiden Arbeitsräumen ganz oder
nahezu der gleiche Druck. Die Pumpe kann aber, wie es sonst der Fall wäre, nicht
durchgehen, weil der Regulatorkolben K in diesem Falle
seine Mittelstellung einnimmt und behält, die Maschine also so lange gedrosselt
bleibt, bis die Störung beseitigt ist.
Dieselbe Wirkung tritt ein beim Bruche eines Ventilkastens, beim Platzen eines
Druckrohres, beim Ansaugen von Luft durch die Pumpe u.s.w. Je geringer der
Druckunterschied, je gröſser also die Gefahr des Durchschlagens ist, desto schneller
ist die Wirkung des Regulators.
Bei einfach wirkenden Pumpen erhält der Regulator zwei Cylinder C mit Kolben K. Jeder der
Kolben erhält aber nur eine Feder, welche denselben bei Druckgleichheit in eine
Endstellung bringt. Die Stutzen a1 und a2 des einen Cylinders sind an die Räume, welche das
Druckventil trennt, angeschlossen, die des anderen Cylinders mit den durch das
Saugventil getrennten Räumen in Verbindung gebracht. Der Anschluſs an diese Räume
erfolgt derart, daſs die Feder des einen Cylinders durch den Druck im Druckrohre,
die des anderen aber durch den Druck im Arbeitsraume zusammengepreſst wird. Zu jeder
Bewegungsrichtung des Pumpenkolbens gehört, bei richtigem Gange der Pumpe, eine
bestimmte Stellung des Regulatorkolbens. Die vereinigte Bewegung beider Kolben wird
durch Hebel u.s.w. derart auf die Drosselung übertragen, daſs nur bei deren
richtiger Stellung die volle Kraftwirkung ermöglicht ist, bis dahin aber die
Bewegung verhindert wird.
Ueber den Erdöl-Transport durch Dampfpumpen und
meilenlange Röhrenleitungen in den Vereinigten Staaten Nordamerikas (vgl. 1877 225 504. 223 438. 1874 214 420) bringt Engineering,
1885 Bd. 40 * S. 108 folgende Mittheilungen. Die verwendeten Pumpen sind meist
Zwillings-Compoundpumpen mit je zwei Pumpencylindern und einem gemeinschaftlichen
Tauchkolben. Die längsten Röhrenleitungen besitzt die National Transit Company, welche im J. 1881 fertig gestellt wurden, 60
Millionen Mark kosteten und zusammen eine Länge von 1416km besitzen. Die längste Leitung ist 480km lang und reicht von Olean (im Oel-Bezirk) bis Brooklyn bezieh. Bajonne.
Der lichte Durchmesser der Röhren beträgt bei Olean 101mm,6 und bei New-York 152mm,4. Auf der
ganzen Strecke sind 11 Pumpwerke vorhanden. Der Druck in den Röhren steigt bis zu
10at. Die Röhren sind aus Schmiedeisen in
Längen von 5m,5 gewalzt, mit über einander
geschweiſsten Rändern versehen und werden mit einander mittels Muffen verschraubt.
Ausgleichsvorrichtungen, welche den Ausdehnungen beim Temperatur Wechsel Rechnung tragen, sind nicht
vorhanden. Die Ausdehnung und Zusammenziehung der Röhren gestatten die groſsen frei
liegenden Curven, in welchen dieselben angelegt sind. Häufig sind aber auch die
Röhren in Gräben von etwa 1m Tiefe eingebettet.
Die Pumpwerke liegen im Mittel 48km aus einander-
der Abstand beträgt aber bei einigen bis zu 170km.
Der gröſste Höhenunterschied der Pumpwerke beträgt etwa 466m. Auf jeder Pumpstation sind 2 Behälter von 27m,5 Durchmesser und 9m,1 Tiefe angeordnet, welche das Oel von der zunächst gelegenen Pumpe
aufnehmen und es unmittelbar an das Saugrohr der nächsten Pumpe abgeben. Jede
Pumpstation kann aber ausgeschaltet werden, so daſs sie einfach überschlagen wird
und z.B. die 4. Pumpstation aus der zweiten ihr Oel erhält. Die Worthington'schen Zwillings-Compounddampfpumpen (vgl.
1883 250 5) haben sich am besten zur Oelbeförderung
bewährt; sie haben eine Leistung von 72cbm in der
Stunde und können gegen einen Druck von ungefähr 15at arbeiten; ihre Stärke wechselt von 200 bis zu 800 Pferd.Die erste Versendung des Erdöles erfolgte in Fässern und wurde bis zum J.
1865 so ausgeführt. Bei dem stark wachsenden Ausbringen verschickte man das
Oel in eisernen Behältern, die auf Eisenbahnwagen gesetzt wurden und etwa
9cbm Oel faſsten. 1871 ersetzte man
die Behälter, wovon gewöhnlich zwei auf einem Wagenuntergestelle standen,
durch cylindrische Kessel, welche auf dem Untergestell befestigt waren und
bis zu 22cbm Oel aufnahmen. Aber schon im
J. 1876 waren 3200km Röhrenleitungen
gelegt und stieg in Folge dessen das Ausbringen an Oel im J. 1884 bis auf
4552821cbm (im Werthe von 85 Millionen
M.) gegen 2016290cbm im J. 1870. Im J.
1862 betrugen die Kosten für die Beförderung von 300l Oel aus dem Oelbezirke bis nach New-York
35 M., heute betragen dieselben 50 Pf. Der erste Oelbrunnen zur Gewinnung
des Oeles im Groſsen wurde am 28. August 1859 niedergebracht und erreichte
die Oelschicht mit 22m. Es begann dann
eine wilde Spekulation, so daſs bald eine Anzahl von Gesellschaften und
Bohrlöchern zur Ausnutzung derselben entstanden. Darunter sind Brunnen,
welche bis zu 567cbm Oel im Tage ergaben.
Der Preis des Oeles fiel auf 0,1, nämlich von 42,50 M. auf 4,25 M. für 1
Faſs (163l,5).
Um das Gestänge von Tiefbrunnen-Druckpumpen lediglich
auf Zug zu beanspruchen, haben nach Engineering, 1885
Bd. 40 * S. 468 John Morison und Rob. Armstrong in Dalkeith folgende Einrichtung
getroffen: Die Cylinder von zwei neben einander liegenden, einfach wirkenden
Druckpumpen mit Scheibenkolben sind am oberen Ende durch einen kurzen Rohrstutzen
vom Querschnitte der Cylinder mit einander verbunden, von diesem Stutzen geht ein
enges Gasrohr aus, das in einen Wasserbehälter mündet, welcher höher als der Ausguſs
der Pumpen steht. Diese Wassersäule ist in Folge dessen im Stande, das im Steigrohre
der Pumpe befindliche Wasser mittels der Pumpenkolben zum Ausgusse zu heben. An die
Kolbenstangen der beiden Pumpen greifen zwei dünne Gestänge oder auch Drahtseile an,
welche über Tage mit einem doppelarmigen, von irgend einem Motor bewegten Hebel
verbunden sind. Wird dieser also hin und her bewegt, so schieben sich auch die
Pumpenkolben in
entgegengesetzten Richtungen hin und her, wobei aber die Gestänge in Folge des auf
den Kolben lastenden Wasserdruckes immer gespannt bleiben, so daſs schädliche
Biegungen und Stauchungen derselben ausgeschlossen sind. Wird der eine Kolben
angehoben, in welchem Falle die betreffende Pumpe saugt, so hat der Motor eine
Arbeit zu verrichten, welche einer Wassersäule von dem Querschnitte des Kolbens und
der Länge des Gasrohres entspricht. Trotzdem findet aber eine Bewegung des Wassers
in letzterem nicht statt, weil die von dem einen Kolben gehobene Wassermenge gleich
in den anderen Cylinder eintritt und hier auf die Entfernung des angesaugten Wassers
in das Pumpensteigrohr hinwirkt. Dabei bleibt aber doch das betreffende Gestänge
immer gespannt, weil der Druck über dem Kolben gröſser
ist als unter demselben.
Gegen die bekannte Anordnung von Gewichten zu demselben Zwecke hat die beschriebene
hydraulische Kraftübertragung den Vortheil, daſs
sie fast gar keinen Raum im Brunnenschachte in Anspruch nimmt. Auſserdem wird das
durch die Stopfbüchsen der Pumpenkolbenstangen verloren gehende Wasser
ununterbrochen wieder ersetzt, weil die betreffenden Räume durch das Gasrohr immer
mit dem über Tage stehenden Behälter in Verbindung stehen.
Bei der Pumpe mit hydraulischem Gestänge von Wilh. Fritz in Tübingen (* D. R. P. Nr. 33813 vom 12.
April 1885) ist das die Kraft- und Arbeitspumpe verbindende Rohr gleichzeitig
Steigrohr der Arbeitspumpe. Die Arbeitspumpe (Fig. 9 Taf. 31) hat einen
hohlen Scheibenkolben d und einen sich daran
anschlieſsenden kleineren Röhrenkolben d1, welcher oben mit Durchbrechungen und unten mit
einem sich nach innen öffnenden Ventile versehen ist. Die Kolben d und d1 sind an ihrer Kolbenstange mit einem Gewichte f versehen, welches im Stande ist, der ganzen
Steigwassersäule bis zur Kraftpumpe, vermindert um deren zulässige Saughöhe, das
Gleichgewicht zu halten. Der Cylinder des Röhrenkolbens d taucht in seiner ganzen Höhe in das Saugwasser. Vom unteren Ende des
Pumpencylinders e geht das Steigrohr bis zur Kraftpumpe
(Fig. 10
Taf. 31), die mit einer Fortsetzung des Steigrohres mit Steigventil c und einen Napfkolben a,
der von irgend einem Motor bewegt wird, versehen ist. Bewegt sich der Kolben a in die Höhe, so drücken die Kolben d und d1 der Arbeitspumpe unter dem Einflüsse des Gewichtes
f eine gewisse Wassermenge durch das Steigrohr in
den Cylinder der Kraftpumpe. Geht der Kraftkolben herunter, so wird ein Theil des
Wassers durch c zum Ausgusse gedrückt, während ein
anderer Theil unter den Kolben d zurücktritt und zur
Hebung von d und d1 dient; d1 saugt dann dabei Wasser an.
Statt der Kraftpumpe (Fig. 10) kann auch eine
wie die Arbeitspumpe (Fig. 9) eingerichtete
Pumpe verwendet werden, wenn nur der Röhrenkolben mit einem sich nach unten
öffnenden Ventile versehen ist. Das von der Arbeitspumpe kommende Steigrohr mündet in den
unteren Theil des Cylinders vom Kolben d ein, während
das Ausguſsrohr mit dem Ventile c sich im unteren
Theile des Cylinders vom Kolben a ansetzt. Die Höhlung
im Kolben d, die mit Luft gefüllt ist, dient als
Windkessel.
Die doppelt wirkende Pumpe von Eduard Buſs in St. Gallen und Em. Müller in
Arbon, Schweiz (* D. R. P. Nr. 33826 vom 9. Juni 1885) besitzt 2 Kolben und 2
Ventile. Wie aus Fig. 11 Taf. 31 zu entnehmen, sind die Kolben Napfkolben und sitzen
unmittelbar an zwei Zugstangen s1 und s2, die durch Schwingung des doppelarmigen Hebels H auf und nieder bewegt werden. Unter dem unteren
Kolben liegt das Saugrohr S, über dem oberen Kolben das
Druckrohr D. Der von den beiden Kolben begrenzte Raum
K steht durch ein Saug- bezieh. Druckventil mit dem
Saug- bezieh. Druckrohre in Verbindung. Nähern sich die Kolben einander, so drücken
sie aus dem Raume K durch das Druckventil eine
Wassermenge von 2hq, wenn h der Kolbenhub und q der Kolbenquerschnitt
ist. Davon tritt eine Wassermenge von hq wieder über
den oberen Kolben, ist also für die Förderung dieses Hubes verloren. Der untere
Kolben geht bezüglich seiner Saugwirkung leer. Gehen die Kolben aus einander, so
drückt der obere das über demselben stehende Wasser hq
in das Druckrohr D und beide Kolben saugen eine
Wassermenge 2hq in den Raum K. Die Pumpe ist also eine doppelt wirkende. Die Zahl ihrer Ventile ist
allerdings auf 2 vermindert, dafür ist aber statt der 2 fehlenden Ventile eine
Kolbenliderung mehr in den Kauf zu nehmen, was als ein Vortheil nicht angesehen
werden kann.
Bei der in Fig.
14 bis 16 Taf. 31 abgebildeten, sowohl als Motor und als Luft- und Wasserpumpe
verwendbaren Kolbenmaschine mit schwingendem Cylinder
von L. Mégy in Paris (vgl. A.
Schmid 1875 215 * 15) ist über dem Cylinder ein
schwingender Muschelschieber M mit Kreisbogen-Spiegel
angeordnet, so daſs die Schildzapfen lediglich zur Zu- und Abführung der Flüssigkeit
dienen. Der Muschelschieber M ist auf einer quer durch
das Schiebergehäuse gehenden Achse befestigt, um welche der Schieberspiegel
cylindrisch ist. Auſserhalb des Schiebergehäuses ist auf diese Achse ein Arm H aufgekeilt, der in einem in dem feststehenden Arme
S angeordneten Kugellager geführt ist. Es ist nun
klar, daſs sich der Schieber bei den Schwingungen des Cylinders, von seinem Arme H geführt, auf seinem Spiegel hin und her bewegen muſs,
was die Vertheilung der Flüssigkeit bewirkt. Die gezeichnete Schieberbewegung wird
wegen des zulässigen groſsen Drehwinkels vom Schieber bei Wassermotoren und Pumpen
angewendet, während bei Dampfmotoren und Luftpumpen der als Hahn ausgebildete
Schieberarm unmittelbar von einem auf der Kurbelwelle sitzenden Excenter bewegt
wird. Als Vorzüge dieser Maschine werden folgende angegeben: 1) Der Schluſs und die
Eröffnung der Schieberöffnungen geschieht in Folge der eigenthümlichen Bewegung des
Schiebers gegen den sich drehenden Cylinder sehr schnell; man kann deshalb bis zu
300 Umdrehungen in der Minute gehen, ohne hydraulische Stöſse befürchten zu müssen.
2) Die Schieberflächen schleifen sich während des Betriebes immer dichter auf
einander, was durch Dauerversuche bewiesen erscheint. 3) Die Verbindungen der
Zuleitungs- und Ableitungsrohre mit den Cylinderschildzapfen sind einfach und leicht
dicht zu halten. 4) Der einseitige Druck der Kraftflüssigkeit auf den Cylinder wird
durch eine Laufrolle e (Fig. 16) mit Stahlbahn
aufgenommen. 5) Die Kanäle a und a1 betragen dem
Querschnitte nach ¼ der Kolbenfläche.
Die Leistung der Maschine als hydraulischer Motor soll unter den günstigsten
Verhältnissen 90 Proc. betragen, im Mittel 75 Proc. bei einer Geschwindigkeit von
100 bis 160 Umdrehungen; die Leistung soll aber nicht unter 30 Proc. bei 300
Umdrehungen fallen.
Osc. Smreker in Mannheim (* D. R. P. Nr. 33824 vom 31.
Mai 1885) hat einen Saugkorb für Rohrbrunnen angegeben,
welcher die gewöhnliche Einrichtung hat, am Boden aber geschlossen ist. Um den an
das Saugrohr der Pumpe angeschlossenen Saugkorb b ist,
wie aus Fig. 3
Taf. 31 zu entnehmen, ein Schutzkorb angebracht, der aus einem durchlochten und
auſsen mit einem weitmaschigen Drahtgewebe umgebenen Rohre a besteht. Auf der Innenfläche dieses Rohres sind vor den Oeffnungen
desselben kleine schräge Schutzdächer angeordnet, welche die vom Wasser
mitgerissenen schweren Stoffe nach unten ableiten sollen. Hier setzen sie sich ab
und können durch das Rohr d, auf welches über Tage eine
kleine Sandpumpe aufgesetzt wird, abgesaugt werden. Das mit Schutzkorb versehene
Rohr wird in das verröhrte Bohrloch eingesenkt und dann das Saugrohr des
Rohrbrunnens in ersteres eingesetzt.
Auf der Görlitzer Gewerbe- und Industrieausstellung 1885 hatte C. Eichler in Berlin einen Pulsometer mit seiner Pendelsteuerung (vgl. 1884 251 * 473) im Betriebe. Die Kammerinhalte desselben betrugen je 112l, die Länge des Pendelventiles war 200mm, die Saughöhe 1m bei 3m langer Saugrohrleitung. Die
nach dem 8m hoch gelegenen Ausguſs führende
Rohrleitung war mehrfach gekrümmt, hatte 225mm
lichte Weite und 34m Länge. Zwei am Pulsometer
angebrachte Manometer zeigten die Spannung des einströmenden Dampfes und die
Widerstandshöhe der Wassersäule in der Druckleitung an. Die Anzahl der Pulsschläge
in der Minute betrug 16 bis 50, welche einer Förderung von ungefähr 1600 bis 5000l entsprachen.
Zwei Versuche mit diesem Pulsometer hatten nach der Zeitschrift des Vereins deutscher Ingenieure, 1885 * S.
755 folgende Ergebnisse:
Betriebsdampfspannung
4at
bezieh.
6at
Einströmdampfspannung (gedrosselt)
1,6at
1,8at
Widerstandshöhe im Druckrohre
1,2at
1,3at
Inhalt einer Pulsometerkammer
112l
112l
Füllung während eines Hubes
100l
95l
Füllungs- bezieh.
Wirkungsgrad
90
Proc. bezieh.
85 Proc.
Pulsschläge in 1 Minute
40
42
Leistung
in 1 Minute
4000l
3990l
„
„ „ Stunde
240000l
239400l
Speisewasserverbrauch in 1
Stunde
300l
375l
1k Dampf fördert Wasser
800k
638k
Erwärmung des gehobenen
Wassers
0,8°
1,0°
Leistung
8e
8e
Dampfverbrauch für 1e und Stunde
37,5k
47k.
Aufgenommene Diagramme der Arbeitsleistung in den
Pulsometerkammern zeigten sehr regelmäſsige Curven.
Bei dem mit Druckluft arbeitenden Wasserheber von Wilh. Schranz in Laurenburg a. d. Lahn (* D. R. P. Nr.
33822 vom 22. Mai 1885) öffnen sich die Eintrittsventile b und b1
(Fig. 12
und 13 Taf.
31), wenn der Apparat unter Wasser liegt und leere Kammern c und c1
besitzt. Das Wasser tritt dann in die Kammern ein und die darin befindlichen
Schwimmer s und s1 verschlieſsen durch die oben an deren Stangen
angebrachten Ventile die nach dem Steuerapparate führenden Oeffnungen e und e1. Wird nun durch das Rohr f Druckluft in den Steuerapparat (Fig. 12) eingeführt und
der entlastete Kolben g steht, wie gezeichnet, links,
so strömt dieselbe durch das Rohr h in die Kammer c und drückt die darin enthaltene Flüssigkeit durch das
Rohr i in das beiden Kammern gemeinsame Steigrohr l und auf die dem Luftdrucke entsprechende Höhe.
Nachdem die Flüssigkeit in c so weit verdrängt ist,
daſs der Schwimmer s sinkt, wird die Ventilöffnung e frei; es strömt dann durch letztere und das
anschlieſsende Rohr m ein Theil der in c enthaltenen Luft auf die Ringfläche p des Kolbens g, schiebt
denselben nach rechts und bewirkt auf diese Weise die Umsteuerung. Sobald diese
erfolgt ist, entweicht die in c enthaltene Luft durch
das Rohr h und den Hohlraum n des Kolbens g unmittelbar oder auch, wenn
der Steuerapparat sich in der Flüssigkeit befindet, durch das Rohr o. Statt der Hohlräume n
und n1 können in den
Kolben auch ebenso wie für die Einströmung Hälse eingedreht sein.
Die durch das Rohr f einströmende Luft gelangt nun durch
den Steuerapparat und das Rohr h1 in die Kammer c1 und wirkt ebenso wie in c, indem sie die Flüssigkeit in das Steigrohr l drückt. Ist die Kammer c1 genügend entleert und die Umsteuerung durch Sinken
des Schwimmers s1
erfolgt, so hat sich vorher der Behälter c wieder
gefüllt, gleichzeitig der darin befindliche Schwimmer d
die Oeffnung e geschlossen und das Spiel beginnt von
Neuem.
Der Schranz'sche Apparat soll beim Sümpfen von
Schächten, Heben von Trinkwasser aus Brunnen u.s.w. Verwendung finden.
Eine nach bekanntem Prinzipe (vgl. Stewart 1883 250 * 145. Oehlmann 1885 255 * 278) von A. Malcotte
aîné construirte rotirende Pumpe (vgl. Revue industrielle, 1885 * S. 474) verdient wegen ihrer
einfachen Einrichtung Beachtung. Wie in Fig. 4 und 5 Taf. 31 veranschaulicht,
sind in einem
cylindrischen Gehäuse A mit je zwei Ein- und Auslässen
auf jeder Seite vier lose sich der Innenwand des Gehäuses anpassende Ringstücke B angeordnet, die durch eine mitten zwischen denselben
angebrachte Röhre G aus einander und in dichter
Berührung mit dem Gehäuseinneren gehalten werden. In der Röhre G liegt excentrisch eine Welle D, die in langen Deckellagern geführt ist und auf welcher Scheiben I befestigt sind, die in Ausdrehungen der Gehäusedeckel
passen. Auf diesen Scheiben sind je vier nach innen zeigende Stifte gleichmäſsig
angeordnet, die in Schlitze der Kopfflächen der hohlen Ringstücke B eingreifen. Dreht man nun die Welle D, so werden die Stücke B
von den Scheiben mitgenommen, aber in Folge der Excentricität der Wellenlager mit
verschiedenen Winkelgeschwindigkeiten, was ein
abwechselndes Nähern und Entfernen der Kolben bewirkt. Hierdurch wird das Wasser in
bekannter Weise angesaugt und fortgedrückt.
Textabbildung Bd. 259, S. 486 Wie bereits mehrfach zum Vorschieben der Kolben an rotirenden Maschinen
die Schwere der Kolben und die Centrifugalkraft benutzt wurde (vgl. Beale 1844 91 * 264. A. Morin 1884 253 * 7 u.a.),
so ist dies auch bei einer auf der Erfindungsausstellung in London 1885 von G. J. Worssam und Sohn in London gezeigten rotirenden Pumpe der Fall, welche hauptsächlich zur
Förderung von dicken Flüssigkeiten bestimmt ist. Die
innere Einrichtung derselben ist aus der nebenstehenden Textfigur ersichtlich. In
einem cylindrischen Gehäuse dreht sich excentrisch ein Rad, in dessen vier
Aussparungen Rollen lose liegen, so daſs dieselben bei der Drehung des Rades durch
die Centrifugalkraft sich an die Gehäusewandung anlegen und dadurch die so
eingeschlossene Flüssigkeit mit fortnehmen. Das Rad ist aus Phosphorbronze, die
Rollen aus Stahl hergestellt.
Die vornehmlich als Gebläse dienende rotirende Maschine von Hermann
Enke in Weiſsenfels (* D. R. P. Nr. 33161 vom 11. November 1884) zeichnet
sich dadurch aus, daſs alle Flächen bis auf zwei schmale Streifen, die gesondert
bearbeitet werden müssen, auf der gewöhnlichen Drehbank herstellbar sind. Die
Maschine gehört zur Gruppe der Räderkapselwerke und kann als eine Verdoppelung des
von Hofmann und Zinkeisen in Zwickau (* D. R. P. Nr.
31495 vom 25. September 1884) angegebenen Kapselwerkes angesehen werden. Das Gehäuse
G (Fig. 7 und 8 Taf. 31) zerfällt in
eine obere gröſsere und eine untere kleinere Kammer, wovon für jede sich mit
entsprechenden Deckeln D und D1, d und d1 verschlossen wird. Die mit ihrer
Achse in den Deckeln D und D1 gelagerte Scheibe S mit den daran sitzenden Kolben K und K1 ist mit der in den Deckeln d und d1
gelagerten Trommel T durch Zahnräder verbunden und
erfahren beide bei entgegengesetzter Drehrichtung die gleichen Umdrehungszahlen. An
den Deckeln D und D1 sind Cylinder Z und
Z1 angeordnet,
welche so tief von beiden Seiten in das Gehäuse eintreten, daſs nur ein Zwischenraum
von der Stärke der Scheibe S freibleibt, in welchem
letztere ihren Platz findet. Die Ausschnitte ab an
diesen Cylindern haben in Folge gemeinschaftlicher Bearbeitung genau dieselbe
Kreisform wie die untere Gehäusewand, so daſs die Trommel T bei ihrer Drehung beide Kreisflächen dicht berührt; dies ist erreicht,
wenn die Ausschnitte ab zu den Trommelaussparungen mno in solche Maſsverhältnisse gebracht werden, daſs
zur Zeit, wo sich beide gegenüber stehen, mno von ab vollständig gedeckt wird und noch auf beiden Seiten
eine Ueberdeckung vorhanden ist. Die Kolben K und K1 sitzen an der
zwischen den beiden Cylindern Z und Z1 schleifenden Scheibe
S und werden von dieser an der oberen Gehäusewand
und um die Cylinder dicht herumgeführt. Die Aussparungen mno, durch welche die Kolben gehen, gestatten, denselben solche
Abmessungen geben zu können, daſs sie trotz ihrer Länge fest und ihre
Dichtungsflächen genügend breit werden; ihre äuſsere Form entspricht den
Trommelaussparungen und ist dabei nur so viel freier Raum gelassen, daſs eine
Berührung beider Theile nicht vorkommen kann. Die Trommel T hat längere Abmessungen als die Kolben K
und K1; die für
letztere nöthigen Aussparungen nehmen nicht die ganze Länge in Anspruch, sondern
lassen rechts und links Scheiben s und s1 stehen, deren
äuſsere Flächen dicht an die Deckel d und d1 anlaufen. Die
Scheibe S hat die in Fig. 7 gezeichnete Form
erhalten; ihr entsprechend ist der Mitteltheil der Trommel T gestaltet, so daſs sich beide Theile beständig dicht abwickeln. Um die
Abwickelung so sanft wie möglich zu gestalten, ist der Trommeltheil mit elastischen
Einlagen versehen, welche nöthigenfalls gegen die Scheibe S nachgeben.
Zum Fördern dicker Flüssigkeiten, wie z.B. Thonbrei,
bringt A. J. A. Dumoulin in Paris (* D. R. P. Nr. 33819
vom 20. Mai 1885) eine einfach wirkende Druckpumpe mit
Tauchkolben und einem Ventil in Vorschlag. Das fehlende
Saugventil wird durch den Kolben ersetzt. Der mit einem Messingfutter versehene
Cylinder C (Fig. 6 Taf. 31) liegt
wagerecht und bildet mit einem Trichteraufsatze B ein
Stück. Der Trichter B ist in dem unteren Theile des
letzteren so gelagert, daſs in demselben eingefülltes Material von allen Seiten den
Cylinder C umgibt und durch die Schlitze a in diesen hinein gelangen kann. Diese Schlitze liegen
dicht vor der Stopfbüchse, so daſs sie nach vollendetem Hube des Kolbens von diesem
ganz frei gelegt werden. Der Kolben hat behufs
leichterer Verdrängung der dickflüssigen Massen vorn eine kegelförmige Spitze. An
den Cylinder setzt sich das Druckrohr T an, welches mit
einem
Kegelsteigventil V mit von auſsen beweglicher Spindel
versehen ist. Die Bewegung des Kolbens geschieht durch eine Kurbel mit doppeltem
Rädervorgelege. Von diesem aus wird auch eine im Trichter liegende Rührvorrichtung
behufs Mischung der Füllung von B und Förderung
derselben gegen den Cylinder hin umgedreht. Geht der Kolben nach links, so entsteht
zwischen diesem und dem Steigventile ein luftleerer Raum, bis der Kolben die
Schlitze o in der Cylinderwandung frei legt. Die
breiige Masse wird dann in Folge des Atmosphärendruckes in den Cylinder
hineingedrückt und beim Rückgange des Kolbens und, nachdem derselbe die Schlitze a wieder geschlossen hat, in das Druckrohr befördert.
Es ist klar, daſs eine derartige Pumpe ihrem Saughube erhebliche Widerstände
entgegensetzt; trotzdem kann sie sich aber zu dem angegebenen Zwecke sehr wohl
eignen.
Tafeln
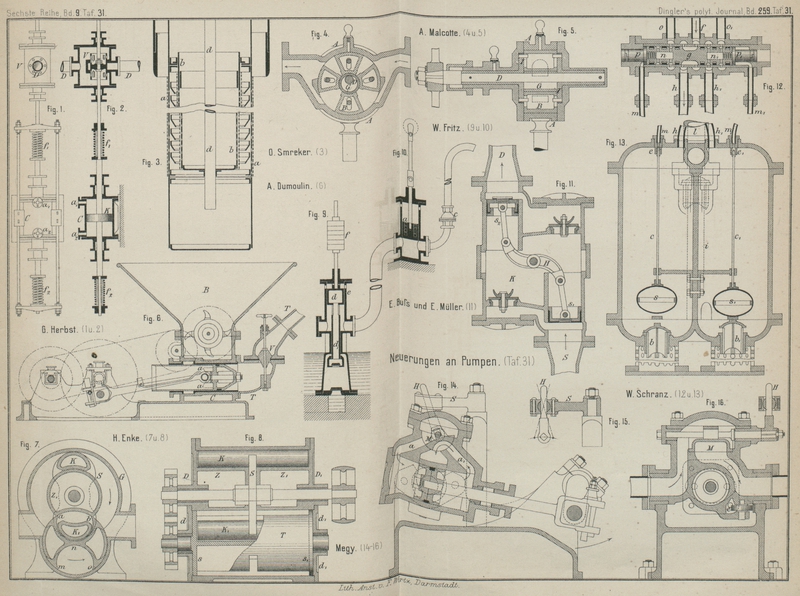