Titel: | Fabrikation schmiedeiserner Gasleitungsröhren aus Holzkohleneisen in Brezowa (Ungarn); von Anton v. Kerpely. |
Autor: | Anton v. Kerpely |
Fundstelle: | Band 264, Jahrgang 1887, S. 201 |
Download: | XML |
Fabrikation schmiedeiserner Gasleitungsröhren aus
Holzkohleneisen in Brezowa (Ungarn); von Anton v. Kerpely.Nach einem Vortrage, gehalten auf der 4. Generalversammlung des Vereines der
Gasindustriellen in Oesterreich-Ungarn in Budapest 1885.
Mit Abbildungen auf Tafel
13.
Kerpely, über Fabrikation schmiedeiserner
Gasleitungsröhren.
Zur Erzeugung schmiedeiserner Rohre sind derzeit zwei von einander wesentlich
verschiedene Methoden in Anwendung, wonach man im Allgemeinen gezogene und gewalzte
Röhren unterscheidet.
Die gezogenen Rohre nennt man schlechtweg auch Gasröhren; die gewalzten,
nachdem man sie in überwiegender Menge zu Dampfkesseln verwendet, Siederöhren; diese Eintheilung ist aber durchaus nicht
gerechtfertigt, da Gasrohre von gröſseren Abmessungen zweckmäſsig ebenfalls durch
Walzen hergestellt werden. Sowohl zum Ziehen als zum Walzen kommt das Eisenmaterial
in Form von Blechstreifen zur Verwendung, welche man entweder durch Walzen
unmittelbar in der gewünschten Breite erzeugt, oder man schneidet sie aus breiteren
Blechen mittels Kreisscheren mit Geradführung. Die Länge und Breite der
Blechstreifen hängt von den Gröſsen der gewünschten Rohre und von der
Fabrikationsmethode ab; man bestimmt sie mit Rücksicht auf die beim Ziehen und
Walzen beobachteten Stauungs- und Streckungsverhältnisse nach der Erfahrung und nach
der Beschaffenheit des Eisens.
Ob es nun zweckmäſsiger ist, die Streifen für kleinere oder für gröſsere Röhren
unmittelbar durch Walzen herzustellen, hängt von örtlichen Verhältnissen, namentlich
davon ab, ob und welche Einrichtungen dafür auf der Werksanlage vorhanden sind. Für
die Beschaffenheit des Eisenmaterials ist das unmittelbare Walzen, besonders wenn
groſse Festigkeit verlangt wird, von Vortheil, da durch dasselbe die Bildung
paralleler, nicht verschobener Sehne, also Gleichmäſsigkeit in der Structur
befördert wird und insbesondere die Dicke sehr gleichmäſsig ausfällt. Sowohl
unmittelbar gewalzte Streifen, als auch zu Streifen zu verwendendes Blech muſs
natürlich frei von oberflächlichen Fehlern, namentlich von Rissen, Blasen und
Schiefern sein, da diese Fehler alle in dem Rohre wieder zum Vorscheine kommen und
zu verhältniſsmäſsig viel Ausschuſs Anlaſs geben würden; denn man darf auch die
äuſsere Ausstattung der Rohre nicht unbeachtet lassen.
Die Dicke der Rohrbleche hängt von dem Durchmesser, von der Verwendung und der
Fabrikationsmethode der Rohre selbst ab. Bei Gasröhren ist der Durchmesser und das Gewicht auf den
laufenden Meter vorgeschrieben, folglich die Dicke des Rohres gegeben, wenn man die
Aenderungen berücksichtigt, welche das Ziehen oder Walzen in den Uebergangs- und
Vollendungsstufen veranlaſst, und den Verlust nicht auſser Acht läſst, welcher in
Folge oberflächlicher Oxydation und Verschlackung des Eisens während der
erforderlichen Glühprozesse unvermeidlich eintritt. Z.B. für ein 4m,5 langes Gasrohr von 2¾ Zoll englisch = 70mm innerem Durchmesser und 13k,45 Gewicht auf das Meter hat man bei gezogenen
gewalzten Röhren:
Breite
des
Blechstreifens
282mm
bis
267mm
Länge
„
„
4500
„
3850
Dicke
„
„
4,5
„
5,5
Wanddicke des fertigen Rohres
5,0
„
5,0
Länge des fertigen Rohres, nach Entfernung der etwa
0m,5 langen Enden 4m,5.
Die während der Fabrikation sich ergebende Stauung und Streckung des Eisenmaterials
ist aus diesem Beispiele deutlich zu entnehmen; aber sie ändert sich nicht nur nach
den Abmessungen des Rohres, sondern nach Beobachtungen in der Entwickelung der Dicke
und des Durchmessers, welche Gröſsen ein geschickter Meister nach Bedarf regelt. Bei
gleichem Durchmesser werden übrigens Gasrohre immer dicker hergestellt als z.B.
Siederohre, weil man in erstere Gewinde einschneiden muſs, in letztere nicht. So hat
man z.B. für Rohre von 3 Zoll englisch = 76mm
innerem Durchmesser bei:
Gasrohren
Siederohren
Breite
des
Blechstreifens
294mm
315mm
Länge
„
„
4500
3850
Dicke
„
„
4,75
3,75
Dicke des fertigen Rohres
6,15
3,5
Länge (fertig)
4m,5.
Gezogenen Röhren gibt man überhaupt gröſsere Wandstärken als gewalzten – gewisse
Verwendungszwecke der letzteren ausgenommen – insbesondere noch darum, weil man bei
gezogenen Röhren die Blechstreifen stumpf an einander schweiſst, also eine gewisse
Berührungsfläche vorhanden sein muſs, bei gewalzten aber die Ränder über einander
geschweiſst werden.
Die Herstellung der gezogenen Röhren
geschieht nun auf den meisten Röhrenfabriken fast ausschlieſslich in folgender
Weise: Ein schmaler Flammofen (600 bis 1000mm) ungefähr von der Länge der zu erzeugenden
Rohre (6 bis 8m) dient dazu, die Blechstreifen der
ganzen Länge nach rasch und gleichmäſsig auf die zum Schweiſsen erforderliche Hitze
zu bringen. Auf der Stirnseite des Ofens ist eine aufziehbare Thür angebracht, mit
einer kleinen Oeffnung (Arbeitsluke) am unteren Rande, durch welche die glühenden
Rohre während des Ziehens ein- und ausgeführt werden. Nahe zur Thür liegt der
geräumige Rost derart angeordnet, daſs die Flamme den ganzen Ofen durchstreicht und
am Ende desselben durch einen abfallenden Kanal zur Esse geführt wird. Unmittelbar
vor der Arbeitsthür steht die Ziehbank (vgl. Fig. 1 und 2 Taf. 13); sie
besitzt die Form eines einfachen starken Eisengestelles, zwischen dessen beiden
Ständern a eine über Kettenscheiben gelegte Galle'sche
Kette ohne Ende b angeordnet ist. Die eine dieser
Kettenscheiben c nimmt die Betriebskraft auf und setzt
sonach die Zugkette in Bewegung. Die Ziehvorrichtung
(Fig. 3
Taf. 13) ist eine starke, doppelgelenkige Schleppzange d; sie befindet
sich auf einem vierräderigen kleinen Wagen, welcher auf Schienen e, die auf der Bankplatte angegossen sind, längs
derselben auf- und abführt. Am hinteren Ende der Zangenvorrichtung ist ein Haken f angebracht, welcher, sobald er in die Kette
eingehängt wird, die Schleppzange sammt Wagen mit fortzieht, so daſs in Folge des
Zuges die Backen der Zangen fest geschlossen werden.
An der der Ofenthür zugewendeten Seite der Ziehbank befindet sich
ein starker eiserner Rahmen (Support) g zur Aufnahme
der das Formen oder Rollen der Rohre bewerkstelligenden Vorrichtung, des aus
Guſseisen hergestellten sogen. Trichters oder Tiegels
h (vgl. Fig. 6). Die vordere, der
Ziehbank zugewendete kleinere Oeffnung des Trichters entspricht dem beiläufigen
äuſseren Durchmesser des Rohres; sie ist immer einige Millimeter gröſser als der
Durchmesser des zu fertigenden Rohres, aber doch eng genug, um die Blechstreifen
unter sehr starkem Drucke einzurollen. Die trichterförmige Erweiterung des Trichters
hat die Aufgabe, das allmähliche Einrollen des
Blechstreifens möglich zu machen; der Trichter muſs also nicht nur eine dem Rohre
entsprechende Erweiterung (Wandneigung) haben, sondern auch eine genügende
Einrollungsfläche darbieten, wodurch man zum Nachtheile dieses Verfahrens genöthigt
ist, bei Röhren von groſsem Durchmesser Trichter von ziemlich bedeutendem Umfange
bezieh. groſsem Gewichte anzuwenden, was die Hantirung derselben wesentlich
erschwert.
Die Fabrikation der gezogenen Rohre beginnt nun damit, daſs man
die Blechstreifen, die natürlich durchaus parallele Ränder haben müssen, an dem
einen Ende in einem Schmiedefeuer erhitzt, mit Hilfe eines Gesenkes etwas einrollt
und dann behufs besserer Handhabung des Blechstreifens eine Schmiedeisenstange i (Fig. 4) von 14 bis 20mm Dicke und 0,8 bis 1m Länge an das eingerollte Ende anschweiſst. Den so vorgerichteten
Streifen bringt man bei etwas gehobener Arbeitsthür in den Schweiſsofen und zwar
derart, daſs 0,5 bis 0,6m der Stange durch die
Thürluke aus dem Ofen herausragt und mit dem Ende in dem sogen. Ziehtrichter zu
liegen kommt. Die Aufgabe des Schweiſsers ist es nun, den Streifen, welchen er von
der Thürluke aus beobachtet, in dem Augenblicke, als derselbe Schweiſshitze
angenommen hat, in die Ziehvorrichtung einzuspannen. Thut er dies zu früh, so
schweiſst das Eisen überhaupt nicht; bleibt es zu lange in der Schweiſshitze, so
verbrennen die Kantenflächen namentlich an der oberen Seite des Streifens und die
Schweiſsung wird mindestens mangelhaft. Der schweiſswarme Streifen wird mit der
Zange an der Stange dicht am vorgerollten Ende gefaſst, der Haken der
Schleppvorrichtung in die Kette gehakt und der Streifen mit etwa 0m,4 Geschwindigkeit durch den Trichter hindurch
gezogen, wobei ein Junge den Wagen der Schleppvorrichtung führt, ein anderer die
durch dieselbe hindurchgehende Stange leitet.
Hinter der Kettentrommel entläſst die Zugkette den Schleppwagen,
das Rohr entfällt dem Schluſsringe der Zange und wird rasch wieder durch die
Thürluke in den Ofen zurückgeschoben, um nach Wiedererlangung der Schweiſshitze
durch einen etwas engeren Trichter noch ein zweites Mal auf gleiche Weise
hindurchgezogen zu werden.
War die Abmessung des ersten Trichters richtig gewählt, so treffen
die beiden Randflächen des Blechstreifens unter einem starken Drucke genau auf
einander, die zwischen diesen Flächen liegende Schlacke wird herausgepreſst und die
metallisch reinen Berührungsflächen durch Schweiſsung vereinigt. Wie groſs der Druck
zum Zusammenpressen der Schweiſsnaht im ersten Ziehtrichter z.B. bei einem Rohre von
70mm innerem und 80mm äuſserem Durchmesser ist, geht aus obigem
Beispiele hervor. Die Berechnung ergibt nämlich: 80 × 3,1415 = 251mm Blechbreite, während man diese in Wirklichkeit
mit 267mm nimmt. Bei 76mm + 12mm-Rohren
ist der berechnete Umfang 277mm,4, die Blechbreite
294mm, so daſs selbst bei Berücksichtigung
dessen, daſs der erste Trichter ungefähr 3mm, also
im Umfange 9mm gröſser ist als das herzustellende
Rohr, noch immer 7 bis 8mm für die
Zusammenpressung erübrigen.
Beim zweiten Ziehen durch einen Trichter, der wohl enger als der
erste, aber noch immer gröſser als der Durchmesser des fertigen Rohres ist, wirkt
der erhöhte Druck
einestheils auf die Vervollkommnung der Schweiſsung, anderentheils wird durch
denselben die Schweiſsnaht vertheilt und der äuſsere Durchmesser des Rohres nahezu
vollendet und, da das Ziehen nicht ohne Streckung vor sich geht, auch die Wandstärke
des Rohres, welche in Folge Stauchens während des ersten Zuges bedeutend zugenommen
hat, dem richtigen Maſse näher gebracht.
Nachdem das Rohr durch den zweiten Zug gegangen ist, bleibt es dem
Ermessen des Betriebsleiters anheimgestellt, ob er noch einen dritten Zug und mit
welchen Abänderungen anwendet, um etwa die äuſsere Abmessung des Rohres mit
Rücksicht auf die in Folge gänzlichen Erkaltens eintretende Schwindung genau richtig
zu stellen. Wie wichtig die richtige Wahl der auf einander folgenden Trichtermaſse
für das Gelingen und den anstandslosen Verlauf der Fabrikation ist, braucht nach dem
Gesagten wohl nicht weiter erörtert zu werden.
Das fertig gezogene Rohr wird nun sogleich von der Ziehbank weg
auf die Richtbank (einer glatten ebenen
Guſseisenplatte) gelegt, durch Aufschlagen und mit Holzschlägeln gerade gerichtet
und hierauf die angeschweiſste Führungsstange abgehauen.
In Brezowa werden die Gasrohre nur bis zu 50mm Durchmesser auf die beschriebene Weise durch
Ziehen erzeugt; alle gröſseren Röhren werden durch Walzen, also mittels des sonst
überall nur für Siederohre angewendeten Verfahrens hergestellt. Diese
Fabrikationsmethode ist zwar ungleich kostspieliger als die oben besprochene und
daher nicht gut geeignet, bei den heutigen Preisen dem Werke Gewinn zu bringen; aber
sie sichert auch so tadellose Fabrikate, daſs man mit denselben in Bezug auf Güte
und äuſsere Ausstattung jeden Wettbewerb aus dem Felde zu schlagen im Stande
ist.
Die Herstellung der gewalzten
Gasrohre geschieht in folgender Weise: Die unmittelbar gewalzten oder aus
Blech geschnittenen Streifen, welche natürlich an allen Punkten gleich breit, deren
Kanten also durchaus parallel sein müssen, werden an diesen unter einem spitzen
Winkel der ganzen Länge nach keilförmig (vgl. Fig. 5 Taf. 13)
abgehobelt, so daſs beim Zusammenrollen des Streifens diese gehobelten Kanten k gleichsam wie Lappen über einander gelegt werden
können; daher auch die verhältniſsmäſsig gröſsere Breite der Streifen. Das Zurichten
des Streifens durch Hobeln seiner Kanten ist zwar nicht unerläſslich, da man diese
auch ohnedies über einander rollen und durch Walzen schweiſsen könnte; aber es wäre
dazu unverhältniſsmäſsig mehr Druck in den Walzen erforderlich und dennoch gelänge
es kaum, die Schweiſsnaht ganz zu entfernen, was zu Ausständen seitens der Abnehmer
Anlaſs geben würde, bei Siederöhren aber ganz unzulässig ist. An den gehobelten
Kanten muſs aber, wenn Schweiſsfehler ausgeschlossen sein sollen, noch so viel
Blechdicke behalten werden, daſs ein Verbrennen der schwächeren und die
Schweiſshitze schneller aufnehmenden Blechtheile sicher vermieden werde.
Das Abhobeln der Kanten geschieht auf
einer der Zugbank ganz ähnlichen Hobelmaschine, nur daſs die mit der Schleppzange
gefaſsten Blechstreifen zwischen zwei am Kopfende der Bank eingeschaltete, je nach
der Blechbreite verstellbare Hobelmesser hindurchgezogen und sehr rasch an beiden
Kanten auf einmal behobelt werden.
Die weitere Vorbereitung des Streifens besteht nun in dem Vorrunden und Vorrollen.
Behufs Vorrundens wird der Streifen an einem Ende erhitzt und mit Hilfe eines
Gesenkes derart eingebogen, daſs man eine Rundung erhält, welche etwas kleiner ist
als der Durchmesser des zu erzeugenden Rohres. Der vorgerundete Streifen kommt
hierauf in einen langen schmalen Glüh-Flammofen (dem Rundofen) von ganz derselben
Einrichtung, wie er oben bei Erzeugung der gezogenen Rohre beschrieben wurde. Nun
werden die Streifen behufs Vorrollens bloſs bis zu Rothglut erhitzt, um dann
unmittelbar mit Hilfe einer gewöhnlichen Ziehbank durch einen Einrolltrichter von besonderer Construction
hindurchgezogen zu werden. Dieser Trichter N (Fig. 7 Taf. 13)
hat nämlich vorn als Führung einen seitlichen Einschnitt derart, daſs beim
Durchziehen des Streifens seine beiden Ränder sich über einander legen müssen. Der
Meister hat hierbei nur darauf zu achten, daſs das Einrollen ordnungsmäſsig vor sich gehe und der
Biechstreifen nicht ungerollt, unförmlich zerknittert aus dem Trichter trete. Das
vorgerollte Rohr wird noch warm mit Holzhämmern gerade gerichtet und gelangt dann
zum Walzen, welches natürlich in Schweiſshitze vorgenommen wird.
Die zur Erhitzung benutzten Schweiſs-Flammöfen sind, entsprechend
der Rohrlänge, etwa 6m lang, bei nur 500 bis
600mm Breite; sie haben auf der einen
Längenseite drei Feuerungen, um die Rohre der ganzen Länge nach rasch und
gleichmäſsig zu erhitzen und sind vorn an der Stirnseite mit einer kleinen
Arbeitsthür versehen, durch welche das Ein- und Austragen der Rohre erfolgt. Die
gegen den Fuchs hin etwas geneigte Sohle des Ofens ist mit grobem Quarzsande
bedeckt, auf welchem 2 bis 3 Rohre der Erhitzung unterzogen werden. Die Rohre liegen
mit den über einander zu schweiſsenden Lappen nach unten, wodurch dem Verbrennen
ihrer Ränder am besten vorgebeugt werden kann. Die richtige Leitung des
Schweiſsprozesses ist überhaupt von gröſster Wichtigkeit und von ihr allein hängt
der Erfolg der weiteren Walzarbeit ab. Der Schweiſser muſs das Rohr in dem
Augenblicke dem Walzwerke zuführen, in welchem dasselbe eben Schweiſshitze
angenommen hat; jedes Versäumniſs in dieser Richtung führt zum Miſslingen der
Schweiſsung. In Folge Ueberhitzung verbrennt das Eisen, wird krystallinisch und
brüchig und die Schweiſsung ist mangelhaft. Die zu verwendende Kohle muſs
langflammig, arm an Asche sein und möglichst wenig Schwefel enthalten, um nicht
durch Bildung von Schwefeleisen die Schweiſsung zu beeinträchtigen. Ebenso muſs der
Eintritt von Flugasche in den Herd und dann zwischen die Rohrlappen möglichst
vermieden werden. Das Schüren auf den Rosten darf daher nur in gewissen
Zwischenpausen vorgenommen werden und ist überhaupt ein geschickter Heizer
unerläſslich.
Das Walzwerk (Fig. 8 Taf. 13) befindet
sich dicht vor der Arbeitsthür des Schweiſsofens. Es besteht aus einem
zweistanderigen Gerüste o, in dessen je zwei Lagern die
auf starken schmiedeisernen Wellen aufgekeilten guſseisernen Walzen p in Form ausgekehlter Scheiben derart über einander
gelagert sind, daſs die in Schalenguſs hergestellten, also mit harter Oberfläche
versehenen Hohlkehlen auf ihrem Umfange ein Rundkaliber bilden, welches dem äuſseren
Durchmesser des zu walzenden Rohres angepaſst ist. Dieses Rundkaliber liegt mit der
Ofensohle nahezu in gleicher Höhe, so daſs das Rohr unmittelbar in dasselbe
eingeführt werden kann. Da jedes Walzenpaar nur ein Kaliber enthält, so müssen für
jede Rohrweite besondere Walzen vorhanden sein, welche dann in das Gerüst nach
Bedarf eingelegt werden. Die Walzen werden mit Hilfe eines Vorgeleges r von einer kräftigen Dampfmaschine in Umdrehung
versetzt und zwar wechselt die Umdrehungszahl, d. i. die Umfangsgeschwindigkeit der
Kaliberwalzen, gewöhnlich nach der Wandstärke der Rohre; sie muſs bei dünneren
Rohren gröſser sein, da diese rascher abkühlen und die Schweiſshitze einbuſsen,
während dies bei dickeren Rohren weniger der Fall ist.
Dicht vor den Walzen liegt eine Walzbank von U-förmigem
Querschnitt s (vgl. Fig. 9); diese dient
einestheils zur Aufnahme des durchgewalzten Rohres, andererseits aber zur
Befestigung einer starken Eisenstange t, an deren Ende
der den inneren Durchmesser des Rohres bestimmende Dorn u sitzt. Dieser Dorn wird in Hartguſs aus Guſseisen hergestellt; er ist
theils cylindrisch, theils von parabolischer Form und der Länge nach mit einer
cylindrischen Oeffnung versehen, mittels welcher er, das parabolische Ende nach
auſsen, aut das abgedrehte Ende der Eisenstange t lose
aufgesteckt wird. Der entgegengesetzte Theil des Dornes wird dem inneren Durchmesser
des zu walzenden Rohres entsprechend genau cylindrisch abgeschliffen. Diese Stelle
des Dornes kommt zwischen die Walzen genau in die Achse des Kalibers zu liegen,
während die denselben tragende Stange sich an eine mit Schrauben verstellbare Platte
am hinteren Ende der Walzbank anstemmt.
Denkt man sich nun die Walzen in der Richtung der Walzbank
gedreht, so muſs selbstverständlich ein zwischen dieselben geschobenes Rohr – alle
übrigen Bedingungen für das Gelingen des Walzprozesses vorausgesetzt – über den Dorn
hinweg durch die Walzen gezogen und über die Haltstange des Dornes hinausgeschoben werden.
Das vorgerollte Rohr wird auch, nachdem es Schweiſshitze angenommen hat, zunächst
rasch mit dem Lappen nach oben gewendet, dann mit einer langarmigen Hohlzange nahe
am Ende gefaſst und äuſserst rasch und mit gröſster Kraft über einen entsprechenden
Dorn in das Walzenkaliber geschoben, welches es, von den Walzen erfaſst, mit
Blitzesschnelle und mit Flintenschuſs ähnlichem Knallen durchläuft.
Die Schweiſsfuge muſs beim Walzen nach oben gekehrt sein, um unter
dem gröſsten lothrechten Drucke der Walzen die Schlacke auszupressen, die beiden
Blechlappen völlig zusammen zu schweiſsen und die Schweiſsnaht möglichst zu
vertheilen. Das gewaltsame Herauspressen der weithin spritzenden Schweiſsschlacke
verursacht das erwähnte Knallen. Das durchgewalzte Rohr wird sogleich von der
Dornstange herabgenommen und wieder in den Ofen zurückgebracht, um nach
Wiederaufnahme der Schweiſshitze über einen etwas gröſseren Dorn als das erste Mal
gewalzt zu werden. Bei diesem zweiten Durch walzen, welches auch die Vervollkommnung
der Schweiſsung und die völlige Entschlackung und Zertheilung der Schweiſsnaht zum
Zwecke hat, wird das Rohr beim Durchwalzen, wie beim Walzen von Rundeisen, um etwa
60° gegen den ersten Durchgang gewendet, um etwaige Unterschiede in der Wanddicke
und Rundung des Rohres auszugleichen. Ferner wird bei diesem zweiten Durchwalzen
dasjenige Ende des Rohres an die der Abkühlung ausgesetzte Schweiſsofenthür
gebracht, welches früher im hinteren Theile des Ofens gelegen war, um aus der
Erhitzung hervorgegangene Ungleichmäſsigkeiten ebenfalls auszugleichen.
Bei Gasröhren sind zwei Walzungen
durchaus genügend; bei Siederöhren folgt meistens noch
ein drittes und zuweilen ein viertes Durchwalzen der Röhren über immer gröſsere
Dorne (immer um 60° gewendet und das Rohrende gewechselt), wenn die Richtigstellung
der Wandstärke, des Durchmessers, der Rundung oder sonst sichtlicher Mängel in der
Schweiſsnaht dies nöthig erscheinen lassen.
Die Arbeit des Walzens selbst dauert nur einige Augenblicke. Das
fertig gewalzte Rohr ist also noch so glühend und das Eisen so zu sagen weich, daſs
es, wollte man es als fertig bei Seite legen, sich derart krümmen, werfen und
verziehen würde, daſs ein Geraderichten kaum gelingen würde; auch wäre der
Durchmesser, schon wegen des möglichen Federns der Walzenachsen, oder, wenn man
nicht alle Uebergangskaliber in den Walzenvorräthen zur Verfügung hat, nicht allemal
genau und das Aeuſsere des Rohres wegen des daran haftenden Sinters ungefällig und
für viele Zwecke nachtheilig. Man begegnet nun diesen Uebelständen dadurch, daſs man
die Rohre nach dem letzten Walzen bis zur Rothglut abkühlen läſst und noch mehrere
Mal auf der sogen. Eratzbank durch Hartguſsringe mit
scharf geschliffenen Kanten zieht, welche etwas enger sind als das Walzenkaliber und
genau dem vorgeschriebenen auſseren Durchmesser des Rohres entsprechen. In Brezowa
werden gegenwärtig Rohre bis zu 140mm (5½ Zoll
engl.) auf die eben beschriebene Weise hergestellt.
Mag nun das Rohr durch Ziehen oder Walzen hergestellt worden sein,
so folgen bei Gasröhren noch nachstehende Vollendungsarbeiten. Zunächst werden die Röhren nach dem Erkalten von
unvermeidlichen Krümmungen mit der Hand oder mit Maschine – je nach der Abmessung –
gerade gerichtet, dann die Enden mit Hilfe einer kreisenden zahnlosen Scheibe mit
Rücksicht auf die vorgeschriebenen Längen der Rohre abgeschnitten und endlich die
Rohre an beiden Enden mit Gewinden und an einem Ende mit Muff versehen. Das Gewinde
ist kein gewöhnliches Normalgewinde, sondern des dichteren Abschlusses wegen viel
feiner als dieses und als Gasröhrengewinde bekannt. Jedes völlig ausgefertigte Rohr
wird in Brezowa mit Hilfe einer Druckpumpe einem Drucke von mindestens 20at unterworfen und bei der geringsten Lässigkeit
von der Verschickung ausgeschlossen. Eine solche Lässigkeit der Rohre könnte nur von
Schweiſsfehlern an den Schweiſsfugen herrühren, was bei fachkundiger Leitung des
Betriebes wohl selten vorkommen wird, trotzdem gerade die Schweiſsarbeit der
wundeste Punkt der Röhrenfabrikation ist. Diese hängt jedoch nicht allein von der
Behandlung des Eisens im Ofen, sondern auch von der richtigen Wahl des Materials ab. Schwefel
haltiges Eisen ist von vornweg zu verwerfen; ebenso die Verwendung an Schwefel
reicher Kohle zur Beheizung der Glüh- und Schweiſsöfen. Auch an Kupfer reiches Eisen
ist zur Röhrenfabrikation nicht gut geeignet; hingegen ist Phosphor ein sehr
erwünschter Bestandtheil der Röhrenbleche, weil er die Schweiſsbarkeit derselben
erhöht. Ein groſser Phosphorgehalt veranlaſst aber Kaltbrach und muſs daher
ebenfalls vermieden werden. Das in Brezowa verwendete Eisen enthält als
Holzkohleneisen erster Güte kaum Spuren von Schwefel, äuſserst wenig Kupfer und
durch absichtlichen Zusatz einer Roheisensorte nur so viel Phosphor, als
„Qualitätseisen“ zur Beförderung der Schweiſsung eben zuläſst. Die
Steinkohle aber ist an Asche arme preuſsische Flammkohle bester Beschaffenheit.
Schweiſsfehler können bei Röhren von groſsen Abmessungen dann noch
vorkommen, wenn man dieselben durch Ziehen und nicht
durch Walzen herstellt. Da nämlich beim Ziehen die
beiden Ränder des Blechstreifens, welche einander nur gegenüber, nicht aber über
einander zu liegen kommen, bei Weiſsglühhitze im erweichten Zustande stellenweise
leicht einsinken, so wird die Berührung und Verschweiſsung derselben mangelhaft,
selbst wenn man sich beim Ziehen eines Dornes bedient, was zuweilen zu geschehen
pflegt. Liegen aber die beiden Blechränder über
einander, so kann eine Unterbrechung der Schweiſsfuge gar nicht eintreten. Es kann
nichts desto weniger selbst bei gut geschweiſsten Röhren vorkommen, daſs die
Schweiſsfugen derselben beim Biegen, insbesondere beim Kaltbiegen, einknicken und
fehlerhaft werden, was aber meistens nur einer fehlerhaften Behandlung beim Biegen
zuzuschreiben ist, da man namentlich Rohre von etwas gröſserem Durchmesser behufs
Erzielung schöner gesunder Biegungen zuerst mit Sand füllen muſs – die Rohrenden
werden mit Holzpfropfen verschlossen – und dann erst die Biegung, ob warm oder kalt,
vornehmen darf.
Um ein Lässigwerden der Rohre an den Gewinden zu verhüten, werden
diese beim Legen der Gasleitungen durch geriebenen Menningkitt abgedichtet. Probirt
man aber die mit Muffen versehenen Rohre noch, bevor jene Dichtung erfolgt ist, so
ergibt sich zuweilen, namentlich bei frisch geschnittenen Gewinden, bevor also das
angewendete Maschinenöl etwas verharzte, ein Lässigwerden an der Muffenverbindung.
Man wird dies fast immer vermeiden, wenn man den Muff bis auf das letzte Gewinde des
Rohres schraubt, so daſs kein Schraubengang leer bleibt, während man bei nicht fest
aufsitzenden Muffen selten völlige Dichtigkeit erzielen wird.
Es kommt zuweilen auch vor, daſs Uebernehmer von Gasröhren,
namentlich Zwischenhändler, die Röhren wegen der auf der Oberfläche derselben vom
Trichter oder Ziehringe herrührenden schwachen Riefeln als Schönheitsfehler
beanstanden, was gewiſs am wenigsten gerechtfertigt ist, da die Riefeln beim
Handhaben der Rohre mit der Rohrzange von Seite des Personales der Gasanstalten
geradezu erwünscht sind.Erwähnungswerth scheint noch, daſs die Röhrenfabrik in Brezowa, welche im J.
1882 gebaut wurde, die erste Anlage dieser Art in Oesterreich-Ungarn war;
Witkowitz folgte derselben sozusagen auf dem Fuſse. Im Auslande sind die
Röhrenfabriken meistens nicht auf Hüttenwerken eingerichtet, sondern bilden
ganz selbstständige Fabrikanlagen. Daſs man in Oesterreich-Ungarn überhaupt
so lange mit der Einführung dieser Fabrikation zögerte, hat seinen Grund,
abgesehen von manchen anderen Umständen, gewiſs auch im Mangel an
Unternehmungsgeist, so daſs bei Einführung dieses neuen Industriezweiges,
wie so oft vorher, wieder Montanistiker im Interesse der vaterländischen
Industrie ihre Rolle als Bahnbrecher aufnehmen muſsten.K.
Tafeln
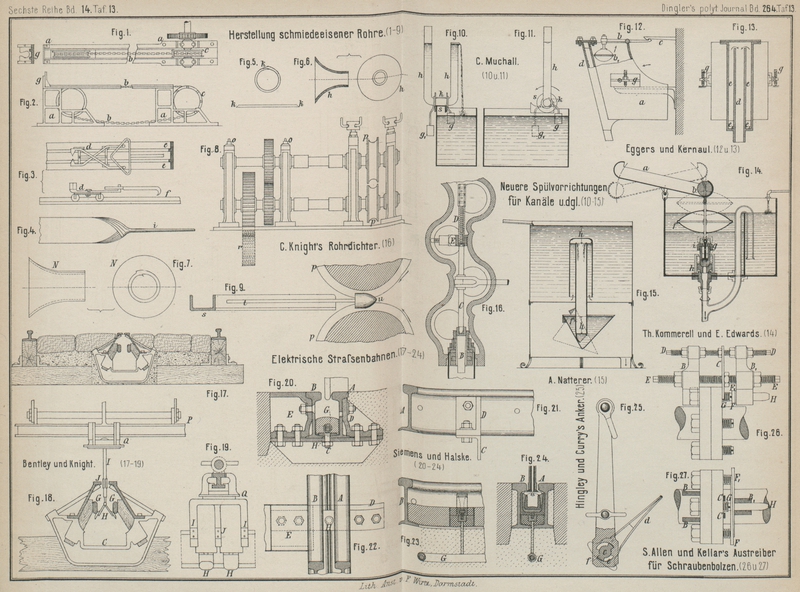