Titel: | Ueber Neuerungen im Eisenhüttenwesen. |
Fundstelle: | Band 264, Jahrgang 1887, S. 216 |
Download: | XML |
Ueber Neuerungen im Eisenhüttenwesen.
(Patentklasse 18. Fortsetzung des Berichtes Bd.
263 S. 471.)
Mit Abbildungen im Texte und auf Tafel 14.
Ueber Neuerungen im Eisenhüttenwesen.
Der Hochofen-Prozeſs.
J. H. Const. Steffen in Luxemburg und M. M. Rotten in Berlin (* D. R. P. Nr. 36301 vom 25.
December 1885) schlagen insbesondere für sehr keiften
Hochofen-Wind die in Fig. 1 Taf. 14 skizzirte
Vorrichtung zum Absperren der Windleitung für
Düsenstöcke vor. Die Absperrung erfolgt hier durch einen Drehschieber F, welcher in einem Ventilgehäuse A1 sitzt und entweder
die Oeffnung b zum Windabblasestutzen D, oder die Oeffnung c
zwischen Hauptwindrohr A und dem Düsenstock verdeckt,
in welch letzterem Falle also die Windabstellung erfolgt. Die Umstellung des
Schiebers F geschieht von Hand mit Hilfe der Zugstange H, welche an dem
mit Umstellgewicht E versehenen Hebel G auf der Schieberachse hängt. Die Windeintrittsöffnung a besitzt in der Regel eine etwas gröſsere
Querschnittsfläche als die Windausströmungsöffnungen b
und c. Die Windpressung drückt deshalb den Schieber F fest und dicht an die Arbeitsleisten des Deckels B an. Wird das Gewichtsverhältniſs von E und H so gewählt, daſs
das Gleichgewicht unterbrochen wird, sobald der Winddruck auf die der
Ausströmungsöffnung entsprechende Fläche aufhört oder sich vermindert, so dreht sich
der Schieber F selbstthätig, so daſs er die Verbindung
mit dem Düsenstock schlieſst und der Wind durch D
austreten kann. Bei dieser Einrichtung dient die Zugstange H nur als Ausgleichgewicht und zum Anheben des Gegengewichtes E, sobald wieder geblasen werden soll.
Die Bochumer Eisenhütte, Heintzmann und Dreyer in Bochum
(* D. R. P. Kl. 27 Nr. 35369 vom 16. Oktober 1885) hat einen Düsenstock entworfen, welcher in zwei
Kugelgelenken beweglich ist, so daſs er ohne weiteres aus der Form gezogen
werden kann, wenn eine Reinigung derselben erforderlich ist; andererseits wird er
bei Explosionen im Ofengestelle zurückgeworfen, ohne dabei Beschädigungen zu
erleiden. Nach Fig.
7 Taf. 14 liegt das eine Kugelgelenk im senkrecht abfallenden Rohrzweige.
An dem festen Anne ist eine Schelle B angebracht, um
die sich zwei Bogen drehen, welche das bewegliche Rohr tragen. Die Flächen zwischen
beiden Rohren sind nach einem Cylinder abgedreht, dessen Achse mit der Drehachse der
Bolzen zusammenfällt. Auf dieselbe Weise ist der senkrechte Rohrzweig mit der Düse
verbunden. Durch entsprechendes Anziehen der Bolzenmuttern kann man die Rohrtheile
mehr oder weniger starr mit einander verbinden. Um die Blasestellung zu erhalten,
ist der bewegliche Rohrtheil mittels eines Schraubenbügels und Feder mit dem
Ofengestelle verbunden, so daſs bei etwa auftretenden Explosionen die Düse unter
Zusammendrückung der Feder und unter Drehung der Kugelgelenke aus der Form
hinausgeschoben wird; nachdem der Ueberdruck im Ofen aber durch die Formen entwichen
ist, wieder in die Düse zurückschnellt. Ein vor den Schraubenbolzen p geschobener Vorstecker gestattet die leichte
Entfernung des Anschlusses des Düsenstockes an das Gestell und damit ein Zurückgehen
des ersteren.
Der von F. W. Lürmann in Osnabrück (* D. R. P. Nr. 38408
vom 3. August 1886) angegebene Düsenstock bezweckt
neben der leichten Handhabung die Möglichkeit, denselben rasch und ganz aus dem
Raume vor dem Formgewölbe zu entfernen, damit bei vorkommenden Arbeiten an der Form
der Arbeiter sich ungehindert in diesem Raume bewegen kann. Die Gründe hierfür sind
einmal die hohen Temperaturen, welche die Wandungen der Düsenstöcke in Folge
Anwendung sehr heiſsen Windes haben, und die hohe Lage der Mittellinie der Formen,
also des Düsenstockes, über dem Standorte der Arbeiter, d.h. der Umgebung des
Gestelles. Aus beiden Gründen ist die Handhabung der Düsenstöcke bei den bisherigen
Anordnungen erschwert.
An das ausgemauerte Windrohr a (Fig. 8 und 9 Taf. 14) ist der
Schieberrahmen b mit dem Schieber c geschraubt. An dem ersteren ist das Rohrende d mit einer Fahrbahn e
befestigt, auf welcher die Rollen oder Kugeln f in den
Gehäusen g laufen. Die Gehäuse g sind fest mit dem Kranze h verbunden und
dieser wieder mit dem Bügel i; in letzterem hängt auf
der Schraube l der Düsenständer kk1 welcher die Düse m trägt. Das Gegengewicht n hält dem Düsenstocke kk1 das Gleichgewicht. Wird die Schraube l etwas gelöst, so ist der Düsenstock kk1 auf den Rollen g leicht drehbar und kann so in die punktirte Stellung
Fig. 9
gebracht werden, in welcher derselbe in keiner Weise bei den Arbeiten an der Form
p hindert.
Nach den Transactions of the American Institute of Mining
Engineers, 1886 Bd. 13 * S. 520 ist auf den Glendon
Iron Works ein abgeänderter Langen'scher Gichtgasfang (vgl. 1886 259
* 361) seit dem J. 1881 eingeführt, welcher gestattet, den Hochofen in derselben
regelmäſsigen Weise zu beschicken, wie dies früher bei offener Gicht möglich
war.
Die Gicht ist durch die Glocke g
(Fig. 2
und 3 Taf. 14)
geschlossen, deren Auſsenwand cylindrisch ist und auf einem losen Ringer ruht,
während die Innenwand einen abgestumpften, unten offenen Kegel bildet, welcher sich
an einen Cylinder c anschlieſst. Die obere Haube von
c ist mit dem in der Mitte liegenden
Gasableitungsrohre a verbunden, welches einer
seitlichen Abführung unterhalb der Gicht bei Hochöfen mit Rauhgemäuer vorgezogen
wird. Der Cylinder c erhält seine Bewegungen durch die
mittlere Stange s und durch den vom Kraftcylinder l bewegten Hebel h. Wenn
die Beschickung auf die Aufgebevorrichtung gekippt wird, so bleibt ein Theil
derselben auf dem Kegel k und dem Ringe r liegen, ein Theil stürzt in die Glocke g. Wenn nun der Kolben im Kraftcylinder l niedergeht, wird durch den Hebel h der Cylinder c der
Aufgebevorrichtung gehoben, so daſs die in der Glocke g
liegende Beschickung in die Mitte des Ofens fällt. Bis dahin verbleibt die Glocke
g in ihrer Lage; alsdann aber trifft der Ansatz o unter den Bugel p und
hebt die mit letzterem verbundene Glocke g, so daſs nun
auch der auf r und k
liegen gebliebene Theil der Beschickung in den Ofen fällt.
Das Rohr a ist mit dem Rohre b durch ein Kugelgelenk verbunden. Das Rohr b ruht auf dem Hebel h1, dessen Schwere durch ein Gegengewicht so
ausgeglichen ist, daſs sich das Rohr b um 80 bis 100mm hebt, wenn der Cylinder c gehoben wird. Senkt sich dieser, so setzt sich der kegelförmig
ausgebohrte Rand f auf den ebenso abgedrehten Rand e und zieht das Rohr a
herunter sowie das Gegengewicht am Hebel h1 in die Höhe und zwar so weit, wie nöthig ist, um
die Glocke g in dem Ringe r zum Aufruhen gelangen zu lassen.
Der Winkel von 70°, unter welchem f und e sich berühren, ist
behufs guten Verschlusses nothwendig. Alle Theile dieser Aufgebevorrichtung sind so
eingerichtet, daſs sie mit dem Gichtaufzuge gehoben werden können; die Glocke g besteht aus 4, und der Ring r aus 3 Theilen. Die Verbindungsflanschen des letzteren ruhen, wie in Fig. 3 links
gezeichnet ist, in Aussparungen des Kegels k.
Bei einer früheren Ausführung setzte sich die Glocke g auf eine abgedrehte Fläche des Ringes r; diese wurde jedoch durch die Beschickung bald so
unregelmäſsig abgenutzt, daſs eine Dichtung nicht möglich war. Jetzt liegt die
Beruhrungsfläche der Glocke g und des Ringes r nicht in der Oberfläche, sondern im Rande des
letzteren und ist so steil gemacht, daſs die Beschickung darüber hinweggleitet, ohne
darauf liegen zu bleiben.
Für die gute Wirkung dieser Vorrichtung ist erforderlich, daſs man
Behufs Wahl der Gröſsenverhaltnisse die obere Weite des Ofens in der Hohe, bis zu welcher derselbe
gefüllt erhalten werden soll, die lichte Weite des Ringes r bezieh. der Glocke g, also den äuſseren
Durchmesser des Cylinders c kennt. In der gezeichneten
Ausführung ist das erste Maſs 2m,86, das dritte
1m,67. Man will bemerkt haben, daſs der Ofen
früher, als diese Maſse 3 bezieh. 2m betrugen,
einen schlechteren Gang hatte. Nachdem man die lichte Weite der Glocke g auf 1m,67
verringert und deren Unterkante um 0m,77
erniedrigt hatte, hob sich die wöchentliche Erzeugung neben bedeutend geringerem
Brennstoffverbrauche von 300 auf 360t.
Der von Wlad. F. Berner in Kuschwinski Zawod, Ruſsland
(* D. R. P. Nr. 34618 vom 31. Januar 1885) vorgeschlagene Gichtgasfang soll den Vortheil bieten, daſs das Auffangen der Gichtgase in
regelmäſsigerer Weise ohne Verluste und ohne den Verlauf des Hochofenprozesses
störende Gasstauungen vor sich geht, da den Gasen gestattet wird, nach allen Seiten
hin gleichmäſsig abzuziehen. Ferner soll der Gichtverschluſs leichter zu handhaben
sein als die üblichen Gichtglocken, die Gasfangkanäle sollen sich leicht reinigen
lassen und die Anordnung ist so getroffen, daſs die Gichtgase, bevor sie zu den
Feuerungen gelangen, gereinigt werden. Vermöge letzterer Einrichtung werden die Gase
von condensirbaren Bestandtheilen befreit, so daſs sie die Leitungsrohre nicht
verunreinigen und mit höherer Temperatur verbrennen.
Wie aus Fig. 4 und 5 Taf. 14 ersichtlich, ist
rings um die Gicht im Schachtmauerwerk ein Kanal a
ausgespart, von dessen unterem Theile aus geneigte Kanäle b in radialer Richtung in den Schacht führen. Die obere Wand des
Ringkanales a wird durch guſseiserne Platten gebildet
und, um den Schachtwänden ungeachtet des Vorhandenseins dieses Kanales die
erforderliche Stärke belassen zu können, ist rings um die Gicht das Mauerwerk
verstärkt; bei kleineren Hochöfen wird der durch diese Verstärkung des Mauerwerkes
verursachte Vorsprung von Säulen oder einer Stützmauer c getragen, welche bei groſsen Hochöfen mit sehr starkem Mauerwerk
wegfallen kann. Um durch die Anlage der geneigten sechs Radialkanäle b die über denselben stehen bleibenden Wandtheile nicht
ihres Auflagers zu berauben, ist die Schachtmauer in der entsprechenden Höhe aus
zwei Lagen von Steinplatten, deren eine mit b1 bezeichnet, hergestellt. Das Verstopfen der Kanäle
b durch die Beschickung wird durch die guſseisernen
Winkelplatten b2
verhindert, welche in der Flucht der Schachtwand so eingemauert sind, daſs sie den
oberen Theil der Kanalausmündungen überdecken. Diese Winkelplatten b2 sind mittels Bolzen
und Klammern an der Schachtwand befestigt und ihre dem Feuer ausgesetzte Fläche ist
beim Gusse rauh hergestellt und wird dann mit feuerfestem Thone verkleidet. Man
könnte die Winkelplatten auch hohl herstellen und mit Luft oder Wasser kühlen. An
zwei gegenüber liegenden Stellen – und zwar bei Hochöfen von elliptischem
Querschnitte an den Enden der groſsen Achse – gehen vom Ringkanale a in tangentialer Richtung Rohre d nach der Glocke e des
Gasreinigungsapparates ab. Diese Glocke taucht in einen Wasserbehälter e1 und ist durch eine
nicht ganz bis an die Wasseroberfläche reichende Wand e2 in zwei Kammern getheilt. Die Gichtgase
treten erst in die gröſsere Kammer, ziehen dann durch die enge Spalte zwischen dem
unteren Rande der Querwand und der Wasseroberfläche, wobei sie mitgerissene
Aschentheilchen absetzen und abgekühlt werden, und gelangen endlich in die engere
Kammer, welche mit der nach den Feuerungen führenden Rohrleitung f in Verbindung steht.
Durch Aenderungen des Wasserstandes im Behälter e1 kann der Abzug der
Gase geregelt werden. Zum Zwecke bequemer Reinigung der Radialkanäle b sind in die äuſsere Wand des Ringkanales a guſseiserne Rohre g
eingesetzt; diese besitzen abhebbare Deckel und über ihren Ausmündungen sind Büchsen
mit nach auſsen aufklappbaren Thüren an den Schachtmauern befestigt. Während man die
Radialkanäle b reinigt, werden für den Gasabzug Blechrohre h aufgesetzt, welche man mit der Hauptgasleitung f verbindet. Dadurch verhindert man die Belästigung der
Arbeiter durch die Gase.
Die Gicht wird von einem Deckel geschlossen, welcher aus zwei
gegen die Mitte geneigten verschiebbaren Halften a
besteht. Die Verschiebung erfolgt durch Zahnstangengetriebe und Winde. Beim Oeffnen
der Gicht wird die auf den Deckel geschüttete Beschickung von dem Rande a1 zurückgehalten und
stürzt in den Ofen.
Edward Walsh in St. Louis hielt auf der
Herbstversammlung 1886 des American Institute of Mining
Engineers (vgl. Engineering and Mining
Journal, 1886 Bd. 42 * S. 311) einen beachtenswerthen Vortrag über Un regelmäſsigkeiten beim Betriebe des Hochofens und
über die Mittel, dieselben zu vermeiden. Bekanntlich ist die Frage noch nicht
gelöst, welches die beste Gestalt für den Hochofen ist
(vgl. 1885 257 235). Walsh
glaubt die Schwierigkeiten durch die in der Textfigur skizzirte Gestalt zu heben.
B ist der sich nach unten etwas erweiternde
Schacht; daran schlieſst sich ein sich etwas stärker erweiternder Theil A, welcher in die sehr niedrige Rast C übergeht.
Textabbildung Bd. 264, S. 220
Es sollen dadurch in letzterer nur noch geschmolzene
Materialien ankommen, deren Niedergang durch die Verengung nicht beeinträchtigt
wird. Auſserdem soll sich bei einer derartigen Form des Ofens der Wind mehr an dem
Umfange desselben halten und auf diese Weise das Hängenbleiben der Beschickung an
den Wänden verhindern. Die Steinlagen im Gestelle und in der Rast sind nach innen
geneigt, um durch das Streben der Steine, nach innen zu gleiten, die Fugen zu
dichten und das Eisen am Austritte durch die schräg ansteigenden Fugen zu hindern.
Der Schacht B wird von zwei Reihen über einander
gesetzter Säulen getragen, so daſs die Theile A und C leicht ausgebessert werden können, ohne den Schacht
angreifen zu müssen. – Die Ofeneinrichtung ist Gegenstand des englischen Patentes
Nr. 13266 vom 18. Oktober 1886.
In der Beseitigung von Versetzungen im Hochofen ist man
jetzt sehr weit vorgeschritten. Ueber einen Fall berichtet F.
ToldlTodt in Neuberg in der Oesterreichischen Zeitschrift
für Berg- und Hüttenwesen, 1886 S. 587 folgendes:
Im Monate April des J. 1884 wurde bei Ofen I in Schwechat Roheisen
der weichsten Marke erzeugt, wozu öfters bei schwerem Gichtsatze bloſs eine
Windtemperatur von etwa 150° verwendet wurde. Ein zur Nachtzeit plötzlich
eingetretener Gewitterregen feuchtete die Beschickungsmaterialien derart an, daſs
schnell Rohgang eintrat; auſserdem wurde die Entwicklung der Betriebsstörung sowohl
durch das während des Gewitters unmittelbar in den Ofen stürzende Wasser, als auch
durch die starke Abkühlung der Winderhitzer, in welchen das feuchte Gichtgas nur
schwer brannte, gefördert. Trotzdem sogleich der Erzzusatz herabgesetzt und die
Windtemperatur erhöht wurde, trat der Rohgang in einer solchen Heftigkeit auf, daſs
das Einfrieren des Ofens zu erwarten stand.
Nachdem der Ofen immer langsamer ging, blieben am 5. Tage die
Gichten hängen; da ferner die Formen sich derart versetzten, daſs sie nicht mehr
durchgestoſsen werden konnten, muſste daran gedacht werden, rasch ein energisch
wirkendes Mittel anzuwenden, um der Bildung von weiteren Versetzungen ehemöglichst
vorzubeugen. Der Ofen faſste 40 Gichten; hiervon waren heruntergeschmolzen am 2. bis
5. Tage bezieh. 8, 15, 13 und 1 Gicht, zusammen 37 Gichten.
Es handelte sich nun bloſs darum, 3 schwere Gichten
niederzubringen, was durch Einführung von Erdöl durch
die Düsen gelang. Dabei stieg die Pressung im Ofen sehr stark, so daſs beim Oeffnen
der Düsen Eisen, Brennstoff und Erz aus denselben geschleudert wurden. Man lieſs
deshalb rasch ein Rohr an der letzten noch hellen Form anbringen, welches vorn eine
Oeffnung von bloſs 5mm hatte, dasselbe mittels
eines Kautschukschlauches mit dem Druckrohre einer Feuerspritze in Verbindung setzen
und nachdem die Spritze mit Erdöl gefüllt war, zuerst etwa 100k, später weitere 200k in den Ofen bringen. Hiernach wurden die Formen wieder hell und bald
nachher meldeten die Gichtarbeiter, daſs der Ofen niederzugehen beginne. Der Ofen
stürzte zwar noch etwas, aber so unbedeutend, daſs man sagen konnte, er sei
unmittelbar nach der Einführung des Erdöles wieder in guten Betrieb gekommen. Die
zugeschmolzenen Formen konnten, bis auf eine, den nächsten Tag geöffnet werden.
Aehnliches theilt James Gayley in den Transactions of the American Institute of Mining
Engineers, 1886 Bd. 14 S. 779 mit:
Am 31. December 1885 muſsten, Arbeiterunruhen wegen, alle Oefen
der Edgar-Thomson-Hütte eingedämmt werden, in welchem
Zustande sie bis 20. Januar 1886 verblieben. Der Ofen „E“ war schon vorher
etwas unregelmäſsiger als alle anderen gegangen, was sich schon seit August 1885
hinzog; der Ofen war damals so stark versetzt, daſs er mittels eines durch die
Formen geführten Gasgebläses (Löthrohr) gereinigt werden muſste und hörte seither
nicht auf zu stürzen. Als am 21. Januar 1886 dieser Ofen wieder geöffnet wurde, fand
man Alles noch in demselben Zustande wie bei der Eindämmung. Bei allen Formen sowie
beim Schlackenstich zeigte sich Brennstoff. Die Winderhitzer wurden mit Holz
angeheizt und bis zu einer Temperatur von 260° gebracht. Man setzte nun den Ofen in
Betrieb und nach einer Stunde erschien eine rohe Schlacke bei den Formen, weshalb
sogleich abgestochen wurde, wobei eine zähe, aus Eisen und Schlacke bestehende Masse
ausfloſs. Um sich des Stiches zu versichern, trieb man eine Stange ein, welche
während des Blasens darinnen gelassen wurde, um nach 1½ Stunden wieder entfernt zu
werden. Der Abstich war dem vorigen gleich. Die nach diesem Abstiche wieder
eingetriebene Stange brach, als sie nach 2 Stunden herausgeschlagen werden sollte,
und Nachdem alle Versuche durchzudringen vergebens waren, muſste man den
Schlackenform-Kühlkasten entfernen, um weiter oben einen Stich anbringen zu können.
Die Füllung war an der Stelle des Ofens gut; doch plötzlich stürzte der Ofen auf
dieser Seite und bald in rascher Aufeinanderfolge an zwei anderen Seiten, so zwar,
daſs in die Formen groſse Mengen Schlacke gedrängt wurden. Fünf Formen waren zu und
man muſste, nachdem die verschiedensten Mittel versucht wurden, endlich die
Gebläsemaschine abstellen, denn die Pressung war von 200 auf 500mm Quecksilber gestiegen.
Am 22. Januar schritt man zur Anwendung des Erdöl-Blaserohres. Eines arbeitete beim Schlackenstich,
ein zweites links davon bei der sechsten Form und in kurzer Zeit war eine Höhlung
ausgeschmolzen, welche immer mehr und mehr wuchs. In einer Entfernung von 450 bis
610mm gegen die Ofenachse war die Füllung sehr
hart und bestand gröſstentheils aus Eisen; später wurde sie weicher und zeigte mehr
beigemengte Schlacke. 6 Stunden nach Inbetriebsetzung des Erdöl-Blaserohres hatte
die Höhlung schon 1800mm Lange, 1500mm Weite, 1200mm
Höhe, 1000mm über dem Mittel der Schlackenform. Da
damit die Versatzoberfläche durchbrochen war und viele gute heiſse Kokes
herabfielen, so konnte eine Form eingelegt werden und das Arbeiten in regelrechter
Weise beginnen. Den Abstich muſste man ausschmelzen, indem man so lange mittels des
Erdöl-Gebläses blies, bis das Eisen zum Durchbruche kam, oder man arbeitete mit dem
Blaserohre in der Nähe des Stiches so lange, bis eine Brechstange leicht
durchgestochen werden konnte. 6 Tage darauf waren alle Formen in Betrieb und der
Ofen ging anstandslos. Das Interessanteste bei diesem Falle war, daſs die
ausgeschmolzene Füllung 60 bis 80 Proc. Eisen enthielt, was bis dahin in ähnlichen
Fällen noch nicht vorgekommen war.
Gleiche günstige Ergebnisse werden von R. H. Lee in
Lewistown, Pa., im Engineering and Mining Journal, 1886
Bd. 42 S. 260 berichtet.
Eine dem vorgenannten Gebläse ähnliche Vorrichtung wird
nach der Revue industrielle, 1886 * S. 26 von M. Weber in Chicago vorgeschlagen, um im Hochofen das
feste Brennmaterial durch Erdöl zu ersetzen. Die
Vorrichtung besteht aus einem doppelwandigen wassergekühlten Rohre f (Fig. 6 Taf. 14), welches
von unten in die Form eintritt. Das Rohr ist mit dem Erdölbehälter in der Weise
verbunden, daſs das Oel durch seine Schwerkraft in den Ofen einflieſst. Damit dies
immer unter gleichem Drucke geschieht, ist der Behälter durch ein
Schwimmer-Zulaſsventil mit einem Hauptbehälter verbunden, so daſs der Stand des
Oeles im ersteren Behälter immer auf einer bestimmten Höhe erhalten wird. Die Menge
des in den Ofen flieſsenden Oeles kann man mittels des Hahnes M regeln. Das Rückschlagventil P verhindert ein Zurückdrängen des Oeles in die Rohrleitung, wenn der
Druck im Ofen steigt. Durch die Mitte der Austrittsdüse für das Oel ist ein dünnes
durchlochtes Rohr angeordnet, durch welches Wind tritt und das Oel zerstäubt.
(Schluſs folgt.)
Tafeln
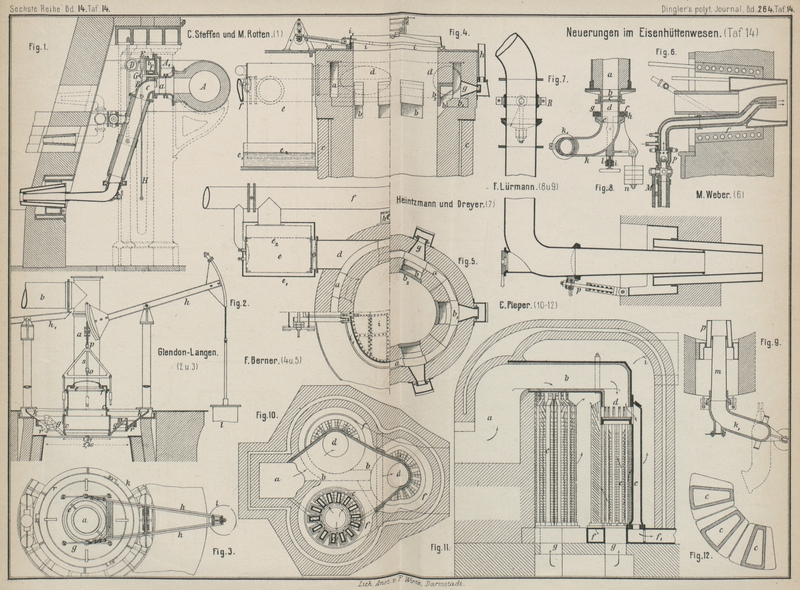