Titel: | Ueber Neuerungen im Eisenhüttenwesen. |
Fundstelle: | Band 266, Jahrgang 1887, S. 386 |
Download: | XML |
Ueber Neuerungen im Eisenhüttenwesen.
(Patentklasse 18. Fortsetzung des Berichtes S. 303
d. Bd.)
Mit Abbildungen auf Tafel 22.
Ueber Neuerungen im Eisenhüttenwesen.
Bereits im Band 263 * S. 477 wurde ein Schachtofen von Husgafoel beschrieben, welcher zur direkten Erzeugung
des Schmiedeeisens aus Erzen dient. Ueber diesen Ofen sind in der Oesterreichischen Zeitschrift für Berg- und
Hüttenwesen, 1887 S. 475 nähere Angaben enthalten, welche Dr. Leo aus Jernkont. annaler,
1887 II entnommen hat und die der Berücksichtigung werth sind. Nach denselben ist
der Ofen aus den alten „Stücköfen“ (vgl. Wedding,
Handbuch der Eisenhüttenkunde, 1864 Bd. I S. 488) hervorgegangen, deren
Betrieb im J. 1875 in Finnland dadurch wesentlich vervollkommnet wurde, daſs man den
Herd auswechselbar anordnete. Dadurch fiel das früher erforderliche Ausblasen des
Ofens nach jedesmaliger Zusammenschweiſsung eines „Stückes“ fort. Dann
ordnete man an den dem Verschleiſs am meisten ausgesetzten Ofentheilen Wasser-,
später Luftkühlung an, und benutzte endlich 110 bis 120° heiſsen Wind, wodurch die
Leistung des Ofens ganz erheblich vergröſsert wurde. Trotzdem blieben aber
Versetzungen im Ofen nicht aus. Man stellte deshalb den Ofenschacht aus doppelten
Blechwänden her und führte durch diesen den Gebläsewind, einerseits um letzteren
anzuwärmen, andererseits um den Ofen abzukühlen. In Folge dessen konnte das
reducirte Eisen am Ofenmantel nicht leicht festschweiſsen; trotzdem herrschte aber
im Herd gute Schweiſshitze. Ein nach diesen Prinzipien auf Wärtsilähütte gebauter
Ofen ergab eine erhebliche Kohlenersparniſs und eine gröſsere Leistung. Die
betreffenden Zahlen in den Jahren 1875 und 1884 sind 1,05 : 2,8 und 3,13 : 5,36. Im
J. 1886 wurde zu
Dobrianskji in Ruſsland ein derartiger Ofen in Betrieb gesetzt; derselbe sollte
10m,75 Höhe (wovon die obersten 2m,75 als Gasfang dienen) erhalten, wurde aber nur
auf 8m Höhe gebracht. Der Kohlensack hat eine
Weite von 1m,50, die Gicht von 1m,20. Der hohle Schachtmantel hat eine Weite von
175mm und besteht aus Blechen von 4mm,75 (oben), 9mm,5 und 12mm,75 (unten) Stärke. Der
untere Theil des unteren Schachtmantels ist 1m,5
hoch und mit 40 bis 50mm starken Chamottesteinen
ausgefüttert. Der obere Schachttheil ist ganz frei. Der Schacht wird von 4 Pfeilern
getragen, welche auf einem von einem Kreuzkanal durchzogenen und mit einer
Guſsplatte bedeckten Mauerklotz stehen. Der auswechselbare Herd besteht aus einem
festen Boden mit Rädern, 2 Formwänden mit je 4 paarweise in 2 Reihen über einander
gelegenen Formöffnungen, 2 Schlackenwänden, jede mit 4 Schlackenabstichen und einem
losen Einlegeboden. Auſsen besitzt der Herd 2 Zapfen, um welche er gekippt werden
kann. Er steht auf einer durch einen Gegengewichtshebel senk- und hebbaren
Plattform. Zum Betriebe sind 3 Herde erforderlich. Ein Ofen nimmt einen Raum von
12m,25 Länge und 8m,5 Breite ein.
Der Ofen zu Dobrianskji war im J. 1886 44 Tage und dann wieder 119 Tage im Betrieb,
und erwies sich nach dem Ausblasen als nicht ausbesserungsbedürftig. Während dieser
Zeit wurden die verschiedensten Materialien: Magneteisenstein, Eisenspath,
Brauneisenerz, Frisch-, Puddel-, Schweiſsofenschlacken und Walzsinter anstandslos
verblasen. Die Tagesproduction bei der Reduction von Schlacken war 475 bis 550k, sie stieg aber bis auf 1500k bei Benutzung von Magneteisenstein. Als
Brennmaterial benutzte man Holzkohle.
Der Betrieb des Ofens findet in folgender Weise statt. Die leeren Räume zwischen dem
losen Boden und den Herdwänden werden mit Kohlengestübbe, der Herd selbst mit Thon
und Kalk oder Dolomit ausgestrichen und dann angewärmt. Man füllt ihn hiernach mit
Kohle, fahrt ihn unter den Schacht, bestreicht seine obere Kante mit Thon und preſst
ihn mittels des Hebels gegen den Schacht. Hierauf schlieſst man die Schlackenstiche
und füllt den Ofen mit nach oben immer schwerer werdenden Gichten. Man bringt dann
durch die untersten Formen glühende Kohle in den Herd und gibt Wind von allmählich
sich steigernder Pressung. Dabei läſst man den Wind in immer höher liegende Theile
des Schachthohlraumes eintreten, je höher die Hitze im Ofen selbst steigt. Mit dem
Anwachsen des „Stückes“ werden auch die stechenden Düsen höher verlegt und
die leeren Formen mit Thonpfropfen geschlossen. Die Schlacke wird nur dann
abgestochen, wenn Ueberschuſs davon vorhanden ist. Ist das „Stück“ groſs
genug, so senkt man den Herd etwas und schiebt ihn vermittels des nächsten Herdes,
welcher bereits mit angezündeter Kohle gefüllt ist, unter dem Schacht fort. Der
volle Herd wird dann gekippt und das „Stück“ unter dem Hammer ausgeschmiedet; der Abgang
hierbei beträgt 10,95 Proc. Das nachherige Schweiſsen in Gasschweiſsöfen und
Auswalzen zu Blechen ergab 7,32 Proc. Abbrand. Die Bleche (75 Proc. erster Qualität)
waren im Allgemeinen weicher und zäher als Puddelbleche. Der Kohlenstoffgehalt des
„Stückes“ kann durch das Stechen der Düsen, die Gröſse des Erzzusatzes,
die Menge und die Wärme des Gebläsewindes geregelt werden, so daſs Schmiedeeisen,
Stahl oder Roheisen erzeugt wird. Zur Beurtheilung des Ofenganges dienen das
Aussehen der Gichtflamme, das Verhalten der Schlacke und die Beschaffenheit des
„Stückes“, welche durch Einführen eines Brecheisens durch eine Form auf
seine Festigkeit untersucht werden kann. Als Mittel zur Aenderung des Ofenganges
dienen hauptsächlich die Höhe, in welcher der Wind in den Ofenmantel eingelassen
wird, und die Pressung desselben. Die bei Schmiedeeisen bezieh. schmiedbarem Stahl
fallende Schlacke enthielt in Dobrianskji 40,8 bezieh. 7,15 Proc. Eisen. Der
Phosphor geht in die Schlacke, und zwar um so mehr, je vollständiger die Reduction
des Erzes stattfindet.
Wenn nun auch eine Verwerthung dieser Resultate in Deutschland ausgeschlossen
erscheint, so geben sie doch einen Beweis dafür, wie schnell und bis zu welchem
Grade ein alter Ofen unter Verwendung der neueren Hilfsmittel der Technik
vervollkommnet werden kann. Zweifellos wird der Husgafoel'sche Stückofen demnächst eine gröſsere Rolle spielen in
Gegenden, wo noch Holzkohle in ausreichendem Maſse zu beschaffen ist, d. i. in
Ruſsland und Schweden, ganz besonders aber in den österreichischen Alpenländern.
Auf demselben Wege will Schmidhammer Luppen erzeugen
(vgl. Stahl und Eisen, 1886 * S. 465). Der von
demselben vorgeschlagene Schachtofen (Fig. 2 bis 4) hat 4m Höhe und 0m,6
Weite. Der untere Theil des Ofens erweitert sich nach der Seite in eine Kammer,
deren Kopſseite durch eine Thür geschlossen ist. An den Seiten der Kammer sind
kleine Arbeitsthüren angeordnet, um das zusammenzuschweiſsende Eisen zusammenpressen
und gegen die Thür hin schieben zu können, aus welcher die Luppe herausgenommen
wird. In der Höhe der Oberkante der Kammer münden in den Schacht Düsen G und W zum Einleiten von
Wassergas und Gebläsewind, welche vorher in Wärmespeichern, die durch die Gichtgase
erhitzt worden sind, auf eine möglichst hohe Temperatur gebracht werden. Eventuell
kann man die Gichtgase vermittels eines Körting'schen
Strahlapparates absaugen. Der Schacht soll mit Erz und soviel Holzkohle als gerade
nöthig ist, um ersteres zu reduciren, beschickt werden. Nimmt man an, daſs die Kohle
nur zu Kohlenoxyd verbrannt wird, so kommen auf 100k Eisen 34k,5 Kohlenstoff und bei einem
Eisengehalt der Erze von 49 Proc. 204k Erz.
Hiervon faſst der Schacht 111k Kohle und 657k Erz. Es wird nun berechnet, daſs zum Reduciren
und Schmelzen von 100k Eisen und zum Schmelzen von
zugehörigen 58k Schlacke unter Hinzuziehung von 20
Proc. Wärmeverlust 272160 Kalorien verbraucht werden, während die erforderliche Kohlemenge von 34k,5 bei der Verbrennung zu Kohlenoxyd nur 85318
Kalorien entwickelt. Demnach müssen durch die Verbrennung des Wassergases noch
186842 Kalorien entwickelt werden. Hierzu sind 41k,7 Wassergas oder 68k,4 Kohlenstoff
nothwendig. Zur Verbrennung des ersteren gehören 129cbm,8 Luft. Sieht man von der Verwendung des Wassergases ab, so müſste man
natürlich mehr Holzkohle aufwenden.
Die Production eines derartigen kleinen Ofens wird zu 600 bis 1000k in 12 Stunden angenommen, und sollen die Luppen
sofort in einen Stahlschmelzofen eingesetzt werden. Die Kosten des Verfahrens sollen
nicht viel mehr als diejenigen der Roheisen-Darstellung betragen.
Hiernach ist der Schmidhammer'sche Vorschlag auch für
Deutschland nicht ohne Werth, weil er von der ausschlieſslichen Benutzung von
Holzkohle absieht. Fraglich bleibt nur, ob sich der Kostenpunkt nach der Anschauung
des Erfinders stellt. Bekanntlich scheitern gerade hieran die meisten Verfahren der
direkten Eisenerzeugung.
Das Shedock'sche Verfahren, worüber besonders in der
englischen Fachpresse viel geschrieben worden ist (vgl. u.a. Eisen-Zeitung, 1887 S. 557) und welches darin besteht, daſs das fein
pulverisirte Erz zusammen mit reducirendem Gas durch ein Metallbad gepreſst wird,
scheint praktisch nicht verwerthbar zu sein, obschon der Gedankengang des Erfinders
theoretisch auf richtiger Grundlage steht. Das reducirende Gas – Kohlenoxyd – soll
das Erz beim Passiren des Metallbades reduciren, so daſs letzteres das Eisen
aufnimmt, während die erdigen Bestandtheile des Erzes vom Bade als Schlacken
abgezogen werden. Einer Verbrennung der Eisenpartikelchen nach der Reduction ist dadurch vorgebeugt.
Einrichtungen an Hochöfen.
In The Iron Age vom 21. Juli 1887 ist eine selbstthätige
Vorrichtung zum Begichten der Hochöfen beschrieben (vgl. auch 1887 263 * 470). Dieselbe macht jede Handarbeit an der Gicht
entbehrlich und ist in Folge dessen ein neuer Schritt weiter in dem Ersatz der
Handarbeit durch Maschinen. Die Vorrichtung ist von Fayette
Brown der Brown Hoisting and Conveying Machine
Company in Cleveland, Ohio, construirt und in den Riverside Iron Works in Steubenville, Ohio, ausgeführt, wo sie bereits
seit längerer Zeit gute Dienste leistet. Eine ähnliche Vorrichtung ist seit 4 Jahren
an den Stewart'schen Hochöfen in Sharon, Pennsylvanien,
ferner an den Oefen des Lucy-Werkes in Pittsburg und
der Ohio Iron Company in Jamesville, Ohio, mit bestem
Erfolge in Betrieb.
Die Vorrichtung Fig. 5 besteht aus einer steil ansteigenden Gichtbrücke T, welche mit ihrem unteren Ende bis in eine Grube des
Möllerhauses hineinreicht und oben die Gicht des Ofens noch um ein beträchtliches
Stück überragt. Auf dieser Brücke ist ein Geleise R2 und zwischen den Schienen dieses Geleises
noch ein engeres Geleise R angeordnet, welches letztere
dicht über der Gicht nach innen umgebogen ist. Die Gichtwagen S sind mittels eines langen Bügels N mit dem Aufzugseil O
verbunden, welches am oberen Ende der Brücke über eine Rolle geht und von einer auf
der Ofensohle stehenden Dampfwinde aufgewunden werden kann. Die Gichtwagen werden,
wenn sie in der Grube des Möllerhauses stehen, gefüllt, was sehr leicht von statten
geht, weil das Material nur in dieselben geschoben zu
werden braucht. Windet man dann die Gichtwagen in die Höhe, so laufen die vorderen
Räder, welche näher zusammenstehen als die hinteren, auf den mittleren Schienen,
während die hinteren Räder auf den äuſseren Schienen rollen. In Folge dessen nimmt
der Wagen S, wenn er die Gicht erreicht, die
gezeichnete Stellung ein, so daſs sein Inhalt in jene entleert wird. Damit der Wagen
diese Stellung richtig einnimmt, ist die Hinterachse desselben in der Fahrrichtung
verstellbar. Die Gicht selbst hat einen doppelten Verschluſs, erstens den Trichter
h, welcher in bekannter Weise durch einen Balancier
B und Luftcylinder C
gesenkt und gehoben werden kann, und zweitens die Klappthüren D, welche durch Zugstangen mit Armen der Wellen G verbunden sind. Diese werden vermittels eines
Seiltriebes von dem auf der Hüttensohle stehenden Handrade W aus gedreht, während neben diesem das die Bewegung des Luftkolbens C bewirkende Ventil angeordnet ist. Die Begichtung ist
also vollständig in die Hand des Betriebsleiters gegeben. Ist der Trichter h geschlossen, so sind die Klappen offen; die
Begichtung kann also geschehen. Soll die Gicht in den Ofen gelassen werden, so
schlieſst man, um Gasverluste zu vermeiden, die Klappen D und senkt dann den Trichter h. Die Höhe der
Ofenfüllung wird durch den Trichter h bezeichnet,
dessen Stellung auf der Hüttensohle bei I ebenfalls
kenntlich gemacht ist. Ebenso wird die Zahl der in den Trichter entleerten Wagen
unten angezeigt, so daſs sich der Leiter über alles vergewissern kann, ohne seinen
Fuſs auf die Gicht zu setzen. Die Spannweite der Gichtbrücke der Riverside Iron Works ist 26m,5 lang, dazu kommen noch 9m,45, welche
die Verlängerung der Brücke in die Grube des Möllerhauses hineinreicht, und 8m,65, um welche die obere Verlängerung der Brücke
den 23m,164 hohen Ofen überragt. Der Durchmesser
des Ofenmantels an der Gicht ist 5m,5. Jeder Wagen
faſst 2cbm,123. Der Möllerboden liegt 5m,79 unter der Ofensohle. Die Dampfwinde hat 2
Cylinder von 25cm Durchmesser und 38cm Höhe, und eine Trommel von 1m,22 Durchmesser mit Bremsband.
An seiner unter * D. R. P. Nr. 34162 vom 4. Juli 1885 patentirten
Begichtungsvorrichtung (vgl. 1886 239 * 361) hat W. van Vloten in Dortmund (* D. R. P. Nr. 39299 vom 21.
Juli 1886) eine Abänderung getroffen. Dieselbe besteht darin, daſs der Raum a (Fig. 6), in welchen die
Beschickung gekippt wird, durch eine Ringwand c in 2
Theile geschieden wird, welche durch je einen besonderen Kegel k bezieh. k1
unten geschlossen
werden. Dementsprechend ist auch unter diesen Kegeln im Ofen eine Ringwand
angeordnet, so daſs beim Senken der Kegel k bezieh. k1, einzeln oder
zusammen, oder beim Heben von sich auf die festen Kegel aufsetzenden Ringwänden, ein Theil der Beschickung gegen die Ofenwand, der
andere Theil gegen den Ring c rutscht, so daſs
hierdurch eine gleich mäſsigere Vertheilung der Beschickung über den Ofenquerschnitt
stattfindet.
Eine bemerkenswerthe Construction des Hochofengestelles gibt Fritz W. Lürmann in Osnabrück in seinem Patente (* D. R. P. Nr. 40428 vom 9. Juli 1886). Bekanntlich ist bei den Hochöfen bekannter Einrichtung das Gestell in
Folge der hier herrschenden hohen Temperatur und der stark basischen Schlacke einem
schnellen Verschleiſs ausgesetzt. Letzterer wird noch dadurch beschleunigt, daſs die
ganze Rast mit den Windformen u.s.w. auf dem Gestell ruht, so daſs die Steine
desselben leicht zerdrückt werden, oder sich verschieben, was natürlich den Ruin des
Gestelles noch mehr beschleunigt. Lürmann hängt deshalb
die ganze Rast mit den Formen an den den Schacht tragenden Säulen auf. Eine
derartige Construction ist in Fig. 7 und 8
dargestellt. Hier ruht auf den Tragsäulen a ein starker
Kastenkranz b, welcher aus gebogenen ⌶- oder ⊏-Eisen
besteht. Auf den Kranz b wird der Schacht c aufgebaut. Unterhalb des Kranzes ist vermittels
Winkelstreben e, Winkeleisen u.s.w. ein kegelförmiger,
aus starkem Eisenblech hergestellter Tiegel d
befestigt, derselbe besitzt an seinem unteren Ende einen starken Kranz f, welcher das Mauerwerk der Rast unterstützt. Die
Bleche des Tiegels d sind durchlocht, damit das an den
Blechen herunterflieſsende Wasser in die Steine dringen und diese dadurch kühlen
kann. Die Rinne f dient zur Aufnahme und Fortleitung
des Kühlwassers. Natürlich kann sich das Rastmauerwerk in dem Tiegel unabhängig vom
Schacht und Gestell ausdehnen und zusammenziehen. An dem unteren Kranz f des Tiegels sind die Kühlkasten k mit den Formen l auf
irgend eine Weise, z.B. durch Hakenkeilbolzen n (Fig. 8)
aufgehängt. Die Querträger des Kranzes b sind nach
auſsen verlängert, um das Heiſswindrohr b4 mit Wärmeschutzhülle b7, das Kühlwasserrohr b5 und die Laufbühne
b6 zu
unterstützen.
Zu dem 1886 262 * 255 mitgetheilten Apparat zur Vornahme
von Biegeproben in Stahlwerken sei hier noch eine andere äuſserst praktische
Maschine der Steel Company in Scotland mitgetheilt (Zeitschrift des Vereins deutscher Ingenieure, 1886 Bd.
30 * S. 434). Wie aus Fig. 9 und 10
ersichtlich, besteht die Maschine aus einem sehr schnell auf und ab gehenden Stempel
D und unter diesem angeordneten 3 Stufenreihen. Der
vorher Was durchgebogene Probestab wird unter diesen Stempel gestellt und von Stufe
zu Stufe gehoben, bis er bricht oder ganz flach zusammengebogen ist.
Tafeln
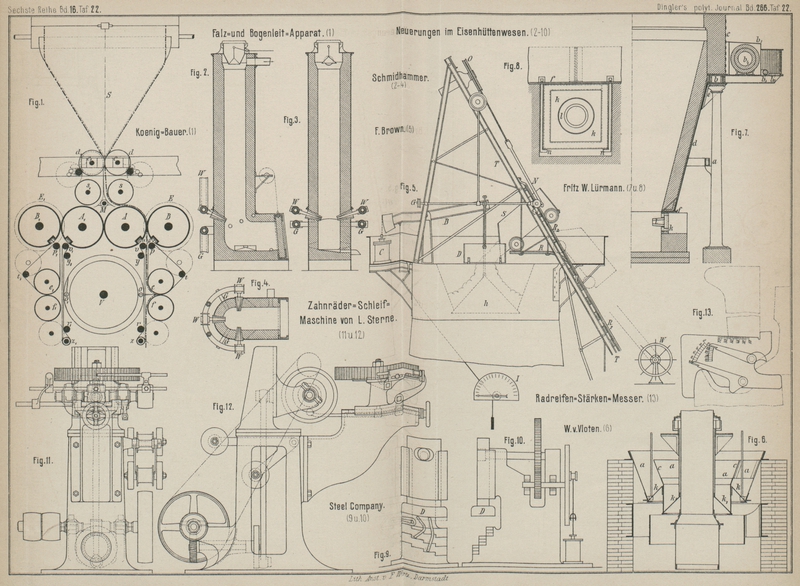