Titel: | Die Herstellung des Weissbleches. |
Fundstelle: | Band 267, Jahrgang 1888, S. 9 |
Download: | XML |
Die Herstellung des Weiſsbleches.
(Fortsetzung des Berichtes Bd. 266 S.
491.)
Mit Abbildungen auf Tafel
3.
Ueber die Herstellung des Weiſsbleches.
c) Das Glühen des Schwarzbleches.
Auf die Vorbeize des Schwarzbleches folgt das Glühen. Das Glühen und langsame
Abkühlen des Bleches hat den Zweck, demselben die durch das Walzen im Blechwalzwerk
und zwischen den Kaltwalzen hervorgerufene Härte und Sprödigkeit zu nehmen. Das
Glühen erfolgt jetzt nur noch in Kisten; Fig. 1 und la. Dieselben
bestehen aus einem Untersatze a mit Längsrippen auf der
unteren Seite und einem Rande b auf der oberen Seite.
In diesen hinein setzt man die eigentliche Kiste c. Als
Material für die Kisten benutzte man bis vor Kurzem ausschlieſslich Guſseisen,
neuerdings auch Guſsstahl, Bessemer-Fluſseisen und Schweiſseisen. Letzteres hat den
Vortheil, daſs man die Kisten bei Verwerfungen wieder gerade hämmern kann. Die
Gröſse der Kisten wird zweckmäſsig derjenigen der Bleche möglichst genau angepaſst,
um todte Räume zu vermeiden. Die Glühöfen zur Aufnahme der Kisten haben verschiedene
Einrichtungen. Als Regel gilt, daſs der Herd in der Höhe der Hüttensohle liegt, so
daſs die Kisten von einer fahrbaren Gabel mit langer Deichsel erfaſst und direkt an
Ort und Stelle in den Ofen gefahren werden können. Jeder Ofen nimmt je nach der
Gröſse der Bleche bis 4 Kisten auf. Zuweilen kommen auch Doppelöfen vor, welche bis
12 Kisten fassen. Die Schwierigkeiten, in derartigen Oefen die Kisten von allen
Seiten gleichmäſsig auszuglühen, hat zur Erfindung der
Kanalöfen geführt, welche einen ununterbrochenen Betrieb haben, so daſs an dem einen
Ende derselben kalte Kisten eingesetzt und an dem anderen Ende geglühte Kisten nach
erfolgtem Abkühlen herausgezogen werden.
Ein in Deutschland in Gebrauch stehender Ofen dieser Art ist in Fig. 2 bis 4 abgebildet. Derselbe
besteht aus einem oberirdischen Kanal a aus feuerfestem
Mauerwerk, dessen beide Enden durch schmiedeeiserne Flügelthüren b geschlossen sind. Die Sohle des Kanales a wird aus einzelnen, eine oder mehrere Glühkisten
aufnehmenden Theilen c gebildet, die auf Rädern, Fig. 5, oder
guſseisernen Kugelbahnen d laufen und vermittels einer
vor einem Ende des Kanales stehenden starken Winde durch den Kanal a geschoben werden können. Laufen die Sohltheile auf
Rädern, so sind sie gegen die Seitenwandungen des Kanales durch einen fortlaufenden
Sandverschluſs e, Fig. 5, abgedichtet, um
die Flamme von dem Laufwerke der Sohltheile fernzuhalten. Diese Einrichtung ist bei
den Kugelbahnen d nicht erforderlich. Letztere sind
trotzdem viel haltbarer als Räderwerk und deshalb vorzuziehen. Auf ein Drittel jeder
Längsseite des Kanales a liegt eine Gasfeuerung f, deren Flamme nur das linke Drittel des Kanales
a durchzieht und am linken Ende desselben durch die
an den Seiten angeordneten Füchse g entweicht. Der
andere Theil (⅔ der Länge) des Ofens bleibt ungeheizt und dient als Abkühlraum. In
einigen Werken ist er sogar durch eine Scheidewand h in
zwei Abtheilungen geschieden, so daſs dadurch ein Glüh-, ein Abkühl- und ein
Kaltraum geschaffen wird. Die Scheidewand h ist nach
oben aus dem Kanal herausziehbar und besteht dann aus einem Stück, oder sie wird aus
zwei Schiebern gebildet (wie gezeichnet), die nach beiden Seiten aus dem Ofen
herausgezogen werden können. In letzterem Falle laufen die Schieber auf Rollen oder
hängen an einer Hängebahn. Sie selbst werden aus einem schmiedeeisernen Gerippe mit
Steinfüllung gebildet. Der Betrieb besteht nun darin, daſs in gewissen
Zeitabschnitten (2 Stunden) die Thüren des Kanales a
geöffnet, die Scheidewand b herausgezogen und die ganze
Sohle c vermittels der Winde um eine Sohltheillänge
entgegen der Flammenrichtung nach rechts geschoben werden. Dadurch wird im Glühraum
(am linken Ende des Kanales d) ein Platz für einen
neuen Sohltheil frei, der unmittelbar vor diesem gelegene Theil wird den Feuerungen
näher gerückt, der zwischen diesen befindliche Sohltheil kommt in den Abkühlraum,
aus diesem gelangt ein Sohltheil in den Kaltraum und letzterer entläſst einen
Sohltheil ins Freie. Nach Einschiebung eines neuen Sohltheiles werden die Thüren
wieder geschlossen und die Scheidewand wird eingeschoben. Die Temperaturen des
Glühraumes, in welchen die Kisten bis 6 Stunden verbleiben, betragen etwa 1000°, des
Abkühlraumes links des Schiebers etwa 150 bis 250°. Die Oefen sind zur Aufnahme von
7 Sohltheilen eingerichtet. Der Kanal hat eine lichte Breite von 1m,8 und eine Länge von 15m. Die Zuggeneratoren f haben Schächte von quadratischem Querschnitt, Um dieselben herum sind
Luftkanäle angeordnet, welche die vorgewärmte Verbrennungsluft durch die
Feuerbrücken in den Ofenraum entlassen. Ebenso ist die Decke der Generatoren und des
zwischen ihnen liegenden Ofengewölbes von Luftkanälen durchzogen, welche über den
Feuerbrücken mit dem Ofeninneren in Verbindung stehen. Zwischen den 6 Luftöffnungen
liegen die 3 Gasöffnungen. Die Gestalt der Luftkanäle ist aus der Zeichnung
ersichtlich. Die Glühkisten stehen auf den Sohltheilen e so, daſs die Längsrippen der Untersätze (Fig. 1) parallel der
Flammenrichtung liegen und die Flamme die Böden der Untersätze bestreichen kann. Die
Bleche werden zu 800 bis 1000 Stück in einem oder zwei Haufen auf die Untersätze
gelegt. Es wird dann die Kiste vermittels eines Krahnes, dessen Greifer unter, an
denselben angegossene oder angenietete, Handhaben fassen, auf den Untersatz
gestülpt, und der Raum zwischen Kiste und Untersatz mit Sand, Lehm, Eisenkitt oder
Hammerschlag vollgeschlagen. Man bringt dann das Ganze in den Ofen. Die Temperatur
beim ersten Glühen soll etwa 1000°, beim Fertigglühen 800° betragen.
Nach dem ersten Glühen folgt das Kaltwalzen zwischen Hartguſswalzen zum Glätten der
Bleche, dann das zweite Glühen und dann die Fertigbeize. Aus dieser kommen die
Bleche naſs zum Verzinnen.
d) Die Verzinnung des Schwarzbleches.
Zur Verzinnung braucht man entweder reines Zinn oder
eine Legirung von 3 Th. Blei mit 1 Th. Zinn. Die mit ersterem hergestellten Bleche
heiſsen Glanzbleche, die anderen Mattbleche. Zur Bedeckung der Metallbäder dient Fett,
und zwar afrikanisches Palmöl; dasselbe siedet bei 300°, entwickelt aber nicht so
viel Dämpfe als der früher allgemein übliche Talg. Die Arbeit des Verzinnens ist in
Folge dessen nicht mehr so ungesund, als sie es früher war. Auſser dem Palmöl kommen
noch, besonders bei den sogen. Verzinnmaschinen, Fluſsmittel (flux) zur Anwendung,
welche die Metallbäder nicht allein gegen Oxydation durch die Luft schützen, sondern
auch das beim Eintauchen in das Metallbad durch das Fluſsmittel hindurch gehende
Blech nochmals beizen sollen.
Die jetzt üblichen Verzinnherde haben 5 Kessel, Fig. 6 bis 8. Dieselben sind in einem
rechteckigen Mauerklotze derart eingemauert, daſs unten und an den Seiten von 4
Kesseln Feuerzüge bleiben. Der Mauerklotz steht entweder frei oder lehnt sich an die
Gebäudemauer an. In letzterem Falle sind die Feuerthüren der Kessel auf derjenigen
Seite des Herdes angebracht, auf welcher die Arbeiter während des Verzinnens stehen.
Im anderen Falle liegen die Feuerthüren auf der entgegengesetzten Seite, was aber
den Nachtheil hat, daſs die Arbeiter ihre Feuerungen nicht genügend unter Aufsicht
haben. In dem ersten Kessel a ist Fett, welches durch
Wärmeleitung vom Grobkessel b flüssig erhalten wird.
Letzteres ist mit schlechterem Zinn und Fett gefüllt und werden beide durch eine
Feuerung auf etwa 400° gehalten. Zwischen b und dem
Bürstkessel c, oder zwischen e und dem Durchfuhrkessel d liegt die
Bürstplatte v. Neben d ist
der Walzkessel e angeordnet. Letzterer ist mit reinstem
Fett gefüllt, während d reinstes Zinn mit einer dünnen
reinsten Fettschicht, c aber weniger gutes Zinn und
Fett enthält. Die Temperatur von d soll etwa 250°,
diejenige von c nicht über 240° betragen, während
diejenige von e zwischen 400 und 250° liegt. Im
Walzkessel e liegen gewöhnlich 5 Walzen, welche derart
umgetrieben werden, daſs das Blech von den oberen beiden linken Walzen nach unten
geführt, und wenn es wieder zwischen die unteren Walzen gehoben wird, von diesen und
den oberen beiden rechten Walzen aus dem Fettbad herausgezogen wird. Wichtig ist,
daſs die Mittellinien der oberen Walzen etwas über der
Fettoberfläche liegen. Die Lagerung der Walzen in den sogen. Walzenstöcken und die
Vorrichtungen zum Heben des Bleches zwischen die unteren Walzen sind verschieden
(vgl. auch 1882 244 * 213). Ein neuerer englischer Walzkessel, welcher sehr
gut arbeitet, ist in Fig. 9 dargestellt. Die Lagerung der Walzen ist im Allgemeinen diejenige
des Ecaille'schen Verzinnherdes (vgl. 1885 256 * 59). Bemerkenswerth ist jedoch die
Umwerfvorrichtung, welche aus 2 einfachen Gewichtshebeln yx besteht. Dieselben werden, wenn das Blech von den Walzen in den Kessel
eingeführt wird, von ersteren zurückgedrückt, bewegen aber das Blech sofort nach
rechts, wenn es die Walzen verlassen hat. In Folge dessen fällt es in den Korb z, welcher in Führungen w
gleitet und vermittels der Ketten v mit dem Hebel a1 verbunden ist. Durch
die Kettenwelle b1 kann
die Länge der Kette verändert und dadurch der Kessel verschiedenen Blechgröſsen während des Betriebes angepaſst werden, was ein
wesentlicher Vortheil ist.
Die Arbeit bei dem Verzinnherd Fig. 6 bis 8 geht nun in folgender
Weise vor sich. Die aus der Fertigbeize kommenden Bleche werden noch naſs in den
Fettkessel a gesetzt, bis er gefüllt ist. Nach etwa 10
Minuten, während welcher das anhaftende Wasser verdampft ist, sind die Bleche
genügend angewärmt, um vermittels einer zweihändigen Zange packetweise in den
Grobkessel gesetzt werden zu können. In diesem verbleiben sie auch etwa 10 Minuten,
während welcher der betreffende Arbeiter sie zuweilen auseinandertheilt, damit das
Zinn sie allseitig berühre. Dann wird ein Packet Bleche aus dem Grobkessel in den
Bürstkessel gesetzt, und werden nach einiger Zeit 20 Bleche aus diesem
herausgenommen und auf die Bürstplatte gelegt. Der Arbeiter faſst dann die Bleche
einzeln mittels einer kleinen Handzange und bürstet sie auf beiden Seiten mit einer
langen Bürste ab. Jedes Blech wird dann schnell in den Durchführkessel getaucht, in
welchem die Bürststreifen verschwinden, und wird dann der Zinnüberzug im Walzkessel
geglättet und geregelt. Derartige Herde sind in mehr oder weniger gleicher Anordnung
in allen Weiſsblech erzeugenden Ländern in Gebrauch. Die Production derselben
beträgt etwa 30 Kisten in einer Schicht.
(Fortsetzung folgt.)
Tafeln
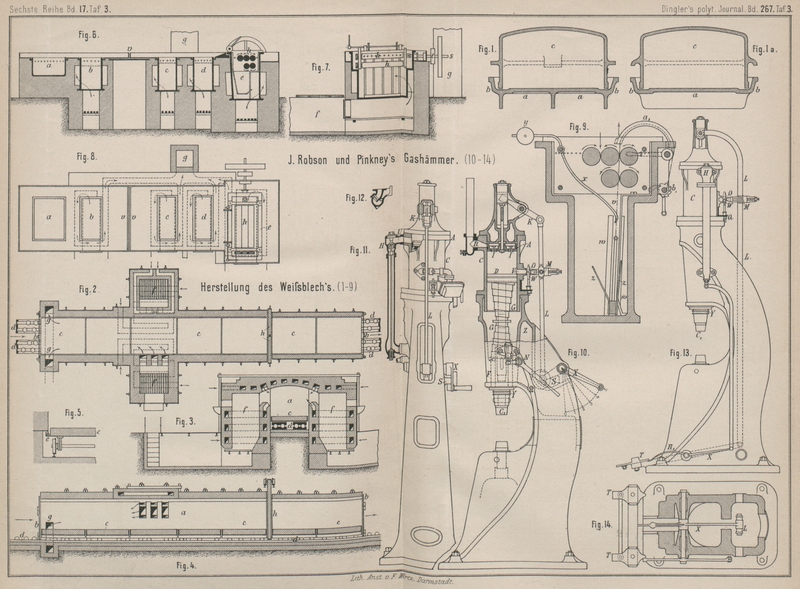