Titel: | Neuerungen in der Anordnung und Herstellung der Röhren. |
Fundstelle: | Band 269, Jahrgang 1888, S. 355 |
Download: | XML |
Neuerungen in der Anordnung und Herstellung der
Röhren.
Mit Abbildungen im Texte und auf Tafel 18.
Neuerungen in der Anordnung und Herstellung der Röhren.
A) Ersatz der guſseisernen Röhren
durch Holz- und genietete Eisenblechrohre.
Mehrfach sind Vorschläge gemacht worden, die bisher gebräuchlichen Guſseisenröhren
durch Röhren aus anderem, billigerem Materiale zu ersetzen, welches entweder am Orte
des Verbrauches sich vorfindet, oder dessen Anfuhr weniger Schwierigkeit bietet, als
die der Guſseisenröhren. Soll zugleich die Leitung widerstandsfähig gegen
bedeutenden Druck sein, so wird Holz und Schmiedeeisen in erster Reihe in Frage
kommen.
Röhrenleitung aus Cement. Für stark
vitriolische Gebirge hat nach den Mittheilungen der Zeitschrift für das Berg-, Hütten- und Salinenwesen in Preußen, Bd. 36 S.
231, die Berginspection in Rammeisberg Röhren von Cement verwendet. Da dieselben
theilweise auf starken Druck in Anspruch genommen wurden und die erhebliche Weite
von 30cm hatten, so verwendete man
Drahtseileinlagen. Die Seile wurden geglüht, in einzelne Litzen, zu 3 Drähten von
3mm,5 Stärke, zerlegt, und diese auf einen
Holzcylinder gewickelt. Die Einrichtung desselben und das Herstellungsverfahren
werden a. a. O. genau beschrieben. Als Material benutzte man 1 Th. Portlandcement
auf 5 Th. Granitsand, welches bei wagerechter Lage des Holzcylinders zunächst an der
oberen Seite, und, nachdem diese hinreichend verhärtet, an der nun nach oben
gedrehten bisher noch freien Seite aufgebracht wurde. Die Cementschicht erhielt eine
Dicke von 12 bis 15mm. Die Auskleidung und
Glättung der Innenwand des Drahtcylinders geschah nachträglich mit der Hand. Die
Länge der Röhren ist 1,5 bis 2m und kosten
dieselben bei 1m,5 Lange 6,50 M.
Fig. 1., Bd. 269, S. 355Hölzerne Wasserleitungen für gröſsere Weiten
werden nach amerikanischen Fachzeitungen (Engineering and
Building Record, 1888 S. 196) neuerdings von der Wasserleitungsgesellschaft
in Denver, Colorado, angewendet. Das Rohr wird, ähnlich einem Fasse, aus durch
Rundeisenreifen zusammengehaltenen Dauben von 100mm Breite und 40 bis 50mm Stärke
gebildet. Je nach der Stärke des Druckes sind die Reifen 12 bis 15mm stark und in Abständen von 100 bis 200mm angebracht. Zum Anspannen und Nachziehen
derselben dient nebenstehend angedeutete Anordnung. In Denver sollen in der
bleibenden Leitung solche Rohre in Weiten von 600 bis 1200mm bei einem Drucke bis zu 4at und mit Krümmungen bis zu 60m Halbmesser liegen. Zum Legen der Leitung wird
bei 600 bis 800mm Weite eine halbe bis ein drittel
Arbeitsschicht für den laufenden Meter erforderlich. Die Gesammtkosten sind
selbstredend in hohem Maſse von den örtlichen Verhältnissen abhängig. Die Abzweigungen werden
immerhin vortheilhaft durch guſseiserne Formstücke bewirkt werden.
Die Zeitschrift „Stahl und Eisen“ hat schon mehrfach darauf hingewiesen, daſs unter
Umständen die gebräuchlichen guſseisernen Röhren vortheilhaft durch solche aus Schmiedeeisen ersetzt werden können. Im Anschlusse an
eine Mittheilung über eine schmiedeeiserne Rohrleitung von 14km,5 Länge und 1270 bis 1350mm Weite, welche angeblich mit groſser
Kostenersparniſs anstatt einer guſseisernen Leitung von der Verwaltung der Stadt
Melbourne verwendet wurde, gibt sie in Nr. 5 vom Jahre 1888 nachstehende Angaben
über einen von Robert S. Moore in San Francisco der Institution of Engineers and Shipbuilders in Scotland
gehaltenen Vortrag, die Ausführungsweise schmiedeeiserner Rohrleitungen
betreffend:
Die von Moore beschriebene Rohrleitung war bestimmt, von
dem etwa 45km entfernten Crystal Springs Lake Wasser nach San Francisco zu führen. Der erste Theil
der Leitung von 1118mm Durchmesser erstreckt sich
von der Quelle bis zu einem Sammelbecken von etwa 150000cbm Inhalt, welches 2km,4 vor der Stadt
in einer Höhe von 61m über derselben gelegen ist.
Von dort ab nimmt der Durchmesser auf 940mm und in
der Stadt selbst bis auf 838 und 762mm ab. Zur
Fertigstellung der Röhren waren von der Risdon Iron and
Locomotive Works Co. in San Francisco besondere hydraulische maschinelle
Einrichtungen getroffen. Die Länge der einzelnen Röhren betrug je 8m,53. Die erforderlichen Bleche waren, aus
pennsylvanischem Schweiſseisen genau zugeschnitten, in Gröſsen von 1118 × 3607
bezieh. 3632mm und in den Stärken nach Blechlehre
Nr. 6 und 7 (5,15 bezieh. 4mm,57) angeliefert. Die
Zerreiſsfestigkeit des Eisens durfte nicht unter 35k,15 auf 1qmm sein und die
Elasticitätsgrenze nicht unter 40 Proc. dieses Maſses liegen.
Die Fabrikation der Röhren ging unter bedecktem Raume vor sich, wobei Bleche und
Nieten vor Feuchtigkeit möglichst geschützt waren. Sie wurden aus engeren und
weiteren Schüssen so zusammengesetzt, daſs die Schüsse kleineren Durchmessers fertig
zusammengenietet in den gröſseren Schüssen fest anschlieſsend paſsten. Behufs
Fabrikation der einzelnen Schüsse wurden die Bleche auf Wagen zu zwei mehrfachen
Lochmaschinen geschafft, auf deren erster die Löcher für die runden Nähte und auf
der zweiten für die Längsnähte ausgestoſsen wurden. Die Tische dieser Lochmaschinen
waren mit selbsthätigem Vorschübe für die Lochung versehen. Die Maschine machte etwa
50 Umdrehungen in der Minute und 10 Löcher während einer Umdrehung. Nach Verlassen
dieser Lochmaschine wurden die Bleche an den Kanten nachgearbeitet und in einer
Biegemaschine mit senkrechten Walzen zu Cylindern von der vorgeschriebenen Weite
gebogen. Nachdem alsdann die Schüsse unter einem Drucke von 4l in einander gepreſst waren, erfolgte die Nietung
auf hydraulischen Nietmaschinen, mit kalten, von auſsen in die Löcher eingesteckten Nieten. Die
Nieten bestanden natürlich aus dem besten Materiale, um die Verarbeitung im kalten
Zustande ertragen zu können. Die Ueberblattungen an den Schüssen wurden in der beim
Kesselbaue üblichen Weise bewirkt. Der gröſsere Theil der Röhren wurde in Längen von
je acht Schüssen so hergestellt, daſs an dem einen Ende ein engerer, an dem anderen
Ende ein weiterer Schuſs sich befand. Alle Nähte wurden mit dem Meiſsel verstemmt,
in ähnlicher Weise, wie man bei bester Kesselarbeit verfährt. Besondere Sorgfalt
wurde auf die Ueberblattungen verwendet. Hin und wieder wurde eine Röhrenlänge unter
dem Drucke von 8at,78 geprüft.
Nach Fertigstellung wurden die Röhren mit einer Mischung von Asphalt und Kohlentheer
überzogen. Zu diesem Zwecke waren zwei groſse Becken von 9m,75 Länge und 1m,20 Tiefe neben einander gestellt und mit direkter Feuerung versehen
worden. Die Asphaltmischung des Beckens, in welche das Rohr zuerst getaucht wurde,
wurde bei hoher Temperatur gehalten, diejenige des zweiten Beckens war niedriger.
Der Asphalt in dem ersten Becken enthielt einen gröſseren Zusatz von Kohlentheer und
war in Folge dessen flüssiger als die Mischung im zweiten Becken. Ersterer diente
hauptsächlich dazu, das Eisen zu erwärmen und an allen Stellen mit einem Ueberzuge
zu versehen. Das Rohr wurde jeweilig in dem ersten Becken 25 Minuten gelassen,
hierauf in aufrechter Lage über demselben aufgehängt, damit der überflüssige Asphalt
abtropfen konnte, und alsdann in das zweite Becken eingetaucht, in welchem das Rohr
verblieb, bis das Eisen die Temperatur desselben angenommen hatte, dann nochmals in
das zweite Bad eingetaucht und diesmal rasch herausgezogen. Durch dieses Verfahren
erhielt man einen die ganze Oberfläche des Eisens bedeckenden Ueberzug, der an der
dünnsten Stelle immer noch eine Dicke von 0mm,8
besaſs.
Der zur Aufnahme der Rohrleitung bestimmte Graben war 2m,13 tief, am Boden 1m,5 und oben 1m,6 breit.
An drei Stellen muſsten Bodenerhebungen durchbohrt werden, und da, wo die
Bodenbeschaffenheit eine Ausfütterung mit schmiedeeisernen Röhren überflüssig
machte, wurde ein (670m langer) Stollen aus
Cementmauerwerk hergestellt, dessen Anschluſsverbindung mit den eisernen Röhren
durch Betonmasse erfolgte.
Zwei andere Stollen von 365 bezieh. 91m Länge
wurden mit eisernen Röhren ausgelegt, welche hier jedoch nur in einzelnen Schüssen
zur Verwendung kommen konnten. Die Nietlöcher an den Rundnähten der groſsen Schüsse
wurden mit 9/16zölligem Gewinde versehen, während die engeren Schüsse auf ⅝ Zoll
Durchmesser glatt ausgestoſsen worden waren. Die engeren Schüsse wurden dann in die
weiteren eingeschoben und so lange gedreht, bis die entsprechenden Löcher einander
genau gegenüber standen; alsdann wurden Schraubenbolzen durch die Nietlöcher gesteckt. Durch das
Anziehen der Schrauben wurde eine vollständig dichte Verbindung hergestellt, indem
die Kante des inneren Schusses verstemmt wurde.
Die mit eisernen Röhren ausgefütterten Stollen wurden in einem Durchmesser von etwa 6
Fuſs im Lichten vorgestoſsen; sobald man einen Schuſs eingebracht hatte, wurde
derselbe mit zwei Schichten Ziegeln und einem Gemenge von Ziegeln und Beton
umhüllt.
Wo der Graben es erlaubte, wurden die Verbindungen der einzelnen Röhren dadurch
hergestellt, daſs das engere Ende einfach in das weitere eingeschoben und beide mit
einander ohne Anwendung von Blechstreifen vernietet wurden. Letztere wurden nur dort
benutzt, wo sie in Folge einer Krümmung der Rohrleitung erforderlich wurden. Bei der
Anwendung von Nahtstreifen wurde der Asphaltüberzug bis auf 3 Zoll Abstand von den
Kanten abgekratzt und eine dichte Vernietung von Eisen auf Eisen durch Vernietung
auf warmem Wege und Verstemmung der Innenkanten hergestellt. Bei besonders starken
Krümmungen schaltete man einen oder mehrere einzelne Schüsse ein. In Folge der
Beschaffenheit der Leitung wurde es nöthig, mehrere hundert Fuſs auf diese Weise zu
verlegen.
Bei der Annäherung an die Stadtgrenze muſste, da die Leitung durch aufgeschütteten
Boden ging, die Verbindung mit Hilfe von Blei vorgenommen werden. Man half sich
dabei durch Anwendung einer 160mm breiten Muffe,
welche über die Enden der zu verbindenden Röhren je 80mm überschoben wurde. Die Röhren waren so eingerichtet, daſs beide Enden
aus weiteren Schüssen bestanden. Zwischen der inneren Wand der Muffe und dem
äuſseren Rohrdurchmesser bestand noch ein lichter Zwischenraum von 10mm, der mit Blei ausgegossen wurde, welches
alsdann verstemmt wurde.Von der Firma Edwin Lewis and Sons in
Wolverhampton wird eine derselben patentirte Flanschenverbindung benutzt,
deren Construction aus nebenstehender Abbildung verständlich
ist.
Verbindungen dieser Art sind erfolgreich in Californien, wo die Rohrleitungen sich
häufig durch gebirgige Gegenden hinziehen, verwendet. Bei einer Bewässerungsanlage
auf den Sandwichs-Inseln wurden 7000 Fuſs 42zöllige Röhren verlegt, um 36
Thaleinschnitte zu überschreiten, und hat die Anlage in 7jährigem Betriebe zu keiner
Klage Veranlassung gegeben.
Fig. 2., Bd. 269, S. 358Fig. 2. Der Druck, welchen die Rohrleitung von San Francisco auszuhalten hat, ist
5at,3. Der Boden hat sich mittlerweile
meistens gesetzt, ohne
daſs indessen irgendwo eine Undichtigkeit entstanden wäre. Die Mannlöcher, Luft- und
Ablaſsventile machten keine besonderen Schwierigkeiten. Mannlöcher wurden
durchschnittlich in je 1000 Fuſs Entfernung angebracht; an einigen Stellen auch alle
500 Fuſs. Bei den Verstärkungsringen der Mannlöcher und Ventile bediente man sich
ausschlieſslich warmer Nieten.
Während der Verlegung der Leitung wurde mit heiſsem Asphalte jede Stelle, welche
durch die Verlegung gelitten hatte, neu überzogen. Bei ordentlichem Arbeitsgange
legte man bis zu 950 Fuſs in der 10stündigen Arbeitsschicht, während man bei
ungünstiger Beschaffenheit des Bodens häufig nicht mehr als 200 bis 300 Fuſs im Tage
vorankam. Nachdem das Wasser eingelassen worden war, brauchte keine einzige Strecke
der 45km langen Leitung behufs Vornahme von
Ausbesserungen geleert zu werden.
Seit Vollendung der oben beschriebenen Rohrleitung haben die Risdon Iron Works eine weitere Rohrleitung von 8km Länge aus 37zölligen schmiedeeisernen Röhren
mit 3/16 Zoll
Wandstärke für die Stadt Oakland gelegt. Hier ging die Leitung durch eine Ebene,
wodurch es möglich wurde, dieselbe innerhalb 6 Wochen zu vollenden.
Ueber die Dauer von Wasserleitungsröhren aus Schmiedeeisen fehlen noch Erfahrungen;
der Umstand, daſs die Wasserwerke in San Francisco bereits vor 20 Jahren zwei
Stränge von 30zölligen Röhren in Betrieb gesetzt haben, läſst indessen darauf
schlieſsen, daſs sie mit denselben hinreichend gute Erfahrungen gemacht haben, wenn
sie sich neuerdings bei einer so ausgedehnten Neuanlage wiederum zur Verwendung von
Schmiedeeisen entschlieſsen.
B) Röhren mit Schweiſsnaht.1887 264 200.
Nach den vorzüglichen Ergebnissen, welche mit dem Fluſseisen bezüglich des
Schweiſsens und der Walzbarkeit erzielt wurden, war es zu erwarten, daſs sich dies
Material mit Vortheil zur Fabrikation von Röhren verwenden lieſse.
Einer Mittheilung des Iron Age vom 9. Februar zu Folge
hatten die Riverside Iron Works in Wheeling sich
entschlossen, eine Röhrenfabrik anzulegen, um ein bestehendes Puddel- und
Eisenwalzwerk auszunutzen, welches früher den Rohstoff für Nagelfabrikation
geliefert hatte, aber in Folge des Umstandes, daſs in letzterer das Schweiſseisen
durch das Fluſseisen vollständig verdrängt wurde, zum Stillstande gekommen war.
Trotzdem also die neu erbaute Röhrenfabrik gerade auf ein vorhandenes Puddelwerk sich
stützte, ging man doch dazu über, Versuche mit Fluſseisen anzustellen, und zwar nahm
man weiches Bessemer-Material. Die fluſseisernen
Streifen, welche sich von den schweifseisernen durch glattes Aussehen auszeichneten,
widerstanden besser der Hitze, als letztere, und war ihre Schweiſsbarkeit
vorzüglich. In Folge dessen fuhr man daselbst fort, jenes Fluſseisen zu verarbeiten,
und zwar nicht nur zu patentgeschweiſsten, sondern auch zu stumpfgeschweiſsten
Röhren. Der Abfall soll wegen der ausgezeichneten Schweiſsbarkeit ein beträchtlich
geringerer sein, so daſs auch in dieser Beziehung die Verwendung von Fluſseisen mit
Nutzen verknüpft ist.
Wie die Revue universelle vom 19. Mai 1888 mittheilt,
sind auch in Bezug auf die Widerstandsfähigkeit gegen Säuren vergleichende Versuche
zwischen Eisen- und Stahlröhren angestellt. Dieselben ergaben, daſs Abschnitte,
welche 24 Stunden einer Lösung von verdünnter Salpetersäure ausgesetzt waren, einen
Gewichtsverlust erlitten: bei Eisen von 234mg, bei
Stahl von 75mg; nach Verlauf von 48 Stunden betrug
der Verlust entsprechend 417mg und 143mg.
Ebenso sind Versuche über die Festigkeit der Schweiſsnaht angestellt worden;
dieselben ergeben für Stahl 37 bis 47k/qmm Bruchfestigkeit bei 18,75 bis 17,25 Proc.
Dehnung, dagegen bei Eisen 25 bis 30k/qmm Bruchfestigkeit bei 2,25 bis 0,5 Proc.
Dehnung.
Einen eigenartigen Weg zur Herstellung von Röhren hat die Spiral Weld Tube Company in East Orange, N. J., eingeschlagen. Sie benutzt
zu ihrer Fabrikation schweiſs- und fluſseiserne Blechstreifen, welche spiralförmig
gewunden, und an der überragenden Kante erhitzt und durch Hämmern geschweiſst
werden.Derartige Spiralröhren, jedoch genietet, sind seit längerer Zeit im
Gebrauche. Das Verfahren soll sich besonders zur Herstellung
dünnwandiger Röhren eignen und sollen die bisher verwendeten Blechstreifen eine
Stärke von 0mm,31 (Nr. 29) bis zu 2mm (Nr. 14 der Birminghamer Blechlehre) gehabt
haben. Als Durchmesser der Röhren ist das Maſs von 100m bis zu 760mm in Aussicht genommen.
Zwischen der Breite des Blechstreifens und dem Durchmesser des Rohres soll keine
bestimmte Beziehung bestehen, und wird für ein 150mm weites Rohr die Breite der Streifen passend zu 150, 210, 270mm angegeben. In der Quelle (Iron Age vom 1. März 1888) wird angegeben, daſs zur
Herstellung einer 30 Fuſs langen 6zölligen Röhre ein 12 Zoll breiter und etwa 49
Fuſs langer Streifen erforderlich sei. (Diesen Angaben entspricht ein
Aufwickelungswinkel der Spirale von annähernd 52°.) Bei der Schwierigkeit, die
betreffenden Streifen länger als 12 Fuſs zu walzen, wird die angegebene Länge mit
Hilfe besonders eingerichteter Schweiſsmaschinen erzielt.
Die zu der Herstellung erforderliche Maschine wird durch nebenstehende Figur
erläutert. Das eine Ende des Streifens wird auf einen Führungstisch aufgelegt,
welcher in den richtigen Winkel je nach dem Verhältnisse der Breite des Streifens zu
dem Durchmesser des Rohres eingestellt wird. Zwei Speisewalzen führen den Streifen
in die Maschine ein,
woselbst er zunächst die passende Biegung erhält. Die Speisewalzen laufen nicht
ununterbrochen, sondern in Pausen, so daſs sie den Streifen bei jedem Vorwärtsschube
um 3 bis 15mm vorrücken.
Textabbildung Bd. 269, S. 361
Die Erwärmung der beiden an einander zu schweiſsenden Kanten
erfolgt in einem Ofen durch ein oder zwei Löthrohre, welche unmittelbar auf das
Metall mittels Oeffnungen von passender Form, in dem feuerfesten Futter des Ofens
ausgespart, einwirken. Das hierbei benutzte Brennmaterial ist Wassergas. Wenngleich eine
Düse genügt, so sollen zwei derselben doch erheblich besser wirken und eine raschere
Arbeit gestatten. Der Gasverbrauch soll nur gering sein und in einem Falle 1cbm für einen Fuſs Schweiſslänge betragen
haben.Leider enthält unsere Quelle über diesen, bei dem ganzen Verfahren jedenfalls
wichtigsten Punkt, keine näheren und verständlichen Angaben.
Sobald die Schweiſshitze erreicht ist, rückt der Streifen unter einen leichten
Hammer, welcher ungefähr 160 Schläge in der Minute macht; jedesmal, wenn der Hammer
sich hebt, rückt der Streifen um die erwähnten 3 bis 15mm vorwärts, bleibt dagegen still stehen, sobald der Hammer ruht. Nur ein
passend geformter Amboſs, aber kein Dorn wird gebraucht.
Die Maschine soll fast selbsthätig wirken und kaum Bedienung durch einen geübten
Arbeiter verlangen. Das Zurichten der Röhren erfolgt in üblicher Weise, indem sie
abgeschnitten und je nach Bedarf asphaltirt, gestrichen u.s.w. werden. Die Maschine
beansprucht einen Raum zur Aufstellung von 2m ins
Geviert.
Ueber die Maschine ist ein besonderer Vortrag in der Versammlung des American Institute of Mining Engineers in Boston am 21.
Februar 1888 gehalten worden; in der demselben folgenden Besprechung machte Henry M. Howe die Mittheilung, daſs in Providence eine
andere Methode zur Erzeugung spiralförmiger Röhren im Gebrauche sei, die sich
dadurch unterscheide, daſs die Verbindungsstellen nicht geschweiſst, sondern
gelöthet werden.
Da die Festigkeit der Wandungen in der Richtung der Walzfasern beansprucht wird, so
sind diese Röhren viel widerstandsfähiger als gezogene Röhren. Nach den Angaben von
The Engineering and Mining Journal vom 14. April
1888 konnte ein sechszölliges Rohr von Nr. 14 Blechstärke bis zu 1383 Pfund auf den
Quadratzoll belastet werden. Die Gewichte für ein sechszölliges Rohr bei
spiralförmig gebildeten, bei geschweiſsten und bei Guſseisenrohren für den laufenden
Fuſs betragen entsprechend 5,2, 18,77 und 28,28 Pfund und entsprechend bei
12zölligen Rohren 10,46, 54,65 und 77,36 Pfund im Mittel. Dabei ist die Weite der
Röhren eine unbegrenzte, während die gezogenen Röhren nur in engen Grenzen und nicht
wohl über 20 Zoll weit hergestellt werden können. Ebenso ist die Länge unabhängig
von der Darstellungsweise und nur durch Gebrauchsrücksichten bestimmt. Bei der
bisher gebräuchlichen Verbindung durch Guſseisenflanschen soll sich eine
Schwierigkeit nicht entgegengestellt haben. Natürlich sind die Röhren vor
Durchrosten gebührend zu bewahren.
Das Benardos'sche Verfahren, über welches wir 1887 264 * 335 und 265 361
berichteten, scheint sich zur Herstellung von Röhren mit elektrisch geschweiſsten
Nähten auch verwenden zu lassen. So soll es gelungen sein, ein Rohr von 50mm lichter Weite und 3mm Wandstärke nicht nur in der Längsnaht zu schweiſsen, sondern auch die Endflanschen mit 170mm Durchmesser und 10mm Wandstärke nach demselben Verfahren anzufügen, und zwar ohne bemerkbare
Schweiſsnaht. Ein Kupferrohr von 60mm Durchmesser
und 3mm Stärke soll nach dem Benardos'schen Verfahren stumpf an ein gleiches
Rohrstück so vollkommen angeschweiſst sein, daſs eine Schweiſsfuge nicht aufzufinden
gewesen ist. Die Versuche über die Verwendung dieses Verfahrens sind zur Zeit noch
nicht abgeschlossen.
Tafeln
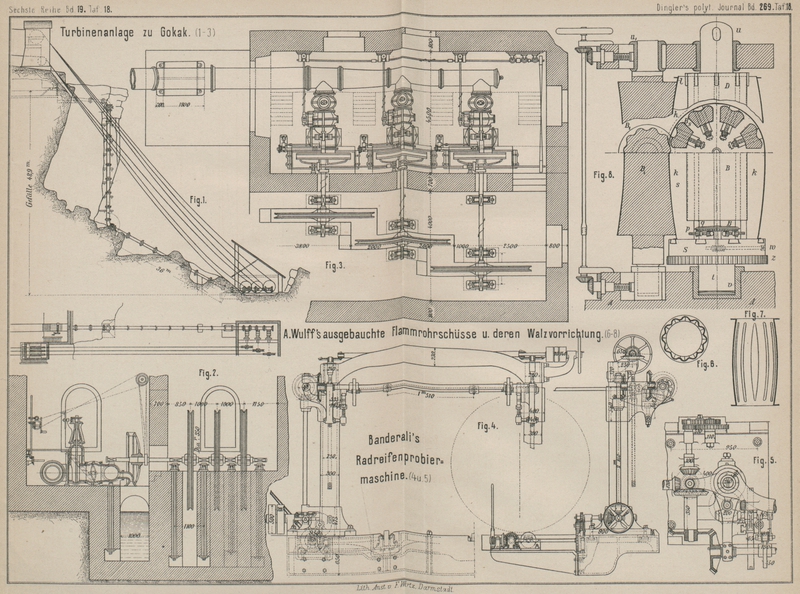