Titel: | Neuerungen im Eisenhüttenwesen. |
Autor: | W. Koort |
Fundstelle: | Band 272, Jahrgang 1889, S. 1 |
Download: | XML |
Neuerungen im Eisenhüttenwesen.
Mit Abbildungen auf Tafel
1.
Neuerungen im Eisenhüttenwesen.
I. Hochofenprozeſs.
Hochofengase. Bei der Berechnung der Zusammensetzung der
Hochofengase und der in den Hochofen eingeführten Windmenge kommen in Kokshochöfen,
abgesehen von dem Wasserdampfe, dessen Menge sich leicht aus der Beschickung
berechnen läſst, drei Bestandtheile in Betracht, nämlich Kohlensäure, Kohlenoxyd und
Stickstoff. Die Kohlensäure stammt zum Theil aus den Erzen und Zuschlägen, zum Theil
ist sie Verbrennungsproduct des Kohlenstoffes. Die in den Gichtgasen befindliche
Sauerstoffmenge wird durch den Gebläsewind, durch die Oxyde, welche reducirt werden,
und durch die Kohlensäure des Möllers eingeführt. Der Stickstoff stammt lediglich
aus der Gebläseluft und verläſst unverändert den Ofen.
Bezeichnet x die Kohlenstoffmenge, welche zu
Kohlensäure, y diejenige Kohlenstoffmenge, welche zu
Kohlenoxyd verbrennt, und z die Stickstoffmenge,
sämmtlich in Kilogramm für 100k Roheisen, so
lassen sich nach B. Osann (Stahl und
Eisen, 1888 S. 592 ff.) zur Ermittelung der drei
Unbekannten die folgenden drei Gleichungen aufstellen:
1)x+y=a,
2)z\,:\,\left\{\left(x\,.\,\frac{8}{3}+y\,.\,\frac{4}{3}\right)-b\right\}=77\,:\,23,,
3)
z\,.\,0,8=\frac{n}{100}\left{z\,.\,0,8+\left(x\,.\,\frac{11}{3}+c\right)\,.\,0,51+y\,.\,\frac{7}{3}\,.\,0,8\right}
wenn a = Kohlenstoffmenge, welche
zur Verbrennung verfügbar ist;
b = Sauerstoffmenge,
welche aus den Oxyden durch Reduction entfernt;
c = Kohlensäuremenge,
durch den Möller eingeführt;
d = Wasserdampf;
(sämmtliche Werthe in Kilogramm für 100k
Roheisen).
n = Factor, welcher, von
a abhängig, entsprechend einzusetzen ist.
In der Gleichung Nr. 2 wird ausgedrückt, daſs die Stickstoffmenge zu der aus der
Gebläseluft stammenden Sauerstoffmenge im Verhältnisse von 77 : 23 steht. Diese
Sauerstoffmenge ergibt sich, wenn man von der von x und
y gebundenen Sauerstoffmenge die Gröſse b abzieht. Die Gleichung Nr. 3 besagt, daſs die
Stickstoffmenge in Volumprocenten der trockenen Gichtgase n
Proc. ausmacht. Der Werth von n kann, wie nachstehend
gezeigt werden soll, mit hinreichender Genauigkeit für die einzelnen Werthe von a festgestellt werden.
Die Gichtgasanalysen von Hochöfen, die unter den verschiedenen Betriebsverhältnissen
arbeiten, zeigen in dem Stickstoffgehalte eine geringe Abweichung, wenn man die
Gichtgasanalyse in Volumprocenten für die trockenen Gase niederschreibt. Dies rührt
daher, daſs 1k Kohlenstoff, zu Kohlensäure
verbrennend, nach der Verbrennung dasselbe Volumen einnimmt (1cbm,87) wie 1k
Kohlenstoff, welches zu Kohlenoxyd verbrennt. Demnach geben 100k Kohlenstoff 187cbm Gas, wobei es gleichgültig ist, wie viel Kohlenstoff zu Kohlensäure
und wie viel zu Kohlenoxyd verbrennt. Für die mit der Luftmenge zugeführte
Stickstoffmenge ist dies nicht gleichgültig. Jedoch schwankt der Stickstoffgehalt in
Volumenprocenten der trockenen Gase nur in den Grenzen von etwa 58 bis 62 Proc. Mit
Rücksicht auf die bekannte Rechnungsmethode von Gruner
läſst sich eine Stufenleiter construiren, in welcher der Stickstoffgehalt den
einzelnen Werthen von a gegenübergestellt wurde. An die
Spitze dieser Stufenleiter wurden die Resultate einer Gruner'schen Rechnung gestellt, die in Gemeinschaft mit Gasanalysen in
Groſs-Ilsede ausgeführt war. Den Fuſspunkt der Stufenleiter nahmen die Resultate der
Berechnung für einen schlesischen Hochofen ein. Für die Zwischenwerthe von a wurde der Stickstoff geh alt in Volumenprocenten
berechnet, indem man die aufzubringende Wärmemenge und das Verhältniſs der direkten
Reduction zur indirekten gleichmäſsig fallend von dem ungünstigen zu dem günstigen
Beispiele annahm.
Es ergab sich für
a =
60
bis
70k
n = 58
a =
70
„
80k
n = 59
a =
80
„
110k
n = 60
a =
110
„
150k
n = 61
a=
über
150k
n = 62.
Durch Einsetzung dieser Werthe gelangt man zu folgenden Werthen für die drei
Unbekannten:
für
z
x
y
a = 60 bis 70ka = 70 „ 80ka
= 80 „ 110ka = 110 „ 150ka = über 150k
z = 0,87c +
3,19az = 0,91c + 3,34az =
0,95c + 3,50az = 1,00c + 3,68az = 1,04c + 3,81a
x=\frac{0,87\,c+3,35\,b-1,28\,a}{4,47}
x=\frac{0,91\,c+3,35\,b-1,13\,a}{4,47}
x=\frac{0,95\,c+3,35\,b-0,97\,a}{4,47}
x=\frac{1,00\,c+3,35\,b-0,79\,a}{4,47}
x=\frac{1,04\,c+3,35\,b-0,66\,a}{4,47}
y = a – x
xk C
verbrennen
zu
x\,.\,\frac{11}{3}\,k CO2
(Kohlensäure)
yk C
„
„
y\,.\,\frac{7}{3}\,k CO (Kohlenoxyd).
Demnach setzen sich die Gichtgase für 100k Roheisen
wie folgt zusammen:
\left(x\,.\,\frac{11}{3}+c\right)^k\,\mbox{CO}_2+y\,.\,\frac{7}{3}^k\,\mbox{CO}+z^k\,\mbox{N}+d^k\,\mbox{H}_2\mbox{O},
woraus die Zusammensetzung in Gewichts- und auch
Volumenprocenten leicht zu ermitteln ist. Für Umrechnung in Volumina setze man 1k CO2 = 0cbm,51, 1k CO =
0cbm,8; 1k N
= 0cbm,8, 1k
H2O = 1cbm,24.
Die Gichtgasmenge in Cubikmeter für 100k Roheisen
ergibt sich auch, da
x\,.\,\frac{11}{3}\,.\,0,51+y\,.\,\frac{7}{3}\,.\,0,8=1,87\,(x+y)=1,87\,a
ist, nach Einsetzen des Werthes für z, wie folgt:
für
a =
60
bis
70k
(1,21c + 4,42a +
1,24d)cbm
„
a =
70
„
80k
(1,24c + 4,54a +
1,24d)cbm
„
a =
80
„
110k
(1,27c + 4,67a +
1,24d)cbm
„
a =
110
„
150k
(1,31c + 4,81a +
1,24d)cbm
„
a =
über
150k
(1,34c + 4,92a +
1,24d)cbm
bei 0° C. und 760mm
Quecksilbersäule.
Die in der Minute erzeugte Gichtgasmenge =\frac{m}{100} obiger
Werthe, wenn m die in der Minute erzeugte Roheisenmenge
in Kilogramm bedeutet.
Aus dem Verhältnisse der Stickstoff menge zur Luftmenge = 77 : 100 folgte die
Windmenge für 100k Roheisen
=z\,.\,\frac{100}{77}\,k\ \mbox{oder}\
z\,:\,\frac{100}{77}\,.\,0^{cbm},77=z^{cbm}
Die in der Minute in den Ofen eingeführte Windmenge
=\frac{m}{100}\,.\,z^{cbm} bei 0° C. und 760mm Druck.
Der Nutzeffect des Gebläses.
=\frac{z\,.\,\frac{m}{100}}{Q\,.\,\frac{273}{273+t}\,.\,\frac{p}{76}}
wobei Q den aus
Kolbenquerschnitt, Hub und Umdrehungszahl ermittelten, in der Minute vom Windkolben
durchlaufenen Raum in Cubikmetern, t die Lufttemperatur
in Graden Celsius und p den Barometerstand in
Centimeter Quecksilbersäule darstellt.
Die Anwendung obiger Formeln und die Ermittelung der Werthe für a, b, c und d möge in
folgendem Beispiele erläutert werden:
Auf einem oberschlesischen Hochofen werke wurden (nach Mittheilung in Wedding's zweitem Ergänzungsbande zu Percy's „Eisenhüttenkunde“) für 100k
Roheisen aufgegeben:
127k,0
Koks
86k,4
Brauneisenerz
86k,4
Schweiſsschlacke
40k,7
Spatheisenstein
75k,3
Kalkstein.
Die Roheisenanalyse ergab 2 Proc. Mn, 2,3 Proc. Si, 3,1 Proc. C und 0,29 Proc. P.
Behufs Ermittelung der Werthe für b, c, d wird folgende
Tabelle aufgestellt:
Für 100k Roheisen.
Gewichts-mengen
b
c
d
Eisen
in Formvon
dem-nachSauer-stoff
Sauer-stoff
Kohlen-säure
Kohlen-säure
Wasser
Wasser
k
Proc.
Proc.
k
Proc.
k
Proc.
k
KoksBrauneisenerzSchweiſsschlackeSpatheisensteinKalkstein
127,0 86,4 86,4 40,7 75,3
1,4627,76 7,4543,1853,02 2,10 0,28
OxydOxydOxydOxydulOxydOxydulOxyd
0,6311,90 3,1912,3422,72 0,60 0,12
0,8010,28 2,7610,63 9,25 0,24 0,09
– 1,01–– 1,3543,85
– 0,87–– 0,5533,02
4,225,92 0,03 0,60 0,09
5,3322,39 0,03 0,24 0,07
ManganSiliciumPhosphor
2k,0 gebunden in Mn3O42k,3 „ „ SiO20k,29 „ „ P2O5
0,78 2,63 0,38
Sa.
37,84
Sa.
34,44
Sa.
28,06
Demnach
b =
37k,84
c =
35k,44
d =
28k,06
Berechnung von a.
Koksmenge
= 127k,0
Verlust durch Transport und Herausschleudern
aus Gicht und Stichloch
= 5k,1
= (4 Proc.)
–––––––––––––
Bleiben
121h,9
= 104k,83 C
(86 Proc.)
Ins Roheisen gehen
= 3h,10 C
––––––––––––––––––––––––––––––––––––––––
Sind zur Verbrennung vorhanden
101k,73 C
(Kohlenst.)
Also a = 101k,73.
Nach Einsetzen der Werthe in die entsprechenden Formeln erhält man
x =
13k,6 C
entsprechend
13,6\,.\,\frac{11}{3}=49^k,9 CO2
y =
88k,1 C
„
88,1\,.\,\frac{7}{3}=205^k,6 CO
z =
388k,7 N
(Stickstoff).
Zusammensetzung und Menge der Gichtgase für 100k
Roheisen.
CO2
= (49,9 + c)
= 84k,3
= 42cbm,99
= 7,8
Proc.
= 8,3
Proc.
CO
=
205k,6
= 164cbm,48
= 29,7
„
= 31,7
„
N
=
388k,7
= 310cbm,96
= 56,2
„
= 60,0
„
H2O
=
28k,1
= 34cbm,84
= 6,3
„
––––––––––––––––––––––––––––––––––––––––––––––––––––––––––––––
Sa
706k,7
= 553cbm,27
= 100
Proc.
= 100
Proc.
bei 0° C und760mmQuecksilber
(Volumen-procente)
Die Gichtgasmenge in Cubikmetern hätte man auch einfacher aus der Formel (1,27c + 4,67a + 1,24d) entwickeln können.
Gichtgasmenge in Cubikmetern in der Minute:
=\frac{m}{100}\,.\,553,3=0,41\,.\,553,3=226^{cbm},8
m = in der Minute producirte
Roheisenmenge = 41k.
Windmenge für 100k Roheisen:
=z\,.\,\frac{100}{77}\,.\,k=505^k=z\,.\,cbm=388^{cbm},7
bei 0° C. und 760mm
Quecksilber.
Windmenge, welche in der Minute in den Ofen eingeführt wird:
=z\,.\,\frac{m}{100}=388,7\,.\,0,41=159^{cbm},4\,.\,
Nutzeffect des Gebläses.
Durchläuft der Gebläsekolben in der Minute einen Raum von 256cbm bei + 10° C. und 75cm Quecksilbersäule, so ist der Nutzeffect des
Gebläses
=\frac{159,4}{256\,.\,\frac{273}{283}\,.\,\frac{75}{76}}=\frac{159,4}{243,7}=0,65=65\
\mbox{Proc.}
Reducirbarkeit der Erze. Dr. Kosmann veröffentlicht über diesen Gegenstand in Stahl und Eisen, 1888 S. 586, einen Aufsatz, nachdem bereits in derselben
Zeitschrift (S. 15) über die Resultate der in dieser Richtung angestellten
experimentellen Untersuchungen des Prof. Wiborgh
berichtet worden war, auf welche Aufsätze hiermit kurzweg verwiesen wird.
Für den praktischen Hüttenmann dürfte aus den betreffenden Mittheilungen hervorgehen,
daſs er auch auf den Grad der Abröstung eines Erzes, welches für das Verhalten
desselben im Hochofen charakteristisch ist, seine Beobachtung lenken muſs.
Hochofeneinrichtungen.
Kühlung. Gordon, Strobel und Laureau (Limited) in
Philadelphia haben auf ein Hochofenfundament das Patent der „Vereinigten
Staaten“ Nr. 379694 erhalten (vgl. Stahl und
Eisen, 1888 S. 107). Die Sohle a des
Ofengestelles (Fig.
1) liegt in Höhe der Hüttensohle. Um das Gestell herum ist ein durch
Eisenplatten überdeckter Hohlraum b angeordnet, dessen Tiefe gleich der
Dicke des Bodensteines ist. Der Hohlraum b ist mit
Wasser gefüllt, welches von der Berieselung des Gestellmantels kommt. Dasselbe kann
nicht nur in und unter den Bodenstein, sondern auch unter die Fundamente der den
Ofenmantel tragenden Säulen gelangen. Der Hohlraum hat ein Ueberlaufrohr c und ein Ablaſsrohr d mit
Ventil. Die Erfinder legen auf die Höhenlage des Bodensteines, die äuſsere
cylindrische Begrenzung desselben und die Gestalt des Hohlraumes b Gewicht.
A. Wheeler in Sharon baut nach dem Patente der
„Vereinigten Staaten“ Nr. 378749 das Hochofengestell in einen mit Boden
versehenen Cylinder aus Kesselblech ein. Der Boden des Cylinders ruht auf einer Lage
von Eisenziegeln, die in einer Tiefe des Hochofenfundamentes derart angeordnet sind,
daſs sie fortwährend unter Wasser gehalten werden können. Durch zahlreiche Rinnen
auf der oberen Seite der Eisenziegel kann das Wasser direkt bis zum Boden des
Gestell-Blechcylinders gelangen und denselben kühlen (nach Stahl und Eisen, 1888 S. 706).
Julian Kennedy in Pittsburg gibt nach Stahl und Eisen, 1888 S. 626, in dem Patente der
„Vereinigten Staaten“ Nr. 378550 Kühlkästen für Hochöfen an. Diese
Kühlkästen bilden, dicht neben einander liegend, einen geschlossenen Ring. Jeder
Kühlkasten ist als Ganzes aus Phosphorbronze gegossen und besteht aus zwei parallel
laufenden, von einander vollständig getrennten Wasserkanälen, die gegen einander
durch Querrippen versteift sind. Im Falle des Durchbrennens des inneren Kanales kann
also der äuſsere Kanal weiter benutzt werden. Der Vortheil dieser Anordnung soll
darin bestehen, daſs Herd und Gestellwände an keiner Stelle ganz durch Kühlkästen
unterbrochen werden. Das Mauerwerk umgibt dieselben vielmehr nach innen und auſsen
und setzt sich auch bis in den Zwischenraum fort, so daſs dadurch die Lage der
Kühlkästen gesichert ist. Eine ähnliche Einrichtung zum Kühlen findet sich in dem
britischen Patente Nr. 11556 vom Jahre 1887.
Begichtungsvorrichtungen. S. Thomas hat eine maschinelle
Gichtvorachtung für Hochöfen construirt (Patent der „Vereinigten Staaten“ Nr.
377873).
Zur Gicht des Hochofens (Fig. 2) führt eine
geneigte Schienenbahn C, welche auf der Hüttensohle in
die wagerechte Schienenbahn des Möllerhauses übergeht. Die in letzterem gefüllten
Wagen I können also bis an die Schienenbahn C vorgeschoben werden. Zum Transporte der Wagen I auf die Gicht dienen die auf einem zwischen der
Schienenbahn C angeordneten Geleise laufenden Wagen O, welche von der Hüttensohle aus durch ein über Rollen
Q geleitetes Seil P
bewegt werden, und von welchen der vordere Wagen O mit
einem den Wagen I vor sich herschiebenden Stöſser O1 versehen ist. Die
Wagen I haben Bodenklappen N, welche durch einen Gewichtshebel J
geschlossen gehalten werden. Kommt der Wagen I auf der Gicht an, so
schiebt er einen Kolben in den Luftcylinder R ein.
Gleichzeitig wird der Hebel J dadurch, daſs das rechte
Ende desselben die Führung G hinansteigt, gedreht, und
die Klappthüren N werden geöffnet. Der Inhalt des
Wagens I fällt demnach durch den Trichter B auf die Glocke F und
nach Senkung derselben mittels des Cylinders A in den
Hochofen. Wird dann das Seil P nachgelassen, so rollen
die Wagen O nach unten, während der Wagen I von dem durch die vorher comprimirte Luft bewegten
Kolben des Cylinders R zurückgeschoben wird und dann
den Wagen O folgt (Stahl und
Eisen, 1888 S. 626).
Damit der Gasdruck in der Düsenzone und allen übrigen Zonen des Inneren eines
Hochofens der gleiche sei und dadurch eine gleichmäſsige Wirkung der Gase auf die
Materialien stattfinden kann, erhält nach dem britischen Patente Nr. 9253 vom Jahre
1888 (Edw. Walsh in St. Louis, Nordamerika) der
Kohlensack im oberen weitesten Theile ungefähr den dreifachen Querschnitt des
cylindrischen Gestelles und den fünf- bis siebenfachen Querschnitt der Gicht. Im
Uebrigen liegen die Düsen in der höchsten Zone des Gestelles. Auf dieses setzt sich
der im unteren gröſseren Theile fast halbkugelig und im oberen kleineren Theile
cylindrisch gestaltete Kohlensack, an den der kegelförmige Schacht sich anschlieſst.
In die Gicht ragt ein groſser Sammeltrichter a (Fig. 3) hinein,
welcher oben durch eine Glocke b verschlossen wird. Das
Gewicht der letzteren wird durch Gegengewichte c
ausgeglichen. Zur Bewegung der Glocke b dient ein
Dampfcylinder d, mit dessen hohler Kolbenstange e die Glockenspindel f
mittels eines Splintes verbunden ist. Da in der Spindel f mehrere Splintlöcher angeordnet sind, so kann mittels des Cylinders d die Glocke b mit dem
Ringe i aus dem Trichter k
herausgehoben und dadurch die Gicht freigelegt werden. Die Materialien füllen den
Trichter ungefähr bis zur Hälfte an, wobei dieselben den Hebel n nach auſsen drücken. Sinkt der Stand der Materialien
bis unter den Hebel n, so legt sich der äuſsere
Schenkel desselben auf einen elektrischen Contact m und
zeigt durch ein Läutewerk an, daſs die Zeit zum Begichten des Ofens gekommen ist
(Stahl und Eisen, 1888 S. 705).
Winderhitzer. H. C. Bull and Comp., Limited, und Henry Clay Bull in London haben nach Stahl und Eisen, 1888 S. 624, einen
Regenerativ-Winderhitzerconstruirt, welcher durch die britische Patentschrift Nr.
10204 vom Jahre 1887 bekannt geworden ist.
Der cylindrische Winderhitzer (Fig. 4) hat radial
angeordnetes Füllmauerwerk. Behufs Heizung desselben werden heiſse Luft durch den
Kanal a in den Schacht b,
und Gas durch das Rohr c und den Kanal d in den Schacht b
eingeführt. Luft und Gas treffen sich bei e. Die
Verbrennungsgase steigen in die Höhe und fallen durch Füllmauerwerk herab, um durch
die Ringkanäle f und das Ventil g zu entweichen. Behufs Erhitzung der Luft wird nach Schlieſsung der betreffenden Ventile die kalte
Luft in die Kanäle f eingelassen, steigt im
Füllmauerwerke in die Höhe und fällt durch den Schacht b in den Kanal a, durch welchen die heiſse
Luft den Schmelz- oder Reductionsöfen zugeführt wird.
Die Frage, ob steinerne Winderhitzer auch für kleinere Hochöfen mit 25 bis 35t täglicher oder 11000t jährlicher Roheisenerzeugung anwendbar sind, hat Fritz W. Lürmann (vgl. Stahl und Eisen, 1888
S. 443) beantwortet. Er zerlegt die Frage in zwei Theile, nämlich:
1) Um wieviel werden die Erzeugungskosten für 1t
Roheisen bei den kleineren Hochöfen erhöht, wenn für dieselben steinerne Winderhitzer errichtet werden?
2) Wie gestaltet sich der Betrieb dieser kleineren Hochöfen, die Güte des darin
erzeugten Roheisens, der Koksverbrauch derselben bei Anwendung von heiſserem Winde,
und um wieviel werden die Erzeugungskosten für 1t
Roheisen vermindert?
Die erste Frage beantwortet Lürmann unter Zugrundelegung
genauer Rechnungen dahin, daſs bei Anlage von zwei Winderhitzern, die, wenn noch
brauchbare eiserne Winderhitzer vorhanden sind, genügen
sollen, und einer täglichen Roheisenerzeugung von 30t oder 11000t jährlich sich der Bau
dieser beiden kleinen Winderhitzer mit Leitungen und Schornstein auf 60 bis 63000 M.
beziffern würde. Die jährlichen Unkosten sollen sich danach auf 9500 M. belaufen,
was einer Erhöhung der Gestehungskosten des Roheisens von 0,865 M. für 1t gleichkommen würde.
Da jedoch in der Regel die eisernen Winderhitzer beseitigt und drei neue steinerne
Winderhitzer angelegt werden müssen, so würden die gesammten Anlagekosten sich auf
71000 M. belaufen.
Danach sollen die jährlichen Unkosten für Zinsen, Amortisation und Erneuerung 12000
M. betragen, was einer Erhöhung der Gestehungskosten um 1,1 M. gleichkommt.
Die zweite Frage läſst sich nicht so bestimmt beantworten, wenigstens soll sich nicht
angeben lassen, wieviel die Ersparniſs an Koks bei Anwendung des heiſseren Windes
auf 1000k Roheisen ausmacht. Lürmann vertritt die Ansicht, und wohl mit Recht, daſs
sie für jeden speciellen Fall besonders erwogen werden muſs. Nur so viel steht fest,
daſs die geringe Höhe der Unterhaltungskosten, die Vermeidung der Windverluste, die
Ersparung an Hochofengasen zum Heizen derselben und die Erzielung von
Windtemperaturen, wie sie in eisernen Winderhitzern nicht erzielt werden können,
Vortheile sind, die zur Anlage steinerner Winderhitzer bei kleinen Hochöfen
ermuthigen sollten.
Sollen die Unkosten derartiger Winderhitzer lediglich durch den Werth der Ersparniſs
an Koks gedeckt werden, so braucht diese Ersparniſs gegenüber dem gegenwärtigen
Koksverbrauch nur 0,865 bezieh. 1,1 M. zu betragen, was beispielsweise für das
Siegerland einer Ersparniſs von 70 bezieh. 90k
Koks für 1t Roheisen gleichkommt.
Der in D. p. J. 1887 266 59
beschriebene Lürmann'sche steinerne Winderhitzer,
welcher durch das D. R. P. Nr. 42051 vom 2. April 1887 gesetzlich geschützt ist, hat
durch das D. R. P. Nr. 42579 vom 6. August 1887 (Zusatz) einige Abänderungen
erfahren, welche die Einrichtung der Gaseinführung und die Windabführung
betreffen.
In den Seitenwandungen des Gaseintrittsschachtes, soweit derselbe aus der
Steinfüllung heraustritt, sind besondere Oeffnungen vorhanden. In das Innere des
Kuppelgewölbes münden Kanäle, welche mit dem den Winderhitzer umgebenden Sammelrohre
in Verbindung stehen. Durch die genannten Oeffnungen im Schachte wird eine
gleichmäſsigere Verbrennung der Gase in der Kuppel erzielt, so daſs das Gewölbe
derselben haltbarer wird.
Benjamin Ford in Middlesborough-on-Tees und John Moncur in Distingtow (England) haben einen
Regenerativ-Winderhitzer construirt. (vgl. Patent der „Vereinigten Staaten“
Nr. 364998).
Der Winderhitzer ist durch mehrere senkrechte Scheidewände in Unterabtheilungen
geschieden, von welchen jede einen besonderen Wind- Ein- und Auslaſs mit je einem
besonderen Ventile hat. Auf diese Weise wird es ermöglicht, die ganze Windmenge
durch eine einzige der Unterabtheilungen zu treiben und dadurch den in der
Steinfüllung abgelagerten Staub abzublasen. Ist dies geschehen, so öffnet man alle
Ventile und läſst den Wind durch alle Abtheilungen gehen. Die Reinigung der
einzelnen Kammern findet wechselweise statt (Stahl und
Eisen, 1888 S. 483).
Hermann Schulze-Berge in Rochester (Pennsylv.)
beschreibt in dem Patente der „Vereinigten Staaten“ Nr. 360973 einen
Röhren-Winderhitzer. Anstatt daſs die Flamme um und der
Wind durch die Röhren geleitet wird, geht hier die
Flamme durch die Röhren, während der Wind dieselben umspült.
In einem Kasten aus Eisenblech mit feuerfestem Futter sind eine obere und eine untere
wagerechte Scheidewand, in welchen die Flammenröhren befestigt sind, und eine
mittlere senkrechte Scheidewand angeordnet, welche den an der einen Seite
hineingeblasenen Wind hinauf und dann hinunter aus dem Apparate hinausleitet.
Entsprechend steigt die Flamme in der einen Hälfte der Röhren hinauf, geht dann
unter der Decke des Apparates entlang und fällt in der anderen Hälfte der Röhren
hinab, um den Apparat zu verlassen.
Hochofenproduction. Die Production der deutschen
Hochofen werke betrug im Monate Oktober 1888 362000t. Von diesen kommen 164963t auf das
Puddelroheisen und Spiegeleisen, 36086t auf
Bessemerroheisen, 111562t auf das Thomaseisen und
49401t auf Gieſsereiroheisen. Die
Gesammtproduction an Roheisen betrug vom 1. Januar bis zum 31. Oktober 1888
3530647t, wohingegen sie in dem gleichen
Zeitabschnitte des Vorjahres nur 3204416t betrug.
Am meisten ist in jüngster Zeit die Production des Thomasroheisens gestiegen. Es steht zu erwarten, daſs
die Production noch mehr sich steigern wird, wenn z.B. durch Kanalisirung der Mosel
die Luxemburger und Lothringer Erze, welche sich für die Erzeugung von
Thomasroheisen eignen, den Hochöfen am Niederrhein und in Westfalen näher gebracht
werden. Nach der Berechnung von Brauns sollen die
genannten Erze für 1000 Jahre ausreichen, wenn die Production an Thomasroheisen sich
in den gegenwärtigen Grenzen hält.
Schlacken. Bekanntlich geht die in der flüssigen
Hochofen- und anderen Schlacke aufgespeicherte Wärme bis jetzt verloren. Es verdient
daher eine eigenthümliche Dampfkesseleinrichtung, durch welche die Schlacke zur
Erzeugung von Dampf ausgenutzt werden soll, Beachtung.
Im Wesentlichen besteht der Dampfkessel (Patent der „Vereinigten Staaten“ Nr.
379625, Adams in Chicago, mitgetheilt in Stahl und Eisen, 1888 S. 707) aus über und neben
einander angeordneten kantigen Behältern a (Fig. 5), in
welchen schwach kegelförmige oder kugelige Schächte b
zur Aufnahme der Schlacke angeordnet sind. Die flüssige Schlacke gelangt zuerst in
mehrere mit feuerfestem Material ausgefütterte neben einander liegende obere
Schächte b, und wenn ein Ueberschuſs an Schlacke
vorhanden ist, durch Röhren c und Rinnen d in die Schächte b1. Die Schächte sind unten durch einfache
Schieberböden e, welche durch Zahnstangen bewegt
werden, abgeschlossen. Excenterhebel gestatten ein festes Anpressen der Böden gegen
die Schachtmündung. In der Mitte des Bodens kann ein Loch f angeordnet sein, welches durch Thon geschlossen wird, aber auch
durchgestoſsen werden kann, um die Schlacke in den darunter liegenden Schacht
flieſsen zu lassen. In dem kugeligen Schlackenbehälter kann die Schlacke erstarren
und dann durch die Oeffnung g zerschlagen werden, um
nach Fortschiebung der Bodenthür e auf eine wagerechte
Transportkette zu fallen und von dieser fortgeschafft zu werden. Zum gleichen Zwecke
fahren Wagen auf den Schienen i.
Orrin Peck will ebenfalls durch Schlackenwärme Dampf
erzeugen (vgl. britisches Patent Nr. 9652 vom Jahre 1888).
Feinprozeſs. W. Inkes, W. H. Glover und F. Bosshardt in Manchester verwenden eine passende
Anzahl von Cupolöfen a (Fig. 6) in enger
Verbindung mit einem einen durchlöcherten Steg b
enthaltenden Sammler c derart, daſs die in den
Cupolöfen geschmolzene Eisenmasse unmittelbar beim Austritte aus denselben und beim
Eintritte in den Sammler c der Wirkung eines durch den
durchlöcherten Weg passirenden Luftstrahles ausgesetzt wird.
Zu diesem Zwecke wird der Sammler c so nahe wie möglich
an die Cupolöfen a angebaut und nach oben durch die
Röhren d und nach unten durch die Kanäle e mit den Cupolöfen a in
Verbindung gebracht. Unmittelbar unterhalb der Kanäle e ist im Sammler c ein Steg b derart
angebracht, daſs die in den Cupolöfen geschmolzene Eisenmasse durch die Kanäle e direkt auf den Steg b
geführt wird.
Letzterer ist so angeordnet, daſs zwischen demselben und den Seiten des Sammlers c sich ein freier Raum bildet, sowie mit senkrechten
Löchern f versehen, welche unten von einer Luftkammer
g umschlossen und durch eine Röhre mit Luft
gespeist werden.
Wenn die in den Cupolöfen a geschmolzene Eisenmasse auf
dem Stege b anlangt, so kommt dieselbe in Contact mit
dem durch die Löcher f eintretenden Luftstrahle,
welcher die geschmolzene Eisenmasse nach der in der deutschen Patentschrift Nr.
44730 vom 24. Januar 1887 enthaltenen Darstellung fein zertheilt, aufwirft und vom
Kohlenstoffe und Unreinigkeiten, welche durch die Röhren abgehen, befreit, ähnlich
wie beim gewöhnlichen Bessemer-Verfahren, während die gereinigte Masse zwischen dem
Stege b und den Seiten des Sammlers c in den unteren Theil des letzteren fällt.
Anstatt den Luftstrahl von der Seite dem Stege b
zuzuführen, kann er auch vom Ende, von unten oder von oben herkommen.
Der Sammler c ist mit einer Thür i versehen und wird die Metallmasse auf gewöhnlichem Wege abgezapft,
gewogen und mit der erforderlichen Menge manganhaltigen Eisens, Spiegeleisens oder
anderer Zusätze versetzt und nachher in Formen nach beliebigem Modelle gegossen.
Wenn man den Zugang zu den Löchern f des Steges b passend absperrt, so können diese Cupolöfen auch für
gewöhnliche Zwecke benutzt werden.
Obwohl die Erfinder glauben, daſs sich ein dem Bessemern analoger Prozeſs hier
abspiele, so dürfte doch, nach der ganzen Einrichtung zu rechnen, allenfalls nur ein
Feinen des Eisens eintreten.
Einem gleichen oder ähnlichen Zwecke dient die durch das D. R. P. Nr. 46157, gültig
vom 16. Oktober 1887, des Joseph Toussaint in Holmes
Hall near Brigg (Lincolnshire, England) bekannt gewordene Neuerung an einem
zweitheiligen Ofen zur Erzeugung von Schmiedeisen oder Stahl.
Dieser Ofen (Fig.
7) bildet einen langen, aufrecht stehenden Cylinder (Fig. 1), dessen Länge
ungefähr das Fünffache seines Durchmessers beträgt, und welcher aus zwei Theilen,
einem oberen A und einem unteren B zusammengesetzt ist. Es wird ohne Anwendung von Wind
gearbeitet.
Der Theil A hat an seiner Basis einen Flansch C, in welchem mehrere Löcher zur Aufnahme der Schrauben
D gemacht sind, welche letzteren zur Vereinigung
des Theiles A mit dem Theile B dienen. Ungefähr in der Mitte des Theiles A
ist ein Loch E vorgesehen, durch welches die Entfernung
der auf dem Eisen schwimmenden Schlacke bewirkt wird.
Der Bodentheil B dieses Ofens ist ungefähr 0m,6 hoch und hat die Gestalt einer Büchse, deren
Boden mit F bezeichnet ist. Der obere Rand dieser
Büchse hat, ebenso wie der untere Rand des Theiles A
einen Flansch G, welcher nach auſsen vorspringt und
ebenfalls zur Aufnahme der Bolzen oder Schrauben D
Löcher hat, die mit denjenigen des Flansches C des
Theiles A übereinstimmen.
An einer Seite (links) hat der Theil B über dem Boden
ein Loch H, um das Metall, mit welchem der Ofen gefüllt
wird, ablassen zu können. Das Loch H wird mit einem
Stöpsel oder Zapfen I verschlossen.
Der Bodentheil B des Ofens erhält inwendig eine
Ausfütterung J, welche von demselben Materiale gemacht
ist, das in Gieſsereien zum Schmelzen von Metallen benutzt wird, wie z.B. feuerfeste
Steine oder Tiegel, jedoch kann die Ausfütterung auch aus Thon oder aus einer
Composition, wie z.B. einer Mischung von Sand mit Thon oder Graphit oder anderen
feuerbeständigen Materialien, hergestellt werden.
Die Ausfütterung J ist mit einer Scheidewand K abgedeckt, welche vollkommen dicht an die
Ausfütterung anschlieſst. Die Deckplatte K enthält
Löcher, welche in Abständen von z.B. 50mm oder
mehr oder weniger von einander angebracht sind. Der Durchmesser dieser Löcher
beträgt ungefähr 6mm oder mehr oder weniger. Auf
dem oberen Rande der Ausfütterung J und der Deckplatte
K ruht der untere Rand des aus feuerfesten Steinen
gebildeten Futters des Theiles A, so daſs die
Ausfütterung J nebst der Scheidewand K in dem Boden des Ofens in ihrer Lage erhalten wird.
Der Bodentheil B hat seitlich (rechts) ein zweites
Loch, durch welches ein eisernes oder aus anderem Materiale gebildetes Rohr L hindurchgeht. Das Rohr L
dient zur Einführung von irgend welchen fettigen oder halbfettigen Stoffen in die
Büchse J. Diese letztere kann aus verschiedenen Stücken
gemacht und von verschiedener Gestalt sein.
Das durch Rohr L zugeführte Fett tritt durch die Löcher
in der Platte K nach oben, kommt mit dem geschmolzenen
oder schmelzenden Eisen in Berührung und soll eine Bewegung oder Reaction
hervorrufen, durch welche nach Ansicht des Erfinders das geschmolzene Eisen durch
und durch, in der ganzen Tiefe, d.h. vom Boden bis zur Spitze des Ofens gepuddelt,
oder wohl besser gesagt, gefeint wird. Die Wirkung des Apparates erscheint
zweifelhaft.
Thwaite in Liverpool will nach dem britischen Patente
Nr. 11972 vom Jahre 1886 das Eisen beim Eingieſsen in den Stahlschmelzofen feinen.
Zu diesem Zwecke ist in dem Gewölbe des letzteren ein feuerfester Einguſstrichter
mit Windmantel angebracht. Der Gebläsewind dringt aus letzterem in zahlreichen
Strahlen in das durchflieſsende Eisen ein.
Bessemerprozeſs. Carlsson zu Ulfshytte (Schweden) hat
den Bessemerprozeſs modificirt. Das zu verwendende Roheisen, welches mit Holzkohlen
erblasen ist, enthält etwa
an
Silicium
1,5
bis
2
Proc.
„
Mangan
0,1
„
0,15
„
„
Kohle
(Graphit)(gebunden)
3,90,1
=
4
„
Die dabei fallende Schlacke ist eher ein Trisilicat, als ein
Bisilicat, wenn die Thonerde als Base gerechnet wird.
Nachdem das Roheisen in die Birne abgestochen ist, wird 5 bis 6 Minuten geblasen,
aber sobald das Erscheinen der blauen Flamme den Beginn der Oxydirung der Kohle
andeutet, das Blasen unterbrochen und eine je nach der Gröſse der Beschickung und
der beabsichtigten Eigenschaften des Schluſsproductes bestimmte Menge des in der
Birne befindlichen Metalles unter sorgfältiger Abschlackung in eine besondere, mit
Wiegevorrichtung versehene Pfanne ausgegossen. Dieser Theil des Metallbades wird
„Reductionsmetall“ genannt und enthält gewöhnlich Kohle 4,15 Proc.,
Silicium 0,05 Proc. und Mangan 0,07 Proc.
Hierauf wird das Blasen wieder aufgenommen und fortgesetzt, bis der gröſste Theil der
Kohle oxydirt und das Product in weiches Eisen verwandelt ist; alsdann wird das
vorher ausgegossene Reductionsmetall sammt den für besondere Zwecke nöthig
befundenen Zusätzen in das Bad in der Birne zurückgebracht. Sobald die hierbei
entstehende Reaction beendet, ist das Metall fertig und kann nach kürzerem oder
längerem Aufenthalt ausgeleert und vergossen werden. Bevor das Reductionsmetall
u.s.w. zugesetzt wird, enthält das Product gewöhnlich eine Spur von Silicium, 0,03
Proc. Mangan, 0,05 Proc. Kohle und höchstens 0,02 Proc. Schwefel; da dasselbe aber
meist rothbrüchig ist, wird zuerst reiches Manganeisen und später, sobald die
Reaction beendet, das obengenannte Reductionsmetall, dessen Menge vom gewünschten
Härtegrade des Schluſsproductes abhängig ist, eingebracht.
Der Siliciumgehalt des Schluſsproductes beträgt in der Regel ein Zehntel des
Kohlegehaltes, so daſs man Eisen mit 0,2 Proc. Kohle, 0,02 Proc. Silicium
erhält.
Der Stahl wird in 40 vierzöllige Coquillen ausgegossen, die so geformt sind, daſs die
Blöcke einen Einschnitt erhalten, um später leichter in kleinere Stücke zerschlagen
werden zu können. Schrott bleibt in der Pfanne nicht zurück.
Die Vortheile dieses Verfahres sollen darin bestehen, daſs bei jeder Beschickung
leichter die gerade verlangte chemische Zusammensetzung des Schluſsproductes in
Rücksicht auf Kohle, Silicium und Mangan eingehalten werden kann. Ferner kann aus
sehr siliciumreichem Bessemerroheisen Metall jeden beliebigen Kohlegehaltes neben
sehr geringem Siliciumgehalte hergestellt werden. Die Erzeugung dichter Stahlblöcke
und dichter Stahlguſswaaren soll bei geringsten Kosten leichter sein, ebenso das
Einhalten der für jeden Fall berechneten Gehalte an Silicium und Mangan. Auch ist es
nicht erforderlich, zur Darstellung von Eisen sehr verschiedenen Härtegrades den
Hochofengang verschieden einzurichten. Endlich soll auch leichter ein blasiger Guſs bei den
Blöcken vermieden werden (vgl. Jernk. Annaler, 1887 Bd.
5, und Stahl und Eisen, 1888 S. 55).
In dem Patente Nr. 358 559 der Vereinigten Staaten (Gordon,
Strobel und Leaurau in Philadelphia) ist eine Bessemerbirne beschrieben,
welche zwei Gruppen von je drei wagerechten Düsen hat. Dieselben liegen in einem
besonderen auswechselbaren Theile der Birne. Der Boden, der Düsentheil und der
Obertheil der Birne werden mittels Splintbolzen b,
welche durch den Windkasten c hindurchgehen,
zusammengehalten. Die angegebene Vertheilung der Düsen auf den Umfang der Birne in
der Weise, daſs je drei Düsen unter jedem Zapfen der Birne liegen, hat zur Folge,
daſs die Birne nur wenig gekippt zu werden braucht, um die Düsen frei zu legen, also
den Wind abstellen zu können.
Quer durch die mit seitlicher Windzuführung versehene Birne legt John Wesley Bookwalter in Springfield, Ohio, Vereinigte
Staaten Amerikas, einen massiven Steg aus feuerfestem Materiale. Das Eisen soll
durch den Wind, welcher durch die unter oder über der Oberfläche des Steges
liegenden Düsen einströmt, in schnelle Circulation versetzt und dadurch die Dauer
des Blasens abgekürzt werden (Englisches Patent Nr. 6951 vom 9. Mai 1888).
Derselbe Erfinder ordnet auch in dem Boden der Birne A
ein Windrohr C (Fig. 8) mit seitlichen
Windkanälen D an. Die Windstrahlen sollen dem Eisen
sowohl in senkrechter als wagerechter Richtung eine Drehbewegung ertheilen, wodurch
die auf der Oberfläche des Bades schwimmende Schlacke seitwärts geschleudert werden
soll. Der Zweck der Construction ist in der Patentschrift nicht genügend
klargelegt.
Entphosphorungsverfahren.
Nach dem Englischen Patente Nr. 13242 vom Jahre 1887 (George
Halton in Hagley, County of Worcester) sind in einem trommelförmigen
Drehofen einander gegenüber zwei Herde angeordnet, welche eine gemeinschaftliche
Arbeitsthür, aber je einen Abstich besitzen. Der eine Herd kann sauer und der andere
basisch sein, so daſs der Einsatz zuerst in dem einen und nach Drehung des Ofens um
180° in dem anderen behandelt werden kann.
Das der Wirkungsweise des Apparates zu Grunde liegende Verfahren, nämlich die
Zerlegung des Entphosphorungsprozesses in zwei Theile, wurde bereits von Harmet und andern vorgeschlagen. Danach soll das Eisen
in einer sauren Birne entkieselt und ganz oder theilweise entkohlt und dann in einer
basischen Birne die Entphosphorung vorgenommen werden. Dieses Verfahren scheint in
abgeänderter Form neuerdings wieder Beachtung zu finden, wie nachstehend gezeigt
werden soll.
M. H. Koppmayer (Stahl und
Eisen, 1888 S. 698) bringt, wenn graues Roheisen mit hinreichendem Siliciumgehalte und
ziemlich geringem Gehalte an Phosphor, welches also weder für den Bessemer- noch Thomas-Prozeſs sich eignet, in ökonomischer Weise zu Fluſseisen verarbeitet
werden soll, das flüssige Roheisen, wie es vom Hochofen kommt oder aber durch
Umschmelzen im Cupolofen erhalten wurde, in einer auf Schienen fahrbaren und
kippbaren Pfanne von etwa 3t Fassungsvermögen vor
eine feststehende, innen vorgewärmte Birne von entsprechenden Dimensionen und mit
abhebbarem Boden. In diese wird das Eisen, nachdem das Gebläse angelassen ist, durch
umkippen der Pfanne entleert und dann verfrischt. Die an der Seitenwand der Birne
befindliche Einguſsöffnung wird, nachdem die Pfanne entleert ist, mit einem Stopfen
aus feuerfestem Materiale geschlossen. Das Frischen geschieht mit Wind von niederer
Pressung (0,5 bis 0k,7 auf 1qcm), der durch sechs einlöcherige Düsen geblasen
wird. Die Düsen, deren lichter Durchmesser etwa 35mm beträgt, sind, parallel mit dem Birnenboden, so in die Seitenwand der
Birne eingebracht, daſs der Wind mit geringem Widerstände nur wenig unter der
Oberfläche des Metalles in dasselbe dringt.
Der Birnenboden ist mit jenem Theile der Seitenwand, in dem sich die Düsen befinden,
in einem Stücke abhebbar und auswechselbar.
In den Vereinigten Staaten, wo die sogen. Kleinbessemerei lebhaft betrieben wird,
werden derartige Birnen in den sogen. Clapp-Griffiths-Hütten mit dem besten Erfolge verwendet, um ein sehr
siliciumfreies Fluſseisen zu erzeugen.
Vor der Birne ist ein Herdschmelzofen mit Regenerativfeuerung so aufgestellt und
eingerichtet, daſs das Fluſseisen, sobald man an der Flamme das Ende des
Frischprozesses erkannt hat, über eine drehbare Rinne in diesen abgestochen werden
kann, wobei jedoch das Mitflieſsen der siliciumreichen Schlacke sorgfältig vermieden
werden muſs.
Die Zustellung des Herdschmelzofens ist eine basische, während die Birnen- oder
Converter-Ausmauerung aus siliciumreichem, feuerfestem Materiale besteht. Das in dem
Converter erfrischte Fluſseisen, welches den gesammten Phosphor des Roheisens
enthält, wird auf dem basischen Herde des Schmelzofens durch auf demselben
vorerhitzte Zuschläge entphosphort. Die Entphosphorung geht im heiſsen Ofen mit den
vorerhitzten basischen Zuschlägen, bei der Abwesenheit von siliciumreicher Schlacke
und dem nahezu siliciumfreien Fluſseisen schnell vor sich. Der Aufwand an basischem
Zuschlage ist ein geringer und nur von dem Phosphorgehalte des Fluſseisens abhängig.
Wenn auf diese Weise das Frischen des Roheisens im Converter und die Entphosphorung
des erhaltenen Fluſseisens im Herd Schmelzofen vorgenommen wird, so kann erstere
Operation in 8 bis 12 Minuten, die letztere in 15 bis 20 Minuten beendet sein und
eine groſse Leistung mit beiden zusammenwirkenden Apparaten erzielt werden.
Reparaturen sind selten und können, eine geeignete Construction des Herdschmelzofens
vorausgesetzt, in möglichst kurzer Zeit vorgenommen werden. Der Boden eines 3t-Converters von beschriebener Construction hält
auf den amerikanischen Clapp-Griffiths-Hütten 40 bis 70
Hitzen und kann in 15 Minuten ausgewechselt werden. Die basische Ausmauerung des
Herdschmelzofens soll, weil dieselbe nur mit fast siliciumfreiem Fluſseisen und
basischen Zuschlägen in Berührung kommt, von groſser Dauerhaftigkeit sein.
Die Anlagekosten sollen ebenfalls im Vergleiche zu denen eines Puddlingswerkes von
gleicher Leistungsfähigkeit gering sein. Dasselbe gilt auch von den Betriebskosten,
welche, soweit dieselben den Brennmaterialaufwand, Abbrand und die nöthigen
Arbeitslöhne betreffen, bei dem Stahlwerke so viel niedriger sind, als die Auslagen
für die basischen Zuschläge und die etwaigen Mehrkosten des feuerfesten Materiales,
des höheren Preises der basischen Zustellung des Herdschmelzofens halber reichlich
durch dieselben aufgewogen werden sollen. Um gröſsere Productionen als 14000t Blöcke bei je 3t Fassungsraum der Birne und des Ofens, bei 50t Fluſseisen in 24 Stunden und in 280 Arbeitstagen zu erreichen, wird das
ganze System vervielfacht.
Das Umschmelzen des Roheisens geschieht in den in der Mitte des Gebäudes liegenden
Cupolöfen. Das flüssige Roheisen wird in kippbaren Pfannen durch eine kleine
Locomotive zu den Birnen gebracht, deren unterer Theil ausgewechselt werden
kann.
Bei den hier zur Verwendung gelangenden Herdschmelzöfen ist nach Stahl und Eisen, 1888 S. 576, das Mauerwerk des
Schmelzraumes nach dem Vorgange von Dick-Riley und
Andern von dem der seitlich davon freistehenden Wärmesammler getrennt, damit durch
den Schmelzherd dringendes Metall letzteren nicht beschädigen kann.
Der auf schmiedeisernen Trägern und Stützmauern ruhende Schmelzraum und die
Wärmesammler haben cylindrische Form, sind mit Blechmänteln versehen und von frei
auf den Seitenmauern derselben aufliegenden Gewölben bedeckt, welche die Form eines
Hohlkugelabschnittes haben und von schmiedeisernen oder stählernen Ringen gehalten
und mittels eines über dem Ofen angebrachten Laufkrahnes abgehoben und ausgewechselt
werden können. Die Verbindungskanäle zwischen dem Schmelzraume und den Wärmesammlern
sind verankert und von in eisernen Klammern gehaltenen Gewölben bedeckt, welche
gleichfalls mit dem Laufkrahne abgehoben und ausgewechselt werden können. Gewölbe
und Einsatzthüren sind mit Wasserkühlung versehen. Müſste gegebener Verhältnisse
halber der Abstich eines anzulegenden Ofens innerhalb einer Entfernung von der
Hüttensohle angebracht werden, welche eine zu geringe Höhe der senkrechten
Wärmesammler bedingen, und dieselben dadurch ungenügend machen würde, so kann man
die Kanäle, welche zwischen diesen und dem Umsteuerungsapparate liegen, zu Kammern erweitern und diese
gleichfalls als Wärmesammler benutzen und damit die über der Hüttensohle
befindlichen ergänzen. Zwischen den Mänteln der freistehenden Wärmesammler und des
Schmelzraumes und der Ausmauerung derselben wird ein etwa 35mm breiter Raum freigelassen und mit erbsen- bis
haselnuſsgroſsen Brocken von mürben Ziegeln aufgefüllt. Sollte bei dem Betriebe des
Ofens das Mauerwerk sich mehr ausdehnen als die Blechmäntel, so werden die
dazwischen aufgefüllten Ziegelbrocken zerdrückt und damit ein Reiſsen oder Platzen
der Blechmäntel verhindert.
Beginnt nach langem Gebrauche das Gewölbe des Schmelzherdes allmählich sich
abzunutzen und endlich dünn zu werden, was immer nur an denjenigen Stellen in der
Flammenrichtung geschieht, welche von der Stichflamme getroffen werden, so wird
dasselbe durch den Laufkrahn um einige Centimeter gehoben, um 90° gedreht und dann
wieder aufgesetzt. Die abgenutzten Theile des Gewölbes befinden sich nun über dem
Abstiche und diesem gegenüber, also an Stellen, wo sie weniger stark angegriffen
werden. Das Gewölbe wird in dieser neuen Lage weiter benutzt, bis daſs es wieder an
den betreffenden Stellen dünn geworden ist und dann durch ein neues Gewölbe ersetzt
werden muſs.
Die Hüstener Gewerkschaft in Husten (Westfalen) bringt
als Bindemittel für basische und feuerfeste Steine Phenolate in Vorschlag (D. R. P.
Nr. 46 237 vom 24. November 1887). Unter Phenolaten sind zu verstehen die chemischen
Verbindungen von Kalihydrat, Natronhydrat, Barythydrat, Kalkhydrat oder Magnesia mit
den Phenolen, welche von der trockenen Destillation der Steinkohle, Braunkohle, des
Torfes oder Holzes herrühren.
Der Theer aus diesen Materialien wird destillirt. Die so gewonnenen Theeröle werden
in bekannter Weise in Phenole und Kohlenwasserstoffe geschieden.
Die ersteren (Carbolsäure, Kreosot) werden mit den oben aufgeführten Alkalien oder
alkalischen Erden zu einem dünnen Brei angerührt. Durch die chemische Action erwärmt
sich die Masse, der man, ehe sie erkaltet und erstarrt, die feuerfesten Materialien
beimischt. Binnen wenigen Stunden erhärtet das Gemisch, welches man sofort in die
gewünschte Form bringen muſs, ähnlich wie Cement. Je reiner die verwendeten Phenole
sind, d.h. je sorgfaltiger die neutralen Oele entfernt sind, desto härter und
haltbarer werden die geformten Massen.
Die Materialien, die in gebranntem Zustande basische Eigenschaften besitzen, wie
Kalkstein, Marmor, Dolomit, Magnesit, können, gebrannt und geeignet zerkleinert,
ohne Weiteres mit den Phenolen zu einer formbaren plastischen Masse verarbeitet
werden, welche beim Erkalten ebenfalls cementartig erhärtet.
Da der Theer als Bindemittel für basische Ziegel ganz allgemein und mit bestem Erfolge bereits
in Anwendung ist, so bleibt abzuwarten, ob die mit dem betreffenden Bindemittel
hergestellten Producte in technischer und ökonomischer Beziehung noch etwas Besseres
zu bieten vermögen.
W.
Koort.
Tafeln
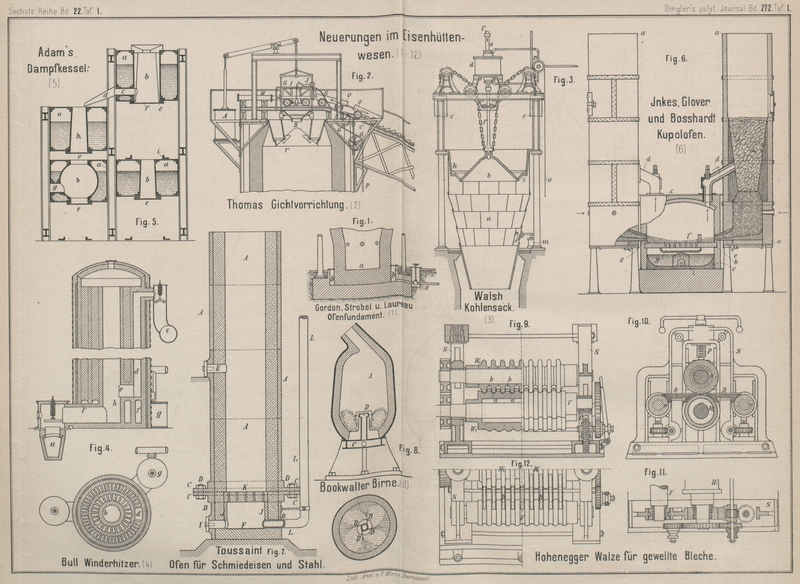