Titel: | Neuerungen im Metallhüttenwesen. |
Autor: | W. Koort |
Fundstelle: | Band 272, Jahrgang 1889, S. 444 |
Download: | XML |
Neuerungen im Metallhüttenwesen.
(Schluſs des Berichtes S. 391 d. Bd.)
Mit Abbildungen auf Tafel
20.
Neuerungen im Metallhüttenwesen.
Kupfer und Zink.
Nach Industries, Bd. 5 S. 103, hat
de
Escozura in Madrid sich ein Verfahren patentiren lassen, welches gestatten
soll, auf elektrolytischem Wege 78 Proc. des Kupfers aus der schwefelsauren
Extractionslauge der Erze zu gewinnen, während* der Rest auf andere Weise erhalten
werden kann. Das Verfahren, welches nicht genauer beschrieben ist, soll auf
spanischen Werken (Riotinto) eingeführt werden.
Walther Feld und Dr. Georg v.
Krone in Charlottenburg haben für ein Verfahren zur Darstellung von
Siliciumkupfer das D. R. P. Nr. 47201 vom 21. April 1888 erworben.
Es wird ein Gemenge von 30 Th. entwässertem Kupferchlorid, 8 Th. Kieselerde und 3 Th.
Kohle mit einem Gemenge von 150 Th. Kupfer, 25 Th. Kieselerde und 20 Th. Kohle
überschüttet. Die ganze Beschickung wird so lange auf Rothglut erhitzt, als in den
entweichenden Grasen noch Chlor bemerkbar ist. Dann steigert man die Temperatur auf
Weiſsglut, um das gebildete Siliciumkupfer zusammenzuschmelzen. Auf diese Weise soll
eine spröde, 8 Proc. Silicium enthaltende Legirung gewonnen werden.
Die Eigenschaft des Kochsalzes, beim Erhitzen mit Kieselerde Chlor abzugeben und bei
der Gegenwart von Kupfer dasselbe zu chloriren, gestattet, das Kupferchlorid durch
Kochsalz zu ersetzen.
Zur Gewinnung einer 8 Proc. Si enthaltenden Legirung sollen sich folgende
Verhältnisse als zweckmäſsig erwiesen haben:
Ein Gemenge von 30 Th. Kochsalz, 25 Th. Kieselerde und 6 Th. Kohle wird mit einem
Gemenge von 150 Th. Kupfer, 25 Th. Kieselerde und 15 Th. Kohle überschichtet. Die
ganze Beschickung wird darauf so hoch erhitzt, daſs Chlor zu entweichen beginnt.
Darauf steigert man, wie vorhin angegeben, die Temperatur auf Weiſsglut, um das
Siliciumkupfer anzusammeln. Selbstverständlich können die Verhältnisse so getroffen
werden, daſs man ein an Silicium reicheres oder ärmeres Kupfer erhält.
Es ist bekannt, daſs ein Gehalt an Silicium die Härte, Festigkeit,
Widerstandsfähigkeit und Guſsfähigkeit des Kupfers und seiner Legirungen erhöht. In
Folge dessen ist das Siliciumkupfer sehr geeignet zur Herstellung von Legirungen,
welche die angegebenen Eigenschaften besitzen sollen.
Die Siliciumkupferlegirungen dürften auch ein ausgezeichnetes Material zur
Anfertigung von Glocken, Kunstgegenständen, Maschinentheilen, Bronzegeschützen,
Drahtseilen, Patronenhülsen und ähnlichen Erzeugnissen bilden, welche in ihrer
Anwendung einer in jeder Beziehung groſsen Widerstandsfähigkeit bedürfen.
Die Eigenschaft des Siliciums, dem schmelzenden Kupfer die letzten Reste von
Sauerstoff zu entziehen, macht das Siliciumkupfer auch geeignet, als Zusatz beim
Läutern des. Kupfers zu dienen.
Wegen des Heusler'schen Verfahrens zur Darstellung von
Siliciumkupfer und dessen Verwendung siehe D. p. J.,
1886 261 478.
Das Extractionsverfahren für Kupferkiese mittels Eisennitrats (vgl.
D. p. J., 1889 271 214) ist
nach der Berg- und Hüttenmännischen Zeitung, 1889 S.
47, durch eine Reihe systematisch angestellter Versuche weiter geprüft und
entwickelt, sowie auf Zinkblende haltige Erze übertragen worden.
Schwefelkupfer und Schwefelzink werden leichter sulfatisirt als Schwefeleisen, was
dem Verfahren zu besonderem Vortheile gereicht.
Man mischt das bis auf 1 oder 2mm Korngröſse
zerkleinerte Erz (Riotinto-Kiese u.s.w.) mit der erforderlichen Menge von
Eisennitrat aufs innigste, bringt das Gemenge in einen entsprechend construirten
Ofen und erhitzt bis auf etwa 40 bis 60° C, wobei die erste kräftigere Reaction vor
sich geht, indem etwa die Hälfte der Salpetersäure sich abspaltet und unter Bildung
niederer Oxydationsstufen den Sauerstoff an das Schwefelkupfer abgibt. Bei
Steigerung der Temperatur auf etwa 130 bis 180° findet die vollständige Spaltung des
salpetersauren Eisensalzes statt und es hinterbleibt Eisenoxyd. Die entwickelten
salpetrigen Dämpfe werden um so vollständiger reducirt und ausgenutzt, je länger sie
mit oxydirbaren Schwefelmetallen in Berührung bleiben, weshalb eine entsprechend
höhere Schichtung des Materiales zweckentsprechend ist.
Da nun das Stickoxydgas bei Gegenwart von atmosphärischer Luft sich wieder leicht zu
N2O3 und NO2 oxydirt und unter Zuführung von Sauerstoff sich
weiter in Salpetersäure umsetzen, so ist damit der Weg der Regenerirung der
Salpetersäure angedeutet.
Während des Sulfatisirungsprozesses leitet man daher einen Luftstrom durch den
geschlossenen, nur mit einem Abzugskanale versehenen Erhitzungsapparat und führt die
salpetrigen Dämpfe nach geeigneten Absorptionsthürmen, woselbst sich die Bildung der
Salpetersäure vollzieht. Der Verlust an Salpetersäure soll hierbei nur 4 bis 5 Proc.
betragen.
Nach dem Verschwinden der braunrothen Dämpfe in etwa 2 bis 4 Stunden ist der
Sulfatisirungsprozeſs vollendet und kann nur das gebildete Kupfersulfat mit Wasser
ausgelaugt werden, ohne den Rückstand weiter zu verwerthen, oder aber man röstet
durch bloſse Steigerung der Temperatur in dem entsprechend eingerichteten
Sulfatisirungsofen den rückständigen Schwefel der Pyrite vollständig ab und
schlieſst eine Schwefelsäuregewinnung an. Das sulfatisirte Material ist durch die
reichliche Gasentwickelung im Sulfatisirungsprozesse äuſserst porös und aufgelockert
und der nachfolgenden Röstung so aufs Beste vorgearbeitet, wodurch dieselbe schnell
und vollständig von statten geht. Das Röstgut wird mit Wasser ausgelaugt und das
Kupfer der erfolgenden Kupfervitriollauge mit Eisen als Cementkupfer gefällt. Die
resultirende Eisenvitriollauge wird mit einer concentrirten Lösung von
salpetersaurem Kalke (durch Einwirkung der regenerirten Salpetersäure auf
kohlensauren Kalk erhalten oder in Salpeterplantagen billigst erzeugt) versetzt, wobei sich
schwefelsaurer Kalk (in Form von sogen. Annaline für Papierfabrikanten von groſsem
Handelswerthe) ausscheidet und eine Lösung von salpetersaurem Eisenoxydul sich
bildet. Letztere wird in Vorlagen durch die salpetrigen Dämpfe des
Sulfatisirungsprozesses weiter zu salpetersaurem Eisenoxyd oxydirt und abgedampft.
Der zu dem beschriebenen Sulfatisirungsprozesse erforderliche Ofen müſste demnach
zwei, je nach Belieben abstellbare Abzugskanäle besitzen, einmal für die salpetrigen
Dämpfe und dann für die schwefligsauren Gase. Auf diese Weise ist in einem Apparate
und in einer Operation Sulfatisirung und Röstung vollzogen und damit eine gesonderte
chlorirende Röstung u.s.w. mit den erforderlichen Arbeitskräften und
Brennstoffverbrauch.
In entsprechender Weise läſst sich das beschriebene Verfahren auch direkt für
blendehaltige Pyrite und sonstige blendige Erze mit gleichem Erfolge verwerthen und
dürfte ein willkommenes Mittel bieten, um die sonst so schwierig zu verarbeitenden
blendigen Kiese und deren Abbrände in einfachster Art zu sulfatisiren und den
Zinkgehalt zu extrahiren. Die zinkischen Abbrände, welche neben Schwefelzink und
Zinksulfat auch gewisse Mengen von Zinkoxyd enthalten, müssen zur vollständigen
Extraction ihres Zinkgehaltes etwas verschieden behandelt werden. Zunächst werden
die gepulverten Abbrände ihrem Schwefelzinkgehalte entsprechend mit der
erforderlichen Menge salpetersauren Eisenoxydes gemengt und wie oben dem
Sulfatisirungsprozesse unterworfen. Der Rückstand wird alsdann mit warmem Wasser
ausgelaugt, wobei nur das gebildete Zinksulfat in Lösung geht, während das
vorhandene Zinkoxyd mit schwefelsäurehaltigem Wasser in einer Nachlauge ausgezogen
wird. Ein anderer vorzuschlagender Weg zur Extraction des Zinkoxydgehaltes ist der,
daſs man den ersten Laugrückstand mit der regenerirten Salpetersäure einige Zeit
stark erwärmt, wobei neben dem im Sulfatisirungsprozesse gebildeten Eisenoxyde auch
das vorhandene Zinkoxyd als salpetersaures Salz sich löst. Das Gemisch beider Salze
wird von neuem als Sulfatisirungsmaterial benutzt und der nach dem Auslaugen mit
Wasser erhaltene Rückstand wieder mit der regenerirten Salpetersäure behandelt, und
so fort, bis eine genügende Anreicherung an salpetersaurem Zinkoxyde stattgefunden
hat, um das Eisenoxyd durch geschlämmtes Zinkoxyd auszufällen. Aus dieser
salpetersauren Zinklösung erhält man wieder direkt Salpetersäure, entweder durch
Zusatz von Schwefelsäure und Abdestilliren oder aber durch Abdampfen und Erhitzen
des Salzes bis zur Zersetzung, wobei Zinkoxyd hinterbleibt und salpetrige Dämpfe
entweichen, welche in Wasser geleitet und unter Salpetersäurebildung absorbirt
werden.
Die Sulfatisirungsverfahren für Einfachschwefelkupfer (CuS) und Halbschwefelkupfer
(C2S) lassen sich ohne Berücksichtigung des
Krystallwassers durch folgende Gleichungen ausdrücken:
I. Fe2(NO3)6 + CuS = 2CuSO4 +
FeO3 + 6NO + O.
II. 2Cu2S + Fe2(NO3)6 + O = 2CuSO4 + 2CuO + 6NO + F2O3.
Aus Gleichung II ist ersichtlich, daſs neben dem Kupfersulfat auch ein Gehalt an
Kupferoxyd entsteht, welcher sich aber theils in der nachfolgenden Röstoperation,
theils durch weitere und stärkere Erhitzung bis zur Zersetzung des Eisensulfates
sulfatisiren läſst (Flechner's Verfahren). Nachstehend
sind einige Versuchsresultate angegeben:
I. Kupferkiese.
1) Riotinto-Kies (3,55 Proc. Cu) mit 30 Proc. Eisennitrat
sulfatisirt und geröstet:
Die Wasser lauge enthielt:
Cu
3,47
Proc.
Fe
3,62
„
SO3
13,71
„
2) Probe Nr. 1 mit 17 Proc. Eisennitrat sulfatisirt und
geröstet:
Wasserlauge:
Schwefelsäurehaltige Nachlauge:
Cu
2,3 Proc.
Cu
1,21 Proc.
Fe
0,4 „
in Summa Cu
3,51 Proc.
Vergleicht man diese beiden Analysenresultate, so ergibt sich, daſs eine geringere
Menge Eisennitrat, als theoretisch erforderlich, keine vollständige Sulfatisirung
erreichen läſst, dagegen eine beinahe eisenfreie Lauge resultirt und daſs sich der
Rest des Kupfergehaltes durch eine nachfolgende Laugung mit schwefelsäurehaltigem
Wasser ausziehen läſst.
3) Pommeron-Kies (0,36 Proc. Cu) mit 10 Proc. Eisennitrat
sulfatisirt und geröstet:
Wasserlauge:
Cu
0,30
Proc.
Fe
2,43
„
4) Schwedischer Kies (4,78 Proc. Cu) mit 17 Proc. Eisennitrat
sulfatisirt und geröstet:
Wasserlauge:
Schwefelsäurehaltige Nachlauge:
Cu
2,31 Proc.
Cu
2,20 Proc.
Fe
Spuren.
in Summa Cu
4,51 Proc.
5) Schwedischer Kies (8,24 Proc. Cu) mit 50 Proc. Eisennitrat
sulfatisirt und geröstet:
Schwefelsäurehaltige Lauge:
Cu
7,71
Proc.
Fe
4,63
„
6) Probe Nr. 5 mit 35 Proc. Eisennitrat sulfatisirt und
geröstet:
Wasserlauge:
Schwefelsäurehaltige Nachlauge:
Cu
4,5 Proc.
Cu
3,41 Proc.
Fe
Spuren.
in Summa Cu
7,91 Proc.
7) Westfälischer Kies (11,16 Proc. Cu) mit 60 Proc. Eisennitrat
sulfatisirt und geröstet:
Wasserlauge:
Schwefelsäurehaltige Nachlauge:
Cu
7,63 Proc.
Cu
2,62 Proc.
Fe
3,41 Proc.
in Summa Cu
10,25 Proc.
Fassen wir die Ergebnisse vorstehender Analysen zusammen, so stellen sich uns für die
Kupferkiese zwei Fälle dar. Entweder benutzt man zur Sulfatisirung die theoretisch
erforderliche Menge Eisennitrat und laugt bloſs mit Wasser aus, oder aber man
beschränkt den Eisennitratzusatz aufs Nothwendigste und laugt mit
schwefelsäurehaltigem Wasser nach.
II. Zinkabbrand.
1) Schlesische Erze (9,98 Proc. Zn) mit 50 Proc. Eisennitrat
sulfatisirt und geröstet:
Wasserlauge:
Salpetersäureauszug des
Rückstandes:
Zn
5,98 Proc.
Zn
3,42 Proc.
in Summa
9,40 Proc. Zn.
2) Probe Nr. 1 mit 80 Proc. Eisennitrat in Lösung erhitzt und zur
Trockne gebracht:
Wasserlauge:
Zn
7,68
Proc.
Für die Extraction des Zinkes ist dem Erfinder des
Verfahrens, Josef Perino, ebenso wie bereits früher für
die Behandlung der Kupfererze, ein D. R. P. unter Nr. 46748, gültig vom 31. Mai
1888, mit folgendem Patentansprüche verliehen worden:
„Extraction des Zinkes aus blendehaltigen Schwefelkiesen, deren Abbränden und
allen schwefelzinkhaltigen Erzen durch einen Sulfatisirungsprozeſs mittels
salpetersaurer Eisensalze bei niedrigen Temperaturen derart, daſs das
Schwefelzink direkt in leichtlösliches Zinksulfat verwandelt wird.“
Nach dem Vorgange von Eichhorn und Liebig sind zahlreiche Ofenconstructionen bekannt
geworden, welche das Todtrösten der Zinkblende in Muffelöfen bezwecken.
Während man früher glaubte, daſs zur Entfernung der letzten 8 bis 10 Proc. Schwefel
ganz besonders hohe Temperaturen erforderlich seien, hat sich jetzt gezeigt, daſs zu
diesem Zwecke die Temperatur der Muffelöfen hoch genug ist. Man muſs nur genügend
lange Zeit auf den Röstprozeſs verwenden.
Eichhorn veröffentlicht in der Berg- und Hüttenmännischen Zeitung, 1889 S. 113 und 114 die
Betriebsresultate solcher Röstöfen, welche er selbst 18 mal in Deutschland und
Belgien zur Ausführung gebracht hat. Der Ofen ist ein Doppelofen mit langgestreckten
Muffeln, äuſserer Beheizung und vier Sohlen. Um die vorhandenen Fundamente von allen
Freiberger oder Hasenclever-Oefen benutzen zu können, wird den Herden nur eine
Breite von 1m,40 gegeben.
Ein solcher Ofen liefert in 24 Stunden 4200 bis 4500k Röstgut, bei einem Verbrauche von vier Schichten für die gesammte
Ofenbedienung und 800k westfälischer Steinkohlen.
Das Röstgut enthält nur 0,1 Proc. Schwefel, bei kalkiger Gangart und der daraus
folgenden Gypsbildung etwa 2½ Proc. Schwefel.
Der geringe Kohlenverbrauch gegenüber den alten Freiberger Oefen erklärt sich daraus, daſs
letztere wegen der kurzen Röstzeit mit unnöthig hohen Temperaturen arbeiten müssen
und daſs der Arbeitsprozeſs es bedingt, vor der Feuerbrücke durch die offenen
Ofenthüren einen enormen Luftüberschuſs einströmen zu lassen, der, um die Temperatur
im Ofen zu erhalten, miterhitzt werden muſs.
Die Gase von den Freiberger Oefen enthalten meist nur 2 Vol.-Proc. SO2 und weniger. Die Gase der Muffelöfen haben, je
nach dem Schwefelgehalte der Erze, 6 bis 8 Vol.-Proc. SO2. Sie sind also geeignet zur Darstellung von Schwefelsäure und zur
Erzeugung wasserfreier flüssiger schwefliger Säure, welch letztere in der
Papierfabrikation, bei der Eisbereitung u.s.w. bereits Anwendung findet.
Eichhorn theilt mit, daſs von jenen 18 angelegten Oefen
12 Oefen die Gase zur Schwefelfabrikation und 6 Oefen zur Herstellung flüssiger
SO2 hergeben. Die Betriebskosten sollen sich
noch dadurch vermindern lassen, daſs die Herdbreite von 1m,40 auf 1m,80
erhöht wird, wodurch die Leistung auf 5200 bis 5400k gesteigert werden kann.
Julius Miche und Robert
Schumann in Dombrowa bei Beuthen in Oberschlesien benutzen das nachfolgend
beschriebene Verfahren, um die in zinkischen Dalomiten und Waschabgängen u.s.w.
enthaltenen 3 bis 5 Proc. Zink auf einen höheren Procentsatz anzureichern (D. R. P.
Nr. 46282 vom 20. April 1888).
In einer Muffel oder Retorte wird das obengenannte Rohproduct, welches aus
kohlensaurem Kalke und Magnesia hauptsächlich, zum geringeren Theile aber aus Zink
und Eisen besteht, geröstet, wodurch fast sämmtliche Kohlensäure ausgetrieben wird,
so daſs nur die Oxyde vorstehender Metalle zurückbleiben.
Schon durch diesen Röstprozeſs nimmt der Zinkgehalt erheblich zu, während das
verarbeitete Rohproduct erheblich an Gewicht verliert. Nun wird diese geröstete
Masse erkalten gelassen, in einen Behälter gebracht und mit Wasser befeuchtet,
später aber mehr Wasser hinzugefügt, so daſs das Product abgelöscht wird. Hierauf
läſst man die hierdurch gebildete Kalkmilch ablaufen und spült je nach Bedarf den
Rückstand, welcher jetzt aus Zinkoxyd, Eisenoxyd und etwas Magnesia besteht, zwei-
bis dreimal nach. Durch dieses Verfahren wird eine Anreicherung des Rückstandes
erzielt, welche vier- bis fünffach so hoch an Zink ist als das ursprüngliche
Rohproduct; wenn also das Rohproduct 4 Proc. Zink enthielt, so wies der Rückstand
bei Versuchen 17,5 Proc. Zink auf.
Durch Versuche wurde folgendes festgestellt: 5000k
Rohproduct verloren durch den Röstprozeſs 2000k
und durch die Ablöschung durch Wasser 1500k, so
daſs von 100 Centnern Rohproduct nur 30 Centner angereichertes, für die Hütte aber
zu verwerthendes Gut von 18 Proc. Zink übrig blieben, wodurch die Zweckmäſsigkeit
des Verfahrens bewiesen wird.
Die Kupferproduction der Erde betrug im J. 1888 nach Merton 261852 engl. Tonnen, gegenüber 151963t im J. 1879. An dieser Production betheiligen sich vorzugsweise (vgl. Berg- und Hüttenmännische Zeitung, 1889 S. 131)
1888
1879
Australien
mit
7450t
9500t
Oesterreich
„
1010t
245t
Bolivien
„
1450t
2000t
Canada
„
2250t
50t
Chile
„
31240t
49315t
Cap der guten Hoffnung
„
5800t
4328t
England
„
1500t
3462t
Deutschland
„
15230t
9000t
Italien
„
2500t
1140t
Mexico
„
2050t
400t
Ruſsland
„
4700t
3300t
Schweden
„
900t
800t
Spanien und Portugal
„
63800t
33361t
Vereinigte Staaten
„
103128t
23350t
Die Zinkproduction der Welt erreichte in den letzten Jahren folgende Ziffern (vgl.
Oesterreichische Zeitung für Berg- und Hüttenwesen,
1889 S. 169):
1888
1887
1886
Rheinland und Belgien
133245t
130995t
129020t
Schlesien
83375t
81375t
81630t
Groſsbritannien
26633t
19339t
20730t
Frankreich und Spanien
16140t
16028t
15305t
Polen
3785t
3580t
4145t
Oesterreich
3827t
3566t
3760t
Vereinigte Staaten
50000t
45530t
38072t
–––––––––––––––––––––––
317005t
300413t
292662t
Edelmetalle.
Zum continuirlichen Abscheiden von Gold und anderen Edelmetallen aus ihren Erzen
benutzt Atkins (vgl. D. R. P. Nr. 45774 vom 27.
November 1887) einen Apparat, welcher aus einer senkrechten, durch eine
Filtrationsvorrichtung E (Fig. 16) in zwei
Abtheilungen A und B
getrennten Kammer besteht, wobei die die Anode bildende Abtheilung A mit einer aus leitendem, elektrolytisch unlöslichem
Materiale hergestellten Vorrichtung versehen ist. Eine solche Vorrichtung kann z.B.
aus einer Schraube D oder schräg gestellten über
einander liegenden Sieben bestehen, wodurch der Durchtritt des Erzes verzögert
werden soll. Die diese Hemmungsvorrichtung enthaltende Kammer A ist mit einem Auslasse M
versehen, durch welchen die Gangmasse continuirlich entfernt werden kann, während
die Kathodenabtheilung eine rotirende, cylindrische Kathode H, biegsame Abstreicher J und unten einen
Auslaſs K enthält, hierdurch soll der von der Kathode
abgestrichene Niederschlag continuirlich entfernt werden.
Statt der beiden Kammern A und B kann auch nur eine Abtheilung vorhanden sein, deren Wand dann aus
leitendem Materiale bestehen muſs, um entweder den positiven oder negativen Pol
bilden zu können,
während die ebenfalls aus leitendem Materiale hergestellte Hemmungsvorrichtung von
einem als Filter dienenden porösen Cylinder eingeschlossen wird.
Der genannte Auslaſs M steht mit dem Einlaſsrohre M1 eines
Amalgamirungsapparates in Verbindung. Letzterer besteht aus einem wagerechten
Cylinder N, welcher eine rotirende Trommel O enthält. Quer über dem Umfange dieser Trommel sind
Rinnen oder Kanäle S hergestellt, und die so gebildeten
Räume sowohl wie der Spielraum zwischen der Trommel und dem Cylinder werden mit
Quecksilber gefüllt. Zur Aufnahme von überschüssigem Quecksilber ist unten im
Cylinder N eine Vertiefung T vorgesehen.
Die Abtheilungen A und B
werden mit einer der bekannten elektrolytischen Lösungen je nach der Natur des zu
behandelnden pulverisirten Erzes gefüllt. Das Erz fällt auf die Schraube D und gelangt in Folge seiner Schwere auf der geneigten
Fläche der Schraube nach unten. Da letztere aber zweckmäſsig in der Richtung gedreht
wird, welche das Erz nach dem oberen Theile der Anodenabtheilung zu heben bestrebt
ist, so wird die Bewegung des Erzes von oben nach unten durch die elektrolytische
Lösung verzögert und das ganze Erz eine erhebliche Zeitlang mit dem Anodenpole in
Verbindung gelassen. Auf diese Weise soll ein Theil der unedleren Metalle sich lösen
und auf der Kathode niedergeschlagen werden, während Gold und Silber vorwiegend nach
dem Amalgamirungsapparate gelangen. Dort tritt es in die Rinnen an dem Umfange der
Trommel O ein, wird bei Drehung dieser Trommel in
Richtung des Pfeiles nach dem unteren Theile des Cylinders N durch das darin befindliche Quecksilber geführt und steigt an der
anderen Seite hoch, sobald die Trommel sich zu drehen fortfährt. Endlich tritt es
aus den Rinnen oder Kanälen der Trommel aus, indem es in Folge der geringeren
Dichtigkeit durch das Quecksilber an einem Auslaſskanale U auf der entgegengesetzten Seite des Cylinders N hochsteigt und durch den Abzug V
weitergeführt wird. Es ist ersichtlich, daſs beim Durchtreten durch den
Amalgamirungsapparat die Erzpartikelchen in stetiger Bewegung sind und in innige
oder reibende Berührung mit dem Quecksilber gebracht werden.
Um den Quecksilberstand in dem Amalgamirungsapparate und dadurch die Menge Erz
reguliren zu können, welche durch den Apparat in einer gegebenen Zeit geht, wird ein
Quecksilberregulator angewendet, welcher aus einem Behälter X besteht, mit dessen Boden ein Rohr X1 verbunden ist, welches in eine Kammer X2 mündet, die durch
ein Rohr X3 mit dem
Quecksilber in dem Cylinder N in Verbindung steht. Das
untere Ende des Rohres X1 geht durch eine Stopfbüchse oben an der Kammer X2, so daſs das Rohr X1 mit dem Reservoir
X innerhalb gewisser Grenzen mittels des durch eine
Kurbel zu bewegenden Kegeltriebes X4 gehoben und gesenkt werden kann.
Das Kegelrad X4 wird
innen angeschraubt und das Rohr X1 hindurch geschraubt, so daſs, sobald die genannte
Kurbel gedreht wird, das Kegelrad ähnlich in seinem Lager gedreht wird und als
Mutter auf den Gewindetheil des Rohres X1 wirkt und dieses zusammen mit dem Reservoir X hebt oder senkt. Soll die Menge von Quecksilber in
dem Amalgamirungsapparate vermehrt werden, um den Zutritt von Erz aus dem
elektrolytischen Apparate zu verzögern, so werden das Reservoir X und Rohr X1 gehoben, und mehr oder weniger Quecksilber gelangt
aus dem Reservoir X nach dem Cylinder N. Will man dagegen die Menge Quecksilber in dem
Amalgamirungsapparate vermindern, um den Zutritt von Erz aus dem elektrolytischen
Apparate zu vermehren, so werden das Reservoir X und
das Rohr X1 gesenkt,
und mehr oder weniger Quecksilber gelangt aus dem Cylinder N in den Behälter X.
Einrichtungen an Muffel- und Cupolöfen,
Flugstaubverdichtung.
Bei den Muffelöfen gewöhnlicher Construction befinden sich über der Sohle eines Ofens
zwei Gewölbe, zwischen welchen die Flamme hindurchschlägt.
Seitens der Direktion des Salzbergwerkes Neu-Staſsfurt
in Löderburg bei Staſsfurt wird nun vorgeschlagen, die Decke des Ofens aus
aufgehängten röhrenförmigen Steinen herzustellen, durch welche die glühenden
Feuergase hindurchstreichen (vgl. D. R. P. Nr. 46215 vom 8. Mai 1888).
Die röhrenförmigen Steine b (Fig. 17) werden mittels
eiserner Haken c an den Trägern d aufgehängt und durch derartiges Aneinanderfügen derselben, daſs die
Oeffnungen auf einander passen, Feuerzüge a
gebildet.
Auch mittels Schrauben, welche in den Steinen befestigt sind, oder durch andere
geeignete Vorrichtungen können dieselben an den Trägern aufgehängt werden. Durch
Aufhängung der röhrenförmigen Steine wird der seitliche Druck eines Ofengewölbes
aufgehoben und auſserdem ermöglicht, daſs sämmtliche Feuerzüge in der gleichen Höhe
über der Ofensohle sich befinden, was bei einem Gewölbe unmöglich ist.
Ernst Boeing in Bad Nauheim will (vgl. D. R. P. Nr.
46584 vom 18. Juli 1888) bei Schmelz- und Cupolöfen aus dem oberen Theile des
Wenschachtes die Verbrennungsgase mittels Ventilators (Gebläsemaschine) absaugen,
wobei die Einrichtung getroffen ist, daſs letzterer je nach Bedarf durch getheilte,
mit Hähnen verschlieſsbare Rohre sowohl aus dem oberen Theile des Ofenschachtes, als
auch aus der freien Luft saugen kann.
Der Ventilator bläst nicht direkt in den Ofen, sondern in einen entsprechend groſsen
mit Manometer und Sicherheitsventil versehenen Windkessel aus Eisenblech oder
Guſseisen, der weiter noch ein Rückschlagventil und ein Absperrventil hat und dazu
dient, die abgesaugten Wengase mit Luft unter entsprechend hohem Drucke zu mischen.
Vom Windkessel aus führt
die mit Absperrventil versehene Rohrleitung zum Windkanale am Cupolofen oder direkt
zu den Düsen.
Die Vortheile dieser Neuerungen, welche für Schmelzöfen aller Systeme angewendet
werden können, sollen darin bestehen:
1) daſs die Ofengase als Brennstoff nutzbar gemacht werden, wobei sie gleichzeitig
zum Erhitzen der Luft dienen, welche unter hohem Drucke zur Verwendung kommt;
2) daſs man den Schmelzprozeſs völlig in die Hand bekommt, indem man durch Regulirung
der Ventile nach Bedarf mit Ofengasen oder Luft oder beiden gemischt unter groſsem
oder geringerem Drucke blasen und mittels der Absperrvorrichtung das Gebläse
plötzlich anlassen oder abstellen bezieh. verstärken oder verringern kann.
Diese Einrichtung dürfte z.B. die Herstellung von weichem oder hartem Eisen in den
verschiedensten Variationen ermöglichen, da auſser den richtigen
Mischungsverhältnissen der Beschickung in erster Linie der richtige Ofengang bezieh.
die gleichmäſsige Regulirung des Schmelzprozesses mit gröſserer oder geringerer
Hitze für die Erzielung eines guten Eisens in den verschiedenen Härten maſsgebend
ist.
Dem Königl. Preuſsischen Berg- und Hüttenfiskus ist für
einen Apparat zur Gewinnung metallhaltigen Staubes aus den Gasen von Schmelz- und
anderen Oefen durch Condensation das vom 21. Februar 1888 ab gültige D. R. P. Nr.
45677 ertheilt worden. Bei dieser Einrichtung erfolgt die Kühlung durch
Wasserröhren, welche von oben in einen Thurm eingehängt sind und in denen das
Kühlwasser ab und auf steigend circulirt.
In den Fig. 18
und 19
bedeuten die Buchstaben a das Zuleitungsrohr des
Kühlwassers, b ein Stück des Deckels des Kühlthurmes,
c das Centralrohr, dd
die dasselbe umgebenden Röhren, e eine eiserne, in eine
entsprechende Oeffnung des Thurmdeckels passende, wasserdicht schlieſsende Scheibe,
in welcher die oberen Enden des Kühlröhrenbündels befestigt sind. Die Kühlröhren
sind etwa so lang zu nehmen wie die Höhe des Thurmes, und die einzelnen Bündel
derselben sind in der Thurmsection annähernd gleichmäſsig zu vertheilen.
Der Thurm A steht auf Säulen über einer etwas weiteren
Staubsammelkammer B, welche zwischen den Säulen mit
Blechscheidewänden versehen ist, um die Gase in der Kammer vor dem Austritte in den
Abzugskanal C noch circuliren zu lassen.
Die mit einer Klappe versehene Oeffnung D dient zum
Herausholen des in der Kammer sich sammelnden metallhaltigen Staubes.
Ein ringförmiger Wasserbehälter E kann auf dem
Kühlthurme angebracht werden, um das Kühlwasser aufzunehmen und mittels wagerechter
Röhren in die Trichter der Röhrenbündel zu vertheilen. Das Rohr h dient zur Ableitung des über dem Thurmdeckel aus den
Röhrenbündeln austretenden erwärmten Kühlwassers.
Durch das Rohr F münden die Ofengase in den
Kühlthurm.
Ein centrales drehbares Wind- oder Dampfrohr G, an
welchem eine Anzahl Querstutzen angebracht ist und welches etwa so weit wie die
Kühlröhren in den Thurm hinabreicht, dient dazu, von Zeit zu Zeit Wind- oder
Dampfstrahlen gegen die Röhrenbündel zu leiten, um diese von Staubansätzen zu
reinigen.
Das Prinzip, durch Abkühlung und Flächenvergröſserung groſse Mengen von Staub
niederzuschlagen, welches dem Apparate zu Grunde liegt, ist ein allgemein bekanntes,
so daſs hier lediglich die constructiven Mittel, welche zur Ausführung desselben
vorgeschlagen sind, in Betracht kommen.
Wie verlautet, hat sich der Apparat in Friedrichshütte in Schlesien im Kleinen gut
bewährt, so daſs gröſsere Ausführungen und Erweiterungen geplant werden.
W.
Koort.
Tafeln
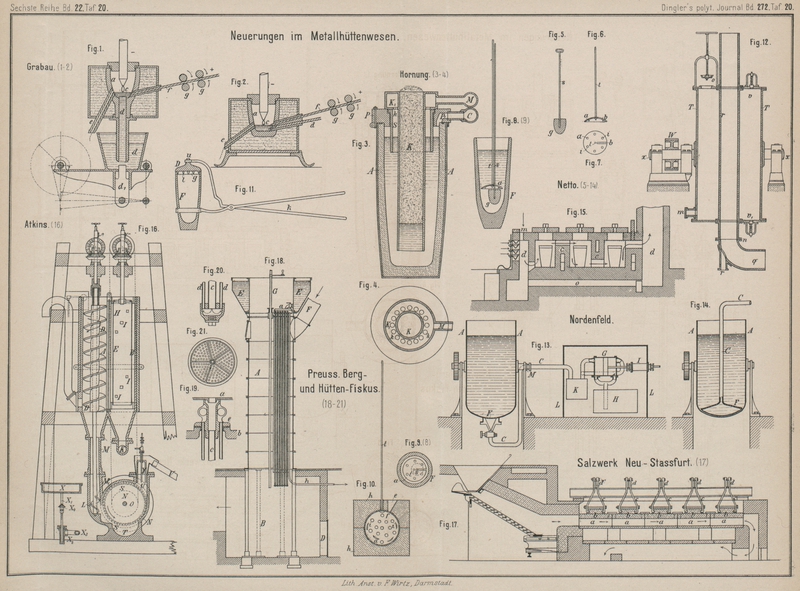