Titel: | Neuerungen in der Tiefbohrtechnik; von E. Gad in Darmstadt. |
Autor: | E. Gad |
Fundstelle: | Band 276, Jahrgang 1890, S. 256 |
Download: | XML |
Neuerungen in der Tiefbohrtechnik; von E. Gad in Darmstadt.
Mit Abbildungen auf Taf.
14.
Gad, Neuerungen in der Tiefbohrtechnik.
Olaf Terp in Breslau hat neuerdings ein Bohrverfahren
erfunden, durch welches er die kostspielige Diamantbohrmethode nicht nur zu
ersetzen, sondern auch in ihren Leistungen zu übertreffen hofft.
Es kommt in einer Diamantbohrmaschine anstatt der Diamantbohrkrone ein kupferner Schleifschuh mit einem Umguſs von Naxos Schmirgelmasse zur Verwendung. Da der Härtegrad
des Diamants 9, der des Schmirgels (Korund) 8 ist, so bleibt die Schmirgelbohrkrone
nur um einen Härtegrad hinter dem Diamanten zurück und ist somit im Stande, alle
übrigen Gesteinsarten zu durchbohren.
Die etwa 15cm langen Schleifschuhe sind so fest mit Schmirgelmasse umgössen, daſs sie eine sehr
starke Reibung und einen sehr hohen Druck aushalten können. Nach der erfolgten
Abnutzung des Schmirgels lassen sie sich sehr leicht und billig durch frische
Schleifschuhe ersetzen. Die groſse Schleiffläche bewirkt gröſsere Leistungsfähigkeit
und Dauerhaftigkeit im Vergleich zu den erbsengroſsen Diamanten. Die Schleifschuhe
sind mit Löchern zum Durchlaſs der fortdauernden Spülung, sowie mit Kernfängern zum
Fördern der Bohrkerne in der üblichen Art versehen.
Vorliegende Bohrproben von 12cm Durchmesser aus
Bunzlauer Sandsteinen, sowie aus festem Granit lassen auf eine gute
Leistungsfähigkeit des Bohrverfahrens schlieſsen. Fernere Versuche werden die
Brauchbarkeit desselben noch festzustellen haben. Das Verfahren könnte auch für die
Erweiterung und Verengerung der Bohrlöcher von hoher Bedeutung werden.
Gleichfalls eine Verbesserung der Drehbohrsystems mit Wasserspülung enthält das neue
„Saxl-Blumencron's Tiefbohrsystem“, über
welches der k. und k. Oberlieutenant Herr Karl Ritter v.
Blumencron am 23. Januar 1890 in der Versammlung der Fachgruppe der Berg- und
Hüttenmänner zu Wien Vortrag gehalten hat.
Der Meiſsel besteht aus der Deckplatte, dem Mittelstück und dem in
letzterem befindlichen und auswechselbaren Schneidemechanismus. Dieser beruht auf einem einfachen Systeme von
Stahlkeilen mit Nachnahmebacken, die unter dem Gestängedruck aus dem Mittelstück
hervortreten. Je nach der Gesteinsbeschaffenheit sind Meiſselschneide und
Nachnahmebacken aus bestgehärtetem Werkzeugstahl, oder für härteres Gebirge mit Korund, für sehr festes Gestein aber mit Diamant armirt.
Eine besondere Eigenthümlichkeit des Systems sind die doppelflügigen Schnecken, deren
Durchmesser nur um ein Geringes kleiner ist, als jener der Verrohrung. Unmittelbar
über dem Meiſsel rotirt die unterste Schnecke, und über dieser sitzen in der ganzen
Länge des Bohrloches von 5 zu 5m auſsen am hohlen
Bohrgestänge weitere Schnecken, welche zugleich als Verbindungsmuffen für die
Gestängetheile eingerichtet sein können. Diese Schnecken erfüllen einen doppelten
Zweck, nämlich eine exakte Meiſselführung, sowie die
sichere und schnelle Aufspülung des Bohrschmande. Die Verrohrung wird grundsätzlich
mit dem Niedersinken des Meiſsels nachgetrieben.
Wie dringend wünschenswerth eine Vervollkommnung der bestehenden Bohrverfahren ist,
um auch weite Bohrlöcher in hartem Gestein abbohren zu können, ergibt folgender Vorfall.
Die von Herrn Fauck am 1. Juli 1889 nach seinem
Freifallsystem im Kurgarten zu Teplitz zur Erschlieſsung von Thermalwasser begonnene
Bohrung (D. p. J. 1883 273
157) ist nach Erreichung einer Gesammttiefe von 22m zu einem vorläufigen Abschluſs gekommen.
Die Bohrung begann von einem 12m tiefen Schachte
aus mit 68cm Bohrlochsweite. Es trat sofort ein
harter Porphyr auf, welcher auf der einen Seite des Bohrloches solch
auſserordentliche Härte zeigte, daſs es trotz gutgeführter Freifallschere nicht
gelang, das Bohrloch von 10m Tiefe in das Loth zu
bringen.
Die Abnützung der 300k schweren Meiſsel, die mit
einem Fallgewicht von 1000k bei 1m Fallhöhe verwandt wurden, war eine derartige,
daſs sie nach Abbohrung von kaum 10cm neu
geschärft werden muſsten. Die Bohrleistung betrug 5 bis 16cm per Stunde. Während aber nach allen
vorhergegangenen Erfahrungen 2 bis 3 Meiſsel für eine ganze Bohrung ausgereicht
hatten, so waren bei dieser Bohrleistung von 10m
Tiefe bereits 6 Meiſsel völlig unbrauchbar geworden. Da das jedesmalige Schärfen
eines Meiſsels 4 Stunden in Anspruch nahm, so muſste üoch eine zweite Schmiede in
Gebrauch kommen.
Der Vertrag mit Herrn Fauck ist gelöst worden.
Dafür haben nun neuerdings die Quellenbesitzer einen amerikanischen Bohrtechniker in
Dienst genommen, der mit einer aus Amerika bezogenen pennsylvanischen Seilbohrmaschine die gestellte Aufgabe lösen will.
Es soll dieses Bohrloch auf dem Schloſsplatze 500m
tief mit nur 20cm Anfangsdurchmesser
niedergebracht werden.
Es ist hierbei zu bemerken, daſs die pennsylvanische Seilbohrmaschine, deren
Alleinherrschaft in dem milden gleichmäſsigen Gebirge Pennsylvaniens unbestritten
ist, in keiner europäischen Formation bisher Erfolg gehabt hat, und schwerlich im
Porphyr mehr leisten wird, als die viel wirksamere Freifallmaschine. Keinesfalls
läſst sich erwarten, daſs die Arbeit in 100 Tagen zur Vollendung kommt, wie es der
amerikanische Bohrtechniker verspricht.
Es entzieht sich der Beurtheilung, warum die Quellenbesitzer nicht die einen sicheren
Erfolg in Aussicht stellende Diamantbohrmethode angenommen haben, besonders da der
Anfangsdurchmesser von anfänglich 68cm bis auf das
geringe Maſs von 20cm herabgesetzt ist. Für diese
enge Bohrung würde der zur Verfügung stehende Betrag von 60000 ö. fl. sicher
ausgereicht haben.
Für leichtere Bohraufgaben bewahrt das Fauck'sche
Freifallverfahren indessen seine volle Bedeutung.
Fauck hat neuerdings unter dem Titel: „Neuerungen in
der Tiefbohrtechnik (Arthur Felix; Leipzig
1889)“, sowie in einem Geschäftsprogramm (Fauck: Wien 1890) die sämmtlichen zu seinem System gehörigen Apparate und
Geräthe zusammengestellt. Das Wichtigste ist bereits in D.
p. J. 1889 271 283 diesseits mitgetheilt.
Bemerkenswerth sind auſserdem noch einige neue Formen von Bohrthürmen.
Wichtiger ist sein neuer Schachtbohrer (Fig. 1), dessen
Construction sich an den selbsthätigen Freifallbohrer (D. p.
J. 1889 271 290; Taf. 14 Fig. 10) anschlieſst.
Die kleinen Meiſsel a sind mittels des Fauck'schen Doppelkeilverschlusses an dem Meiſselblatte b befestigt und bilden zusammen die
Arbeitsschneide. In dem Meiſselschaft c ist kreuzweise
zu der Längsrichtung der Arbeitsschneide ein Paar Nachschneider d, nach Art der in D. p.
J. 1883 271 282 beschriebenen, durch innerlich
angeordnete Spiralfedern in ihrer Arbeitslage gehalten.
Der obere Theil des Meiſselschaftes ist als Abfallstück der Freifallschere e eingerichtet. Die 4 Schienen f umschlieſsen das ganze Instrument zur Führung. Die Zuverläſsigkeit der
Führung wird durch die kreuzweise Anordnung von Arbeitsschneide und Nachschneide
wesentlich erhöht.
Das Fauck'sche Werk enthält noch die Beschreibung des
Erweiterungsbohrers von Lentz und Sorge in Baku (D. R. P. Nr. 9092
vom 27. August 1879), der besondere Beachtung verdient.
Die beiden Stahlschneiden a (Fig. 2) sind über dem
gemeinschaftlichen Drehbolzen b verlagert und ragen mit
Verlängerungen als Hebelsarme über den Drehpunkt hinaus. Das schwere guſseiserne
Gewicht c, frei aufwärts und abwärts verschiebbar, ruht
auf diesen Hebelsarmen auf. Das Gehäuse d umschlieſst und führt den ganzen
Mechanismus. Beim Einlassen ist der Druck des Gewichtes c auf die Hebelsarme gering und unschädlich, weil die Entfernung x y im Verhältniſs zu y z
klein ist, und Klemmungen nicht zu befürchten sind, sobald Winkel x mehr als 90° beträgt. Beim Heraustreten unter der
Verrohrung nimmt die Schneidevorrrichtung unter dem Drucke des Gewichtes c die punktirt gezeichnete Lage an, wobei die
anstoſsenden Flächen von Schneiden und Hebelsarmen feste Anlehnung finden. Nach
Beendigung der Bohrung bewirkt ein einfaches Aufziehen des Instrumentes, daſs die
Schneiden durch die Berührung mit der Verrohrung einklappen und das Gewicht mittels
der hochtretenden Hebelsarme anheben.
Vortheilhaft erscheint bei dieser Einrichtung, daſs die Stellung der Schneiden nicht
durch Federkraft, sondern durch einfaches Gewicht geregelt wird.
Die Schneiden lassen sich in verschiedenen Gröſsen auswechseln; auch ist der Apparat
leicht zur Wasserspülung einzurichten.
Eine sehr sinnreiche Seilbohrmaschine (Fig. 3) für Tiefen bis zu
200m hat W. C.
Wells in Ohio construirt und in Amerika unter Nr. 399459 vom 12. März 1889
patentirt erhalten.
Das Bohrgeräth ist der für das pennsylvanische
Seilbohren übliche Bohrmeiſsel.
Das Bohrseil a zeigt die besondere Eigenthümlichkeit,
daſs es gleichsam wie ein Gestänge aus einzelnen Theilen zusammengefügt wird. Die
Bohrung beginnt mit dem Bohrmeiſsel am Gestänge, das an den Wirbel b befestigt wird. Sobald das Bohrgeräth in den Erdboden
eingebohrt ist, fügt man das erste Bohrseilstück zwischen das als Schwerstange
dienende Gestänge uad den Wirbel, worauf die nöthige Verlängerung des Bohrseilzuges
durch Einfügung neuer Seiltheile erfolgt. Das Bohrseil kann aus Draht oder aus Hanf
gefertigt sein, nur muſs es eine gröſsere Stärke als das Stoſsseil c besitzen.
Das Querhaupt d ergreift mit zwei Klauen das Gestänge,
bezieh. das Bohrseil und läſst es vom höchsten Stande aus fallen, indem sich die
Klauen automatisch öffnen. Das Querhaupt ist mittels der Zugstange e mit dem Kurbelrade f
verbunden, welches auf der Welle g sitzt, auf deren
anderem Ende das Zahnrad h steckt. Der Excenter i auf der Welle k, welche
auch die Riemenscheibe l und das Schwungrad m trägt, kann durch den Hebel n auf das Zahnrad h eingestellt werden,
wodurch sich die Bewegung der Maschine auf das Kurbelrad f nebst Zugstange und Querhaupt überträgt.
Das Stoſsseil c führt zunächst über die eigenthümlich
eingerichtete und in dem Schlitz o an der Spitze des
Bohrmastes p bewegliche Seilscheibe q. Das Zapfenstück r wird
durch den Bügel s erfaſst, welcher seinerseits an dem
Riemen t hängt, der über die Stirn des federnd
construirten Rades u führt und an demselben befestigt
ist. Durch Wirkung dieses Federrades erhält das in Bewegung gesetzte Bohrgeräth eine groſse
Elasticität. Das Sperrrad v dient zur Regulirung der
federnden Bewegung. Von der Seilrolle q aus geht das
Stoſsseil nach der Stoſsseiltrommel w.
Die Nachlaſsvorrichtung beruht auf dem Zahnrade x am Vorderrande der Trommel w und dem darin eingreifenden Schneckenrade y.
Das Fördern des Bohrseils geschieht, indem das Zahnrad
z durch den Hebel n
mit dem Excenter i eingestellt wird, wodurch sich die
Bewegung der Riemenscheibe l auf die Seiltrommel w überträgt. Beim Einlassen des Bohrgeräthes tritt
event. zur Hemmung die Bremse a1 mit dem Fuſshebel b1 in Thätigkeit.
Auf der Löffelseiltrommel c1 ist das Löffelseil aufgewickelt, welches über eine seitliche Seilrolle
am Bohrmast führt und die Sandpumpe, bezieh. die Ventilbüchse trägt. Die Löffel
Seiltrommel ist hinten mit einer Friktionsscheibe verbunden. Die gemeinschaftliche
Welle k hat ein bewegliches Lager und kann mittels des
Hebels d1 an die Stirn
des Schwungrades m zur Aufnahme der Bewegung angedrückt
werden. Es ist dabei erforderlich, daſs man durch den Hebel n den Excenter i von den beiden Zahnrädern
h und z abstellt.
Der Hebel d1 steht
ebenfalls mit einer Bremsvorrichtung in Verbindung, die den Gang des Löffels regeln
kann.
Beim Bohren im milden Gebirge wird das Querhaupt d durch
eine Nachlaſsschraube ersetzt, die ganz wie bei der pennsylvanischen
Seilbohrmaschine eingerichtet ist, auch mittels des Krückels durch die Hand des
Bohrmeisters ihre Umstellung erhält.
Einen bemerkenswerthen Spülbohrapparat hat neuerdings
Herr Fr. W. Miller in Brooklyn, New York, erfunden und
darauf das amerikanische Patent Nr. 406457 vom 9. Juli 1889 erhalten.
Der Bohrschuh a (Fig. 4) ist ein hohles
Eisenstück mit einem linksläufigen Muttergewinde in der
Stufe der Spitze zur Aufnahme des Verbindungsnippels mit dem Bohrschlauch e, sowie einem rechtsläufigen Muttergewinde am oberen Theil.
Die Sandkammer b, ein eiserner Hohlcylinder, wird mit
seinem unteren Theil in das rechtsläufige Muttergewinde des Bohrschuhes
geschraubt.
Das Siebstück c findet durch eine gewöhnliche äuſsere
Muffe Anschluſs an den Bohrschlauch.
Der Bohrschlauch d führt durch alle diese Eisentheile
hindurch, und es werden von vornherein so viel Verrohrungsstücke e über den Bohrschlauch gezogen, als voraussichtlich zur
Verwendung kommen müssen. Die Druckpumpe f preſst das
Spülwasser durch den Bohrschlauch.
Um zu verhindern, daſs bei der Bohrarbeit das mit Bohrschmant gesättigte Spülwasser
nicht durch die Sieböffnungen in das Innere der Röhren dringt, sondern den Weg
auſserhalb derselben zwischen Rohr- und Bohrlochswand nach oben nimmt, findet eine Abliderung
oberhalb des Siebstückes durch die in Fig. 5 dargestellte Liderungsvorrichtung statt.
Der Bohrschlauch a wird zerschnitten, und das hohle Guſsstück b mit den Verbindungsstücken c in den Bohrschlauchenden befestigt. Der ausgekehlte
Ring d trägt den hohlen Gummiring e, dessen Umfang in ungespanntem Zustande den Raum bis
zur Innenwand der Röhre f nicht ausfüllt. Die in Gang
gesetzte Spülung füllt indeſs den Gummiring mit Wasser, da dessen Inneres mit dem
Inneren des Guſsstückes b in Verbindung steht, wodurch
der Raum zwischen Bohrschlauch und Verrohrung während der Spülung gelidert wird.
Nach Beendigung der Bohrung bleiben meist die Verrohrung mit Schuh, Kammer und Sieb
im Brunnen, während der Bohrschlauch entschraubt und ausgezogen wird.
In sehr origineller Weise ist bei dem neuen Tiefbohrapparat des Herrn H. K. Goodrich aus
Sherman in Texas, mit dem amerikanischen Patent Nr. 406898 vom 16. Juli 1889, die
Wasserspülung durch einen Strom von Wasserdampf, bezieh. gepreſster Luft ersetzt. Es
ähnelt dies Verfahren wesentlich der zufälligen Verwendung von Luftpumpung bei
geringem Wasservorrath, wie sich solche bei der im diesseitigen Bericht (D. p. J. 1889 273 156) bei
den für Crefeld ausgeführten Brunnenbohrungen ergeben hat.
Der Bohrmeiſsel a (Fig. 6) ist aus 3
Meiſselschneiden zusammengesetzt, so daſs der wagerechte Durchschnitt ein ☡ ergibt.
Das Hohlgestänge b wird aus der erforderlichen Anzahl
von Röhren luftdicht zusammengefügt. Das Gestänge ist nach dem Innern des
Bohrmeiſsels zu offen.
Der Wirbel c ist einerseits am Bohrseil d befestigt, welches über Rollen am Bohrgerüst nach der
Förderwelle e führt und nimmt andererseits die
Röhrenleitung f auf, die sowohl zu dem Dampfkessel g, als auch zu dem Preſsluftcylinder h führt.
Die Maschine i setzt den Bohrmeiſsel in stoſsende
Bewegung. Sobald eine angemessene Menge von Bohrmehl erzeugt ist, wird das Stoſsen
eingestellt, und aus dem Dampfkessel g durch den Hahn
k Dampf mit starkem Druck bis nach der Bohrsohle
gelassen, welcher das Bohrmehl bezieh. den nassen Bohrschmant kräftig zwischen
Rohrgestänge und Bohrlochswand zu Tage treibt. Der Hahn l dient zur Regulirung.
Wasserdampf eignet sich indeſs nur für geringere Tiefen, während für gröſsere Tiefen
Preſsluft zur Verwendung kommen muſs. In diesem Falle wird die gepreſste Luft aus
dem Luftkessel h entnommen, mit welchem das Leitrohr
f durch den Hahn m
verbunden wird.
Ein Regulirungshahn nach Art des Hahnes l ist alsdann
bei n anzubringen. Das Pressen der Luft findet in dem
Cylinder o durch die Maschine i statt.
Die Firma C. Bornet in Paris, rue Faraday 13, hat in der
vorjährigen Pariser Weltausstellung ihr sehr beachtenswerthes System von Gesteinsbohrmaschinen zur Ausstellung gebracht, das
auch in Deutschland unter Nr. 45603 vom 1. Dezember 1888 patentirt ist.
Diese Apparate sind in 4 Typen von wachsender Stärke vorhanden, doch beruhen alle auf
der eigenthümlichen federnden Druckregulirung (Fig. 7).
Die Bohrspindel a wird durch die Schraubenmutter b bewegt. Letztere hat in der Mitte die Stoſsscheibe
c, an die sich beiderseits je eine Feder d stützt, deren entgegengesetztes Ende gegen die
entsprechenden Kugellager e e1 drückt. Bei normalem Bohrwiderstande sichert der verstellbare Riegel f gegen Dehnung. Bei vermehrtem Bohrwiderstande aber
geht die Bohrspindel unter Zusammendrückung der Feder d
zurück und löst den Riegel f aus der Haltescheibe g aus. Dann dreht sich die Schraubenmutter auf der
Kugelbahn, bis bei nachlassendem Druck die Federn d die
Mutter wieder vorbewegen und den Riegel f an die
Haltescheibe g schieben.
Die gleiche Einrichtung beider Bohrspindelenden und die Anordnung von 2 Federgruppen
gestatten die Umkehrung des Bohrapparates.
Der Apparat wird in verschiedenen Gröſsen von etwa 35 bis 120k Gewicht mit Gestell, zu Preisen von 1u0 bis 1200
M. hergestellt.
Die kleineren Formen sind für Handbetrieb, die gröſseren für Preſsluft, bezieh.
Wasserdruck.
Eine andere in Paris, und zwar von der Firma Hanarte et
Balant, Mons, Belgien, ausgestellte Gesteinsbohrmaschine (Fig. 8) zeigt ein
besonders zweckmäſsig eingerichtetes Bohrgestell.
Die Bohrer a sind meist von denselben Formen, wie sie
schon bei den Tunnelarbeiten in St. Gotthard, Mont Cenis und Arlberg zur Verwendung
gekommen sind.
Das leichte stählerne Gestell b ist durch die Blockräder
c fahrbar gemacht und mittels der Stellschraube d am First und der Stellschraube e auf der Sohle vor Ort festgestellt. 2 Bohrmaschinen
f sind an dem mit äuſserem Schraubengewinde
versehenen Hinterpfosten g in wagerechter und
senkrechter Richtung verstellbar durch die Klemmvorrichtungen h gehalten. Der gleichfalls mit äuſserem
Schraubengewinde versehene Vorderpfosten i trägt
ebenfalls zwei Stellvorrichtungen k mit Seitenarmen l, so daſs eine Auflage des vorderen Theils der
Bohrmaschinen in allen erforderlichen Bohrrichtungen erreichbar ist. Die Preſsluft
wird dem Apparat durch das gemeinschaftliche Rohr m
zugeführt und durch die Schläuche n auf die einzelnen
Bohrmaschinen vertheilt. Der Vorschub läſst sich durch das Gewicht o an der Kette p in
Verbindung mit der Sperrvorrichtung q bewerkstelligen.
Es können 1500 Stöſse in der Minute erfolgen. Zum Abräumen der Berge vor Ort werden
die Bohrmaschinen aus dem Gestell entfernt, wodurch der nöthige Raum gewonnen wird.
Es genügen 2 bis 3 Mann zur Bedienung dieser Maschine nebst allen Nebenarbeiten vor
Ort.
Eine beachtenswerthe Vereinfachung des durch Preſsluft beweglichen Drehmechanismus einer Gesteinsbohrmaschine zeigt der
Apparat der Firma J. E. Powel, R. J. Powel and W.
Whitaker, Wrexham, Denbigh (Englisches Patent Nr. 18284 vom 14. December
1888) (Fig.
9).
Die Preſsluft tritt durch den Einlaſs a ein und wird
durch die Zugänge b an die Enden des Kolbens c geleitet. Die Zugänge sind geschützt in dem
schwalbenschwanzförmigen Guſsstück d angeordnet und
nach beiden Seiten gleichmäſsig, damit der Kolben der gleichmäſsigeren Abnützung
wegen umgekehrt werden kann. Die Kolbenstange e ist
durch die Metallliderung f mit der Gummieinlage g abgedichtet. Die Drehung des Kolbens wird in
bekannter Weise durch die geriefelte Stange h und das
Sperrrad i bewirkt. Um mehr Luftraum ohne Verlängerung
des Cylinders zu erhalten, ist dieser durch die Löcher k mit der Luftkammer l verbunden.
Im Anschluſs an die in D. p. J. 1890 275 124 aufgeführten Methoden zur Bohrarbeit im
schwimmenden Gebirge sei hier noch das Verfahren zum Vortreiben von Tunnels mit der
Vorrichtung von Hermann Vering in Hamburg (D. R. P. Nr.
45562 vom 22. April 1888) erwähnt (Fig. 10).
Der Ring a des Schildes b
wird durch Druckwasser, das in die sich an die Tunnelwand c lehnenden Pressen d gedrückt wird,
vorgepreſst. Zugleich erfüllt der im Cylinder e auf den
Schild b wirkende Druck von Preſsluft oder Druckwasser
eine Unterbrechung, indem man in dem Zuleitungsrohre f
ein Ventil öffnet. Dadurch bleibt der Schild b selbst
in seiner Stellung, während der Ring a mit dem daran
befestigten Cylinder e vorrückt, indem der durch den
Ring verdrängte Boden im Cylinder Aufnahme findet, wobei sich auch der Schild, um
dem verdrängten Boden Platz zu machen, nach rückwärts bewegen kann. Sobald der Ring
in Folge Beendigung des Hubes der Pressen d oder in
Folge Vergröſserung des Widerstandes des zu verdrängenden Bodens seine
Vorwärtsbewegung eingestellt hat, wird durch die Rohrleitung f Preſsluft oder Druckwasser in den Cylinder e geleitet, wodurch der im Cylinder befindliche Boden unter Druck
verdrängt oder gefördert, der Schild b aber an den Ring
a in seine Grundstellung zu demselben vorgerückt
wird.
Nachstehend seien die wichtigsten anderweitigen Erfindungen erwähnt.
Die sehr interessante neue Diamantschürfbohrmaschine mit elektrischem Betriebe von der Sullivan Diamond
Prospecting Co. ist diesseits in D. p. J. 1890
275 317 besprochen worden.
M. Harold, Lima, Ohio, hat eine Seilbohrmaschine
construirt (Amerikanisches Patent Nr. 407202 vom 16. Juli 1889), die das Stoſsseil
an einem senkrecht beweglichen Schlitten führt.
G. Pech, Storm Lake, Jowa, hat seine Drehbohrmaschine
mit weiter Schappe wesentlich verbessert und auf das alte Amerikanische Patent Nr. 315826 vom 14. April
1885 das Zusatzpatent Nr. 398649 vom 26. Februar 1889 erhalten.
Einen sehr sinnreichen Drehbohrapparat hat M. T.
Chapman, Aurora, Illinois (Amerikanisches Patent Nr. 409272 vom 20. August
1889) hergestellt.
Die dritte Ergänzung des im deutschen Reich zuerst unter Nr. 25015 vom 27. Februar
1883 patentirten Gefrierverfahrens von Fr. H. Poetsch
in Magdeburg (vgl. D. p. J. 1889 273 158 und 1889 272 257) betrifft ein durch D.
R. P. Nr. 50105 vom 9. Februar 1889 geschütztes Verfahren, in Schächten durch
Formationen von wechsellagernden festen und schwimmenden Schichten, durch letztere
je nach der Ausdehnung der Frostmauer von innen nach auſsen, erst engere Bohrlöcher
abzuteufen und diese demnächst zu erweitern.
Ein ferneres Verfahren ist Herrn Poetsch patentirt (D.
R. P. Nr. 47214 vom 26. September 1888), welches im Aufsaugen eines Kolbens mit
daran befestigtem Bohrgeräth im Bohrloche durch Wasser, Dampf, warme oder kalte Luft
und demnächst folgendem Fall des Bohrgeräths beruht. Bei Verwendung von kalter Luft
wird zugleich Gefrieren erzielt.
Ph. Forchheimer, Aachen, will nach dem D. R. P. Nr.
48020 vom 16. December 1888 beim Schachtbohren die Bohrsohle versumpfen und ohne
Hebung des Bohrgeräthes ausbaggern.
Einen eigenthümlichen Spülbohrer mit Bohrkopf hat B.
Andrews, New Orleans (Amerikanisches Patent Nr. 401404 vom 25. August 1888)
hergestellt. Ein ähnlicher neuer Bohrkopf ist von L. B.
Hart, Plaquemine, Louisiana (Amerikanisches Patent Nr. 411660 vom 24.
September 1889) erfunden.
Der neue Erweiterungsbohrer von M. T. Chapman
(Amerikanisches Patent Nr. 410311 vom 3. September 1889) beruht auf ähnlichem
Prinzip wie der oben beschriebene von Lentz und
Sorge.
H. W. Blaisdell, Yuma, Arizona, beabsichtigt nach dem
Amerikanischen Patent Nr. 409446 vom 20. August 1889 bei Brunnenbohrungen im
Schwimmsand Filtrirröhren innerhalb einer Verrohrung einzusetzen, dann die ersteren
mit Sand zu hinterfüllen und schlieſslich die Verrohrung, auszuziehen.
Einen transportablen eisernen Bohrthurm hat M. C.
Bullock, Chicago (Amerikanisches Patent Nr. 408652 vom 6. August 1889)
construirt.
In Bezug auf Oel- und Gasbrunnen sind Verbesserungen: Eine Oelpumpe von M. Lytle, Duke Centre,
Pennsylvanien (Amerikanisches Patent Nr. 406302 vom 2. Juli 1889); eine Gaspumpe von
E. A. Cook, Mc. Comb, Ohio (Amerikanisches Patent
Nr. 408652 vom 6. August 1889); und eine Liderung für Oel- und Gasbrunnenböden von
W. A. Donnel, Greensburg, Indiana (Amerikanisches
Patent Nr. 406162 vom 2. Juli 1889).
M. Wolf, Berlin, hat auf ein Verfahren zur Ermittelung
des Streichens der
Schichten in Bohrlöchern (vgl. D. p. J. 1888 270 163 und 1889 271 300) das
D. R. P. Nr. 47221 vom 27. October 1888 erhalten.
Mannigfache Formen von Gesteinsbohrmaschinen und deren Theilen sind in nachstehenden
Patenten enthalten: W. Walker, Saltburn by the sea,
York, England, Vorrichtung zum Bearbeiten der Ortsstöſse mittels Hohlbohrer (D. R. P. Nr. 50262 vom 2. Juni 1889); J. Mc Culloch, Minas di Rio Tinto, Huelva, Spanien,
Gesteinsbohrmaschine (D. R. P. Nr. 46691 vom 27. Mai 1888); A. B. Drautz, Stuttgart, Gesteinsbohrmaschine mit stoſsendem Werkzeug für
gasförmige Betriebsflüssigkeit (D. R. P. Nr. 48541 vom 25. October 1888); O. Gebhardt, Charlottenhof, Gesteinsbohrmaschine mit
Wassermotor und stehendem Werkzeug (D. R. P. Nr. 48659 vom 20. Februar 1889); D. Giese, Peoria, Illinois, Kohlenbohrer für
Handbetrieb (Amerikanisches Patent Nr. 406040 vom 2. Juli 1889); J. L Williams und Th. H. Williams, Shenandoah,
Pennsylvanien, Kohlen- und Gesteinsbohrmaschine mit Dampfbetrieb für die Rand-Drill Co. zu New York (Amerikanisches Patent Nr.
408878 vom 13. August 1889); A. J. Cooper, Duryes,
Pennsylvanien, Gesteinsbohrmaschine mit Handbetrieb am Handgestell (Amerikanisches
Patent Nr. 409772 vom 27. August 1889); E. A. Rix, San
Francisco, Californien, Gesteinsbohrmaschine mit Preſsluftbetrieb (Amerikanisches
Patent Nr. 410334 vom 3. September 1889); H. B. Utter,
Rockford, Illinois, Seilbohrmechanismus für Gesteinsbohrung (Amerikanisches Patent
Nr. 411078 vom 17. September 1889). Schrämmaschinen
sind: E. Caillet, Paris (D. R. P. Nr. 48854 vom 22.
März 1889) und H. C. Sergeant, New York (D. R. P. Nr.
49554 vom 8. Mai 1889 und Amerikanisches Patent Nr. 407258 vom 16. Juli 1889).
Letzterem Erfinder ist auch durch Amerikanisches Patent Nr. 407257 vom 16. Juli 1889
ein neues Gestell für Gesteinsbohrmaschinen geschützt.
Schlieſslich sei noch angeführt: R. Pauk, Felixdorf,
Niederösterreich. Gefahrloses Wegthun von Sprengschüssen durch Abkühlen der Gase in
einer mit Wasser gefüllten Hülse (D. R. P. Nr. 46444 vom 24. Juni 1888).
In Bezug auf ausgeführte Bohrungen ist zunächst zu melden, daſs der Bohrversuch bei
Sulz im württembergischen Schwarzwalde (D. p. J. 1889
273 155) bei einer Tiefe von 900m ergeben hat, daſs auch an dieser
hoffnungsreichsten Stelle des Königsreichs – wie gewöhnlich im Schwarzwalde – das
Rothliegende unmittelbar auf dem krystallinischen Grundgebirge aufliegt, und somit
die gehoffte Steinkohlenformation fehlt.
In der Stadt Alzey hat der Bohrunternehmer, Herr W.
Kramer, Gütersloh, unter Aufsicht des Herrn Stadtbautechniker Schmitt vom 19. September 1888 bis zum 19. Juli 1889
mit einfachem Spülbohrsystem und Handbetrieb 287m
tief gebohrt.
Die Bohrung wurde in Folge eines Gestängebruches eingestellt, ohne das gewünschte
Wasser gefunden zu haben. Die Kosten haben mit Verrohrung etwas über 11000 M.
betragen.
Neuerdings sind von dem Brunnenmeister Herrn G. Anger in
Magdeburg zahlreiche
Tiefbohrungen theils zur Bodenuntersuchung für Festungsbauten, theils zu
Nachsuchungen nach Wasser oder Braunkohle in der Provinz Sachsen 20 bis 100m tief ausgeführt. Das Bohrgeräth war meist
Drehbohrer am Gestänge im weichen Boden und Fabian'scher Freifallbohrer im festen Gebirge; beides mit Handbetrieb. Die
Kosten stellten sich auf 15 bis 50 M. für 1m
laufend.
Von den in Oberschlesien ausgeführten Bohrungen (D. p.
J. 1889 273 154) ist wiederum eine, und zwar bei
Knieczenitz auf ein starkes Kohlenflötz gestoſsen.
In demselben Kreise Rybnik wird nunmehr bei Belk von einer Gesellschaft neu gebohrt.
Zahlreiche Bohrungen im Stadtforst von Guben haben auf
100m Tiefe die gesuchte Braunkohle nicht in
abbauwürdiger Mächtigkeit gefunden.
Die Seefüllung im Grunewald bei Berlin mit Hilfe von 2
artesischen Brunnen ist gelungen.
In England wird zur Zeit sehr eifrig bei Dover nach
Steinkohle gebohrt, um festzustellen, ob die gefundenen Flötze abbauwürdig sind.
Die Bohrungen in Galizien auf Erdöl beginnen stellenweise eine gröſsere Tiefe als
300m zu beanspruchen. So muſste man bei Sloboda rungurska zur Erweiterung des alten, in der
Ergiebigkeit nachlassenden Feldes bereits 450m
tief bohren.
Bei Baku waren im October 1889 207 Brunnen im Betriebe,
71 Bohrungen im Gange, während 61 erschöpfte Werke leer standen. Auch dort erfordern
die Bohrungen bereits gröſsere Tiefe als bisher und zwar bis 300m. Daſs seit dem Mai 1889 fast alle Brunnen ihren
springbrunnenartigen Erguſs eingestellt haben und in Folge dessen gepumpt werden
müssen, hat nichts Bedenkliches, da nunmehr kein Naphta mehr verloren geht, wie es
früher der Fall war.
In Pennsylvanien beträgt die erforderliche Bohrlochstiefe schon oft über 1000m.
In Bezug auf die in dem diesseitigen Bericht (D. p. J.
1889 273 159) erwähnten Concurrenzversuche mit
Gesteinsbohrmaschinen System Frölich und Brandt auf den Mansfelder Gruben, ist neuerdings in der
Zeitschrift für das Berg-, Hütten- und
Salinen-Wesen im preuſsischen Staate 1889 37 295
eine sehr ausführliche Arbeit von Herm. Schrader unter
dem Titel: „Die Anwendung von Gesteinsbohrmaschinen beim
Mansfelder Kupferschieferbergbau“ erschienen. Dieser Artikel gibt
klare und erschöpfende Auskunft, wie sich unter den obwaltenden Gruben Verhältnissen
die nutzbringende Verwendbarkeit der Gesteinsbohrmaschine von ihrem ersten Versuch
an bis auf den heutigen Tag entwickelt hat.
Zunächst ist zu berücksichtigen, daſs die Handarbeit der Mansfelder Gesteinshäuer
stets auf einer hohen Stufe der Leistungsfähigkeit gestanden hat, die durch die
fortschreitende Verbesserung des Bohrgezähes, die Verdrängung des Sprengpulvers
durch Dynamit, die Einstellung geübter italienischer Tunnelarbeiter bis heut immer
noch gesteigert ist.
Im Durchschnitt werden zur Zeit bei 2m,5 Ortsweite
und 2m,2 Ortshöhe für einen Arbeitstag je nach den
örtlichen Verhältnissen aufgefahren:
im Conglomerat
0,6
bis
1m,
im Sandstein und thonigen Rothliegenden
1
bis
1m,4
im Flötz
1,4
bis
2m.
Trotz der hohen Leistungen beim Handbohrbetriebe wurden von 1865 an unausgesetzt
Gesteinsbohrmaschinen versucht, doch erreichte man mit diesen zunächst keine
zufriedenstellenden Resultate. Vor allem stellte sich die Maschinenarbeit im
Vergleich zur Handarbeit viel zu theuer, wenn auch ein bedeutender Zeitgewinn zu
erzielen war. Erst als in den 80er Jahren die geschäftlichen Verhältnisse auf
Anspannung aller Kräfte zur Massenförderung hindrängten, trat der durch Maschinen zu
erzielende Zeitgewinn als solch bedeutender Vortheil hervor, daſs dagegen die
Mehrkosten nicht mehr in Betracht kamen. Zudem gelang es mit der Zeit, diese Kosten
erheblich zu vermindern, vornehmlich nachdem der Bohrmaschinenbetrieb seitens der
Grubenverwaltung in eigene Regie genommen war. Man konnte zunächst die Erfahrungen
ausnutzen, die man in den Jahren 1883 bis 89 bei den Arbeiten der beiden
Bohrunternehmer gemacht hatte, in welcher Zeit mit der Frölich'schen Preſsluftmaschine 6808, 3m
laufend, mit der Brandt'schen hydraulischen Maschine
6609m laufend aufgefahren waren.
Man entschied sich für die Annahme der von Jäger
verbesserten Frölich'schen Preſsluftmaschinen. Bis zum
Mai 1889 ist es nun gelungen, im vollen – sogen. forcirten Maschinenbohrbetriebe
stellenweise eine 4,52 mal so hohe Leistung bei nur 11,71 Proc. höheren Kosten als
mit Handbohrbetrieb zu erzielen. Zugleich hat man erprobt, daſs man die Kosten bis
auf die des Handbetriebes herabmindern kann, wenn man sich bei langsamem
Maschinenbetrieb mit dem nur doppelten Bohrfortschritt des Handbetriebes
begnügt.
Neuerdings ist zur Schiefergewinnung eine Probemaschine der Duisburger
Maschinenbauaktiengesellschaft nach D. R. P. Nr. 47661 (s. D. p. J. 1890 275 394) im Versuch, welche sich
durch groſse Leichtigkeit (55k gegen 90k der Jäger'schen
Maschine) auszeichnet und sich zu bewähren scheint.
Tafeln
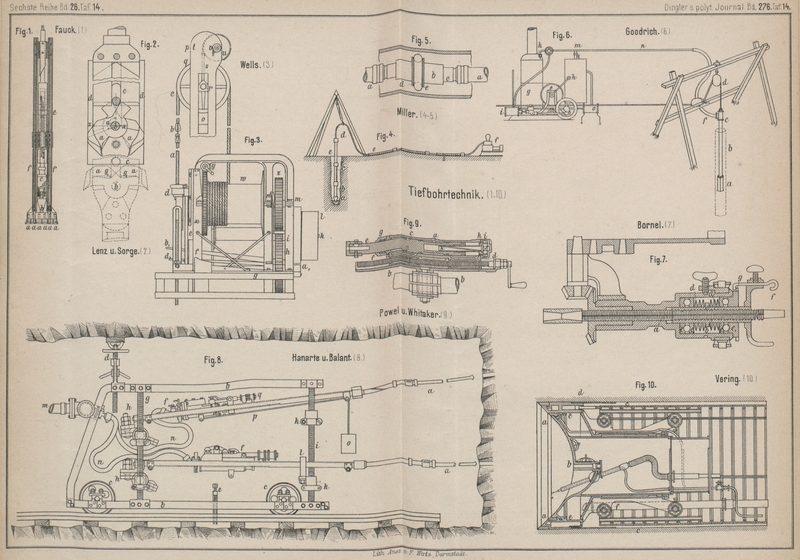