Titel: | Neue Holzbearbeitungsmaschinen. |
Fundstelle: | Band 277, Jahrgang 1890, S. 193 |
Download: | XML |
Neue Holzbearbeitungsmaschinen.
(Patentklasse 38. Fortsetzung des Berichtes S. 145
d. Bd.)
Mit Abbildungen auf Tafel
11.
Neue Holzbearbeitungsmaschinen.
Schränken und Schärfen von
Sägen.
Der Apparat von C. F. Hax in Kempten i.
B. (D. R. P. Nr. 48684 vom 6. Januar
1889) gestattet das gleichzeitige Sehränken zweier Zähne. Der Apparat ist in
Fig. 17
dargestellt.
An dem Gehäuse a sitzt ein Gelenk i, in welchem sich zwei Arme b1 und b2 bewegen lassen. An den unteren Enden der Arme
befinden sich zwei Stifte f1 und f2,
welche sich in einem Schlitz verschieben lassen, zum Zweck der engeren und weiteren
Stellung, je nach Zahnlänge. Neben diesen Stiften f1 und f2 sind zwei Stellschrauben g1 und g2 angeordnet, welche dazu dienen, je nach Bedarf die
Schränkung herzustellen. Ein Riegel, ein Hebel und ein Spannbacken e halten das Sägeblatt zwischen dem Gehäuse a fest. Mit einem Zug des Hebels nach vor- oder
rückwärts schiebt sich der Backen e zur Festspannung
oder zum Loslassen des Sägeblattes. Beim Gebrauch öffnet man die Arme b1 und b2, schiebt das Sägeblatt l
in das Gehäuse a, setzt den Stift h auf einen Zahn, spannt das Blatt mit den Spanntheilen
fest, drückt die Arme b1 und b2
zusammen, wodurch die Stifte f1 und f2 auf die Zähne einen Druck ausüben, so daſs der
eine Zahn nach links, der andere nach rechts gebogen wird.
Als Schränkwerkzeug bringt H. Kreeb in Göppingen,
Württemberg (D. R. P. Nr. 51714 vom 24.
September 1889), ein aus zwei Handgriffen bestehendes Geräth in
Vorschlag, dessen einer ein Schlitzblech zur Führung der Säge trägt, während der
andere an einem Winkel des ersten drehbar ist und ein so geformtes Eisen trägt, daſs
durch Hin- und Herdrehen des letzteren Handgriffes eine beiderseitige Schränkung der
Säge herbeigeführt wird.
Ein Schränkapparat von G. Wibel und Barth in Göppingen (D. R. P. Nr.
49110 vom 9. April 1889) ist in Fig. 18 dargestellt.
Das Sägeblatt A wird zwischen die ein Scharnier
bildenden Backen a und b
eingelegt. Haken c und Schraube d dienen zum Schlieſsen der Backen a und b. Je nach der Dicke des zu behandelnden Sägeblattes
wird die Schraube d angezogen oder nachgelassen. Die
Tieflage des Sägeblattes A wird begrenzt durch die
Stellung der Winkel e und f. Diese Winkel sind mit Schlitzen gh und
Fixirschrauben g1
h1 versehen und können
je nach der Breite des Sägeblattes höher oder tiefer eingestellt und fixirt werden.
Die Höhenlage bestimmen die mittels Stifte in Backen b
gelagerten runden Plättchen iK.
Im Lager mm1, welches
mit Backen b verbunden ist, liegt der Bolzen n, an welchem die Triebscheibe B befestigt ist, die wiederum. durch Kurbel D in Bewegung
gesetzt wird. Der Arm C, dessen Drehachse im Lager q sitzt, erhält durch den auf Scheibe B excentrisch sitzenden Stift p seine Bewegung.
Mit dem Arm C sind die Schränkplättchen r und s verstell- und
justirbar verbunden. Die Stärke der Schränkung ist vom Profil der Schränkplättchen
r und s abhängig.
Auf der Drehungsachse x sitzt auf verkeiltem Ring q[ der Stift
t fest; derselbe erhält mit Arm C von der Triebscheibe B
aus seine Bewegungen. Hierbei wird der Hebel u auf- und
durch eigene Schwere nieder bewegt, wobei, vermittelt durch Hebel v, der Schieber w vor und
zurück bewegt wird. Die Länge der Vorbewegung des Schiebers w bezieh. des Sägeblattes A (Schieber w greift in die Zähne ein) ist durch die Länge des
Stiftes t, die Länge der Rückbewegung (ohne Einfluſs
auf die Stellung der Säge) durch die Flügelschraube r1, welche auf das Lager q aufzuliegen kommt, bestimmt. Es läſst sich also durch
richtiges Einstellen der Flügelschraube r die Länge der
Vorbewegung des Sägeblattes genau bestimmen.
Die Wirkung des Stiftes t auf Hebel u wird durch die lose sitzende Rolle z vermittelt. Das Drehbolzenlager des Hebelwerkes u v w ist mit Lager m in
Verbindung gebracht. Der Hebelarm C kann auf dem
vierkantigen Ende der Achse x verstellt und durch
Schraube y fixirt werden. Der Schieber w macht seine Rückbewegung, bevor die Schränkplättchen
r oder s auf die Zähne
des Sägeblattes ihre bestimmte Wirkung ausüben, so daſs während des Schränkens der
Zähne das Sägeblatt vollständig ruhig steht.
Das Schränkwerkzeug von G. Wüste in
Remscheid-Bliedinghausen (D. R. P.
Nr. 48380 vom 9. Januar 1889), Fig. 19, besteht aus zwei
Handhaben A, die, in der Mitte durch den Bolzen B verbunden, ein Scharnier bilden. Einerseits sind an
diesen Stücken A die Backen C und andererseits die Backen D angebracht,
welch letztere durch die Schraube E verstellt und somit
auch CC enger oder weiter, je nach der Stärke der zu
setzenden Säge, gestellt werden können. An jedem Stück A ist nun die um den Bolzen a sich drehende
Backe b mit dem Zeiger d
angebracht, welch letztere sich an der Scala e
vorbeibewegen und durch die Stellschraube c sich
feststellen läſst.
Soll nun eine Säge geschränkt werden, so wird die Schraube c bezieh. der Zeiger d an der Scala e auf das angegebene Schränkmaſs gestellt, und bewirkt
dann die Backe b mittels des Endes f und die Backe C beim
entsprechenden Bewegen der Handhaben A die gewünschte
Schränkung. Alle Zähne der Säge müssen hierbei ganz genau gleich weit gesetzt
werden, da bei dieser Arbeit sich die Backen CC an die
Säge legen und ein weiteres Setzen der Zähne, als an dem Zeiger eingestellt, nicht
zulassen.
Durch Verstellen der Schraube E kann dieser Sägensetzer
auf jedes Blatt und
durch Scala e und Zeiger d
auf enge oder weitere Schränkung eingestellt werden.
Die in Fig. 20
dargestellte Maschine von J. H. Landis in Oerlikon,
Schweiz (D. R. P. Nr. 49714 vom 9. April
1889) dient zum Ausfräsen, Schärfen und Schränken von Bandsägeblättern
und beruht auf dem Grundsatz, daſs auf ein zahnweise geschaltetes Sägeblatt bezieh.
dessen Lücken eine universell lenkbare, genau einzustellende und von Zahn zu Zahn
selbsthätig sich hebende und senkende Schmirgelscheibe wirkt, wie auch hernach zwei
zur Schränkung entsprechend geformte Klemmbacken mit Gegenhaltern.
Der Ständer A trägt die Mechanismen, welche von der
Welle a angetrieben werden, die nach auſsen im Ständer
oder Support B gelagert ist und die Antriebrolle trägt.
Links und rechts seitlich vom Maschinenständer sind Ständer mit Rollen zur Führung
des zu bearbeitenden Sägebandes d angeordnet. Auf der
Welle a sitzt eine Scheibe a2, von welcher aus über die Leitrollen
e eine Antriebschnur e1 zur Rolle e2 der Schmirgelscheibe f geht, die in dem um die Achse drehbaren Bügel f1 gelagert ist. Um der
Schmirgelscheibe eine beliebige Schrägstellung ertheilen zu können, ist der Bügel
f1 drehbar
einstellbar zu dem mit Scala versehenen Kopf des Armes g.
Das Andrücken der Schmirgelscheibe an das zu bearbeitende Sägeblatt erfolgt durch das
Eigengewicht des Bügels und seiner Theile. Die Regulirung des Eindringens der
Schmirgelscheibe in das Blatt bezieh. in die Zahnlücke, sowie das Zurückgehen
derselben geschieht mittels des Supports h.
Fig. 20 zeigt
den Support in der Vorderansicht; derselbe trägt die verstellbare Gleitfläche i, auf welche sich der Schmirgelscheibenbügel mittels
der schiebbaren Führungsstange n stützt. Auf der
Hauptwelle a sitzt auch die Riemenrolle a3, deren Riemen auf die Rolle führt, die auf der
Welle k montirt ist, von welcher die Bewegung auf die
Achse l übertragen wird. Von der Achse l wird eine Bewegung abgeleitet mittels eines
Kurbelzapfens, der Stange m1, des Doppelhebels m2
m3 und der Zugstange
m4 auf den Support
h zur Deplacirung derselben in geeigneten
Momenten.
Der Vorschub des Sägeblattes erfolgt bei gehobener Schmirgelscheibe auf folgende
Weise: Auf der Welle l sitzt der Daumen; dieser bewegt
mittels Anschlages die Zugstange o2; festgeklemmt an obige Zugstange ist der
Gleitapparat p, welcher wiederum den Vorschieber trägt,
bestehend aus einer gekrümmten Stahlstange p1, die in die Zahnlücken eingreift. Die
Rückwärtsbewegung der Zugstange o2 bewirkt die Blattfeder q; eine Vergröſserung oder Verkleinerung des Hubes kann leicht erfolgen,
z.B. durch die Stellschraube o3; eine Regulirung des Vorschiebers p1 findet statt durch
die Schraube mit Gleitbacken p2.
Um beim Ausfräsen des Sägeblattes bezieh. bei der Bearbeitung des Zahnlückengrundes ein Schwingen
des Schmirgelscheibenbügels f1 um die Hauptwelle zu verhindern, ist die Stange r am Zapfen r0 eingehängt.
Das Schärfen der einen Seite der Zähne erfolgt in gleicher Art wie das Ausfräsen;
dasjenige der anderen Seite hingegen erfolgt entsprechend folgender Anordnung: Der
Support h kommt auſser (seiner auf intermittirender
Verschiebung beruhenden) Thätigkeit, indem derselbe mittels der Schrauben h1 am Maschinengestell
beliebig festgelegt wird; die Zugstange m4 wird aus m1 aus- und in einen ebenfalls vorhandenen festen
Zapfen r0 eingehängt. Dagegen wird die Zugstange r, die beim Ausfräsen dazu dient, eine Schwingung des
Schmirgelscheibengestelles zu verhüten, an einen Zapfen m des Hebels m2 angehängt, wodurch eine schwingende Bewegung des Schmirgelscheibenbügels
erzielt wird. Die Gleitschiene i am Support, die jetzt
also in Ruhe ist, verleiht dem Schmirgelscheibenbügel bezieh. der Schmirgelscheibe,
je nach der mehr oder weniger geneigten Lage von i, die
gewünschte Schwingung und somit den Sägezähnen ihre Schärfen in kleineren oder
gröſseren spitzen Winkeln. Der Vorschub des Sägeblattes erfolgt ganz analog, wie
beim Ausfräsen beschrieben.
Die Schränkvorrichtung erhält ihre Bewegung von der Welle l aus durch conische Räder, die im Verhältniſs von 1 : 2 übersetzt sind;
ein Daumen oder Excenterorgan wirkt in beliebiger Weise auf den zum Sägeblatt
senkrecht stehenden Schränkschlitten t, der die
Schränkkluppe t1 trägt,
Fig. 21.
Der Schränkkluppe t1
ist die feste Schränkkluppe t2 gegenüberstehend, aber um etwa eine Zahndistanz versetzt. Die Kluppen
können natürlich ausgewechselt werden, entsprechend der Zahnschiefe. Zwischen den
Stahlkluppen hindurch wird das Blatt d geführt.
Gegenüber t steht die selbstverständlich ebenfalls
feste Stirnfläche t0;
t1 preſst d an t0, während die Zähne oder Vorsprünge t1 und t2 die Blattzähne an
die (entsprechend den Stirnflächen der Vorsprünge ebenfalls abgeschrägten)
gegenüberstehenden Flächen t3 bezieh. t4
pressen. Um kleinere oder gröſsere Schränkung zu erzielen, werden die Preſsstücke
oder deren Werkzeugplatten t1 bezieh. t2
regulirbar gemacht. In Folge der Uebersetzung der Räder kommen die Werkzeuge oder
Kluppen t1
t2 nur zur Wirkung,
nachdem zwei Schaltungen von je einem Blattzahn erfolgt sind, dafür werden aber zwei
Zähne auf einmal geschrägt. Der Daumen oder das Excenter muſs ausrückbar sein, um
die Schränkbewegungen während des Ausfräsens und Schärfens nicht zu haben. Wenn ein
Daumen statt eines gewöhnlichen Excenters angewendet wird, ist für den Rückweg von
t eine Feder vorzusehen. Es könnten auch beide
Kluppenwerkzeuge tt1
und t0t2 von Excentern gegen
einander bewegt werden.
Vorschubvorrichtung für Schärfmaschinen von R. Hesse
und J. Patleich in Wien (D. R. P. Nr. 49373 vom 7. Mai
1889), Fig.
22.
Der Antrieb der Schärfscheibe A kann auf beliebige Weise
erfolgen: Nothwendig
ist, daſs der Ständer, in welchem sich die Achse der Schärfscheibe lagert, in einer
Führung verschiebbar ist, damit die Schärfscheibe bei Kreissägen an den Umfang
derselben angestellt werden kann. Auf der Rückseite der Schärfscheibe A ist eine Stahlplatte C
befestigt, deren vorderes Ende c in einer Ebene mit der
Scheibe liegt, während auf ihr anderes Ende c1 eine Stellschraube c2 einwirkt, so daſs der Platte jeder
beliebige Neigungswinkel zur Rückfläche der Schärfscheibe gegeben werden kann.
Es wird demnach, wenn das Ende c1 der Platte C von der
Rückfläche der Schärfscheibe so weit absteht, als die Zahnentfernung des Sägeblattes
beträgt, von der Platte C ein Druck auf den Zahn des
Sägeblattes ausgeübt und letzteres so viel weiterbewegt, daſs nach beendeter
Umdrehung der Schärfscheibe diese in die nächstfolgende Zahnlücke eingreift.
Damit das Sägeblatt durch die Platte C fortbewegt werden
könne, ist die Schärfscheibe mit einem Ausschnitt a1 versehen, welcher sich nahezu über die ganze
Breite der Platte C erstreckt.
Für Bandsägeblätter mit verschiedener Zahntiefe empfiehlt es sich, den Rücken des
Sägeblattes in eine verschiebbare Unterlage einzulegen, welche beim Eingreifen der
Schleifscheibe in die tieferen Zahnlücken sich senkt. Das Heben der Unterlage beim
Anlangen einer weniger tiefen Zahnlücke besorgt eine Feder, welche in eine
Führungshülse der Unterlage eingesetzt ist. Die Führungshülse ist sammt der
Unterlage verstellbar, wodurch das Anstellen des Sägeblattes an die Schleifscheibe
leicht geregelt werden kann. Diese Vorrichtung kann am Ständer des Schärfapparates
fest oder abnehmbar angebracht sein.
Eine Feile zum maschinellen Schärfen von Sägen mit unterfeilten Zähnen wird von der
Karlsruher Werkzeugmaschinenfabrik vorm. Gschwindt und Co. in
Karlsruhe (D.
R. P. Nr. 51934 vom 8. November 1889) angegeben.
Bei den Maschinen zum Schärfen von Sägeblättern, bei welchen die Hebung der Feile
nach Vollendung ihres Vorganges senkrecht zu einer über die Zahnspitzen gedachten
Linie erfolgt, war es bisher mit den gewöhnlichen Sägefeilen nur möglich, der
Zahnbrust einen rechtwinkligen Stand zur Zahnspitzenlinie zu geben. Die auf diese
Weise gezahnten Sägeblätter schneiden nicht so gut als die mit der unterfeilten
Verzahnung versehenen, bei welcher die einzelnen Zähne unterfeilt sind, deren Brust
mit der Zahnspitzenlinie einen stumpfen Winkel bildet. Um auf den
Sägeschärfmaschinen, deren Feilenträger sich beim Rückgang senkrecht zur
Zahnspitzenlinie hebt, die in Fig. 23 gezeichnete
Verzahnung ohne besondere Vorrichtung zum seitlichen Ausheben der Feile
herzustellen, dient diese Feile.
Der Querschnitt derselben kann derjenige der gebräuchlichen Sägefeilen mit
gleichseitigem Dreieck sein oder auch eine andere Figur bilden, je nachdem der Winkel,
den die Brust und der Bücken des vorhergehenden Zahnes mit einander einschlieſsen,
gewählt wird.
Das Eigenthümliche der Feile besteht darin, daſs dieselbe an der Spitze und an dem
gegenüberstehenden Ende Verlängerungen trägt deren Querschnitte mindestens so viel
kleiner sind, als das Maſs des Unterfeilens beträgt, so daſs die Feile, wenn sie in
ihren Endstellungen angekommen ist, sich wieder frei aus dem Blatt herausheben oder
in dasselbe hineinlegen kann, ohne die Zahnspitze zu berühren; wenn also die Feile
am Hubende steht, so muſs sich die Feile frei ausheben und c frei einlegen können. Das Mindestmaſs, um welches der Querschnitt der
Verlängerung vor dem Querschnitt der eigentlichen Feile zurücktreten muſs, ist d; damit aber bei einem Nachhauen der Feile die
Verlängerungen nicht auch nachgearbeitet werden müssen, macht man dieses Maſs
gröſser, ungefähr dd1.
Zum Glattziehen verschränkter Sägeblätter dient die in Fig. 24 dargestellte
Anordnung von C. F. Böhnhardt in Dresden (D. R. P. Nr.
48689 vom 15. März 1889).
Der Apparat besteht aus zwei eisernen Backen B1 und B2, welche nach oben rechtwinklig abgekröpft und
durch Schrauben s1 und
s2 mit einander
verbunden sind, zwei kleinen Walzen w1 und w2, welche durch Metallstücke m1
m1
m2 und m2 in der Kröpfung der Backen B1 und B2 derartig gelagert sind, daſs dieselben durch die
in den Backen befestigten Schrauben r1
r1
r2 und r2 zusammen- oder auseinandergestellt werden können,
einer Rolle o, drehbar auf einem Schraubenbolzen b, und einer Preſsschraube p. Die Metallstücke m1
m1
m2 und m2 sind entweder
rechteckig oder länglich oval in die Backen B1 und B2 eingelassen, so daſs dieselben beim Drehen der
Schrauben r vor oder zurück gehen, wobei sich die
Schrauben r entweder mit ihrem Bund u oder mit der aufgenieteten Flügelmutter f an die Backen B
anlegen.
Die Rolle o ist in der Art und Weise in einer Nut n1 in der Backe B1 und n2 in der Backe B2 verstellbar
angebracht, daſs der Bolzen b in einem Schlitz l der Backe B2 herauf oder herunter gestellt werden kann.
Die Backen B1 und B2 werden durch die
Schrauben s1 und s2 zusammen- oder
auseinandergestellt, wobei dieselben durch die Preſsschraube p auseinandergehalten werden.
Um die geschränkten Zähne eines Sägeblattes mit diesem Apparat gleichmäſsig zu
ziehen, stellt man zunächst die Backen B1 und B2 durch die Schrauben s1
s2 und p so aus einander, daſs man das Sägeblatt B mit dem unverzahnten Theil dazwischen hindurchziehen
kann; die Rolle o stellt man so, daſs, wenn der Rücken
des Sägeblattes auf derselben aufliegt, die Zähne z vom
Sägeblatt noch etwas über die Kröpfung der Backen B1 und B2 hervor, zwischen die Walzen w1 und w2 zu stehen kommen.
Die Walzen w1 und w2 werden durch die
Schrauben r1
r1
r2 und r2 so zusammengestellt, daſs dieselben gleichmäſsig
von der Mitte aus und
der Breite der Verschränkung entsprechend von einander abstehen, dann setzt man das
Sägeblatt mit dem Rücken auf die Rolle o auf und zieht
es durch den Apparat hindurch, wobei die zu weit geschränkten Zähne des Sägeblattes
durch die Walzen w1 und
w2 in ihre richtige
Lage gedrückt werden.
Hobelmaschinen.
Wird eine Welle von einem Riemen oder Seil (auch Räder) angetrieben, so erhält sie
von dem treibenden Mittel nicht allein eine drehende Bewegung, sondern auch
seitliche Drucke, wodurch die Welle eine excentrische Stellung annehmen kann. Da
aber die seitlichen Drucke nicht immer gleich sind, so verändert sich die Lage der
Welle in ihrem Lager fortwährend.
Um die Schwankungen in der Wellenlage an der Arbeitswelle zu vermeiden, wird dieselbe
nach dem Vorschlag von C. L. P. Fleck Söhne in Berlin
(D. R. P. Nr. 49210 vom 19. Februar 1889) so mit der Antriebswelle verbunden, daſs
sie von ersterer nur die Drehbewegungen erhält. Hierzu kann man mannigfache
Kupplungen verwenden. Z.B. werden beide Wellenenden ausgehöhlt und in dieselben ein
curvenförmig profilirtes Stück gelegt.
Während bei Hobelmaschinen, die mit Messerköpfen arbeiten, also mit Messern, deren
Schneiden während der Arbeit einen Cylindermantel beschreiben, Druckbalken und
Spanbrecher nur einen verhältniſsmäſsig schmalen Streifen zwischen sich freilassen,
war man bisher bei Scheibenhobelmaschinen gezwungen, selbst wenn je eine Druckwalze
unmittelbar vor und hinter die Scheibe gelegt wurde, ein groſses, mindestens dem
Durchmesser der Messerscheibe gleichkommendes Stück des bearbeiteten Brettes, und
zwar unmittelbar beim Werkzeug ohne Andruck zu lassen.
Um diesem Uebelstande bei Scheibenhobelmaschinen zu begegnen, hat B. F.
Stoltz in Berlin (D. R. P. Nr. 48863 vom 12. April
1889) die in Fig. 25 veranschaulichte
Einrichtung getroffen.
Zur Zu- und Abführung des Holzes werden in der Zeichnung Walzen e benutzt, doch kann ebenso gut die Zuführung des
Holzes mittels eines Wagens oder Schlittens, auf dem es festgespannt ist,
erfolgen.
Die Messerscheibe a, deren senkrechte Welle d im Gestell der Maschine gelagert ist und die
Riemenscheibe d1 trägt,
ist auf der unteren Seite mit der inneren Aushöhlung a1 versehen. In letzterer befindet sich
die halbringförmige Druckplatte b, welche an den Enden
der im Maschinengestell geführten Stangen b1 befestigt ist. Letztere werden durch die sich
gegen die Bunde b3
setzenden Schraubenfedern b2 niedergezogen, so daſs die Druckplatte b
innerhalb der Messerscheibe das Brett auf den Arbeitstisch niederdrückt und
Hohlliegen wie Schwankungen desselben fernhält. Zum Niederziehen der Druckplatte b kann auch an der Stelle der Federn ein Gewicht verwendet werden. Auch
kann man in die untere Fläche der Druckplatte b
Reibungsrollen einlassen.
Die obere Fläche der Messerscheibe a ist mit Rippen a2 ausgerüstet, welche
wie die Flügel eines Ventilators wirken.
Da sich dicht an den äuſseren Rand der Messerscheibe das Gehäuse c anschlieſst, werden die Hobelspäne von dem durch die
Rippen a2 erzeugten
Luftstrom fortgerissen und durch die Mündung des Gehäuses c herausgeschleudert.
Die im letzten Bericht besprochene Hobelmaschine, deren wagerecht arbeitende Messer
um eine stehende Welle umlaufen, ist von Th. Küpper in
Bonn (Zusatz D. R. P. Nr. 48690 vom 16. März 1889) wesentlich abgeändert worden,
siehe Fig.
26.
Das Hauptpatent enthält eine Hobelmaschine mit wagerecht arbeitenden Messern, welche
in geneigter Lage radial an den schrägen Rändern einer Scheibe befestigt sind und
mit einer Kante oder der ganzen Schneide das Werkstück abhobeln; um die abgehobelten
Späne abzuschneiden, werden bei vorliegender Einrichtung unter die Schneideflächen
der hier nicht radial, sondern excentrisch angeordneten Hobelmesser noch
segmentartig eingelegte Messer angebracht.
Die auf der senkrechten Achse a sitzende, beinahe flache
Hobeleisenscheibe b ist an ihrer Unterfläche mit
excentrischen und schräg eingeschnittenen Flächen versehen, auf welchen die Messer
d mittels Schrauben verstellbar befestigt werden,
so daſs durch die geneigte Lage der Messer d die
abgeschrägten Spitzen derselben wagerecht zu liegen kommen und mittels eines
wagerecht darüber gehaltenen Schleifsteins genau geschliffen werden, weil die Messer
d eine Kleinigkeit über den Rand m der Scheibe b
hervortreten; durch Anhalten eines Schleifsteins unten an die Scheibe b werden auch die anderen Schneidflächen der Messer
geschliffen, so daſs die Schneiden genau rund laufen.
Die sich unten an die Schneiden der Messer d mit ihren
Schneiden scharf anlehnenden schrägen Messer e werden
bis beinahe unter die Schneiden von der auf der Nabe der Scheibe b sitzenden Scheibe f
umhüllt; dieselbe ist mittels Schrauben g in ihrer Höhe
verstellbar, um die Messer e mehr oder weniger
freizugeben. Die Messer e rotiren mit den Messern d, sind mittels Schrauben am Rand m der Scheibe b
verstellbar befestigt und haben zum Zweck, die von den Messern d vom Holz abgetrennten Späne abzuschneiden und
wegzuschaffen, welche durch die Scheiben durchfallen.
Das Werkstück wird durch zwei oder mehrere Druckwalzen h
und i auf den Tisch gepreſst und seitlich geführt,
damit es beim Bearbeiten nicht ausweichen kann. Der über den Hobeleisen d angebrachte Deckel k
kann bei kleinen Maschinen auf der Achse a befestigt
sein und mitrotiren, bei gröſseren Maschinen wird derselbe zweckmäſsig mit den
Lagerständern der Druckwalzen h i fest verbunden und
nicht mitrotiren.
Sind die Schneiden der Messer abgenutzt und durch Schleifen verkürzt, so kann man
dieselben nachstellen; um während des Betriebes der Hobelmaschine einen verschieden
starken Span nehmen zu können, wird entweder die Welle a gehoben oder gesenkt, oder die Arbeitsplatte gehoben oder gesenkt.
In dem zweiten Zusatz D. R. P. Nr. 51123 vom 25. Juli 1889 ist die Messerscheibe so
angeordnet, daſs sie von oben das unter ihr hindurchgeführte Holz bearbeitet.
Eine Kehlmaschine zum Schneiden von Kehlleisten mit Vorrichtung zum Einschneiden von
Falzen wird von K. Weiser in Zeulenroda i.
S. (D. R. P. Nr. 49372 vom 30. April
1889) angegeben. Hinter der Messerwelle, welche oberhalb des Brettes die
Kehlungen hobelt, ist unter der Tischplatte eine in wagerechter und senkrechter
Richtung einstellbare Welle vorgesehen, welche mit Falzfräsern und Schneidscheiben
so ausgerüstet ist, daſs sie von unten die Falze einschneiden und gleichzeitig das
Brett in die einzelnen Leisten zerlegen kann.
Eine Schutzvorrichtung für Abrichthobelmaschinen ist nach dem Vorschlage von F.
Bock in Eſslingen (D. R. P. Nr. 49067 vom 11. April
1889) in Fig. 27 dargestellt.
Die Anforderung an solche Maschinen, daſs Hölzer von jedem beliebigen Querschnitt,
ohne vorheriges Verstellen einer Schutzvorrichtung und somit ohne Zeitverlust mit
gröſstmöglicher Sicherheit für den daran beschäftigten Arbeiter abgerichtet werden
können, gab die Veranlassung zu dieser Construction. Es ist deshalb der ganze
Apparat unter dem Hobeltisch angebracht, so daſs nur die Schieber c, welche die Hobelmesser zum Schütze decken, aus dem
Tisch hervorsehen.
Diese Schieber, welche sämmtlich gleiche Breite haben und in einem bestimmten Radius
derart gebogen sind, daſs die hervortretenden Theile die Messer gut decken, ohne an
denselben zu streifen, erhalten ihre Führung in einem zweitheiligen Gehäuse bb1, welches unter dem Tisch angeschraubt wird. Die Anzahl
der Schieber und folglich auch die lichte Weite des Führungsgehäuses bb1 hängen von der
Breite der Hobelmesser ab. Jeder Schieber ist unten mit einem Nocken n versehen und einzeln an einem entsprechenden
Scharnierstück s mit Klinke k und Feder f aufgehängt, während die
Scharnierstücke s sich um einen gemeinschaftlichen
Bolzen z, welcher am Führungsgehäuse b1 seine Befestigung
erhält, drehen können. Durch diese Aufhängung werden alle Schieber nach oben
gehalten. Wird nun ein Stück Holz auf dem Tisch vorwärts gegen das obere Ende der
Schieber geschoben, so lösen sich durch den Druck eine Anzahl solcher Schieber
entsprechend der zu hobelnden Breite selbst aus, wodurch diese in dem
Führungsgehäuse nach unten gehen und zugleich einen Hebel mit Gegengewicht nach
unten drücken. Der Druck des Hebels nach oben kann auſser durch das Gegengewicht
auch noch durch Spannfeder mit Flügelmutter regulirt werden. Verläſst das Holz die Oeffnung des
Tisches oder werden einer oder mehrere Schieber vom Druck frei, so werden letztere
sofort durch den Hebel in ihre ursprüngliche Lage gebracht und in die Klinken k eingehängt, so daſs die Messer alsbald wieder an den
freien Stellen gedeckt sind. Der ganze Apparat ist noch unten durch ein Blech t gegen Staub geschützt.
Bei der Fräsmaschine für geschweifte Hölzer von W. Heinrich in
Eſslingen (D.
R. P. Nr. 51930 vom 9. August 1889) wird eine Schablone als Träger des zu
führenden Holzes durch Vorschub walzen mit zur Fräsachse senkrecht stehenden Achsen
bewegt und durch einen Zapfen in einer festen Leitcurve geführt. Letztere ist aus
der Schablone in der Weise entworfen, daſs die Mittelpunkte der Schablonencurven
während ihres Durchganges unter den Fräsmessern stets in diejenige Ebene fallen,
welche durch die Fräsachse und die Achsen der Vorschubwalzen gelegt werden kann.
Die Patentschrift gibt auſser Zeichnungen der Maschine
Anweisungen zum Entwerfen der Schablone und Leitcurven.
Ein Fräskopf mit auswechselbaren Messern von F. G. A. Häser in
Bremen (D. R.
P. Nr. 48374 vom 8. December 1888) ist in Fig. 28 dargestellt.
Auf der Frässpindel a ist ein Kegel b mittels der Unterlegscheibe c festgeschraubt. Kegel b ist radial
geschlitzt. In dem Schlitz sitzen zwei Profilmesser d
(zum Vor- und Rückwärtsschneiden); dieselben werden durch die Zwischenlage e in ihrer Lage gehalten und beim Anziehen der Mutter
auf der Frässpindel durch die Scheibe e
festgeklemmt.
Die Abschärfung der Profilmesser ist nach innen gekehrt, um den Spänen Platz zu
bieten; das radiale Hinausfliegen der Messer beim Rotiren verhindern die beiden
Nasen f und g.
Der in Fig. 29
abgebildete, gleichfalls mit auswechselbaren Messern versehene Fräskopf von G. Heymeier und der Firma von Schmitz und
Co. in Bremen
(D. R. P. Nr. 49711 vom 24. Februar 1889) ist mit
einer Schutzvorrichtung ausgerüstet.
Die Fräser welle a, der sogen. Dorn, ist zur Aufnahme
der Fräser geschlitzt. In diesen Schlitz wird zunächst ein Schuh c aus sehr hartem Stahl eingesetzt, der mittels des
Zapfens b in einer entsprechenden Vertiefung der
Fräserwelle a sitzt und an seinen beiden Seiten mit
Anschlagnasen e versehen ist. Der Schuh c ist gegen radiale Verschiebung durch einen Zapfen b verhindert und dient zur Aufnahme und zum Festhalten
der Stahlmesser mm1. Zu
diesem Zwecke ist der Schuh c an seiner inneren Seite
bei c1 mit feinen
Riffelungen versehen, und die Messer mm1 sind in gleicher Weise geriffelt, um ein
Festhalten der Messer und ein möglichst feines Verstellen derselben gegen den Schuh
c zu ermöglichen.
Die Messer mm1 sind
derart eingerichtet, daſs das eine zum Fräsen bei Rechtsdrehung und das andere zum
Fräsen bei Linksdrehungen dient. Beide Messer mm1 liegen auf einander und werden durch eine bei m3 armförmig gebogene Platte w2 versteift. Diese Messer liegen in dem Schlitz der
Fräserwelle; den anderen Befestigungspunkt für die Messer bildet der Ring d, welcher über den Messern sitzt und bei d1 geschlitzt ist,
während die Messer bei e1
e1 ausgekehlt sind und
so eine Anschlagnase für den Ring d bilden. Die Messer
mm1 sind durch den
Schutzring f überdeckt, welch letzterer einen etwas
gröſseren Durchmesser, als der von den Messern beschriebene ist, besitzt, so daſs er
die Messer vollständig überdeckt.
Die Scheibe f ist mittels Unterlagsscheibe g und Mutter h
festgeklemmt. Der Ring f ist an der Innenseite mit vier
Nasen ii versehen, welche den Zweck haben, die Messer
seitlich zusammenzuhalten. Die Scheibe f, welche mit
der Unterkante nur etwas höher liegt als die Decke des zu fräsenden Holzes, dient
dem Arbeiter als Schutzvorrichtung und verhindert, da sie bei ff unterbrochen ist, die Uebersicht über die Messer
beim Arbeiten nicht.
Bei kleineren Messern, namentlich bei solchen, welche ganz versteckt im Holze
arbeiten, kann die Schutzscheibe f entbehrt werden.
Statt daſs die Messer durch die Scheibe f gehalten
werden, wird dann ein zweiter gezahnter Schuh gleich demjenigen c in die Schlitze der Fräserwelle geschoben und hier
der Schuh durch einen ähnlichen, wie Ring d
geschlitzten Ring gehalten. Ring b wird durch die
Mutter h befestigt. Der ersterwähnte Ring dient sodann
beim Fräsen des Holzes letzterem als Führung. Die Befestigung ist bei beiden
Ausführungsarten leicht und sicher zu erreichen und zu lösen.
Eine Maschine zur Herstellung von Kehlungen und Verzierungen auf Holz ist in der sehr
umfangreichen Patentschrift von C. L. Göhring in Alleghany,
Nordamerika (D. R. P. Nr. 50192 vom 19. December
1888) angegeben.
Die Muster und Verzierungen werden erzeugt, indem der Werkzeughalter gegen das
zugeführte Arbeitsstück in schwingende Bewegung versetzt wird. Letztere wird unter
Einschaltung einer Querverschiebung der Messerwelle von Schablonen aus
veranlaſst.
Schuhleisten-Copirmaschine von H. Höber
in Alfeld a. d. Leine (D. R. P. Nr. 51687
vom 13. Oktober 1888).
Alle seither benutzten Schuhleisten-Copirmaschinen haben den Nachtheil, daſs sie die
vorderen Zehenpartien der Leisten nicht oder doch nur zum geringeren Theil, und zwar
je nach der besonderen Façon des Modelles copiren können, und zwar aus dem Grunde
nicht, weil sie keine geeigneten Einrichtungen besitzen, welche solches ermöglichen
lassen, was daher zur Folge hat, daſs die Fertigstellung der Leisten an diesen sehr
wichtigen Stellen mittels höchst mühevoller Handarbeit beschafft werden muſs. Keine
Hand, selbst wenn sie durch das geübteste Auge unterstützt wird, ist im Stande,
derartige plastische Formen links- und rechtsseitiger Figuren so genau dem gegebenen Modelle
nachzubilden, wie es die Maschine vermag.
Das nothwendige Vordringen des Copirradkranzes bis zu diesen Punkten wird bei den
Maschinen durch die Spindel des Modellhalters bis zu einem gewissen Punkte, der
einestheils von der Dicke des Modellhalters, sowie anderentheils durchlas
Nichtvorhandensein eines der Dicke des letzteren entsprechenden Schlitzes im
Copirradkranze abhängig ist, begrenzt. Hieraus ergibt sich, daſs auch die zu
copirenden Leisten durch die rotirende Messerscheibe nur bis zu diesem bestimmten
Punkte copirt werden können.
Diese Nachtheile sollen vermieden werden. Fig. 30 zeigt die
Oberansicht einer Leisten-Copirmaschine mit den bekannten Theilen: der feststehenden
Straſse D mit den beiden auf dieser zwischen den
Punkten x und y (Fig. 31)
beweglich hergestellten und durch das Gestänge G mit
einander verbundenen Schlitten T und T1, von welcher T mit dem sogen. Copirrade C, und T1 mit
der rotirenden Messerscheibe M, welche beide gleiche
Durchmesser haben und mit ihren Achslinien in eine zur Straſse D parallele Linie l
zusammenfallen, versehen ist, sowie des Wagens E,
welcher sich mit der gemeinschaftlichen Achslinie m der
Spindeln der Spindelblöcke S und S1 und des Reitstockes
R, in wagerechter und paralleler Richtung zur
Achslinie l in dem Abstande von Linie n, jetzt nur bis annähernd nach m bewegt, derselbe aber sich ganz bis m
bezieh. dem Punkte x des Copirradkranzes C,
Fig. 31,
bewegt, wenn, wie es die Fig. 30 ergibt, der
Reitstock R mit der Spindel s und der Copirradkranz C mit einem Schlitze
versehen ist, wodurch eine vollständige Copirung der vorderen Zehenpartien des
Modelles M1 an dem in
den Leistenhalter s1 in
bekannter Weise einseitig eingespannten rohen Leistenholzes L bewirkt wird.
Die Arbeit des Copirens der Leisten nach dem Modell an den vorderen Zehenpartien ist
folgende:
Das Modell M1 wird
einerseits durch den Körner K der Spindel s und andererseits durch die klauenförmige Spitze der
Spindel des Bockes S getragen und durch die
Riemenscheibe S1 in
rotirende Bewegung versetzt, während das rohe Leistenholz in dem mit Einspannbacken
versehenen Klemmfutter s1 befestigt und durch die Riemenscheibe S1 in gleichartige Bewegung des Modelles gebracht
wird.
Die Seite B1 des
Copirradkranzes, Fig. 32, wird nun so gestellt, daſs dieselbe mit der äuſsersten Spitze
des Modelles abschneidet. Hierauf beginnt die Copirung des Modelles an der
äuſsersten vorderen Zehenpartie, und zwar in der Weise, daſs man zunächst das
Segment B mit der Hand oder einer anderen geeigneten
Vorrichtung in die Lage, wie Fig. 32 es zeigt,
zurückschiebt, das Modell, das rohe Leistenholz und die Messerscheibe in Umdrehungen
versetzt und dann die Spindel s – welche gleichzeitig
mit durch den Wagen E, der bekanntlich durch Feder- oder
Gewichtsdruck selbsthätig zwischen den Punkten n und
m,
Fig. 30, und
zwar je nach der besonderen Form des Modelles vor- und rückwärts bewegt bezieh. in
der Richtung gegen m gedrückt wird – in einen Schlitz
des Kranzes C hineingleiten läſst. Während dieser
letzteren Verrichtung hat sich die äuſserste Zehenspitze am Leistenholze bereits
gebildet, und beginnt hiernach die bekannte selbsthätige Fortbewegung der Schlitten
T und T1 in der Richtung von x
nach y, wobei im Beginn der gleichzeitigen Fortbewegung
des Copirradkranzes C der Schlitz desselben es
gestattet, daſs die Spindel s in dem letzteren, und
zwar in correspondirender Art mit den vorderen Zehenformen des Modelles zwischen den
Punkten x bis o,
Fig. 31, sich
vor- und rückwärts schiebt. Während dieser Verschiebungen wird nun das Segment B mit der Nase B1 zu Folge der Spannfeder D stets gegen den Körner K gedrückt und somit
der Schlitz an den Copirflächen des Kranzes von den Punkten x bis o stets geschlossen gehalten, wodurch
eine völlig richtige Copirung des Modelles auch an den vorderen Zehenpartien
erfolgen kann.
Ob hierbei nun der Copirradkranz feststehend oder drehbar (volles Rad) ist, bleibt
sich gleich. Nach vollendeter Copirung der vorderen Zehenpartie bezieh. dem
Verlassen der Spindel s aus dem Schlitze schlieſst sich
letzterer selbsthätig nicht nur von dem Punkte x bis
o, sondern auch bis zum Punkte z, und steht der weiteren richtigen Arbeit des
Copirradkranzes nichts im Wege.
Maschinen zur Fabrikation von Holzschuhen von Fd. Arbey et Fils, Paris. Auf der letztjährigen Pariser
Ausstellung bot die Firma wieder Gelegenheit, diese eigenartigen
Holzbearbeitungsmaschinen zu beobachten.
Drei verschiedenartige Maschinen sind es, welche bei der Massenfabrikation von
Holzschuhen zur Verwendung kommen. Auf der ersten erhält der Schuh seine äuſsere
Form, die zweite dient zum Aushöhlen derselben von der Ferse bis etwa in die Mitte
des Schuhes, soweit die Oeffnung des Schuhes reicht, und die dritte ist zum
Aushöhlen der Schuhspitze eingerichtet.
Die Maschine zum Façonniren und Schweifen der Holzschuhe bearbeitet je nach ihrer
Gröſse zwei, vier oder sechs Schuhe gleichzeitig. Man spannt die mit der Bandsäge
roh vorgeschnittenen Hölzer ähnlich wie bei einer Drehbank auf dem verschiebbaren
Arbeitstische der Maschine ein, so daſs sie in deren Längenrichtung parallel neben
einander liegen. Die neben einander liegenden Spindeln werden dann mittels conischer
Zahnräder und einer quer zu dieser liegenden Welle von der Antriebswelle der
Maschine aus in umlaufende Bewegung gesetzt, während gleichzeitig eine oder zwei in
der Längenrichtung des Werktisches liegende Schraubenspindeln diesen allmählich in
der Faserrichtung des Holzes vorwärts bewegen. Die Fräsmesser, deren natürlich für
jede Spindel bezieh. jeden Schuh eins vorhanden ist, sitzen auf einer senkrecht zu
diesen laufenden
Welle, welche in zwei um feste Achsen drehbaren und mittels Querstück und Zugstange
fest mit einander verbundenen Armen gelagert ist. Sonach vermögen die Fräsmesser
eine zweifache Bewegung zu machen, einmal ihre eigene umlaufende Bewegung und dann
diejenige der im Kreisbogen schwingenden Arme, welche nach Maſsgabe der den Schuhen
zu ertheilenden Gestalt durch eine guſseiserne Schablone beeinfluſst wird, wie auch
die Umdrehung der Hölzer selbst der Formgebung entsprechend eine ungleichmäſsige
ist. Wie die Firma Fd. Arbey et Fils angibt, braucht
eine solche Maschine je nach ihrer Gröſse zur Herstellung von sechs bezieh. vier
oder zwei Schuhen nur 10 bis 15 Minuten Zeit; dabei erhält man die Schuhe genau in
der gewünschten Gestalt, so daſs dieselben späterhin bloſs noch mit Glaspapier
geglättet zu werden brauchen. Diese Maschine eignet sich auch zur Façonnirung von
Gewehrschäften, Pistolenkolben, Radspeichen, sowie namentlich auch zur Erzeugung von
Schuhmacherleisten.
Der nach seiner äuſseren Form fertiggestellte Schuh wird nunmehr auf den Support der
ersten Aushöhlmaschine eingespannt. Diese hat groſse Aehnlichkeit mit einer
gewöhnlichen Senkrechtbohrmaschine. Eine nach vorn gekröpfte guſseiserne Säule trägt
die senkrechte Frässpindel nebst deren breiter Antriebsriemenrolle, welche mittels
halbgekreuzten Riemens von der Antriebsscheibe in Umdrehung gesetzt wird. Diese
sitzt nebst Fest- und Losscheibe und einer Seilrolle zum Betriebe eines kleinen
Ventilators auf einer Welle, deren Lager sich in einem am Hintertheil des
Maschinengestelles befestigten Doppelarm befinden. An der Vorderseite der Maschine
ist der Support angebracht, welcher durch Schrauben in beliebiger Höhe feststellbar
ist und einen von vorn nach hinten, sowie einen quer zu dieser Richtung beweglichen
Schlitten besitzt. In dem auf dem obersten Schlitten angeordneten Schraubstock
werden ein oder zwei Schuhe eingespannt und diese werden mittels zweier die
Schlitten bewegender Handhebel, dem Fortgang der Bearbeitung entsprechend, dem
Werkzeug dargeboten. Letzteres, ein an rotirender Spindel sitzender Fräser, wird
durch Niedertreten eines Fuſshebels auf das Arbeitsstück herabgesenkt, wie bei einer
gewöhnlichen Bohr- oder Fräsmaschine. Damit die bei der Bearbeitung des Holzes
entstehenden Späne das Werkzeug nicht verstopfen und dessen Bewegung nicht
erschweren, ist für die fortwährende Entfernung der abgeschnittenen Holztheilchen
gesorgt. Zu diesem Zwecke dient ein am Fuſse des Maschinengestelles angeordneter
kleiner Ventilator, dessen Flügel mittels Schnurgetriebe in schnelle Umdrehung
versetzt wird. Das Windrohr des Gebläses ist an dem Maschinengestell empor geführt
und richtet seine Mündung nach dem zu bearbeitenden Gegenstande, so daſs fortwährend
ein Windstrom gegen diesen geblasen wird, welcher kräftig genug ist, die
entstehenden Späne sofort zu entfernen.
Ist dann das Aushöhlen des hinteren Theiles der Schuhe bis zur Ferse erfolgt, so bleibt endlich
noch die Höhlung im vorderen Theile übrig. Das kastenförmige Gestell der hierzu
verwendeten Maschine trägt auf seiner Tischfläche einen mittels Handrad und
Schraubenspindel in wagerechter Richtung in einer Schlittenführung beweglichen
Ständer, mit dessen Vorderseite ein Rahmen zum Einspannen der Holzschuhe verbunden
ist. Der Rahmen ist um seine untere Querachse mittels Scharniere an dem Ständer
drehbar, bei welcher Bewegung der Rahmen an einer nach vorn gerichteten Handhabe
gehalten wird. Eine zweite seitlich angeordnete Handhabe gestattet auſserdem eine
beschränkte Senkrechtbewegung der Arbeitsstücke während des Aushöhlens. Hierzu
dienen die zu beiden Seiten befindlichen senkrecht stehenden Messer, welche in
rotirende Bewegung versetzt werden, worauf ihnen die Holzschuhe in der angedeuteten
Weise zur Bearbeitung entgegengeführt werden. Eine dritte senkrechte Welle, die ein
passend geformtes Schlichtewerkzeug trägt, dient zum Nacharbeiten der fertig
ausgehöhlten Schuhe.
Um ein Beispiel von der Arbeitsweise einer Fabrik für Holzschuhe und von der
Leistungsfähigkeit der in einer solchen verwendeten Maschinen zu geben, möge bemerkt
werden, daſs eine Anlage zur Erzeugung von täglich 200 Paar Schuhen auſser dem
Betriebsmotor nur 5 Maschinen nöthig hat, trotzdem die Arbeit durchweg mit Maschinen
verrichtet wird. Man braucht für die angegebene Leistung auſser der etwa 8pferdigen
Dampfmaschine eine Bandsäge, um die Hölzer in passende Blöcke zu zerschneiden, eine
zweite Bandsäge, um die Blöcke roh vorzuformen, eine Façonnirmaschine der
beschriebenen Art, um 6 Schuhen gleichzeitig die äuſsere Form zu geben, eine
Fräsmaschine, um den offenen Theil je eines Schuhes auf einmal auszuhöhlen, und eine
zweite Fräsmaschine, um die vordere Höhlung der Schuhe, je zweier gleichzeitig,
herzustellen.
Die Holzdrehbank von J. N. Beach in London (D. R. P. Nr.
48983 vom 11. August 1888) bearbeitet regelmäſsig und unregelmäſsig
geformte Holzgegenstände durch umlaufende auf das gleichfalls umlaufende Holzstück
einwirkende Messer.
Wie aus Fig.
33 zu ersehen, ist in dem Gestell A der
Maschine eine hin und her gehende Platte B zum Tragen
des Drehstahles und eine hin und her gehende Platte C
zum Aufnehmen des Holzes angeordnet. Die Platte B
gleitet auf drei Schienen b und trägt auf ihrer
Unterseite mehrere Zahnstangen, welche in Eingriff stehen und mit Hilfe von
Zahnrädern oder dergleichen in Bewegung versetzt werden, welche auf einer ein Rad
D tragenden Welle befestigt sind. Das Rad D ist gleichfalls mit dieser Welle fest verbunden;
daher wird jede Bewegung, welche dieses Rad in einer Richtung empfängt, auf Welle
und Bettplatte übertragen. Auf der Nabe des Rades D
ruht lose ein Schneckenrad F, welches seine Bewegung
von einer mittels eines Rades E in Drehung zu
versetzenden Schnecke G erhält. Die von dem Rade F ausgehende Bewegung übt jedoch nur eine Wirkung auf die
Welle und das Bett B aus, wenn das Rad F an die Nabe des Rades D
fest angeschlossen wird. Dies geschieht mittels einer Frictionsklaue D1, welche durch die
Nabe in eine Aussparung D2 des Maschinenrahmens geschraubt ist. Durch Drehen dieser Klaue wird das
Rad D nach dem Schneckenrade F gezogen und durch den Druck seiner Nabe auf der Innenseite der Nabe des
Schneckenrades bindet es dasselbe, so daſs, wenn dieses Bewegung durch das Rad E und Schnecke G erhält,
das Rad D gleichfalls in Drehung versetzt wird und mit
ihm das Bett B. Dieser Druck hört selbstverständlich
durch Drehung der Klaue D1 in entgegengesetzter Richtung auf. Das gröſsere Rad D dient zur Hervorbringung einer gröſseren Bewegung der
Platte B, während das kleinere Rad E die feinere Einstellung der Platte während der
Thätigkeit der Maschine bewirken soll. Das gröſsere Rad wird daher dazu benutzt, die
Schneidvorrichtung oder den Drehstahl in eine Lage zu bringen, damit er auf das Holz
einzuwirken vermag; das kleinere Rad E dagegen, welches
stets unter der Controle des Arbeiters steht, vermittelt die Bestimmung der Tiefe
des Schnittes.
Die Drehstahlspindel ist mit zwei Griffen h versehen,
mittels welcher sie leicht gehoben werden kann, wenn man sie in die Maschine
einsetzen oder aus derselben entfernen will. Diese Spindel wird von drei Ständern
a getragen, welche aus der Platte B ragen, und läuft in Lagern, welche in dem um ein
Scharnier drehbaren Lagerträger J ruhen, so daſs man
behufs Auswechselns der Schneid köpfe die Spindel sammt den Lagern herausnimmt. Auf
der Spindel ist eine Scheibe I befestigt, welche ihren
Antrieb von einem Riemen c empfängt. Der Schneidkopf
K ist auf der Spindel in einer solchen Lage
angebracht, daſs die Drehstähle, welche in den kleinen Schlitzen d untergebracht sind, demjenigen Theil des Holzes, auf
den sie einwirken sollen, gegenüberstehen. Dieser Schneidkopf besteht aus einer
beliebigen Anzahl von Scheiben und an jeder derselben sind ein oder mehrere Stähle
befestigt. Diese Scheiben können gleiche oder verschiedene Durchmesser besitzen und
durch leere Scheiben, d.h. solche ohne Schneidstähle, von einander getrennt sein.
Sämmtliche Scheiben werden durch eine Feder L gegen den
Bund am Ende der Spindel gedrückt. Natürlich hängt die Form des gedrehten Balusters,
Sesselfuſses o. dgl. von der Anordnung der mit Drehstählen versehenen und der leeren
Scheiben ab. Beim Bearbeiten von hartem Holze verschleiſsen die Stähle in kurzer
Zeit, so daſs man sie häufig erneuern muſs. Hierbei stellt sich jedoch der
Stillstand der Drehbank behufs Entfernung der Stähle aus dem Schneidkopf oder behufs
Entfernung des Schneidkopfes von der Spindel als ein sehr ernster Uebelstand heraus,
da dieser Vorgang gewöhnlich ½ bis ¾ Stunden und manchmal noch länger dauert.
Die eigentlichen Lager bilden einen Bestandtheil der Schneidkopfspindel, d.h. sie werden auf dieselbe
aufgeschoben, von ihr entfernt, nachgestellt und geschmiert, während die Spindel
nicht in der Maschine sitzt, indem jeder Maschine zwei oder mehr Schneidkopfspindeln
beigegeben sind und jede Schneidkopfspindel die ihr zugehörige Ausrüstung an
Schneidköpfen, Stählen und Lagern besitzt. Wird die Spindel in die Maschine
eingesetzt, so kommen die Lager auf derselben in den Lagerträger J, von welchem der Boden, eine Seite und der Obertheil
massiv sind, während die andere Seite von einem offenen Rahmen gebildet wird,
welcher durch ein Excenter M gehoben und gesenkt werden
kann, so daſs man denselben beim Herausnehmen des Lagers über die Zähne oder Ansätze
am freien Ende des oberen Theiles des Lagerträgers zu schieben vermag; diese offene
Seite fällt dann zurück und das Lager kann mit der Schneidkopfspindel entfernt
werden. Das Excenter M ist in dem betreffenden Ständer
a mittels einer Kurbel e drehbar, deren Ende einen Knopf trägt, welcher während der Arbeit von
einem an der Bettplatte B durch Schrauben befestigten
Klemmhaken f gehalten wird, da während dieser Zeit das
geringste Spiel in dem Lager oder dem Lagerträger unterdrückt werden muſs. Der
Lagerträger kann also in sehr kurzer Zeit geöffnet und das Lager und die Spindel
herausgenommen werden, indem man die Schrauben der Haken f lockert, um den Knopf der Kurbel e frei zu
machen, und hierauf letztere mit der Hand hebt. Das Excenter M hebt die offene Seite des Lagerträgers, so daſs dieselbe von den
Ansätzen am oberen Theil des Lagerträgers zurückgeklappt werden kann. Nachdem das
Oeffnen sämmtlicher Lagerträger vorgenommen, wird die Schneidkopfspindel mit ihren
Lagern sofort herausgenommen und eine neue an ihre Stelle gesetzt.
Die Holzplatte C erhält die nöthige Hin- und Herbewegung
in selbsthätiger Weise und läuft hierbei auf Schienen, welche in der Zeichnung nicht
dargestellt, aber derartig angeordnet sind, daſs die Platte die erforderliche
Bewegung ausführen kann, welche ihr in folgender Weise ertheilt wird. Durch einen
mit dem Motor verbundenen Riemen g wird die Scheibe N einer Welle i in Drehung
versetzt, welche nahe am anderen Ende das Kegelrad O
trägt, welches in ein auf der Welle j angeordnetes
Kegelrad O1 greift, um
die Drehbewegung auf das Holz zu übertragen. Die Welle i hat ferner am äuſseren Ende ein kleines Zahnrad k erhalten, welches durch ein Zahnrad k1 und ein zweites, nicht gezeichnetes Zahnrad mit
dem groſsen Zahnrad k2
einer Welle l in Verbindung gebracht ist. Letztere
lagert im Gestell und bethätigt eine Curvenscheibe P,
welche auf einen Winkelhebel Q wirkt, um der Holzplatte
eine hin und her gehende Bewegung zu ertheilen.
Das Holz ist zwischen einem Futter m und einem Reitstock
n eingespannt, welcher in bekannter Weise mittels
einer durch ein Rad R bethätigten Schraube vorgeschoben
wird. Das Futter m wird mittels eines Schneckenrades
S in Drehung versetzt welches auf dem äuſseren Ende desselben
angeordnet ist und seine Bewegung von einer Schnecke empfängt, die sich auf der
Welle j befindet. Wenn die Holzplatte sich unter der
Einwirkung der Curvenscheibe P hin und her bewegt, um
die gewünschte Unregelmäſsigkeit in der Gestalt des Holzes zu erzielen, so wird das
Schneckenrad S mit der Holzplatte vor- und rückwärts
bewegt. Damit nun auf die Schnecke Druck nicht ausgeübt oder das Rad S bei der Hin- und Herbewegung auſser Eingriff mit
derselben gebracht wird, versieht man die Welle j mit
einem Keil, mittels dessen die Schnecke S1 mit der
Welle; nicht allein fest, sondern auch gleitbar verbunden wird, um sich der
jeweiligen Stellung des Rades S anzupassen.
Die Zahl der Seiten, welche das Werkstück bei der Bearbeitung erhält, hängt von dem
Verhältniſs der Umdrehungszahl des Werkstückes zur Zahl der Hin- und Herbewegungen
der Holzplatte ab. Ist beispielsweise das Verhältniſs der Zähnezahl des Rades k und k1 derart, daſs die Holzplatte vier Bewegungen macht,
während das Holz sich einmal dreht, so erhält das Holz durch die Drehstähle vier
Schnitte bei jeder Umdrehung und erhält dem zu Folge annähernd eine quadratische
Gestalt. Bringt dagegen die Holzplatte bei jeder Drehung des Werkstückes dieses
zweimal an die Stähle, so erhält man ein Oval; ist das Verhältniſs 1 : 1, so erhält
man wie bei einer gewöhnlichen Drehbank einen Kreis, da der Verlust in der einen
Richtung durch den Gewinn in der anderen Richtung ausgeglichen wird und das Ganze
auf dasselbe hinauskommt, als ob die Holzplatte feststünde. Bringt die Holzplatte
das Werkstück mehr als viermal an die Stähle, während es sich einmal dreht, so
erhält man natürlich eine entsprechende polygonale Gestalt. Dieser Theil der
Vorrichtung controlirt demnach lediglich die Zahl der dem Holze zu gebenden Flächen,
jedoch nicht die Concavität, Convexität oder Ebenheit der Flächen. Die Curvenscheibe
P dagegen hat den Zweck, das harmonische
Zusammenspiel der Holzplatte, des Holzes und der Stähle derartig zu reguliren, daſs
man dem Holze concave, convexe oder ebene Seiten ohne Rücksicht auf die Zahl der
letzteren geben kann. Dies wird durch die der Curvenscheibe gegebene Gestalt
bewirkt, und innerhalb gewisser Grenzen bestimmen die Tiefe der Aussparungen und die
Höhe der Ansätze der Curvenscheibe die Krümmung der Seiten, welche am Holz
hervorgebracht werden. Natürlich erhält man, wenn die einspringenden Winkel in der
Curvenscheibe so scharf sind, daſs der rotirende Stahl in das Holz nicht so scharf
eindringen kann, im Holze nur annähernd diese einspringenden Winkel. Die
Curvenscheibe P sitzt auf der Welle l und wird von derselben gedreht. Die Führungsfläche
der Scheibe wirkt auf eine kleine Rolle p, welche lose
auf dem Winkelhebel Q ruht. Das obere Ende des
letzteren ist starr mit einer im Gestell A gelagerten
Welle q verbunden und ertheilt der Holzplatte C unter der Bettplatte B
durch die stellbare, geschlitzte Kurbel T, welche an
dem Ende der Welle q angebracht ist, Bewegung. Die
geschlitzte Kurbel ist mit einem Blocke v verbunden, welcher
in derselben auf und ab gleitet und weicher in irgend einer Stellung durch eine
Mutter t gehalten wird, um die Stärke der Bewegung,
welche der Holzplatte ertheilt werden soll, zu regeln. Der Block v ist mit der Holzplatte C
durch eine Stange v1
angeschlossen, welcher unter der Bettplatte B hergeht.
Wenn der Gleitblock v mit der Kurbel T im Mittelpunkt verbunden ist, so wird die Holzplatte
natürlich keine Bewegung erhalten, da die Kurbel um den Block v einfach herumgeht, ohne ihn zu bewegen. Die Gröſse
der Bewegung der Holzplatte hängt daher von dem Abstande ab, in welchem der Block
v vom Mittelpunkt der Kurbel befestigt ist. Am Ende
der Welle q befindet sich eine zweite Kurbel, welche in
der Zeichnung durch die Triebscheibe N verdeckt ist und
in ähnlicher Weise mit einem Blocke am anderen Ende der Holzplatte verbunden ist.
Eine Rolle p ruht frei auf der Leitfläche der
Curvenscheibe P und wird durch das Seil V an dieselbe angedrückt. Dieses Seil ist am unteren
Ende des Winkelhebels Q angebunden, geht um die Scheibe
r, die am Boden aufgeschraubt ist, durch das
Maschinengestell hinauf und über eine an der Decke befestigte Scheibe (welche in der
Zeichnung nicht dargestellt ist) und trägt ein Gewicht, welches nicht nur
hinreichend schwer ist, um die Holle p stets gegen die
Curvenscheibe P zu drücken, sondern auch um die
Maschine vor Stöſsen zu bewahren, welche beim schnellen Gange eintreten könnten.
Der Façondrehapparat von H. Forstmann in Cöln (D. R. P. Nr. 51842
vom 21. September 1889) kann auf die Wangen einer gewöhnlichen Drehbank
aufgespannt werden. In einer gegen die Achse des umlaufenden Arbeitsstückes
geneigten Lage werden durch Schrauben drei Messer nach einander vorgeschoben. Das
erste bewirkt das Vorschruppen, das zweite arbeitet die Form aus, während das dritte
nachschlichtet. Zum Schluſs gelangt noch ein Polirpolster zur Wirkung.
Tafeln
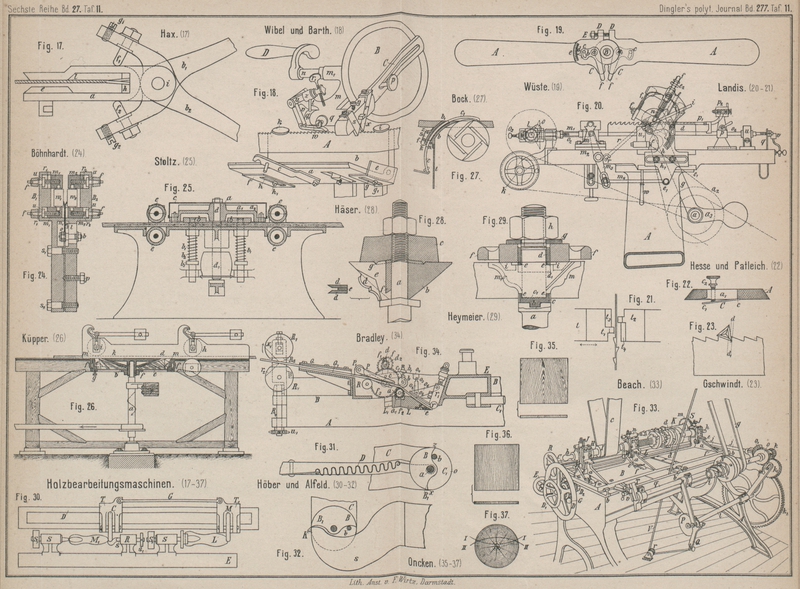