Titel: | F. G. Kreutzberger's Fräserschleifmaschine. |
Autor: | Pregél |
Fundstelle: | Band 278, Jahrgang 1890, S. 198 |
Download: | XML |
F. G. Kreutzberger's Fräserschleifmaschine.
Mit Abbildungen auf Tafel
14.
Kreutzberger's Fräserschleifmaschine.
Eine wohldurchdachte Maschine zum Schleifen jeglicher Fräsewerkzeuge, Reibstähle und
gewundener Bohrer hat Kreuzberger, Direktor der
Artillerie-Werkstätten in Puteaux gebaut, deren Beschreibung
nach Revue générale, 1890 Bd. 4 Nr. 5 * S.
33, folgt:
Gerade Cylinderfräser, einfache und doppelte Kegelfräser mit scharfem oder
kreisförmig abgerundetem Uebergang, überhaupt alle Fräserarten, deren
Formquerschnitt mit Kreisen oder Geraden begrenzt ist, können regelrecht, Zahn um
Zahn ohne Schwierigkeiten nachgeschliffen werden, während zum Schleifen der
Formfräser Schablonen verwendet werden müssen, die je nach der Formentwickelung des
Fräserquerschnittes entweder bei rechtwinkeliger Schlittenverschiebung oder bei
Drehung der Tischtheile zur Mitwirkung gelangen. Im ersten Falle findet eine
einfache (orthogonale) Uebertragung der Berührungstellen statt, im zweiten Fall
dagegen erfolgt eine Uebersetzung zwischen Formschiene und Fräserkante bei einer
günstigeren Lage des Schleifrades zur schärfenden Zahnschneide, weshalb diese Art
Schablonenführung bei stark ausweichendem Formquerschnitt vortheilhafteste
Verwendung findet.
Die Maschine zum Fräserschleifen (Fig. 1 bis 4) besteht aus einer
Tischplatte A mit entsprechend hohem Standfuſs, aus dem
Triebwerkständer B für das Schleifrad und dem
Schlittenwerk F bis K mit
den Einspanntheilen MNO für das Fräsewerkstück.
Das im Ständer B lagernde Triebwerk enthält auf der
ersten Welle D Fest- und Losscheibe X und X1 und die Stufenscheibe Y finden erforderlichen Wechsel der Umlaufszahlen, ferner auf der
Zwischenwelle z die zugehörige Stufenscheibe y und die auf w wirkende
Antriebscheibe Z, und endlich im seitlich abgekröpften
Vorderarm T (Fig. 4) das Klemmlager für
einen kurzen Zapfen, auf welchem die Riemenrolle w
frei aufläuft, während die Schleifradspindel x an die
Rolle w leicht beweglich angekuppelt ist. Durch diese
Anordnung wird die Schleifradspindel x vom Riemenzug
entlastet und das so wichtige Rundlaufen derselben gesichert.
Auch ist der Wechsel der Schleifräder in der Weise erleichtert, daſs die
verschiedenen Schleifräder nicht unmittelbar auf die Spindel x aufgeschoben, sondern durch Vermittelung eines Zwischenstückes (Fig. 5)
aufgesetzt werden, wodurch der Rundlauf an Genauigkeit gewinnt. Jedes in Verwendung
befindliche Schleifrad ist auf einen solchen Hilfszapfen (Fig. 5) centrisch
aufgespannt und jederzeit gebrauchsfertig bereitgestellt. Vermöge des im Mitteltheil
des Kegelzapfens eingeschnittenen cylindrischen Gewindstückes erfolgt die
Festklemmung, wie Centrirung auf die Spindel w rasch
und sicher. Die Riemengabel u gleitet mit Hilfe eines
angegossenen Klemmringes v auf der äuſseren Lagernabe,
eine Anordnung, welche ebenso einfach als bequem zur Einstellung ist.
Der zweite sehr bemerkenswerthe Haupttheil dieser Maschine ist der Aufspannsupport
für das zu schärfende Fräserwerkzeug.
Während das Schleifrad in festgelegter Lagerung läuft, sind sämmtliche Einstell- und
Arbeitsbewegungen in den Support verlegt, deren Kreuz- und Rundschlitten mit
Noniustheilungen versehen sind, welche Ablesungen bis zu 0mm,1 zulassen, wobei die Einrichtung getroffen
ist, daſs der Nullpunkt des unteren Stellschlittens G
mit der geometrischen Achse des Drehstückes L und mit
der Achsenebene der Schleifradspindel zusammenfällt, während die Nullpunktstellung
des Kreistisches L die winkelrechte Stellung der
Schlittenbahnen H und J
bestimmt.
Hierdurch wird nach erfolgter vorheriger Abmessung des Schleifrad- und
Fräserdurchmessers jede noch so feine Einstellung und Abschärfung ermöglicht.
Der Support besteht aus dem Untertheil F (Fig. 1 bis 3), welcher
mittels eines einzigen Schraubbolzens an die Tischplatte A befestigt wird, darauf verschiebt sich das Kreuzstück G vermöge einer feingeschnittenen Schraubenspindel b, welche durch Mitverwendung der kleinen
Kreistheilscheibe g Verschiebungen bis 0mm,1 anzeigt.
Eine Theilschiene c, welche an den Nonius d spielt, gibt die Einstellung bezieh. die Entfernung
des Nullpunktes dieser Theilung vom Schleifradmittel in positiver und negativer
Richtung an. Auf der oberen Bahn von G wird der
Schlitten H mit der Schraubenspindel i in rascher Gangart bewegt, was in sinnreicher Weise
dadurch ermöglicht wird, daſs diese Spindel zur Hälfte mit rechts, zur anderen
Hälfte mit linksgängigem Gewinde versehen ist. Indem nun die entsprechenden Muttern
im Schlitten H und im festgelegten Kreuzstück G angebracht sind, findet bei einmaliger Drehung dieser
Spindel i eine Schlittenverschiebung H von der doppelten Steigungsgröſse der Spindel statt,
was in Anbetracht der Selbsperrung dieser Bewegung von Wichtigkeit ist.
Zur Hubbegrenzung dienen die Klötzchen R, welche an eine
vorstehende Seitenleiste von H geklemmt werden, deren
Stellschrauben an einen festen Ansatz von G
anschlagen.
Auf dem Schlitten H ist eine kreisrunde Auflage
angegossen, zu welchem ein Drehstück mit gerader Führungswange L gehört. Beide Theile werden vermöge eines Klemmhebels
k (Fig. 1), welcher an einer
vorstehenden Ringleiste der Auflage H ansetzt, mittels
einer Griffschraube k1
in jeder beliebigen Winkelstellung festgestellt, während bei Lösung dieser Schraube
eine freie Drehbewegung ermöglicht wird, die durch ein stellbares Klemmstück f die etwa gewünschte Hubbegrenzung erhält. Dieses
Klemmstück f befindet sich ebenfalls auf der
vorerwähnten Ringleiste, während der Hebel k als
Anschlag wirkt.
Auf der Führungswange L gleitet frei der Schlittentisch
J, welcher an seiner linken vorspringenden
Seitenleiste ebenfalls ein stellbares Anschlagstück S
bekommt, welches an einem Zapfen von L anschlägt.
Die Verbindung des Schlittentisches J mit dem Drehstück
L ist durch einen Handhebel P mit der Hebelschiene P1 in der Weise bewerkstelligt, daſs bei gelöster
Schraube k1 sowohl
Drehung, als auch Verschiebung möglich ist. Die Aufeinanderfolge dieser Bewegung ist
durch die entsprechenden Anschlagklötzchen f und S bestimmt, welche in diesem Fall gleichsam die
Stützpunkte für die Hebelkraft abgeben.
Wird hingegen durch die Klemmschraube k1 der Drehtisch L in
irgend einer Winkellage festgelegt, so kann mit dem Handhebel P nur eine geradlinige Verschiebung des
Schlittentisches J hervorgerufen werden.
Auf dem Schlittentisch J ist eine getheilte Kreisauflage
K vorhanden, welche das Drehstück E trägt, das wieder zwischen Seitenleisten geführt ist.
Mit der Schraube m werden diese Theile in der
gewünschten Winkelstellung und Ausschiebung zum Drehstück L festgelegt. Der obere, mit einem Längsschlitz versehene Theil M bildet mit der Querstange h und den beiden Klemmarmen N die
Aufspannvorrichtung für die auf einem Dorn geschobene Fräserscheibe. An den
Armflügeln N sind Lappen für die Befestigung der
Stellfeder n vorgesehen, mit welcher die Fräserscheibe
in Lage erhalten wird.
Um nun die Achsenlage des Fräserdornes zur Schleifscheibe zu regeln, bezieh. eine
kleine Verdrehung der Trägerarme NN zu ermöglichen, ist
ein Klemmring O auf die Querstange h angebracht, welcher mittels einer Stellschraube O1 und zweier
Seitenschrauben (Fig. 1 und 2) gehalten wird.
An Stelle der Spitzen wird hingegen ein Kolbenfräser mit Ansatzzapfen unmittelbar in
einem der beiden Trägerarme fliegend eingespannt und ebenso die Stellfeder n behandelt.
Sollen hingegen Fräser mit gewundenen Riffen geschliffen werden, so muſs die
Stellfeder an einem festgelegten Ort, am besten in der Spannnuth V des Kreuzschlittens G
angebracht sein, soll mit der axialen Verschiebung zugleich eine Drehung des Fräsers
verbunden sein.
Wie bereits bemerkt, werden Form fräsen bei Mitverwendung von Lehren (Schablonen)
geschliffen und hierbei je nach der Ausgestaltung der Fräser zwei Verfahren in
Anwendung gebracht.
Nachdem durch Auslösung der Spindelmutter von b der
Stellschlitten G freibeweglich gemacht ist, wird
derselbe vermöge eines über die Schnurrolle C geführten
Gewichtes beständig nach rechts geschoben, diese Bewegung aber durch die am
Schlitten J angeordnete Formlehre Q bezieh. Q1 begrenzt, indem diese mit ihrer Formkante an die
Stellrolle j sich legt. Der Rollenträger besteht aus
einem Schraubstift mit feiner Einstellbewegung, einem Gabelsupport l und dem Winkelschlitten t, welcher am Vorgelegeständer B befestigt
wird.
Wird ferner mit der Schraube k1 das Drehstück L mit dem Schlitten H verkuppelt, so daſs jede Verdrehung ausgeschlossen
und nur eine rechtwinkelige Kreuzverschiebung zwischen G und H möglich bleibt, so wird eine genaue
Uebertragung der Schablonenform auf den Fräser statthaben, sofern die Leitrolle j und der Schleifscheibenrand gleiche Begrenzungskreise
besitzen.
Dieses Schleifverfahren würde aber bei Fräsern mit stark ausweichendem
Formquerschnitt, wie Zahnradfräsern u.s.w., ein ungenaues Ergebniſs liefern, weil
die Schleifscheibe abwechselnd mit den Rändern in Wirksamkeit tritt, wie es in Fig. 6
angedeutet erscheint.
Um diesen Uebelstand zu umgehen, wird auf die Querverschiebung mittels E verzichtet, dafür aber hauptsächlich die Verdrehung
des Drehstückes L, J in Anwendung gebracht, wobei der
Schlitten G frei beweglich bleibt. Hierdurch gewinnt
man eine bedeutende Uebersetzung zwischen Formquerschnitt des Fräsers und Schablone
und den weiteren Vortheil, daſs die Schleifscheibe sich annähernd winkelrecht zur
Tangente im Berührungspunkte der Fräsercurve stellt.
Alsdann wird der Hebel P, P1 an den Schlitten G und an die Tischplatte
A gekuppelt, während an J der Griffknopf P zur Bethätigung belassen
bleibt. Der Schleifvorgang wird Zahn um Zahn in der Weise durchgeführt, daſs die
Formfräse mit dem abzuschärfenden Zahn an die Stellfeder n gedreht und mit derselben gehalten wird, während entweder durch
Bethätigung der Schraubenspindel i der Schlitten H sammt den beschriebenen Theilen sich längsseits des
Schleifrades bewegt, wobei durch Einwirkung des Belastungsgewichtes an G derselbe der Form der Schablone gleichzeitig folgt,
oder indem durch Drehung des Obertheiles J mit der
linken Hand bei gleichzeitigem Andruck an die Schablone mittels des Handhebels P der Fräsezahn am Schleifrad vorbeigeführt wird.
Umständlich bleibt immerhin bei Formfräsern mit gewundenen Fräsezähnen die
Anbringung der Stellfeder n. In diesem Fall wird die in
V eingespannte Stellfeder möglichst breit zu machen
sein, damit bei der
relativen Verschiebung oder Verdrehung der Eingriff mit dem Fräsezahn nicht verloren
geht.
Als Erklärung, wie die Einstellung durchzuführen ist, möge das in Fig. 7 zur Anschauung
gebrachte Beispiel dienen.
Mit einem Schleifrade von 50mm Durchmesser sind die
Zähne einer Fräserscheibe von 81mm Durchmesser,
deren Mantelfläche nach einem Kreise von 50mm
Halbmesser geballt ist, auf 80mm Durchmesser
nachgeschliffen worden.
Da der Nullpunkt der Schlittentheilung (dc) genau die
Lage des Drehstücksmittels L unter der Spindelachse x angibt, so muſs bei der convexen Form des
Fräsermantels dieses Mittel in die Entfernung 50 + 25 = 75 gebracht werden. Alsdann
wird der Fräserträger üf bis zur Berührung der Fräse an das Schleifrad angeschoben
und mittels der Schraube m festgestellt. Hierauf wird
der Schlitten G mit der Schraubenspindel b um 0mm,5
vorgerückt, was bei g abzulesen ist. Dieser Vorschub
entspricht der Abminderung des Fräsedurchmessers von 81 auf 80mm. Nun wird für jeden Fräsezahn der Drehtisch
mittels des Handhebels P in Schwingung versetzt und
derart Zahn um Zahn nachgeschärft.
Ist ferner an diesem geballten Fräsetheil noch ein kegelförmiges Stück angesetzt, so
wird die Ausschwingung mittels eines Stellklötzchens f
begrenzt und die geradlinige Verschiebung des Oberschlittens J eingeleitet. Wenn aber der Fräser aus zwei Kegeltheilen zusammengesetzt,
die scharf (also ohne Abrundung) zusammenstoſsen, so wird das Mittel des Drehstückes
L in den Abstand 0 + 25 = 25 eingestellt, und die
Schlittenverschiebung mit P und i auf einander folgend durchgeführt, wobei für den einen Kegeltheil die
Schräglage des Aufspanndornes gegen den Kreuzschlitten H und für den andern die Lage des Stellklötzchens f auf der Leiste der Kreisunterlage maſsgebend ist.
Wenn aber der Fräser aus einem Hohlkehlen-, einem Cylinder- und einem Kegeltheil
(Fig. 8)
zusammengesetzt ist, so muſs der Schleifvorgang für einen Zahn in zwei Abtheilungen
zerlegt werden, und zwar entweder Kegel mit Hohlkehle, oder Hohlkehle und Cylinder
auf einmal.
Vorrichtung zum Schleifen gewundener
Bohrer (Fig. 9 und 10).
Die soeben beschriebene Maschine wird auch zum Schleifen von Spiralbohrern
eingerichtet, indem an Stelle des Fräserträgers K, E, M
die in Fig. 9
und 10
dargestellte Vorrichtung auf den Oberschlitten J
gesetzt wird.
Diese besteht aus der Gabelplatte D und einer Platte C mit den Lagern A und B für den Bohrer und der Gegenspitze b. In das Vorderlager A
wird eine, dem Bohrerdurchmesser entsprechende Büchse a
eingesetzt, während der Bohrer mittels eines aus c und
l zusammengesetzten Klemmrahmens an die Gegenspitze
gekuppelt wird.
Diese Gegenspitze b ist in die Büchse d eingeschraubt und kann vermöge des Handhebels O gleichzeitig gedreht und vorgeschoben werden, sofern
diese Büchse d festgehalten wird. Dies geschieht sowohl
durch einen Einlegehebel e, als auch durch einen
kleinen Stift f, welcher im Lagerauge B eingeschraubt ist und der in einem Ausschnitt des
Hinterbordes der Büchse eingreift. Wird der Einlegehebel e herausgedreht, so kann die Büchse d sammt
Bohrer zurückgeschoben und um 180° verdreht werden, so daſs der gegenüberliegende
Bordeinschnitt in die Richtung des Stiftes f
gelangt.
Hierdurch wird die Einstellung der beiden Bohrerschneiden zur Schleifscheibe
ermöglicht. Um aber diese Schneiden in die Scheitelstelle der Schleifscheibe
einzubringen, wird die um den Bolzen g schwingende
Lagerplatte C vermöge einer Daumenwelle h in die Schräglage (Fig. 9) gehoben, durch die
Klemme i an das Führungsstück m gepreſst und dadurch in der gewünschten Lage erhalten.
Geschliffen wird die Bohrerschneide, indem man den Hauptschlitten H mit der bereits beschriebenen Spindel i (Fig. 8) bethätigt. Damit
aber diese Schneide vor dem, die Bohrerspitze bildenden Grundkegel vorsteht, genügt
nicht eine einfache axiale Drehung des Bohrers, sondern es muſs gleichzeitig damit
ein kleiner Vorschub in der Achsrichtung des Bohrers verbunden sein.
Dies wird in sinnreicher Weise dadurch erreicht, daſs bei festgelegter Büchse d die Gegenspitze b mit
dem Handgriff O gedreht und zugleich vorgeschraubt
wird, wozu das Gewinde in d bezieh. b vorgesehen ist. Ein in dem Hinterbord der Büchse d angebrachter Zahn p
spielt ferner in einem halbkreisförmigen Ausschnitt der Nabe von O, wodurch diese Drehung auf einen halben Kreisbogen
beschränkt bleibt und die zweite Bohrerschneide vor Beschädigung durch das
Schleifrad gesichert wird.
Soll auch die innere, durch die Schraubennuth gebildete Schneidfläche des Bohrers
nachgeschliffen werden, so wird die Lagerplatte C durch
Verdrehung des Daumens h in die Wagerechtstellung
gebracht und eine dem Nuthquerschnitt des Bohrers entsprechend abgerundete
Schleifscheibe auf die Maschinenspindel gesteckt.
Diese Schleifscheibe greift von oben her in die Auslaufstelle der Bohrernuth ein, und
es wird durch eine sanfte Drehung des Bohrers mittels des Griffhebels O die Schärfung der inneren Schneidfläche, bezieh. der
Schneidkante des Bohrers ohne Umspannen durchgeführt. Die zweite Nuthfläche wird in
der vorbeschriebenen Weise bei einer Drehverstellung des Bohrers mit der Büchse d um 180° angeschliffen. Zu diesem Behufe wird vorher
der Kreuzschlitten G zurückgestellt und somit der
Bohrer vom Schleifrad entfernt, alsdann wird der Einlegehebel e herausgedreht, die Büchse d sammt dem Bohrer zurückgeschoben, wobei der hintere Bordrand aus dem
Stellstift f tritt, wodurch eine Verdrehung der Büchse
um 180° erst ermöglicht wird.
Damit das Schleifrad in die gewundene Bohrernuth eingreifen kann, muſs selbstverständlich das
Drehstück L mit der ganzen Vorrichtung so weit verdreht
werden, daſs die Ebene des Schleifrades mit der Auslaufstelle der Nuth
übereinstimmt, was gegen die Lage (Fig. 10) eine annähernd
winkelrechte Einstellung bedingen würde.
Pregél.
Tafeln
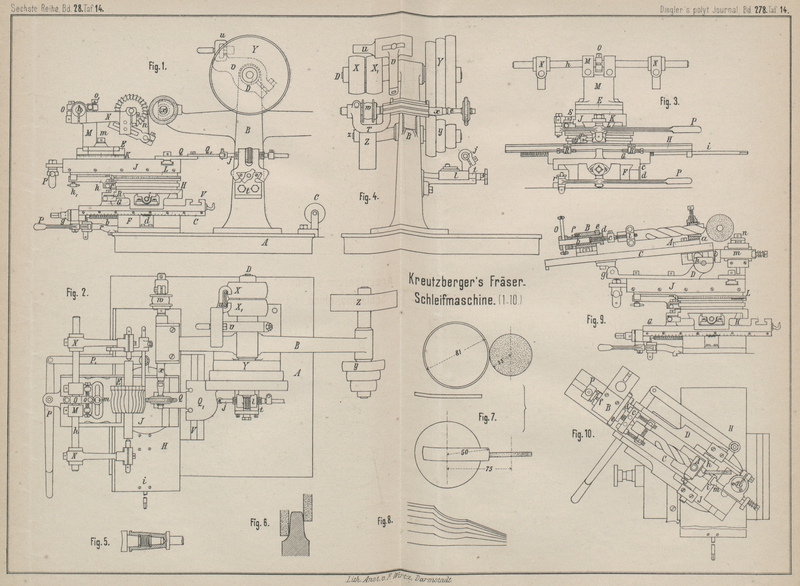