Titel: | Neuerungen an Walzwerken. |
Fundstelle: | Band 278, Jahrgang 1890, S. 433 |
Download: | XML |
Neuerungen an Walzwerken.
(Fortsetzung des Berichtes Bd. 277 * S.
543.)
Mit Abbildungen auf Tafel
23.
Neuerungen an Walzwerken.
Wenn auch die so hervorragende Neuerung, wie sie das Mannesmann'sche Walz verfahren bildet, zur Zeit die Aufmerksamkeit der
Walztechniker in vorwiegendem Maſse auf sich zieht, so fehlt es doch nicht an
Fortschritten auf dem bisherigen Wege des Walzwerksbetriebes und der
Walzwerksconstructionen, die unseres Erachtens bemerkenswerth sind. Wenn auch das
Mannesmann'sche Verfahren ganz neue Bahnen eröffnen
wird, so wird doch das alte Verfahren für manche Zweige der Technik seinen Werth
behalten und sich dauernd behaupten.
Wir wollen im Nachstehenden über die bemerkenswerthen Neuerungen sowohl in den
Constructionen selbst, als auch über deren Einfluſs auf den Betrieb eingehend
berichten.
Walzwerk für Bandeisen und Draht
von E. Stegmann in Kaczagorka bezieh. G. Brisker in Prag.
Das Walzwerk besteht aus mehreren hinter einander stehenden Walzgerüsten, von denen
jedes zwei über einander liegende von einander getrennte Walzenpaare enthält, D. R.
P. Nr. 50168 vom 5. Januar 1889 bezieh. Nr. 52512 vom 9. August 1889 (Fig. 1).
Die Anordnung von hinter einander stehenden Walzgerüsten ist nicht neu, ebenso die
Anordnung von zwei Paar Walzen über einander in einem Gerüste. Bei den bisherigen
Ausführungen des ersteren Systems haben jedoch die hinter einander stehenden
Walzgerüste nur je zwei Walzen, es wird in jedem Gerüste nur ein Stich gemacht, und
in den auf einander folgenden Walzenpaaren wird mit zunehmender Geschwindigkeit
gearbeitet, um eine Schlingenbildung zu vermeiden; letzteres ist jedoch nur durch
sehr complicirte Räderübersetzungen oder sonstige Transmissionen zu erreichen;
auſserdem ist es äuſserst schwierig, die Streckung in den einzelnen Kalibern unter
allen Umständen stets in dem richtigen Verhältnisse zur Umfangsgeschwindigkeit der
Walzen zu erhalten, und es sind in Folge dessen mit dem betreffenden Walzwerke so
viele Nachtheile verbunden, daſs dasselbe nur in sehr beschränktem Maſse zur
Anwendung gekommen ist.
Die Anordnung von zwei Paar Walzen in denselben Ständern über einander wurde bis
jetzt nur bei in einer Linie neben einander liegenden Walzgerüsten zur Anwendung
gebracht; die auf einander folgenden Walzenpaare erhielten durch complicirte
Räderübersetzungen ebenfalls eine zunehmende Geschwindigkeit, um eine
Schlingenbildung zu vermeiden; dabei wurde das Walzgut aus dem unteren Walzenpaare
eines Gerüstes in das darüber liegende und von hier sofort in das untere Walzenpaar
des nächsten nebenan liegenden Gerüstes geführt, so daſs in jedem Gerüst zwei Stiche oder
Durchgänge gemacht wurden. Auch solche Walzwerke bieten aus den gleichen Gründen,
die bei dem ersteren Walzwerkssystem angeführt wurden, Schwierigkeiten.
Das nachstehend beschriebene neue Walzwerk ist eine Vereinigung der angeführten zwei
Walzwerkssysteme; es werden durch dasselbe die Nachtheile jener beiden Systeme
vermieden und man erhält ein in Anlage und Betrieb bedeutend einfacheres und
billigeres Walzwerk.
Das Walzwerk besteht, wie bereits Anfangs erwähnt, aus mehreren hinter einander
stehenden Walzgerüsten, von denen jedes zwei Paar Walzen in denselben Ständern über
einander enthält (Fig. 1). Die Uebertragung der Bewegung von einem Gerüst zum anderen
geschieht am besten durch Zahnräder. Zur Uebertragung der Bewegung auf die Walzen
eines jeden Gerüstes dienen entweder Kammwalzen in besonderen Ständern, wie in Fig. 2
gezeichnet, oder es werden auf die verlängerten Zapfen der Walzen Zahnräder aus
Stahlguſs aufgeschoben und durch Räder r angetrieben,
wie in Fig. 3
dargestellt. In Folge der beschriebenen Anordnung haben immer die beiden Walzenpaare
eines Gerüstes dieselbe Umfangsgeschwindigkeit.
Fig. 4 zeigt
den Antrieb der Walzen im letzten Gerüste beim Walzen von Bandeisen, wenn
Schleppwalzen zur Verwendung kommen.
Die Walzarbeit geht in dem beschriebenen Walzwerke in folgender Weise vor sich: Der
Knüppel wird in einem gewöhnlichen Trio-Vorstreckgerüste V (Fig.
2) bis zu einem bestimmten Querschnitte vorgewalzt. Der vorgewalzte Stab
wird dann aus dem letzten Kaliber sofort in das Gerüst a des Fertigwalzwerkes Fig. 1 und 2, zwischen die Walzen 1–2 geführt, bei seinem
Austritte durch eine mechanische Umführung selbsthätig nach oben gebogen und
zwischen die Walzen 3–4
gebracht, bei seinem Austritte aus diesen Walzen nach unten, wieder zwischen die
Walzen 1–2, jedoch durch eine schräge Umführung in ein
neben dem ersteren liegendes Kaliber und von hier aus durch eine gerade Führung in
das Gerüst b geführt, in welchem, und nötigenfalls auch
in den nachfolgenden Gerüsten, sich die gleiche Umführung des Walzgutes wiederholt.
Es werden daher in jedem Gerüste drei Stiche oder Durchgänge gemacht.
Speciell beim Walzen von Bandeisen erhält das letzte Gerüst zwei Paar Schlichtwalzen.
Das Bandeisen geht dann aus dem unteren Walzenpaare des vorletzten Gerüstes in das
obere Walzenpaar des letzten Gerüstes c und zwischen
den Walzen 3–2 hindurch in
das untere Walzenpaar, aus welch letzterem es fertig heraustritt (Fig. 1) – oder das
Bandeisen tritt, wie in Fig. 1a gezeichnet, zuerst in das untere Walzenpaar des
letzten Gerüstes und geht zwischen den Walzen 2–3 hindurch in das obere Walzenpaar. Es findet daher
zwischen den auf einander folgenden Walzenpaaren eines jeden Gerüstes eine
Schlingenbildung statt.
Zwischen den auf einander folgenden Gerüsten nimmt die Walzengeschwindigkeit zwar zu, jedoch findet
dies nur in einem solchen Maſse statt, daſs auch hier eine bedeutende
Schlingenbildung eintritt, und es wird daher im Gegensatze zu den angeführten
bekannten Walzwerkssystemen zwischen allen, sowohl den über einander liegenden als
auch zwischen den hinter einander liegenden Walzenpaaren mit Schlingenbildung
gearbeitet.
Die zum Umführen des Walzgutes in den über einander liegenden Walzenpaaren dienenden
mechanischen Umführungen besitzen folgende Construction: Zwischen zwei Platten S (Fig. 5 und 6) befindet sich das feste
Bogenstück n, ferner das feste Bogenstück o und der mit letzterem um einen Bolzen i drehbare Bügel b. Diese
Theile sind zwischen den Platten S durch Bolzen
befestigt und können gewechselt werden; dieselben sind für Bandeisen innen glatt,
während sie für Draht zur Hälfte eine Quadratspur, zur Hälfte eine Ovalspur
besitzen, so daſs in der Führung selbsthätig ein Drehen des Walzstabes um 90°
stattfindet, in ähnlicher Weise, wie dies bei wagerechten Umführungen der Fall ist.
Die Verbindung mit den Walzenkalibern ist durch die Führungsbüchsen f und f1 hergestellt.
Fig. 5 zeigt
die geschlossene Führung in dem Augenblicke, wo das Walzgut aus einem Walzenpaare in
das andere tritt; der Bügel b, welcher in seiner oberen
Hälfte bedeutend stärker ist als in seinem unteren Theile, wird in Folge dessen
durch das Gewicht der oberen Hälfte in der gezeichneten Stellung gehalten; dieses
Gewicht kann entsprechend dem Querschnitte des Walzgutes regulirt werden.
Hat der Walzstab die Führung durchlaufen und ist derselbe in das zweite Walzenpaar
getreten, so wird von der sich nun bildenden Schlinge der Bügel b aufgeklappt und die Schlinge tritt, wie in Fig. 6
angedeutet, aus der Führung heraus, und fällt, sowie sie sich erweitert, senkrecht
nach unten. Es kommt auf beiden Seiten der Walzen die gleiche Construction zur
Anwendung, da es gleichgültig ist, ob das Walzstück von unten nach oben oder von
oben nach unten geführt wird; nur für den Uebergang des Walzstabes aus dem einen
oberen Walzenpaare schräge in das nebenan liegende Kaliber des unteren Walzenpaares
sind die betreffenden Umführungen schräg gestellt, bei Bandeisen auch noch
entsprechend gekrümmt, da hier trotz der schrägen Stellung der Führung die Ein- und
Auslaufstellen parallel bezieh. senkrecht zu den Walzen stehen müssen. Die zwischen
den auf einander folgenden Gerüsten befindlichen geraden Führungen haben ebenfalls
nach unten aufklappbare (durch Hebel und Gegengewicht geschlossene) Bügel (Fig. 1), so
daſs die Schlingen auch hier nach unten austreten können, Sämmtliche Schlingen,
sowohl die zwischen den über einander als auch die zwischen den hinter einander
liegenden Walzenpaaren sich bildenden, fallen senkrecht nach unten in einen
schmalen, im Fundamentmauerwerke ausgesparten und in der Mitte des ganzen
Fertigwalzwerkes sich
hinziehenden Schacht T (Fig. 2, 3 und 4). – RR (Fig. 1) sind breite
eiserne Gerinne, durch welche das von den Walzen herablaufende Kühlwasser abgeführt
wird, ohne den Schacht T naſs zu machen.
Damit das bei den einzelnen Umführungen bezieh. geraden Führungen aus dem einen
Walzenpaare zuerst austretende Ende des Walzgutes nicht in den Schacht herabfallen
kann, da hierdurch ein Verwirren der in dem Schachte hängenden Schlinge bewirkt
werden könnte, dient nachstehende Einrichtung: An der Einlaſsseite der Führung, also
der Austrittsstelle des Walzstabes, sind ein oder zwei Paar Rollen rr (Fig. 5 und 6) in die Umführung (bei
den hinter einander stehenden Gerüsten in die gerade Führung) eingeschaltet, von
welchen die unteren durch einen Hebel mit Gegengewicht G mit einer bestimmten Kraft gegen die oberen angedrückt werden. Das in
die Führung eintretende Walzgut muſs zuerst zwischen diesen Rollen
hindurchgehen.
Hat nun das Ende des Walzgutes das betreffende eine Walzenpaar verlassen, so kann es
nicht in den Schacht hinabgleiten, sondern es wird durch die Rollen so lange
festgehalten, bis das andere Walzenpaar die Schlinge vollständig aufgearbeitet hat.
Das Gegengewicht, durch welches die unteren Rollen gegen die oberen angedrückt
werden und daher das Ende des Walzgutes nach seinem Austritte aus den Walzen
gehalten wird, kann stets, entsprechend dem Gewichte der in den Schacht
herabhängenden einen Hälfte der Schlinge, eingestellt werden.
Je nachdem die Dicke und somit das Gewicht dieses Theiles der Schlinge gröſser oder
kleiner ist, wird die Kraft, mit welcher die unteren Rollen gegen die oberen
angedrückt werden, gröſser oder kleiner sein müssen, um das betreffende
Schlingenende zu halten. Da mit dem Gewichte der herabhängenden Schlinge jedoch auch
die Dicke und daher die Steifigkeit des warmen Walzstabes zunimmt, so wird auch der
in die Rollen rr erst eintretende Theil stets steif
genug sein, um den Eintritt zwischen die betreffenden Rollen zu bewirken, ohne sich
zu stauchen.
Es können bei ganz schwachen Eisensorten auch drei Paar Rollen hinter einander
angebracht werden, jedes Paar hat dann nur ⅓ des Gewichtes des herabhängenden
Schlingentheiles zu tragen, die Belastung jeder unteren Rolle ist dementsprechend
dann auch nur ⅓ und in Folge dessen auch der Durchgang des Walzstabes durch die
Rollen um soviel leichter. Das neue Walzwerk ist durch nachstehende Vortheile
charakterisirt:
1) Es sind dadurch, daſs in jedem Gerüste drei Stiche oder Durchgänge gemacht werden,
für eine gleiche Anzahl von Stichen weniger Walzgerüste, Walzen u.s.w. nöthig als
bei anderen Walzwerken.
2) Da ein unmittelbarer Uebergang des Walzgutes aus einem Walzenpaare in das andere
nicht stattfindet, sondern mit Schlingenbildung gearbeitet wird, so entfallen die
vielen complicirten Räderübersetzungen und es werden alle die Schwierigkeiten
vermieden, welche bei zunehmender Walzengeschwindigkeit und unmittelbarem Uebergange des
Walzgutes unausbleiblich sind.
3) Durch das Austreten der Schlingen nach unten und in einen unter der Hüttensohle
befindlichen Schacht werden auch alle die Nachtheile, welche mit der
Schlingenbildung verbunden sind, vermieden; die Schlingen nehmen keinen Raum über
der Hüttensohle ein, es ist jede Gefahr für die Arbeiter beseitigt und die Abkühlung
der Schlingen, welche sich stets in einem erwärmten Raume befinden, ist auf ein
Minimum herabgemindert.
Duowalzwerk mit senk- und hebbarer
Unterwalze von E. Stegmann bezieh. G. Brisker (D. R. P. Nr. 50168 vom 5. Januar
1889).
Bei den bisherigen Walzwerkssystemen bedingt das Heben des Walzstückes oder das
Reversiren der Walzen auſser einem bedeutenden Zeitverluste einen groſsen Dampf- und
Schmiermaterialverbrauch und einen starken Verschleiſs von Maschinentheilen.
Nachstehend ist nun ein Walzwerk beschrieben, welches ein leichteres und schnelleres
Arbeiten ermöglicht, als es bei allen anderen Walzwerkssystemen der Fall ist, und
bei welchem sowohl die Anlagekosten als auch die gesammten Betriebs- und
Unterhaltungskosten bedeutend geringer sind. Die Eigenthümlichkeit des Walzwerkes
besteht darin, daſs das Walzstück nach jedem Durchgange zwischen Ober- und
Unterwalze hindurch auf die Vorderseite zurückgeschoben wird, ohne daſs die
Umdrehungsrichtung der Walzen sich wie bei einem Reversirwalzwerke ändert; es wird
nur, um das Zurückschieben des Walzstückes zu ermöglichen, die Unterwalze gesenkt
und nach erfolgtem Rückgange wieder gehoben.
Um ein solches Walzverfahren praktisch durchführbar zu machen, muſs das Senken und
Heben der Walze genügend schnell, leicht und mit gröſster Betriebssicherheit
erfolgen, was Zweck der nachstehend beschriebenen Constructionen ist.
Die Oberwalze ist, wie jetzt meist üblich, durch hydraulische Cylinder CC (Fig. 7) und einen
Gewichtsaccumulator ausbalancirt, ebenso erfolgt das Nachstellen der Walze in der
gewöhnlichen Weise. Die Unterwalze jedoch ist nicht wie gewöhnlich fest in den
Ständern gelagert, sondern ruht in den Einbaustücken EE
und kann mit diesen gesenkt und gehoben werden; dieselbe ist ähnlich wie die
Oberwalze durch zwei hydraulische Cylinder D und einen
Gewichtsaccumulator P ausbalancirt. Die
Gewichtsausgleichung erfolgt jedoch nur in dem Maſse, daſs die Walze noch mit einem
geringen Uebergewichte auf den zwischen den Einbaustücken E und den Walzenständern befindlichen Unterlagen U aufliegt. Die betreffenden Unterlagen können durch zwei in einem
gemeinschaftlichen Cylinder G (Fig. 8) befindliche
Dampfkolben verschoben werden. Oberhalb des Accumulators P befindet sich ein zweiter Dampfcylinder F,
dessen Kolbenstange beim Niedergange des Kolbens direkt auf den Plunger des Cylinders P drückt und dadurch die Unterwalze hebt. Die Steuerung
der beiden Cylinder F und G wird durch einen gemeinschaftlichen Hebel bewirkt.
Das Senken und Heben der Unterwalze geschieht in folgender Weise: Sobald das
Walzstück auf der Hinterseite aus den Walzen getreten ist, wird die Unter walze
durch ein geringes Niedergehen des Kolbens des Cylinders F etwas angehoben und die Unterlagen U
zurückgezogen. Ist letzteres geschehen, so hört der Druck auf den Dampfkolben auf
und die Unterwalze sinkt. Alles dies erfolgt fast augenblicklich durch Verstellen
des Hebels ab.
Nach erfolgtem Rückgange des Walzstückes auf die Vorderseite wird durch Zurückstellen
des Hebels die Unterwalze gehoben, die Unterlagen unter die Einbaustücke
zurückgebracht und hierauf der Dampfkolben des Cylinders F entlastet; die Walze setzt sich vermöge ihres Uebergewichtes wieder fest
auf die Unterlagen und der nächste Durchgang kann erfolgen.
Die Steuerung der beiden Cylinder F und G ist in Fig. 7 im Prinzip
veranschaulicht: Die Schieber der beiden Cylinder sind durch die Zugstangen Z und Z1 mit dem Handhebel ab
verbunden. Die Schieberstange des Cylinders F trägt an
ihrem unteren Ende eine kleine Rolle r und wird durch
Dampfdruck oder durch ein Gewicht stets nach unten gedrückt, so daſs sie mit der
Rolle r auf der Zugstange Z aufsitzt; diese Zugstange besitzt eine Vertiefung u. Befindet sich nun
der Steuerhebel in der Stellung ab, so ist der Schieber
des Cylinders F in seiner höchsten Lage, der
Dampfeintrittskanal ist geschlossen, auf dem Cylinderkolben befindet sich kein
Dampfdruck und der Plunger des Accumulators P ist in
Folge des Uebergewichtes der Unterwalze gehoben; die Unterlagen befinden sich unter
den Einbaustücken. Wird der Hebel ab in die punktirte
Stellung cd gebracht, so gleitet zuerst die Rolle r in die Vertiefung u der
Zugstange Z, der Schieber des Cylinders F wird heruntergedrückt, es tritt Dampf über den
Kolben, drückt diesen und mit demselben den Plunger des Accumulators P herunter und die Unterwalze wird etwas angehoben. In
dieser Stellung verbleibt die Walze so lange, als die Rolle r der Schieberstange in dem vertieften Theile der Zugstange Z gleitet. Während dieser Zeit wird durch den
Steuerhebel ab auch der Schieber des Cylinders G verstellt; es tritt Dampf gleichzeitig vor beide
Kolben und die Unterlagen U werden unter den
Einbaustücken weggezogen. Jetzt ist die Zugstange Z so
weit nach rechts gegangen, daſs die Rolle der Schieberstange wieder steigt, der
Schieber wird gehoben, dadurch der Dampfkolben entlastet und die Unterwalze sinkt.
Durch Zurückbringen des Hebels in seine ursprüngliche Stellung wird wieder zuerst
die Unterwalze gehoben, die Unterlagen U unter die
Einbaustücke zurückgebracht und zuletzt durch Entlastung des Dampfkolbens die Walze
wieder fest aufgesetzt. Es ist deicht einzusehen, daſs sich die Wege oo1 und db, welche die betreffenden Theile der Zugstangen beim
Verstellen des Handhebels zurücklegen, ferner die Länge der auf der Zugstange Z befindlichen Vertiefung u, sowie endlich die Schieberwage der beiden Dampfcylinder so bemessen
lassen, daſs das Anheben der Unterwalze, das Verschieben der Unterlagen und das
nachfolgende Senken der Unterwalze bezieh. das Aufsetzen auf die Unterlagen
vollkommen präcise in den richtigen Momenten erfolgt. Der Dampfcylinder zum
Verschieben der Unterlagen kann anstatt unter der Unterwalze auch vor den Walzen
liegen; es ist in diesem Falle nur ein gewöhnlicher Cylinder mit einem Kolben nöthig
und die Unterlagen werden dann, wie in Fig. 9 gezeichnet, durch
über Rollen RR1 gehende
Ketten verschoben. Die Kuppelungsspindeln an der Unterwalze können stets von
genügender Länge sein und werden dieselben in entsprechender Weise ausbalancirt.
Durch die hydraulische Gewichtsausgleichung der
Unterwalze, sowie dadurch, daſs der Hub der Walze sehr klein ist und nur ungefähr
60mm beträgt, erfolgt das Senken und Heben
selbst beim schnellsten Walzen ruhig und leicht, und es ist in Folge der geringen
Bewegung der betreffenden Theile und der unbedeutenden Arbeit, welche die zwei
kleinen Dampfcylinder F und G zu verrichten haben, der Dampf- und Schmiermaterialverbrauch, sowie die
Abnützung aller Theile so gering, wie dies bei keinem anderen Walzwerke der Fall
ist.
Die Walztische sind unbeweglich; für schwere Bleche erfolgt der Antrieb der
Tischrollen wie bei den Reversir walz werken durch eine besondere kleine Maschine,
oder es erfolgt der Antrieb durch Frictionsrollen mm,
auf welche sich die Unterwalze beim Senken aufsetzt, wie in Fig. 11 und 13
gezeichnet.
Das beschriebene Walzwerk ist hauptsächlich für schwere Bleche bestimmt; um mit
demselben jedoch auch leichtere Bleche walzen zu können, dient nachstehende
Einrichtung. Bei festen Walzentischen ist die Lücke, welche bei dem Sinken der
Unterwalze zwischen beiden Tischen entsteht, für kleine Brammen eventuell zu groſs,
und es können bei dem Zurückgeben solcher Brammen Störungen verursacht werden; es
wird für diesen Fall der mittlere Theil der Tische fahrbar gemacht. Sinkt die
Unterwalze, so fahren beide Tische gleichzeitig gegen die Walze vor und nehmen die
in Fig. 12
und 13
gezeichnete Stellung ein. Beim Heben der Walze fahren die Tische wieder in die
ursprüngliche Stellung (Fig. 10 und 11) zurück.
Das Bewegen der Tische erfolgt entweder durch die Frictionsrollen mm (Fig. 11 und 13) oder durch
einen der beiden Dampfcylinder F und G, immer aber selbsthätig, und gleichzeitig mit dem
Senken und Heben der Unterwalze. Das Senken und Heben der Unterwalze kann auch durch
Schrauben erfolgen. Unterhalb der Unterwalze befinden sich in den Walzenständern die
Schrauben S (Fig. 14 und 15). In den
mit den Walzenständern fest verbundenen Halslagern L (Fig. 15) drehen sich die
Zahnräder R. Die letzteren und die Schrauben S sind derart durch Keile mit einander verbunden, daſs
beim Drehen der Räder die Schrauben auf und nieder steigen, die Räder jedoch an
ihrer Stelle verbleiben. Die Räder R werden mittels der
auf der Welle w w sitzenden Kegelräder und eventuell
eines weiteren Zahnradgetriebes durch eine kleine schnelllaufende Reversirmaschine
unabhängig von der Anstellvorrichtung der Oberwalze angetrieben. Die beschriebene
Walzmethode, mit senk- und hebbarer Unterwalze, kann auch bei Blockwalzwerken mit
Vortheil zur Anwendung gelangen.
Die Lauth'schen Triowalzen (Fig. 16 bis 21).
Das Wesen der Triowalze für Blech nach Lauth's
Construction besteht bekanntlich darin, daſs die mittlere Walze geringeren
Durchmesser hat als die äuſsere. Diese Anordnung soll ein beschleunigtes Strecken
bewirken und wird bei dem Arbeitsvorgange das Packet abwechselnd über oder unter die
Mittelwalze gegeben (vgl. 1881 242 322, 1887 266 491). Ueber den Betrieb und die Construction des Lauth'schen Trios und dessen Einführung in den
Feinblechbetrieb bringt die Oesterreichische Zeitschrift für
Berg- und Hüttenwesen vom 8. Februar 1890 nachstehende bemerkenswerthe
Mittheilungen, die das Interesse des Praktikers dadurch besonders beanspruchen kann,
daſs sie eine Kritik über die praktische Verwendbarkeit des Lauth'schen Trios an der Hand von Zahlenangaben durchführen:
Von einigen der bedeutendsten Werke des In- und Auslandes ist bei der Neuanlage von
Feinblechwalzwerken zum Vorstrecken der Plattinen das Lauth'sche Trio gewählt worden. Zu dieser Wahl gab in erster Linie
Veranlassung die bedeutende Leistungsfähigkeit dieses Systems, welche sich auf sein
groſses Streckvermögen gründet. Lauth hat nämlich nach
dem Grundsatze, daſs Walzen um so stärker strecken, je schwächer an Durchmesser sie
sind, die Mittelwalze seines Trios schwächer gehalten als Ober- und Unterwalze,
erzielt also beim Vor- und Rückgange des Walzgutes eine stärkere Streckung als mit
drei gleichstarken Walzen. Da nun auſserdem die Hubhöhe beim Rückgange gegenüber der
gewöhnlichen Anwendung von zwei gleich starken Walzen vermindert wird und die
Oberwalze gleichzeitig mit der Arbeit des Streckens die Rückführung des Bleches
übernimmt, erhöht sich durch diese drei Vortheile die Leistungsfähigkeit des Systems
ganz bedeutend. Wir werden später vergleichende Angaben der Leistungen geben, wollen
aber vorher eine kurze Beschreibung und zugleich Begründung der zweckmäſsigsten
Construction und Abmessungen für die Feinblecherzeugung einschalten.
Was zuvörderst die Walzenabmessungen betrifft, so wähle man die Bundlänge derart,
daſs man auch die sogen. Mittelbleche, für deren Erzeugung sich das Lauth'sche Trio, wie wir später sehen werden, so wie
so am besten eignet,
vorstrecken bezieh. auswalzen kann, und bestimmt danach den Durchmesser des Bundes
und die Zapfenmaſse, z.B.:
1)
Für
Ober-, Mittel- und Unterwalze, Bundlänge
=
1500mm
2)
„
Ober- und Unterwalze, Walzendurchmesser
=
600mm
3)
„
Ober- und Unterwalze, Zapfendurchmesser
=
400mm
4)
„
Mittelwalze, Walzendurchmesser
=
400mm
5)
„
Mittelwalze, Zapfendurchmesser
=
280mm
6)
„
Ober-, Mittel- und Unterwalze, Zapfenlänge
=
340mm
Den Radius der Hohlkehle der Laufzapfen wählt man für Ober- und Unterwalze mindestens
= 40mm, den für die Mittelwalze = 20mm.
Unter der Annahme, daſs Mittel- und Oberwalze von der Unterwalze geschleppt werden,
ist der gröſste Abstand der Achsen der Unter- und Oberwalze = 300 + 400 + 300 + 25 =
1025mm. Die Erfahrung hat nämlich bewiesen,
daſs Plattinen über 25mm Stärke von Schleppwalzen
nicht mehr gefaſst werden. Da durch die Stärke, Länge und Breite der Plattinen ihr
Gewicht und damit das des daraus gewonnenen Feinbleches bedingt ist, wird eben
dadurch die Grenze gezogen, bis zu welchem gröſsten Gewichte und dann bis zu welchen
gröſsten Dimensionen Feinbleche mittels des Schleppwalzentrios erzeugt werden
können.
Um mit Ziffern zu rechnen, seien Feinbleche von 1200mm Breite und 1mm,0 Stärke zu walzen.
Die hierzu vorbereiteten Plattinen sind bei der gröſsten zulässigen Stärke von 25mm und der üblichen Breite von 152mm 1230mm lang,
haben demnach ein Gewicht von 2,5 × 15,2 × 123 × 7,8 = 36k,4. Rechnet man auf das fertige Blech 20 Proc.
Verlust ab, so bleibt ein Blechgewicht von 29k,1,
dem bei der angenommenen Breite von 1200mm und
Stärke von 1mm,0 eine Länge
x=\frac{29,1}{120\,\times\,0,1\,\times\,7,8=3110^{mm}}
entspricht. Aus diesem Beispiele ist zu ersehen, daſs
Feinbleche über 30k Gewicht die Tafel bei der
üblichen Plattinenbreite von 152mm dem
Schleppwalzentrio nicht zugetheilt werden können.
In Fig. 16 bis
18 ist
nun die Oberwalze sammt der dazu gehörigen Vorrichtung zum Ausbalanciren in der
tiefsten Lage gezeichnet. Zur Ausgleichung des Oberwalzengewichtes dürfen aber nur
so viel Gegengewichte angebracht werden, daſs beim Leergange die Oberwalze auf der
Mittelwalze aufläuft, auch ohne daſs sie mit der Druckschraube angepreſst wird. Die
Summe der am Hebel wirkenden Gegengewichte muſs also etwas leichter sein als das
gesammte Oberwalzengewicht, sonst bleibt die Oberwalze auch beim Leergange
stehen.
Beim Trio ist es für den guten Gang erforderlich, daſs die Achsen der drei Walzen zu
einander parallel und in einer und derselben senkrechten Ebene gelegen sind. Die
Achse der Unterwalze ist unveränderlich gelagert; sie und jene der Oberwalze
bestimmen die Ebene, in welche die Achse der Mittelwalze durch die seitliche
Keilstellung ihrer Lagerschalen genau eingestellt werden kann. Die Mittelwalze kann sich nun mit
ihren Lagerschalen zwischen den Platten, auf welche die Keile wirken, in der
Höhenrichtung frei verschieben; die Oberwalze wird in gewöhnlicher Weise durch zwei
Druckschrauben, die mittels einer wagerechten Zwischenwelle und Kegelrädern stets
die gleiche Drehung erhalten, parallel zu sich selbst gehoben und gesenkt.
Zur Lagerung der Zapfen wird man nicht allein für die Mittelwalze, sondern auch für
die beiden anderen Walzen auſser Unter- bezieh. Oberlagern auch Seitenlager
anbringen, um die theuern Lagerkörper nicht zu massig construiren zu müssen. Zu dem
Lagermetall verwendet man am zuverlässigsten eine Mischung von 90 Th. Kupfer und 10
Th. Zinn; diese besitzt die gröſste Zähigkeit und die entsprechende Härte, bei der
sich selten die Zapfen verreiben, wenn nur das Zapfeneisen nicht gar zu weich ist
und auf sorgfältige Schmierung mit Wasserkühlung der Zapfen geachtet wird. Kommen
aber trotzdem, in Folge von zu groſser Weichheit des Zapfengusses, Verreibungen vor,
so wurden mit groſsem Erfolge die Metallschalen mit einer Composition von 12 Th.
Kupfer, 18 Th. Antimon und 70 Th. Zinn ausgegossen und frisch abgedreht. Mit diesem
Ausgusse liefen sich die Zapfen ganz ausgezeichnet ein, blieben blank und glatt,
ohne starken Lagerverschleiſs zu zeigen.
Als Schmiermittel für den Zapfen der mittleren Walze dient Schmieröl, für den der
Ober- und Unterwalze hat sich Rohunschlitt, besonders aber riechender Speck als ganz
praktisch erwiesen. Man braucht hiervon für das Gerüst in 24 Stunden 0,5 bis 2k.
Die Stärke der Pressung, welche durch die Druckschraube bei einer Umdrehung des
Spillerrades erzielt wird, richtet sich bekanntlich nach dem Umsetzungsverhältnisse
der Kegelräder und der Ganghöhe der Schraube. Ist letztere gleich 35mm und sind die Zähnezahlen der gleichen Räder =
48, so beträgt der Druck bei der Drehung um einen Zahn
\frac{35}{48}=0^{mm},73. Unter Berücksichtigung der geringen
Erwärmung, die man den Plattinen zur Erzielung zünderfreier Feinbleche angedeihen
lassen darf und die naturgemäſs bei jedem Stiche abnimmt, ist eine Pressung von etwa
18 Proc. der Plattinenstärke bei den zwei ersten Stichen und ebenso viel Procente
der nach jedem weiteren Stiche resultirenden Stärke des Streckers genügend.
Auch hier führen wir an einem bestimmten Beispiele diese Angabe unter der
Voraussetzung durch, daſs, wie fast allgemein üblich, mit zwei Plattinen zugleich
gearbeitet wird. Der Endzweck seien Feinbleche von 1000 × 2000 × 0mm,50, die dazu gehörigen Plattinen sind 1040mm lang × 152mm
breit und 7mm,5 stark. Für den ersten Stich unten
(zwischen Unter- und Mittelwalze) gibt man eine Pressung von 7,5 × 0,18 = 1mm,35. Man hat also die Druckschraube so weit zu
öffnen, daſs beim Durchgange der Plattine ein Spielraum von 7,5 – 1,35 = 6mm,15 bleibt, das sind 6,15 : 0,73 = 8,5 Zähne. In
derselben Weise rechnen sich die weiteren Pressungen (in Millimeter) aus, die aus
folgender Zusammenstellung ersichtlich sind:
I. Stich
II. Stich
III. Stich
unten
oben
unten
oben
unten
oben
1,35
0,36
1,46
0
1,10
0,36
IV. Stich
V. Stich
unten
oben
unten
oben
1,10
0,36
0,73
0
Bei diesen fünf Stichen ist jede Plattine für sich durchgelassen worden. Rechnen wir
diese Pressungen zusammen, so erhalten wir einen Gesammtdruck von 1,35 + 0,36 + 1,46
+ 1,10 + 0,36 + 1,10 + 0,36 + 0,73 = 6mm,82. Da
die Plattine ursprünglich 6mm,5 stark war, bliebe
eine Stärke von 7,5 – 6,82 = 0,68. In Wirklichkeit beträgt diese Stärke nun 3mm, also das Vierfache der gerechneten. Es erklärt
sich dies daraus, daſs bei jedem Stiche in Folge des Widerstandes, den die Plattine
dem Zusammengepreſstwerden entgegensetzt, die Schraube durchschnittlich um einen
halben Zahn zurückgeht, und zwar bei den ersten Stichen mehr als bei den letzteren,
abnehmend mit der Stärke des Streckers. Die wirkliche Pressung vermindert sich
dadurch gegenüber der theoretischen um nahezu 6 Proc., so daſs 12 Proc. Druck
bleibt. Die beiden Plattinen sind also jetzt auf je 3mm Stärke herabgestreckt, werden nun auf einander gelegt, wodurch sie eine
Gesammtstärke von 6mm erreichen, und mit derselben
Hitze wie folgt weiter gewalzt. Erster Druck, da die Strecker schon ziemlich kalt
sind, nur 15 Proc., also etwa 0,90. Geöffnet werden sieben Kämme von je 0mm,73 Oeffnung = 5mm,11. Demnach die Pressung des ersten Stiches 6,0 – 5,11 = 0,89 und
folgende Tabelle:
I. Stich
II. Stich
III. Stich
unten
oben
unten
oben
unten
oben
0,89
0
1 K. = 0,73
½ K. = 0,37
1 K. = 0,73
0
IV. Stich
V. Stich
VI. Stich
VII. Stich
unten
oben
unten
oben
unten
oben
unten
oben
1 K. = 0,73
0
½ K. = 0,36
0
½ K. = 0,36
0
½ K. = 0,36
0
also Gesammtdruck 0,89 + 0,73 + 0,37 + 0,73 + 0,73 + 0,36 +
0,36 + 0,36 = 4,53, bliebe eine Eisenstärke von 6,0 – 4,53 = 1mm,47 beider Tafeln zusammen, während aus dem
schon erklärten Grunde, in Wirklichkeit eine Tafel allein 1mm,5, also beide zusammen 3mm stark sich zeigen. Bei dieser Stärke haben die
Strecker eine Länge von 600mm erreicht und werden
nun zur Vollendung dem Duobetrieb übergeben. Denn es empfiehlt sich durchaus nicht,
etwa drei Strecker oder mehr über einander gelegt mittels des Trios auf eine
geringere Stärke, also gröſsere Länge ausziehen zu wollen. Die einzelnen Lagen
verschieben sich zu leicht unter einander, wodurch während des Durchganges
Druckveränderungen in der Fläche der Tafeln und in Folge dessen ungleiche
Streckungen entstehen, welche bis zu Faltenbildungen gehen und dadurch Anlaſs zu Ausschuſs schon beim
Vorstrecken, jedenfalls beim Vollenden geben. Auf die Einzelheiten des Betriebes
kommen wir bei der Besprechung über den Werth des Lauth'schen Trios zur Feinblecherzeugung zurück.
Durch unsere Ausführungen über die passendsten Druckverhältnisse werden wir auf die
Brechkappen geleitet, welche, wie schon die Bezeichnung andeutet, von Guſseisen,
nicht zu stark im Querschnitte, gemacht werden, damit sie bei zu bedeutender oder
unvorsichtiger Inanspruchnahme der Streckleistung zuerst „brechen“, ehe die
theueren Bestandtheile des Gerüstes oder der Strecke dieser Gefahr des
Gebrochenwerdens ausgesetzt sind. Denn da während der Arbeit durch das Bindeglied
des Streckers die Kraftmaschine mit Schwungrad von der ersten Kuppelung bis zum Ende
des Walzengerüstes ein zusammenhängendes Ganzes, eine feste Verbindung bildet, muſs
eines der Verbindungsglieder „nachgiebig“ construirt sein. Deshalb ist es ein
ebenso groſser als unbegreiflicher Fehler, wenn man diese Brechkappen von
Schmiedeeisen herstellt. Man wählt das Guſseisen auch aus einem weiteren Grunde.
Wenn sich beim Steckenbleiben einer Platte oder eines Streckers die Druckschraube in
der Ständermutter so verbeiſst, daſs sie mit Hebel und Winde nicht aufwärts gedreht
werden kann, wenn also die erwähnte feste Verbindung zu einer starren wird, dann ist
sie am einfachsten zu lösen dadurch, daſs man die Brechkappe mit einem Meiſsel
anhaut. Wäre sie von Schmiedeeisen, müſste man sie durchhauen. Dabei ist wohl darauf
zu achten, daſs nicht Stücke der Brechkappe, die in Folge des gewaltigen Druckes,
der durch die Schraube und die Vermittelung der Walzen auf ihr lastet, mit groſser
Gewalt aus einander geschleudert werden, die dabei beschäftigten Arbeiter verletzen.
Um dieser Gefahr vorzubeugen, bindet man am besten den Körper der Kappe locker mit
einem breiten schmiedeeisernen Ringe, aber nur locker, daſs einerseits die
Widerstandsfestigkeit der Kappe gegen das Brechen nicht erhöht wird, andererseits
aber nicht einzelne Stücke, wie beschrieben, aus einander fliegen können. Man hat
für die geschilderten Brechkappen schon verschiedene Surrogate zu schaffen gesucht.
Wir sagen absichtlich Surrogate, denn bis jetzt hat sich unseres Wissens keines
derselben, weder beim Trio, noch beim Duo, einzubürgern vermocht. Der nächstliegende
Gedanke war, an Stelle der Brechkappen Federn mit einer bis zu einem bestimmten
Grade reichenden Widerstandskraft zu geben, welche pufferartig construirt sind. Die
Versuche damit schienen aber zu keinem annehmbaren Ergebnisse geführt zu haben,
wahrscheinlich weil die Datier der Stahlfedern zu kurz war, also diese Anordnung
sich viel zu kostspielig erwies. Der Ersatz der guſseisernen Brechkappen durch ein
anderes, billiges, die Gefahr eines gröſseren Bruches verhütendes Mittel ist demnach
unseres Wissens vorläufig eine noch ungelöste Aufgabe. (Vgl. in Verfolg dieses
Berichtes: Brechtopf der Duisburger Maschinenfabrik und
Parges' Brechkapsel.)
Ueber die Walzentische, Abstreifmeiſsel und Ueberhebvorrichtungen wollen wir nur
folgendes bemerken: Die Lage der Abstreifmeiſsel muſs der Austrittstelle des
Walzgutes gut angepaſst sein, da sie sonst, besonders wenn sie zu hoch liegen,
leicht vom Strecker gefaſst und weggeschleudert werden, der sich selbst dann
zwischen den Walzentischen, den Stangen und den Walzen verwickelt. Für kleinere
Blechwalzwerke ist empfehlenswerth, für das Ueberheben auf der Rückseite bis zum
Durchgange durch die Mittel- und Oberwalze die Umdrehung der Walzen selbst zu
benutzen. Die betreffende Anordnung ist bekannt.
Ehe wir die Einzelstücke des Gerüstes verlassen, möchten wir auf einen für das
bequeme Herausnehmen und Einbauen der Walzen wichtigen Punkt aufmerksam machen. Der
Ständer muſs so weit construirt sein, daſs der Walzenkörper auch in seinen oberen
Partien luftig Platz hat. Bei einem Durchmesser von 600mm macht man die lichte Weite zwischen den beiden Ständerhälften
mindestens = 650mm.
Die Leistungsfähigkeit eines derartigen Trios ist nun in Folge seines bedeutenden
Streckvermögens und der anderen schon erwähnten Vortheile eine sehr bedeutende.
Auch hier greifen wir, um zu vergleichenden Ergebnissen zu kommen, zu bestimmten, die
Leistung des Trios oder Duos bedingenden Annahmen. Da das Trio bis zu 1mm,5 Stärke herab strecken kann, setzen wir
voraus, daſs Feinbleche in dieser Stärke zu erzeugen sind. Das Trio bedarf in diesem
Falle zu seiner vollständigen Ausnutzung bezieh. Ergänzung zweier
Vollendwalzengerüste, da, wie wir sofort sehen werden, bei Erzeugung dünner
Feinbleche ein Fertiggerüst die vom Trio geleisteten Strecker absolut nicht in
derselben Zeit fertig auswalzen kann. Drei Gerüste erfordern eine Betriebskraft von
mindestens 100 bis 120 , während das Vorstreckduo mit dem dazu gehörigen
einen Fertiggerüste mit 80 auskommt. Die Umdrehungszahl der Walze ist für
beide Fälle etwa 50 in der Minute, der Arbeiterstand ebenfalls für beide Fälle 1
Vorwalzer, 1 Hintermann, 1 Schraubensteller, 1 Schmierjunge,
1 Ofenarbeiter, unter Umständen 1 Doppier. Diese Mannschaft ist nun im Stande, in der
Schicht von 12 Stunden mittels Trioarbeit und zwei Wärmöfen gewöhnlicher Art etwa
6000 bis 7000k Plattinen von dem mittleren
Durchschnittsgewichte von 10k, also 600 bis 700
Stück zu strecken. Rechnet man auf die zur Ruhe und zum Plattinenwärmen nöthigen
Pausen reichlich 2 Stunden ab, so kommt auf die Stunde eine Arbeitsleistung von 60
bis 70 Stück.
Das Strecken von zwei Plattinen (da mit zwei Plattinen zugleich gearbeitet wird) auf
die angegebenen Stärken erfordert also annähernd 2 Minuten, während welcher 12
Doppelstiche (je einer unten und oben) gemacht werden.
Wir haben gesehen, daſs die Trioarbeit in der Stunde etwa 60 Plattinen zu 10k zu strecken vermag, und gehen gewiſs nicht irre,
wenn wir behaupten, daſs
das Duo in derselben Zeit nicht mehr als 40 Stück bewältigt, also ⅔ der
Trioleistung. Aber auch diese Bruchtheilleistung ist nur für ganz bestimmte
Blechsorten möglich, in welche die Vorstrecker umzuwandeln sind. Denn sobald die
Vorstreckarbeit verrichtet ist, tritt der bedeutende Unterschied zwischen den beiden
Arbeitsweisen auf, der eine ganz verschiedene Organisation der weiteren
Vollendarbeit bedingt. Beim Duobetrieb übernimmt dieselbe Arbeiterpartie, welche
vorgestreckt hat, auch die Fertigarbeit, während der Triobetrieb wegen seiner
enormen Streckleistung mindestens eine besondere Fertigpartie erfordert, welche aus
1 Vorwalzer, 1 Hinterwalzer, 1 Schraubensteller, 1 Schmierjungen und 1 Ofenarbeiter
besteht und zur raschen Förderung der Arbeit zwei Flammöfen zur Verfügung hat. Ist
nun bei längeren und zugleich dünneren Blechen, z.B. bei der Sorte 650 × 1300 × 0mm,65, welcher eine zweitaflige Plattine im
Gewichte von etwa 10k zukommt, die Arbeit des
Vollendens durch die nothwendig gewordene Doppelung und sorgfältige Wärmung des
Doppiers eine schwierigere und damit zeitraubendere geworden, so vermag eine und
dieselbe Partie beim Duobetriebe die erzeugten 40 Strecker, jetzt Doppier, nicht in
der Zeit aufzuarbeiten, in der die neue Plattinencharge nachrückt. Dadurch wird die
Raschheit der Vorstreckarbeit von selbst gedämmt. Es kann in unserem Falle der
Einsatz bis auf 30 Plattinen herabgedrückt werden, das wäre die Hälfte der
Trioleistung. Dieses Verhältniſs zwischen Vorstreck- und Vollendarbeit wird beim
Duobetriebe mit einer Arbeiterpartie um so ungünstiger, je dünnere Blechsorten
vorliegen, während der Triobetrieb insofern dadurch nicht gestört wird, als die
zweite Küre sofort alle erzeugten Doppier auf sich nimmt, die Triomannschaft also in
keinerlei Weise gehemmt ist. Allerdings ist es eine andere Frage, ob die
Fertigpartie alle die Doppier in derselben Zeit aufzuarbeiten vermag, in der das
Trio sie abwirft. Häufen sich dieselben an, so muſs man in der Lage sein können,
Sorten zuzutheilen, bei denen die Vollendarbeit rascher geht als die Streckarbeit.
Nun wird man wohl selten in dieser vorgeschriebenen Weise die Arbeit vertheilen
können. Wir haben deshalb auch früher angenommen, daſs auf ein Trio zwei
Fertiggerüste kommen, denen dann auch zwei Fertigpartien und vier Flammöfen
zugetheilt werden müssen. Da läge demnach der Vortheil des Triosystems nicht allein
im Systeme selbst, sondern auch in der dadurch hervorgerufenen Arbeitsvertheilung.
Diese erheischt also beim Triobetriebe für dünnere Bleche drei Arbeiterpartien mit
einem Vorstreck- und zwei Fertiggerüsten. Nun unterliegt es aber nicht dem
geringsten Zweifel, daſs dieselben drei Arbeiterpartien beim Duobetriebe in
derselben Zeit von solchen dünneren Blechen mindestens ebenso viel fertig bringen.
Uebersehen wir aber nicht, daſs sie dazu sechs Gerüste, also das Doppelte von der
Trioarbeit benöthigen, also auch eine erhöhte Betriebskraft durch den Plusaufwand in
Reibungen, erhöhten Schmiermaterialverbrauch und vermehrter Maschinenwartung beanspruchen.
So kommen wir bei der Betrachtung der Erzeugung dünnerer Bleche auf ein
eigenthümliches Resultat. Die Fertigarbeit tritt hier so stark in den Vordergrund,
daſs der Werth der mehr oder weniger raschen Streckarbeit beinahe verschwindet. Der
Duobetrieb verlangsamt sie durch sich selbst, der Triobetrieb erfordert so viel
Hilfsmannschaft, daſs, was die Vorstreckarbeit in jeder Beziehung an Vorsprung
gewinnt, die Vollendarbeit wieder einbüſst. Bei der Fabrikation dünner Bleche
besteht der Vortheil der Trios nicht in der Erhöhung der Erzeugung, sondern in
Ersparungen an Betriebskraft, an Betriebsmaterial, an Betriebskraftbedienung und an
den geringeren Anlagekosten mit geringerer Amortisation. Ob diese Vortheile immer im
einzelnen Falle die Vortheile aufwiegen, werden wir später sehen.
Im besten Lichte zeigt sich das Triosystem bei der Erzeugung von mittleren Blechen
mit einem Gewichte von 20 bis 30k, zu denen
Plattinen von 23 bis 35k gehören. Mit zwei der
genannten Arbeiterpartien können in der Schicht von solchen Sorten 600 bis 700
Stück, also 12000 bis 21000k, fertig hergestellt
werden, eine Leistung, welche der Duobetrieb mit denselben Arbeitern in derselben
Zeit nicht einmal zur Hälfte erreicht. Hier kommt das hervorragende Streckvermögen
des Trios, die der Vollendarbeit wenig zu thun übrig läſst, zur eigentlichen
Geltung, und da Feinbleche in den angegebenen Gewichtsgrenzen auch von bedeutenderer
Stärke sind, machen sich die Schattenseiten des Triobetriebes, auf den wir sofort
übergehen, weniger bemerklich.
Eine volle Ausnützung der Form des Triobetriebes, welche durch das
Schleppwalzensystem in zu engen Grenzen gehalten wird, erscheint uns auch nur durch
Antrieb der Oberwalze mittels Krausein erreichbar.. Nimmt man eine längere Form der
Zähne, so kann man mit der Plattinenstärke bis zu 60mm gehen, wobei die Krauselzähne immer noch vollständig genügend in
einander greifen. Bei einer Bundlänge der Walzen von 1500mm kann man Bleche bis 1400mm Breite sammt Abschnitten bequem durch die Walze
gehen lassen. Die dazu gehörigen Plattinen erhalten eine Länge von 1450mm und wägen dann bei der Breite von 152mm und Stärke von 60mm 145 × 15,2 × 6 × 7,8 = 103k das
Stück. Das daraus gewalzte und beschnittene Blech ist an 88k schwer und bei einer Länge von z.B. 4000mm noch immer 2mm,0 stark. Für die Kräuseln wendet man in neuerer Zeit ausschlieſslich
Stahlguſs an.
Aber auch noch eine andere Betrachtung läſst die Anwendung von Krausein zum Antrieb
der Oberwalze, wobei die Mittelwalze aber immer Schleppwalze nach unten und oben
bleibt, gegenüber dem Schleppwalzensystem räthlich erscheinen. Bei letzterem werden
Mittel- und Oberwalze nur durch Reibung mitgenommen, welche beim Betriebe durch das
Walzgut vermittelt wird. Dieser Vorgang soll sich theoretisch auf der ganzen Länge
der Berührungslinien entwickeln. Bei Leergang wird man diesem Ziele um so näher
kommen, je genauer die Walzen abgedreht sind. Nun tritt ja beim Trio auch während des
Walzens stets der Leergang, und zwar zwischen Mittel- und Unterwalze auf, sobald die
Plattine oben durchgesteckt wird, und da stets die Unterwalze es ist, die den
direkten Antrieb durch Reibung überträgt, so ist hauptsächlich hier die Entwickelung
der Reibung auf der ganzen Länge von Wichtigkeit. Sind nun aber auch Unter- und
Mittelwalzen auf das sorgfältigste abgedreht, so werden sie sich doch, besonders
beim häufigen Strecken von kurzen Plattinen, sehr bald in der Mitte auslaufen und
klaffen. Je kürzer der Walzenbund ist, desto störender wirkt dieser Uebelstand, weil
die Wahrscheinlichkeit groſs ist, daſs auf der kurzen Linie zu wenig
Annäherungsstellen sich vorfinden, wodurch die Reibung wesentlich verringert,
dagegen die Neigung der Mittelwalze zum Stehenbleiben aufs höchste gesteigert wird.
Man ist deshalb beim Schleppwalzensystem von den kurzen Trios zu den längeren
übergegangen, auch wenn die Breite der zu walzenden Bleche es nicht erfordert. Man
hätte wohl durch Vergröſserung des Durchmessers der Mittelwalze und damit ihres
Umfanges die Zahl der Berührungsstellen vermehren können, hätte aber damit zugleich
einen Hauptvortheil des Systems, das groſse Streckvermögen, theilweise aufgegeben.
So hat man von zwei Uebeln das kleinere gewählt und auch zur Erzeugung von kürzeren
Blechen den Walzenbund der Triowalzen nicht unter 1200mm Länge genommen. Ein Nachtheil ist und bleibt es immer, kurze Plattinen
auf langen Walzen zu strecken, weil, wie schon erwähnt, die Walzen in der Mitte sehr
bald auslaufen. Auch ist es wenig wirthschaftlich, für schmale Bleche lange schwere
und deshalb unverhältniſsmäſsig theure Walzen anzuschaffen; beim Schleppwalzensystem
würde also geradezu für den Triobetrieb eine Beschränkung der passenden Walzenwahl
eintreten. Man hat nun wohl versucht, diesem raschen Angriffe und Verschleiſs der
Walzenmitte dadurch entgegenzutreten, daſs man auch während der Arbeit Wasser auf
die Walzen flieſsen läſst und dadurch zugleich das Abzündern der Plattinen bezweckt
und erzielt. Die Walzen erhalten sich dadurch kühl und sind in der That in Folge
dessen widerstandsfähiger. Man übersehe aber ja nicht die Schattenseite dieser
Walzmethode, welche durch ihr unaufhörliches Wassergeriesel nicht allein die Walzen,
sondern auch die zu streckenden Plattinen abkühlt. Das Streckvermögen der Walzen
wächst mit ihrer Erwärmung, wird also durch die Abkühlung stets auf der ersten
Leistungsstufe erhalten. Die Plattinen müssen wegen dieser Abkühlung höher erwärmt
werden, was nicht nur einen erhöhten Kohlenaufwand, sondern eine stärkere
Cylinderbildung im Gefolge hat. Es ist nicht zu verkennen, jede scheinbar gewonnene
Ausnützung der Triovortheile für dünnere Bleche, die meistens schmal und kurz sind,
hat sofort ihre Kehrseite. Versieht man das Trio auch zum Vorstrecken dünner Bleche
mit Krauselantrieb, wozu uns die vorstehende Betrachtung zu drängen scheint, so
entgeht man den geschilderten Nachtheilen. Dagegen bezweifeln wir sehr, ob es mit diesem
Antriebe möglich ist, die Strecker unter 3mm
Stärke herunterzubringen, weil ja bei dieser Stärke die Kämme schon ganz am Grunde
greifen müſsten. Vorstrecker von 3mm Stärke für
dünne Bleche sind nun aber von sehr fraglichem Werthe, weil sie noch nicht gedoppelt
werden können, sie müſsten also beim Duo erst dazu präparirt werden. Wo bleibt aber
da die Ausnützung des Triostreckwerkes? Je mehr wir uns in die einzelnen Fälle
vertiefen, desto deutlicher erkennen wir die Grenzen, welche den Trios in der
Feinblechwalzerei gestellt sind.
Bei unseren bisherigen Erörterungen haben wir den wichtigsten Punkt in der
Feinblechfabrikation, die Forderung der gleichmäſsigen Stärke für jede einzelne
Tafel noch nicht ins Auge gefaſst. Geschirrfabrikanten räumen beim Bezüge der
Geschirrbleche keinen gröſseren Spielraum ein als 5 Proc. der Stärke auf- und
abwärts, 0mm,50 starke Bleche können also zwischen
den Grenzen von 0,525 bis 0mm,475 sich bewegen.
Dasselbe gilt für sämmtliche Feinbleche, welche zu Druckarbeiten verwendet werden.
Sehen wir zu, wie sich die Trioarbeit hierzu eignet. Die Plattinen zur Erzeugung
dieser Feinbleche werden in der ersten Hitze mittels der Vorstreckwalzen – in
unserem Falle des Schleppwalzentrios – möglichst lang und dünn, bis zu 0mm,5 herab, ausgestreckt und je nach der Stärke
der Bleche einmal, zweimal, auch dreimal gedoppelt (nach jedem Doppeln werden sie in
Blechflammöfen mit stark kohlender Flamme aufgewärmt und gestreckt bezieh. zur Länge
im fertigen Zustande sammt Abschnitten ausgewalzt). Soll nun die Forderung der
gleichmäſsigen Stärke jeder Tafel erzielt werden, so ist es unbedingt nöthig, daſs
schon das Product der Vorstreckwalzen, Sturz oder Strecker genannt, an allen Punkten
seiner Fläche eine gleichmäſsige Stärke besitzt. Bei einer bedeutend wechselnden
Stärke des Streckers an verschiedenen Flächenstellen ist es auch für die best
zusammen passenden Vollendwalzen ganz unmöglich, die geforderte Gleichmäſsigkeit der
Tafelstärke zu gewinnen. Ja es liegt die Gefahr sehr nahe, daſs der an und für sich
gleiche Druck der Vollendwalzen, ausgeübt auf die ungleich starke Strecker- oder
Dopplerfläche, Walzenkanten und Falten auf denselben hervorruft, die sich bis zu
Rissen in den Tafeln steigern und sogar mit ihren erhabenen Rändern die
Vollendwalzen durch Eindrücke in dieselben betriebsunfähig machen, so daſs man sie
zeitweise im Wasser leer laufen, oder in den Ständern abschmirgeln, oder im
schlimmsten Falle zum Abdrehen herausnehmen muſs. Zu diesem Uebelstande, daſs ein
ungleich starker Strecker oder Doppier entsteht, gibt nun leider das Trio sehr
häufig Veranlassung, sei es, daſs die Stellung der Walzen beim Einbau und Betrieb
nicht auf das sorgfältigste geregelt, sei es, daſs sich die Walzen, wenn auch aufs
beste abgedreht und eingebaut, in kurzer Zeit aus den schon genannten Gründen
ungleich auslaufen. Die Erfahrung bestätigt es, daſs die Trios zu sehr ungleich starken Tafeln,
unter Umständen zu einem ganz bedeutenden Ausschuſsfalle führen.
Der Duobetrieb kann, wenn zweckmäſsig geleitet, auch bei dünnen Blechen bis zu etwa 4
Proc. durchschnittlichem Ausschuſs heruntergebracht werden. Die Trioarbeit ist für
Bleche unter 0mm,50 Stärke kaum mehr zulässig, hat
aber jedenfalls das Doppelte, wenn nicht Dreifache des Ausschuſsfalles zur Folge.
Dabei kommen bei ihren Erzeugnissen Ungleichmäſsigkeiten in der Blechstärke der
einzelnen Tafeln bis zu 0mm,05, ja 0mm,10 vor. Früher haben wir gesehen, daſs bei
solchen dünnen Blechen auch die Menge der Leistung des Trios nicht über die der
Duoarbeit gesteigert werden kann. Bei der Betrachtung des wichtigsten Punktes, für
die Erzeugung dünner Bleche, der Gleichmäſsigkeit ihrer Tafelstärke, muſsten wir
geradezu einen Uebelstand des Triobetriebes feststellen. So glauben wir unsere
nachstehende Schluſsfolgerung genügend vorbereitet zu haben. Sie gipfelt darin, daſs
wir die Verwendung des Lauth'schen Trios für
Fabrikation der eigentlichen Feinbleche jedenfalls unter 0mm,60 für nicht rathsam erklären. Das eigentliche
Arbeitsfeld dieses Systems in Verbindung mit dem Antriebe der Oberwalze durch
Krausein liegt in dem Feinblechgebiete, wo die einzelne Tafel über 20k schwer und über 1mm stark ist und etwa 90k nicht
übersteigt. Bei solchen Blechgattungen, z.B. bei sogen. Meterblechen stärkerer
Sorte, treten die hervorragenden Eigenschaften dieses Systems, das in gröſster
Leistungsfähigkeit gipfelt, in glänzender Weise hervor, ohne daſs die
gekennzeichneten Schattenseiten – ungleiches Ausarbeiten der Walzen, häufiges
Steckenbleiben des Walzengutes oder erhöhter Kohlenverbrauch und starker Verlust,
bedeutender Ausschuſsfall beim Fertigmachen in Folge ungleicher Strecker – sich zu
bedeutend bemerkbar machen.
Zum Schlusse machen wir kurz noch auf eine weitere Eigenthümlichkeit mehrerer der
erwähnten Neuanlagen aufmerksam. Man hat nämlich, wahrscheinlich um an Dampf und
Bedienungsmannschaft der Arbeitsmaschinen zu sparen, an eine einzige sehr kräftige
Maschine (bis 300 ) eine Reihe von Gerüsten, 5 bis 6 an der Zahl, darunter 2
Schleppwalzentrios, gehängt. Es würde uns auf ein ganz anderes Gebiet als das
diesmal behandelte führen, wollten wir Vor- und Nachtheile dieser Anordnung
erwähnen. Nur das eine möchten wir den Constructeuren dieser langen Straſse zu
erwägen geben, daſs jeder Unfall, der bei dem ersten Gerüste eintritt, nicht nur
dieses, sondern auch alle folgenden zeitweise zum Stillstande bringt. Unfälle sind
bei bester Construction der Streckerbestandtheile und bester Betriebsführung einmal
nicht zu vermeiden und ziehen bei der genannten Anordnung jedenfalls groſse
Zeitopfer und deren Folgen nach sich. Wir würden schon aus diesem Grunde auch das
Lauth'sche Trio nie mit mehr als zwei Fertigduos
kuppeln.
Triouniversalwalzwerk mit Umführung von Ernst Stegmann in Kaczagorka, Vertreter Gust.
Brisker in Prag (D. R. P. Nr. 50397 vom 16. Juli
1889).
Das Walzwerk besitzt drei Walzen von gleichem Durchmesser, deren mittlere fest
gelagert ist, während die Ober- und Unterwalze verstellbar sind.
Auf der Vorderseite des Walzwerkes (Fig. 22 und 23) befinden
sich zwei Paar senkrechte Walzen V und V1, welche unabhängig
von einander verstellbar sind und entweder von den Kamm walzen aus angetrieben
werden, und zwar das eine Paar von oben, das andere Paar von unten, oder es kann der
Antrieb des einen senkrechten Walzenpaares durch ein auf die festgelagerte
Mittelwalze aufgekeiltes Zahnrad erfolgen. – Vor und hinter den wagerechten Walzen
befinden sich die durch einen – nicht gezeichneten – Hebecylinder und die Rollen RR1 gleichzeitig
hebbaren Walzentische.
Ueber dem Walzentische W1 der Hinterseite befindet sich ein Bügel B,
welcher durch den Cylinder C oder mittels einfachen
Hebels um den Bolzen O gedreht werden kann.
Das Walzen geht in folgender Weise vor sich: Die Bramme wird zuerst in mehreren
Durchgängen in gewöhnlicher Weise vorgestreckt, indem das auf der Hinterseite
austretende Walzstück stets mit dem Walzentische W1 gehoben und dann zwischen Mittel- und Oberwalze
gestoſsen wird.
In Fig. 22
sind die gehobenen Walzentische durch punktirte Linien angedeutet; der Bügel B ist hochgehoben.
Ist das Walzstück nach einigen Durchgängen bis auf eine bestimmte Länge und Dicke
ausgewalzt, so wird vor dem nächsten Durchgange zwischen Unter- und Mittel walze der
Bügel B herabgelassen, wie aus Fig. 23 zu ersehen, und
der Walzentisch W1 ein
wenig angehoben, so daſs die Rolle r desselben etwas
über die Abstreicher vorsteht. Der austretende Walzstab wird in Folge dessen
umgebogen und sofort zwischen Mittel- und Oberwalze geführt. Ist das Walzstück
zwischen die letzteren Walzen getreten, so wird der Bügel B wieder hochgehoben und die umgebogene Schleife des Walzstabes kann sich
ungehindert nach hinten erweitern.
Das Charakteristische des Walzwerkes ist die Anwendung von zwei Paar senkrechten
Walzen auf eine Seite des Walzgerüstes und die Anwendung einer
Umführungsvorrichtung, durch welch letztere man das Walzstück bei jedem einzelnen
Durchgange ganz nach Bedarf und Belieben entweder umbiegen und zurückführen oder auf
der Hinterseite gerade austreten lassen kann, welche Umführungsvorrichtung ein
Erweitern der Schleife des umgebogenen Walzstabes gestattet, sobald derselbe
zwischen Mittel- und Oberwalze getreten ist.
Die senkrechten Walzen werden, wie bereits erwähnt, unabhängig von einander
angetrieben und unabhängig von einander verstellt.
Durch die beschriebene Walzmethode wird das Auslaufenlassen des langen Walzstabes bei
jedem Walzstiche auf der Hinterseite erspart, das Walzen geht bedeutend schneller
vor sich, es wird wärmer gewalzt und kann daher Universaleisen in bedeutend
gröſseren Längen hergestellt und eine wesentlich gröſsere Production erzielt werden.
– Endlich soll nach Meinung des Erfinders diese Walzmethode noch den Vortheil
gewähren, daſs durch das öftere Umbiegen und wieder Geraderichten des Walzstabes die
etwa eingewalzte Schlacke, Glühspäne u. dgl. eher abspringen und man ein reineres,
fehlerfreieres Product erhält. – Wir können diese Meinung bezüglich der Schlacken
nicht theilen.
Wir schlieſsen an Vorstehendes einige Universalwalzen an und erwähnen zunächst das
Universalwalzwerk von Levi D. York in Portsmouth und
James Edwin York in Ashland.
Das in Fig. 24
gezeichnete Walzwerk ist zum Auswalzen von H-Eisen bestimmt. Das Kaliber wird
gebildet von zwei wagerechten a und zwei senkrechten
Walzen b, deren Achsen in einer und derselben Ebene
liegen. Vor und hinter den Walzen sind Führungen i
angeordnet. Diese und alle Walzen können von einem Handrade o aus verstellt werden. Zu diesem Zwecke sind die Führungen i durch Bolzen mit den auf starken, in den
Walzenständern befestigten Bolzen gleitenden Schlitten e verbunden, die auch die Lager für Gegendruckwalzen s tragen. Je zwei der letzteren, welche um einen Winkel
von etwa 90° aus einander liegen, nehmen den Druck der senkrechten Walzen b auf. Dadurch können diese sehr leicht gelagert
werden. Die schwachen Lager derselben bestehen aus auf den Zapfen der wagerechten
Walzen a ruhenden Pfannen, die mittels je zwei Bolzen
mit den Schlitten e verbunden sind. Auf diesen stehen
je zwei Bolzen, auf welchen Lager für die Wellen r
gleiten. Diese stehen durch Kegelräder unter einander und mit den Stellschrauben für
die Oberwalze a, sowie für die Schlitten e in Verbindung, so daſs durch Drehen des Handrades o alle Walzen gleichmäſsig eingestellt werden können.
Dabei gleiten die Lager für die Kegelgetriebe auf den betreffenden Wellen, nehmen
dieselben aber bei ihrer Drehung mit.
Nach The Iron Age, Nr. 30, soll diese Neuerung den
gewöhnlichen Kaliberwalzen gegenüber wesentliche Vortheile dadurch bieten, daſs
Träger von 100 bis 600 Höhe mit 50 Proc. Ersparniſs an Betriebskosten angefertigt
werden können.
Die zulässige Trägerhöhe kann so sehr erweitert werden, daſs dieselbe keine
Schwierigkeit bis 1500 hat, während jetzt Träger von 500 eine vorzügliche
Arbeitsleistung erfordern. Ebenso leicht können die Maſse des Steges und der
Flanschen in der Stärke geändert werden. Da der Druck in zwei Richtungen erfolgt, so
wird eine gleichmäſsige Streckung in Steg und Flanschen und somit eine Verstärkung
der Träger erzielt.
Das Gewicht der Walzen beträgt nur 8 Proc. derjenigen des alten Systems, und soll die
Verminderung der Zahl der Walzen und der Lagerungen eine Ersparniſs an Kraft von
etwa 40 Proc. bedingen, trotz einer gröſseren Leistungsfähigkeit von wenigstens 50
Proc.
Die erheblichen, hier ja nur schätzungsweise angegebenen Vortheile, die der
Wirklichkeit sich allerdings nähern werden, haben schon mehrfach die Lösung der
Aufgabe nach dieser Richtung angeregt. Die Kalibrirung (Fig. 25 und 26) bietet
aber nach Daelen's Ansicht nicht wenig
Schwierigkeiten.
Da anzunehmen ist, daſs von den Erfindern als gefügigstes Material nur Fluſseisen
vorgesehen ist, so kann, da die Herstellung von Blöcken mit I-förmigem Querschnitte
in Coquillen bis jetzt durchschlagende Erfolge nicht aufzuweisen hat, nur der
rechteckige Querschnitt in Frage kommen.
Ein Blick auf die Figur ergibt indessen, daſs hier ein wesentliches Glied in der
Kette fehlt, indem die Theile o beim Beginne des
Walzens keinen Druck erhalten und deren Oberfläche daher zerreiſsen muſs, bevor das
Kaliber soweit geschlossen ist, daſs ein Druck durch die Walzen a erfolgt. Da ferner das Material, welches durch diese
gestreckt wird, das unter o liegende mitreiſst, so
erscheint es fraglich, ob das Kaliber sich füllen wird.
Nach Art der Universalwalzen ist auch das Walzwerk zur Herstellung von glattkantigem
Flacheisen von Gebrüder Schmidt in Hagen (D. R. P. Nr.
44721 vom 20. November 1887) angeordnet. Die Erfinder wollen die
Schwierigkeiten beseitigen, welche sich bei der Herstellung von Nägeln durch
Zerschneiden von Bandeisen dann ergeben, wenn die die Nägelköpfe bildenden
Schmalseiten des Bandeisens Grate oder unsaubere Kanten haben. Man walzt deshalb das
Bandeisen vor dem Zerschneiden durch ein Vierwalzwerk (Fig. 27), dessen
Walzenachsen in einer Ebene liegen und von denen die obere und untere Walze die
Schmalseiten des Bandeisens mittels eines eingedrehten Kalibers umfassen und
glätten. Bei der Herstellung von Nägeln mit profilirtem Schafte werden demselben
entsprechende Kaliber in die senkrechten Walzen eingedreht.
Wir sind der Meinung, daſs in den meisten praktisch vorkommenden Fällen mit der
vorstehend beschriebenen Erfindung eine Schweiſsung nicht mehr zu erreichen ist. Die
Grate werden wohl herunter gedrückt und die Kante glatt, der Uebelstand wird aber
beim nachfolgenden Zerschneiden ungeschwächt wieder zum Vorscheine kommen.
Umführungen in verschiedenen Abänderungen zum Gebrauche
beim Walzen von Blech, Universaleisen, Bandeisen und anderen Walzeisensorten gibt
E. Stegmann bezieh. G. Brisker
in Prag an (D. R.
P. Nr. 50637 vom 13. April 1889).
Die Neuerung besteht darin, daſs bei Duo- oder Triowalzwerken das aus den
Arbeitswalzen tretende Walzstück durch eine oder mehrere heb- und senkbare Walzen
(Umführungswalzen) derart umgebogen wird, daſs es, bei Duowalzwerken über die Oberwalze hinweg, bei
Triowalzwerken zwischen Mittel- und Oberwalze hindurch, auf die Vorderseite
zurückgeht und daſs, sobald es hier vollständig ausgetreten ist, sofort wieder der
nächste Durchgang zwischen Ober- und Unterwalze bezieh. zwischen Unter- und
Mittelwalze erfolgt.
Die heb- und senkbaren Umführungswalzen können in verschiedener Weise angeordnet
werden, immer ist die Anordnung jedoch eine solche, daſs das Walzstück bei jedem
einzelnen Durchgange entweder umgebogen und nach der Vorderseite zurückgeführt
werden, oder daſs es auf der Hinterseite gerade austreten kann.
Ist auf der Hinterseite ein hebbarer Walzentisch vorhanden, wie bei Blech- und
Universalwalzwerken, so kann derselbe bei jeder der nachstehend beschriebenen
verschiedenen Anordnungen der Umführungswalzen, nach jedem einzelnen Durchgange
beliebig, ohne Weiteres auch zum Heben und Zurückführen des gerade ausgetretenen
Walzstückes benützt werden, so daſs auch beim schnellsten Walzen nach jedem
einzelnen Durchgange ganz nach Bedarf oder Belieben mit Umführung oder ohne
Umführung des Walzgutes gewalzt werden kann.
Bei Triowalzen kann in Folge der eigenthümlichen Anordnung und Verwendung der heb-
und senkbaren Umführungswalzen die Schleife des umgebogenen Walzstückes sich
ungehindert nach hinten erweitern.
Die Umführungswalzen können in nachstehender verschiedener Weise angeordnet
werden:
1) Eine heb- und senkbare Walze w (Fig.
28).
Die Walze kann durch einen Cylinder c gehoben und
gesenkt werden.
Vor dem Austritte des Walzstückes auf der Hinterseite wird die Umführungswalze w etwas angehoben, das aus den Walzen tretende
Walzstück erhält dadurch sofort eine Krümmung nach oben; in dem Maſse, wie der
Austritt weiter erfolgt, wird auch die Walze w weiter
gehoben und das Walzstück dadurch so umgebogen, daſs es zwischen die obere
Arbeitswalze und eine Schleppwalze x1 bezieh. beim Trio zwischen Mittelwalze und
Oberwalze tritt. Eine Platte verhindert ein zu hohes Steigen des Walzstückes. Durch
Abstreifer und die Richtwalzen xx1 wird das auf der Vorderseite austretende Walzstück
wieder gerade gerichtet. Nach erfolgter Umführung wird die Walze w sofort wieder in das Niveau des Walztisches
gesenkt.
2) Die Umführungswalze w kann auch, wie in Fig. 32
gezeichnet, mit dem Walztische verbunden und mit diesem gehoben und gesenkt
werden.
3) Statt einer Walze können, wie Fig. 29 zeigt, auch zwei oder mehrere heb- und
senkbare Umführungswalzen ww1 zur Anwendung kommen; dieselben können entweder gleichzeitig oder
unabhängig von einander gehoben und gesenkt werden.
4) Die Walzen ww1
können, wie in Fig.
30 dargestellt, durch einen Bügel verbunden werden. Die Walze w dreht sich lose auf einer Welle, welche excentrisch
gedrehte, fest gelagerte Zapfen z (Fig. 30a) besitzt. Der
Bügel wird vor dem Austritte des Walzstückes durch einen Cylinder c um die Zapfen z
bogenförmig aufgerichtet, wobei in Folge der Excentricität der betreffenden Zapfen
die Walze w ebenfalls etwas angehoben wird. Das
austretende Walzstück wird dann in einfacher Weise nach oben umgebogen und in die
Arbeitswalzen zurückgeführt; sobald es von diesen Walzen gefaſst worden ist, läſst
man den Bügel wieder sinken, so daſs die Umführungswalzen in das Niveau des
Walzentisches zu liegen kommen; für einen etwaigen geraden Austritt des Walzstückes
bilden dieselben dann einen Theil des Walzentisches.
5) Die durch einen Bügel verbundenen Umführungswalzen ww1 können auch, wie in Fig. 33 dargestellt, mit
dem Walzentische verbunden und mit diesem gehoben und gesenkt werden. Der
Walzentisch wird vor dem Austritte des Walzstückes in die mit vollen Linien
gezeichnete Stellung gehoben und bleibt in dieser Stellung, solange man mit
Umführung weiter walzen will.
Soll das Walzstück nach der Fertigstellung oder eventuell auch während des Walzens
gerade aus den Arbeitswalzen austreten, so läſst man vor diesem Austritte den
Walzentisch sinken, wie durch die punktirten Linien angedeutet. Diese Anordnung der
Umführungswalzen eignet sich nur für Duowalzwerke, da bei derselben ein Erweitern
der Schleife nach hinten nicht möglich ist.
6) Die eine Umführungswalze w liegt hinter den
Abstreifern der unteren Arbeitswalze (Fig. 31) und dreht sich
lose auf einer Welle, deren Zapfen, ähnlich wie in Fig. 30a dargestellt, excentrisch
gedreht und fest gelagert sind. An der oberen Platte ist scharnierartig ein Bügel
mit einer zweiten Umführungswalze w1 befestigt, welcher Bügel durch einen Cylinder c gesenkt und gehoben werden kann. Vor dem Austritte
des Walzstückes wird die Walze w durch Drehung mittels
eines Hebels um 180°, also Benutzung der Excentricität der Walzenwelle, etwas höher
gestellt und zugleich der Bügel mit der Walze w1 herabgelassen. Die Umführung des Walzstückes
findet dann wieder leicht und sicher statt. Ist die Vorrichtung bei einem
Triowalzwerke angebracht, so wird nach erfolgter Umführung die Walze w in die ursprüngliche Lage zurückgedreht und die Walze
w1 mit dem Bügel
gehoben, so daſs die Schleife des umgeführten Walzgutes sich ungehindert nach hinten
erweitern kann.
Durch die vorstehend in verschiedenen Abarten angegebene Vorrichtung zum Umführen von
Blech, Universaleisen, Bandeisen und anderen Walzeisensorten werden nachstehende
Vortheile erreicht:
a) Während die bis jetzt bekannten Umführungen nur zum Walzen von Draht und feinem Bandeisen
bestimmt und nur hierzu geeignet sind, auch nur zum einmaligen Durchgange eines und
desselben Walzstückes dienen, kann die vorliegende Umführungsvorrichtung zum
Umführen aller, auch der breitesten und stärksten Bandeisen-, Flacheisen- und
sonstiger Walzeisensorten, sowie beim Walzen von Blech und Universaleisen benutzt
werden, und zwar in der Weise, daſs man das Walzstück während seines Auswalzens bei
jedem Durchgange durch dieselbe Umführungsvorrichtung gehen läſst (bei Kaliberwalzen
wird die Umführungsvorrichtung erforderlichen Falles von einem Kaliber zum anderen
weitergeschoben) und daſs man ferner bei jedem einzelnen Durchgange ganz nach
Belieben die Umführung benutzen oder das Walzstück gerade austreten kann.
b) Beim Walzen von Universaleisen und Blech mittels Umführung fällt durch das
abwechselnde Umbiegen und Geraderichten des Walzgutes sämmtliche eingewalzte
Schlacke (?), Glühspan u. dgl. ab; auſserdem kommt bei jedem Durchgange immer eine
andere Seite des Bleches nach oben zu liegen und können daher beide Blechseiten
abwechselnd abgefegt und in jeder Weise gereinigt werden.
Man erhält in Folge dessen reinere Bleche und weniger Ausschuſs.
c) Beim Walzen von Flach- und Bandeisen in Kaliberwalzen erspart man das zur
Vermeidung einer Gratbildung nothwendige Wenden des Walzstabes um 180° nach jedem
Durchgange.
d) Bei Benutzung der Umführung kommt auch bei Duowalzwerken nach jedem Durchgange
immer ein anderes Ende des Walzstabes zuerst in die Walzen, so daſs derselbe ebenso
wie beim Trio nach beiden Richtungen hin und her gewalzt wird.
e) Endlich erzielt man durch das Walzen mit Umführung in der beschriebenen Weise eine
gröſsere Production und eine bedeutende Ersparniſs an Arbeitslöhnen.
(Fortsetzung folgt.)
Tafeln
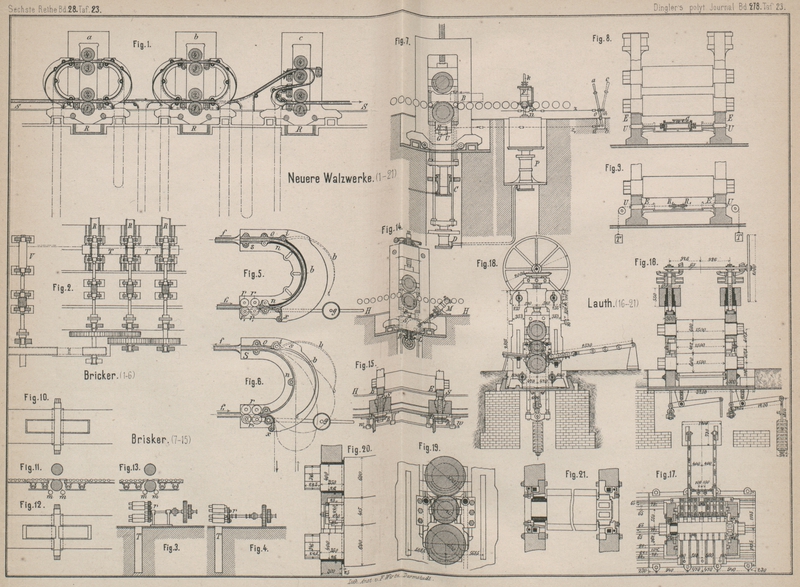